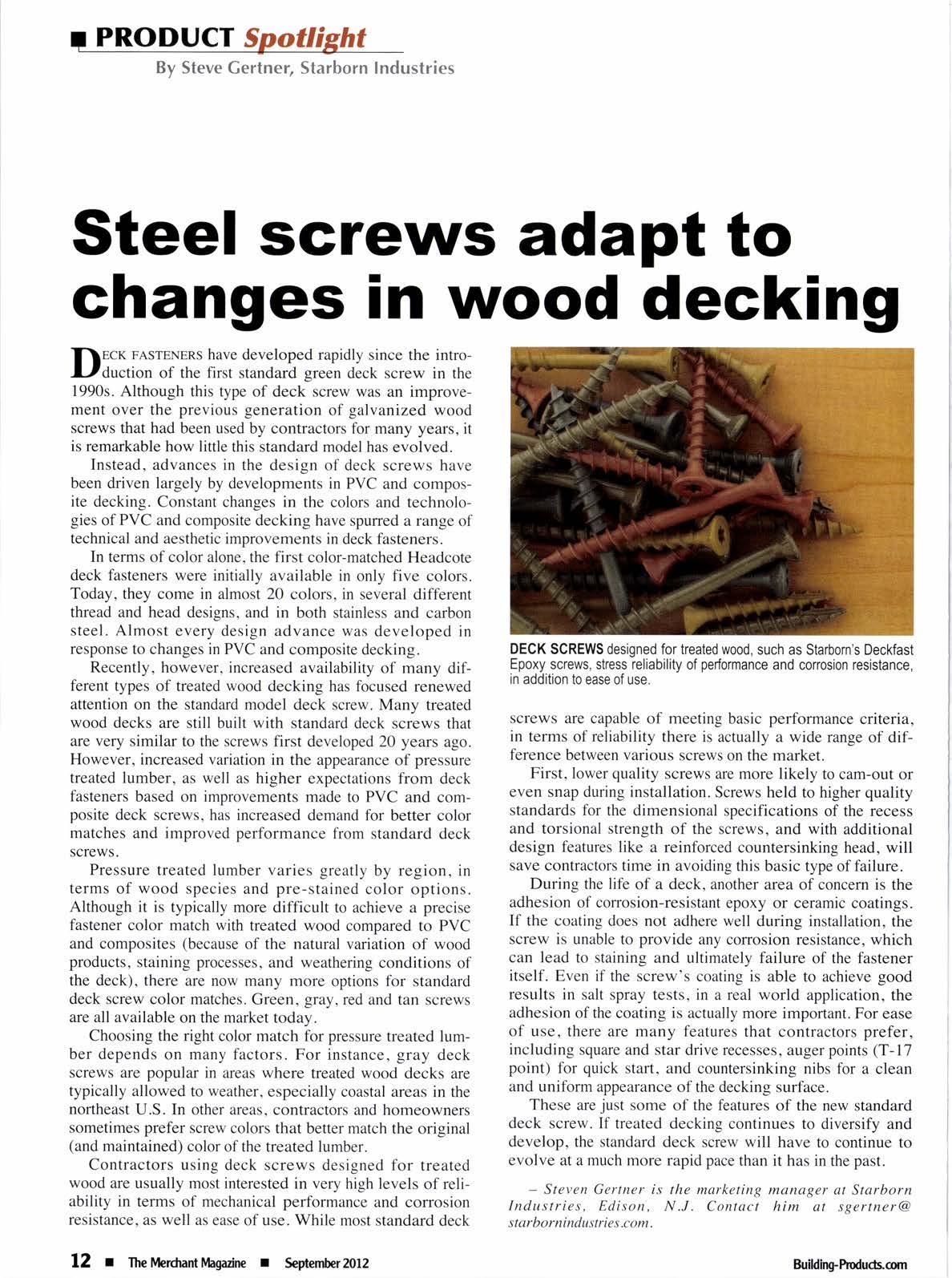
7 minute read
Steel screws adapt to changes in wood decking
f\ecx FASTENERS have developed rapidly since the introI:Tduction of the first standard green deck screw in the 1990s. Although this type of deck screw was an improvement over the previous generation of galvanized wood screws that had been used by contractors for many years, it is remarkable how little this standard model has evolved.
Instead, advances in the design of deck screws have been driven largely by developments in PVC and composite decking. Constant changes in the colors and technologies of PVC and composite decking have spurred a range of technical and aesthetic improvements in deck fasteners.
In terms of color alone, the first color-matched Headcote deck fasteners were initially available in only five colors. Today, they come in almost 20 colors, in several different thread and head designs, and in both stainless and carbon steel. Almost every design advance was developed in response to changes in PVC and composite decking.
Recently, however, increased availability of many different types of treated wood decking has focused renewed attention on the standard model deck screw. Many treated wood decks are still built with standard deck screws that are very similar to the screws first developed 20 years ago. However, increased variation in the appearance of pressure treated lumber, as well as higher expectations from deck fasteners based on improvements made to PVC and composite deck screws, has increased demand for better color matches and improved performance from standard deck screws.
Pressure treated lumber varies greatly by region, in terms of wood species and pre-stained color options. Although it is typically more difficult to achieve a precise fastener color match with treated wood compared to PVC and composites (because of the natural variation of wood products, staining processes, and weathering conditions of the deck), there are now many more options for standard deck screw color matches. Green, gray, red and tan screws are all available on the market today.
Choosing the right color match for pressure treated lumber depends on many factors. For instance, gray deck screws are popular in areas where treated wood decks are typically allowed to weather, especially coastal areas in the northeast U.S. In other areas, contractors and homeowners sometimes prefer screw colors that better match the original (and maintained) color of the treated lumber.
Contractors using deck screws designed for treated wood are usually most interested in very high levels of reliability in terms of mechanical performance and corrosion resistance, as well as ease of use. While most standard deck screws are capable of meeting basic performance criteria, in terms of reliability there is actually a wide range of difference between various screws on the market. f, s r<.ur \IATERI.\L pRO\ II)IRS for the building flindustrv- C)SB manufacturers have seen thc effccts of the country's cconomic conditions firsthand. Fortunately, thc first half of 20 l2 has carriccl with it slow but persistent growth in the denrand tbr OSB. thanks in part to the low invcntory of new and existing homes. Although anticipated housing stalts for the year are well below pre-recession avcra-ges. they are much nore positive than the nunrbers frorn just a few ycars ago. Forecasters are calling fbr more -growth by 2013.
DECK SCREWS designed for treated wood, such as Starborn's Deckfast Epoxy screws, stress reliability of performance and conosion resistance, in addition to ease of use.
First, lower quality screws are more likely to cam-out or even snap during installation. Screws held to higher quality standards for the dimensional specifications of the recess and torsional strength of the screws, and with additional design features like a reinforced countersinking head, will save contractors time in avoiding this basic type of failure.
During the life of a deck, another area of concern is the adhesion of corrosion-resistant epoxy or ceramic coatings. If the coating does not adhere well during installation, the screw is unable to provide any corrosion resistance, which can lead to staining and ultimately failure of the fastener itself. Even if the screw's coating is able to achieve good results in salt spray tests, in a real world application, the adhesion of the coating is actually more important. For ease of use, there are many features that contractors prefer, including square and star drive recesses, auger points (T-17 point) for quick start, and countersinking nibs for a clean and uniform appearance ofthe decking surface.
These are just some of the features of the new standard deck screw. If treated decking continues to diversify and develop, the standard deck screw will have to continue to evolve at a much more rapid pace than it has in the past.
As the building industry slowly enterges from the bottom of this downturn, there is some light at the end of thc tunnel. Although a revived housing market may present a new set of challenges, the opportunities for innoviition and product developrnent seen along the way are already creating a stronger, more diversified industry.
Opportunities for lnnovation
Engineered "vood products, including OSB, bring flexibility to product development and innovation. With an intentional design and purposcful variation in properties. OSB products can be developed to proviclc solutions for specific construction challenges.
As the pioneer in OSB, LP Building Products is among the producers committed to ongoing innovation in the design and application of OSB products. This mcans listcning to builders, architects and enginccrs and working with these groups to create custom product solutions that meet their needs.
New product development-such as the recently launched LP FlameBlock Fire-Rated
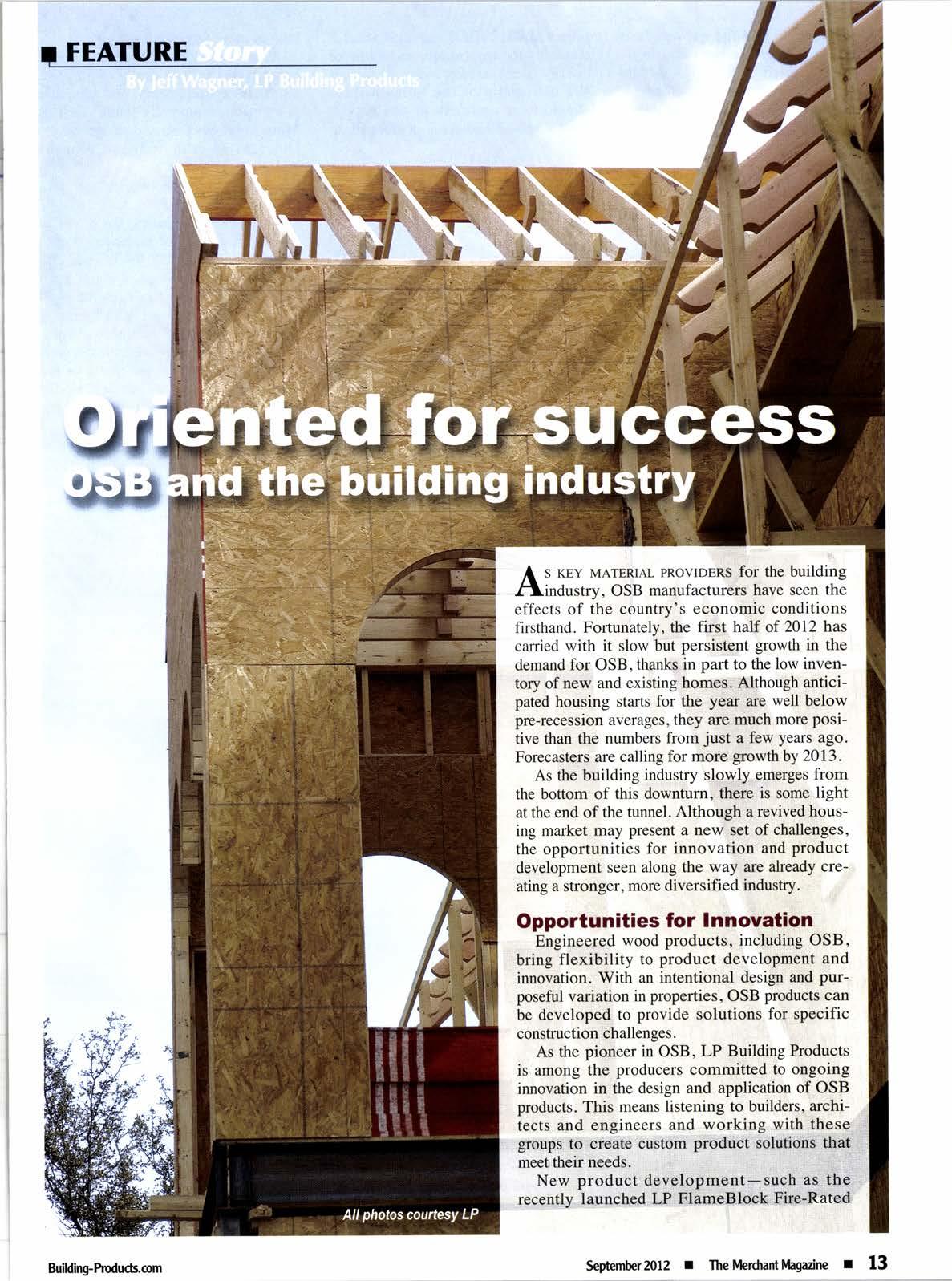
OSB Sheathing and the growing use of LP TechShield Radiant Barrierprovides builders with more options when meeting construction challenges. As many segments of the building industry are navigating through the proposed 2Ol2IECC energy code, LP stands by the importance and value of energy codes across North America. We also believe the homebuilder should have a variety of products at their disposal and have choices as to
Full-Service Strategy Gives Dealer Edge
JL Schwieters Building Supply, Hugo, Mn., is more than just an LBM dealer. It's a service provider whose custom packages from plates to peak are making life for builder customers a bit easier.
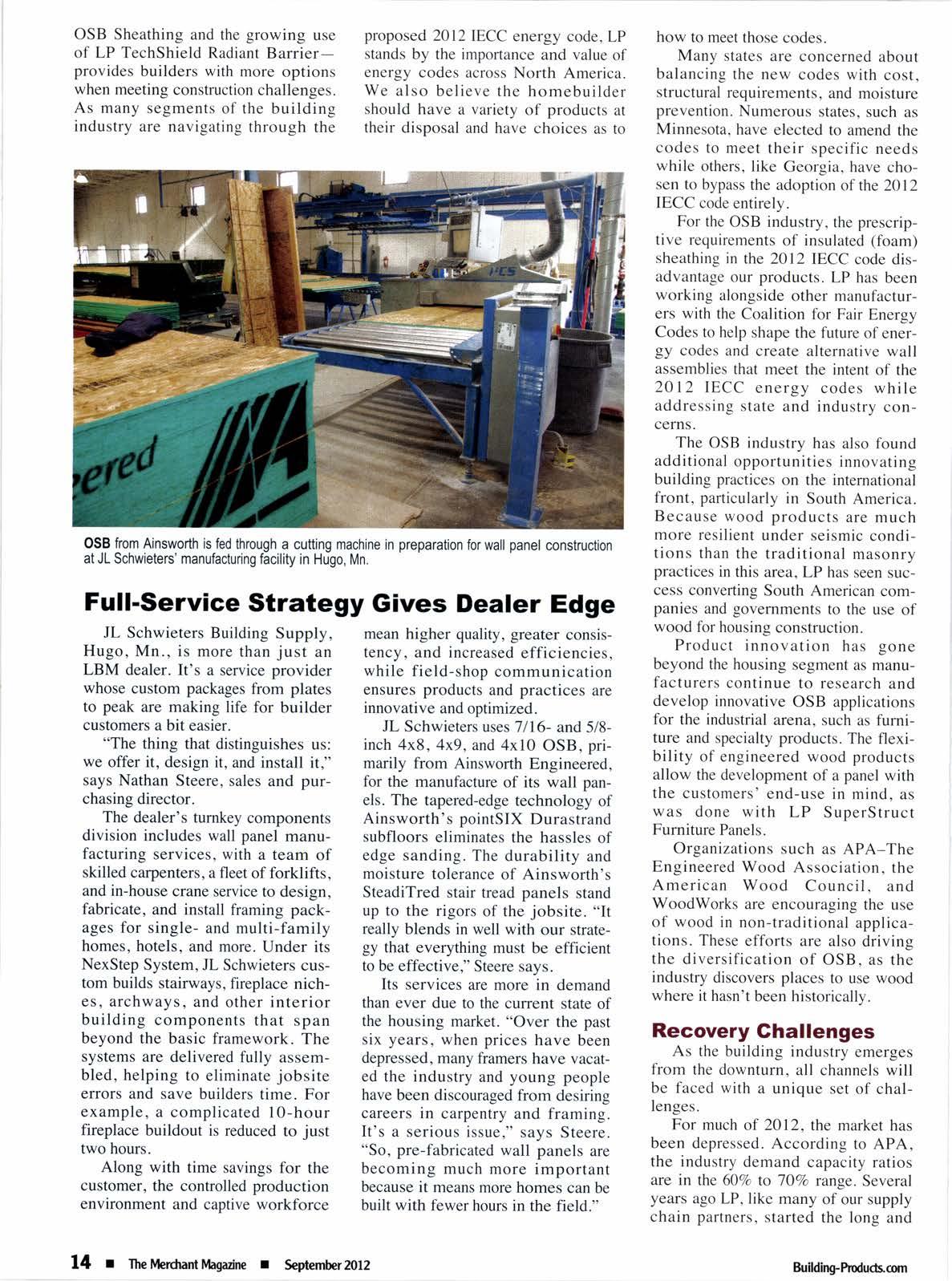
"The thing that distinguishes us: we offer it, design it, and install it," says Nathan Steere, sales and purchasing director.
The dealer's turnkey components division includes wall panel manufacturing services, with a team of skilled carpenters, a fleet of forklifts, and in-house crane service to design, fabricate, and install framing packages for single- and multi-family homes. hotels. and more. Under its NexStep System, JL Schwieters custom builds stairways, fireplace niches, archways, and other interior building components that span beyond the basic framework. The systems are delivered fully assembled, helping to eliminate jobsite errors and save builders time. For example, a complicated 1O-hour freplace buildout is reduced to just two hours.
Along with time savings for the customer, the controlled production environment and captive workforce mean higher quality, greater consistency, and increased efficiencies, while field-shop communication ensures products and practices are innovative and optimized.
JL Schwieters uses 7/16- and 5/8inch 4x8, 4x9,and 4x10 OSB, primarily from Ainsworth Engineered, for the manufacture of its wall panels. The tapered-edge technology of Ainsworth's pointSIX Durastrand subfloors eliminates the hassles of edge sanding. The durability and moisture tolerance of Ainsworth's SteadiTred stair tread panels stand up to the rigors of the jobsite. "It really blends in well with our strategy that everything must be efficient to be effective," Steere says.
Its services are more in demand than ever due to the current state of the housing market. "Over the past six years, when prices have been depressed, many framers have vacated the industry and young people have been discouraged from desiring careers in carpentry and framing. It's a serious issue," says Steere. "So, pre-fabricated wall panels are becoming much more important because it means more homes can be built with fewer hours in the field."
how to meet those codes.
Many states are concerned about balancing the new codes with cost, structural requirements, and moisture prevention. Numerous states, such as Minnesota, have elected to amend the codes to meet their specific needs while others, like Georgia, have chosen to bypass the adoption of the 2Ol2 IECC code entirely.
For the OSB industry, the prescriptive requirements of insulated (foam) sheathing in the 2OI2IECC code disadvantage our products. LP has been working alongside other manufacturers with the Coalition for Fair Energy Codes to help shape the future of energy codes and create alternative wall assemblies that meet the intent of the 2012 IECC energy codes while addressing state and industry concerns.
The OSB industry has also found additional opportunities innovating building practices on the international front, particularly in South America. Because wood products are much more resilient under seismic conditions than the traditional masonry practices in this area, LP has seen success converting South American companies and governments to the use of wood for housing construction.
Product innovation has gone beyond the housing segment as manufacturers continue to research and develop innovative OSB applications for the industrial arena, such as furniture and specialty products. The flexibility of engineered wood products allow the development of a panel with the customers' end-use in mind, as was done with LP SuperStruct Furniture Panels.
Organizations such as APA-The Engineered Wood Association, the American Wood Council. and WoodWorks are encouraging the use of wood in non-traditional applications. These efforts are also driving the diversification of OSB, as the industry discovers places to use wood where it hasn't been historically.
Recovery Ghallenges
As the building industry emerges from the downturn, all channels will be faced with a unique set of challenges.
For much of 2012, the market has been depressed. According to APA, the industry demand capacity ratios are in the 60Vo to TOVo range. Several years ago LP, like many of our supply chain partners, started the long and painful task of right-sizing our operations and infrastructure to accommodate the depressed demand levels of the past six years. Through this process, our objective has been to balance our supply by region against the demand our customers have for our products.
THE CONSTRUCTION industrv can count on OSB manufacturers to continue to develop better-perfoiming, more efficiently installed products.
Market conditions suggest the revived industry may encounter shortages across the board from inventory to transportation. The logging infrastructure-including both the logs themselves and the trucks used to move themhas shrunk based on demand and has the potential for a slower comeback than the market itself.
There is also a shortage of flatbed trucks across North America. As manufacturers start to ramp up production facilities to meet customer demand, there is a very real concern about having the trucking infrastructure to meet those needs. LP is aware of these challenges and is working with suppliers and customers to help mitigate them.
Looking to the Future
The building industry has gone through the toughest five years in its history, facing changes and adjusting operations as needed. But through product innovation, there have been bright points along the way.
OSB's place in the building products industry remains strong. As the market improves, competitive lessons learned in the downturn will provide a new emphasis on service to the customer and the end users' needs for our products.