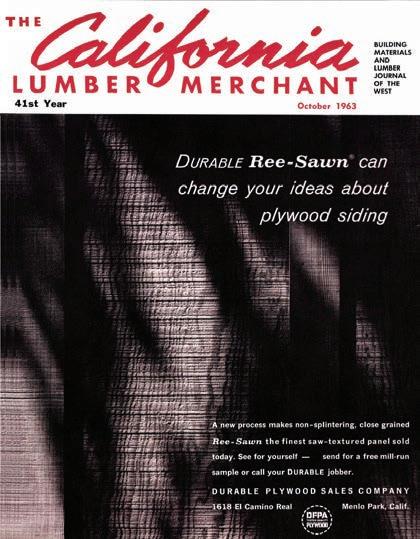
4 minute read
FLASHBACK
58 Years Ago This Month
Fifty-eight years ago this month, in October of 1963, The California Lumber Merchant covered a slew of technological and design innovations, as forest products companies ramped up their research and development efforts to better serve the ongoing building boom.
Perhaps most notably, Weyerhaeuser Co. unveiled the fi rst commercially marketed, completely prefi nished wood siding.
The new product carried a written performance warranty that the siding would not require repainting for at least seven years and that the factory-applied paint film would never peel or blister. It was initially offered in two sizes of beveled siding (1/2x 8 and 3/4x10) in five light colors (Super White, Seafoam Green, Golden Yellow, Silver Grey, and Desert Sand).
E.M. Williston, technical director for softwood lumber, described the fi nish as a two-coat “breathing paint” of 4-mil thickness. The fi rst coat consisted of blister-resistant baking alkyd resin primer, the same as that on their Primewood siding introduced early in 1962.
The finish coat was a bakedon acylic resin described as “an
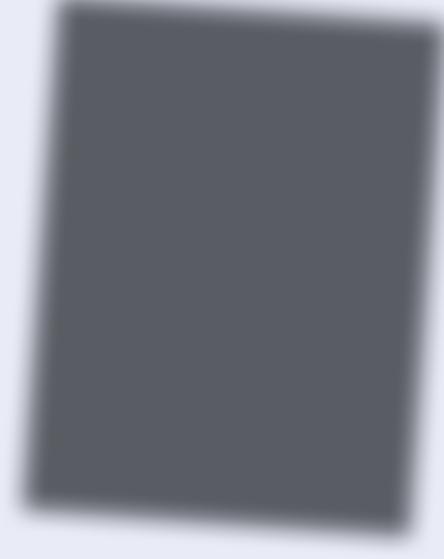

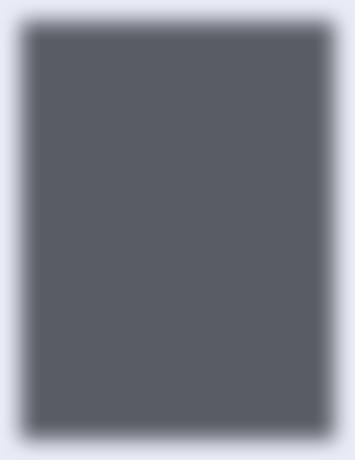
IN THE EARLY 1960s, aerospace industry aerospace industry supplier Rocket Chemical Co. expanded the marketing of their fl edgling rust-prevention/ degreaser WD-40 to sawmills, through ads in The California Lumber Merchant. THE OCTOBER 1963 issue of The California Lumber Merchant announced the debut of Durable Plywood Sales Co.’s extra-durable Ree-Sawn brand plywood siding. issue
exclusive Weyerhaeuser formula” four years in the making.
Along with the siding, Weyerhaeuser also introduced matching nails with baked-on enamel, plastic snap-on hammer caps to guard against marring paint, prefinished outside metal corners, touch-up paint, and matching PuttyStik pencils for coating cut ends.
The new prefinished siding was priced at about two-thirds more than unfinished vertical grain material. “This means,” Williston said, “that prefinished siding will cost about $100 to $200 more for the average house for material, but this is off set by the savings in painting costs. Most important, the factory prefi nish assures better appearance, longer service life of the paint surface, and less maintenance.”
In other news of October 1963: • Union Lumber Co., Fort Bragg, Ca., became the fi rst member mill of the California Redwood Association to introduce redwood glulam beams.
Branded as “Noyolam,” the beams were offered in sizes from 3x4 up to a “huge” 11x16, in lengths up to 40 ft. Each beam featured up to 20 laminates, each at least 1” in thickness. They also boasted top architectural grade redwood, a waterproof exterior adhesive, and dimensional stability aff orded by kiln drying.
Targeted applications included ridge and roof elements, carports, wide entryways, headers and posts.
“We think we’ve combined the flexibility features of glulams with the proven advantages of kiln dried redwood,” noted VP of sales Sherman Bishop. “And we’re anticipating a good future for the Noyolam in the building industry.”
• National Gypsum announced plans to build its first production facility on the West Coast—a $5-million gypsum wallboard plant in Richmond, Ca.
The facility opened the following summer and is still in operation.
• A record 10 billion bd. ft. of timber was cut from National Forests in fi scal year 1963, a 1 billion bd. ft. jump over the preceding year. The nation’s highest cut was on National Forests in Oregon (3.1 billion bd. ft. from 13 forests), followed by Washington (1.5 billion ft.) and California (1.4 billion ft.).
The harvest included over 1.3 billion bd. ft. of storm-damaged timber, primarily resulting from a devastating storm on Columbus Day 1962 that ravaged the Pacific Northwest.
“Prompt salvage of this valuable timber not only will prevent great monetary losses, but will help fire hazard and risk of further damage from insects and disease in the storm area,” said U.S. Secretary of Agriculture Orville L. Freeman.
For comparison, in fiscal year 2020 about 2.5 billion bd. ft. was harvested from National Forests.
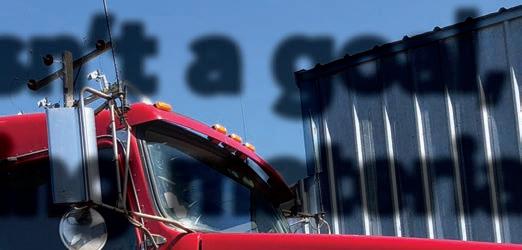
Quality isn’t a goal, it’s a building material.
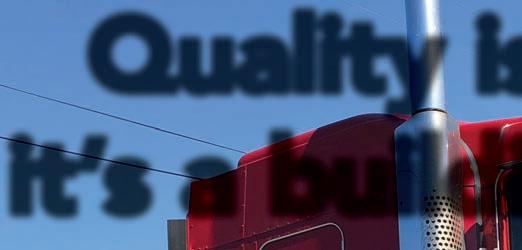
California Cascade Building Materials

California Cascade has been offering innovation and quality in the building products industry since 1974. Our extensive selection of products includes: pressure treated wood, redwood, cedar, fascia, and a variety of specialty branded products.
• Stocking Pressure Treated Lumber, Redwood, Cedar (incense and
Western red), Allura, Timbertech/Azek, TruPine, Gatorbar, Cascade
Ultra Lite Trim, Fascia • State of the art treating facilities in Woodland and Fontana, along with our newest plant in Junction City, Oregon • Rail spurs available at all locations • 18 company owned trucks • California Cascade Building Materials produces treated wood products using wood preservatives from Koppers Performance Chemicals.
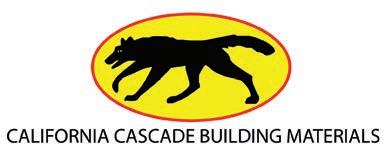

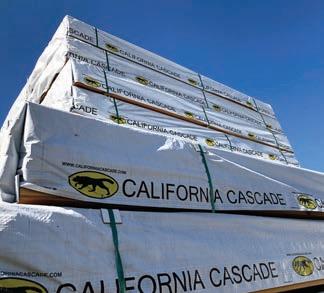
REDWOOD

Composite can’t compare.
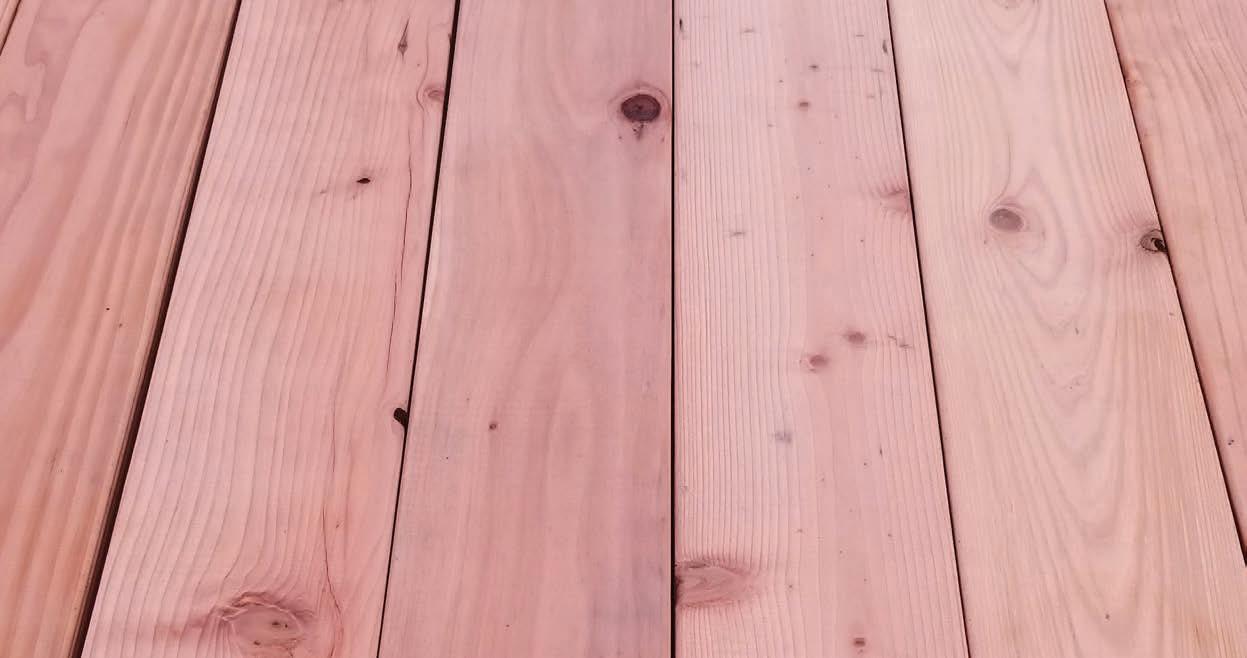
Like the foods we buy, when it comes to decking, we want natural and real. Redwood is always available in abundance of options. So stock the shelves! Unlike mass-produced and inferior products, Redwood is strong, reliable and possesses many qualities not found in artificial products. They maintain temperatures that are comfortable in all climates.
Redwood Empire stocks several grades and sizing options of Redwood.
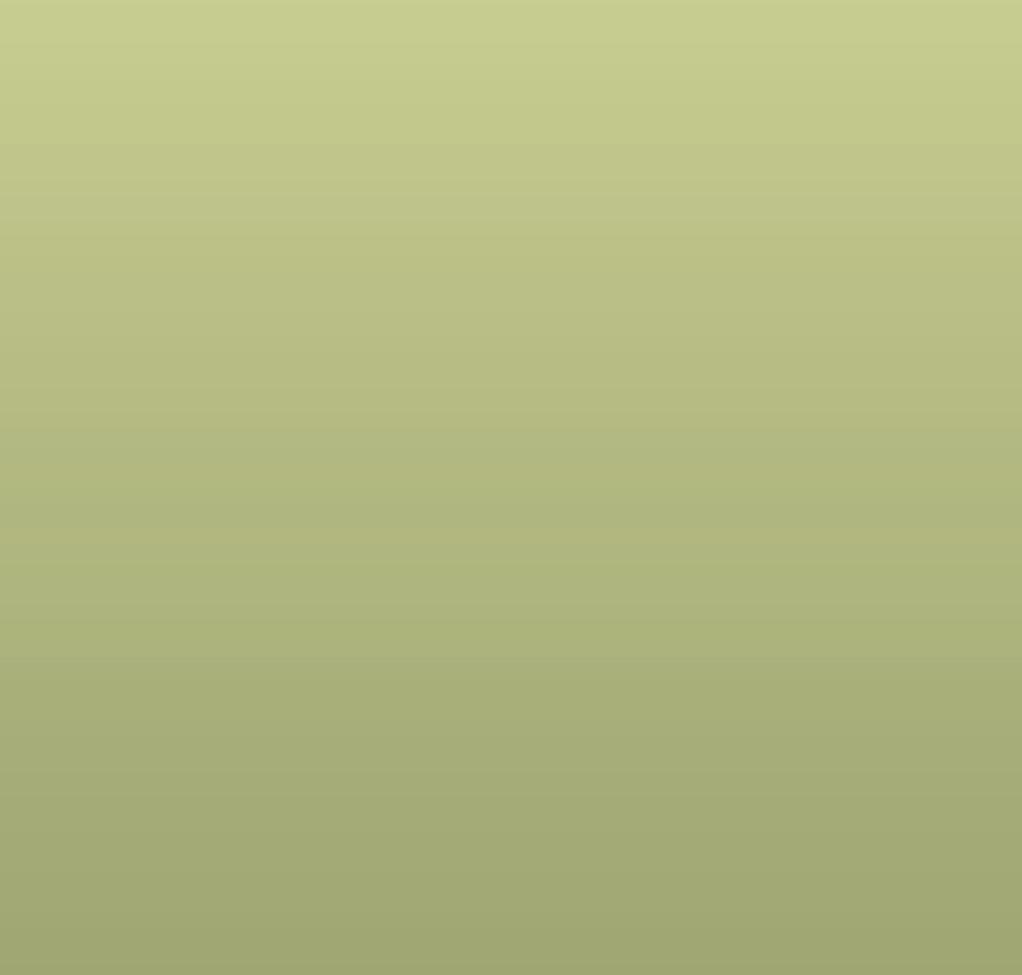