Grand Opera House Belfast
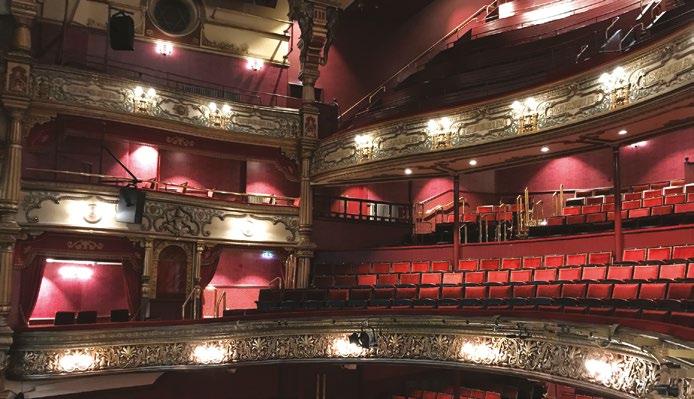
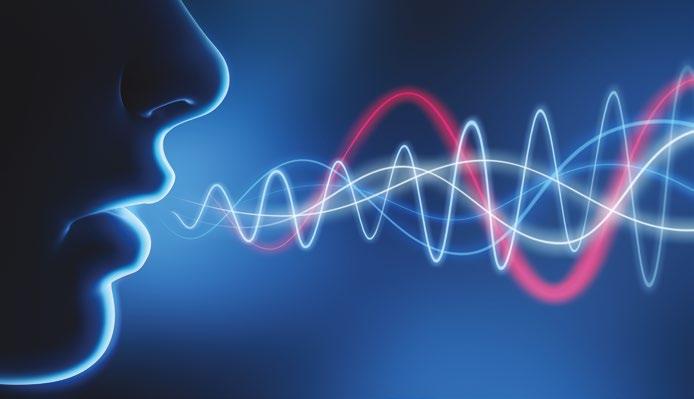
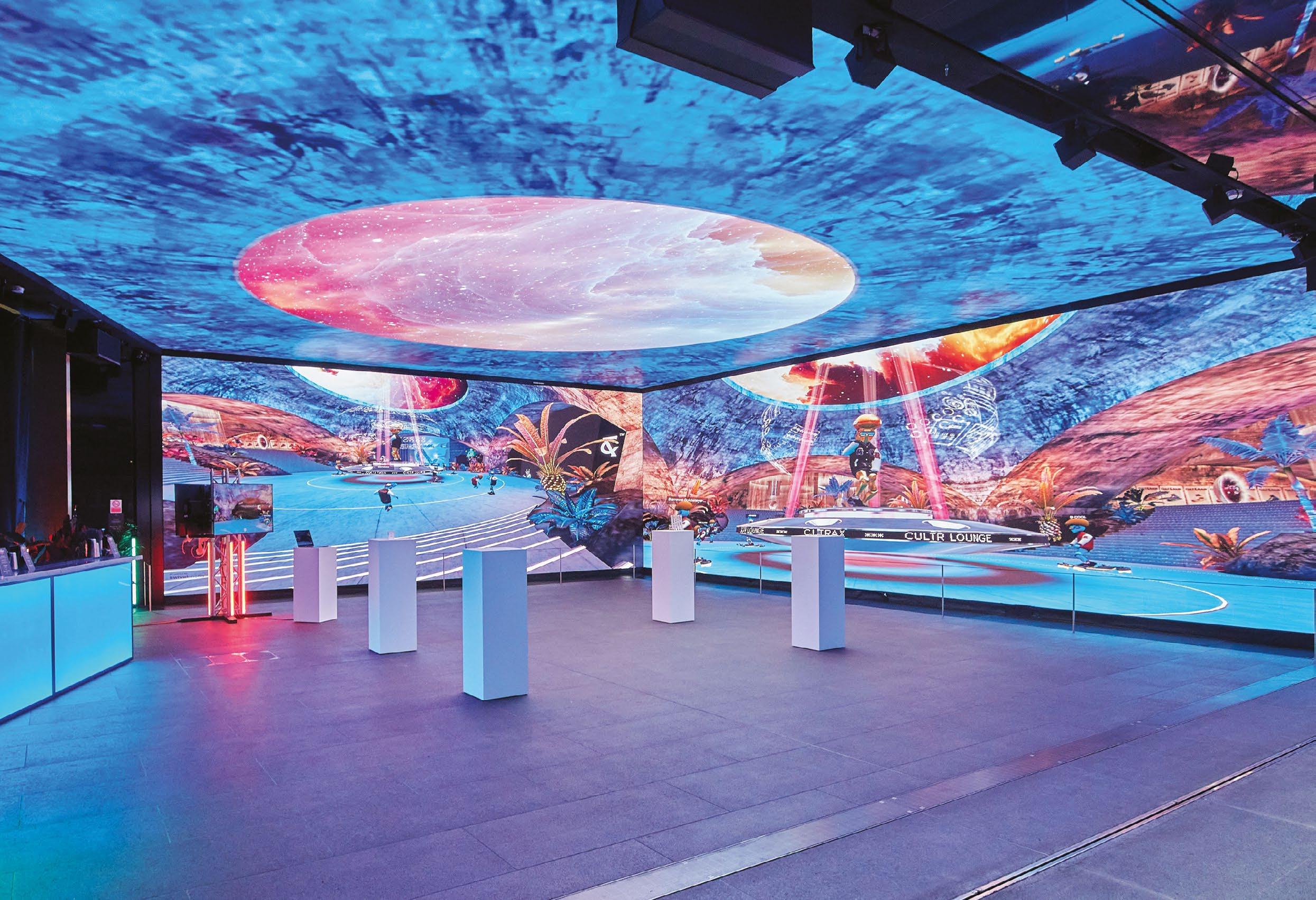
PSI spill the beans on this phenomenal project.
A Canford Production
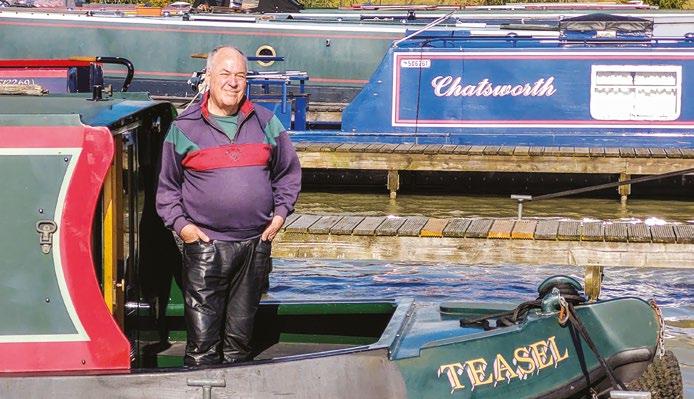
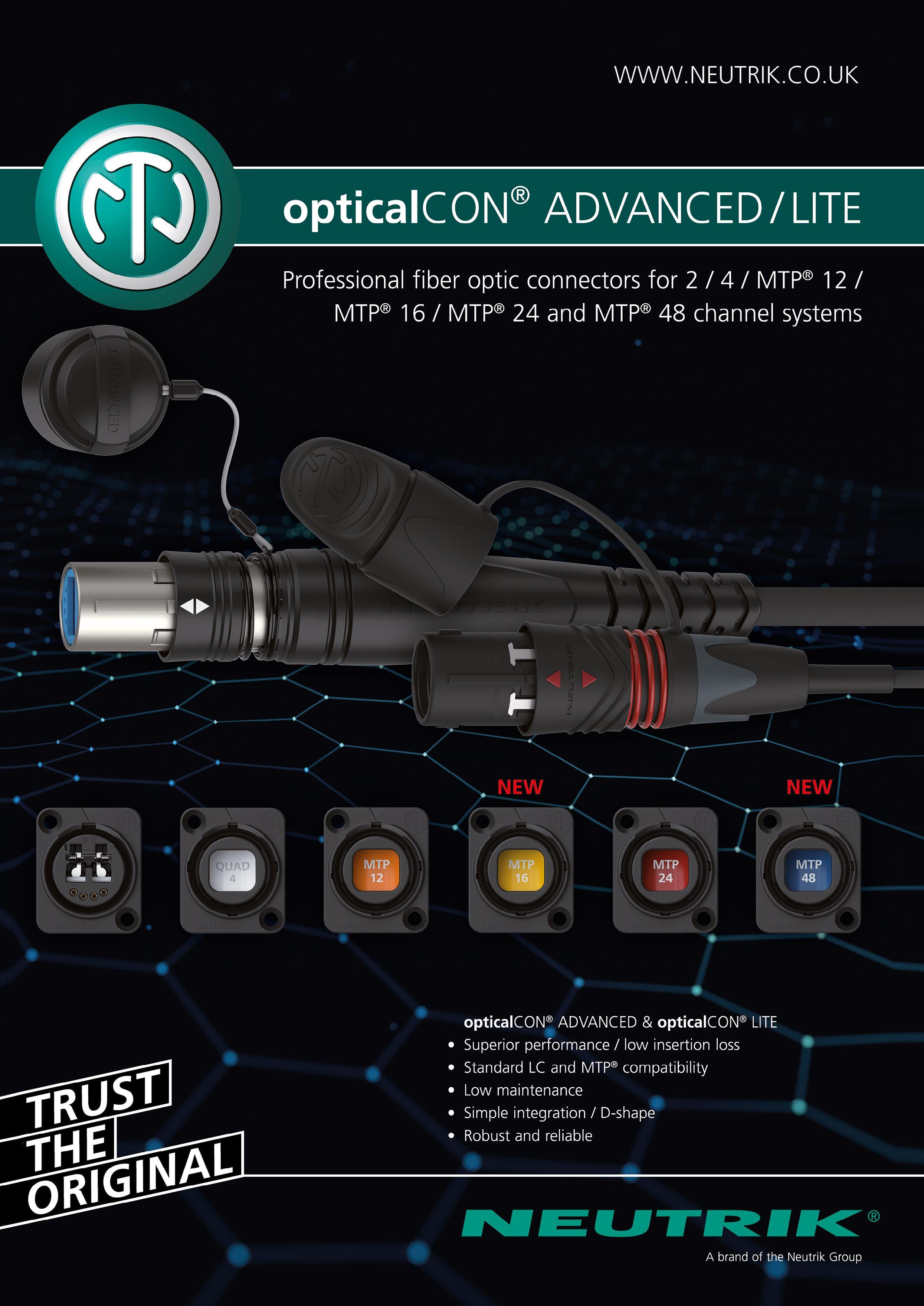
PSI spill the beans on this phenomenal project.
A lot has changed at Canford over the last twelve months! One thing that remains the same however, is the commitment we have for delivering the best possible service to our worldwide partners. We do this by developing, manufacturing, and distributing superior quality solutions for the Broadcast, Theatre, Live Events and AV markets through innovation, consultation, and design.
When Iain Elliott created the business, back in 1976, he never wanted Canford to become just “another box-shifter”. We continue with that ethos and have developed a Canford SMPTE fibre cable, which will complement our current offering. The EMO range has also seen some additions, with the introduction of a new breed of rackmount and floor box power distribution units. These new units, and the entire EMO range, continue to be assembled at our head office in Washington, Tyne & Wear, something that was very important to Iain.
Whether you deal with our head office in Washington, our manufacturing site at Portland, or one of our sales offices in Strasbourg or Dubai, I simply say THANK YOU! We wouldn’t be here without you, and we look forward to working with you again soon.
Alan Wilson, CEOWe use Carbon Balanced Paper for Source Material magazine, the wall planner and the outer wrapper.
This year we balanced the equivalent of 7,985kg of carbon dioxide. This helped in the protection of 1,525m2 of critically threatened tropical forest.
Carbon balancing is recognised as one of the fastest ways to halt the rise of CO2 in the atmosphere and therefore reduce the effects of global warming.
CANFORD GROUP LTD
Elliott House, Crowther Road, Washington, Tyne & Wear, NE38 0BW, UK canford.co.uk
Admin
t: +44 (0) 191 418 1000
e: info@canford.co.uk
UK Sales
t: 0191 418 1122
e: sales@canford.co.uk
International Sales
t: +44 191 418 1133
e: international@canford.co.uk
Dubai Sales t: +971 50963 1201
e: dubai@canford.co.uk
Customer Services
t: +44 (0) 191 418 1155
e: custservices@canford.co.uk
e: enquiries@canford.co.uk
Custom Metalwork
e: custommetal@canford.co.uk
e: marketing@canford.co.uk
We are continually developing and fine tuning our marketing activity to ensure that we share appropriate information, relevant to your industry sector and specialism. To help us improve our communication with you, please let us know any updates to your details by emailing marketing@canford.co.uk. Thank You.
Festive Season shut down 2022
Last day of trading will be Friday 23rd December 2022. We re-open on Tuesday 3rd January 2023.
Canford has a new CEO. Who is he? Where did he come from? And what is his favourite colour?
Vita Gorkina sits with David McKeown (Project Estimation & Design at PSI) to find out more about the incredible project they just completed: the Grand Opera House Belfast.
The winner will be notified via e-mail on the 1st February 2023.
Iain Elliott was one of four founders of Canford Audio, and the only one to remain with the company until the end of his career. After graduating in 1974, he put together Metro Radio, so he was already an experienced and practical audio engineer. In 1976, the idea of an audio ‘one stop shop’ came to him, and Canford Audio was born, with its first premises in Ryton, Tyne and Wear. Canford Audio became a limited company in August 1978.
Iain was a man with many interests, and he pursued all of them with passion and attention to detail. I first got to know him in about 1973 as a fellow student in Durham, meeting socially, and occasionally on industrial archaeology bus trips, organised by him. Iain’s interest in buses and trains manifested itself in that era and he formed a business called ‘Catch a Coach’ with the aim of getting students to, and from, university more cheaply than the railways were offering; years later Iain found out the Student Rail Card had been inspired as a response to this new competition.
Iain was Canford’s guiding force from beginning to end, despite a few months away from the company in 1999/2000. He knew everybody; his management style was to go around talking to people. His knowledge of ‘products’ can scarcely have been rivalled in the industry and he maintained excellent relations with key customers and suppliers.
Iain’s passions were by no means confined to business. He and his wife Liz bought a 15th century pele tower in Longhorsley, Northumberland, in 1997 and he threw himself into its restoration and the management of a large garden – his vegetable plantings were meticulously documented. Iain and Liz engaged totally with the community, and Iain was chairman of the Parish Council for fourteen years. Iain was a good cook, a connoisseur of wine, and a generous host. Membership of the Northumbrian Wine and Food Society has been an important part of Iain and Liz’s life. They both loved Old English Sheepdogs (‘Dulux Dogs’ if you are old enough to remember) and owned three of them in succession. Iain’s interests in transport extended to inland waterways and narrowboats, and for 26 years he and Liz owned a narrowboat called Teasel (a pet name for one of the dogs, an ardent boating enthusiast). A final voyage on Teasel was a highlight of 2021, just before his illness made normal activities difficult.
Iain’s passion for the business was such that questions about retirement tended to be shrugged off, and his fellow shareholders were left wondering what the way forward might turn out to be. These uncertainties were resolved in discussion with our Newcastle auditors, UNW, in 2019. We considered what options were available. We did not want to
sell the business to another company, since we were afraid of losing what makes Canford unique. Iain and I preferred the idea of selling it to an Employee Ownership Trust (EOT) and pursued this, concluding the sale in December 2019. As a result, the business is now owned and managed for the benefit of present and future employees.
Iain had the confidence to do this because he knew that we would be leaving the company in very capable hands. Unfortunately, that time came much sooner than anybody had expected, with a diagnosis of pancreatic cancer in September 2021. Iain struggled on despite difficulties with his eyesight, remaining CEO of Canford until his death on December 29th, 2021. Iain was laid to rest in the old churchyard at Longhorsley on January 7th after a short graveside service, attended by just a few. On the village green, the Northumberland flag was flown at half-mast in his honour.
Iain dedicated his life to Canford. To honour this, we wanted to do something which would serve as a long-standing, fitting tribute. Canford’s head office in Washington has never had either a number or a name. This was rectified on May 25th this year when the building was renamed “Elliott House” in a short ceremony attended by all local staff, Liz, and business friends. The ceremony itself went well; the unveiling duties were carried out by Marcus Brooke, Managing Director of Sonifex (a supplier/friend who worked closely with Iain over many years). It was lovely to see so many people get together to reminisce and remember Iain, who will always be in our thoughts.
Rest in Peace Iain.
There are approximately 55.5 million smartphone users in the UK today and it has been reported that a key use of the smartphone is for sound, whether that is for listening to music, podcasts, or watching a movie. In general, some form of headphone facilitates the consumption of sound on a smartphone, and a study carried out by Deloitte in 2019 found that of the 3,952 respondents, 64% used wired in ear type headphones and 33% used wired headband types. Headphone sales are continuing to rise; the latest forecast for growth difference in headphone sales, between 2021 and 2026, is $18.45 billion according to PR newswire. 1
There are four main headphone designs, supra-aural, circum-aural, intra-concha, and insert. Essentially, supra-aural sit on the ear, circum-aural sit around the ear, insert fit into the ear canal, and intra-concha sit just at the entrance to the ear canal, these four versions can be seen on the right. Different earcups are used on circum-aural and supra-aural headphones, these are open back and closed back types. Closed back headphones allow passive attenuation of environmental sounds and help to reduce spill to people in close proximity. Open back headphones allow spill and also let sounds from the listening environment in but have benefits that they allow ventilation when used for long listening periods and provide a more open and broader soundstage when compared to closed back. The fit and seal of a headphone to a listener’s ear is critical since small movements, and improper seal, can change the perceived bass with variations of up to 20dB in the headphone’s response.2 This is also further complicated by the fact that no two people have the same shaped pinna, meaning that the seal provided by one headphone for one listener may not be ideal for another listener.
Acoustically closed earphone (minimum leakage)
EARPAD PROTECTOR
Intra-concha Insert
HOUSING TRANSDUCER EARPAD PROTECTOR
HOUSING TRANSDUCER
HOUSING PROTECTOR
Circumaural
TRANSDUCER EARPAD
EARPAD
Supra-aural
HOUSING TRANSDUCER
Dorsal Rostral
back front
Dorsal Rostral
back front
Dorsal Rostral
back front
Dorsal Rostral
back front
Stereo sound is the most accepted way to listen to music, whether that is in monitoring, mixing, mastering or for pleasure. In general, this takes place using a room which has been treated for optimal monitoring, such as a recording studio, or, in a domestic situation, a living room. It would seem obvious that headphone sound should approximate this listening experience in some way. Historically, manufacturers have had two choices, with respect to the target sound of their headphones, and used either the diffuse field or free field correction curve. The two approaches differ by their method to create the reference curve; the first method uses a diffuse sound field, and the second uses a free field. The diffuse sound field is created with the use of a reverberation chamber by using an omni directional speaker where a sound field is created through many reflections from the chamber’s surfaces, and the direction of sound arrival is equal in all directions around an acoustic mannequin. A free field is essentially the opposite; there are no reflections from the room’s surfaces and it is just the direct sound that reaches the mannequin from a speaker placed directly in front. These methods seem far away from the previously mentioned environments (e.g recording studio or domestic living room). As a result of this, researchers at Harman International have proposed an alternative, the Harman target curve.3
The target curve is based on measurements of good speakers in a room approximating an average living room, and through extensive objective measurements, and subjective testing with many listeners, they have come up with an equalisation curve which most listeners prefer. Harman/AKG call this the reference response acoustic curve. The target curve allows headphones to be equalised to this curve in an attempt to provide a headphone sound which suits most listeners and approximates the sound signature of a good pair of speakers in a good sounding room. In addition, with reference to the previously mentioned issue of incorrect seal causing issues with the bass response, the headphone ear cup has also been re-engineered to be oval shaped and include slow retention foam earpads. Harman/AKG have justified this design stating that the ear is oval shaped, not round, and state that this helps obtain a good seal, ensuring accurate bass response. Two pairs of headphones that utilise the aforementioned technology are the AKG K371 and the AKG K371-BT. 4
When listening to music using loudspeakers, by the time the sound hits the ear drum it will be a combination of the direct sound and the room’s acoustics milliseconds later. Crosstalk also occurs. This is where the sound from the left speaker goes to the left ear and then also a delayed version to the right ear, and vice versa. When listening using headphones, this is not the case as the sound arrives directly on axis of the ear, resulting in a different spectral composition compared to that of loudspeakers, and the sound is minus the effects of the room and crosstalk. One thing manufacturers do to ameliorate this is to angle the drivers within the headphone ear cup so that the higher frequencies interact with the pinnae as it would when listening using speakers. An example of headphones that use this to improve the soundstage are the Sennheiser HD 400 pro. Typically these are manufactured, and marketed, as reference monitoring headphones. 5
Listening to music using loudspeakers, the sounds are localised outside of the head, somewhere in the area between the loudspeakers. Listening using headphones, this is not the case, and the phenomenon of in-head localisation is relevant. Inhead localisation refers to the phenomenon of, when listening using headphones, all of the sounds appearing to be within the centre of the head, which is not a realistic experience. Audio research has developed DSP that can filter sounds so that they appear outside of the listener’s head and are effectively externalised, this technology is included in services provided by Netflix and Apple music amongst others. Contrary to this, recent studies have found that, for some applications, inhead localisation has been found to be advantageous. Recent research by American universities UC San Diego, UCLA, and UC Berkeley, have found that listening to messages and announcements on headphones increases feelings of empathy, connectivity and engagement.6
The upshot of this research is that if the aim of a message or announcement is to persuade the listener, or to evoke some kind of emotional connection, then the messages should be available on media most consumed using headphones.
Headphones 3.0 is a term coined by Sonical Sound Solutions, essentially a next generation headphone termed hearable. Sonical have identified 3 stages of headphone development over the years, which can be seen at sonical.ai/headphone3. Headphones 1.0, which were just wired headphones, headphones 2.0, which have wireless bluetooth and DSP, and headphones 3.0, which are currently in development and will essentially be a computer in your ear. Sonical have partnered with Segotia [segotia.xyz] who specialise in neurotechnology coupled with audio processing; the partnership will open up a host of facilities. Sonical and Segotia will create the hardware and software which differs from other developer’s offerings which come with fixed applications that cannot be changed or added to. Sonical and Segotia will develop a hearable that works on an open platform operating system, allowing app developers to add their own content, and offer the end user the ability to select apps based on their requirements, much like a smartphone. Hearables are blurring the line between
References
hearing aids and earphones, since augmented reality is utilising hearables to allow “hear through” with these devices, meaning that everyday sounds can be amplified and enhanced, becoming a kind of smart hearing aid. Recently the FDA, in the US, have approved the purchase of hearing aids over the counter without prescription. 7
This opens up the market for a device that will assist people that are hard of hearing and cannot afford the cost of traditional hearing aids and, as a result, have to suffer. Hearing loss has been reported to be the third most common physical condition and is linked to depression, anxiety, and dementia, amongst other health issues.
Due to the convenience factor, headphones continue to grow in popularity and research is ongoing to ever improve sound quality and add features to further enhance our lives and our listening experience.
1. https://www.prnewswire.com/news-releases/headphones-market-to-record-usd-18-45-bn-incremental-growth-driven-by-increasing-penetration-of-smart-devices--technavio-301647450.html
2. https://www.grasacoustics.com/files/MiscFiles/Cases/CA_ImprovedMeasurementofLeakageEffects_Harman.pdf
3. https://acousticstoday.org/he-perception-and-measurement-of-headphone-sound-quality-what-do-listeners-prefer-sean-e-olive
4. https://akg.com
5. https://www.canford.co.uk/Products/54-082_SENNHEISER-HD-400-PRO-HEADPHONES-120-ohms-single-sided-3m-coiled-1.8m-straight-cable
6. https://www.theguardian.com/tv-and-radio/2022/mar/02/podcasts-headphones-perceived-intimacy-host-increased
7. https://www.fda.gov/news-events/press-announcements/fda-finalizes-historic-rule-enabling-access-over-counter-hearing-aids-millions-americans
• No loss of audio clarity
• Protects from hearing damage
• Fitted in-line or discreetly within the earcup
• Fast turnaround – evaluation, fitting, calibration, test
Find out more at www.canford.co.uk/ Hearing-protection-and-noise-control
Telmaco S.A. is a leading European Audio Visual and Broadcast Systems Provider and Integrator located in Athens, Greece. The company has been operating very successfully for many years in Greece and Cyprus, with a branch office in Thessaloniki, Northern Greece. In recent years Telmaco has expanded operations internationally and is involved in Turnkey System Integration projects in Northern Europe, the Balkans, Middle East, Asia and Africa.
Telmaco is active in 3 main areas:
1. Audio Visual and Lighting Systems
2. Broadcast Television and Radio Systems
3. Communications Systems and Test Equipment for RF and Telecoms
Using their highly skilled personnel, Telmaco can design, supply, implement, and support complete turnkey systems. Telmaco’s experience of over 45 years of operation, plus their financial credibility, guarantees the smooth implementation and support of even the most demanding and prestigious of projects.
Telmaco enjoys the collaboration and partnership of most of the major manufacturers in the industry. Building on close relationships with both their technology partners and customers enables the right flow of information and technological know-how necessary in order to design the appropriate solution for each requirement.
Telmaco and Canford have been working together since Canford was founded in 1976. From cables to connectors, racks to connection panels, studio furniture to lights and clocks; Telmaco always use Canford products in their installations and always recommend appropriate Canford products to clients. This long-standing relationship has been incredibly beneficial for both companies.
These are a few of Telmaco’s recent projects in which Canford products have been essential:
Telmaco were asked to install a large amount of equipment at the Ministry of Civil Protection, mainly for various crisis rooms. These rooms were to contain large video walls which needed to be able to display camera and data feeds from all of the various departments. This meant they could be organised into one unit when crisis events occurred. Barco Unisee video walls were used due to their exceptional resolution and contrast, which makes it safer and easier for the operators to be able to work long hours. These video walls receive a 4K@60Hz video signal, so Canford’s line of optical HDMI cables were used as they
not only provide great resolution but are also armoured. This means there would be no problems when installing the cable and the client could rest assured that any future damage or wear and tear would be very unlikely.
Each room also had a rack that contained all of the workstations and KVM extenders, which were also sourced from Canford, alongside all of the necessary rack accessories, shelves, cable trays, mains distribution units, and rapid assembly panels for the breakout connections. For this installation, Telmaco won an accreditation from Innovation Awards 2023.
We use Canford a lot! We know the quality is always great, quotes for the products are competitive, and shipping is always on time which is incredibly important as we are usually working to a tight timescale.
OTE TV is one of the largest subscription channels in Greece. Telmaco provided, and installed, a large amount of studio equipment from Ross and Clearcom, consoles from Lundhalsey, and routers, cameras, and control units from Grass Valley.
Because of the challenges that come from working in a 24/7 live studio environment, Telmaco opted for camera cable from Canford’s line of SMPTE hybrid fibre cables. This gave the client peace of mind that the cable would stand up for many years to come, with no faults, even though they would be worked incredibly hard. In the main apparatus room, Canford was again used for power distribution units, video jackfields, and termination panels among other things.
Open TV is a new, free-to-air television channel that has recently opened in Greece. As usual, Telmaco were involved in the project from very early on.
Open TV was to be built in a brand new, purpose designed building and would broadcast a wide range of content; everything from large, live broadcast sound stages to news bulletins and sporting events.
As the cameras in this type of environment are moved around a lot, it is easy for cables to become damaged or worn. For this reason, Telmaco again opted for Canford’s SMPTE hybrid fibre camera cables in order to mitigate damage as much as possible.
The same cable was also used for long-run connections from the studios to the control rooms. Sometimes these runs were over 300 metres, and Canford’s optical cables posed no problems. Canford’s optical HDMI range of cables were used to send signals to the video walls that had been built on the sets of the studios.
Astarti Productions OB Vans are a large provider of Outside Broadcast vans for live events such as music concerts, football and other sports fixtures, and political assembly live broadcasts.
Once again, Telmaco opted to use Canford’s SMPTE hybrid fibre camera cable, this time on cable drums, as reliability and durability is essential during live events.
As these events are held in all kinds of weather conditions, the cable and equipment have to be able to endure very harsh environments and be able to be deployed, and then packed up, many times over. Canford also provided video and audio patch panels, which provided stable connections in all conditions.
The development of Network Audio / AOIP has been slowly progressing in the background over the last few years and is now a big part of the live sound industry. This progression has been slow for several reasons and the IEEE standards bodies have been cautious in their approach, but standards have been developed based on their research and recommendations.
Now that AOIP has become more accessible, reliable, and affordable, training (or lack thereof) is becoming a key issue. Training is a little thin on the ground currently and
this has led professionals, like me, to lean on podcasts, online resources, and manufacturer documentation. As the next generation move into the industry, troubleshooting network problems in a live environment will become much more commonplace and the knowledge required is perhaps best learned through specialised training courses, as well as practical application. I hope to see the development of this kind of education increase steadily over the coming years, otherwise we may end up with a supply-over-demand issue.
by CanfordBeing in a high-tech industry, we’re often eager to promote and use the latest technology in the AV system designs we propose to clients. There’s a sense of excitement, even pride, when we introduce the newest products or software but, sooner or later, the initial excitement dwindles, and the technology will only survive the test of time based on its overall practicality.
For example, analogue products are no longer frowned upon like they were ten years ago when digital solutions started to emerge. The advantages of digital solutions were indisputable but, at the same time, analogue signals can travel much greater distances, and do it cost effectively. Today’s system designers recognise the feature strengths that each technology has to offer. Often, it is a combination of technologies that provide the best value to a specific application. Simply put, if a technology makes good sense, use it. That is certainly true of RDL’s Format-A products, which have gained considerable popularity since their introduction.
Format-A is RDL’s exclusive audio transmission solution that sends, receives, and distributes short and long-distance signals over standard CAT5, 5e or 6 (CATx) twisted pair cable. The three wire pairs in each cable, called Pairs A, B, and C, are used to send up to three analogue audio signals. The fourth pair is reserved for 24 Vdc power.
Currently, there are almost 80 different endpoints available from RDL, which are categorised into Senders and Receivers. These modules offer standard audio connectors and/or removable terminal blocks that support various audio signals including mic level, line level, balanced, unbalanced, mono, and stereo. In addition, RDL also offers Format-A audio amplifiers, headphone amplifiers, mixers, selectors, distributors, loudspeakers, Bluetooth interfaces, and more. The solutions are provided in a variety of form factors for mounting in walls, cabinets, racks, and at other convenient locations.
Some modules use 1, 2, or 3-Pairs, which allows for up to three Senders and three Receivers to be looped together on each home run cable. This provides easy system expansion
and incredible design flexibility by allowing you to locate each input, or output, exactly where it’s needed.
Although they don’t operate on a network, Format-A systems do resemble audio network systems where they use the same standard CATx cables to send and receive multiple audio signals plus power. This similarity will be very familiar to integrators, which makes installation quick and easy, whilst also saving time and reducing labour costs. Just like the high fidelity associated with audio networks, these products are engineered for studio-quality performance, making them equally suited for high-end broadcast and recording studios as well as standard commercial projects.
Another significant feature is that Format-A’s signals can span up to 900 metres (3,000 feet) or more, depending on the wire gauge of the CATx cables. This far exceeds a network’s 100 metres distance limitation between hubs. This distance is achieved, in part, by converting all source signals to balanced line-level audio. Balanced signals are extremely noise resistant, making them ideal for short and long-distance applications.
Of course, DC power won’t travel as far. Typically, distances of 250 metres (800 feet) can be safely achieved before the voltage naturally drops, or decays, to an unusable level. For this reason, RDL offers several Format-A power options. Most modules have power jacks for directly connecting external power supplies. Since modules can also be powered through their RJ45 port, power supplies can be inserted at the sending end, the receiving end, or both. If the cable distance is greater than 250 metres (800 feet), simply install a power supply at each end. Or you could use one of RDL’s Format-A Power Inserters, which will power the Senders and Receivers from
anywhere in-between, wherever electrical power is conveniently located.
This year, RDL introduced three new 24-Channel Senders and Receivers. These large channel products are designed to integrate multiple Format-A endpoints to industry-standard Digital Signal Processors (DSP), audio mixers, or power amplifiers. These products are eight-section audio chassis that support up to eight Format-A home run cables. Each section supports up to three Format-A signals through an associated RJ45 port and provides three line-level inputs or outputs on removable terminal blocks for connecting to standard audio equipment.
This remarkable system has been used in many interesting installations over the years. Here are a few examples that will hopefully inspire some project designs of your own:
• A college wanted an alternative solution to expensive fibreoptic cable for delivering two paging signals to two zones in a new music hall. This facility was located on the opposite side of a sports field over 750 metres away. Using one TX-TPS3A Sender, the signals were sent over one CATx cable to two TX-TPR1A Receivers. One Receiver was set to receive signals from Pair-A, the other from Pair-B. The RJ45 Loop-through port on the first Receiver made it easy to distribute the signals to the second Receiver located in the next zone. Pair-C remains available for any future needs.
• A ski resort needed to send background music (BGM) and live page alerts from their lodge to the ski-lift terminal located over a kilometre away. The BGM player and paging station’s signals were fed into an ST-VP2 Automatic Ducking Module, which allows live pages to instantly override the BGM signal. The output of the ST-VP2 was fed into a TX-TPS1A Sender, which sent the signal over one CATx cable to a TX-TPR1A Receiver located in the terminal. The Receiver’s output fed the local power amplifier.
• A three-story office complex wanted to distribute facilitywide paging to separate businesses occupying each floor. Three paging sources were fed into one TX-TPS3A Sender. Its RJ45 output was fed to a TX-TPR1A Receiver on one floor then, in turn, was looped to additional receivers on the other two floors. By setting each Receiver to a different pair (A, B, or C), each floor receives its own paging source. The Receivers on each floor delivered line-level paging audio to the local amplifiers. An All-Call page, initiated at the main paging station, could page all floors simultaneously.
There are so many Format-A design possibilities, yet RDL recognizes that some applications need to make signal routing changes. Therefore, RDL developed several Format-A to Dante conversion interfaces that allow signal routing changes to be made using “Dante Controller” software. As Format-A endpoints are less expensive than Dante endpoints, these interfaces allow very cost-effective Dante systems to be designed. You can also add Dante routing functionality to existing Format-A systems, now or in the future, allowing customers to expand their systems when the time is right. And all this is done without wasting any products, related expenses, time or installation labour. No other manufacturer has such a comprehensive, full featured system in place, which is a primary reason why RDL’s Format-A system has truly stood the test of time.
Canford’s team has extensive knowledge of Format-A products and are ready to support their clients with practical advice to get the best out of every system. Canford has invested heavily in their recruitment and staff training to ensure that they are at the forefront with RDL’s industryproven products.
When a large client had issues with some fibre cable assemblies and turned to their supplier Systems Design for assistance, there was only one name on Mr Hamza’s lips.
We asked Vita Gorkina (International Business Development Manager for Canford) to get in touch with Mr Hamza, Technical Manager for Systems Design, to find out more about the project and the reasons why Canford is always their first port of call.
Founded in 2003, Systems Design (based in Egypt) is a leading systems integrator in broadcasting and media technologies specialising in Playout Centres, Media Asset Management, and Archiving Solutions. They have grown into a team of thirty and have gone on to work with DMC, CBC, MBC-Egypt and many other large clients around the world.
“We have a lot of experience in building Studio Complexes and Playout Centres, and have provided several turnkey solutions. We cover almost all broadcast applications including Newsrooms, TV and Radio Master Control Rooms, Virtual and Augmented Reality Studios, as well as Professional AV Solutions”, said Mr Hamza, Technical Manager for Systems Design. “When we at Systems Design put together the spec for our projects, we regularly turn to Canford due to their wealth of experience and stock availability”.
“We had a client”, continues Mr. Hamza, “who had a problem with a large amount of fibre cable. They tried to get it repaired but kept getting turned away. When they approached us about replacing the entire twenty-kilometre cable line I knew immediately who I was going to trust with this”.
20,000 metres of fibre cable were required and, as is usual in this type of situation, it was required very quickly. To avoid disruption to this $500,000 project, sixty 400-metre drum assemblies were needed as soon as possible. We managed to get ten of these produced and ready to go within a week, with the rest following less than a month later.
“This is why we rely on Canford”, states Mr Hamza, “you always manage to find a solution”.
We first set up our Fibre Termination service in 2016 and it has grown exponentially since then. In order to keep ahead of demand, we expanded our facility (located at our Washington, Tyne and Wear headquarters) in early 2020 and our teams worked tirelessly throughout the COVID-19
pandemic so that we could continue to fulfil orders, such as this, with very short lead times. It was at IBC where Mr Hamza originally spoke to us about our fibre operation and cited that the “fast delivery and the Canford quality” were the main reasons for choosing Canford when it comes to fibre assemblies.
“Canford’s service is very professional, and their team is highly responsive in responding to inquiries and clarifications”, concluded Mr Hamza.
We’ve now made it easier than ever for customers to make use of our fibre termination service, as John Driver (Head of Design and Fibre Technology) explains:
“To try and make things easier for the customer, we have created fibre assemblies with standard product codes which makes ordering significantly easier, and much quicker. Amongst the product range you can now find standard FUW – PUW SMPTE cable assemblies with Draka, Belden and Furukawa, either with or without cable drums. We’ve also added a new series of breakout cables which take either SMPTE, opticalCON or HMA and breakout on tails to LC, SC or ST connectors. These breakouts make testing much easier by allowing connection direct to a Light Sources or OTDR.”
20x
Lemo 3K.93C FUW-PUW, Belden 7804EPU 9.2mm SMPTE, 200m, CD3 drum (50-2054)
40x CABLE DRUM ASSEMBLY
Lemo 3K.93C FUW-PUW, Belden 7804EPU 9.2mm SMPTE, 400m, CD3.45 drum (50-2057) Find out more
We are pleased to reveal that we have been working hard in the background to come up with a Canford developed SMPTE cable. We have undertaken extensive research and development in order to create a cable that we are proud to put our name on.
Manufactured to the SMPTE311M standard for HDTV camera connections, our cable is a hybrid of single-mode fibre optic and copper cores. Perfectly suited for handling
video, audio, and control signals, as well as providing power between camera and base units, the Canford SMPTE is compatible with many industry-standard hybrid connectors, including those made by Canare and Lemo. With a maximum optical attenuation of 0.50db/km (@ 1310nm), the Canford SMPTE cable offers a comparable alternative to some of the biggest brands in the industry.
And last but not least, for the outer sheath, we explored several different options and eventually settled on a robust, but flexible, polyurethane which makes this cable perfect for both OB and studio floor use.
Alan Wilson formally accepted the job of CEO of Canford in July this year. He’d previously been installed as Acting CEO in order to provide stewardship over Canford during the difficult time of Iain Elliott’s short illness and untimely passing. Being brand new to the Canford team myself, I wanted to take this opportunity to sit with our new CEO and find out who he was, where he came from, and what his favourite colour is…
How did you get started at Canford? And how did you end up as CEO?
I first started out as a Purchasing Apprentice at Canford in July 2000. Over the years I have progressed through the company and held various positions in different departments. This has given me great insight into how different areas of the business work, and the unique challenges that each department faces.
After being successful as an apprentice, I was taken on as a full-time Buyer within the Purchasing team. After a short time away from the business in 2012, I returned as the Purchasing Manager. I also became responsible for overseeing the scheduling operation for the Production department. Eventually I became Acting and Deputy CEO. This was a very tough period for both the company and I, as this was around the time that Iain had been informed he was terminally ill. He sadly passed away a short time later. In July of this year I was offered, and accepted, the position of CEO on a permanent basis.
During your time as Acting CEO, what led you to accept the job on a permanent basis?
To be honest, it was the staff around me. The amount of support I have received from everyone connected to the business was, and continues to be, fantastic. As CEO there is a lot to learn, and many new challenges every day, but the incredibly supportive workforce around me makes things a lot easier. There are thousands of years of experience at Canford, and I’m fortunate enough to be able to draw on all of it.
During your time at Canford, what has been the biggest change?
Two big changes really spring to mind.
The first is when we relocated our manufacturing facility and incorporated it into our Washington HQ. It had previously been in another building on the same industrial estate but, after a strategic review of all Canford facilities, we were presented with an opportunity to move it in house. We worked with a specialist consultant who designed, and installed, a bespoke production facility which expands over two floors. This has brought many benefits including a much more streamlined workflow. From the receipt of raw materials, to production, testing, packaging, and then finally back into the warehouse for despatch; having everything under one roof continues to save many hours of logistical work and has made communication between departments much more efficient.
That same year also saw us investing heavily into our warehouse infrastructure, all part of the same project.
The second big change was in 2019 when the business was transferred to an Employee Ownership Trust (EOT), an incredible gesture by the former shareholders. Employee ownership is on the rise as businesses like ours continue to see the benefits. Research into the performance of employee-owned companies over recent years has concluded that
employee ownership typically results in:
• year-on-year productivity increases,
• transparent and clear inter-company communication,
• improved staff retention and morale,
• better engagement with local communities,
• and the tendency to take corporate social responsibility more seriously.
Something that was very important to Iain, and therefore baked into the trust deed, was that Canford was not to be sold or moved away from the North East for at least 125 years. This ensures that all Canford staff, many of whom have been with us for decades, continue to be well looked after and supported. He had complete trust in our ability to run, and further develop, the business and to look after our customers, all whilst retaining the character that makes Canford truly unique.
I want to get to know our CEO outside of Canford. How do you spend your time when not working?
Well, playing football, or watching my daughter play football, takes up most of my free time. We also have a Whippet called Norman, so we are all often found on long country walks. I say all… usually I’m tasked with carrying our son.
You recently took part in the Great North Run too. How did that go?
I enjoyed it, and did okay, but it could have been better! I suffered an ankle injury three weeks before the big day which meant I couldn’t do any training on the lead up to the event. I’d also planned a summer holiday… badly. I returned from a week-long, all-inclusive holiday five days prior to the race.
I felt okay for the first four miles, but then the pain started to creep in. Bad cramps in both hamstrings from mile six resulted in a finish time of two hours and thirty-seven minutes; not bad considering I had to walk the last two miles.
The most important part of course, was that I did finish and that, in the process, I managed to raise a decent sum of money for cancer research; a charity which is very close to my heart.
I bet all of that exercise makes you hungry. What is your favourite food?
Sunday dinner with all the trimmings!
What about your favourite colour?
Black and White (#NUFC). As a Newcastle supporter, there was no other option really.
What makes us unique is that over 40% of our business is our own manufactured product. Canford own brands have continued to go from strength to strength and I’m sure this is where future growth will come from.
Our in-house fibre termination service has also been incredibly successful and contributes to the business significantly. Interest in our service continues to grow and we are looking into how we can best support our customers; we will soon be investing further in our facility in order to meet demand.
Are there any challenges you see for Canford, or the industry as a whole, on the horizon?
This is always the hardest question to answer. There is so much uncertainty at the moment. With the threat of recession looming over us, the wild fluctuation in currency values, the short supply of raw materials, and, of course, the geopolitical tensions and conflicts affecting the whole world, it really is hard to say.
If Covid taught us anything however, it is that Canford, and the industry as a whole, is incredibly resilient, and we’ll be doing what we can to support our customers, and our employees, through whatever may come next.
And lastly: imagine bumping into yourself on your first day at Canford back in July 2000. What advice would you give to your younger self?
I don’t think I’d say anything. I’m a great believer in things happening for a reason. Maybe I’d remind myself of that.
Another eventful year, and an exceptionally busy one! The diminishing threat of Covid meant that schools were opening their doors for visitors, and I could once again begin a series of activities to promote the four pillars of STEM (Science, Technology, Engineering and Maths) to their pupils, which unfortunately resulted in me contracting the virus in July.
STEM is an organisation that works in collaboration with the UK Government, employers (large and small), and educational establishments. It recruits “Ambassadors”, who give their time freely, with the aim of spreading the word about what the study of the four pillars can lead to (in terms of career path). Being a STEM Ambassador myself, and therefore visiting a variety of schools, has given me the opportunity to not only promote STEM activities and careers, but also Canford and what we have to offer.
...in 2010 the Labour Force Survey found only 10% of those working in engineering were female. The most recent survey shows that it has risen to 16% so although progress is being made it is painfully slow.
I have been asked why we sponsor these two schools in particular. EDT approached us and mentioned that these two schools were still looking for sponsorship and if we’d be interested. I was already currently involved with nine other schools around Newcastle and the North Tyneside region, and was devoting a significant amount of time to them; so I did have some early misgivings about sponsoring two fee-paying schools. However, the late Iain Elliott and I both recognised that women are totally underrepresented in the various engineering disciplines, and that companies such as Canford have a duty to try and rectify this situation.
John Slider, Canford Community AmbassadorThe engineering professions have historically been male dominated. In 2010, the Labour Force Survey found only 10% of those working in engineering were female. The most recent survey shows that it has risen to 16%. So although progress is being made, it is painfully slow.
Last year, Canford sponsored two schools as part of our work with the Engineering Development Trust (EDT): Dame Allan’s (who went on to win an award for their project), and Newcastle High School for Girls.
Each and every one of us at Canford, and in the wider industry, has their own special memories of Iain. One of the things I think of when I think of Iain, is of the passion he shared with me for encouraging young people, especially
females, to enter the world of engineering. This is why we jumped at the chance to get involved with Dame Allan’s and Newcastle High School for Girls.
One of the more disadvantaged schools that I work with asked if I would write a grant application for them. They have since been awarded £3,000 to spend on a project in which the children will create their own vegetable garden, learn how to recycle waste, and how to use rainwater in a variety of ways.
Over the past 12 months I have been very encouraged by the support I have received from my colleagues at Canford.
Jen Cassidy, Creative Designer in the Marketing Department, put together a video showcasing Canford and the various products we manufacture, plus an outline of the types of careers that Canford has to offer. This has proven invaluable in assisting the many presentations I give to schools.
The Engineering Development Trust held an end of year presentation and awards ceremony, which took place at Newcastle University, and I was joined by Chad Phelps and Katie Slater from our engineering and technical support team. They set up a stall showcasing our Green-Go and NEAL products, which attracted a lot of interest from the pupils attending the ceremony, and I know that Chad and Katie were very impressed by the quality of the projects submitted by the schools too.
John Driver, our Head of Fibre and Design, has been superb in showing the visiting schools around our facility and sharing
his vast engineering knowledge with them. John also came up with a great idea for a careers presentation, and I look forward to working with him on its production.
October 2022 sees the beginning of the new school year and we will, once again, be working with the EDT and many schools. I’ll be calling on my colleagues for their strong support and I know I’ll continue to receive it.
I fully anticipate that we will host a number of school visits and that we will, hopefully, be able to resurrect teacher visits to Canford HQ. Teachers play a vital role, perhaps the most important, in spreading the message of what a career in engineering can offer.
Canford’s Green Group brings together members from around the business to discuss, and action, eco-friendly initiatives that can help to reduce our impact on the planet. Chaired by Karl Thoroughgood (Site Services and HSE Manager), the team meets once per month, and I was lucky enough to sneak into a recent meeting to find out more about the latest Canford environmental initiatives.
It turns out that we have quite a lot going on! We have a couple of major projects in the works including:
• Replacing the entire roof (so that’s what that banging is)
• Covering a large portion of the roof with solar panels
• Refreshing existing, and introducing new, insulation
• Upgrading heating systems.
On top of that we are also exploring the possibility of:
• Thermally insulating, and cladding, exterior walls
• Installing rain harvesting and water reuse systems
• Improving glazing insulation
• Installing electric vehicle charging points (to encourage employees to invest in electric vehicles)
• And many others.
But it’s also the little things that can mount up and have a significant impact. That is why we’ve:
• Recently replaced almost all lighting with LED (using only a third of the energy we were previously using, and without giving off any heat). LED light bulbs last significantly longer than incandescent, greatly reducing waste.
• Installed PIR / motion-detection lighting in all communal areas (and are currently trialling this throughout other areas of the business).
• We’ve had boiling water outlets installed in communal kitchens, replacing the need for energy-hungry kettles, for years. On top of that we recently upgraded all five of these to smart versions which are programmed to only run during business hours.
• Encouraged use of public transport by making it easy for our employees to pay using a salary sacrifice bus-pass scheme.
• Adopting the government’s Ride to Work scheme to encourage employees to lessen their use of private vehicles even further by investing in quality bicycles.
• For those who can’t cycle or use public transport, we encourage car sharing where possible and many of our employees run their own car-share scheme which reduces commuter emissions, and has a positive impact on personal finance too.
That’s not all, we’ve been busy in the warehouse too. Busy:
• Transitioning over to pure recycled and recyclable air-fill packaging. Our newest air-fill packaging comes from 100 percent recycled sources and can, in turn, be entirely recycled…multiple times
• Exploring options to eliminate plastic altogether in our packaging by using alternatives such as paper, and compostable ‘plastics’ made from renewable sources (such as wood pulp).
We are committed to sustainable business practices and are set to invest significant amounts of money over the next few years. The Green Group has serious aspirations to expand the size and scope of the operation and will be recruiting other members from around the business in the near future.
Canford were one of the first independent companies in the UK to switch to lead-free solder. In 2003 we took part in a group study comprising of companies based all around the EU. We experimented with lead-free solder in our manufacturing process, reported results, and even submitted products for age testing (where the product is heated and cooled repeatedly, which encourages damage to solder joints). The results were very positive, and we migrated fully to using lead-free solder by the end of 2003. Not only is lead potentially incredibly harmful to health, but it’s also bad for the environment. RoHS (Restriction of Hazardous Substances) legislation came into effect in 2006 which made lead-free solder a legal requirement across the EU.
We asked Vita Gorkina (International Business Development Manager) to sit with David McKeown (Project Estimation & Design at PSI) to find out more about the incredible project they just completed: the Grand Opera House Belfast.
PSI Lighting Rigging and Audio was established in 1996, with the aim of raising, and developing, the standard of production within the performing arts and entertainment sectors in Ireland. Since then, they have gone on to provide technical solutions that meet the growing demands of the corporate, arts, and entertainment industries for high-quality events delivery. With dedicated departments providing expertise in audio, lighting, rigging, and training, they continue to exceed expectations by paying close attention to the details of each project, and by always upholding the highest levels of professionalism. Using this approach, they have successfully established themselves as Ireland’s principal technical production company. Located in Belfast and Dublin, PSI holds the largest stock of professional lighting equipment (for sale or hire) to be found anywhere in Ireland.
We’ve known each other for several years now David, but how long have you been using Canford?
I’ve personally been using Canford for the past 25 years, so a little before your time Vita! There is always a solution within the product range, and the service I receive is always excellent; the staff really know the products and the industry.
If products are out of stock, or have a long lead time, the team are always incredibly quick to offer alternatives or work out a solution, the staff really do know their stuff, which isn’t necessarily true of all vendors. Also, the portfolio of products available from Canford are of the highest quality.
Come on then, spill the beans. The Grand Opera House looks incredible, I’d love to know more about it.
The Grand Opera House Belfast is a Frank Matcham designed theatre which originally opened in 1985. The theatre, stage, auditorium, and all public foyers were stripped back to the bare bones of the building. PSI were responsible for the delivery, installation, and implementation of every single technical service including production lighting control, house lighting, sound reinforcement, comms, paging, cue lights, and stage engineering.
The main contractor took possession of the building in January 2020, and we were ramping up work when Covid hit. In addition to this, we had the problems of Brexit and the Northern Ireland protocol, so to say this project was
logistically challenging would be a serious understatement. Along with these external obstacles, we also had the issues of installing modern infrastructure within a listed Victorian building. Placing containment routes and keeping separation between LV and ELV services, all whilst trying to maintain the original aesthetic of such a wonderful auditorium, posed some significant challenges.
It certainly sounds challenging, but the results are amazing. It was extremely challenging, but we did achieve our goals and the auditorium looks fantastic. A lot of the technical staff from Northern Ireland have worked in the Grand Opera House and all have a special affinity with it. It is an intricate part of Belfast and intrinsically linked to its culture, its people, and its history. All at PSI feel a real sense of privilege and pride to be part of the team that has brought this elegant old lady back to her best.
When working on a project like this, who would usually specify the equipment for those projects? And what are the main drivers behind product selection? All of our projects are usually split 50/50 between our in-house team and, in this case, a Theatre Consultant. The principal driver for product selection is always: ‘will it do the job’? Next will be the cost, and then the level of technical support that is available from the manufacturer or distributor. Regarding cost, we will always consider the secondary cost implications. For example: the ease of installation, the longevity of the components, etc.
We asked Canford to supply some of the cable, all of the patch field and patch cables, as well as tasking you to come up with a solution for getting AV services to the IWB mounted on the balcony façade.
It’s nice to know we had a part to play in this amazing project. Have you been back to see it since it reopened?
Unfortunately not. I haven’t been back to see a show as of yet, but family and friends have, and they absolutely love the refurbishment.
You mentioned earlier that you started the Grand Opera House project just before Covid hit. How was the project, and business as a whole, affected?
Business has actually been really good over the last couple of years. We were lucky that we had the Grand Opera House project, and another large project, to work on during the pandemic. Since that ended, we’ve been very busy with projects all over the island of Ireland.
And lastly, do you see us working together for another 25 years?
Provided Canford doesn’t change their core business model, and the principles that they were founded upon, then I cannot see any reason why PSI and Canford will not continue to work together long into the future.
This year, our very own Erika Dobie (UK Business Development Manager) celebrated 20 years of working at Canford. Knowing that she has seen and experienced many changes in the industry throughout her successful career, we wanted to catch up, and get to know a little more about her.
Tell us a little about yourself, who is Erika Dobie and where does she come from?
I grew up in a small village in Bedfordshire where I had a fairly strict upbringing. This ultimately served me well and taught me the right values in life. Initially I was shy and unassuming and quickly learned the value in respecting other people; treat others as you would wish to be treated. I’ve always had a natural interest in people, and my various roles and life experiences have moulded me into the person I’ve become. My younger years weren’t at all easy, however, what hasn’t killed me has certainly made me stronger!
originally?
It seems like a world away since the day that I was introduced to the industry, and found my vocation in life, quite by accident really, it’s strange to think that it very nearly didn’t happen…
After having been made redundant from a previous job in 1999, I was offered a temporary position of sales support via an agency, working for Yamaha Music UK within the Pro Music department based in Milton Keynes. The role included the processing and expediting of sales orders for Yamaha dealers across the UK and providing support for the regional managers. My eyes were opened to the complexities of a drumkit, and the vast number of component parts involved! The combination of this, in addition to the seemingly complicated in-house computer programme, was enough for me to immediately put in a request with the agency to place me somewhere else. However, they encouraged me to stick it out for a further couple of weeks and, looking back, this was the best piece of advice that I could have received during my career.
Everything started to fall into place shortly afterwards and I grew to love working with the great team of people there, as well as developing some strong relationships with the dealers. I quickly discovered that it is an industry like no other, full of characters, business partners who become lifelong friends, and a unique and unrivalled close-knit community where everybody knows each other. I was introduced to dealer events and exhibitions, which were to become very familiar experiences over the years. I had to learn how to drink! I remember my time at Yamaha with considerable fondness, with lasting friendships and very happy memories indeed.
I was lucky enough to meet my husband there who was based in the North East of England and ultimately the reason for me being here today.
I joined Canford in the summer of 2002 after having relocated from the south. An unexpected but easy decision, yet scary at the same time – I was completely ready for the next chapter of my life. Both Canford and the North East welcomed me with open arms and I can honestly say that I have never looked back.
I was already familiar with Canford as a Yamaha dealer, although its business model, involving an incredibly diverse range of markets, was foreign territory at that time. There is cross over with the music industry, but it’s a very different beast and it was a whole new learning curve. My role was to help with the newly established Quotations department, dealing with project enquiries and identifying further business potential. This was my introduction to the world of broadcast and AV system integration and getting to grips with our own printed catalogue containing 16k+ of manufactured and distributed products.
After a while, an opportunity became available for a Key Account Manager which involved occasionally visiting customers, a role of which I was completely ready for and one that I fully embraced. This helped to further evolve and cement customer relationships as well as my own development. I received a taste of life on the road, and it prepared me for what was to follow.
In 2010, the company was developing a new sales strategy and approach. It was decided that we would invest in a field sales team with regional coverage, and I was chosen to become a home-based Field Sales Executive primarily covering the North, Northern Ireland, and Scotland, whilst still retaining many accounts in the south with whom I had already developed strong relationships. It was a role in which I would have autonomy and the opportunity to find new and grow existing business. Having been a company that hadn’t previously had the experience of a proficient field sales team offering full coverage of the UK, it came with some challenges and frustrations. Canford was perceived to be expensive and the ‘go to’ for the widgets and problemsolving products that couldn’t be found elsewhere. With Canford’s existing reputation for quality and having the right product portfolio, pricing, and service levels, I knew that we had the capability to be so much more to our customers.
So how did you go about changing this?
It is hugely important to invest time with our customers, and to develop a far greater understanding for what they do. Projects such as the new range of EMO Power Distribution panels and floor boxes is testament to this; the range evolved after thorough research with customers and users. Teamwork back at base was fundamental to the process, and further examples have since followed, together with making customers aware that there are pricing structures tailored to suit and support what they do.
The Covid period took me off the road and provided me with a far greater insight into the opportunities that we were lucky enough to receive. Proactivity and service levels were ramped up to a whole new level and, as a result, we are seeing many new customers as well as repeat business. This has allowed us to re-evaluate our sales strategy and has provided us with a clear vision for the future. We have never worked so well together as a team. This, together with our current success, would be something of which I know that our dearest co-founder Iain Elliott would be so immensely proud. I know that he will be up there watching with interest and with a smile on his face.
The discovery and development of Green-Go Digital has opened doors for us within the live events and touring markets. This was a complete game changer to Canford when we acquired exclusivity. Green-Go was a relatively unknown brand in the UK which John Driver (Tech Manager) and I took out on the road to introduce to multiple customers within the industry. It has since gained significant traction and has helped us to develop further into the live events and touring markets. It has involved a phenomenal amount of time and investment, which really has paid off.
This year I am proud to celebrate my 20th year with Canford. As I mentioned at the beginning, my philosophy in life from very early on has been to work hard, be honest, respect others and treat people as you wish to be treated. It’s served me well over the years and, with the support of my colleagues and customers, I very much look forward to what the next few years will bring.
What roles have you had within Canford and how have you progressed through the company?
Have there been any products or services that have assisted in any further development or introductions to new customers/markets?Gavin Drake (Sales Director), Erika Dobie (Business Development Manager) and Alan Wilson (CEO). Erika receiving her 20 Year Service award.
Whether helping to identify and purchase (or hire) cutting-edge broadcast equipment needed to deliver stunning 4K footage, designing innovative broadcast systems architecture to streamline workflows, or finding and equipping outside broadcast vehicles, ES Broadcast have you covered.
To find out a little more about the ES Broadcast operation, and to pick the brains of an industry veteran, we sent Ian Sadler (Business Development Manager for Canford) to meet with Joel Cullen, Engineering Manager at ES Broadcast.
Looking at recent projects, it appears to have been an incredibly busy time for you and the whole ES Broadcast team. How are things going?
Very well. ES Broadcast first established itself in the marketplace as a sales and hire company and has grown massively over the last decade; we now have one of the largest rental fleets of UHD systems cameras anywhere in the world. Five years ago, we set up our systems integration division, where I am the Engineering Manager, and we really hit the ground running. We must be doing something right, because we are constantly busy like you said; I barely get a moment’s rest!
With so much experience in broadcast, how do you feel the industry is developing and changing? Do you think your job as a Systems Integrator is going to evolve based on new technologies?
My job will remain very similar. It’s always the same; when technology has improved in the past, it’s always a little slow to fully take hold. That said, we are always looking to remain at the forefront, and we’ve invested a lot of time in understanding emerging technologies, especially cloud-based solutions. We’ve got accredited engineers who can install systems of that ilk; we are building an increasing number of remote cloud and virtual solutions for clients.
We’ve also expanded into other areas of broadcast too. With the popularity of the internet and YouTube, everyone is now capable of creating content; we find ourselves working with corporate clients of all kinds who require their own systems in place. Likewise with the livestreaming of events, such as gigs and concerts, over the internet.
YouTube aside, have you noticed much of a change in the industry due to the rise of the various streaming services?
There has been a real boom in building and creating new studios. All of those streaming services require a constant supply of content and, as such, the demand for production houses and studios is incredibly high. We are finding all kinds of niche little markets; we were recently involved in setting up a studio for the Wine Channel. There is a real boom at the moment, and long may it last!
complex requirements, we use a variety of the EMO MDUs too, as well as custom-branded jackfields and patchbays. Your support helps us to deliver our projects on time, every time. You know what it’s like, it’s broadcast! So, we are always up against hard deadlines and often have to turn projects around very quickly.
The last year or two has been challenging with component shortages etc. Has that affected you at all?
We’ve been quite fortunate with that to be honest. Over the years we’ve done some quite large decommissioning projects, which means we have a large store of quality broadcast equipment.
We’ve always dealt with Canford. You are always a nice bunch of people to deal with, a real sense of professionalism but with a friendly face. The website is really easy to use; prices, stock levels, everything you need, it saves us quite a bit of time. Any project we do has a component requirement from yourselves. Whether its clocks, lights, headphones…it’s not just the nuts and bolts and cable. We have our own branded Mains Distribution Units that you make for us, and for more
Most of our clients know the situation too, so they are tending to place their orders a little earlier than they usually would have done in order to mitigate for shipping delays, and we’re doing the same with our suppliers. Where there are gaps, we’ve usually been able to fill those with equipment we have in our store and, if needs be, we can swap them out at a later date. We’ve also been keeping a rolling stock of key pieces that we know feature in nearly all of our systems.
ES Broadcast and Canford have known each other for a while now, why do you keep coming back to us as one of your preferred suppliers?
I have spent over a decade studying and working within the live sound industry around the North East. I started out as a crew member and worked my way up to Sound Engineer, working in venues with 2,000 plus capacities.
As my career progressed, I decided to make the move to Canford Audio as an Audio & Video Engineer within the Technical Support department. My time here so far has not only allowed me to enhance my knowledge and skills, but also to continue working in the industry after the turbulent times of Covid.
In 2016, the proportion of women in the overall UK music industry was reported to be 45.3% - which had risen to 49.6% by 2020. Considering that I had only met one other female when I first started working in the music industry ten years ago, this is a very positive step. With the connections that Canford has built up over the years, and now working in a technical support role, I have a lot of optimism for the future of the industry as I have met with many people from many different backgrounds, including a lot more women and younger people.
As this is not the easiest of industries to work in, because it is one of the most economically sensitive and often deemed to be one of the most unstable, nurturing the initial curiosity, giving encouragement, and providing support where needed are just a few of the ways we can encourage young people to see this industry as offering a viable career.
Having spent so long as a live sound engineer (and continuing to do so) I’m often asked about what some of the most common challenges are:
When it comes to bleeding out monitors, the way I learned was to pick up the microphone and use your voice to identify the frequencies that are likely to feedback with that particular monitor. But, you also need to learn your personal tone of voice in order for that to work. As a female, my voice is typically a little higher in frequency range than a male’s, so hitting the low end can be quite difficult. As a result, I have to consider that there may be problems with frequencies during the performances that were below what I can actually reach.
A very common problem is communication. Whether you are an engineer or anybody in the tech team or crew, communication is key. You must communicate clearly with the team you have around you. If the day is going to be difficult, tell them and let them know why (in a diplomatic way). Otherwise, this can result in a disgruntled and confusing day all around.
The audience is a problem! This is a weird statement to make because the audience is the whole reason that the live industry exists. Humans are about 60% liquid, which makes them great absorbers of low to mid-frequencies and RF.
You spend all day prepping for the show. You have dialled in the PA so that it sounds epic. You’ve adjusted and tweaked the mix on the desk and scanned / synced all of your RF wireless systems for the day and everything feels perfect.
Then the audience comes in…where has all of the low / low-mid gone?!
If you don’t consider this when setting up throughout the day, then you can find yourself making quick decisions, drastically adjusting the mix, and scratching your head as to why RF signals are not getting where they should.
I was asked to pick the top five most essential Canford products for a live sound engineer. This is very hard to do as there are so many different things you might need day to day! But I just about managed.
The amount of times I’ve needed this on a gig. Having this in your back pocket can make you a real hero on the night!
This is something you may need over time. When I first started I had a pen and paper, to make a channel list, a jack adapter, and headphones. Over time your kit will grow, and you’ll need somewhere safe to store and transport it.
16-551
As audio over IP network becomes more and more common in the industry, one of the Canford Dante interfaces is becoming an essential part of my kit.
Another ‘hero’ item.
I consider this a real hidden gem.
20-073
46-539
This litter tone generator will help you with the day-to-day setup in the live environment. The 700hz tone will help clear any doubt about the route your audio is taking is clear, together with having an indication as to whether your line is receiving phantom power. This can be a real time saver.
38-072 38-076 25-064
At a sparkling awards ceremony on November 17th, Lucas made the whole Canford team incredibly proud by winning Apprentice of the Year.
We nominated Lucas for this year’s Sunderland Echo Business Excellence Awards, in the category of Apprentice of the Year, after an exceptional first year at Canford. Working in the Production team under the supervision of Production Manager Shawn Pretorius, Lucas has gone from strength to strength, leaving all colleagues incredibly impressed by his attitude, enthusiasm, and ability.
We are delighted that Lucas has been formally recognised and has received this prestigious award and would like to congratulate the runners-up in this tightly contested category. If the awards proved anything this year it is that the future of business in the North East is in very safe hands.
With fraud soaring, compensation claims at an all-time high, and the average disciplinary hearing or unfair dismissal costing companies thousands, impartially recording important interviews is becoming an essential way of working.
NEAL recorders are used by many law enforcement agencies and organisations around the world.
They are complex, precise machines which often take years to fully understand.
Lucas has successfully learned the art of making, repairing, diagnosing, and calibrating these machines in less than one year, prompting Canford’s Production Manager, Shawn Pretorius, to label him “an actual genius”.
Lucas was born in Tenerife but moved to the North East when he was nine. Despite doing well at school he didn’t really know what he wanted to do. He looked at his options and decided the academic path wasn’t for him, he wanted to do something practical.
After completing his Level 2 and 3 in Electrical Installation, Lucas began looking around for an apprenticeship, something to help him to make the next step. He wasn’t able to find anything and was steered towards a career in electronic/ electrical engineering. In September 2021, Sunderland College, where he continues to study, helped him to get an interview here at Canford, and we were so impressed that we quickly contacted him to tell him that he had been successful and wanted him to join the Canford team as soon as possible. Since then, he has really found a love for electronic engineering and appears to be a natural. His favourite part of the job is that it is so varied. Whether it is product design, testing, assembling, or troubleshooting equipment, it is the problem solving that really lights him up.
Since Lucas started working for me just over a year ago, I have been surprised by him almost every day. He’s a very intelligent, fast learning individual and is always keen to learn.
Lucas started working in our NEAL police recorders department about 7 months ago. Just to learn to manufacture these takes months but Lucas has already mastered building these and has also learned how to setup and test the units. This is the fastest I’ve ever seen anything like this happen.
Lucas has a very positive attitude towards work and does whatever he’s asked to do. Most importantly he will never do anything he’s unsure of without asking first.
Lucas is progressing faster than any other apprentice I’ve ever seen and I’m proud to call myself his manager.
Pretorius, Production managerAlongside these two key testimonials, from well-respected and senior members of staff, anecdotally his peers mention how he is calm, courteous, intelligent, and pro-active. He is never sat idling, waiting for instruction on what to do. Having learned so much about our NEAL recorders department, Shawn is looking at moving him around other areas of production so that he can experience other areas
Lucas started working in the NEAL test department and has been trained up on the full 9000 series, which includes two drive and three drive portable and “stand alone” recorders. Testing these recorders involves adjusting the BIOS settings, which can be quite complex, but Lucas picked this up straight away, finding his way around the menu with ease. Other parts to the test include setting voltages with a DVM and checking decibel levels with an RTS. He’s managed to learn and to use both bits of test equipment and rarely needs me now for direction. Setting up the recorders also involves programming ICs and entering various versions of software, including giving each recorder its own identity. Again, Lucas has learnt and managed this without problem.
Quite often the recorders have faults during testing and recently he’s managed to rectify some problems successfully without my help.
Lucas shows good initiative; knowing what to do next when these recorders are being manufactured in here. I’m just about to suggest doing something and when I turn around, he’s already onto it. Administration wise, he was quick to pick up the system of labelling and adjusting the job status on the Canford Production App.
As well as testing the recorders, Lucas has been building them, learning new skills like crimping and soldering. His crimping and soldering are good too. From coming in on a morning to going home on an evening, he never shirks and is always working.
If Lucas remains in here for a while longer, I intend on training him up on the service side of things (which are customer returns). I also intend training him up on calibration, as we calibrate a lot of our test equipment inhouse.
Lucas is always pleasant, polite and keen to learn new stuff.
of the business which may be of interest. There is lots of manufacturing that happens at Canford and Lucas is not only eager to learn as much as possible, but to also share his thoughts and insight.
It has been a pleasure having Lucas here so far, and everybody at Canford will be watching his career with excitement; he has a very bright future ahead of him.
Any live event, whether drama, music or broadcast will inevitably involve a number of operational roles. Most occupants of those roles will require access, at some point in the production, to a communication system, and in theatre and event usage at least, this has typically been through the use of ‘party line’ systems. Comprising of one or two communal channels, these systems use a readily available twisted pair audio cable per channel to daisy chain full duplex audio alongside power. Digital alternatives offer higher channel counts, more complex feature sets, function lists, and bespoke configurability.
For the majority of operational roles a fixed position or wired intercom is still the most appropriate solution, providing unmatched stability and usually being more cost effective. For those with more mobile roles, however, wireless solutions are better suited. Within the analogue domain, we typically see the use of walkie talkies, which meet the needs of those operators who need to cover large areas of the production. Unfortunately, this platform leaves much to be desired in operational use, due to its simplex nature (one way audio) and lack of additional AV oriented functions. Going digital, we can send more information over a single connection, so multichannel full duplex audio and control is achievable per device, although within a comparably smaller RF coverage area due to the attenuation or absorption of the typical frequencies used.
Radio interfaces present four wire conversions (audio line level input and output) alongside PTT (push to talk) emulating normally open contacts and DC signalling (call alert) passthrough. This method utilises the accessory port of a captive radio, connecting the two systems through an analogue link. If you want to add two wireless radios to a solution, you will need a third permanently linked to the interface. Beneficial for linking into existing infrastructure or extending past the range of the alternative digital offering yet
limited by the inability to talk over one another or segregate more efficiently than having an interface and captive radio per translation of desired radio channels.
Working within the licence free 1.9GHz DECT space, GreenGO wireless provides two subscription types: Up to four belt packs with one antenna. OTA offers a quick and easy setup for smaller applications without the need for a computer or software devices to search for each other and establish a connection “over the air”. Up to four belt packs with up to seven antennas, Pools is the suggested method for most applications, providing the ability for devices to roam between different antenna deployments, configured via a subscription platform within the software.
Green-GO is a decentralised solution, providing the facility for the purchase or rental of only what is required, with no real practical limits to the number or bespoke configuration of each device. This more modular approach provides the opportunity for a staggered integration and deployment, making it a common choice when adding wireless to an existing party line solution. Requiring an interface between the analogue and digital, followed by the desired quantity of antennas based on the total number of desired wireless belt packs and roaming RF environments. Each antenna can support the simultaneous use of up to 4 belt packs and environment dependant, capable of a range of up to 300m.
For all things Tecpro please get in touch with us via: enquiries@canford.co.uk
More than one year after the first beta release of Version 5, the Green-GO development team continues to deliver feature updates and bug fixes, transparently working closely with Global users via the greengoconnect.com forum. During this period, Green-GO released an “i” variants of key devices, to meet the demands of the marketplace. Functionally identical to their predecessors, these devices are optimised for the latest platform and will therefore only work from version 5 onwards. The following are some of my tips and tricks for getting the most out of your v5 experience.
Stick with a 32 kHz configuration sample rate. it is currently the optimal blend of frequency bandwidth and network data bandwidth.
Utilise your own colour and ID conventions. This allows you to visually segregate User devices and interfaces by ID and colour. You can create multiple at the same time by changing the “amount” in the add user and add group menus.
Multiple “Users” can be addressed at the same time. Using the tick boxes on the left-hand side of the Users view and then clicking “Details”, with the topmost box selecting all listed.
Make use of Templates. They provide a way to store and recall any settings or card of settings to the computer version of the configuration file (not saved on devices). You can save multiple cards to the same template and use them on other configs via the “MERGE” function.
Create “User” profiles for interfaces. A channel allocation with Listen enabled allows external audio into Green-GO, and a channel allocation with the autotalk channel mode sends Green-GO audio out to the external connection.
Where possible work in the User tree. A user can be made up of multiple device types and changes should translate to their associated device live. working in the devices tree creates a proxy of the user profile which will later need to be synced for changes to be saved to the configuration file.
Get into the habit of syncing devices, saving to devices, and saving to your computer. v5 will work “as live”, but a clean, stored configuration supports system stability and rigidity
Configure smarter. Within the channel assignment view you can modify the display via the icon in the bottom left hand corner. You can then right click on the column of the channel you wish to address, rather than double clicking on a channel to open up its settings window and then viewing changes per channel.
Work alongside the manual. The developers have put significant effort into their documentation both online and compiled with the software package; it offers an invaluable, searchable quick reference.
The roadmap for Green-GO is exciting! with new features and bug fixes being implemented, the release notes for the latest and greatest SOFTWARE and FIRMWARE can be found at: manual.greengoconnect.com
For all things Green-GO UK, please get in touch with us via: greengo@canford.co.uk
https://www.dpamicrophones.com/mic-university
Acoustic interference tubes are used to increase the directionality of microphones. Over the last decades, DPA Microphones has extensively researched and improved the interference tube technology to an unprecedented new level of performance.
In some audio situations, it is a struggle to isolate sound sources enough from the surroundings. In the broadcast and film sector, it is about preserving the intelligibility of reporters or actors and separating their dialog from disturbing elements like passing traffic or other environmental noise. In these situations, either a very narrow directional microphone characteristic or a bodyworn microphone is necessary.
The PA/Live music sector faces the same type of challenges. When riding the faders, it is crucial to control only the intended source. Isolating the audience from the PA system during live recording is another example. These challenges are solved by either placing the microphone very close to the source by, for example, close miking instruments or choosing a highly-directional microphone.
Highly directional microphones are often referred to as shotgun microphones, named after the practice of use. Usually, it is mounted on a boom pole and pointed to “hit” the sound source, for instance a person. Shotgun mics are also used in this way in the surveillance and security industry as well as music production for stage miking of, for instance, opera soloists.
Directional microphones – pressure gradients
Conventional directional characteristics like cardioids, wide cardioids (hypo cardioids), supercardioids or hypercardioids benefit from the pressure gradient transducer principle of a microphone. To further sharpen the directional characteristics, an acoustic interference tube can be added. Even a pressure transducer (that is innately omnidirectional) can make use of an interference tube.
Generally, directional microphones become directional due to the pressure gradient working principle. Pressure gradient transducers work by registering the pressure difference between the front and the backside of the diaphragm. With no further modification, this capsule design, results in a figure-of-eight characteristic.
Interference Tube - what is it? “Interference” is a strange word to use in conjunction with a high-quality audio product. In the case of the interference tubes for microphones, it refers to the actual way the tube works.
A small tube is placed in front of the diaphragm. This tube has a certain length and its walls have a certain density, which attenuates the sound coming in and delays sound from all off-axis directions. It is not a vacuum tube; all the processes are strictly acoustical, there are no DSP-functions or the like in this technology. The tube creates level interferences on the capsule.
The interference tube is covered with a protection grid with slots cut along the side. The audio directly in front of the tube is unaffected. For every other direction, wavecancellation (due to different length of travelling) eliminates most of the off-axis sound.
The main challenge is that the off-axis response often is very nonlinear and sounds terrible, has many side lobes, and a spike-shaped polar pattern.
Ideally, the interference should be so extensive that it efficiently creates audio wave cancellation. In the real world, this is difficult. Sound will be almost completely canceled at some angles of incidence and some frequencies. Other directions and other frequencies will be attenuated to a certain level. It is due to this phasing working principle (named interference) that shotgun microphones have previously (and rightfully) been known for their poor audio quality in any other direction than on-axis. In addition, it is often also true that when a shotgun microphone is rotated, the surroundings sound different due to shifts in sound color.
DPA Microphones research and improvement have been aimed at minimizing the phase cancellation shifts and off-axis peaks and dips. This was achieved during the development of the 4017 Shotgun Microphone.
A closer look at how it works: Here is some basic knowledge about wavelengths, their relation to frequency and wave cancellation. An audio wave’s length, λ, is related to its frequency, given by this expression: λ= c/f where
c is the speed of sound (approximately 340 m/s) f is the specific frequency
A 200 Hz tone, for instance, will have a wavelength of 340/200 = 1.7 meter (5.58 ft).
If two sound waves hit the same spot at the same time, we say they are coincident or without phase differences. If not, there will be a phase offset between them. Phase equals distance and it also equals time.
A complex acoustic phenomenon occurs inside a microphone with an interference tube. Its underlying theory asserts that the key to useful interference is the different distances or traveling paths that any sound incident will have. Creating wave cancellations for off-axis directions and thereby increasing directionality, is the main purpose.
inverted phase in phase
o -axis sound incidence o -axis sound incidence
Left: Two in-phase waves result in amplitude doubling.
Right Two 180° out-of-phase waves result in amplitude cancellation.
mic element
Length, diameter, material and the flow resistance of the mesh are some of the parameters that can be changed when designing an interference tube. Here is an example of how alterations in the tube might affect more than one parameter and the overall sound of the microphone: Increased interference tube length will result in increased attenuation at lower frequencies. However, the longer the tube, the larger the sound flow resistance and delay time for the sound inside the tube. This increases the risk of getting nonlinear off-axis frequency responses.
Improving the control of the interference tube parameters and combining them to the preferred sound qualities is quite an achievement. DPA Microphones can deal with multiple directivity patterns, sensitivities and frequency responses, while at the same time producing within narrow tolerances.
delivers sparkling clear and distinct natural sound for both recording and sound reinforcement of choirs, instrumental or vocal groups, speech or live audiences.
It has a discreet, elegant and lightweight design. Extremely low in profile, the integrated gooseneck provides the ability to easily aim the mics, ensuring perfect positioning with minimal visual impact since the optional extension cables are very slim and nearly invisible.
The 4017 is the result of intense research and improvements of interference tube technology.
It is a short and exceptionally lightweight shotgun microphone that offers a highly-directional pickup pattern while maintaining natural DPA clarity.
Due to its remarkable clarity, wide dynamic range and excellent rejection characteristics, the 4017 is equally at home in the recording studio as well as for sound reinforcement and live music.
The 4017 has one of the sharpest directional patterns compared to the length of its interference tube.
The 4080 is well suited for broadcast, conference and other live performances in the studio or the field.
It is acoustically pre-equalized, offering a 4 dB presence boost, which makes the voice more distinguishable and improves speech intelligibility. Professionals will appreciate the lightweight and excellent speech reproduction.
With its supercardioid polar plot, the 4097 offers a highlydirectional pick-up pattern as well as low self-noise and high sensitivity. The mic is capable of handling high SPLs, which allows it to deliver undistorted natural sound, even when users speak loudly or yell. With a linear response, low distortion and an extremely large dynamic range, it works well in challenging environments. In addition, dialog and background noise off to the side (off-axis) of the microphone preserves the audio quality; it just drops in level.
Dedicated to hanging applications in churches, orchestra pits, theatres and TV studios, among others, this 4098 variant
The 4099 is a unique miniature clip microphone that has inherited similar sonic characteristics as the legendary DPA studio microphones. The 4099 microphone and mounting system are meticulously designed and optimized specifically for instruments. This ensures the best possible mount and audio reinforcement is achieved when performing live. Representing years of research and development, the 4099 features a supercardioid polar pattern for superior gain-before-feedback.
The 5100 is a mobile surround microphone whose compact size and ease of use come at no sacrifice to its high sound quality. It can be regarded as a surround ambiance augmenter, ideal for bringing genuinely engaging surround ambiance to sports events, documentaries and other ambiance applications for many types of production. No external signal processing is required. The 5100 can be mounted on a camera or microphone stand, suspended or simply handheld via a handgrip. Extremely lightweight and portable, the unit sports a robust build quality that is also highly resilient to inclement weather conditions.
A completely self-contained “plug and play” solution for 5.1 audio capture, the 5100 employs five miniature pressure transducers that exhibit extremely low sensitivity to wind and mechanical noise, low distortion, highly consistent lowfrequency response and extended dynamic range. Appropriate channel separation and directionality are achieved through a combination of DPA’s proprietary DiPMic™ (Directional Pressure Microphone) technology, which mounts interference tubes on the L/C/R omni capsules, and the use of acoustic baffles that further preserve the accuracy of levels between the discreet analog output channels.
Bigoni, Francisco; Agerkvist, Finn; Brixen, Eddy B.:
A stepped acoustic transmission line model of interference tubes for microphones.
AES Convention 145, NY, NY, USA. Preprint 10094 (2018).
by CanfordTransporting information from point A to B is the goal but how we get there is the task. Following on from last year’s “knowing your nodes”, IT within AV is nothing new but it is becoming more widely adopted within our industry. Typically segregated from site services, confusion tends to arise when blending multimedia solutions over the same hardware backbone.
From the ambitious digitisation of the BBC’s National Radio Network feeds in the 1970s, through the increased use of digital recording techniques in the 1980s and from the widespread use by broadcasters of ISDN in the 1990s to its replacement by VOIP technology in the noughties, the use of digital technology for the exchange or transmission of audio, video and text has increased exponentially. Correspondingly, the techniques employed to make systems more robust and reliable have seen parallel development. Part of that has been the use of Encapsulation, where, in the programming system, data about the original material is bundled with the methods used to control the data. The following article seeks to explain some of the techniques involved, together with help in deciphering some of the widespread use of abbreviations! Readers with only a modest technical knowledge may like to find a comfy chair and mug of tea before proceeding!!
For a given network, DATA is encapsulated into the wrapper of a PACKET which provides a standardised format for packet switched networks to transport information effectively. A piece of media is segmented into packets alongside source and destination information and an error CSC (checksum). The destination tells the network where this information is going, the Source for any reply and the CSC provides a quick way for a receiving device to disregard a corrupted packet. Depending on the IP PROTOCOL, these packets will then be transported around a given network via further labelling/tagging based on the ruling of each network node in the transmission pathway.
Often referred to as the “handshake”, the first step in transmitting any information is to establish a connection from the sender to the receiver. If the destination IP is not already logged within the sender’s ARP (Address Resolution Protocol) table, the Sender broadcasts an ARP request which every local device, except the targeted device, will see and discard. The receiver will then reply with its MAC (Media Access Control) address to be recorded in the sender’s ARP table for future reference, and the transmission of data can be established. If the receiver address is within the same IP subnet as the sender, the packet can be sent directly. Otherwise, the packet is sent to the default gateway which will then check the receiver address against its routing table, discarding it if unknown. If the receiver network is known, then the packet is encapsulated into a data-link FRAME and forwarded on through the relevant port. This process can repeat through multiple “hops” depending on the number of network nodes between sender and receiver. De-encapsulating, checking, and re-encapsulating before forwarding on to the next node in the pathway. The last router removes the packet wrapper from the data link layer for delivery to the receiver, assuming the packet contains no error.
Considering the analogy of the postal service from which IP originates. Our letter (data) is broken down into sections and placed inside envelopes (packets) which are delivered to a post office (switch). It is then transported to the sorting office (router) which then puts it in the relevant bag/container (gateway) to be transported to the relevant destination, unpacked from the district sorting office, forwarded to the local postal service, and finally collected by the recipient. Postal sorting offices have known connections (ARP) to their connected devices and checks (CSC) can be undertaken throughout transit for damaged or illegal goods.
The above visualisation depicts a modelled transmission of a typical IP packet. Running from Sender to Receiver we can think about the wrapping and unwrapping of information in relation to the ISO and TCP/IP networking models. For any given IP transmission, the sender and receiver both need to be known by not only each other, but every node in between. An IP address provides a definable superficial identifier, which is stored against either a local port or a static MAC address on the routing tables of each relevant network node. This signal flow creates a potential issue regarding bandwidth limitations, as without some guidance or prioritisation, a given network can quickly become flooded and unusable.
Using unmanaged switching provides a “best effort” attempt to packet routing, where all traffic is given the same priority, enabling a plug and play style application but limiting control, making any existing QoS like VLAN tagging redundant. The alternative being managed switches, “with great power comes great responsibility”. Being able to monitor and control throughput through solutions such as partitioning and trunking, lock down ports to specific tasks, prioritise a preferred transmission, or discard of unregistered multicast information, can all be used to streamline transmission. Yet it can be damaging for non-immediate processes that may cause issues to an operation further down the line.
“Hops” also present a potential for loss, as the most susceptible part of any transmission is the physical connection, the more connections between nodes the higher the theoretical chance of failure. Many services use a “shortest path” approach to reduce potential error. However, this can lead to throughput congestion, with multiple services all trying to transport through the same or similar routes. Going a step further, some network optimisation can monitor latency, taking
account of the least number of hops whilst opportunistically switching routes, in a bid to find the balance between data loss and time taken.
Because IP transport is typically made up of many nodes, it requires greater consideration for potential route and processing bandwidth in comparison to a point-to-point analogue or digital solution, even if a repeater or booster is inline. For unmanaged networks, diagnosis comes through monitoring from the endpoints and physically creating optimal routes through hardware segregation. For managed networks, monitoring is usually built in and these services can then be used from a single control surface to automatically adjust flows whilst following user configured segregations and prioritisations to get the best performance from the platform. IP networks are a multi-faceted solution, and it is important to account for the accessibility of control. If a signal is not reaching its destination, then a route trace should provide some insight into where it is getting stopped. Checking the routing tables and/or IP subnets should confirm the desired path is possible. Intermittent signals are usually the result of throughput limitations or snooping protocols. Looking at the latency of transmission or a route trace should confirm, the action being to look at rerouting, segregation, or prioritisation. Often overlooked, any issue with transmission can still be down to cabling, checking a solid continuity on cable assemblies and node ports is a plausible avenue to eradicate as a potential point of failure or intermittency. When faced with adversity for any given IP solution, check the documented network guidance.
From theatre to sporting events, lavalier microphones like TwinPlex, DuraPlex and the brand new UniPlex face special conditions and challenges. But a great mic is only as good as its connection. John Born, Associate Director, Product Management at Shure, explains what it took to create the revolutionary Shure Plex cable.
When working with new lavaliers and headsets, endusers mainly interact with the cable. And typically, when a subminiature microphone fails, it’s usually the cable that fails, not the microphone itself.
One might think when we develop lavaliers and headsets at Shure, we spend all the time on the microphone (to be clear – we do spend a LOT of time developing the microphone!) However, if the cable fails it’s as though the microphone doesn’t matter. In fact, the cable is at least as important as the subminiature microphone itself, as it interacts with the user wearing it, the technician putting it on the singer, actor or person speaking, let alone the audio professional at the mix board. In mission critical deployments – from NFL referees in the ‘big game,’ the next Hollywood blockbuster, West End’s latest musical, or your favourite award shows –a lavalier or headset microphone, and its cable connection, simply cannot fail.
In the early stages of designing TwinPlex mics, I laid the gauntlet down with the team that we needed two completely new cables, 50 percent thinner than anything we’d designed, and it had to be an absolute ‘beast.’ Then, of course, we had to define what being a beast actually meant.
To be successful in high-tier, demanding situations, I knew that the cable needed to be highly flexible, paintable (for theatre
amazing strategic supply department along with our cable commodity team – yes, we have a whole team devoted to cable construction – went to work. We searched for a partner in designing a new cable to our specification and from start to finish. The cable specification, design, iterations, and approval took almost four years.
The cable partner that we selected – a specialist in medical cable construction – quickly understood our needs as we immersed them in use cases in the audio world. We tortured the first cable they developed: pull-to-failure, flexto-failure, chemical reaction, artificial sweat, different paints, pens and markers, electrical specifications – we really ran it through the ringer.
After the first round of flex testing, we realised we were on the right path. The first samples exceeded our benchmark by 20 times! This was due to the unique grounding construction that we co-developed with our partner.
The Shure Plex Cable has dual, redundant grounding, which is typically the first thing that fails in a subminiature lavalier/ headset cable. These tinsels reinforce and re-connect the shield throughout the cable. This means that you can have a complete break in the shield in one spot and our grounding tinsels maintain the ground connection at a different location in the cable, ensuring nothing is lost or heard,
Additionally, we also deployed this tinsel technology in the conductors, making the cable extremely flexible and ‘relaxed’ as there is not a traditional copper strand to kink. This allows the cable to lay and route easily, which is really important to anyone who places lavaliers and headsets on talent for a living. It also means that Shure Plex Cables are highly resistant to kinks!
As mentioned above, from start to finish it took about four years. From establishing all new specifications and processes and ground-breaking testing (literally, hundreds of samples were destroyed in qualification) we have come to know how to expertly build and test the finest audio connection from microphone to bodypack.
And that means audio professionals, singers, actors, anchors, and audiences everywhere never again have to worry about whether the lavalier and its cable are going to work! FEATURE IP
Lastly, an amazing cable is only as good as its connector. We soon realised we would need all-new designs that not only mate properly with our 1.1 mm and 1.6 mm cables, but actually extend, or add to, the product’s reliability. Working with a leading connector partner, we specified and codeveloped new reinforcements in all the major connector types, ensuring that Shure Plex Cables mate with nearly any bodypack.
Four/three
Alongside Outernet, Canford partner Qvest has established an incredible new sight-seeing highlight in London. Featuring the world’s largest wrap-around screen installation, Outernet London’s Now Building offers visitors a unique media experience space, the likes of which has never been seen before, as the core element of a new culture district in London’s Soho neighbourhood. As Master Systems Integrator, Qvest was responsible for the technical design of the largescale and cross-media backbone for all event venues, as well as its delivery, vendor management, and integration.
Matthias Reintgen, Senior PR Manager for Qvest, got in touch to tell us the full story.
Outernet London brings together the best content partners and the latest immersive video technologies to create new experiences for music, arts, culture, and creators. Its centrepiece is the imposing Now Building, which features the world’s largest wrap-around LED screen installation. With its particularly performant technology setup, the multimedia LED environment, with 4D and interactive capabilities, offers new possibilities for visually spectacular staging and creative storytelling. The Now Building, and other parts of Outernet London, has already been used for exclusive events since autumn 2021 including product launches, interactive exhibitions, and broadcast programs.
Very few places in London offer such a concentrated music history as Denmark Street. Since the 1950s, Denmark Street has been closely linked to British pop culture; initially through publishing houses, and then later through recording studios and music stores. Denmark Street has played host to Jimi Hendrix, Eric Clapton, Bob Dylan, and David Bowie among many other music icons. The Sex Pistols lived at number 6 and recorded their first demo tapes there, The Rolling Stones made their first album in the famous Regent Sounds studio, and John Paul Jones met Jimmy Page there. Sadly, many of the recording studios, rehearsal rooms, guitar stores, live music venues, sheet music, and instrument stores have gradually disappeared, though a handful do still remain.
Thankfully, the music heartland of England’s capital is being revitalised with a new entertainment district where communities can come together and enjoy each other‘s culture in stunning ways. At the intersection of the digital and physical worlds, Outernet combines the storytelling of television with the physicality of experiential marketing to deliver emotional, multi-sensory experiences and entertainment at scale. Two new venues have been built; HERE at Outernet (2,000 capacity) and The Lower Third (250 capacity) which aims to return music, and other cultural events, back to Denmark Street. Utilising the latest screen technology, the spectacular atrium of the Now Building offers visitors an unparalleled, multi-sensory experience with the chance to immerse themselves inside the largest, and most advanced, wrap-around installation of LED screens on the globe. The four-story-high, floor-to-ceiling, 360-degree canvas of immersive, 16K screens measures more than 2,100 square metres. From now on, the world’s best storytellers, brand partners, advertisers, and news providers can showcase themselves here with new content every day. Special guests have already attended exclusive events in the Now Building (such as UNICEF’s 75th anniversary Blue Moon Gala celebrations, and the launch of Paramount+).
The decisive factor in commissioning Qvest, above all, was their internationally proven expertise in media technology and their unique consulting-orientated design approach.
Mike Whittaker, CTO of Outernet Global: “What we have achieved with our teams at Outernet and Qvest is truly extraordinary and unique; it by far exceeds the usual technology solutions. Qvest’s understanding for our vision, methodical approach, and knowledge transfer during the process made them the natural choice to deliver this installation. We are very happy that clients and visitors of London can now enjoy this new centre for culture and creativity which is spectacular in so many ways.”
Thomas Müller, CTO of Qvest Group: “What makes this project so special, among our numerous international media installations, is that this audio-visual spectacular can be experienced by the public. Crucial for this immersive experience, in the Now Building, is the intelligent orchestration of all tech components behind the scenes. We are proud to have realised this unique media space for concerts, brand events, and art, with our consulting and technology experience.”
Qvest’s responsibilities as Master Systems Integrator included the overall design and implementation of the operations and data centre (and its networking). This centre is where the threads of the various venues of the over 23,200 square metres. Outernet ensemble come together. When it came to technical equipment, Outernet’s requirement was simple: the best of the best. For this reason, the choice fell on products and solutions from renowned technology companies. In addition to 360-degree LED displays from AOTO, the equipment used includes 12K 4G BNC Termination panels from Canford, 3D real-time rendering software from Ventuz outputting a total of 26K resolution, storage solutions from Dell, and IT routing systems from Cisco. The core component of the operations centre is a facility with content scheduling, automation control and real-time playback, monitoring and immersive audio processing.
Open to the public since November 2022, the Now Building is expected to be visited by up to 50 million residents, commuters, and tourists annually; all of whom can experience this groundbreaking project and discover how creative storytelling is being brought to life in a new, and inspiring, way.
In April 1999, Canford bought Swift Precision Engineering, a partnership situated on the Isle of Portland, Dorset. It would be fair to say that this acquisition raised a few eyebrows at the time. What would a thriving business based in Washington, Tyne and Wear, possibly want with a small, failing video connector manufacturing company, 375 miles away, at the opposite end of the country? Many people, both within the business and externally, thought that Canford had completely lost the plot. Iain Elliott commented at the time, “the acquisition of Swift represents a major opportunity for the Group. Not only can we expand our manufacturing capability, but we can also look further afield and explore new markets. We expect that the acquisition will add around one million pounds a year to company turnover”. Despite those words, few were convinced… That was the essence of Iain; he saw opportunities where others didn’t and was prepared to take risks where many wouldn’t. His entrepreneurial and ambitious mind would often see him heading off in what seemed, from the outside, some very strange directions. To a lot of people, it made little sense. To Iain it all made perfect sense. Portland was definitely a case in point!
Stabilising the business was the first priority, quickly followed by the development of a business plan that would see significant investment in plant and resource. Innovation was another critical factor. This required a clear understanding of what the market needed, and the capabilities to design the required solutions. Canford’s and Swift’s existing knowledge and experience, coupled with the fundamental principle of listening to what customers wanted, would prove to be key. Listening to customers was nothing new for Canford and, as such, new product ideas came thick and fast! The final, and probably most important, piece of the jigsaw was in developing the right culture; a “can do” attitude that allowed the Portland team to be responsive to customer demands and needs, often within very short timescales.
Early plans included making the operation largely self-sufficient, so that it didn’t have to rely on third parties regarding its major functions. This, in turn, would go on to not only improve lead times, but also provide us with the ability to offer custom solutions where required which was, from our early investigations, a significant problem for many customers. Today, the site boasts an impressive set-up which includes three modern vertical CNC machining centres, a full sheet metal facility, a powder coating suite, laser engraving capabilities, and an extensive assembly workshop.
A further part of the original vision was that if the major project customers were using Canford for their standard and custom metalwork requirements, then it was likely they would also want to talk to us about quoting for other aspects of their projects such as cables, racks, MDU’s, comms, etc. This was a master stroke and in practice proved to be exactly the case! Further to that, it also set Canford apart from many of our major competitors, especially in markets that were increasingly looking more towards single sourcing as a way of improving efficiency. Canford’s existing extensive range, with an ability to manufacture niche and custom solutions, was the winning formula that few could match.
Wind the clock forward 24 years and the Portland operation of today is now one of the main foundation stones of modern day Canford. It has evolved from those early roots, of simply manufacturing broadcast video connectors, into the preferred global market leader for reliable, high quality 19” rack mount and enclosure connectivity solutions, encompassing not just our traditional broadcast markets,
but also theatre, live events, and Pro AV. It has become the supplier of choice for a large majority of systems integrators not just in the U.K., but internationally too. Our products can be found in regular use at major events across the world and are playing a significant role in the Qatar 2022 World Cup.
This year has already proved to be the most successful one on record for Portland, and that despite the many current global challenges it has faced. The biggest challenge of all was sadly losing Iain at the end of 2021. Based on the foresight and vision he had for the operation, way back in 1999, and the fact he didn’t listen to those that questioned the approach, it is fair to say that his legacy lives on.
Iain did get one fundamental aspect wrong however… the estimated £1 million annual turnover was a significant under valuation.
TTL Video is one of the UK’s leading providers of outside broadcast infrastructure and facilities to the domestic and international market. Since the year 2000, they have solidified a reputation for building turnkey communication and broadcast solutions for venues and sports stadia, and have installed systems into 46 football stadiums in order to satisfy the Premier League’s requirements for broadcast. We wanted to know more about this unique part of the industry, so we asked Erika Dobie (Business Development Manager at Canford) to get in touch with Stefan Bewsey, Chief Engineer at TTL.
By Erika Dobie, UK Business Development ManagerAs 2022 draws to a close, how will you look back on it? What stands out most for you this year?
This summer we completed another football stadium, Nottingham Forest F.C., and are continuing to work through a series of upgrades at all Premier League stadia. The Premier League have, understandably, strict requirements for broadcast infrastructure that all clubs must adhere to. Earlier in the year, we also completed a comprehensive system installation at the All England Lawn Tennis Club at Wimbledon. This is the first time they’ve had a permanent broadcast cabling installation at the venue, so we’ve been kept pretty busy!
One of the biggest challenges for us is the short off-season that football has. When a club is promoted to the Premier League, we don’t have long at all to equip them with the broadcast infrastructure that they need. This year has been particularly challenging due to the unprecedented long lead times for materials, especially cable.
This kind of work seems to have become a bit of a niche for TTL.
It definitely has. The company was originally founded in 1986 with a background in the supply of operational television facilities to international broadcast companies. We now
TTL have used Canford for many years. I first got introduced maybe ten years ago by our previous Managing Director, Alan Green…and I’ve never looked back.We keep coming back to Canford because of the good customer service, competitive pricing, and the very good website.
occupy the niche you talked about; being the foremost supplier of Outside Broadcast cabling and infrastructure to sporting venues. We cover the full range too: camera, audio, video, data and fibre cabling, as well as specialist facilities such as goal-line technology and player tracking. We’ve now installed infrastructure into 46 football stadia, since the year 2000, and we are continually being chosen as the preferred supplier for this kind of work.
What other cool tech are you seeing, particularly in relation to sports broadcast?
One of our clients is currently working on an upgraded player tracking system. They use a series of mobile phones to produce high quality video images that can track the players; it’s pretty impressive.
Canford and TTL have worked together for years, how did that originally come about? What keeps you coming back?
You ‘re right! We buy a variety of cable from Canford: SMPTE 311M Camera, Triax Camera, 8 Pair Starquad Audio Multicore, Video Cables, and Fibre Optic Multicore . Oh, we also have you manufacture and supply our custom panels and metalwork for our racks and enclosures, as well as a load of connectors and cabling accessories.
TTL have used Canford for many years. I first got introduced maybe ten years ago by our previous Managing Director, Alan Green…and I’ve never looked back. We keep coming back to Canford because of the good customer service, competitive pricing, and the very good website.
Lastly, what do you think the future of the industry is going to look like? And where does that leave TTL? Broadcast at UK football stadia only seems to increase in scope as the interest around the globe intensifies and technologies advance. I can see further upgrades in the future as expanded broadcast scope is required. There will certainly be more remote production in the coming years, resulting in a reduction in the need for OB trucks at venues. The usage of high-speed mobile data networks (such as 5G) is also going to be vital to support production.
For us, we’ll continue to assist the growth of sports broadcast in the UK. We’ve been expanding into other areas such as player tracking, VAR monitoring, and branching out into sports other than football too. We’ve also recently started installing systems for the Women’s Super League as that continues to grow in popularity.
Audio. Control. Power
Audio level meter displays, audio loudness measurement tools and audio metadata monitoring are at the very foundation of what audio professionals are used to. However, as technologies evolve, engineers and operators require audio solutions that also serve to improve their workflows.
Built on the SAM-Q platform, the SAM-Q-SDI brings the freedom to monitor SDI, MADI, AES and analogue audio sources with maximum operational efficiency, offering multiple modes and up-gradable licences within one unit, ensuring that you get the most value out of your investment.
SAM-Q-SDI brings the freedom to monitor SDI, AES and analogue audio sources with maximum operational efficiency. Offering multiple modes and upgradable licences within one unit, with pin protection and a customisable feature-set.
Advances in technology are enabling the creation of ever more exciting content, as well as serving to increase new possibilities in content delivery. Comprehensive audio monitoring tools are now becoming a ‘must have’ for those needing to guarantee both content quality and quality of service.
channel selection. The video mode provides 16 audio level meters and single or multiple channel selection, complete with video confidence display. The mix mode is a graphical gain bar representation showing the relative mix levels of up to 8 audio sources. The names mode allows selection from 8 named audio sources, including audio presence indicators. Finally, the phase metering mode displays 8 sources and allows one audio source to be selected, monitored and checked for audio phase.
IP Control Buddy is a powerful yet compact control system that can be used standalone or integrated with a larger 3rd party control system. It can perform simple or complex functions and is perfect for flyaway kits, small production tasks and one button applications.
TSL’s basic power distribution units are compact in size and constructed of steel. With a rigid platform, power bus-bar construction and no crimped cables. They offer unrivalled reliability in all applications.
There are five standard modes included in the SAM-QSDI. Firstly, a traditional audio meter mode that displays 16 audio level meters with single or multiple audio
To find out more about TSL’s full range of solutions contact Matt Plant: T. +44 7771 543 713 E. sales@tslproducts.com tslproducts.com
ability to configure an audio monitor based on the task at hand is becoming more important than ever before.
SAM-Q-SDI brings the freedom to monitor SDI, AES and analogue audio sources with maximum operational efficiency. Offering multiple modes and upgradable licences within one unit, with pin protection and a customisable feature-set.
IP Control Buddy is a powerful yet compact control system that can be used standalone or integrated with a larger 3rd party control system. It can perform simple or complex functions and is perfect for flyaway kits, small production tasks and one button applications.
TSL’s basic power distribution units are compact in size and constructed of steel. With a rigid platform, power bus-bar construction and no crimped cables. They offer unrivalled reliability in all applications.
To find out more about TSL’s full range of solutions contact Matt Plant: T. +44 7771 543 713 E. sales@tslproducts.com tslproducts.com
With decades of joinery and cabinet-making experience, Canford are proud to offer a range of hand-crafted racks and cabinets in a wide variety of styles and finishes. Readymade or fully bespoke, Canford has you covered. Think quality…think Canford.