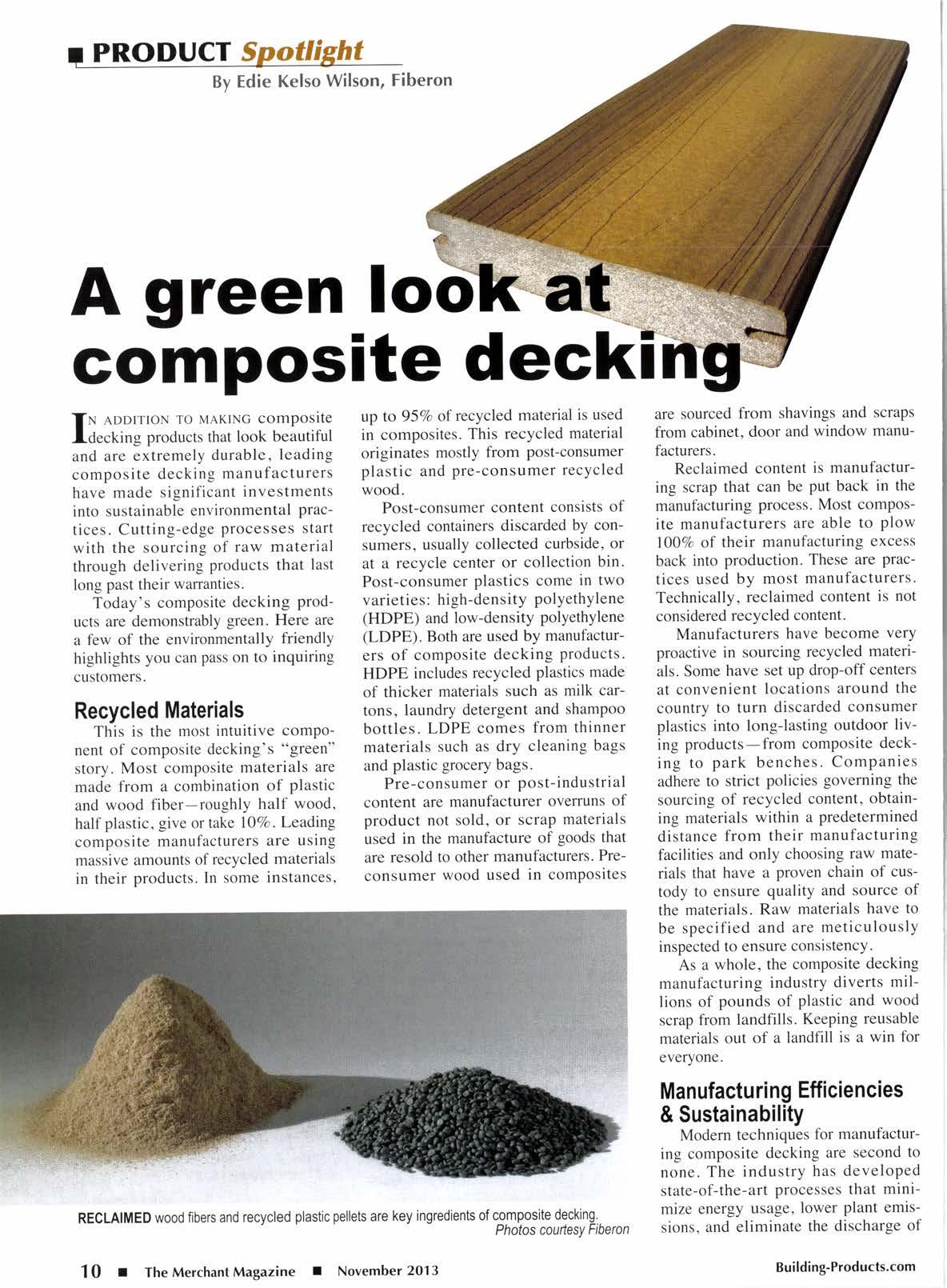
3 minute read
A green lo composite deck
fN enorrtoN To MAKING composlte
Idecking products that look beautiful and are extremely durable, leading composite decking manufacturers have made significant investments into sustainable environmental practices. Cutting-edge processes start with the sourcing of raw material through delivering products that last long past their warranties.
Today's composite decking products are demonstrably green. Here are a few of the environmentally friendly highlights you can pass on to inquiring customers.
Recycled Materials
This is the most intuitive component of composite decking's "green" story. Most composite materials are made from a combination of Plastic and wood fiber-roughly half wood, half plastic, give or take lOVo Leading composite manufacturers are using massive amounts of recycled materials in their products. In some instances, up to 957o of recycled material is used in composites. This recycled material originates mostly from post-consumer plastic and pre-consumer recycled wood.
Post-consumer content consists of recycled containers discarded by consumers, usually collected curbside, or at a recycle canter or collection bin. Post-consumer plastics come in two varieties: high-density polyethylene (HDPE) and low-density polyethylene (LDPE). Both are used by manufacturers of composite decking products. HDPE includes recycled plastics made of thicker materials such as milk cartons, laundry detergent and shampoo bottles. LDPE comes from thinner materials such as dry cleaning bags and plastic grocery bags.
Pre-consumer or post-industrial content are manufacturer ovemrns of product not sold, or scrap materials used in the manufacture of goods that are resold to other manufacturers. Preconsumer wood used in composites are sourced from shavings and scraps from cabinet, door and window manufacturers.
Reclaimed content is manufacturing scrap that can be Put back in the manufacturing process. Most composite manufacturers are able to Plow l00%a of their manufacturing excess back into production. These are practices used by most manufacturers. Technically, reclaimed content is not considered recycled content.
Manufacturers have become verY proactive in sourcing recycled materials. Some have set up drop-off centers at convenient locations around the country to turn discarded consumer plastics into long-lasting outdoor living products-from composite decking to park benches. ComPanies adhere to strict policies governing the sourcing of recycled content, obtaining materials within a predetermined distance from their manufacturing facilities and only choosing raw materials that have a proven chain of custody to ensure quality and source of the materials. Raw materials have to be specified and are meticulouslY inspected to ensure consistencY.
As a whole, the composite decking manufacturing industry diverts millions of pounds of plastic and wood scrap from landfills. Keeping reusable materials out of a landfill is a win for everyone.
Manufacturi ng Efficiencies & Sustainability
Modern techniques for manufacturing composite decking are second to none. The industry has develoPed state-of-the-art processes that minimize energy usage, lower plant emissions, and eliminate the discharge of waste water into the environment. Advanced green technologies and a sincere desire to deliver truly environmentally friendly products have made the composite decking industry a leader in sustainable practices.
Shipment of Product
As both a cost- and energy-saving strategy, two top composite decking and railing manufacturers have invested in manufacturing facilities on both coasts. This investment reduces the hidden waste-time, energy and vehicle emissions-of shipping composite decking across the country.
In addition, shipping product by rail whenever feasible reduces fuel costs and carbon emissions. In fact, according to the U.S. Energy Information Administration and its Annual Energy Outlook 2013 reporr, shipping freight via rail saves 92Vo in carbon emissions (converted from petroleum consumption) compared to shipping via truck.
A Sustainable Replacement
While obvious. it is important to remind customers that building with composite decking materials saves trees. Wood decks deteriorate in l0 to 12 years if not properly maintained.
Boards will twist, splinter, split and rot over time and will require replacement even when maintained properly. And for wood to achieve any longevity, it requires regular staining or painting to withstand Mother Nature's harsh conditions.
On the other hand, composite decks are made to last 30, 40 or 50 years or more without splintering, twisting or rotting. Decks made from composite materials don't require chemical stains or sealers. Bottom line. composites are designed to last for decades, while wood degrades much more quickly, necessitating more frequent replacement and use of resources.
For both residential and commercial builders, composite decking provides the added benefit of contributing points to green buildings. Points are awarded for post-consumer recycled material used, amount of sourced materials within a 500-mile proximity of the jobsite, and other resource efficiencies, such as termite-resistant materials.
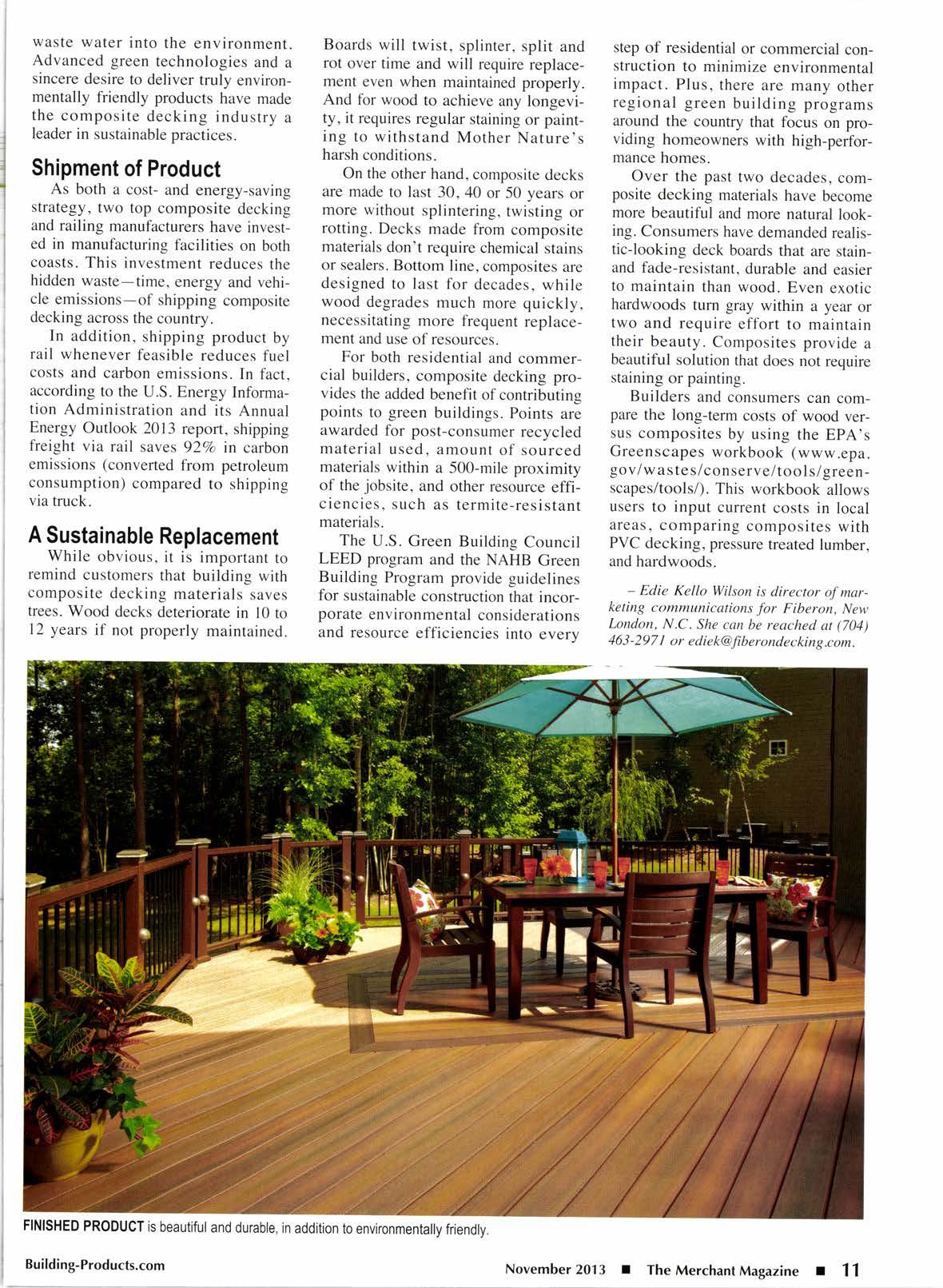
The U.S. Green Building Council LEED program and the NAHB Green Building Program provide guidelines for sustainable construction that incorporate environmental considerations and resource efficiencies into every step of residential or commercial construction to minimize environmental impact. Plus, there are many other regional green building programs around the country that focus on providing homeowners with high-performance homes.
Over the past two decades, composite decking materials have become more beautiful and more natural looking. Consumers have demanded realistic-looking deck boards that are stainand fade-resistant, durable and easier to maintain than wood. Even exotic hardwoods turn gray within a year or two and require effort to maintain their beauty. Composites provide a beautiful solution that does not require staining or painting.
Builders and consumers can compare the long-term costs of wood versus composites by using the EPA's Greenscapes workbook (www.epa. gov/waste s/conserve/tools/greenscapes/tools/). This workbook allows users to input current costs in local areas, comparing composites with PVC decking, pressure treated lumber, and hardwoods.
- Edie Kello Wilson is director of marketing communications for Fiberon, New London, N.C. She can be reached at (704) 463-297 1 or ediek@fiberondecking.com.