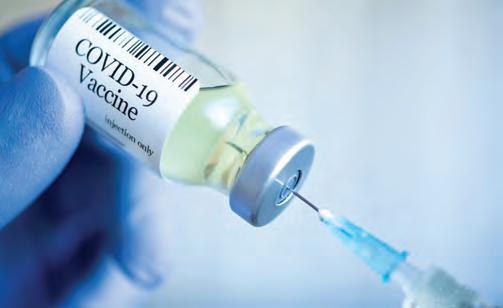
13 minute read
tranSForMIng teaMS
Vaccine accommodations
We know there is a lot of confusion around vaccine mandates and applicable accommodations. In order to provide more in-depth information for you to consider when planning the best course for your company, we wanted to share some of the resources we have found on these topics.
President Biden’s Vaccine Mandates
President Biden recently announced several initiatives to help the country recover from the ongoing pandemic. One of those initiatives, “Vaccinating the Unvaccinated,” will implement vaccine requirements which will cover 80 million employees. These new rules will extend vaccine mandates to all federal workers and federal contractors and subcontractors. In addition, employees of private employers with 100+ employees will either have to be vaccinated or be tested weekly. These employers will also need to provide paid time off for their employees to get vaccinated and to recover from any side effects of the vaccines.
OSHA is expected to issue an Emergency Temporary Standard (ETS) in 30 to 60 days with a short time frame before it becomes a requirement. After six months, OSHA is expected to replace the ETS with a permanent standard.
Accommodations
Conversations about vaccine mandates trigger questions about reasonable accommodations. While the EEOC has not said employers can require employees to be vaccinated, it clarified that there is no law preventing an employer from establishing the requirement. Employers must apply the same requirement to employees regardless of protected group (race, gender, religion, age) and must offer reasonable accommodation due to disability or religious belief.
Reasonable accommodation could include allowing the employee to work from home, requiring the employee wear a mask and socially distance from others, modifying the employee’s work shift or schedule to reduce personal interactions, mandating the employee to regularly present a negative COVID-19 test and/or creating a job reassignment.
While there are many possible accommodations, employers must only offer those that are reasonable, meaning they do not cause an undue hardship on the company. This means that what works for one company or employee may not be possible for another.
Employers must be consistent in their consideration of accommodations for all employees, but every employee’s case should be assessed individually using factors such as the reason for the need and the accommodations needed as well as their job duties and impacts of the accommodations on the company and other co-workers.
Employers should name one person to review and maintain any reasonable accommodation requests to maintain consistency. A good process for considering a reasonable accommodation includes: ● the employee making a request for accommodation; ● employer starting a dialogue to determine what accommodations are needed and what is reasonable; ● employee providing acceptable documentation of possible accommodations; ● employer considering each accommodation to determine what is reasonable; and ● employer offering reasonable accommodation, if any.
The employer should then have the employee sign a written acknowledgement of the details of accommodation including requirements, timing, an on-going review process, repercussions if the employee fails to maintain certain standards, and the right to rescind the accommodation if needed or the situation changes. Each arrangement should be reviewed regularly to ensure it is working for the employee and the company and, if not, adjusted accordingly. The whole process must be kept confidential with only the necessary people knowing of the details behind the need for the accommodation.
Medical: Under the Americans with Disability Act (ADA), people who have a disability which prevents them from receiving the vaccine should be offered reasonable accommodation. While most people with health issues are encouraged to get vaccinated, there are some medical conditions which may make it contraindicated such as being allergic to the components in the vaccine or having a neurological condition such as Guillain-Barre Syndrome. Anyone needing reasonable accommodation due to a disability should provide documentation from their personal health
care provider certifying that the employee cannot receive the vaccine due to medical reasons and outlining possible accommodations.
Religious: Under Title VII of the Civil Rights Act, employees cannot be required to get a vaccine if it violates their religious belief, practice, or observance or their sincerely-held belief. Employers do not need to accept general statements or form letters but should require documentation from the employee’s personal religious leader explaining the reason the vaccine violates the person’s beliefs.
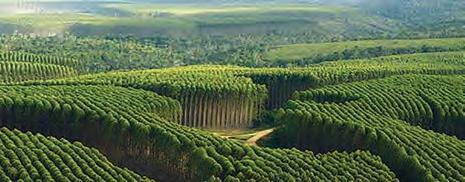
Q. We are thinking about hiring our first remote employee. Is there anything we need to do differently?
A. Yes, there are several employment aspects to consider when hiring an employee who will be working outside of the office. You should establish policies around remote work such as availability, use of equipment, confidentiality, and information security. If you will be issuing equipment such as laptops or cell phones, you should have employees sign an Equipment Issue & Return Form to track the issued equipment as well as to document any costs, rules of usage, and expectation of return. You also want to make sure you properly on-board the employee so they understand their job duties and are integrated into the team.
If the employee will be working in a different state, you will need to follow employment laws that may differ from those in your state. These may include mandated sick pay, leaves, paid jury duty, paying out accrued vacation upon termination, etc. You will also need to establish new hire reporting, Workers’ Comp, and unemployment accounts for that state as well as setting up proper tax withholdings.
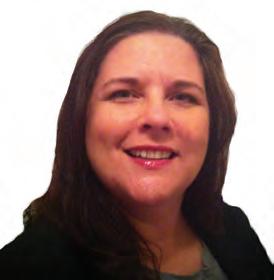
Many religious leaders have come out in support of COVID-19 vaccines in the name of public health and safety, which you can read in detail at US Embassy, ABC News and Newsweek. A common cited belief cites the usage of aborted fetal cells; however, as noted in these articles as well as at Science.org, the vaccines themselves do not contain fetal cells. These cells were used in research as they have been for numerous other vaccines and medical products such as ibuprofen, Tylenol and Pepto-Bismol. If an employee uses all of those products without hesitation then you may be able to challenge the request.
Employers have the right to challenge a request that is not supported by documentation from the employee’s health care provider or religious leader. Even if they disagree with the documented reason, both employer and employee should defer to parameters given by the provider or leader.
If employees have vaccine hesitancy, you can refer them to some unbiased resources, such as the CDC, UCLA and Nebraska Medicine.
If you have any questions or need guidance on vaccine mandates, accommodations, or anything COVID-19-related, please reach out to us at Affinity HR Group at (877) 660-6400 or contact@ AffinityHRGroup.com.
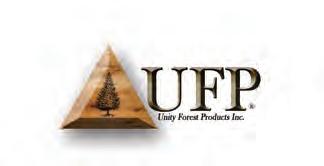
FSC Hardwood Decking RED GRANDIS
Red Grandis is a Plantation Grown FSC Hardwood Decking, cultivated in the North East region of Uruguay. Plantation Grown means 100% of the harvested area is reforested for future generations. Year-round harvesting ensures a continuous, uninterrupted supply.
Red Grandis is a low-maintenance decking that stands up to wear and tear in any climate. Take pride in the look and feel this exceptional decking delivers while knowing the oversight of FSC is protecting the environmental aspect. Rot- and insect-resistant Red Grandis delivers on Performance demands.
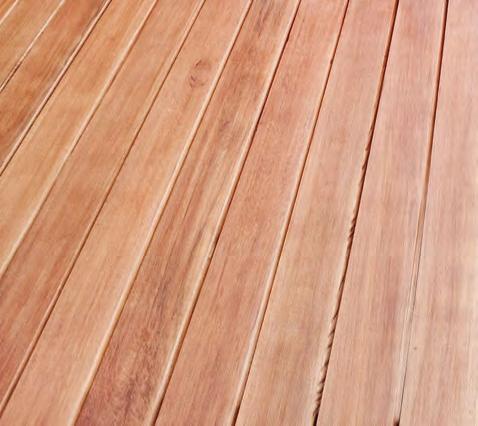
1 Specie + 1 Plantation + 1 Mill = Red Grandis Decking
For Distribution Information, Call 800-248-4940
Paige McAllister, SPHR Affinity HR Group contact@affinityhrgroup.com Unity Forest Products
Yuba City, CA.
Kodiak Acquires PNW Dealer
Kodiak Building Partners, Denver, Co., has acquired Carl’s Building Supply, Port Hadlock, Wa., effective Oct. 1.
Former owner Lawrence Johnson will continue to remain active with Carl’s following the transaction, and Tom Rider will remain president, responsible for the overall business, as well as the go-forward strategy. Carl’s will join the Retail Lumber and Gypsum group of Kodiak and will report to Pat Flood, executive VP.
Johnson and his wife, Lori, bought Carl’s in 1992 from his father (Carl), who had founded the business in 1947. From its 8-acre yard, Carl’s and its 44 employees supply framing materials, doors, windows, hardware, tools and roofing primarily to custom builders in western Washington.
Retailer Adds 2 More Aces
Brothers Nick and Kirby Kuklenski have increased their Ace Hardware franchise to eight locations with their acquisition of Kroegers Ace Hardware’s stores in Durango and Farmington, Co.
Earlier this year, the Durango store celebrated its 100th anniversary.
The new owners, who opened their first location 14 years ago in Colorado Springs, Co., have big expansion plans for the Kroeger locations, including hiring more employees and adding new products.
Cameron Ashley Opens Denver Distribution Center
Cameron Ashley Building Products has opened a new distribution center in Aurora, Co., to serve the Denver market and complement its existing DC in Pueblo, Co.
“We are thrilled to enter the Denver market and build our coverage throughout the state of Colorado and beyond,” said district manager Gary Cannaday. “Our new customers can expect fantastic service, customer-focused delivery options, and a great local team.”
Managed by Chase White, the Denver facility features fully enclosed storage and will stock roofing and accessories, gypsum wallboard, cement backer board, joint compound, wall system accessories, and a full line of fiberglass and spray foam insulation products.
Based in Greenville, S.C., Cameron Ashley distributes roofing, insulation, gypsum, siding and other specialty building products from a network of over 45 distribution centers throughout the U.S.

www.superiorwoodtreating.com
Machinery, Tool Giants Merge
USNR and Wood Fiber Group are merging to create the world’s most comprehensive supplier of equipment, technology and tooling for wood processing facilities.
Woodland, Wa.-based USNR is a global supplier of sawmill and plywood mill machinery, aftermarket parts, and technical and engineering services.
Wood Fiber Group, Fitchburg, Ma., is the largest supplier of cutting tools and filing room equipment, with such brands as Simonds International, Burton Saw & Supply, BGR Saws, Global Tooling, and U.S. Blades.
LSI Re-brands as Arxada
Specialty chemicals company LSI has rebranded as Arxada, effective Oct. 21. The new name follows the firm’s recent launch as an independent business, after the completion of Lonza Group’s sale of Lonza Specialty Ingredients.
The re-brand reflects the company’s passion for delivering high performance and realizing potential, both for its customers and within its own operations.
The name Arxada derives from arx and arcis, Latin for citadel and fortress. Just as a citadel protects, Arxada’s solutions strengthen the performance of its customers and their products, and protect people, places and the planet.
NEWS Briefs
Ace Hardware is taking over a former Dollar General storefront in Hesperia, Ca.
Ganahl Lumber now stocks
NewTechWood All-Weather and European Sidings at several of its Southern California locations.
Meyer Hardware, Golden, Co., has closed its doors after 76 years.
Estacada True Value ,
Estacada, Or., will transition to Ace Hardware affiliation by March.
Roseburg, Roseburg, Or., completed the purchase of 30,000 acres of Southern timberland from Forest Investment Associates, Atlanta.
Huttig Building Products,
St. Louis, Mo., has retained Lincoln International as financial advisor to assist with “a process to evaluate potential strategic alternatives to maximize shareholder value.”
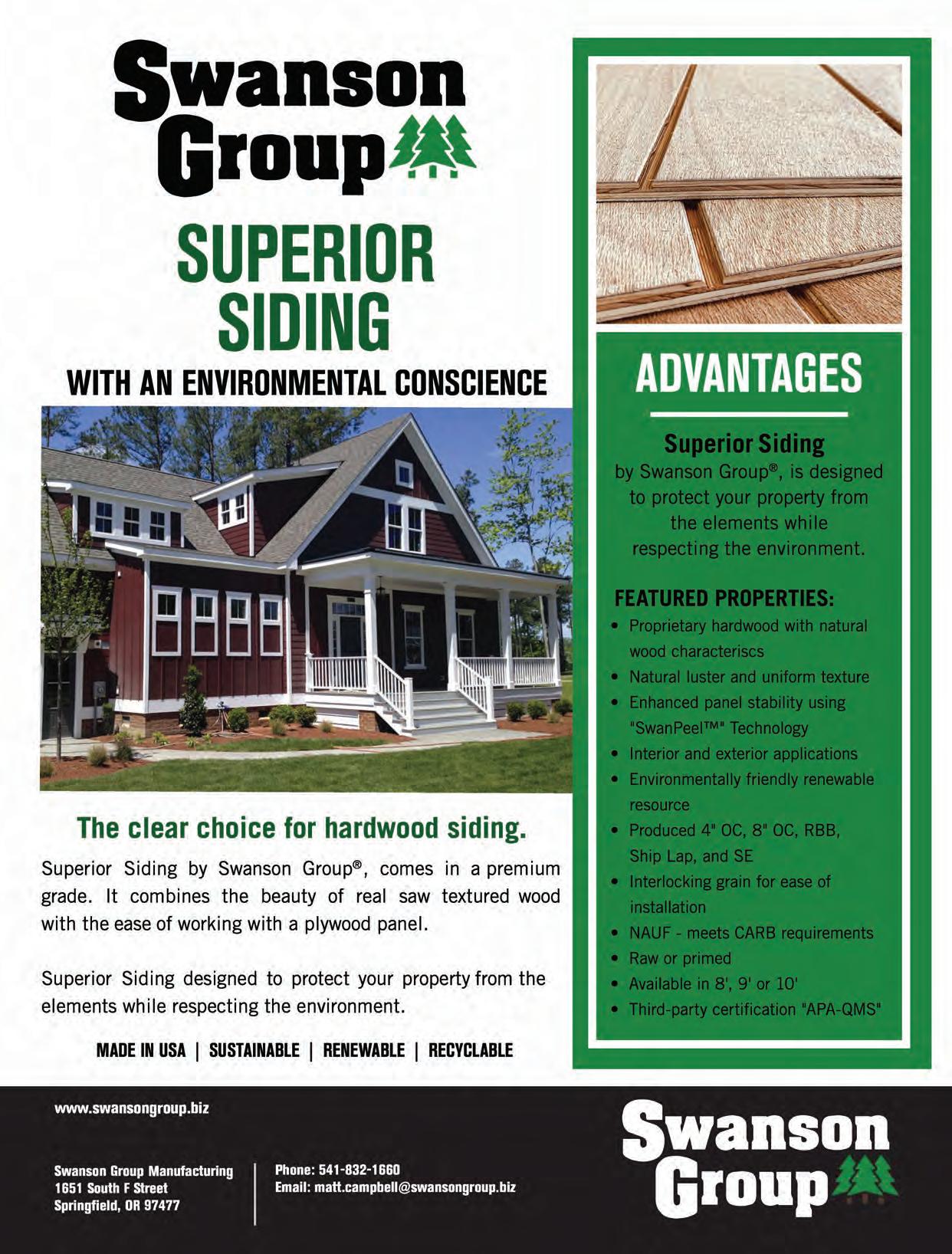
Barrette Snaps Up Another Railing Manufacturer
One week after purchasing Missouribased railing producer Madden Manu- facturing, Barrette Outdoor Living acquired vinyl railing/fence maker National Vinyl Products, Nephi, Ut., from the Hadfield family.
As part of the new partnership, the facilities and teams at both NVP and Barrette Outdoor Living will continue to function independently while combining the manufacturing strengths and strategic plant locations of both partners. NVP will continue to service its existing customer base while also increasing its product offering.
“Joining the Barrette Outdoor Living family gives us the ability to elevate our product offerings to our customers and continue to support their growth,” said Zack Clark, general manager of NVP.
PWL Updating Veneer Plant
Pacific Wood Laminates is undertaking a top-to-bottom renovation of its veneer production facility in Brookings, Or., to increase capacity.
Working around a fixed steam capacity, USNR’s solution involves a highly complex, complete dryer replacement along with major system upgrades to existing equipment that will raise production levels across the board.
PWL currently has three dryers in this facility; one dryer will be replaced and another modified to more efficiently utilize available steam. The modifications will allow the plant to gain more valuable production capacity and realign the product mix to suit evolving markets.
The new USNR Longitudinal Dryer system includes a veneer feeder and dryer infeed, right angle unloading system, grade line, and stacker system. The new grade line will utilize a Ventek GSc2000 grade scanner, Sequoia Sentry veneer moisture meter, complete controls system, and a 10-bin stacker to handle half and full sheets of veneer products.
An existing dryer is receiving Automatic Dryer Efficiency Control in addition to Automatic Cooler Pressure Balance systems. These upgrades combined create a dramatically more efficient steam drying system to maintain balanced steam usage across the entire facility. Modifications to an existing Coe dryer stacker will allow it to stack random-width veneer as well as full sheets, offering the ability to run a more varied product mix through each dryer.
SPI Finalizes Seneca Purchase
Sierra Pacific Industries, Anderson, Ca., has completed its acquisition of Seneca, Eugene, Or.
The union positions SPI as a West Coast forest products leader with more than 2.3 million acres of sustainably managed timberlands, 18 sawmills and eight renewable biomass energy cogeneration facilities, along with millwork and windows operations.
“This is a meaningful day for Sierra Pacific Industries, as well as for Seneca,” said SPI president George Emmerson. “The combined company brings together an outstanding team of people that will leverage our shared expertise in sustainable forest management and innovation in manufacturing, working together to provide quality lumber and wood products to the marketplace.”
Koppers Sells Denver Facility
Koppers Inc. has sold its 60-acre crosstie treating facility in Denver, Co., to real estate redeveloper Hines.
Early this year, Koppers completed cleaning, decommissioning and demolition of its wood-treating operations at the site, after transitioning crosstie treatment activities to another production facility.
Ace Garners Big Turnout
More than 10,000 attended Ace Hardware’s recent fall convention in Orlando, Fl.
Ace occupied more than 800,000 sq. ft. indoors, with an additional 150,000 sq. ft. outdoors for grilling and outdoor power equipment. The outdoor space— featuring outdoor power and BBQ demos as well as the latest grilling innovations from the top grill brands —was twice the size of Ace’s last inperson show held in Atlanta in 2019.
In all, there were over 3,300 Ace stores in attendance from all 50 states and over 1,200 vendor exhibits making this year’s event one of the most successful in recent years, with attendance exceeding Ace’s last in person convention in Atlanta in 2019.
Additional show highlights included more than 15,000 new items added to the RSC network, countless impactful programs unveiled, 8,000 vendor deals, nearly 50 live and virtual training sessions, more than 200 Ace Handyman Services franchisees attending for the first time, and—despite torrential rains—more than 5,500 attendees participated in the private Ace night at Universal Studios.
PROUDLY SERVING THE FOREST PRODUCTS INDUSTRY SINCE 1896
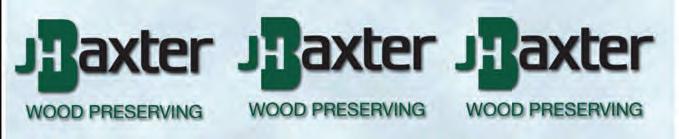
CONVENIENTLY LOCATED IN THE HEART OF THE PACIFIC NORTHWEST “TREATING COASTAL DOUGLAS FIR IS OUR SPECIALTY”
TSO MARKETS & APPLICATIONS SERVED RAILROAD TIE MARKET • HIGHWAYS & BRIDGES • MARINE/AQUATIC AGRICULTURE • MILLWORK • EXPORT • SAWN LUMBER & TIMBERS ROUND TIMBER PILING (MARINE, FRESH WATER & FOUNDATION) GLUE-LAMINATED BEAMS, COLUMNS & ARCHES
THE INDUSTRIAL TSO SPECIALIST CHEMONITE® ACZA PENTACHLOROPHENOL TYPE A 50-50 CREOSOTE PETROLEUM CLEAN CREOSOTE (P1/13)
CUSTOM TREATING RAIL TIE PREPLATING HEAT STERILIZE/KILN DRYING (KD & KDAT) 5 RETORTS: FROM 50’ TO 156’ RAIL SERVICE (UP & BNSF)
www.JHBaxter.com
Paul Krotts • pkrotts@jhbaxter.com 3494 ROOSEVELT BLVD., EUGENE, OREGON 1-866-960-9703 Customer Service & Order Status: 1-541-689-3801 x2 or CustomerService@JHBaxter.com
JHBaxter & Co. is WBE Certified
