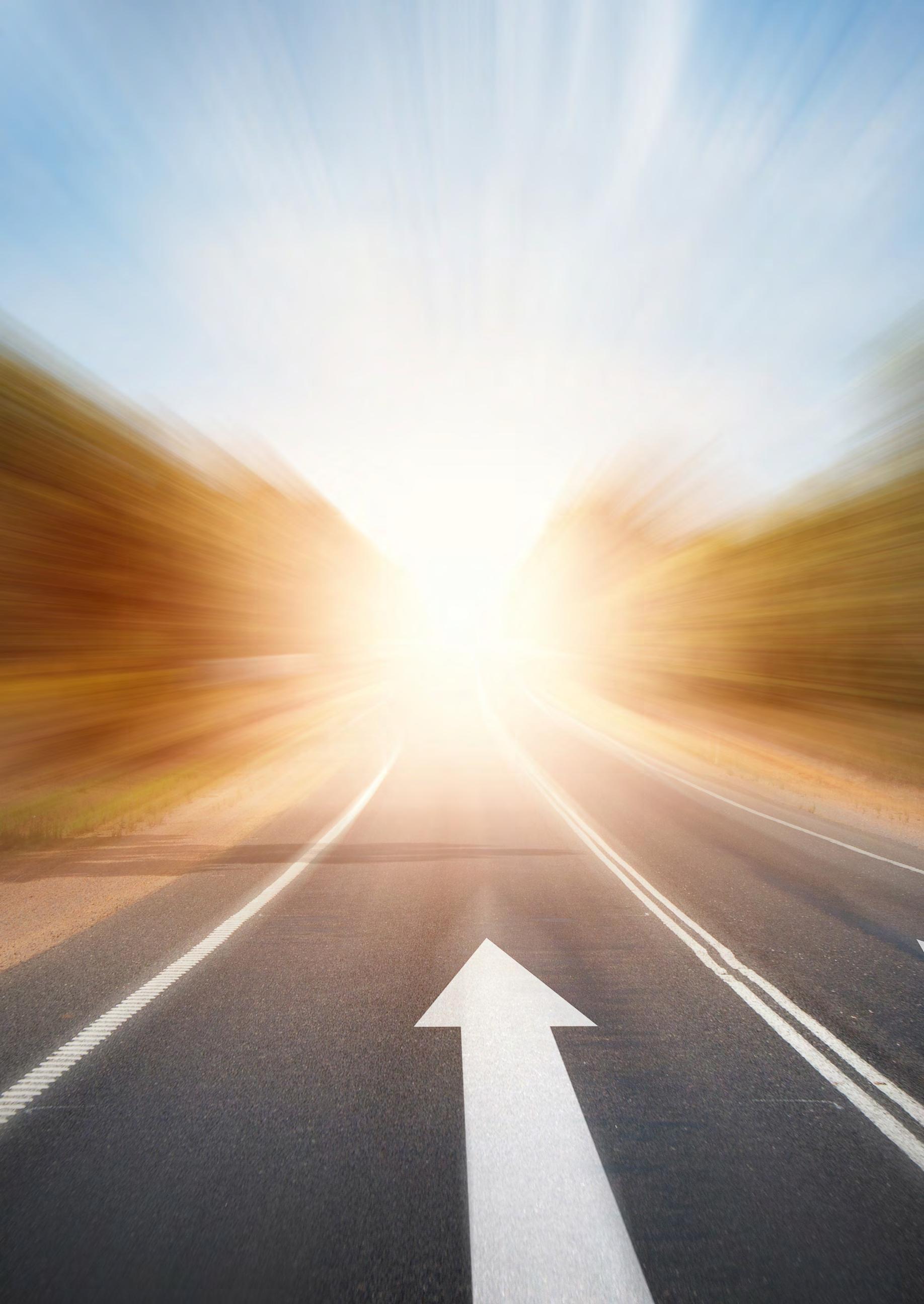
6 minute read
Altilium Group
PROJECT DIRECTED BY Jamie Waite
WRITTEN BY Romana Moares
Christopher Gower, CEO, Altilium Group

Fuelling the Future
UK-headquartered Altilium Group is set to take an active part in the global transition to electric vehicles, providing several of the key metals needed by the industry, generated in an environmentally friendly manner that will help local communities.
As demand for electric vehicles (EVs) increases, so will demand for the metals needed to manufacture lithium-ion batteries, especially nickel. UK-headquartered Altilium Group may provide an answer to this increased demand with its unique metal extraction process.
Although the company was established in the UK in 2019, its operating business has a much longer heritage, dating back to 2008 when it initially acquired the rights to the ground-breaking DNi Process™ - a revolutionary and patented technology that extracts valuable metals and co-products without leaving a harmful legacy, to help realise the sustainable, responsible and efficient use of the world’s resources.
Sharing a vision
Chris Gower, Chief Executive of Altilium Group Ltd., explains that the original patent was developed in the US by a talented chemical engineer who cracked the one problem that the industry had not resolved – how to recycle nitric acid, the most efficient acid for dissolving metals in ore. In the early stages of development, the company worked closely with Australia’s respected Commonwealth Scientific and Industrial Research Organisation (CSIRO), testing the process at a pilot plant in Perth, Australia. The testing, completed in 2014, delivered highly successful and encouraging results.
In 2016 the ownership of the company with the rights to the process changed, which is when Chris Gower came in as CEO. He himself has had ample experience of international undertakings, and, amongst others, led a team to implement one of the world’s largest environmental remediation projects.
Today, Altilium Group has several offices and facilities around the world, employing a mixture of nationalities and talents. Chris says: “I have been very lucky in terms of having the right team of people with a range of skills, dedicated to our common goal. We are a small team of people that get on very well. We share the same vision which is to fuel the future of greener motoring in a commercially viable way. With a shared vision, management is easy,” he affirms.
Altilium Group
A unique process
Chris explains that the DNi Process™ is a novel, patent-protected method for extracting nickel, cobalt and the other constituent metals contained in laterite ore. “The DNi Process™ utilises a nitric acid leach under atmospheric conditions. Ensuring the sustainability of natural resources, our process maximises extraction, minimises cost, minimises residue and realises the full polymetallic value in earth’s lateritic resources.”
“The DNi Process™ can process even low-grade ore. We can do this profitably because our technology extracts all the available metals in the ore. This could at least double the world’s estimated nickel reserves. And, with more saleable products, the process will generate more revenue. Technically efficient and environmentally sensitive, our game-changing technology will revolutionise the way that MHP is produced for the EV battery industry.”
He further points out that the DNi Process™ is the only method of generating battery-grade MHP while minimising the environmental impact. “Its unique feature is the ability to process the entire laterite profile. This is a zero-waste operation – the residue that we do produce contains trace amounts of magnesium nitrate which acts as a fertiliser. This means that residue can be returned to the mine to help with revegetation. Replenishing the earth, restoring the natural balance.”
battery industry “
Research is also under way to discover how the residue can be used to create other beneficial products, creating yet more value and supporting the circular economy. To this end, last year Altilium entered into a partnership with the Spanish company RUMBO 5 CERO SL with the aim of converting 300 million metric tonnes of toxic mine waste into a zero-residue mint.
Altilium Group’s revolutionary DNi Process Flowchart
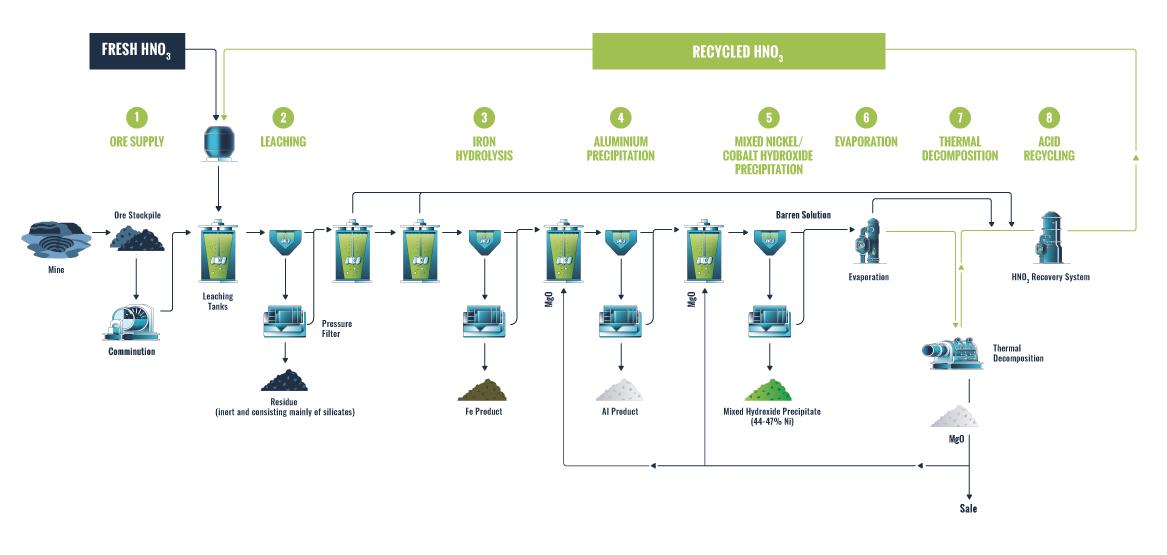
Technology Feature
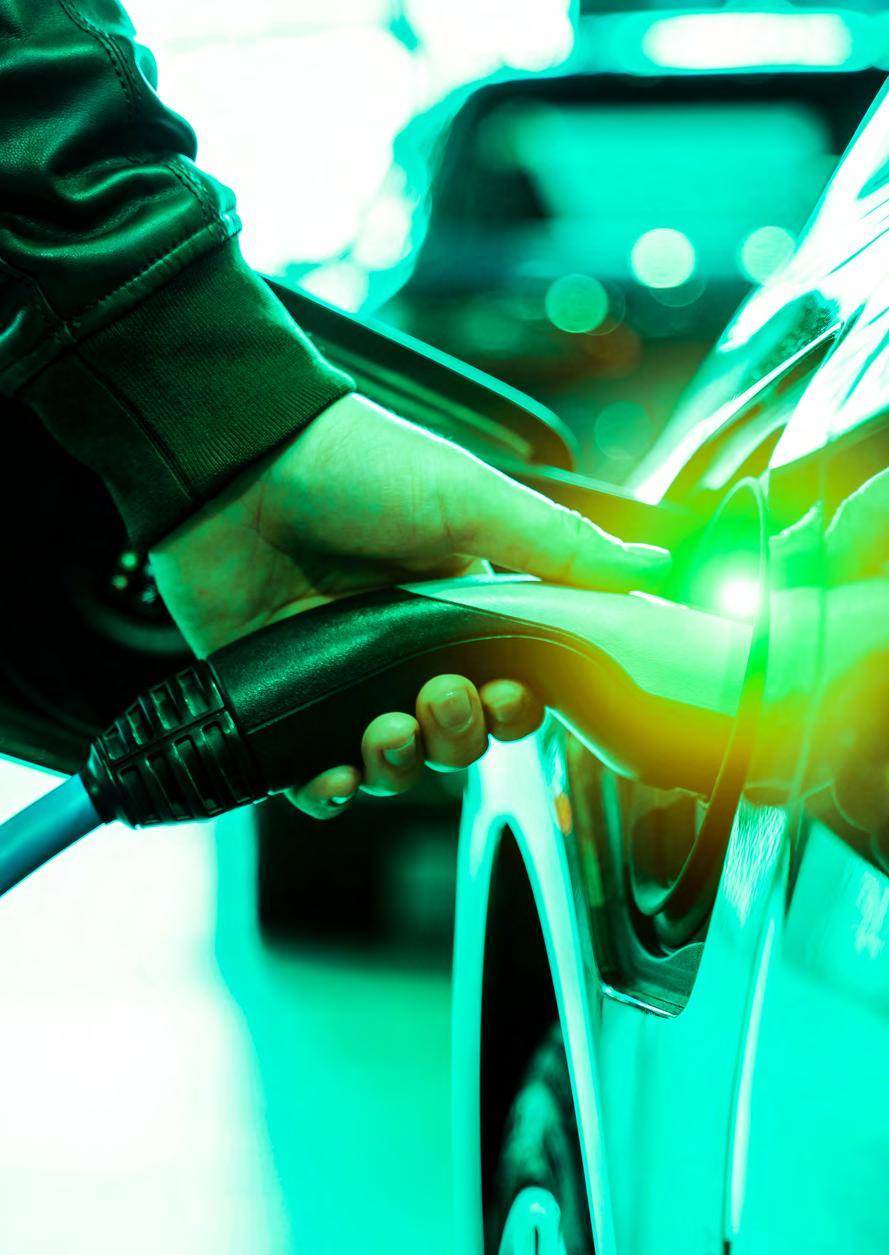
Technology Feature

Altilium Group
Local benefit
While the company’s activities are spread globally, Chris is firmly set in Indonesia. “My personal goal is to develop the operation here in Indonesia. Indonesia holds the world’s largest nickel reserves and the country will be a major exporter of nickel because of both the sheer volume and the high grades of ore.”
“Production targets for the vehicles have been set for 2025 and the relevant stakeholders are aware that securing the necessary metals is now a priority. China controls much of the world’s supply but I personally believe that there is a real opportunity for countries like Indonesia to develop direct relationships with British, European and North American entities - be it giga factories or electric vehicle manufacturers - and supply them directly,” he says.
“Full commercialisation of the process will bring real benefits to Indonesia in terms of developing the local economy, and I really want to see this in each country we work in – the country should benefit from the value of its resources, and this is something I’m very passionate about.” And the development of local benefit has already started. Altilium Group has recently signed an agreement with PT Indo Mineral Research, a member of the Sebuku Group, one of Indonesia’s largest mining groups, to co-operate in the development and promotion of the DNi Process™ in Indonesia. The two companies have agreed to commit financial, technical and logistical resources to accelerating the adoption of the DNi Process™ and to play a key role in the EV battery supply chain.
“
Chris Gower comments: “We are very excited to take this first major step forward with the Sebuku Group. Together, we will help make Indonesia the premier producer of cleaner nickel and other metals which are needed to enable the mass adoption of EVs. There is a premium to be had for people involved in this industry. My personal target is to have at least one plant operating here in Indonesia, a commercial plant by 2024.”

Altilium Group
Sustainable value
Altilium Group is now licensing the process, with the first success already achieved: Queensland Pacific Metals (QPM) was the first company to sign a licence in 2021 for the DNi Process™ to be used in its plant designed in Australia that is set to deliver at least 16,000 tonnes of nickel in MHP.
The plant, called the ‘TECH Project’ and fully owned by QPM, will be an advanced, modern and sustainable producer of critical chemicals for the emerging lithium-ion battery and electric vehicle sector. In December 2021 QPM raised additional substantial funding and expect to complete their feasibility study by early 2022. Construction is expected to commence in April 2022, with a plan to start operations in 2024. While current focus is on nickel production, the process has a much wider potential application, offering significant opportunities for other industries as well. “It is simple chemistry but it is elegant chemistry. As a result of that, we have recently completed test work, focusing on re-processing tailings from previous processes to extract the metals,” says Chris.
“We are also looking at other ores. Testing on Spanish mining samples confirmed our DNi Process™ achieved good recoveries for gold, silver, copper, and iron along with an inert reusable residue. The key point is that our innovative, patented technology delivers valuable metals without costing the earth.”
www.altiliumgroup.com
Technology Feature
