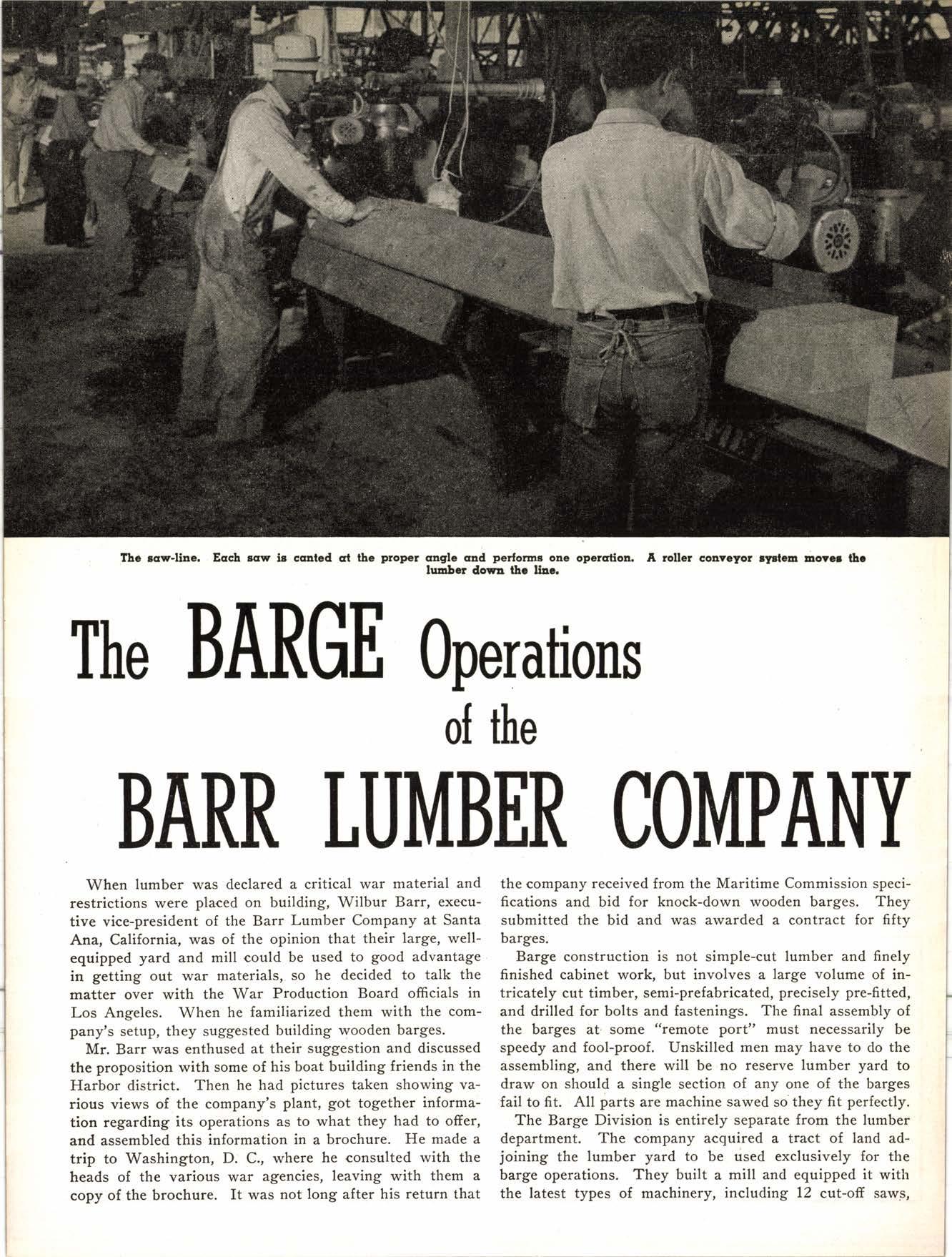
6 minute read
The BARGE Operations of the BARR LUMBER COMPANY
When lumber was declared a critical war material and restrictions were placed on building, Wilbur Barr, executive vice-president of the Barr Lumber Company at Santa Ana, California, was of the opinion that their large, wellequipped yard and mill could be used to good advantage in getting out war materials, so he decided to talk the matter over with the War Production Board officials in Los Angeles. When he familiarized them with the company's setup, they suggested building wooden barges.
Mr. Barr was enthused at their suggestion and discussed the proposition with some of his boat building friends in the Harbor district. Then he had pictures taken showing various views of the company's plant, got together information regarding its operations as to what they had to offer, and assembled this information in a brochure. He made a trip to Washington, D. C., where he consulted with the heads of the various war agencies, leaving with them a copy of the brochure. It was not long after his return that the company received from the Maritime Commission specifications and bid for knock-down wooden barges. They submitted the bid and was awarded a contract for fifty barges.
Barge construction is not simple-cut lumber and finely finished cabinet work, but involves a large volume of intricately cut timber, semi-prefabricated, precisely pre-fitted, and drilled for bolts and fastenings. The final assembly of the barges at. some "remote port" must necessarily be speedy and fool-proof. Unskilled men may have to do the assembling, and there will be no reserve lumber yard to draw on should a single section of any one of the barges fail to fit. All parts are machine sawed so they fit perfectly.
The Barge Division is entirely separate from the lumber department. The company acquired a tract of land adjoining the lumber yard to be used exclusively for the barge operations. They built a mill and equipped it with the latest types of machinery, including 12 cut-off saws, dado machine, band saw, stationary boring machine, heavy duty rip saw, heavy duty cut-ofi saw, electric drills, pneumatic air hammers, etc. The offices are adjacent to the mill.
H. G. Larrick, well known Southern California lumberman and manager of the company's yard at Solana Beach, was called to Santa Ana to manage the Barge Division. William Eckles, who has been superintendent of the company's Santa Ana mill for many years, is superintendent of this division. There are five departments, each one under an experienced supervisor: Frank Runge, gussets; George Telford, miscellaneous fabrication; Sid Babcock, saw and assembly line; John Dohmer, boxes; and Frank Fitzpatrick, loading and unloading crews. LaVerne Knox is purchasing agent; Tom Harper, receiving clerk; Lawrence Van Vliet, shipping clerk, and Mrs. Pauline Allison, office secretary. Eighty-four men, all skilted and experienced, are working specifically on the barges.
Barr Lumber Company has had many years experience in the operation of lumber yards and prefabrication work. To do the barge job, streamline factory methods were adopted, a saw-line set up, assembly tables installed, and new devices of their own were developed to speed the barges to destination.
Actual construction calls for the use of patterns of dozens of various shapes and sizes. In the lofting room, the architect's plans for the barges are translated line by line, angle for angle, to the mold floor. From these full-sized plans, proven for accuracy, templates are made. These patterns, also made from wood, are cut for every piece of lumber going into the barges. Each template shows the various cuts, angles, and markings for drill holes to be followed on the assembly line.
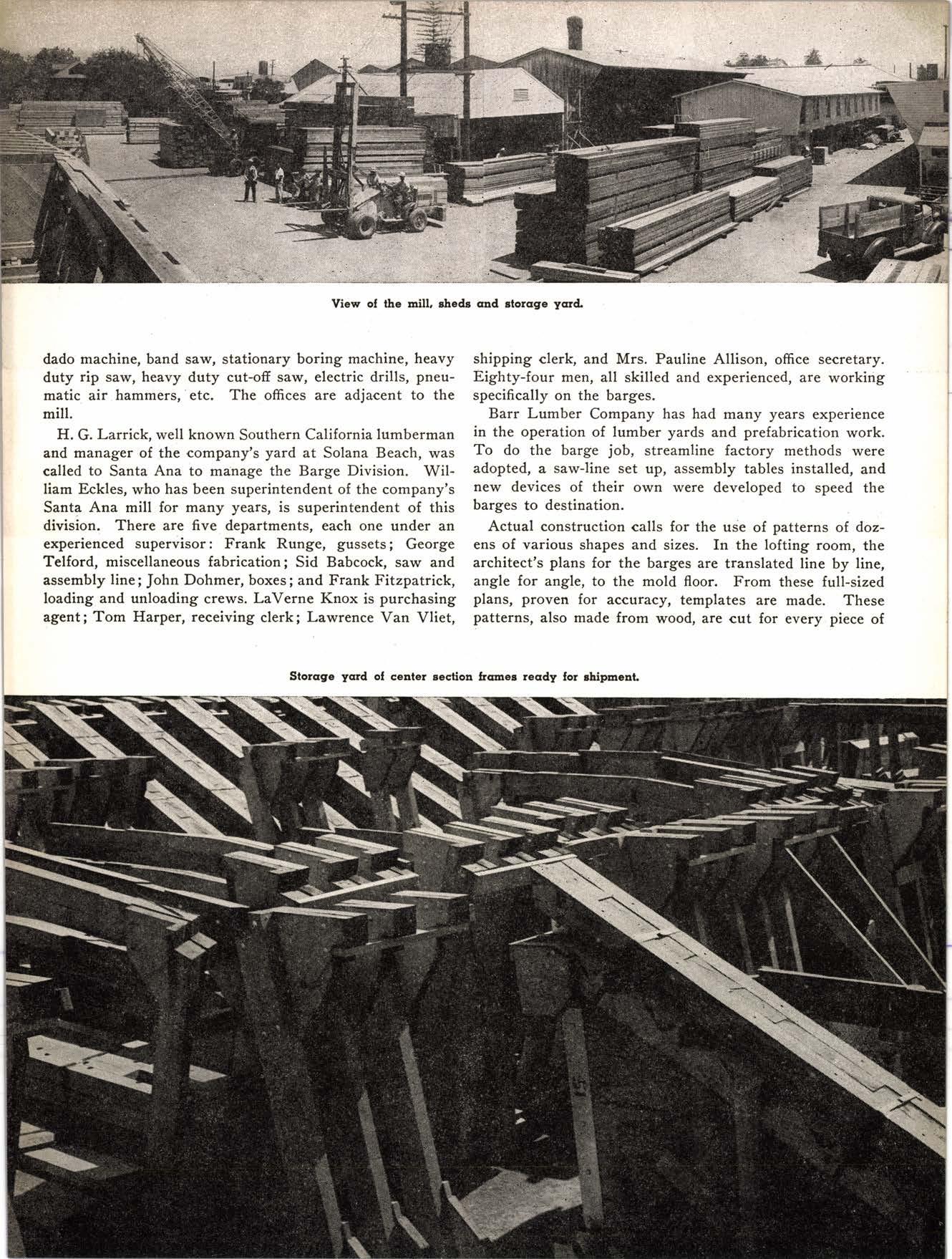
In one corner of the yard., a mock-up, or the model of a full-size actual barge, has been set uP to see that all parts fit perfectly. Each barge must conform to the model. The barges arre 78 feet long, and the hold which has a capacity of 160 tons of cargo, is 54 feet long and 8 feet in depth.
The barges are floating warehouses, and especially useful where there are no port facilities. As they are covered with removable hatches, goods can be stored in them indefinitely.
The actual beginning of the barge construction starts at the saw-line where there are 12 cut-ofi saws, canted at the proper angle, each saw performing one operation to the timber or plank. At the end of the saw-line is the dado machine which cuts a notch for the limber chain. The material coming from the sawline is turned on a simple pivot as it comes from the mill, and rollers convey it to storage in different parts of the yard where it waits until needed in assembly. There are seven acres of yards adjacent to the mill.
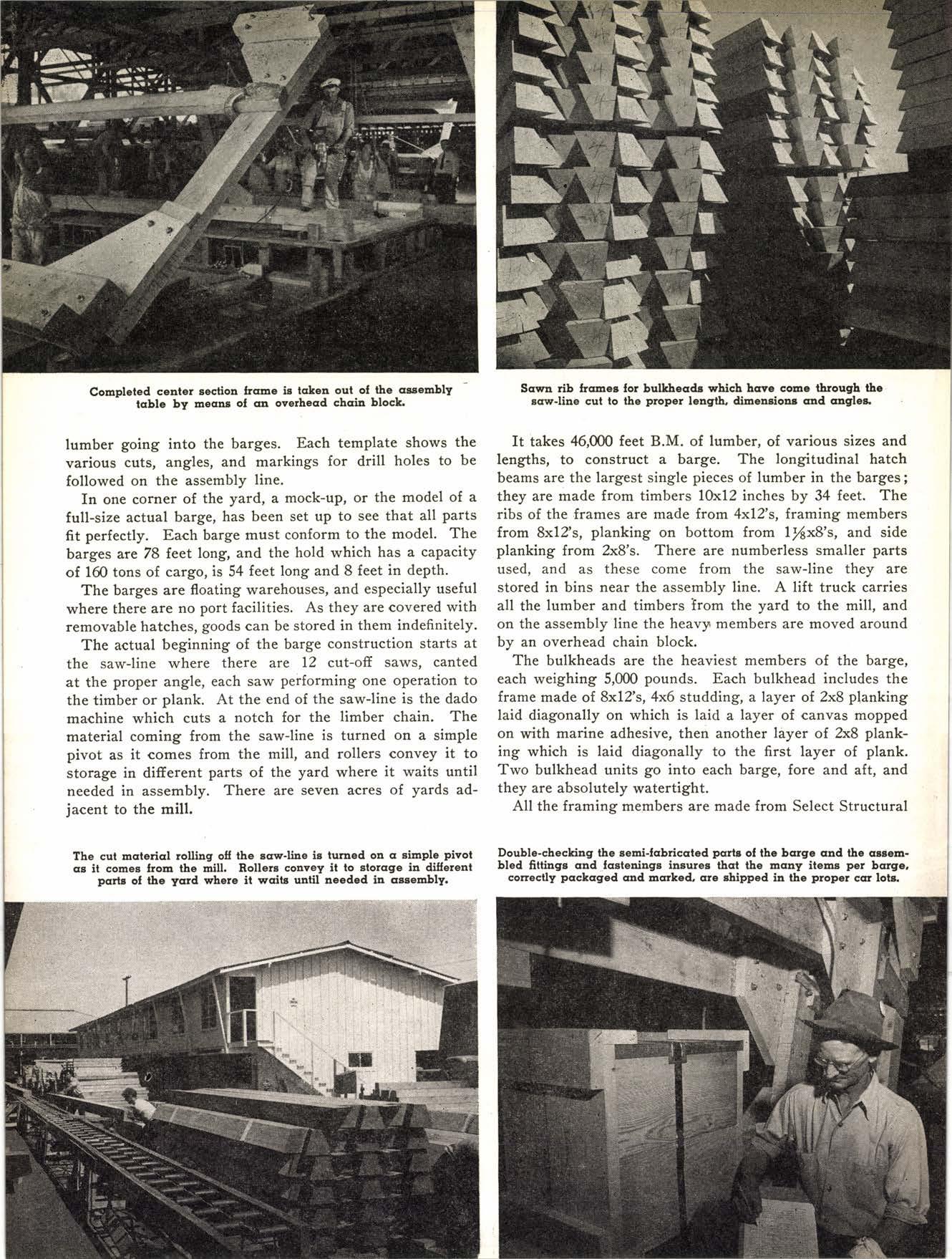
The cut mqtericrl rolling ofl lhe raw-line is turned oa a ainple pivot qr it cones lrom lhe rrill. Bollerr convey it to slorcae in diferenl pcrtr ol the ycnd where it wqitr until aeeded in as:enbly.
It takes 46,000 feet B.M. of lumber, of various sizes and lengths, to construct a barge. The longitudinal hatch beams are the largest single pieces of lumber in the barges; they are made from timbers l0xl2 inches by 34 feet. The ribs of the ,frames are made from 4x12's, framing members from 8x1?s, planking on bottom from l/sx8's, and side planking from 2x8's. There are numberless smaller parts used, and as these come from the saw-line they are stored in bins near the assembly line. A lift truck carries all the lumber and timbers lrom the yard to the mill, and on the assembly line the heavy members are moved around by an overhead chain block.
The bulkheads are the heaviest members of the barge, each weighing 5,000 pounds. Each bulkhead includes the frame made of 8x12's, 4x6 studding, a layer of 2x8 planking laid diagonally on which is laid a layer of canvas mopped on with marine adhesive, then another layer of 2xB planking which is laid diagonally to the first layer of plank. Two bulkhead units go into each barge, fore and aft, and they are absolutely watertight.
All the framing members are made from Select Structural
Douglas Fir, while the planking on the bottom is Clear Vertical Grain Douglas Fir.
The gussets, or ship knees, are made from precut material in the "gusset factory" section of the mill. Laminated with a lfu-inch core and with a /s-inch plywood face on each side, they are run through the glue roller, then stacked in hydraulic presses which the company made specially for this job-where they are left standing for two hours under 25 tons of pressure. These presses are unique as pressure is applied from four opposite directions at the same time, performing three glue operations, side, top and bottom. IJrea resin glue, impervious to water, is used as a binder.
Making the gussets is the most difficult job in the whole operation as they have different kinds of notches cut at various angles. The company built a special saw for this work. There are 22 different types of gussets used which brace the many members that make up the barge.
After the material leaves the mill, the various parts that are used in the barge are assembled. This work is done on the assembling tables. There are three tables for assembling the center section frames; two tables are used to put the short deck beams onto the ribs; two tables for putting together the frames for the bow and stern, and another table to assemble the budget and rider beam. Then there is also a large table for building up the bulkheads.

The final step is the binding of all the parts into packages for shipment. The parts and members, fittings and fastenings, for each barge, are shipped as a unit, and it takes four gondola freight cars to transport each unit from the plant in Santa Ana to the ship which will take it to some "remote port."
. The company sent a man to the United States Forest Service Laboratory at Madison, Wisconsin, to attend a course in crating and boxing to make certain that all parts would be properly packaged. A variety of ingenious packaging devices is used.for the oddly assorted shaped parts and members to be shipped. Three center section ,frames are shipped in one parcel, and they are held together by several pieces of plank that are well nailed. Steel strappings tie the head logs to other frames of the same length, and this bundle will nest in a package of center section frames. Planking for the sides, bottoms, and decks is tied together with steel strapping; most of the bound planks are of uniform lengths, however, every shipment includes two or three packages containing miscellaneous planking of odd lengths. All the equipment used to fit the barges for service is shipped in boxes. There are 52 separate packages for each barge unit. fhc 'Giulet Fcctotl" rcclion ol the -ill.
The barges would be incomplete without the materials, fittings, fastenings and equipment to fit them for service afloat, including such items as paint, waterproofing, adhesive, nuts and bolts, steel bindings, canvas, lanterns, anchor chain, 6CI feet of hawser for mooring, four oars, kegs of nails, shovels, sand-box and buckets for fire fighting, one 285 pound anchor, etc. Like a prefabricated house, each barge is complete to the last detail. It even includes a small cabin, 4x6 feet, with a stove for the watchman.
The company is turning out a eomplete barge every day, and when the present contract is completed will have made 100 barges, and shipped 400 carloads of parts, or 154,000 individual items.
The Barr Lumber Company is doing a fine job, and can feel mighty proud of the part they are taking in the war effort. The officers of the company are: O. H. Barr, president; Wilbur Bair, executive vice-president and general manager; Gilmore Ward, secretary, and Frank l{arrington, treasurer.