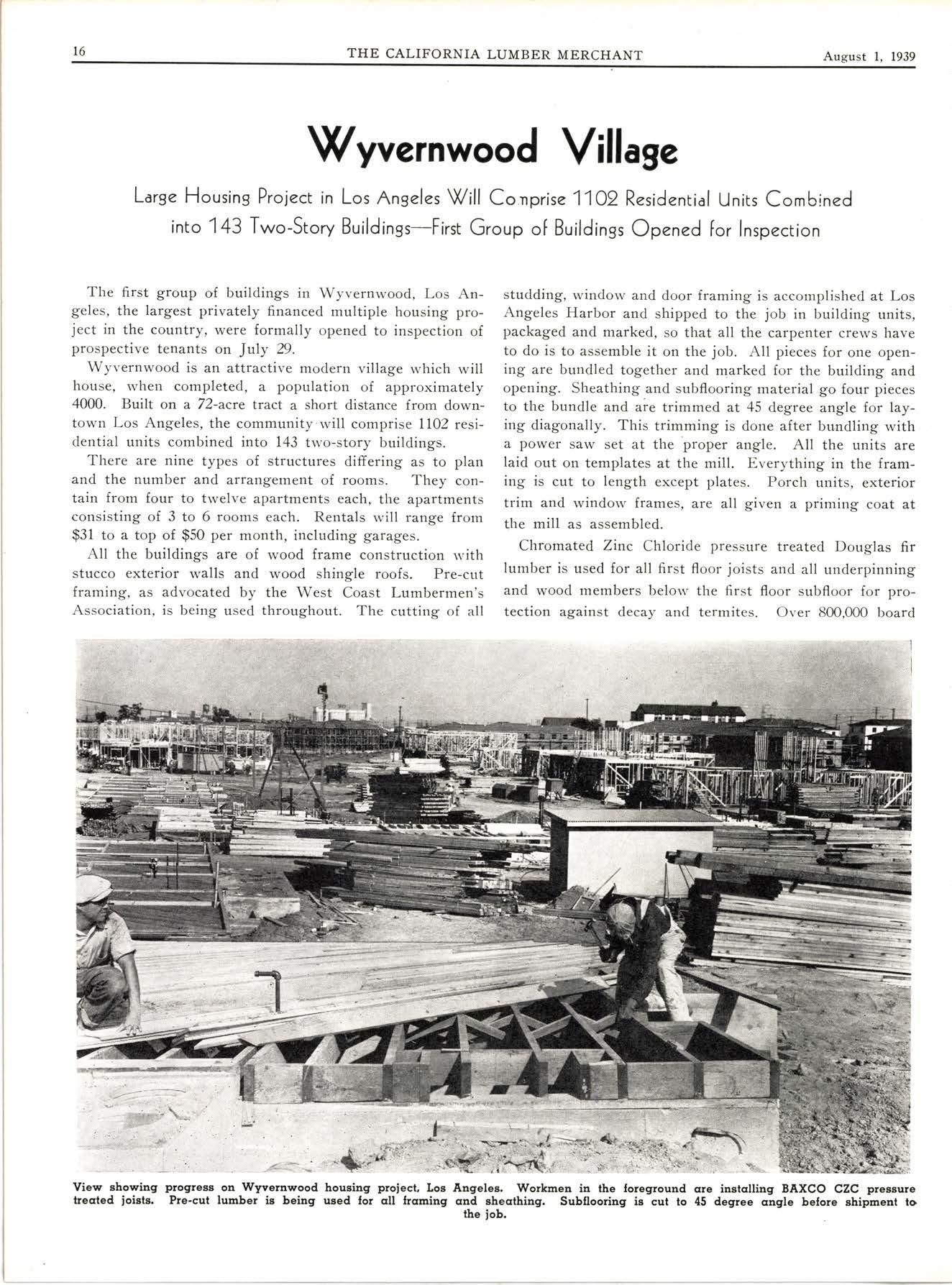
3 minute read
Wy"ernwood Village
Large Housing Project in Los Angeles Will Corprise 11Og Residential Unirs Combined into 143 Two-Story Buildings-First Group of Buildings Opened for Inspection
The first group of buildings in Wyvernwood, Los Angeles, the largest privately financed multiple housing project in the country, were formally opened to inspection of prospective tenants on July D.
Wyvernwood is an attractive modern village which will house, rvhen completed, a population of approximately 4000. Built on a 72-acre tract a short distance from downtown Los Angeles, the community will comprise 1102 residential units combined into 143 two-story buildings.
There are nine types of structures differing as to plan and the number and arrangement of rooms. They contain from four to twelve apartments each, the apartments consisting of 3 to 6 rooms each. Rentals will range from $31 to a top of $50 per month, including garages.
All the buildings are of wood frame construction n'ith stucco exterior r,r'alls and wood shingle roofs. Pre-cut framing, as advocated by the West Coast Lumbermen's Association, is being used throughout. The cutting of all studding, window and door framing is accomplished at Los Angeles Harbor and shipped to the job in building units, packaged and marked, so that all the carpenter crews have to do is to assemble it on the job. All pieces for one opening are bundled together a.nd marked for the building and opening. Sheathing and subflooring material go four pieces to the bundle and aie trimmed at 45 degree angle for laying diagonally. This trimming is done after bundling with a power saw set at the proper angle. All the units are laid out on templates at the mill. Everything in the framing is cut to length except plates. Porch units, exterior trim and windorv frames, are all given a priming coat at the mill as assembled.
Chromated Zinc Chloride pressure treated Douglas fir lumber is used for all first floor joists and all underpinning and wood members belorv the first floor subfloor for protection against decay and termites. Over 80O,00O board feet of CZC tteated lumber is being installed in the project..
Consolidated Lumber Co., at Wilmington, is furnishing 8,000,C00 board feet of lumber required for rough framing. 'Ihe CZC treated lumber used was processed for this firm by J. H. Baxter & Co. at its Long Beach pressure treating plant.
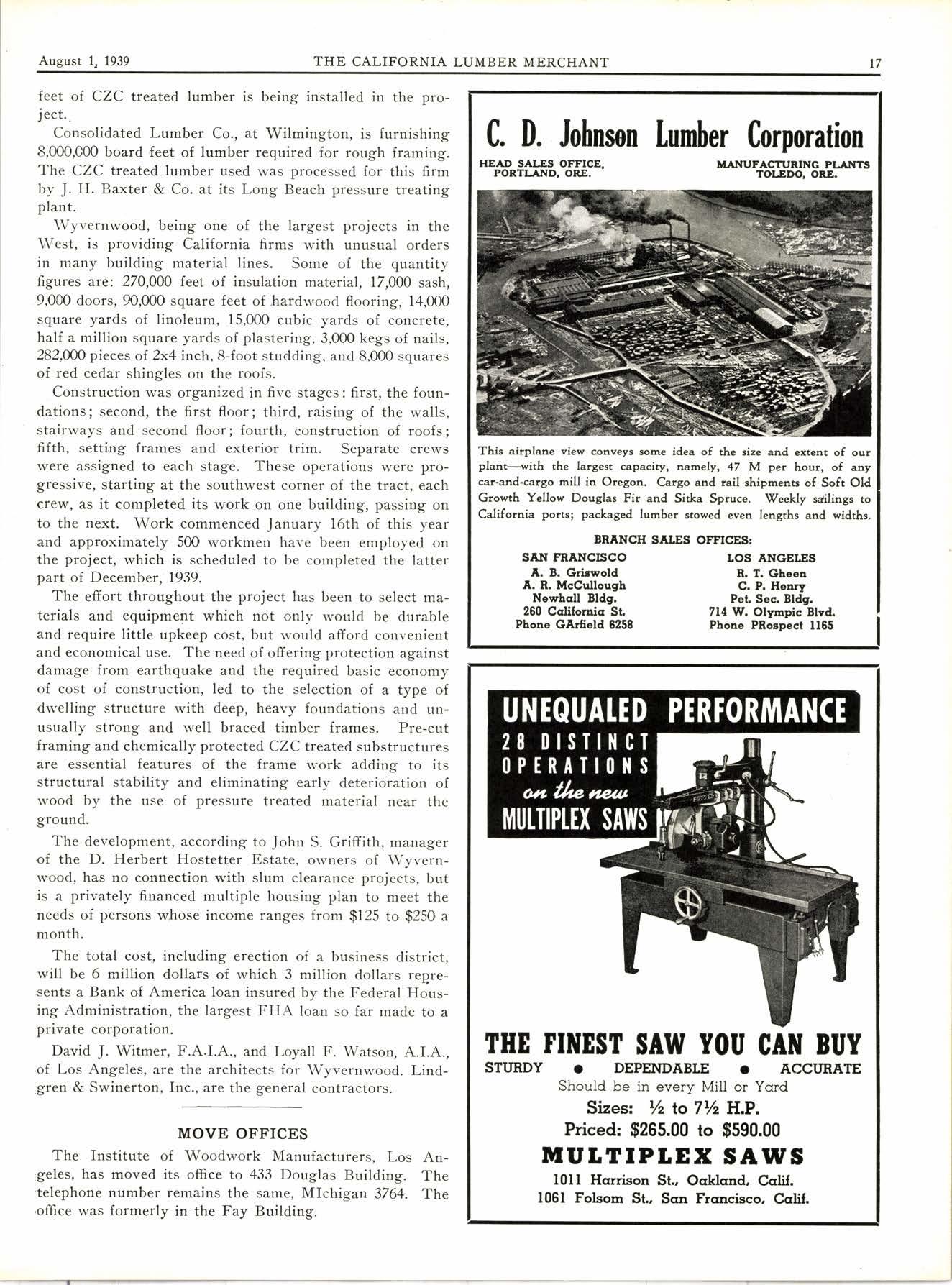
Wyvernwood, being one of the largest projects in the West, is providing Califor.nia firms with unusual orders in many building material lines. Some of the quantity figures are 270,0N feet of insulation material, 17,000 sash, 9,000 doors, 90,000 square feet of hardwood flooring, 14,000 square yards of linoleum, 15,000 cubic yards of concrete, half a million square yards of plastering, 3,00O kegs of nails, 28Z,WO pieces ol 2x4 inch, 8-foot studding, and 8,000 squares of red cedar shingles on the roofs.
Construction was organized in five stages : first, the foundations; second, the first floor; third, raising of the walls, stairways and second floor; fourth, construction of roofs ; fifth, setting frames and exterior trim. Separate crews were assigned to each stage. These operations were progressive, starting at the southwest corner of the tract, each crew, as it completed its work on one building, passing on to the next. Work commenced January l6th of this year and approximately 50O workmen have been employed on the project, which is scheduled to be completed the latter part of December, 1939.
The effort throughout the project has been to select materials and equipment which not only 'vvould be durable and require little upkeep cost, but would afford convenient and economical use. The need of offering protection against damage from earthquake and the required basic economy of cost of construction, led to the selection of a type o,f dwelling structure with deep, heavy foundations and unusually strong and well braced timber frames. Pre-cut framing and chemically protected CZC treated substructures are essential features of the frame work adding to its structural stability and eliminating early deterioration of wood by the use of pressure treated material near the ground.
The development, according to John S. Griffith, ma,nager of the D. Herbert Hostetter Estate, owners of Wyvernwood, has no connection with slum clearance projects, but is a privately financed multiple housing plan to meet the needs of persons whose income ranges from $125 to $250 a month.
The total cost, including erection of a business district, will be 6 million dollars of which 3 million dollars repre:sents a Bank of America loan insured by the Federal Housing Administration, the largest FHA loan so far made to a private corporation.
David J. Witmer, F.A.I.A., and Loyall F. Watson, A.I.A., .of Los Angeles, are the architects for Wyvernwood. Lindgren & Swinerton, Inc., are the general contractors.
Move Offices
The Institute of Woodwork Manufacturers, Los geles, has moved its office to 433 Douglas Building. 'telephone number remains the same, Mlchigan 3764. .office was formerly in the Fay Building.