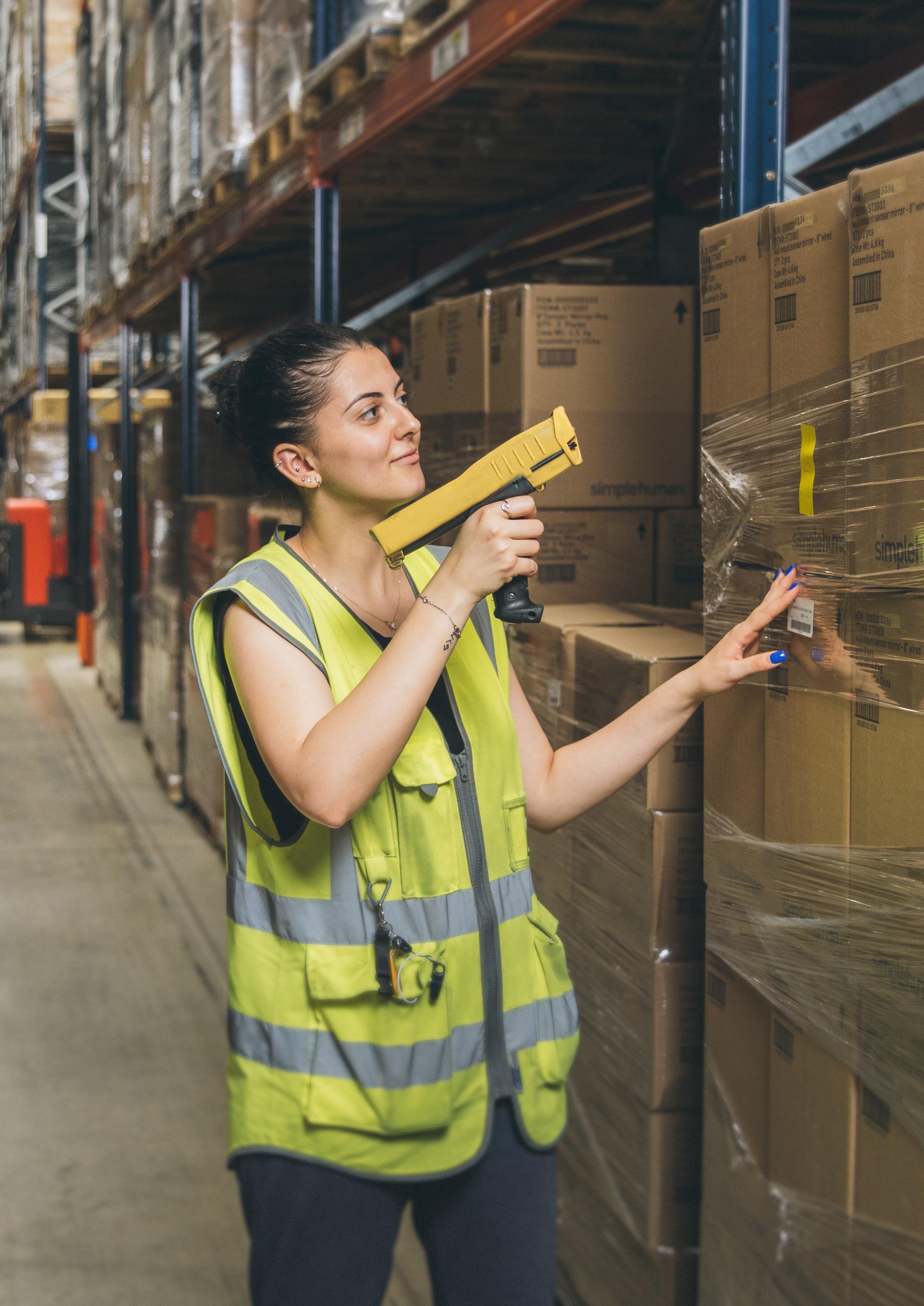
INNOVATIVE SOFTWARE OFFERING THE FULL PACKAGE TO FULFILMENT

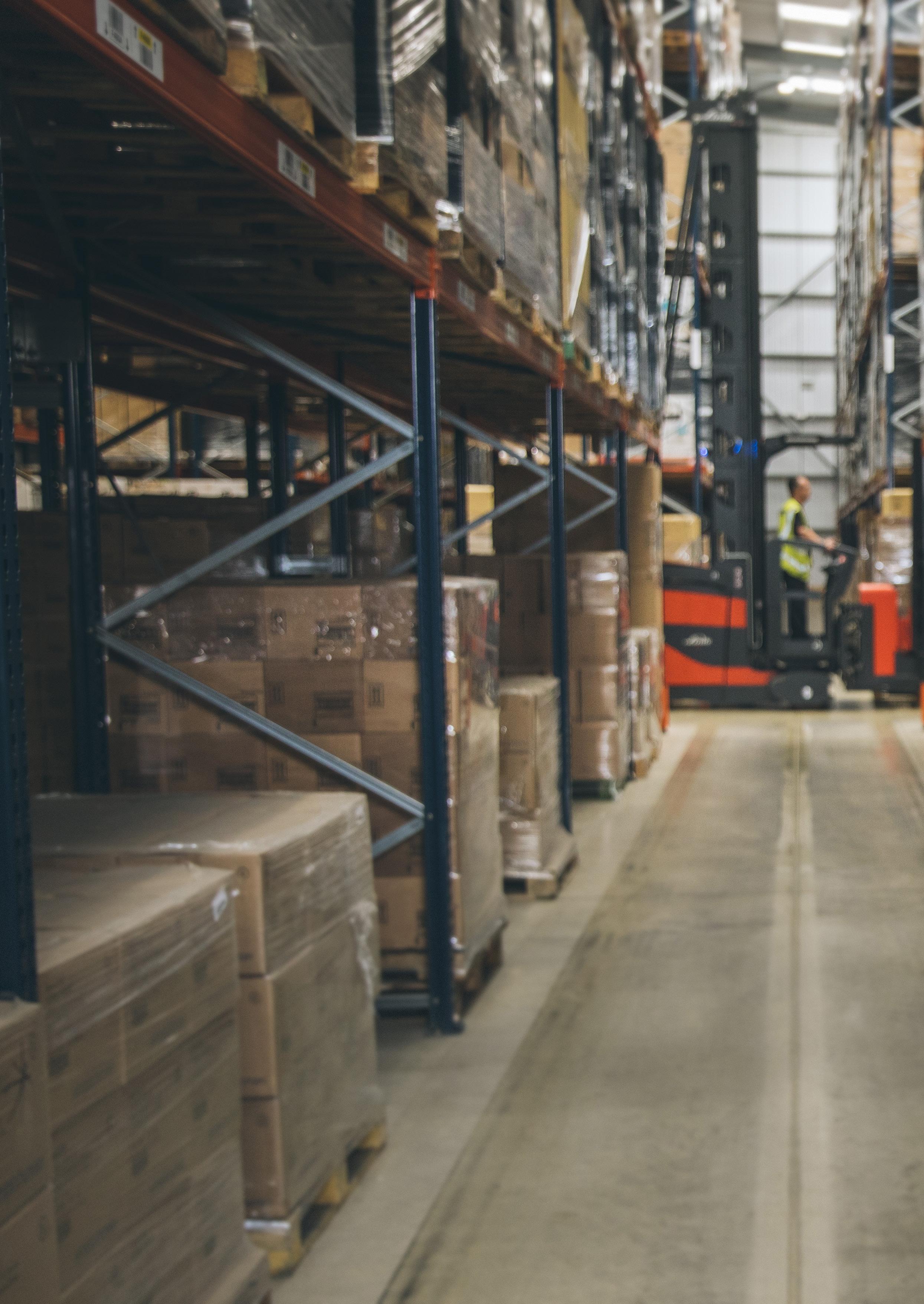
Providing a suite of warehouse management systems, Synergy Logistics has become synonymous as a leader within its space.
SNAPFULFIL
PROJECT
DIRECTED BY: JAMIE WAITE
ARTICLE WRITTEN BY: LAURA WATLING
For more than 50 years, its technology has powered the warehousing operations of some of the world’s most successful companies, such as 3PL, Huhtumaki, SSE, and Vax.
Within Synergy Logistics’ portfolio of solutions, SnapFulfil is a cloud-based, Tier 1 warehouse management system (WMS) with flexibility at its core.
Keeping customer’s needs at the heart of its strategy, SnapFulfil delivers cutting edge technology at a fraction of the cost of traditional installations, saves valuable down-time, offers a rapid return on investment, and evolves to meet the ever-changing demand of warehousing and logistics needs.
SnapFulfil enables its variety of customers to implement automated, system driven fulfilment into their warehouses, reducing errors and enhancing order accuracy. In addition, SnapFulfil’s technology enables faster order processing and offers a flexible rules engine to assist its customers in using the WMS to its full potential.
Chief Product and Delivery Officer for SnapFulfil, Smitha Raphael, discussed with Business Enquirer the many benefits of implementing SnapFulfil into your fulfilment centre. Why should businesses implement automated, system-driven fulfilment?
“The greatest gain from transitioning away from a manual paper picking process to an automated, system-driven solution is efficiency, which ultimately saves businesses money,” explains Smitha.
The software integrates with Enterprise Resource Planning (ERP) systems, shopping carts, carriers and more, updating inventory and order status information in real time and providing a ‘single version of the truth’ across all critical business systems and sales channels.
“SnapFulfil’s accurate reporting allows staff to view their low stock versus their order level, as well as monitor seasonal trends. In turn, this prevents back orders and order cancellations, improving customer perception and satisfaction,” shared Smitha.
SnapFulfil’s implementation into Vax saw the appliance manufacturer realise a wide range of improvements across its omnichannel business.
In line with its objectives, the company required a WMS which could be implemented efficiently without substantial IT resource requirements, had simple interfacing capabilities and which didn’t require a significant capital outlay.
Amongst the results, it saw an increased number of despatches with no increase in labour and decreased indirect costs
resulting from pick errors and product returns. In turn, this improved customer service across all channels.
It also found improved space utilisation and improved inventory control, including goods received pallet identification and shipping container management.
The impact of the implementation of SnapFulfil into Vax has also provided the business with scalability for future business growth.
Further, SnapFulfil’s WMS allows for barcode verification, ultimately leaving no margin for error. The solution triggers inventory audits, offers packing and shipping station verification, and provides cycle counts whilst picking.
“Our software reduces the need for inventory related down-time,” added Smitha. With Smitha and her team continually evolving SnapFulfil to meet
customer’s requirements, new features are frequently being added.
“Additionally, our WMS can integrate with warehouse robotics. SnapFulfil effectively works alongside Synergy Logistics’ SnapControl, a multiagent orchestration platform (MAO) that provides a device agnostic, unified approach to automation. The sky really is the limit with our solutions,” said Smitha.
A key strength of implementing SnapFulfil into a warehouse is its “order grouping” functionality, which can be set to different picking rules to increase efficiency.
“Our WMS also integrates automatic label printing which can be done at the end of picking or packing to suit the business needs,” explained Smitha.
Working with SnapFulfil’s team, Moran Logistics, experts in multi-temperature controlled transport and warehousing, saw almost immediate results after a swift three week implementation.
With multiple picking and packing options made available to the logistics firm, production output quickly and efficiently ramped up four-fold, from an initial 10,000 cases per day to around 40,000. Now well embedded into Moran Logistics’ operations, it has experienced a further increase to between 75-88,000 cases in a 24-hour period.
“A key focus for our Product Development is ensuring that our product is flexible for our customers, no matter their operation,” shared Smitha, “We work closely across the business, with the Support team, Delivery team, Account Management and Customer Success, to ensure our customers feedback is actioned and that we are successfully meeting their individual needs and expectations.”
SnapFulfil’s innovative technology and customer-centred approach to software integration has seen Synergy Logistics positioned in the Gartner® Magic Quadrant™ for WMS for the 12th year (May 2024).
Of the eight “niche” vendors identified for 2024, Synergy Logistics was the closest towards the ‘visionary’ quadrant axis. Its robust and flexible rules engine, which allows for high levels of noncode adaptability to support customerspecific and vertical-industry-specific requirements was highlighted.
“The recognition from Gartner adds further authority to SnapFulfil and demonstrates our ongoing commitment to deliver a technologically advanced system where customers can enjoy swift
and agile deployment, and a rapid return on investment,” said Smitha.
But whilst industry recognition such as being listed within Inbound Logistics’ Top 100 IT Providers, and Technical Project Manager (Synergy North America Inc.), Charles Thompson, being named a winner in Supply & Demand Chain Executive’s 2024 Pros to Know award, the proof of SnapFulfil’s success is in its customer’s numbers.
The 43-day implementation and integration of SnapFulfil with The Topps Company’s (known for its series of trading cards) Oracle ERP has led to a significant increase in operational efficiency, with its five operatives more than doubling its shipping from 500 orders per day to between 1,200-1,800 orders per day.
Considered one of the most successful projects completed by Topps, it also saw the business save $200,000 in the first quarter of SnapFulfil’s integration.
Additionally, as a direct result of implementing SnapFulfil, energy company SSE experienced immediate and significant efficiency improvements, which included order fulfilment improving from less than 90% to more than 98%, pick lines per hour per full time employee increasing from 13 to 19 and staffing levels reducing by 15%.
“There are a number of steps I believe businesses in the fulfilment industry should be taking to improve their operational efficiency and OpEx, this includes prompt order delivery, inventory accuracy and real-time visibility, and automation. SnapFulfil is proven to support businesses in all of these areas and we will continue to develop the software to meet ever-changing needs,” finalised Smitha.
www.snapfulfil.com
www.synergy-logistics.com