
3 minute read
COVID SUPPLY ISSUES AND THE IMPACT ON YOUR BUSINESS (Industry Column
Having trouble getting staff? Try a Robot waiter. Call 0450 267 851 for a FREE trial.
MTROBOT AUTOMATION PTY LTD TOO. mtrobot.au@gmail.com
Advertisement
Covid supply issues and the impact on your business
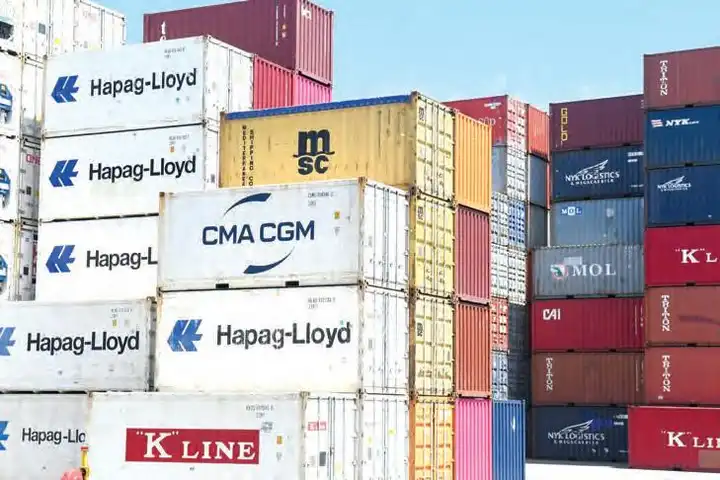
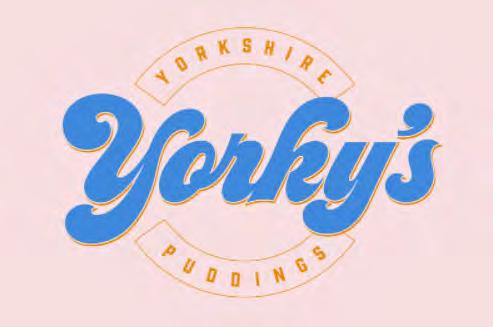
YORKY’S TRADITIONAL YORKSHIRE PUDDINGS 3 different sizes: (Small, Medium & Large) Made traditionally with fresh ingredients Fully HACCP certified PH: 0416 933 274
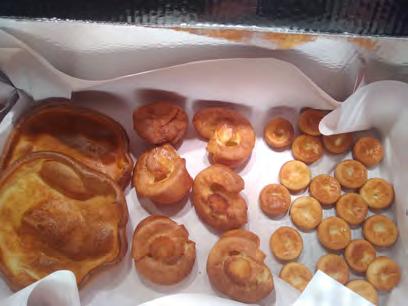
The world has definitely changed since COVID-19 surfaced in December 2019. At first, we were all worried about our jobs and how we would financially survive as the first lockdowns surfaced around the world. Australia except for our Victorian and NSW cousins, have escaped the extended lockdown curse. Yes of course there have been restrictions on us all whether that’s travel, or social distancing requiring reduced numbers at our favourite hospitality venues. Not to mention the fact that we’ve been restricted, unable to travel for holidays or to see family and friends either interstate or overseas.
What has come out of this pandemic is that the demand on goods and services in Australia has increased unexpectedly. And the fact this is not consistent across the world is now causing all suppliers of any manufactured products significant delays, from cars through to the latest electronic devices. As consumers, we have become used to the instant gratification of getting our newly purchased product straight away, whether sourced online or through traditional retail options. So why is this delay occurring? There are many factors that have caused a perfect storm, starting with international freight. Well before the pandemic, many major shipping companies were losing money and made decisions to reduce their infrastructure. This basically means they were starting to scrap ships rather than replace them, which reduced the need for sea containers as well. Once the pandemic hit, the requirement for shipping increased for some markets and reduced in others. Along with reduced air freight, this culminated into what was the start of extended shipping delays. World manufacturers not only couldn’t produce in certain jurisdictions due to COVID-19, they couldn’t even ship goods they had manufactured because there was no capacity on the ships, even more baffling, there were no containers available to pack their goods in. This has been an issue since December 2020 which has now seen a shortage worldwide that has led to delays in anything that requires components like semiconductors. This has been well-outlined in the general media with Toyota slashing car production by 40 per cent. These parts however, are not exclusive to cars. They are required for anything that has an electronic component, which in the hospitality industry, means items like ice machines, combination ovens, coffee machine or anything electronic you would use in your standard restaurant or café operation. We are now seeing increases not only in freight charges but all raw materials, and if you have put fuel in your car lately I’m sure you have seen how much this has increased.
If you do your research you can see this is not going to improve in the short term, with some analysts suggesting it won’t begin to improve until mid to late 2022.
Unfortunately, with anything we purchase in the future this will become the new norm and your suppliers if they aren’t already, will be having ongoing issues with certain stock lines and supply. So plan well and make decisions early to ensure you limit the impact on your business no matter how large or small that may be.
By Brian Garcia of Moffat