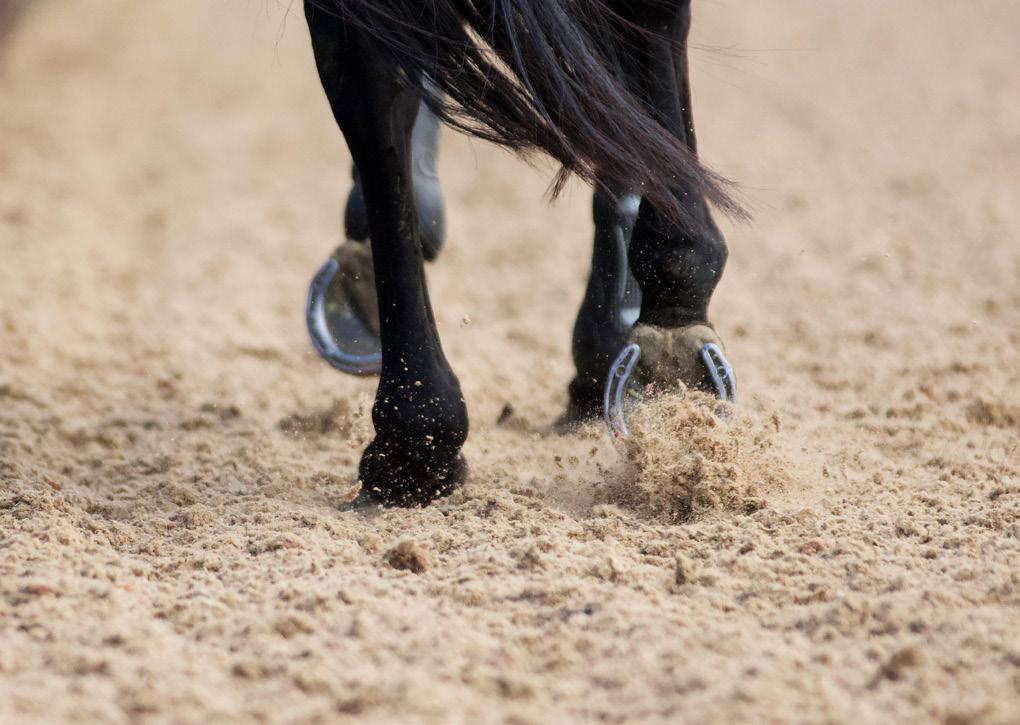
3 minute read
A Burnley carpet, five continents and a determined family business: the story of Equestrian Surfaces
Equestrian Surfaces makes, as you might expect, all-weather equestrian surfaces from their premises on Phoenix Way in Burnley
But what you might not be aware of is how these high-quality surfaces are made. While 95 per cent of the finished product is made from sand, the remainder is made from a special additive that is manufactured on site…and recycled carpets.
Advertisement
Indeed, we were greeted by piles of carpets taken from recycling centres when Luke Wilkinson, Equestrian Surfaces’ finance manager, showed us around.
“The carpets are processed and they turn into a fine texture and this goes into our surfaces. Our method saves around 6-7,000 tonnes of carpet going to waste every year and we’ve won green awards for this,” Luke explained.
In fact, one carpet thrown away in
Burnley could find itself on any of five continents across the world, with the family business shipping their finished products globally. Contracts include the Liverpool International Horse Show, the Sunshine Coast Turf Club in Australia and the Hollywood Park Racetrack in the USA, to name but a few.
One recent client win was the World Clydesdale Show 2022, which was held for the first time ever in the UK, all the way up in Aberdeen. They were tasked with supplying over 1,000 tonnes of their signature Cushion Track™ surface to the P&J Live Arena whilst constructing and installing two arenas. The main arena was an impressive 76m x 43m in size, whilst the second was a smaller collecting ring, 18m x 25m in size – both complete with perimeter fencing and approximate 1,700sqm of rubber walkways.
“We were given full confirmation that we had received the contract six weeks before the show! Of course, we’d already been doing preparations in the background so we weren’t on the backfoot. Once we arrived in Aberdeen, we had 40 hours to install everything (this usually takes up to seven days!) and then were given 24 hours to remove it all once the show ended. We managed it within 23 hours when it normally takes three days. This just shows how hard everyone worked,” operations coordinator Holly Lund told us.
The Equestrian Surfaces team also had to make sure they didn’t damage the arena’s polished concrete floor and had to protect the electrical ducting from the irrigation process. The heavy traffic of the competing Clydesdale horses, as well as spectators, meant the team regularly maintained the surfaces throughout the day, as well as graded equestrian equipment, which they also manufacture.
A family business with full-team effort
It’s clear the team are proud of pulling off such a huge project within tight timescales and you get a sense of the pride the staff have at Equestrian Surfaces.

The business was started in 1986 by Paul and Rita Harper, who have a farming background. They originally ran it from their home in Pendle, before moving into a facility in Padiham, before buying their current home on Phoenix Way in 2007. Today, the business employs 20 staff. Sadly, Paul passed away in 2015 and Rita is recently retired, with their sons James (managing director) and Thomas (sales director) heading up the company. Luke is their cousin, whilst Janet (Rita’s sister) still works in sales and has done since day one. Thomas and James’s aunty, Carol, works as an admin executive, whilst her husband and Thomas and James’s uncle, Frank, works on production.
Frank’s son Ryan works in fabrication.
“It can be a bit stressful working with family, you’re often expected to do more than you normally would do, but of course you’re happy to go that extra mile for family. Rita has so much passion for the business, and we all want to do her proud,” Luke said.
They’re also passionate about keeping the team as local as possible. All employees are from the area, and they take on Burnley College apprentices. Luke himself was a Themis finance apprentice, the operations manager is also currently studying for a Chartered Manager degree apprenticeship, whilst Holly is on a project management course at the college.
“We love working in our hometown – there are some incredible Burnley businesses and we’re delighted to announce that we have joined the Burnley Bondholders so we can connect with others and find out more about what’s happening here and how we can partner with and support others,” Luke added.
So, next time you throw out a carpet, it could very well end up in a Burnleymade high-end equestrian surface that’s installed somewhere across the world.

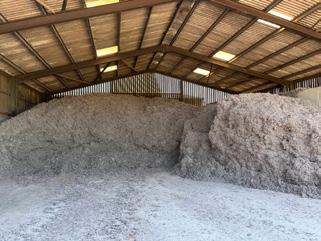