Same High Standards at Wood
by RennayAlberta was built on the strength of its natural resources, and over the last few years, three legacy companies in that sector have amalgamated to create Wood Canada, a powerhouse that is forging a path as the premiere Engineering, Procurement and Construction (EPC) service provider in Western Canada.
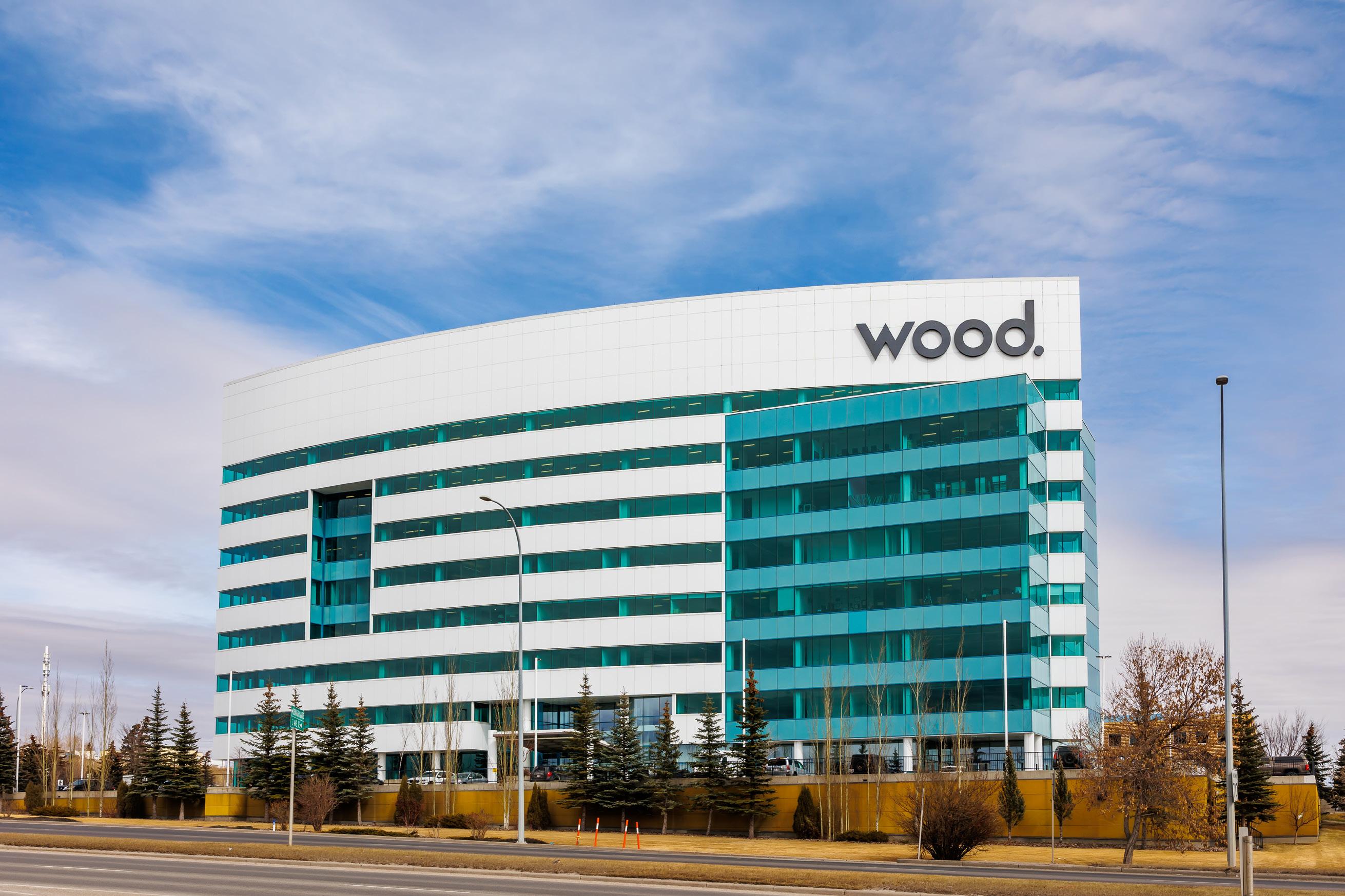
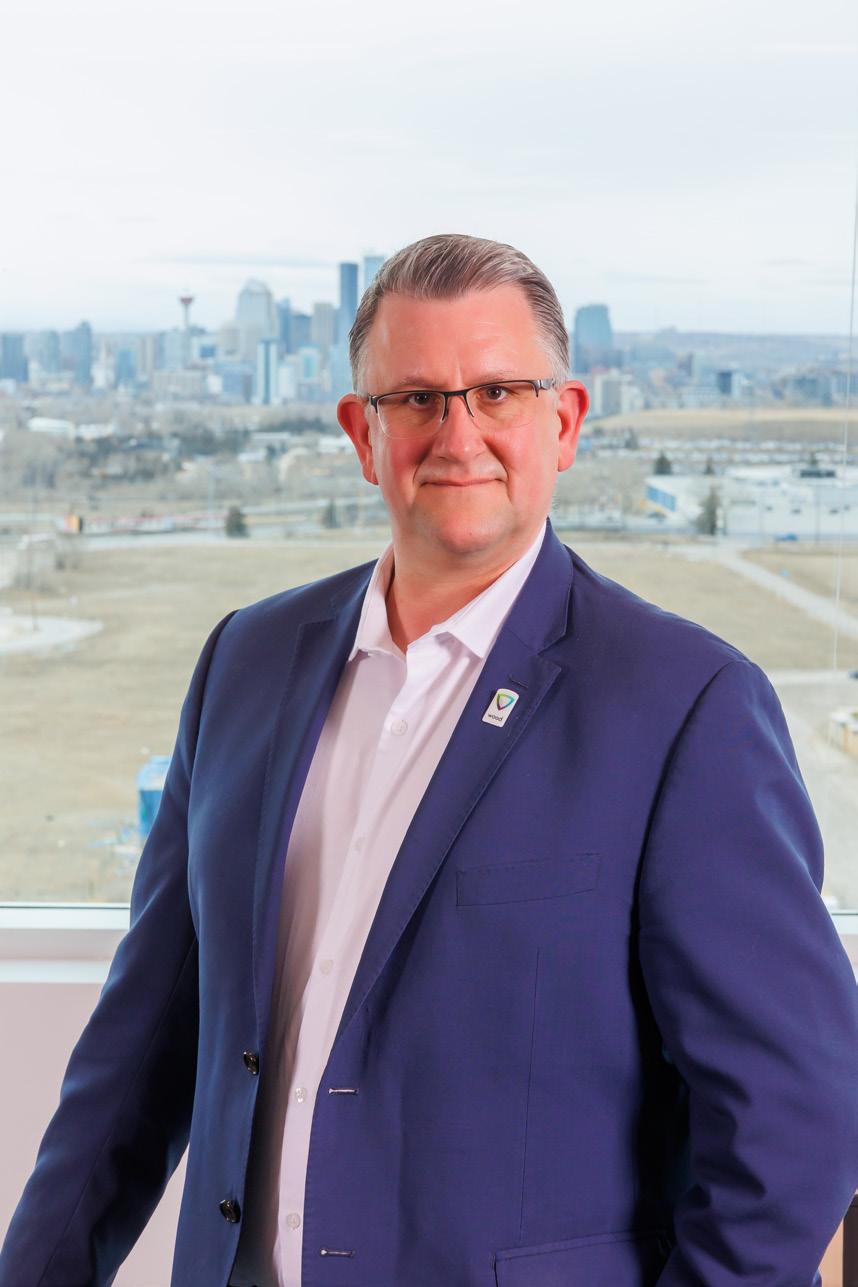
“Amec purchased Foster Wheeler to make an integrated upstream and downstream business and then Wood Group saw an opportunity and purchased the two to create that combined upstream, midstream and downstream business with a global footprint,” says Jason Westrup, vice president of oil and gas, Canada, at Wood.

CONGRATULATIONS
The result is an impressive full-service organization that draws on the Wood network of 37,000 employees across more than 60 countries to provide quality solutions to its oil and gas clients. As an integrated EPC firm specializing in oil sands, petrochemicals and refining, pipelines, carbon capture, hydrogen, mining and biofuels, Wood can not only engineer greenfield and brownfield facilities but also procure the necessary materials and equipment and execute the design in the field. Unlike many EPC companies, Wood has an experienced construction arm in Leduc that creates a one-stop shop for clients as they take a project from conception through to operation.
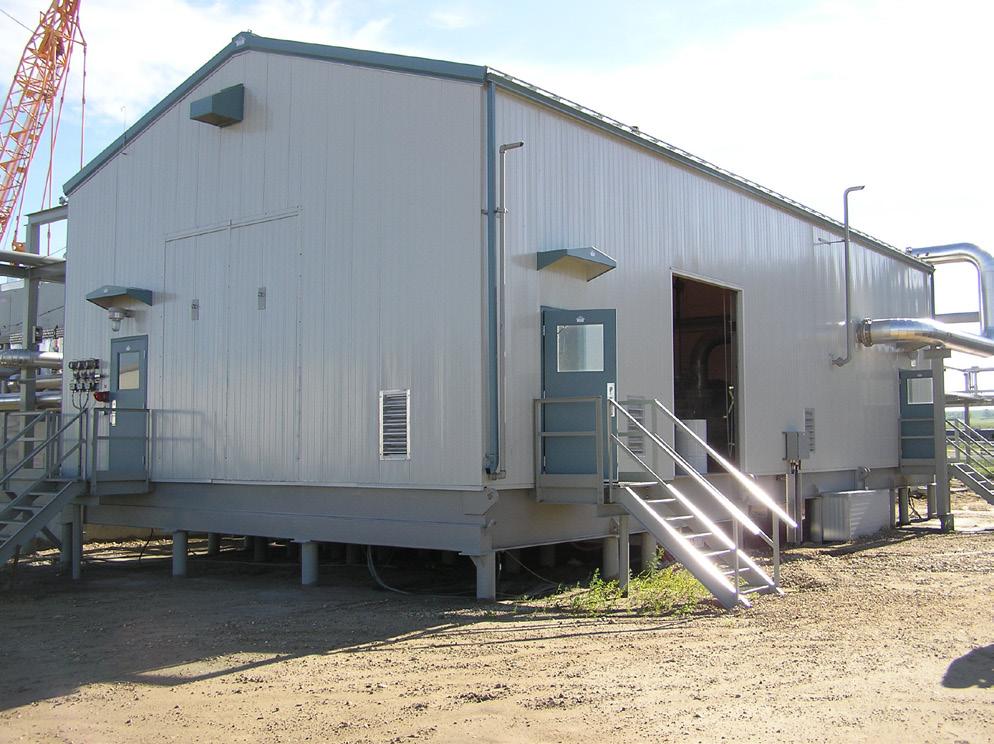
Wood has also added an “F” to the EPC capabilities with the introduction of fabrication, developing fit-for-purpose solutions that include anything from well pads to pump house modules to marine assets for tailings ponds. These value-add propositions present a significant opportunity for Wood in the market while helping customers reduce capital costs on their projects at the same time.
“We have several inhouse products that we’ve developed and are in the process of developing where we can disrupt some of the incumbent solutions typically used here in Western Canada,” says Westrup.
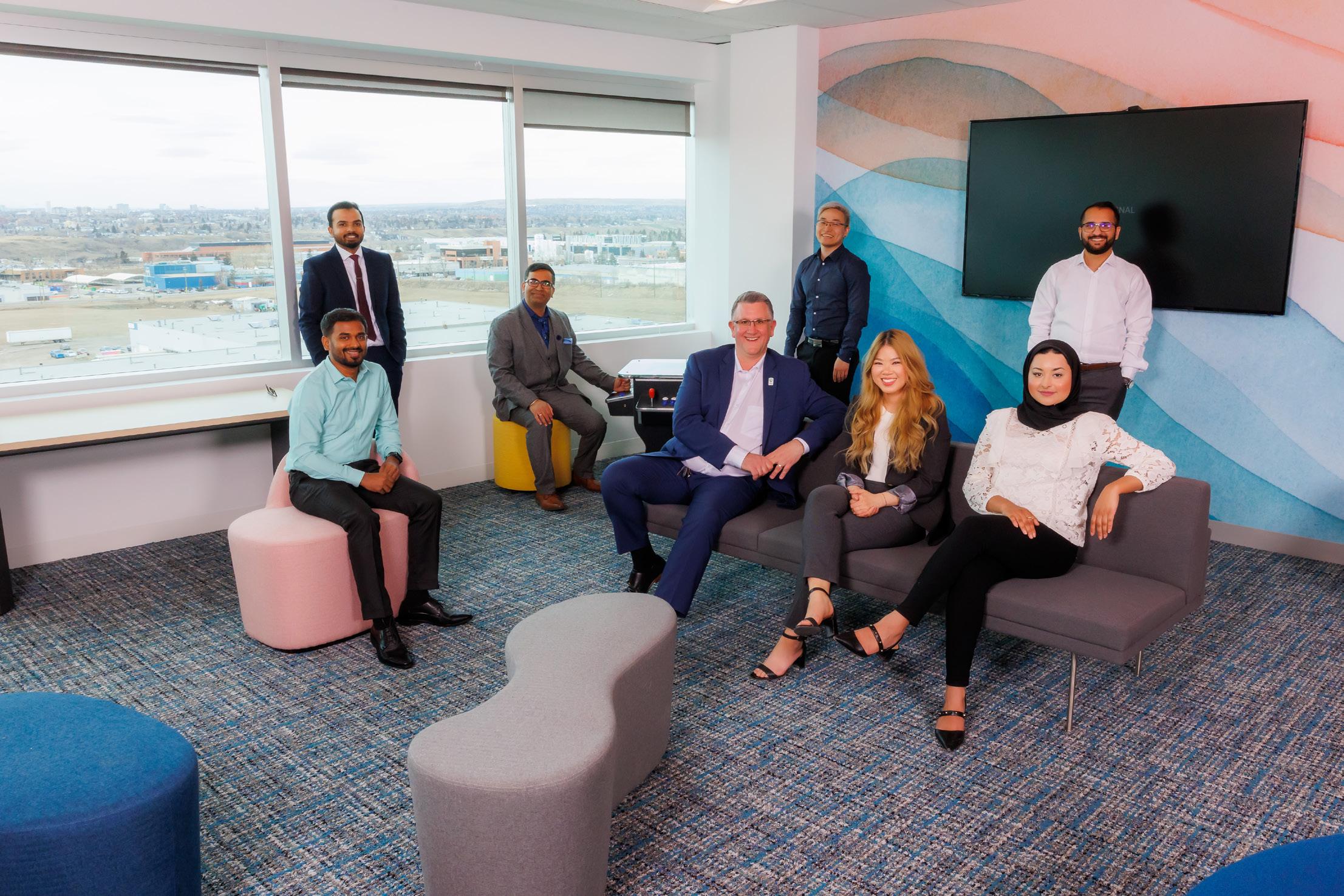

Bucking traditional methods is something Wood has settled into as it has grown and diversified in an increasingly challenging and changing market. A key example is carbon capture, an emerging market assisting Canada’s net-zero goals across a number of industries, and Wood is accessing local specialists and global subject matter experts to apply strategies being employed in countries that are further ahead of Canada in the energy transition.
As key part of Canada’s decarbonization journey, Wood is proud to be the incumbent engineering services provider of the Pathways Alliance CO2 trunkline project. This initiative sees Canada’s largest oil sands producers working toward their goal of net-zero emissions by 2050. The ambitious flagship project will link more than 20 oil sands facilities along a 400-kilometre trunkline and collect CO2 for permanent storage in a Cold Lake, Alberta, hub. Wood is currently executing the Front End Engineering and Design (FEED) project scope for the Pathways Alliance.
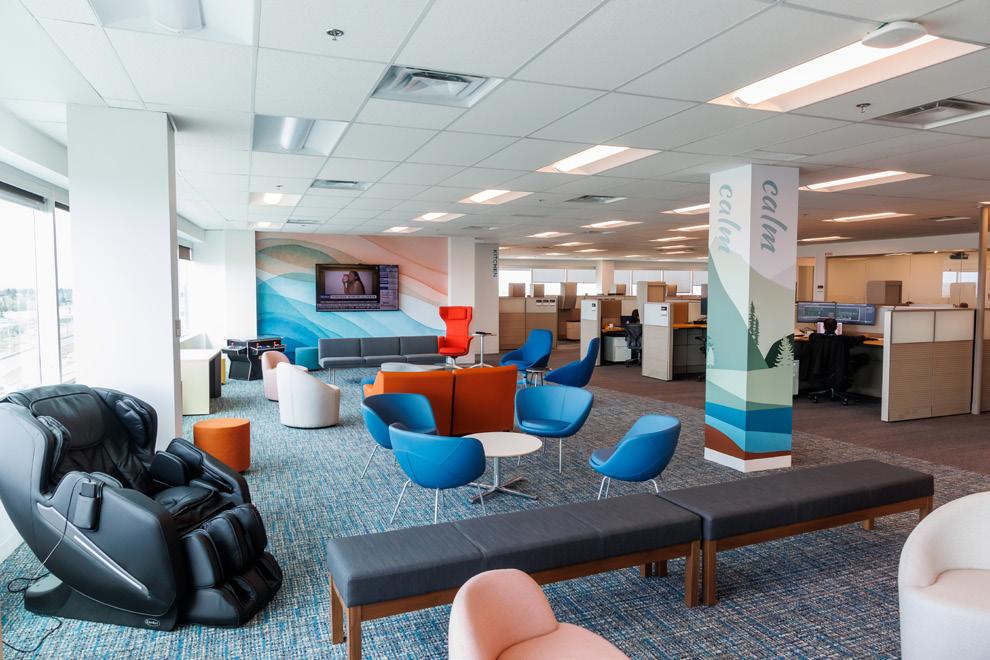
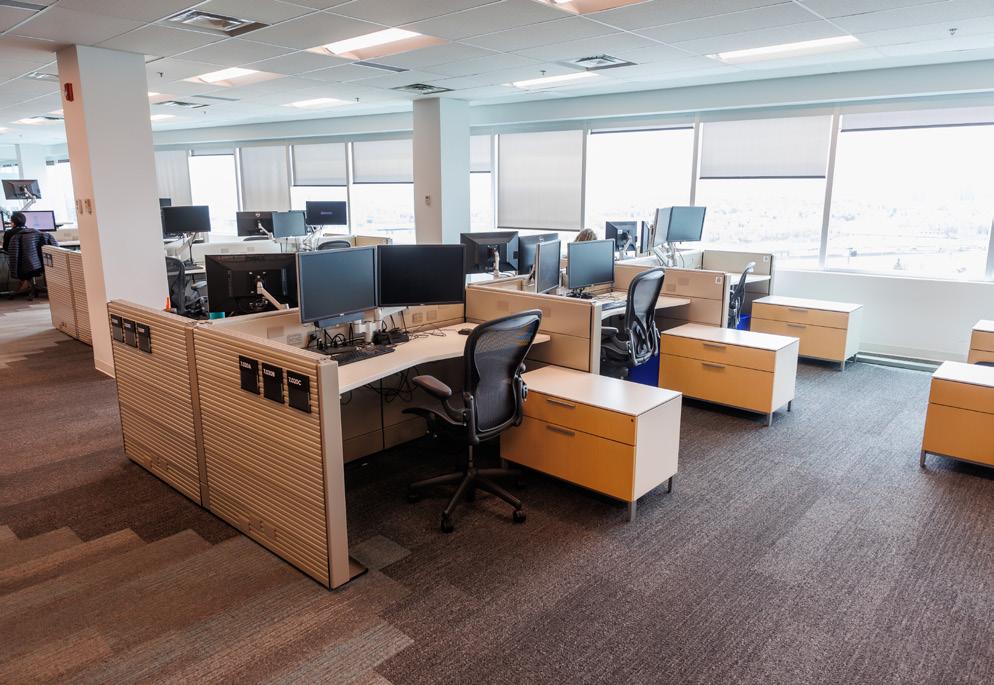
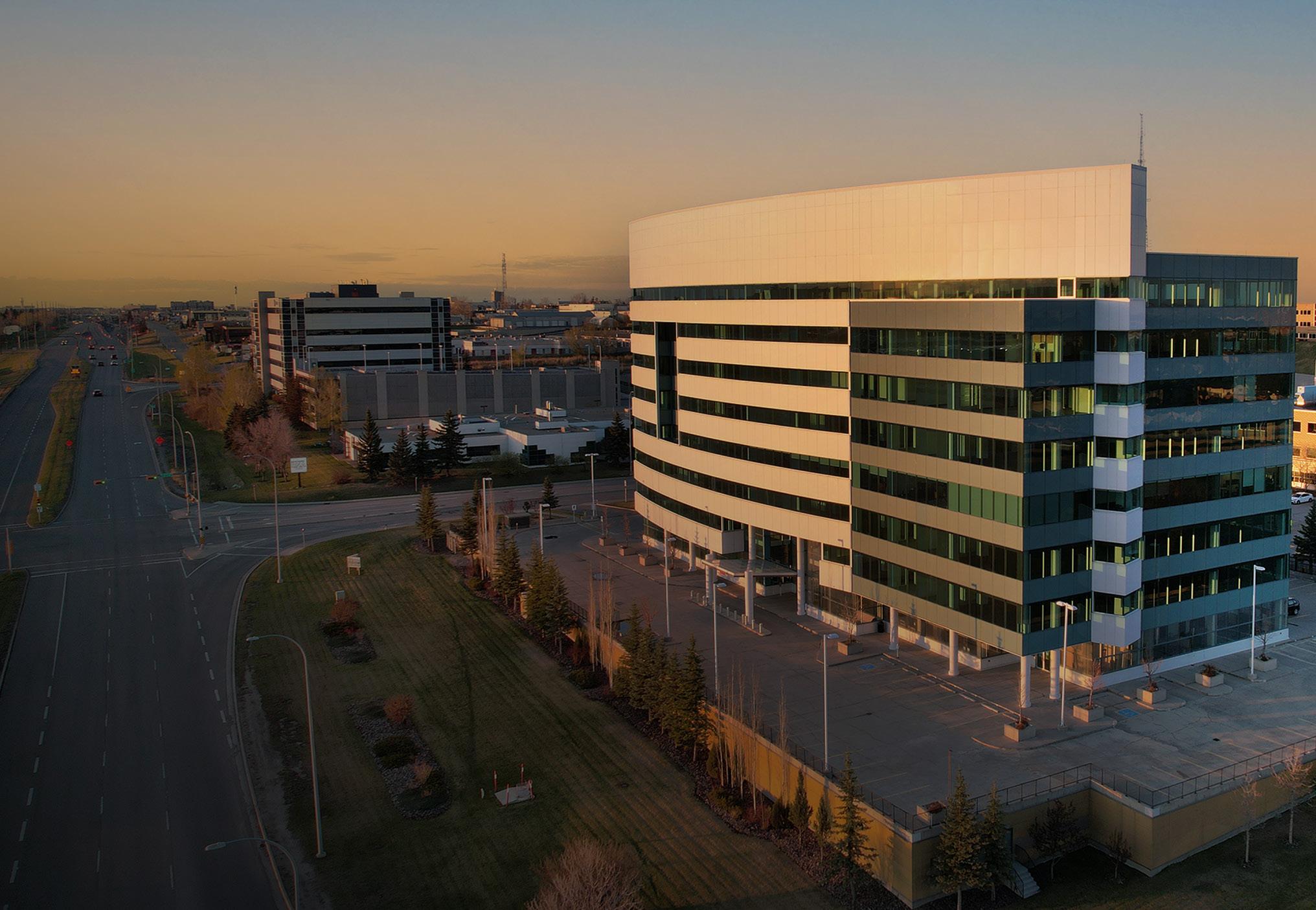
Hydrogen is also playing an important role in the energy transition in Alberta, whether clients are looking at blending hydrogen with natural gas for energy, transporting hydrogen via pipeline or converting to ammonia, or altering their combustion engines to fire on hydrogen instead of natural gas. Wood supports the full hydrogen lifecycle.

“Wood owns its own SMR (steam methane reforming) hydrogen production technology, and we are one of only a few companies in the world that can actually license that technology to companies,” he says.
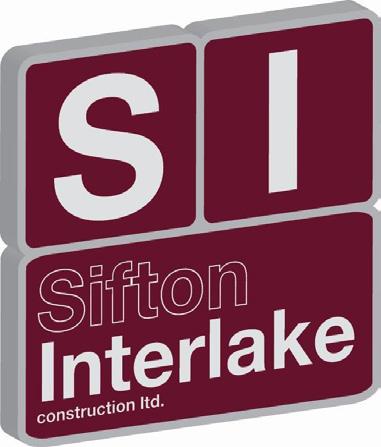

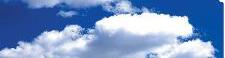
Wood is clearly not a standard EPC company, and it is striving to be both a client’s first choice service provider and a professional’s first choice employer.
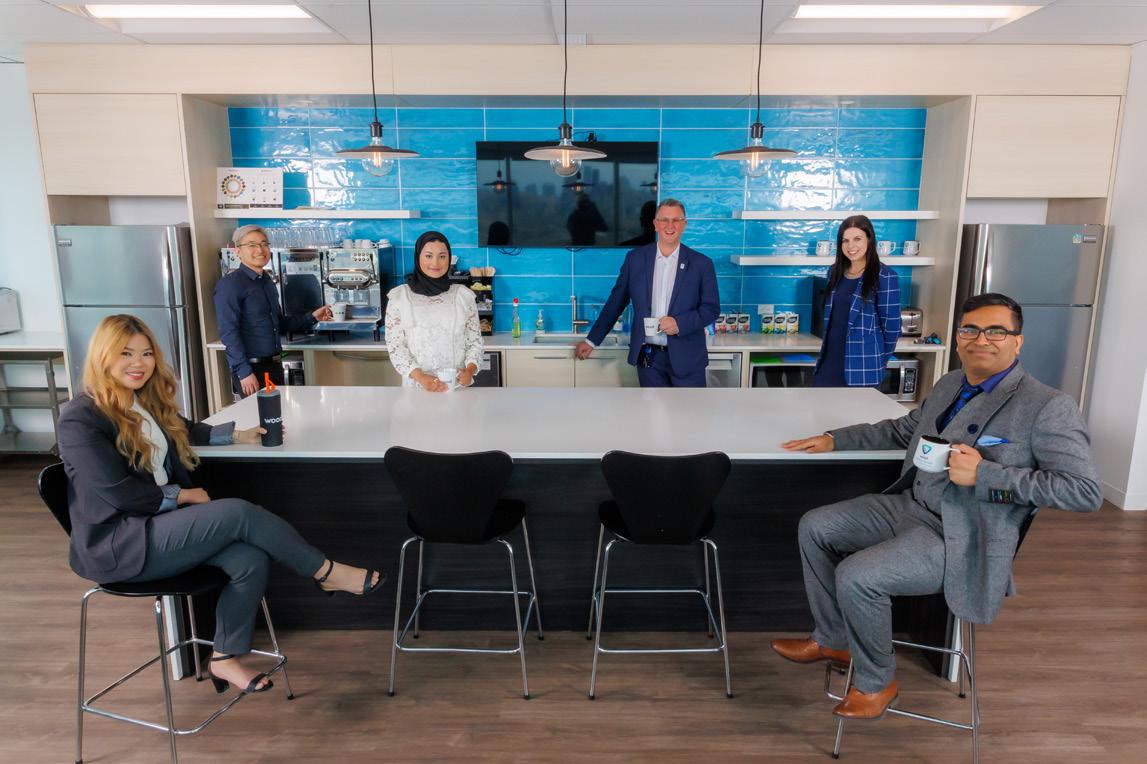





Wood’s focus on attracting, training and retaining the best people in the business culminated in a move in February from its long-time downtown offices into an incredible purpose-built space at Memorial Drive and Barlow Trail. The impetus for the move was simple: to improve value for clients while offering the kind of amenities and environment that appeals to today’s workforce.

From ample free parking for the 760 Wood employees and the free on-site gym to complimentary gourmet coffee and a flexible hybrid work model, Wood has checked every box on an employee’s wish list. And that focus on employees is reinforced in the details. Enclosed management offices are concentrated in the building’s core, leaving the million-dollar panoramic view and natural light to the staff throughout the open-concept space. With its ping-pong, foosball and pool tables, massage chairs, televisions and comfortable lounge furniture, Wood’s three floors feel more like a tech space than an engineering firm. And being equipped with WiFi6 technology throughout means the team enjoys full connectivity to perform 3D modeling and process simulations from anywhere in the office without worrying about plugging in.

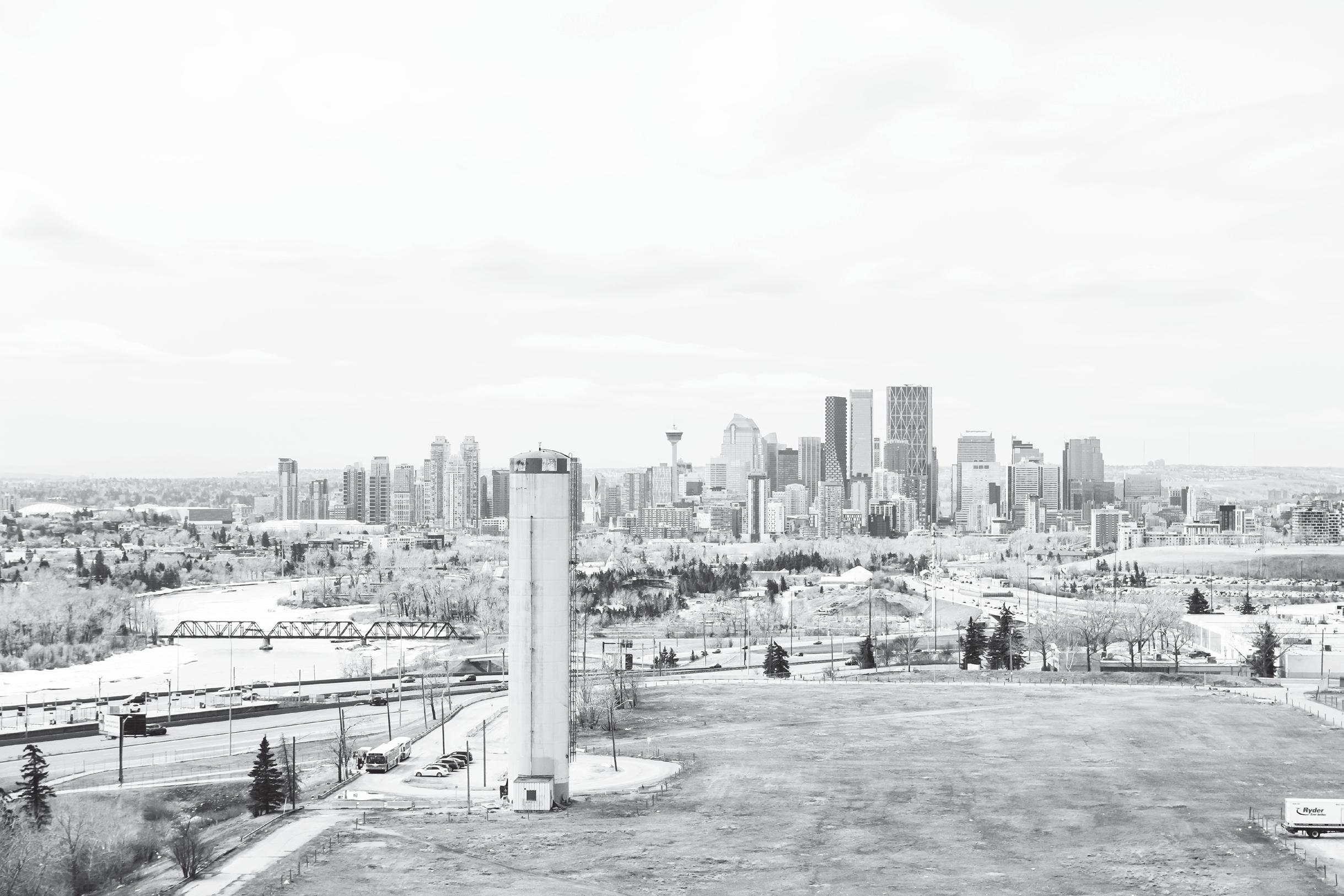
“Retaining and attracting is not only about salary anymore; it’s about environment, the dynamic,

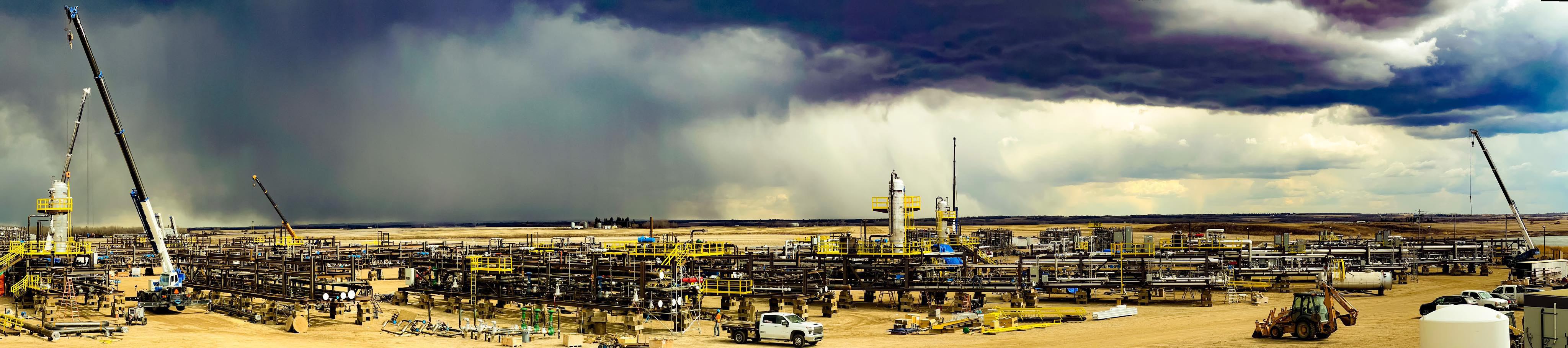
the ambiance, the behaviours of people and the ability to connect. All of those things play a factor and ultimately they drove us to this type of office. If you want to hold onto the next generation of employees, you need to provide this type of working environment and the flexibility of a hybrid model,” says Westrup.
While born out of necessity during COVID, that hybrid working model proved effective and popular enough to adopt permanently after restrictions eased. About 85 per cent of staff now adhere to a formal hybrid schedule where two employees share a desk on a five-day rotation that straddles the weekend. If employees want to come in on their remote days, they can by booking hoteling stations or breakout rooms found throughout the office.
Wood is providing incredible service out of its new office and staff are enjoying the amenities and atmosphere that have come with it. Through professional development support, intercompany networking, flexible work models, and social and wellness clubs coupled with a forward-thinking, creative professional culture, management is investing in the future of both the organization and the industry – and what a bright future it is for Wood.