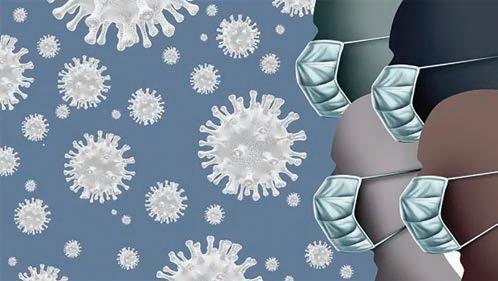
13 minute read
THINKING AHEAD
By Harris Gant & Michael Calloway
Processing the pandemic
Nindustry saw CO I -1 coming; but when it did show up, ECM , Inc. was ready.
As a process-driven company, the culture of our business from inception has been to have procedures in place guiding everything we do, in every imaginable situation. We figure out the best way to do things and then we have everybody do it that exact best way every time.
Taking on the pandemic was no exception. aving a system, and having trust in that system, allowed us to pivot swiftly and seamlessly—or relatively so. Early recognition of the enormity of the crisis prompted immediate action. A deep-seated commitment to take care of our employees formed and guided the processes we implemented, and transparent channels of communication kept everybody on the same page company-wide.
Once it became clear that the public health threat was here for the long haul, the company knew it needed to get out in front of the problem rather than wait for the inevitable to happen. In the earliest meetings, it was warned repeatedly that it was not a matter of if, but when, ECM , Inc. would have an issue related to the crisis.
To head off trouble, the first move was to leverage established processes. Although developed with tornadoes, wildfires, and similar events in mind, our isaster Recovery Center became a central component of the early pandemic response. By March, we had sent about half of our customer service representatives to that alternative worksite, located in our manufacturing plant across town. Equipped with a duplicate server that mirrors the server in our corporate o ce in Wilkesboro, N.C., that facility allowed our CSRs to plug in and keep working without disruption while also providing a simple social-distancing solution.
To thin the ranks even more, many others quickly transitioned to remote work from home. It was already SOP for each employee to have a company-issued laptop and to take that device home every night, so that made the changeover a lot smoother than what some other businesses experienced.
Existing processes would only carry us so far, though. uring a presidential briefing on the virus, it really dawned on us that this thing is real and we need to get ready. We knew we needed a CO I -specific plan. With that in mind, we assembled a crisis management team, made up of all the operating company and division presidents. The team met daily to report such information as what was happening in the different operating companies and whether there were any potential cases of infection.
At the same time, we set about putting together response protocols for cases where an employee exhibits symptoms at work or called in after exhibiting symptoms at home. Following C C guidelines, detailed processes, procedures, and scenarios were defined. The management team and supervisors within our 1 locations were provided training, coaching, and talking points to prepare their teams and keep everyone informed. We also had tabletop drills so that we knew exactly what we were going to do when we had our first positive case.
That wouldn’t happen until uly. As it turned out, one of our customers had a positive case first—and it unfortunately ended with a fatality. When the customer was sidelined for a week because its people were afraid to go to work, we at ECM , Inc. realized that job one for us was going to be to protect our employees and make them feel safe to work. That was the guiding principle of all our CO I -1 policies and procedures.
About NAWLA
North American Wholesale Lumber Association is the association that delivers unparalleled access to relationships and resources that improve business strategy and performance through sales growth, cost savings, and operational efficiencies for wholesalers and manufacturers of forest products and other building materials that conduct business in North America. Learn more about how NAWLA can help your business at nawla.org.
A Special Series from North American Wholesale Lumber Association
Inspirational Vet to Keynote NAWLA Virtual Summit
North American Wholesale Lumber Association has enlisted inspirational military veteran John Kriesel to keynote its 2021 Leadership Summit: The Virtual Experience on March 16.
In “Still Standing. Still Smiling,” Kriesel will share how the power of an amazing support system, positive attitude, and sense of humor can save your life, literally. After being pronounced dead by doctors three times after an explosion attack while serving the military in Iraq, he found that the accident and then transition to civilian life gave him a new perspective on life. Attendees can learn how to bounce back stronger than ever, no matter your lifechanging situation.
The Leadership Summit will present more than five hours of thought-provoking and motivational education sessions, and leave you with actionable ideas and business strategies to boost your business in 2021.
Other highlights will include icebreaker networking sessions, roundtable discussions, and Women of Lumber panel.
Find more info at www.nawla.org.
Employee Care
We were designated as an essential business and, therefore, not told to shut down, but we still had a duty to protect our employees. That’s really the key: keeping employees safe and making them feel comfortable, not only with the process but with the work environment. aily wipe-downs of contact surfaces began as early as February, followed by symptom and temperature checks. Our process dictated that if someone was symptomatic or if there was a chance that they might be carrying the virus, we would get them out of the building, quarantine them for a period of time, and test them.
The company also embraced transparent communication, providing regular updates to employees as well as trainings, posters, and the like. We did a lot to communicate to staff and, as a result, they were confident we knew what was going on and had their best interests at heart.
Challenges
While our process-centric nature helped soften the blow of the pandemic to some extent, that doesn’t mean we were without hurdles—including some adjustments in how we did business. ECM , Inc. is highly reliant on technology, as distribution centers and sales teams conduct business in real time, with very little paper flow, but this is also a very people-oriented industry where territory reps and sales associates traditionally gravitate toward face-to-face interaction. Forced to telecommute and fall back on telephone contact, we found ourselves having to teach many employees the art of oom and Go-To Meetings. Most didn’t even know what that was, so we started from the ground up on those kinds of platforms. Not surprisingly, company laptops also lacked the camera feature. That was another thing that we did have to go out and invest in, but it was a relatively quick and easy fix.
It took a little longer to get up to speed on our CO I specific SOPs. Based on C C guidelines, for instance, early on we were shutting facilities down, deep cleaning, and restarting operations the next day when positive cases surfaced at a location. After doing so three times in a single week, it became clear that this approach wasn’t sustainable.
It also sunk in that the time frame between when somebody got tested for CO I and when they received their results took as long as 1 days. With an employee out of the facility for seven to 1 days after testing positive, however, there really was no need for a shutdown and deep cleaning. Instead—sparing no expense—we contracted with a testing lab so that we could get results back in as soon as three days and targeted cleaning to areas the infected employee occupied. We were able to remain in operation in the meantime, but only after navigating the learning curve.
The Takeaway
Our takeaway from this pandemic experience is to trust in the process. Because it does work. id we have a couple of challenges we had to navigate? Sure. But if you’ve got the right people in place and the right processes in place, all it takes is a tweak here and there. ECM , Inc. took this approach, and we didn’t miss a beat.
– Harris Gant (below right) is product manager, and Michael Calloway (below left) is safety, health & environmental manager for ECMD, Inc., North Wilkesboro, N.C. (www.ecmd. com). Divisions include EastCoast Mouldings, Klumb Forest Products, Crown Heritage Stairs, ECMD Distribution, and Arndt & Herman Building Products.
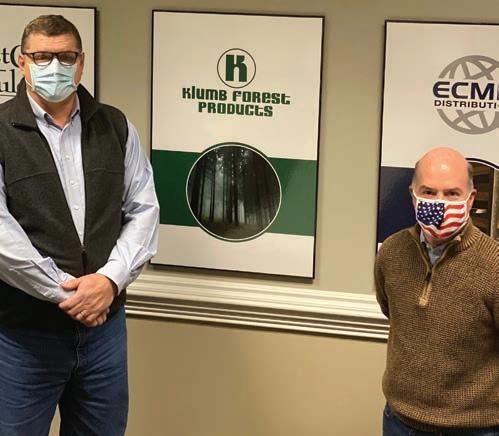
Josh Hamilton has been promoted to president elect for International
Wood Products LLC, Clackamas,
Or., transitioning to succeed David
Stelle as IWP president over the next one to two years. Following the transition, Stelle will continue as a member of the board and management team. Blair Buchanan has retired as executive P of Mendocino
Companies, Santa Rosa, Ca., after 0 years in the industry. e continues as a senior advisor.
Laurie Creech has been promoted to executive vice president of supply chain. Nick Stokes, executive P of Boise
Cascade’s Building Materials istribution division, Boise, Id., is retiring next month after years with the company. e will be succeeded by Jeff Strom. Karsten Vardas, ex-Louisiana-Pacific, is now the senior EWP outside salesperson for Boise Cascade,
Lathrop, Ca., covering Northern
California and Western Nevada. Michele Matson, ex-Friedman’s ome Improvement, is new to outside sales of windows doors at
Golden State Lumber, Sonoma, Ca. Mike Olosky has joined Simpson
Manufacturing Co., Pleasanton, Ca., as chief operating o cer. Randy Vernetti is the new western regional mgr. for Chamelon
Power, Novi, Mi., software and visualization tool developer for the building industry. John Edwards, panel trader, Buckeye
Pacific, Tualatin, Or., was named winner of the company’s 0 0 Terry
Simpson Award. Shara Gamble was promoted to P of sales marketing for Envision
Building Products, Lamar, Mo. Kristie McCurdy, ex-Woodgrain
Millwork, has joined RoyOMartin,
Alexandria, La., as a senior sales rep. Bobby Byrd, director of OSB sales, was re-elected to a two-year term on the board of directors of the
Reflective Insulation Manufacturers
Association International. John Somerville, president and CEO,
LMC, is retiring in une after 0 years in the industry. Victoria Nye is the new designer at
Bloedorn Lumber, Torrington, Wy. Joe Weston has been promoted to P of cost forecasting pricing and
Rich Scalise to P of inventory management at Lumber Co. Ben Skoog, ex-Articell, has joined o it Best Corp., as director of brand integration. Michelle Baker was promoted to sales support coordinator. New to IB are Autumn
McDermott, as a stock representative; Brian Schneider, sales support coordinator; and Chris
Snyder, associate merchandise mgr. Ernie Couillard was promoted to president of Regal ideas Inc., elta, B.C. Quinton Weber is now director of sales U.S.; Clifton
Phelps, director of sales Canada; and Jim Topliss, director of commercial development U.S. Kris Tellball is now handling forecasting for Mungus-Fungus Forest
Products, report co-owners Hugh
Mungus and Freddy Fungus.

LUNAWOOD.com
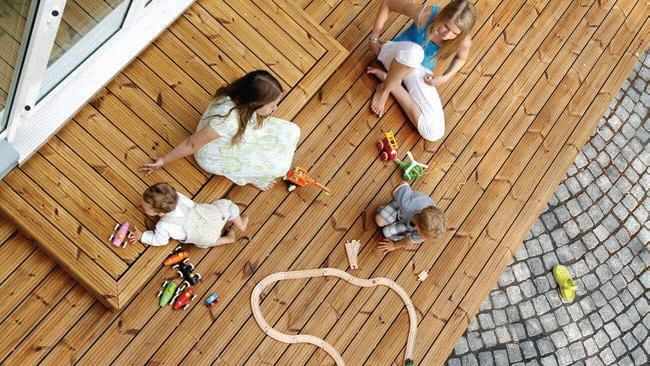
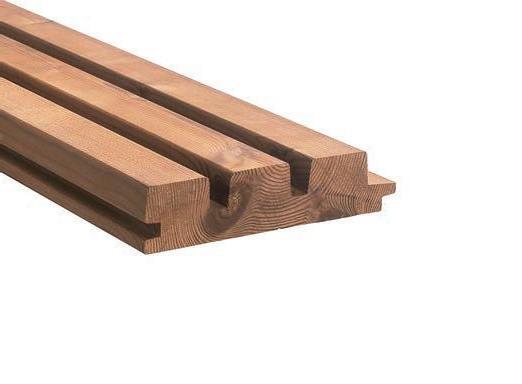


ARCATA redwood lath producer Joe Lindgren has sold his three-decadeold business to his Tribe.
Tribe Purchases Redwood Mill
The urok Tribe has purchased redwood lath manufacturer Lindgren Lumber Co., Arcata, Ca., from its owner, oe Lindgren.
Lindgren, an elder with the Tribe, retired last year after running his mill for years, but will stay on to volunteer as an unpaid advisor “to ensure that the mill continues to perform at full capacity during and after the transition.
“The Lindgren Lumber Co. has a longstanding reputation as a premier producer of finest quality redwood products,” said oseph L. ames, chairman of the urok Tribe. “We added this business to our economic development portfolio because it is a successful enterprise with an exemplary environmental track record. We will not be altering the operation of the company. owever, we have a plan to capitalize on existing business relationships to bring the well-established brand into new markets.”
Established in 1 , the Lindgren Lumber employs more than 0 workers, many of whom have been with the company for multiple decades.
Milling Complex Coming to Arizona
Good Earth Power A through its operating entity, NewLife Forest Products, has acquired a ,000-sq. ft. industrial manufacturing facility in Bellemont, Az., which they are converting into a -ace sawmill.
Employing about 00 at full capacity, the mill is targeting a March start-up. It will produce 1 0 million bd. ft. of lumber annually, plus engineered wood products. It will substantially increase the regional log processing capacity needed to restore the health of . million acres of wildfire-susceptible forest land in collaboration with the U.S. Forest Service under the Four Forest Restoration Initiative.
The facility will house a sawmill, planer mill, dry kilns and EWP lines, plus room for warehousing and staging high-value products. A rail spur will be added.
Good Earth Power A and NewLife Forest Products are backed by private equity firm Lateral Investment Management, San Mateo, Ca.
Home Depot Expanding in Pasadena
ome epot has begun hiring for a new home center now under construction in Pasadena, Ca.
Anticipated to open this spring, the new store will sit on a 1 -acre site that ome epot has been negotiating to build on since 01 .


MOSO® Bamboo X-treme®
Manufactured with precision. Made of over 90% natural, fast-growing bamboo.
WUIAPPROVED
ClassAFireRated
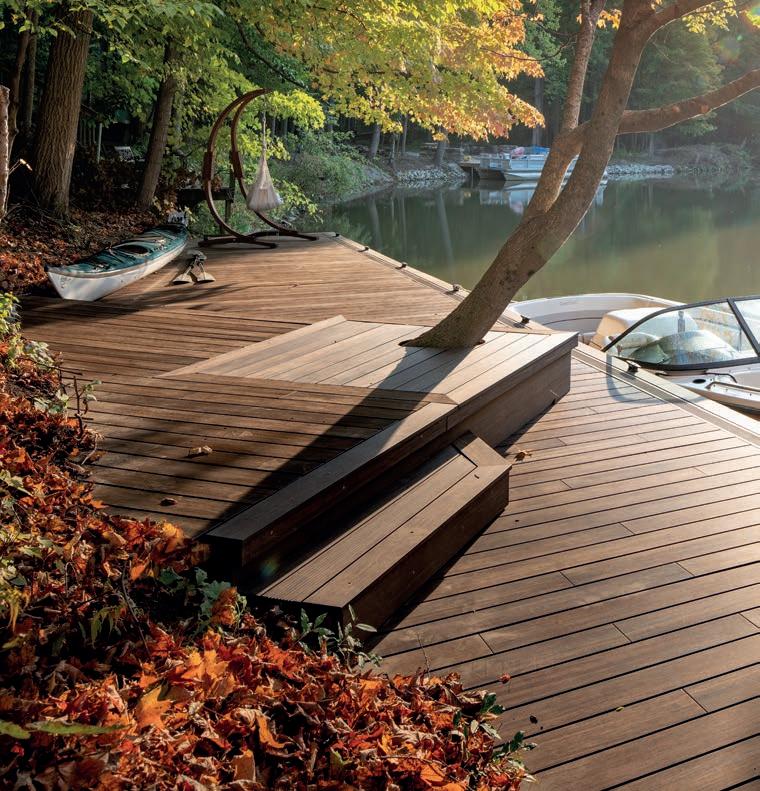
moso-bamboo.com/x-treme
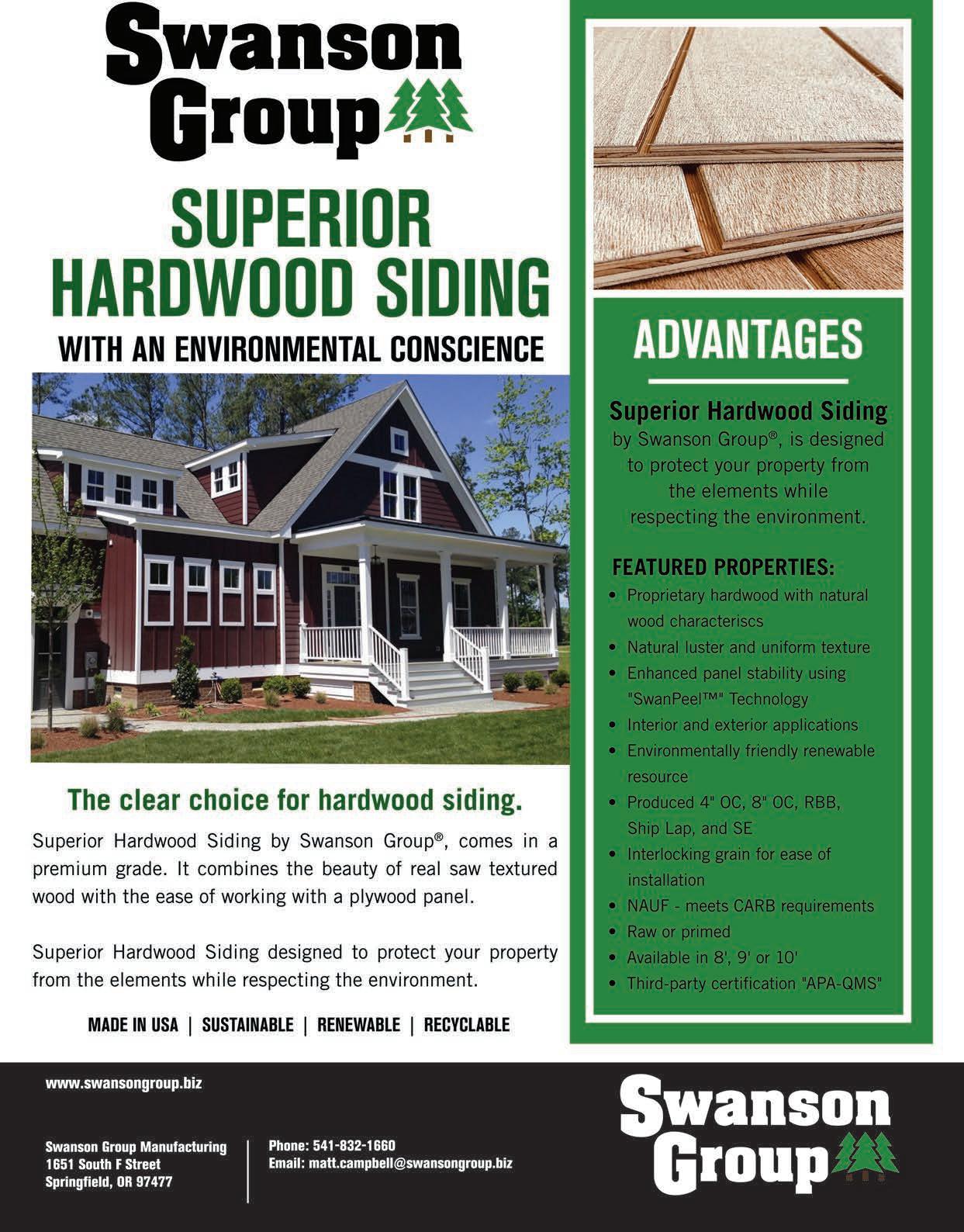
Envision Building Products, Lamar, Mo., has purchased Fairway Architectural Railing Solutions, seeing Fairway’s railing repertoire as a perfect complement to its composite decking.
“We believe this is the right partnership to meet the evolving needs of our customers while furthering our ability to create best-in-class outdoor products and achieve our vision in becoming the undisputed market share leader of non-wood railing in the U.S. market,” said Fairway CEO Greg Burkholder.
Fairway’s existing management team will remain in place and its current product lines will continue to be offered under the Fairway brand, with Fairway also having the ability to provide its customers access to Envision composite decking. Envision will likewise be able to offer its customers access to the suite of Fairway railing products.
“This acquisition expands Envision’s footprint in the outdoor living category and will not only increase market reach but will also provide operational efficiencies,” said Shara Gamble, P of Envision sales marketing. “The individual strengths of each company are complementary and will have a positive impact on our combined service and product offerings.”
The acquisition provides railing solutions in vinyl, aluminum, steel, composite, and cellular P C.


Trex Caps $200M Expansion
Trex is entering 0 1 celebrating an historic milestone: the start-up of its new irginia production facility to culminate a 00-million expansion program.
Trex also improved production capabilities and capacity at its manufacturing site in Fernley, Nv., where new lines were installed and made operational in une. Combined, the expansions will increase production capacity by approximately 0% while adding 0 new jobs.
“For every company there are moments that are history making, and this is definitely one of those for Trex,” said CEO Bryan Fairbanks. “Thanks to the foresight and confidence of the Trex team and our board of directors to invest in this capacity expansion, we are embarking upon the next era of growth for our company.”
In 01 , Trex announced plans to invest 00 million in the infrastructure, people and processes to up capacity in both of its plants. At the center of the plan is 00,000 sq. ft. of newly constructed manufacturing and support facilities dedicated to producing Trex decking. The state-ofthe-art manufacturing plant, adjacent to the company’s existing Winchester, a., campus, features approximately , 00 cubic yards of concrete in its foundation, ,000 sq. ft. of exterior precast, 1, 00 tons of structural steel, and million linear ft. of wiring.
“This will be the most productive and e cient composite decking facility designed for maximum output,” noted Adam ambanini, president of Trex Residential Products. “The building is equipped with state-of-the-art, proprietary extrusion technology that allows us to manufacture Trex decking using % recycled content, with an emphasis on quality and energye cient systems.”