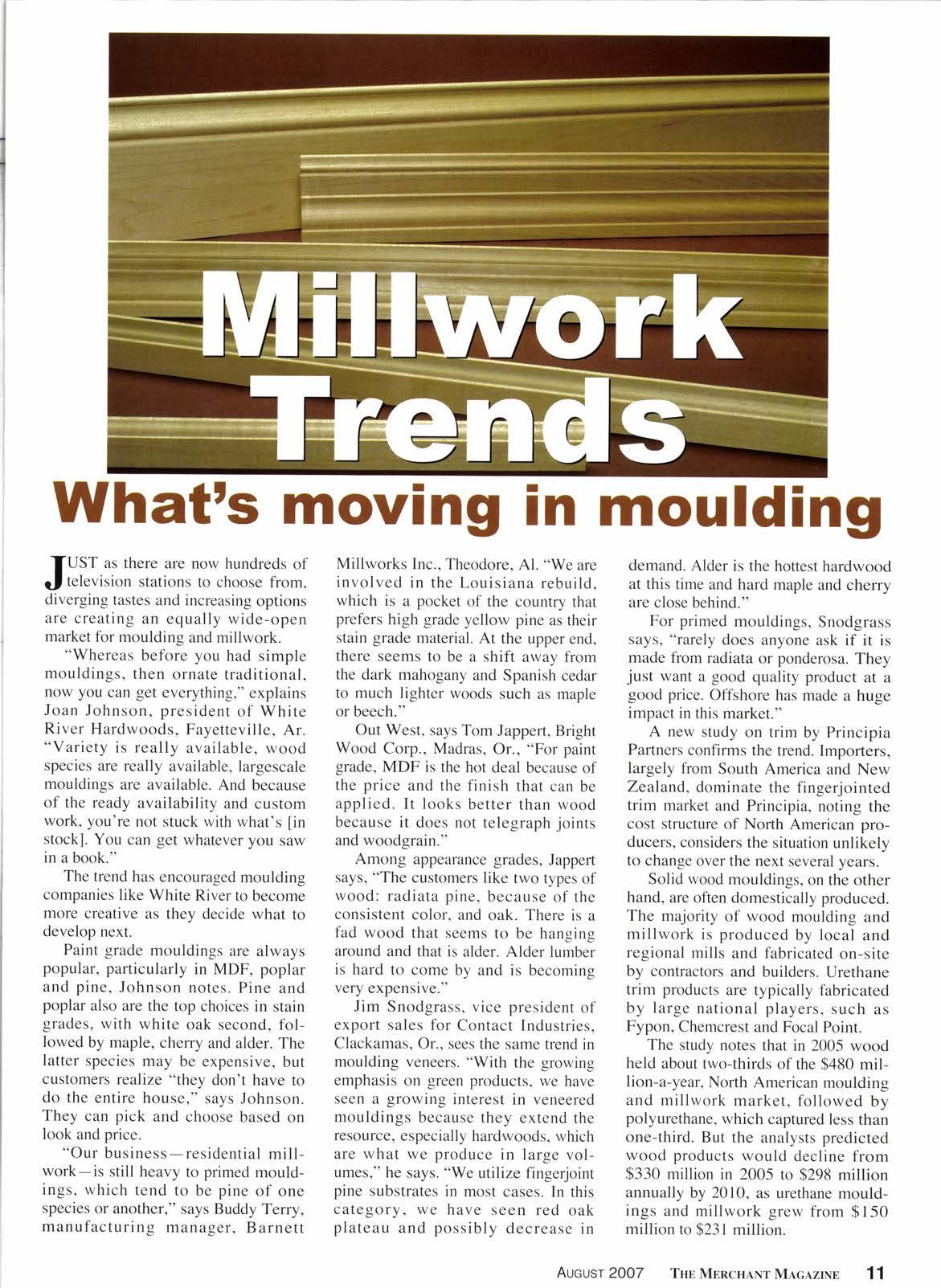
5 minute read
Whatts moving in moulding
fUST as there are now hundreds of j television stations to choose from. diverging tastes and increasing options are creating an equally wide-open market for moulding and millwork.
"Whereas before you had simple mouldings, then ornate traditional, now you can get everything," explains Joan Johnson, president of White River Hardwoods, Fayetteville, Ar. "Variety is really available, wood species are really available, largescale mouldings are available. And because of the ready availability and custom work, you're not stuck with what's [in stock]. You can get whatever you saw in a book."
The trend has encouraged moulding companies like White River to become more creative as they decide what to develop next.
Paint grade mouldings are always popular, particularly in MDF, poplar and pine, Johnson notes. Pine and poplar also are the top choices in stain grades, with white oak second, followed by maple, cherry and alder. The latter species may be expensive, but customers realize "they don't have to do the entire house," says Johnson. They can pick and choose based on look and price.
"Our businessresidential millwork-is still heavy to primed mouldings, which tend to be pine of one species or another," says Buddy Terry, manufacturing manager, Barnett
Millworks Inc., Theodore, Al. "We are involved in the Louisiana rebuild, which is a pocket of the country that prefers high grade yellow pine as their stain grade material. At the upper end, there seems to be a shift away from the dark mahogany and Spanish cedar to much lighter woods such as maple or beech."
Out West. says Tom Jappen, Bright Wood Corp., Madras, Or., "For paint grade, MDF is the hot deal because of the price and the finish that can be applied. It looks better than wood because it does not telegraph joints and woodgrain."
Among appearance grades, Jappert says, "The customers like two types of wood: radiata pine, because of the consistent color. and oak. There is a fad wood that seems to be hanging around and that is alder. Alder lumber is hard to come by and is becoming very expensive."
Jim Snodgrass, vice president of export sales for Contact Industries, Clackamas. Or.. sees the same trend in moulding veneers. "With the growing emphasis on green products, we have seen a growing interest in veneered mouldings because they extend the resource, especially hardwoods, which are what we produce in large volumes," he says. "We utilize fingerjoint pine substrates in most cases. In this category, we have seen red oak plateau and possibly decrease in demand. Alder is the hottest hardwood at this time and hard maple and cherry are close behind."
For primed mouldings, Snodgrass says, "rarely does anyone ask if it is made from radiata or ponderosa. They just want a good quality product at a good price. Offshore has made a huge impact in this market."
A new study on trim by Principia Partners confirms the trend. Importers, largely from South America and New Zealand, dominate the fingerjointed trim market and Principia, noting the cost structure of North American producers, considers the situation unlikely to change over the next several years.
Solid wood mouldings, on the other hand, are often domestically produced. The majority of wood moulding and millwork is produced by local and regional mills and fabricated on-site by contractors and builders. Urethane trim products are typically fabricated by large national players, such as Fypon, Chemcrest and Focal Point.
The study notes that in 2005 wood held about rwo-thirds of rhe $480 million-a-year, North American moulding and millwork market, followed by polyurethane, which captured less than one-third. But the analysts predicted wood products would decline from $330 million in 2005 to $298 million annually by 2010, as urethane mouldings and millwork grew from $ 150 million to $231 million.
IIAMLEY & Co., the oldest llleather saddle manufacturer in the U.S., purchased more than 15,000 bd. ft. of gorgeous red oak millwork to breathe new life into a business that has operated for more than 100 years in the same building in Pendleton, Or.
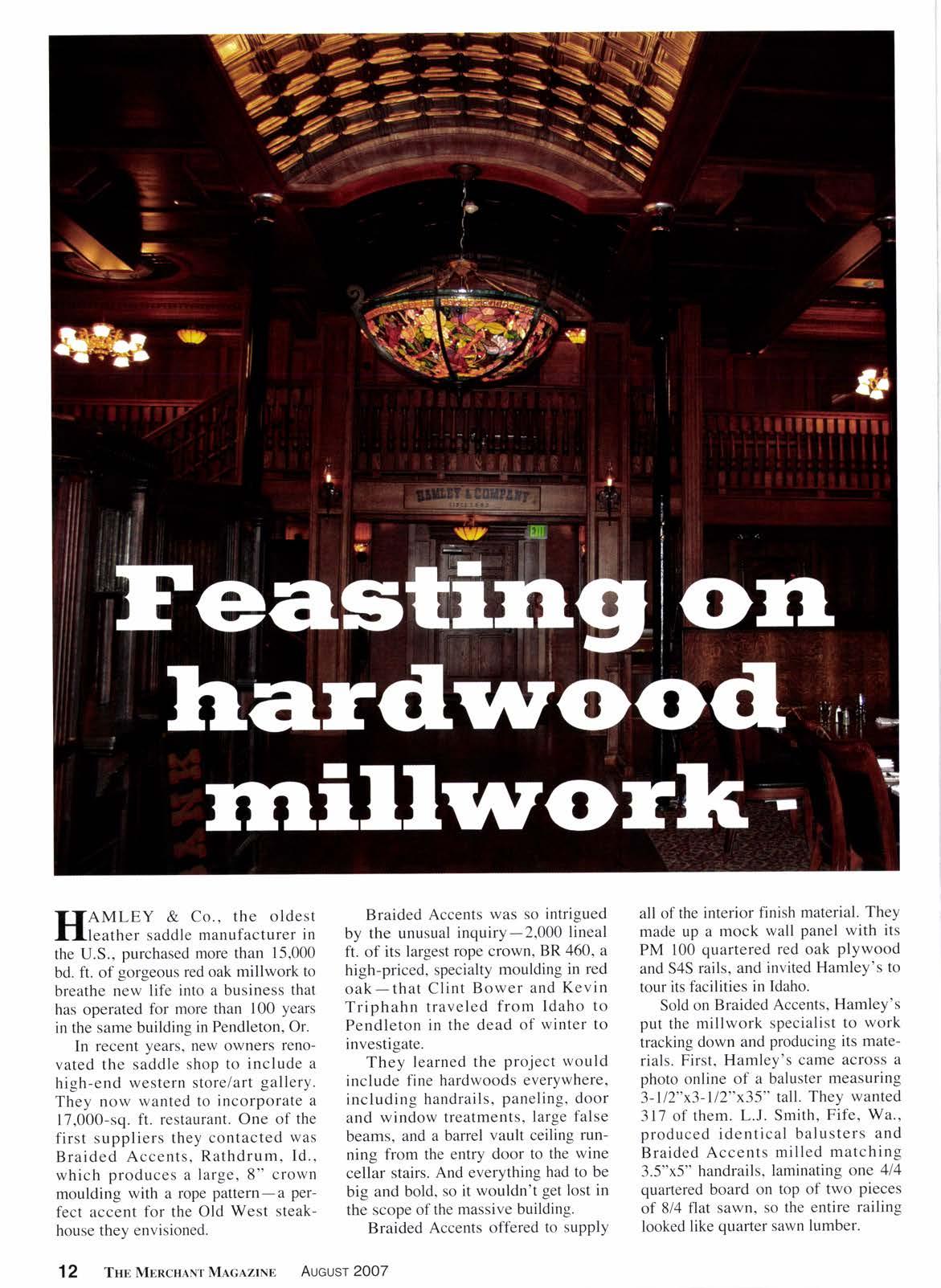
In recent years, new owners renovated the saddle shop to include a high-end western store/art gallery. They now wanted to incorporate a 17,000-sq. ft. restaurant. One of the first suppliers they contacted was Braided Accents, Rathdrum, Id., which produces a large, 8" crown moulding with a rope pattern-a perfect accent for the Old West steakhouse they envisioned.
Braided Accents was so intrigued by the unusual inquiry-2,000 lineal ft. of its largest rope crown, BR 460, a high-priced, specialty moulding in red oak-that Clint Bower and Kevin Triphahn traveled from Idaho to Pendleton in the dead of winter to investigate.
They learned the project would include fine hardwoods everywhere, including handrails, paneling, door and window treatments, large false beams, and a barrel vault ceiling running from the entry door to the wine cellar stairs. And everything had to be big and bold, so it wouldn't get lost in the scope of the massive building.
Braided Accents offered to supply all of the interior finish material. They made up a mock wall panel with its PM 100 quartered red oak plywood and S4S rails, and invited Hamley's to tour its facilities in ldaho.
Sold on Braided Accents, Hamley's put the millwork specialist to work tracking down and producing its materials. First, Hamley's came across a photo online of a baluster measuring 3-l 12"x3-l 12"x35" tall. They wanted 317 of them. L.J. Smith, Fife, Wa., produced identical balusters and Braided Accents milled matching 3.5"x5" handrails, laminating one 414 quartered board on top of two pieces of 8/4 flat sawn, so the entire railing looked like quarter sawn lumber.
The quartered oak was supplied by McDermott, Oh.-based Taylor Lumber, which operates a yard in Portland, Or. The initial order, which included 4/4, 514,414-lO" and wider, and 51410" and wider, filled an entire semi.
In the meantime, Hamley's designs changed from Old West to a more refined turn-of-the-century San Francisco theme. Rope mouldings were out. Dentil mouldings were in. Hamley's, however, found all of the mill's sample profiles too small. So Braided Accents developed alarge 2" dentil profile that maximized the capabilities of its machine. They then designed a five-piece crown build-up to cover up to 15". Working with the lead trim carpenter. the mill also craft- ed a frieze block, inside corner, large dentil. S4S. and SC-725.
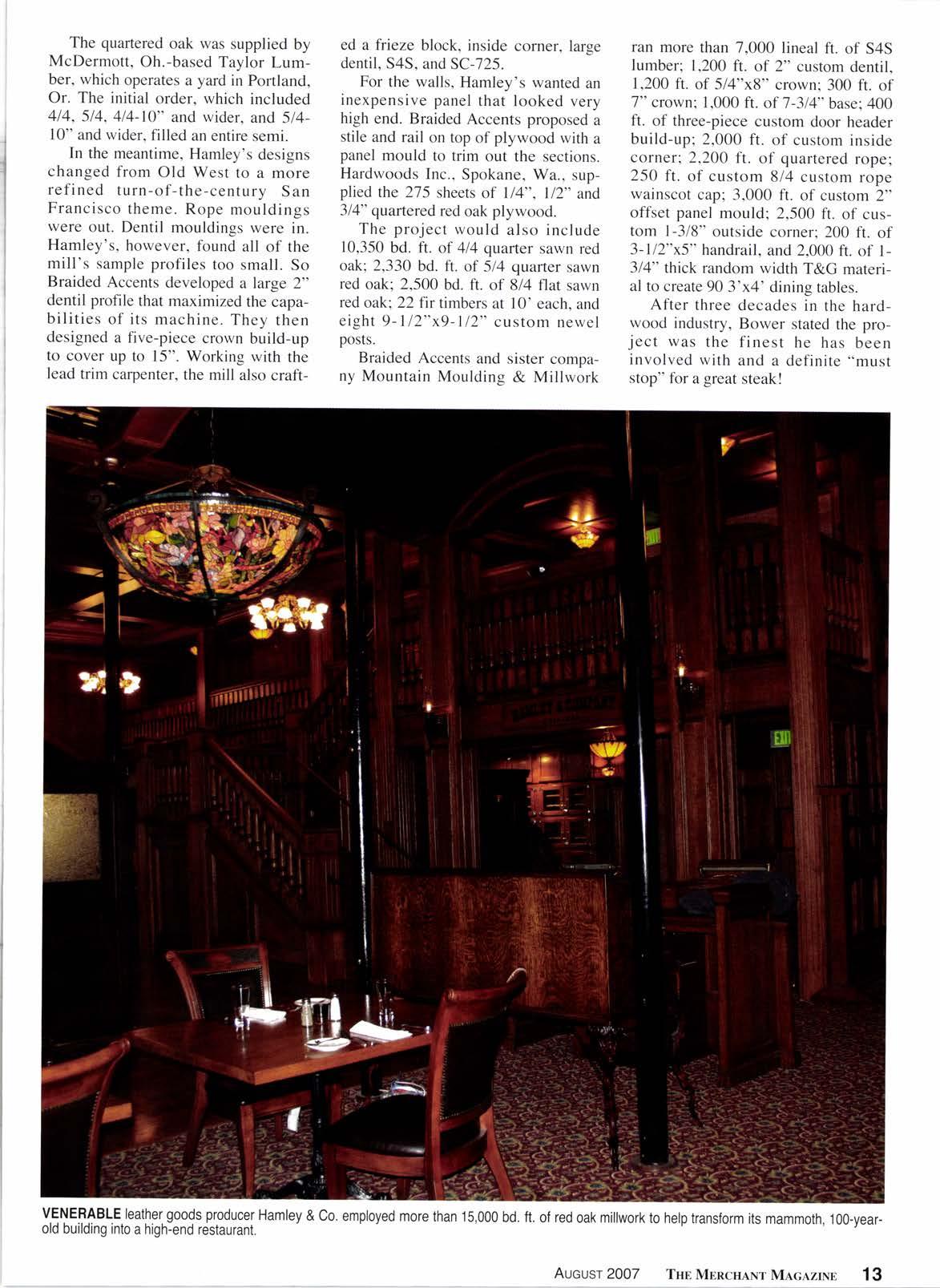
For the walls, Hamley's wanted an inexpensive panel that looked very high end. Braided Accents proposed a stile and rail on top of plywood with a panel mould to trim out the sections. Hardwoods Inc., Spokane, Wa., supplied the 275 sheets of 114", 112" and 314" qtartered red oak plywood.
The project would also include 10,350 bd. ft. of 414 quarter sawn red oak; 2,330 bd. ft. of 5/4 quarrer sawn red oak; 2.500 bd. ft. of 8/4 flar sawn red oak; 22 fir timbers at l0' each, and eight 9-112"x9- l/2" custom newel posts.
Braided Accents and sister company Mountain Moulding & Millwork ran more than 7,000 lineal ft. of S4S lumber; 1,200 ft. of 2" custom dentil, 1,200 ft. of 514"x8" crown; 300 ft. of 7" crown; 1,000 ft. of 7-314" base; 400 ft. of three-piece custom door header build-up; 2,000 ft. of custom inside corner; 2,200 ft. of quartered rope; 250 ft. of custom 8/4 custom rope wainscot cap; 3,000 ft. of custom 2" offset panel mould; 2,500 ft. of custom 1-3l8" outside corner: 200 ft. of 3-ll2"x5" handrail, and 2,000 ft. of l314" thick random width T&G marerial to create 90 3'x4' dining tables.
After three decades in the hardwood industry, Bower stated the pro- ject was the finest he has been involved with and a definite "must stop" for a great steakl