
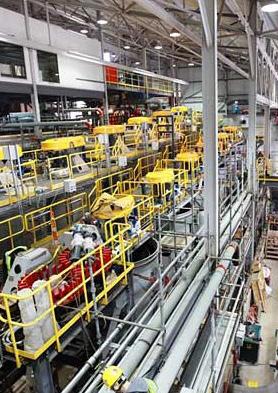
Eagle Mine is owned by Lundin Mining, a diversified Canadian base metals mining company with operations and projects in Argentina, Brazil, Chile, Portugal, Sweden, and the United States of America, primarily producing copper, zinc, gold, and nickel. Its Eagle Mine operation is led by Managing Director Darby Stacey and stands as a significant player in the mining industry, focusing on the production of nickel and copper. Under his leadership at Eagle Mine has been instrumental in ensuring operational excellence, sustainability, and continuous improvement in the challenging mining sector.
The Eagle Mine is located in Michigan’s Upper Peninsula, a modern underground mine host to a high-grade nickel/copper deposit operated by Lundin Mining Corporation. The mine is situated in Marquette County near the town of Big Bay. The ore body consists of high-grade sulphide minerals, including chalcopyrite and pentlandite, which are extracted through underground mining methods. The extracted ore from the underground mine is transported to the surface processing facility, where it undergoes primary crushing and grinding. After crushing and grinding, the ore is mixed with water and chemicals in flotation tanks. Air is then introduced into the mixture, causing the valuable minerals, such as nickel and copper sulphides, to attach to air bubbles and rise to the surface as froth. The froth is skimmed
off, containing the concentrated minerals, while the waste material sinks to the bottom as tailings.
The froth containing the concentrated minerals is further processed through a series of dewatering steps to remove excess water and create a thickened concentrate. This concentrate is then filtered and dried to reduce moisture content, making it suitable for transportation and further processing. The dried concentrate is transported to a smelter, where it undergoes smelting to extract the nickel and copper metals. Smelting involves heating the concentrate to elevated temperatures in a furnace, causing the sulphide minerals to decompose and release the metal content. The molten metal is collected and cast into ingots or other forms for transportation to refineries or customers. The
nickel and copper metals obtained from smelting may undergo further refining processes to purify them and remove impurities. Refining techniques may include electrolysis, solvent extraction, or other chemical processes to achieve the desired metal purity levels. Once the nickel and copper concentrates are processed and refined, they are packaged into containers or
bulk shipments for transportation to customers worldwide.
Darby Stacey’s strategic operational planning aims to ensure efficiency, safety, and environmental responsibility throughout the mining process. Stringent quality control measures are implemented to ensure that the final products meet or exceed industry specifications and customer
requirements. Environmental management practices are also integrated into the processing operations to minimise environmental impact and ensure compliance with regulatory standards. By following these steps, Eagle Mine can efficiently process ore, produce high-quality nickel, and copper concentrates for the global market.
Improved infrastructure plays a crucial role in supporting Eagle Mine’s operational activities. He oversees infrastructure development projects to enhance operational efficiency, safety standards, and logistical capabilities. By investing in modernising facilities, upgrading equipment, and maintaining a reliable infrastructure network, Eagle Mine ensures the seamless operation of its mining activities while prioritising the safety and well-being of its workforce. They invested in improving access roads and transportation networks to facilitate the movement of personnel, equipment, and materials to and from the mine site. Upgrades to roads, bridges, and railway connections have enhanced planning and re-
duced transportation costs.
Furthermore, significant investments have been made in upgrading and expanding the processing facilities at Eagle Mine. Modernization of crushing, grinding, and flotation circuits has increased throughput capacity and improved recovery rates, leading to higher production efficiency and profitability. They implemented advanced water management systems and infrastructure to minimise water consumption, mitigate environmental impact, and comply with regulatory requirements. This includes the construction of water storage facilities, water treatment plants, and tailings management facilities to ensure responsible water stewardship. To reduce its
environmental footprint and dependence on fossil fuels, Eagle Mine has invested in energy infrastructure upgrades and renewable energy solutions. This includes the installation of energy-efficient equipment, the development of solar power projects, and the implementation of energy management systems to optimise energy usage and reduce greenhouse gas emissions.
XPS is an industry leader, collaborating with clients in delivering industry relevant solutions to improve process performance, asset integrity and environmental sustainability.
We provide expertise in:
• Geometallurgy & Mineral Science
• Mineral Processing
• Hydrometallurgy
• Pyrometallurgy & Furnace Integrity
• Process Modelling & Simulation
• Process Control & Automation
• Materials Technology & Asset Integrity
Main services offered to clients:
• Orebody characterisation
• Process & flowsheet development
• Operational support & continuous improvement
• Process Control strategies & optimization
• Asset Integrity assessment
• Metals recycling & refining
• Decarbonization & SO2 Abatement
• Effluent treatment & arsenic stabilization
Eagle Mine’s technology transformation has been instrumental in its success on several fronts. Under Darby Stacey’s guidance, the mine has integrated digital solutions to optimise processes, enhance data-driven decision-making, and drive operational efficiency. By adopting automation, data analytics, and remote monitoring technologies, it has optimised mining processes, increased productivity, and reduced operational costs, enhancing overall efficiency. Implementation of innovative safety technologies and environmental monitoring systems has
ensured regulatory compliance and minimise risks to personnel and the environment. The adoption of innovative technologies has given Eagle Mine a competitive edge in the mining industry, enabling it to adapt to changing market dynamics and maintain its position as a leading mining operation.
Sustainability is a core focus area for Eagle Mine, reflecting Darby’s commitment to environmental stewardship and community engagement. The mine implements sustainable mining practices, resource conservation initiatives, and community development programs to minimise environmental impact and
create shared value for stakeholders. The mine implements water recycling and reuse initiatives to minimise freshwater consumption and reduce the discharge of wastewater into the environment. Additionally, Eagle Mine invests in water treatment technologies to ensure that water discharged from the mine meets regulatory standards and does not harm local ecosystems. By adhering to stringent environmental standards, managing water resources responsibly, and prioritising biodiversity conservation, Eagle Mine contributes to a sustainable future for the mining industry.
Eagle Mine collaborates closely with suppliers, contractors, and partners to ensure the prompt delivery of equipment, materials, and services needed for mining activities such Expert Process Solutions (XPS). Many suppliers offer technical support and services to aid Eagle Mine in optimising equipment performance, troubleshooting issues, and implementing best practices. These services include training programs, on-site support, and access to engineering expertise to address complex challenges and improve operational efficiency.
Safety is a top priority at Eagle Mine, and suppliers of safety equipment play a critical role in ensuring the health and safety of the mine’s workforce. These sup-
pliers offer a wide range of safety gear and personal protective equipment, including helmets, gloves, safety glasses, respirators, and safety harnesses, helping to prevent accidents and injuries in the workplace. By promoting a culture of safety and accountability, Eagle Mine aims to prevent accidents, injuries, and occupational illnesses, thereby safeguarding the well-being of its workforce.
By fostering strong relationships, Eagle Mine strengthens its operational resilience, cost-effectiveness, and overall sustainability. Under the leadership of Managing Director Darby Staacey, Eagle Mine continues to uphold its position as a responsible and successful mining operation within Lundin Mining.