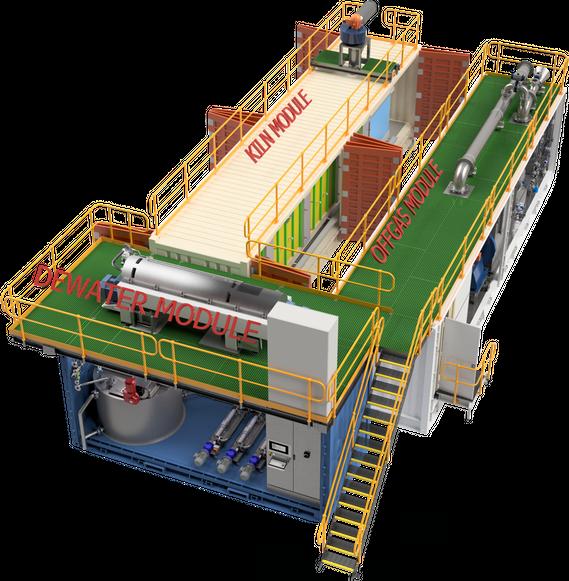
5 minute read
Adelaide Control Engineering
A.C.E
A 3D render of ACE’s Complete Modular Process Plant
Resources Feature
Expert Consultants in the Uranium Industry
Adelaide Control Engineering (ACE) was born in 1999 with a simple goal: making uranium mining safer and more cost effective.
However, since its inception the company has grown from its base in southern Australia to help companies in Europe, the US, Canada, Africa, and even Kazakhstan with equipment and engineering services. Now working as a multidisciplinary consultancy offering everything from design to project management and construction, ACE is continuing to help clients get uranium out of the ground for a lower cost.
But success was far from guaranteed for ACE. At the turn of the 21st century, ACE was working with Heathgate Resources to build the Beverly Uranium Mine in South Australia. ACE took care of the drying and drum packaging plant, as well as assisting with commissioning and start-up of the operation.
“In 1999 the, uranium price was only $15 per pound,” explains CEO Glenn Jobling. “That’s why no new uranium mines had been built in a long time. Unfortunately, the price didn’t increase due to stockpiled Russian uranium coming onto the market following the end of the Soviet Union.” As a result, ACE didn’t work on another uranium mine until 2007. But, thanks to its previous experience building drying and drum packaging plants, ACE had an ace up its sleeve – it had the know-how that very few companies could match allowing it to win the contract for the Langer Heinrich Mine in Namibia for Paladin Energy. Since then, under Jobling’s leadership, ACE has grown and expanded its operations to encompass a range of different services and products to help companies mine uranium. Perhaps the jewel in the crown is ACE’s Modular System, a proprietary technology that ensures the safe and efficient extraction of uranium.
ACE built its first modular plant in 2010 when it teamed up with Urtek LLC to design a process to extract uranium from phosphate. Phosphate deposits are often associated with large concentrations of uranium and this process was to decontaminate the phosphate ore used in fertiliser production and to also provide a saleable uranium by-product. The plant was constructed in a modular form allowing it to be easily transported and allowing the technology to be tested on different phosphate deposits around the world to ensure the process was robust.
“That’s how we got into building modular plants,” explains Jobling. “We realised that building modular plants could significantly lower our capital costs.”
“Most uranium mines are found in developing countries in very remote locations where component availability is limited and technical skill level is often low,” says Jobling. “This makes building the technically specialised plants on the ground very expensive and time consuming. Our modular plants, however, can be built and fully tested in our workshop, then transported to the mine with only minimal work required on-site to install and commission. Our engineering and manufacturing times are significantly reduced thereby lowering costs and allowing us to bring more advanced engineering to the mines.”
Resources Feature
“Some other important advantages are that it gives us the ability to quote firm price, delivery and startup dates to the client, which comes with some risk for site constructed plants,” says Jobling.
The modular system are designed with Category 4 safety systems that feature a single, all-encompassing kill switch designed to maximise plant utilisation through equipment availability. “Instead of an operator having to find an electrician to isolate the motors, turn off the valves, and lock all the machinery before doing routine task inside the module, they can simply flip the kill switch and have it all happen automatically,” Jobling says. “This makes the process faster and easier – as well as removing the risk of human error.”
The current issues with the Covid-19 virus and the conflict in Europe are posing many hurdles for manufacturers to overcome in order to meet contractual arrangements and expected delivery. Delays due to extended lead times for overseas components means that detailed engineering needs to be completed so that orders can be placed early, and the same applies to materials with prices increasing sharply. These issues favour delivery of ACE modular plants ahead of other options.
Despite being one of the most established and longstanding businesses in the uranium sector, ACE is not standing still, nor resting on its laurels. Constant improvement, according to Jobling, was, and remains, integral to the business’ success.
“Throughout our involvement in uranium projects, we have been astounded by the lack of innovation – particularly in those processes undertaken by the larger engineering houses,” he says. “Sometimes the process flowsheets, for example, are simply copied from one project to another with very little effort put into refinement and innovation, despite the chance to save significant amounts in operating costs over the course of the mine’s life – it’s perplexing.”
“It’s essential to advise your clients about better technologies, as well as quantifying and communicating the benefits of informed decision making. We always aim to provide our clients with the best, most cost-effective solution in the shortest timeframe possible.”
ACE is also the only company in the world licensed to use fluid bed precipitation technology originally developed by Areva and now owned by Orano. “The fluid bed technology produces larger crystals which makes the dewatering, calcining, drying and drum packing more efficient, so putting Orano’s fluid bed precipitation technology in front of our modular technology made every other module perform better and deliver a higher throughput and lower operating costs,” he explains.
So, with an enduring spirit for innovation and improvement, ACE is already eyeing the next opportunities in the uranium market.
“Right now, we have modules at the front end for in-situ mine leaching, as well as the modules at the back for precipitation, drying and drum packaging,” says Jobling. “We’re building more modules in the middle, including one for ion exchange, so we can further simplify our plants and minimise costs for our clients.”
“We are also working on pilot plant modular designs for other minerals including graphite and lithium where we can assist our clients by de-risking new mines – and there’s some innovation that I can’t yet talk about! We’re very busy working in the background and moving the business forward.”
It might have been in operation for almost half a century but, with nuclear power likely to play a larger role in power generation around the world, as well as potential trade embargoes on Russian-produced uranium, the coming years could be the company’s most fruitful yet.
www.adelaidecontrolengineering.com
A.C.E
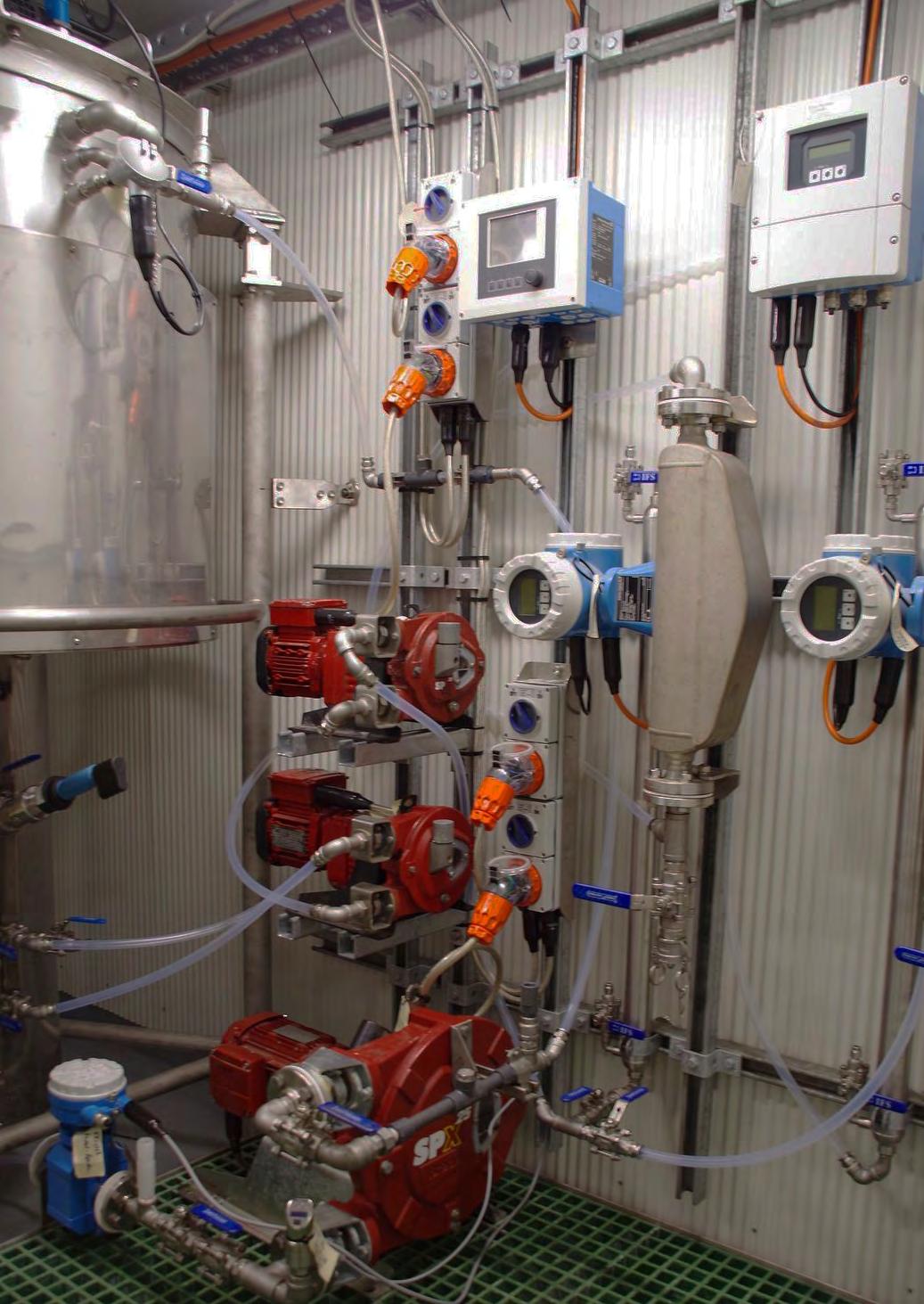
Plant testing using ACE’s new precipitation technology