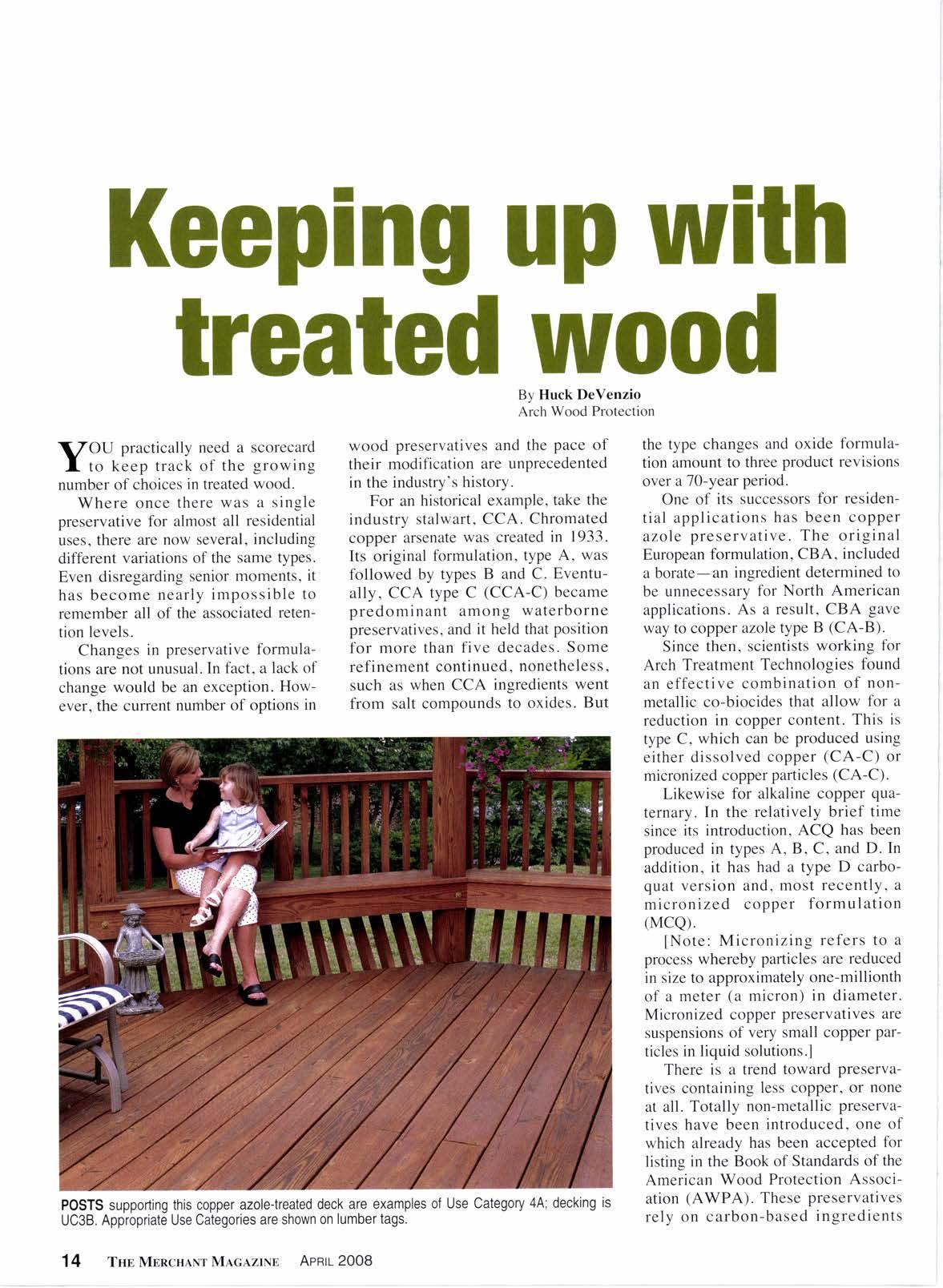
3 minute read
Keeping up with treated wood
By Huck DeVenzio Arch Wood Protection
\ZOU practically need a scorecard I to keep track of the growing number of choices in treated wood.
Where once there was a single preservative for almost all residential uses, there are now several, including different variations of the same types. Even disregarding senior moments. it has become nearly impossible to remember all of the associated retention levels.
Changes in preservative formulations are not unusual. In fact, a lack of change would be an exception. However, the current number of options in wood preservatives and the pace of their modification are unprecedented in the industry's history.
For an historical example, take the industry stalwart, CCA. Chromated copper arsenate was created in 1933. Its original formulation, type A, was followed by types B and C. Eventually, CCA type C (CCA-C) became predominant among waterborne preservatives, and it held that position for more than five decades. Some refinement continued, nonetheless, such as when CCA ingredients went from salt compounds to oxides. But the type changes and oxide formulation amount to three product revisions over a 7O-year period.
One of its successors for residential applications has been copper azole preservative. The original European formulation, CBA, included a borate-an ingredient determined to be unnecessary for North American applications. As a result, CBA gave way to copper azoletype B (CA-B).
Since then, scientists working for Arch Treatment Technologies found an effective combination of nonmetallic co-biocides that allow for a reduction in copper content. This is type C, which can be produced using either dissolved copper (CA-C) or micronized copper particles (CA-C).
Likewise for alkaline copper quaternary. In the relatively brief time since its introduction, ACQ has been produced in types A, B, C, and D. In addition, it has had a type D carboquat version and, most recently, a micronized copper formulation (MCQ).
INote: Micronizing refers to a process whereby particles are reduced in size to approximately one-millionth of a meter (a micron) in diameter. Micronized copper preservatives are suspensions of very small copper particles in liquid solutions.l
There is a trend toward preservatives containing less copper, or none at all. Totally non-metallic preservatives have been introduced, one of which already has been accepted for listing in the Book of Standards of the American Wood Protection Association (AWPA). These preservatives rely on carbon-based ingredients rather than copper or other metals. The elimination of copper results in several desirable characteristics, although current formulations are suitable only for wood that is used out of the ground.
It is very unlikely that preservative evolution will end soon or that retention levels will become the same for all treatments. There could be future types of existing chemicals and, certainly, there will be new chemicals. The treated wood market will continue to push for preservatives with features that users want. and manufacturers can be expected to develop formulations which address those desires.
Hemembering Retention Levels
Retention level is the amount of preservative retained in a given assay zone following treatment. This level is measured in pounds of preservative per cubic foot of wood, or pcf. Different applications pose different hazards from wood-destroying organisms, so wood needs diJferent levels of protection.
When CCA was the sole preservative for most uses, remembering its minimum retention levels was relatively easy-0.25 pcf for above ground, 0.40 pcf for ground contact, and something more for critical structural members and saltwater immersion.
Those days are gone. Nearly each of the new preservatives has unique retention requi-rements. This makes sense since the chemicals are not alike, but it can be trying for specifiers who are accustomed to referring to retention numbers.
Simplifying the growing number of retention numbers is the Use Category system, now being used by the American Wood Protection Association and gaining acceptance by code and construction professionals.
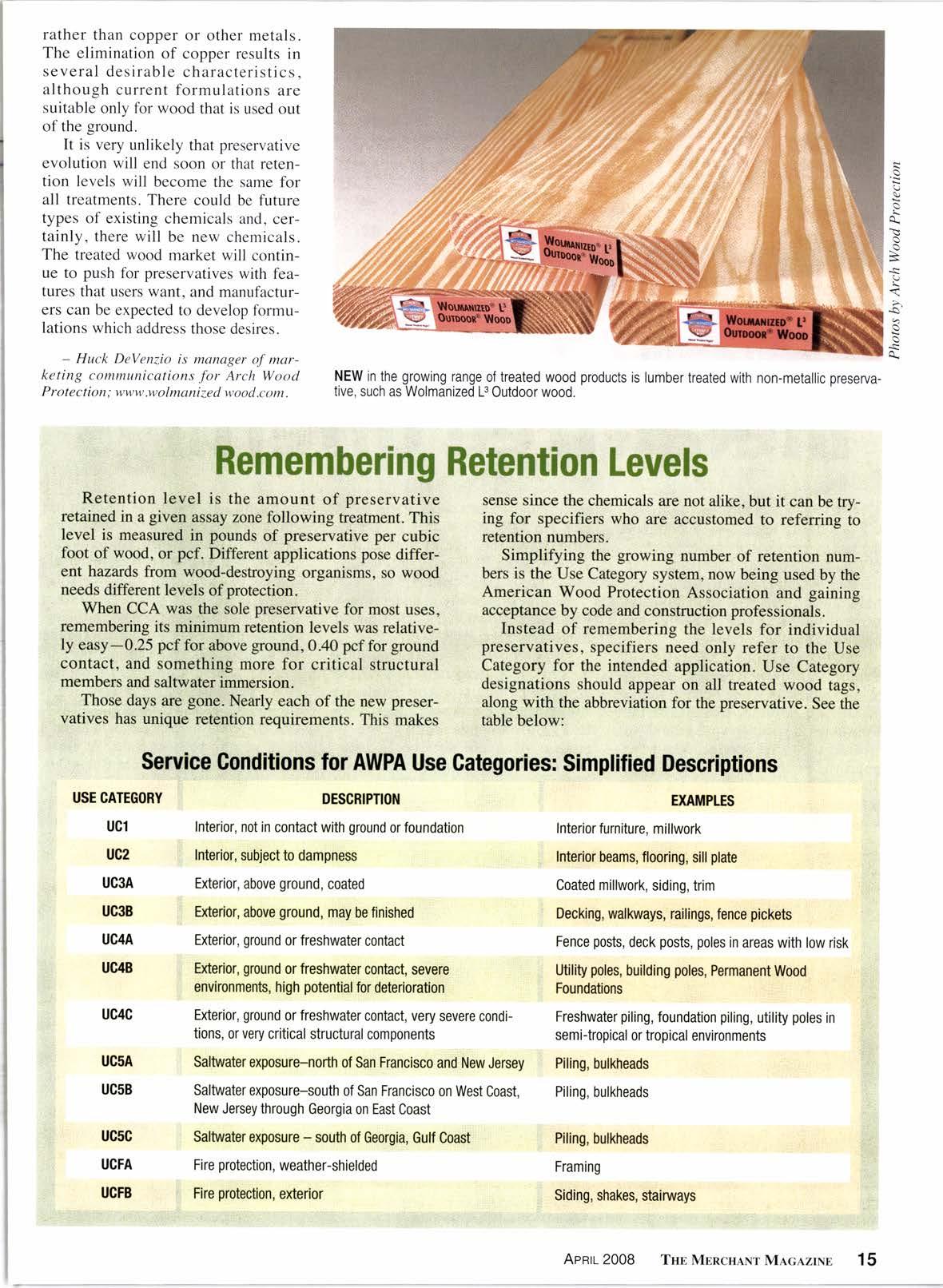
Instead of remembering the levels for individual preservatives, specifiers need only refer to the Use Category for the intended application. Use Category designations should appear on all treated wood tags, along with the abbreviation for the preservative. See the table below:
Service Sonditions for AWEA use Gategories: Simplified Descriptions
DESCRIPTION
Interior, not in contact with ground or foundation
Interior, subject to dampness
Exterior, above ground, coated
Exterior, above ground, may be finished
Exterior, ground or freshwater contact
Exterior, ground or freshwater contact, severe environments, high potential for deterioration
Exterior, ground or freshwater contact, very severe conditions, or very critical structural components
Saltwater exposure-north of San Francisco and New Jersey
Saltwater exposure-south of San Francisco on West Coast, New Jersey through Georgia on East Coast
Saltwater exposure - south of Georgia, Gulf Coast
Fire protection, weather-shielded
Fire protection, exterior
EXAMPLES
Interior furniture, millwork
Interior beams, flooring, sill plate
Coated millwork, siding, trim
Decking, walkways, railings, fence pickets
Fence posts, deck posts, poles in areas with low risk
Utility poles, building poles, Permanent Wood
Foundations
Freshwater piling, foundation piling, utility poles in semi{ropical or tropical environments
Piling, bulkheads
Piling, bulkheads
Piling, bulkheads
Framing
Siding, shakes, stainrays