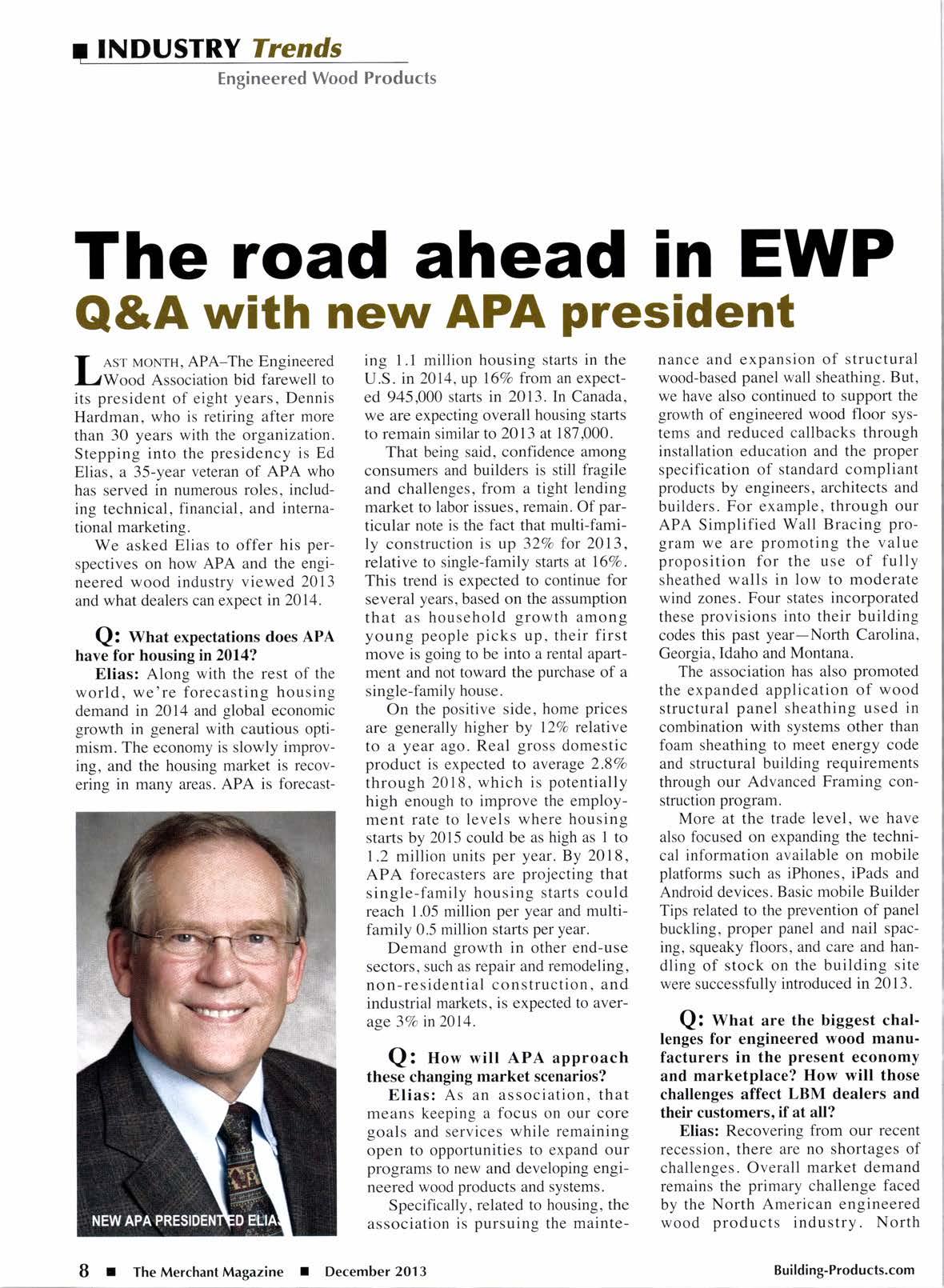
8 minute read
The road ahead in EWP Q&A with new APA president
f nsr MoNrH. APA-The Engineered LWood Association bid farewell to its president of eight years, Dennis Hardman, who is retiring after more than 30 years with the organization. Stepping into the presidency is Ed Elias, a 35-year veteran of APA who has served in numerous roles, including technical, financial, and international marketing.
We asked Elias to offer his perspectives on how APA and the engineered wood industry viewed 2013 and what dealers can expect Ln2014.
Q: Wt ut expectations does APA have for housing in20l4?
Elias: Along with the rest of the world, we're forecasting housing demand in 2014 and global economic growth in general with cautious optimism. The economy is slowly improving, and the housing market is recovering in many areas. APA is forecast- ing 1.1 million housing starts in the U.S. in 2014,up 167o from an expected 945900 starts in 2013. In Canada, we are expecting overall housing starts to remain similar to 2013 at 187000.
That being said, confidence among consumers and builders is still fragile and challenges, from a tight lending market to labor issues, remain. Of particular note is the fact that multi-fami ly construction is up 32Vo for 2013, relative to single-family starts at 167o. This trend is expected to continue for several years, based on the assumption that as household growth among young people picks up,their first move is going to be into a rental apartment and not toward the purchase of a single-family house.
On the positive side, home prices are generally higher by l27o relative to a year ago. Real gross domestic product is expected to average 2.87o through 2018, which is potentially high enough to improve the employment rate to levels where housing starts by 2015 could be as high as 1 to 1.2 million units per year. By 2018, APA forecasters are projecting that single-family housing starts could reach 1.05 million per year and multifamily 0.5 million starts per year.
Demand growth in other end-use sectors, such as repair and remodeling, non-residential construction, and industrial markets, is expected to average 3Vo in20l4.
Q: Ho* will APA approach these changing market scenarios?
Elias: As an association, that means keeping a focus on our core goals and services while remaining open to opportunities to expand our programs to new and developing engineered wood products and systems. Specifically, related to housing, the association is pursuing the mainte- nance and expansion of structural wood-based panel wall sheathing. But, we have also continued to support the growth of engineered wood floor systems and reduced callbacks through installation education and the proper specification of standard compliant products by engineers, architects and builders. For example, through our APASimplified Wall Bracing program wearepromoting the value proposition for the use of fully sheathed walls in low to moderate wind zones. Four states incorporated these provisions intotheirbuilding codes this past year-North Carolina, Georgia, Idaho and Montana.
The association has also promoted the expanded application of wood structural panel sheathing used in combination with systems other than foam sheathing to meet energy code and structural building requirements through our Advanced Framing construction program.
More at the trade level, we have also focused on expanding the technical information available on mobile platforms such as iPhones, iPads and Android devices. Basic mobile Builder Tips related to the prevention of panel buckling, proper panel and nail spacing, squeaky floors, and care and handling of stock on the building site were successfully introduced in 2013.
Q: Wttut are the biggest challenges for engineered wood manufacturers in the present economy and marketplace?How will those challenges affect LBM dealers and their customers, if at all?
Elias: Recovering from our recent recession, there are no shortages of challenges. Overall market demand remains the primary challenge faced by the North American engineered wood products industry. North
American structural wood panel production in2Ol3 is forecast to reach 21.3 billion sq. ft. on a 3/8" thickness basis. We remain well below the 43 billion sq. ft. of production during 2005 and the peak of our housing market that totaled 2.3million housing starts that year.
Government fiscal policy is a challenge that we cannot directly address but clearlyimpacts labor markets, interest rates, and consumer confidence. The trend of depressed employment rates across all age classes, most notably in the under-35 age group, continues to adversely impact household growth and homeownership.
Global supply and demand of wood products may also impact future consumption patterns of North American construction materials. The cost of raw materials and labor, and the availability of transport for distribution, will need to be balanced against trade policies between developing and developed nations. Competitive use of wood fiber for non-structural applications, such as wood pellets to meet clean energy targets, could also impact future availability. Other potential constraints deal with expanding regulatory concerns on formaldehyde emissions and those of methanol, as well as green building legislation.
There are no shortages of challenges; prioritizing them will be a key role of the association. its board of trustees, and membership.
Q: Whut" the industry production forecast for 2Ol4 and beyond? Which categories are expected to be the strongest performers?
Elias: For 2014, we forecast U.S. and Canadian plywood and OSB production to rise by 1.9 billion sq. ft. reaching 25.7 billion ft., up 97o from 2013. By 2018, U.S. and Canadian structural wood panel production is expected to reach 27.4 billion sq. ft.
For 2014, North American production of engineered wood products, such as glued laminated timber, structural composite lumber, and wood Ijoists, are forecast to improve by 5Vo, l2%o andTTo,respectively as the North American economy improves. Overall glulam demand in North America is expected to grow from 251 million bd. ft. in 2013 to 328 million bd. ft. in 2018. Structural wood I-joist production is expected to grow from 625 linear ft. in 2Ol3 to 887 million linear ft. in 2018. LVL volumes will increase from 61.5 million cubic ft. in 2013 to
79.8 million cubic ft. in 2018. An increase in housing starts is expected to be the main driver for this increasing demand for engineered wood in North America. We also believe that recovery in non-residential construction will lag behind but follow home building. In this latter sector, we expect to see 3l%o growth by 2018 in comparison with 2013.
Q: Wttat are some of APA's chief highlights from 2013?
Elias: APA's website, www.apawood.org, had almost 5,000 visits per day, every day of the year. Nearly 6,000 end-users had technical issues addressed by the APA Product Support Help Desk. New and updated technical publications were added to our library, and close to 150,000 publications were downloaded.
We developed a bi-national ANSI standard for cross laminated timber and published a performance-rated structural insulated panel ANSI standard for use in wall applications. Promotion and education supported several APA wall sheathing systems to expand the specification and application of structural wood panels.
APA established a strategic partnership with WoodWorks and, with the U.S. Forest Products Lab, hosted two Carbon Challenge competitions. Our field services staff hosted six dealer training events in the past year and presented a variety of educational sessions around the U.S.
Q: Wttut resources can engineered wood retailers and end-users expect from APA in2014?
Elias: We will continue to support the cost-effective use of structural wood wall sheathing to meet state energy and building codes. We will promote the preference of continuously sheathed wood structural panel walls to builders and code officials through field calls, publicity, seminars and publications.
We will also continue to promote the specification and proper application of engineered wood products in APA wall, roof and floor systems, both in residential as well as commercial construction applications. The latter will be in conjunction with the industry-wide WoodWorks campaign.
As well, increased incorporation of web-based programs, mobile applications, and social media will continue to be a priority.
Engineered Wood Panel Demand Growing Sharply
Demand for OSB and plywood structural engineered wood panels in North Americais expected to reach about 30 billion (3/8" basis) sq. ft. in 2013 and grow to nearly 40 billion sq. ft. by 2016, according to Principia Consulting.
SpecialtyOSB and plywood panels are the fastest growing segments within the business. Specialty panels offer value-added performance benefits compared to commodity panels, which enable manufacturer product differentiation in the market and some protection from competitive pressures through specificationselling, leading to steady demand and higher margins.
"Industry pricing and margins are subject to wide swings due to the cyclical nature of the structural engineered wood panels business," said Steve Van Kouteren, Principia's business director-industry reports. "As manufacturers bring capacity back online and plan new greenfield plants for the next growthcycle,awell-positioned specialty panels business provides higher margins and price stability during these cycles."
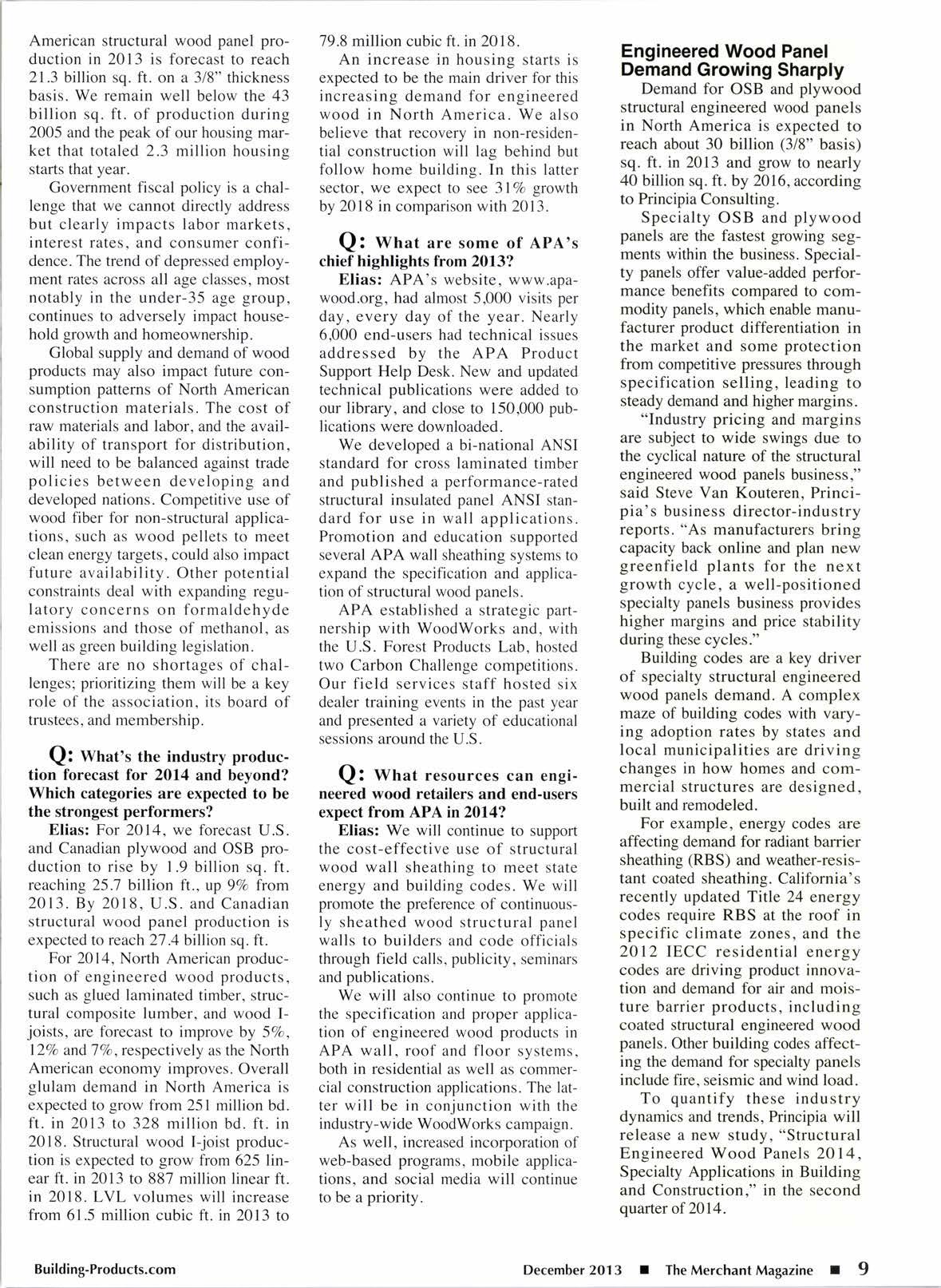
Building codes are a key driver of specialty structural engineered wood panels demand. A complex maze of building codes with varying adoption rates by states and local municipalities are driving changes in how homes and commercial structures are designed, built and remodeled.
For example, energy codes are affecting demand for radiant barrier sheathing (RBS) and weather-resistant coated sheathing. California's recently updated Title 24 energy codes require RBS at the roof in specific climate zones, and the 2Ol2 IECC residential energy codes are driving product innovation and demand for air and moisture barrier products, including coated structural engineered wood panels. Other building codes affecting the demand for specialty panels include fire, seismic and wind load.
To quantify these industry dynamics and trends, Principia will release a new study, "Structural Engineered Wood Panels 2Ot4, Specialty Applications in Building and Construction," in the second quarter of 2014.
[1nnlclslcY IN THE warehouse is I)lparamount to the success of any LBM company. It's amazing how simple tweaks to processes can have big impacts on efficiency-and an organization's bottomline.Despite this, many companies fail to make the necessary changes.
Here are five simple things that can improve efficiency in warehouse management:
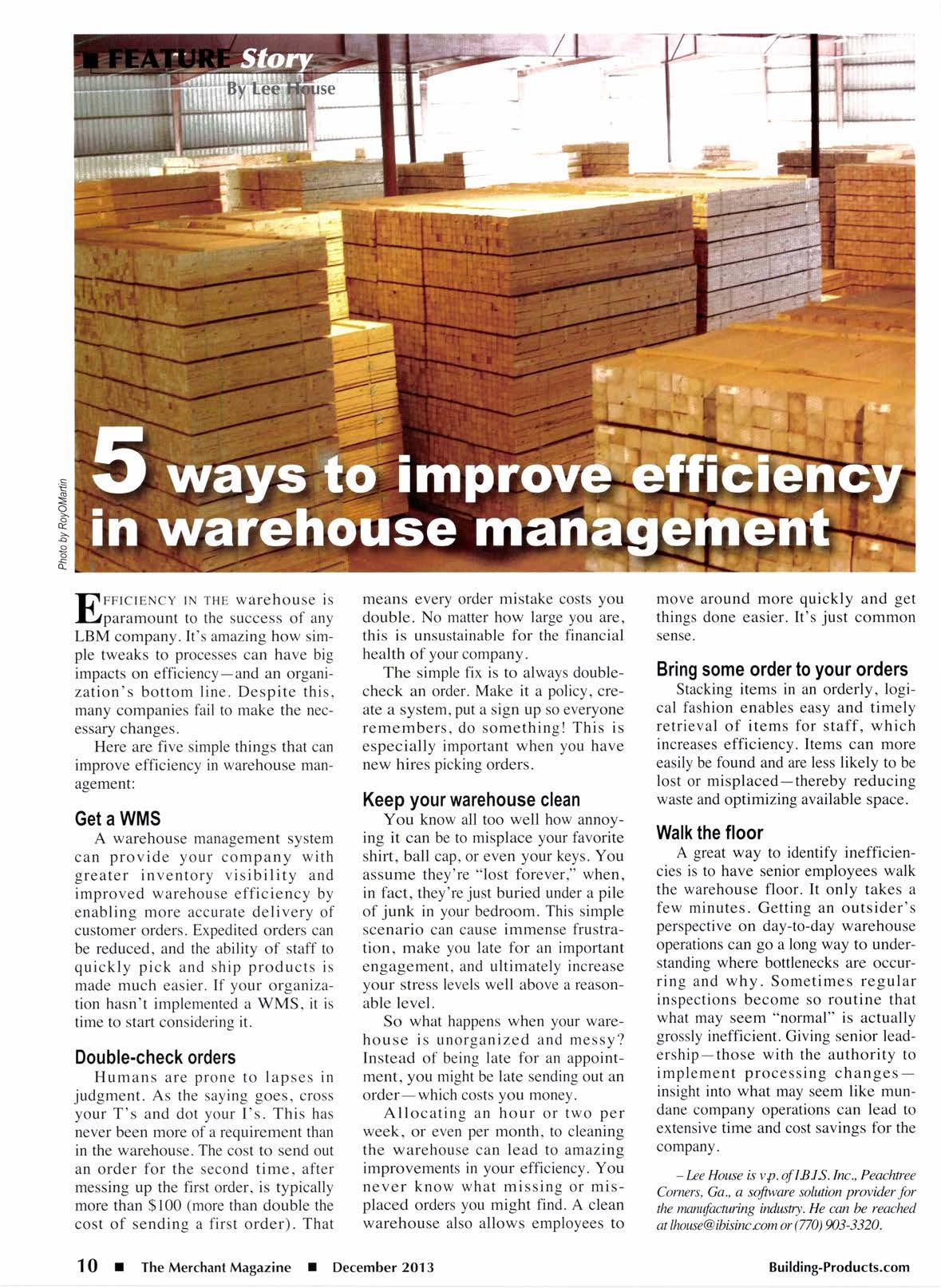
Get a WMS
A warehouse management system can provide your company with greater inventory visibility and improved warehouse efficiency by enabling more accurate delivery of customer orders. Expedited orders can be reduced, and the ability of staff to quickly pick and ship products is made much easier. If your organization hasn't implemented a WMS, it is time to start considering it.
Double-check orders
Humans are prone to lapses in judgment. As the saying goes, cross your T's and dot your I's. This has never been more of a requirement than in the warehouse. The cost to send out an order for the second time, after messing up the first order, is typically more than $100 (more than double the cost of sending a first order). That means every order mistake costs you double. No matter how large you are, this is unsustainable for the financial health ofyourcompany.
The simple fix is to always doublecheck an order. Make it a policy, create a system, put a sign up so everyone remembers, do something! This is especially important when you have new hires picking orders.
Keepyour warehouse clean
You know all too well how annoying it can be to misplace your favorite shirt, ball cap, or even your keys. You assume they're "lost forever," when, in fact, they're just buried under a pile of junk in your bedroom. This simple scenario can cause immense frustration, make you late for an important engagement, and ultimately increase your stress levels well above a reasonable level.
So what happens when your warehouse is unorganized and messy?
Instead of being late for an appointment, you might be late sending out an order-which costs you money.
Allocating an hour or two per week, or even per month, to cleaning the warehouse can lead to amazing improvements in your efficiency. You never knowwhatmissing or misplaced orders you might find. A clean warehouse also allows employees to move around more quickly things done easier. It's just sense. and get common
Bring some order to your orders
Stacking items in an orderly, logical fashion enables easy and timely retrieval of items for staff, which increases efficiency. Items can more easily be found and are less likely to be lost or misplaced-thereby reducing waste and optimizing available space.
Walk the floor
A great way to identify inefficiencies is to have senior employees walk the warehouse floor. It only takes a few minutes. Getting an outsider's perspective on day-to-day warehouse operations can go a long way to understanding where bottlenecks are occurring and why. Sometimes regular inspections become so routine that what may seem "normal" is actually grossly inefficient. Giving senior leadership-those with the authority to implement processing changesinsight into what may seem like mundane company operations can lead to extensive time and cost savings for the company.