
4 minute read
Manufacturing Red Cedaf Shin$les
To the materials in most common use and particularly those constantly before us 1\'e give perhaps less thought than to those which .are .not so comtnon ,but wrhich have been more recently brought to our notice, because of the newl properties they may possess, or because of a suprposed need they may seem to fill.
Shingles, for examrple, are one of the oldest of our building materials, having'been in constant use in this country for nearly three hundred years. Because of the great demancl for them the old methods of manufacture have long hundred in the Pacific Northwest devoted to the exclusive rnanufacture of Red Cedar Shingles, and are intended ito show as nearly as possible the complete process of their manufacture.
Nearly all ,shingls mills are located on some body of water where the logs may be conveniently floated to the "storage pond" adjoining the mill (Fig' 1)- They are twostory structures with a islip or chute running out into the water over which the logs are drawn from the pond to the since been done away with and have been replaced by the use of 'the 'most modern machinery. Shingles were first rived from the solid wood and later split in order to obtain a straight and more even grai'n. Now they are manufactured. in a most scientific and economical manner'
To correct the impression that shingles are manufactured frorn branches, slabs and 'other waste from the log, these reproductions showing the various steps of manufacture from the log to the finished product have been made' These views were taken in a typical shingle mill,rone of some firre tirst floor of the mill by means of a lheavy conveyor chain (Fig. 2). ' A large saw running at the end of the slip cuts ofr sections of r'the loglas it advances into the mill (Fig 3)'
These sections, usually termed "blocks," are sixteen, eighteen, or twenty-four inches long, depending u'pon the length of the shingles to be manufactured. When cut frotn thJ,log they drop on to a moving carriage which "feeds" them into a second a'nd smaller saw where they are "quartered" (Fig. a) 'by cutting across the diameter of the "blocks," turning them and'again sawing through them at right angles to the first cut. This process not only works them down to a more practical size to be handled 'in the process of manufacture, but also opens up the block in a mallner that pernrits the cutting of edge or verticle grain shingles.
Edge grain shingles, because of the natrlral grain of the wood will not warp or curl when'in place on. the roof of a building because of atmospheric conditions and are therefore much preferable to the flat grain type for the roofing of buildings. Flat grain shingles, while they are eminently suitable for coviring the sides of buildings, lwhere they will give perfect satisfaction, cup and curl on a roo{ rvhen subjected to atmosp,heric changes.
The smaller blocks produced in the quartering operation are passed along to a third saw, where the bark is trimmed off and any surface de'fects cut out (Fig. 6). When this operation is completed the blocks are ready to be placed in the shingle machines and are taken by m€ans of another
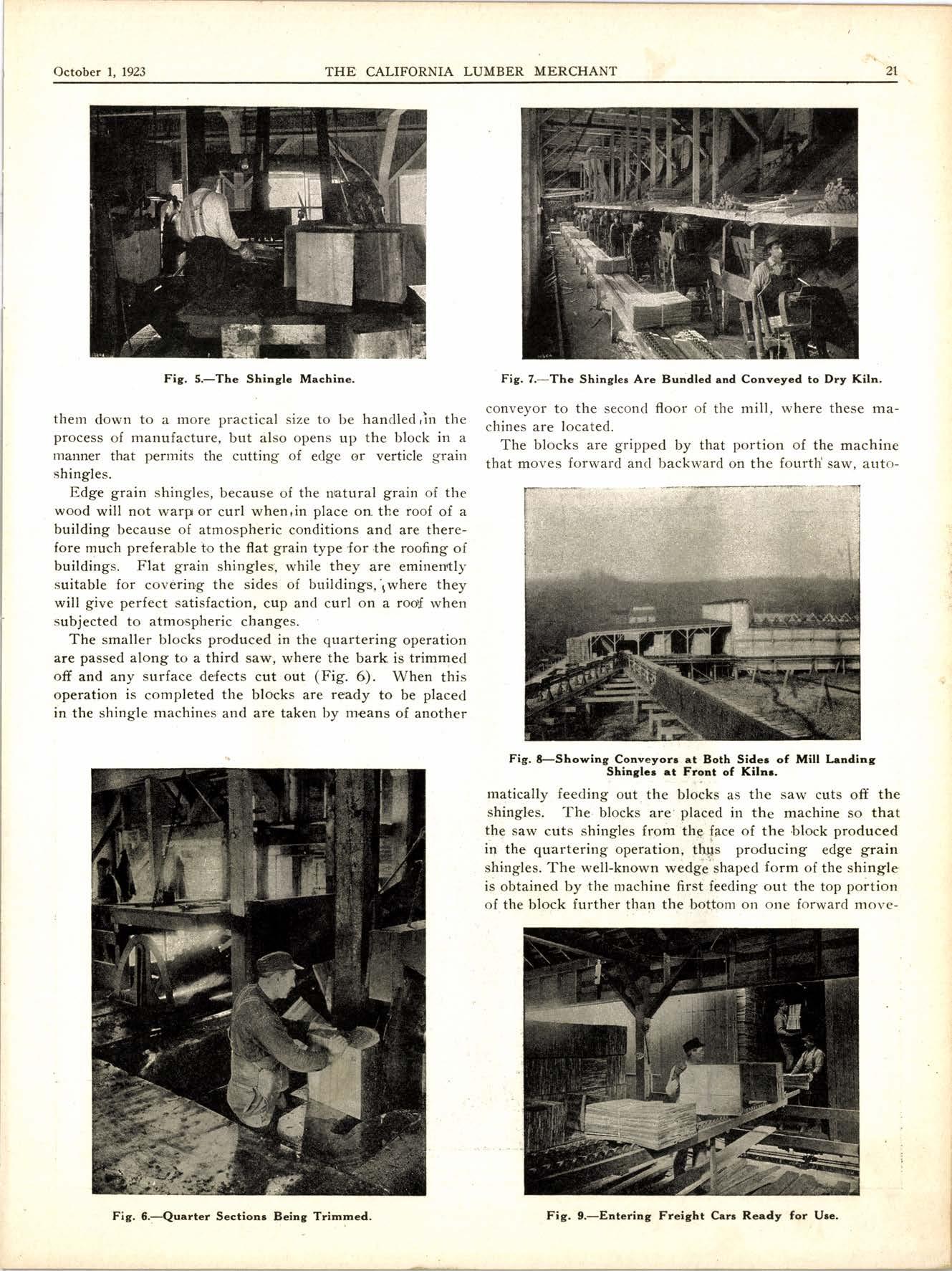
The blocks are gripped by that portion of the machine that moves forward ancl backward on the fourth saw, auto- matically feeding out the blocks as the saw cuts ofi the shingles. 'fhe blocks are placed in the machine so that the saw cuts shingles from the face of the block produced in the quartering operation, thgs producing edge grain shingles. The well-known wedge shaped form of the shingle is obtained by the nrachine first feeding out the top portion of the block further than the bottom on olle forward move- ment and then reversing this on the next.
The machine op€ra,tor,rcalled the "sawyer," removes the shingles as they are crlt (Fig. 5). He squares up the edges and cuts out any interior defects by means of a fifth and last saw. He then completes this part of the work by passing the shingles down a chute to bins on the floor below. Defective shingles go to a.separate.bin, and are not rnixed with the better grades.
"Packers" stationed beside the bins pack the shingles in bundles of standard size, bind thertr, and place ,them on a con.veyor (Fig. 7) which takes the bundles to the dry kiln.
At the en,trance of the kiln the bundles are stacked on trucks and run into the kiln (Fig. 8.;. They'remain in this heated compartment from ten days to two weeks, i.n order that the drying will take place slowly at a temperature of about 180 degrees. Faster drying at high temperatures has the tendency to cause the shingles .to warp or become brittle.
A shrinkage accomipanies the clrying of wood so when the bundles are removed from the kiln they are somewhat loosely held together. They are tightened by being run through a small power press which exerts a pressure on the e,nds of the bundle. This is the final process and the shingles are then ready to be loaded abroad cars or boats for shipment (Fig. 9).
The number of shingles produced in the United States during the year 1920 was over six and one-half millions squares, four-fifths of which amount were manufactured in the State of Washington. These shingles ii laid the correct number of inches to the weather would cover an area of 650,000,000 square feet or 23 square miles.
It will be seen tha't the production of shingles form an important industry. Six thousand men are employed directly in the mills and over $16,000,0C0 is invested in the shingle rl,ills of the P,acific Northwest. The product furnishes 1'early 40.000 cars of freight to the railroads and is shipperl to elery State in the Union.
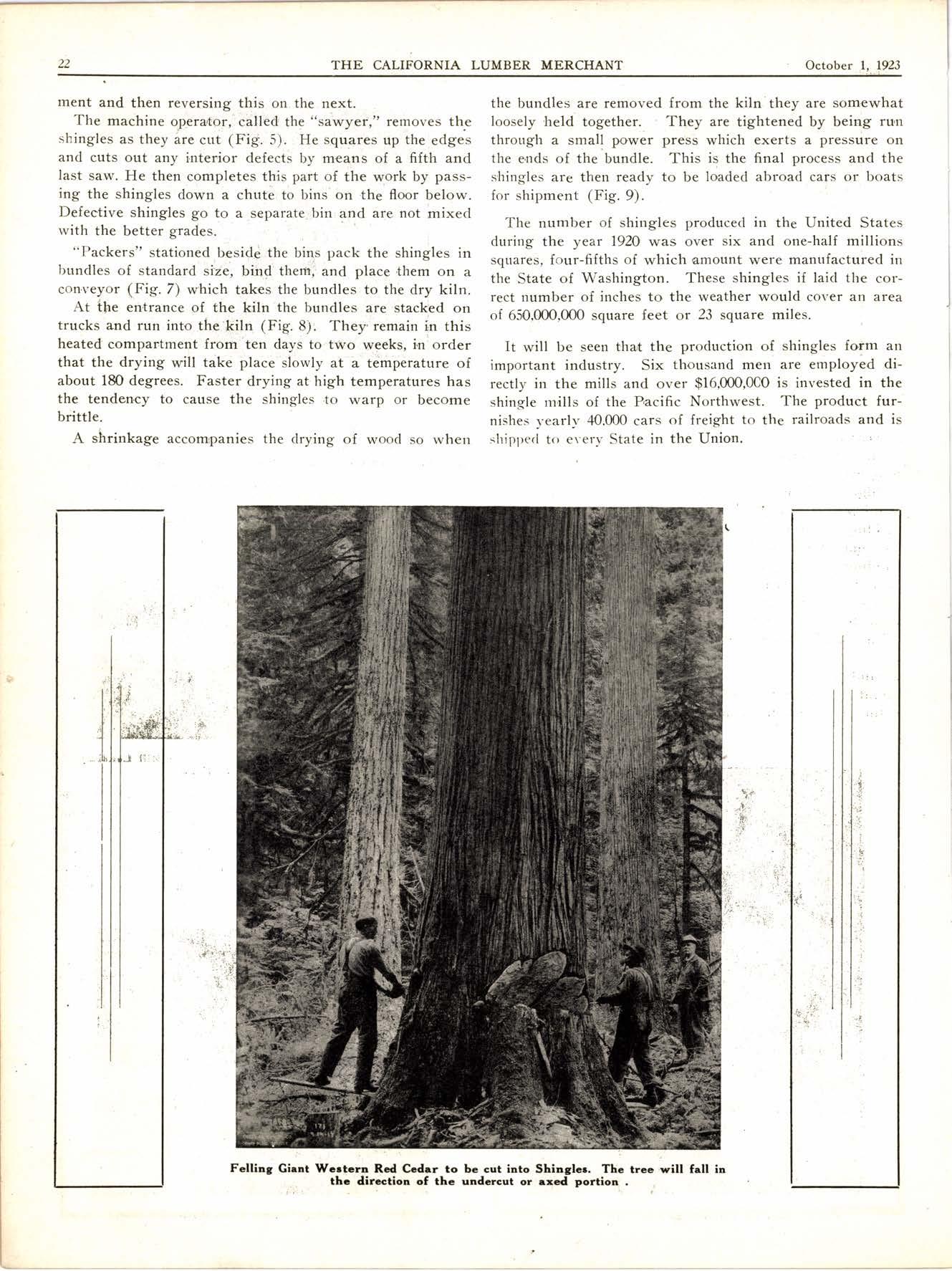