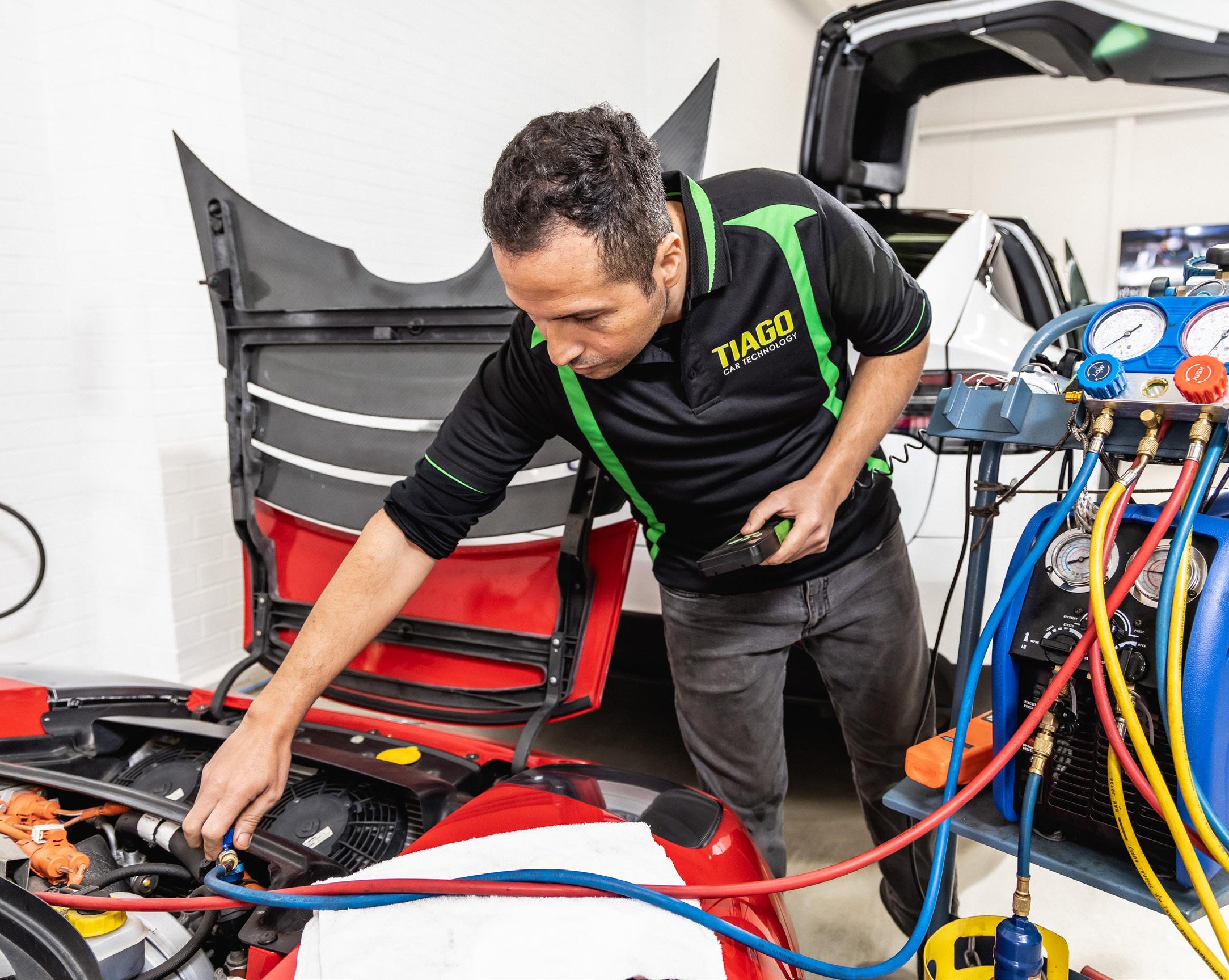
13 minute read
Advanced Driver Assistance Systems
While we are all familiar with the term ADAS, it is likely that there are still a great many of us who are not fully across the entire suite of systems and how they operate – both individually and collectively.
Advanced driver assistance systems (ADAS), as the name suggests, are installed to assist the driver in the safe operation of a vehicle. Of course, there are various definitions of driver assistance. The U.S. Society of Automotive Engineers provides a succinct summary highlighting the progression from driver assistance to driver automation as the systems become more complex. This is shown in Figure 1.
If you’re thinking that the driver assistance system “won’t affect me” – it probably already has, as these interconnected systems are well and truly operational. The latest estimate is that ADAS is installed in more than 300 models from various manufacturers currently operating in our market.
ADAS is, of course, not just a feature of luxury vehicles; it is now standard equipment on base model, everyday family cars and its use is growing daily. As a consequence, the calibration of ADAS is becoming an increasingly important factor for collision repairers and we need to understand some of the key points and our responsibilities when dealing with these systems.

David Erickson of Bosch Automotive Service Solutions outlines some of the components: forward-facing stereo camera, rearview cameras, long- and medium-range radar, lidar, surround cameras and ultrasound. All of these sensors input data for functions such as adaptive cruise control, lane departure warning, lane keeping assist, automatic emergency braking systems, intelligent headlight control and more. Figure 2 shows that these various systems are positioned throughout the vehicle.
“The initial set-up for these systems requires a levelling device that attaches to the radar, use of a three-position radar reflection mirror, and targets to calibrate the cameras. The processes include static and dynamic calibration, combinations of the two, plus the need for diagnostic tools to access the system to perform the calibration. Recalibration of these systems is required following — amongst other processes — the repair of the body that mounts the radar, changing the windscreen, changing and/or repairing the suspension, chassis repairs that may have changed the geometry in any way, sensor replacements, and even adjusting the wheel alignment can all impact the performance of ADAS,” added Erickson.
In a similar vein, Hella Gutmann points out that it’s always essential to refer to the vehicle manufacturer’s instructions, and they too provide some scenarios when radar sensor calibration or adjustment is necessary: after radar sensor replacement or dismantling/installation, after post-accident repairs to the body geometry, after changes to the vehicle level at the front or rear axle, after a suspected impact on the sensor, if the electronic control unit (ECU) detects exceeded tolerance levels for the measuring field, or after the impact carrier has been dismantled.
It is of critical importance to understand the difference between “adjustment” and “calibration” of these sensors. According to Gutmann, adjustment of many radar sensors can be done vertically and horizontally using two screws, similar to headlamp adjustments. This is purely a manual adjustment. However, the CU needs to be taught the new adjusted position, which automatically calibrates the ADAS.
Other generations of radar sensors are not equipped with mechanical adjustment features. If the system detects an error, or after any of the above-mentioned repairs/changes, the measuring field must be calculated again, and a compensation value configured in the ECU. In this case, calibration via the vehicle’s software and diagnostic tool is required.
I’m sure by now you’re getting the picture: returning ADAS to manufacturer specifications is critical to the safety of the vehicle and its occupants. What could possibly go wrong?
Well, according to a recent study by the U.S. Insurance Institute for Highway Safety (IIHS), curves in the road are posing a
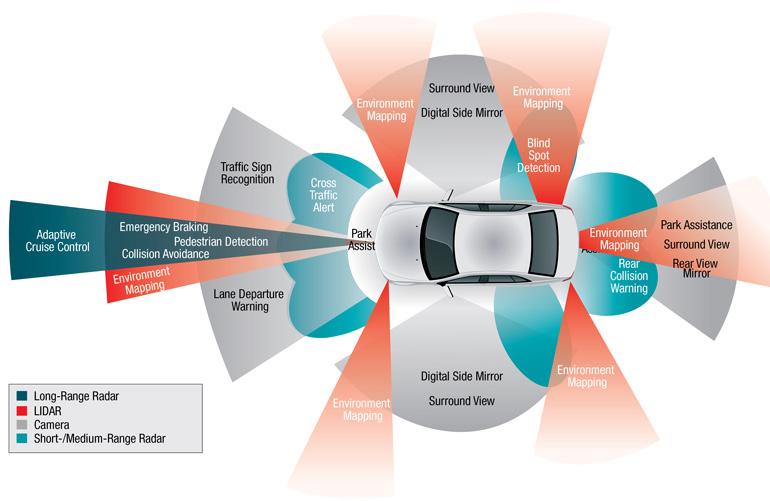
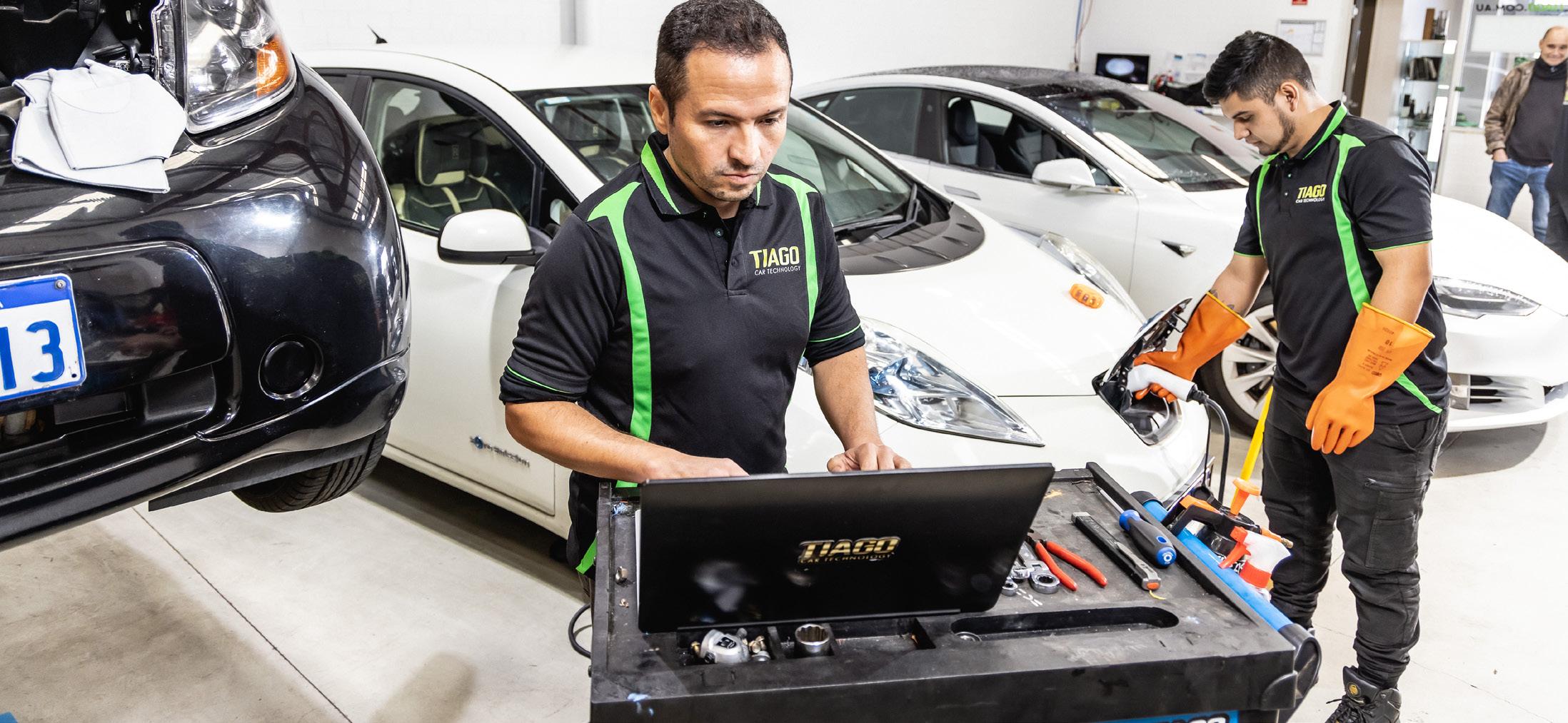
challenge to advanced driver assistance features like adaptive cruise control (ACC) and more sophisticated partial automation systems, limiting their potential safety benefits. manipulates the steering wheel or uses the indicator, or when the system’s sensors cannot detect the lines painted on the road. ACC deactivates when the driver applies the brakes.
Hu highlighted: “The fact that Pilot Assist was frequently inactive on the sharpest curves is an important limitation, since the kinds of crashes lane centring could help prevent are more likely to occur on curves than on straight roads.”
Interestingly, in a separate IIHS study, police-reported crashes showed that front crash prevention cuts rear-end crash rates in half and reduces rear-end crashes involving injuries by 56%. In addition, the appropriate use of ACC could further improve these figures since it typically results in greater following distances, giving drivers more time to react to an emergency ahead.
So, there is little doubt that the introduction and application of ADAS has had a significant impact on road safety when it operates in the manner in which it was intended.
All that being said, what is the takeaway?
Essentially, it’s the repairer’s responsibility to return the vehicle to pre-accident condition and ensure that the safety systems are fully operational. How the driver uses the technology is a separate matter.
In summary, as ADAS technology continues to develop and vehicles begin to make the transition to partial autonomy, the challenge becomes even greater. Fortunately, there are several global organisations that operate in this space and can provide you with advice, solutions, equipment and training to help you navigate what appears to be an ever-increasing technology minefield.
ACC and more advanced partial automation that combines ACC with lane centring are often disabled on some of the sharper curves present on limited-access roads, either because drivers switch the features off or they deactivate automatically. “We know that advanced driver assistance features may help prevent crashes, but obviously they can only do so if drivers use them,” said Wen Hu, IIHS Senior Research Transportation Engineer. “The study suggests that these technologies will only be able to reach their full potential if drivers trust them to handle the curves.”
ACC works like conventional cruise control, but it automatically slows the vehicle to maintain a preselected following distance from the vehicle ahead, so the driver doesn’t need to repeatedly brake and reset the system. Lane centring provides automated steering assistance designed to keep the vehicle in the middle of the lane.
Hu and her co-authors used data collected by the Massachusetts Institute of Technology’s advanced vehicle technology consortium. Onboard data-acquisition systems collected information from two 2016 Land Rover Range Rover Evoques and two 2017 Volvo S90 vehicles driven by 39 drivers over four weeks. The Evoques were equipped with ACC, and the S90s were equipped with both ACC and Volvo’s Pilot Assist partial automation system, which combines ACC and lane centring.
The data revealed that ACC and Pilot Assist were less likely to be active as curves became sharper. In the Evoque vehicles, drivers were 72% less likely to use ACC on the sharpest curves than on straight roads. In the S90 vehicles, drivers were 75% less likely to use Pilot Assist and 66% less likely to use ACC on the sharpest curves.
However, the researchers did not determine whether the driver switched off the system or it deactivated automatically. Lane centring can automatically become suspended when the driver
For more information on the vehicle autonomy levels, scan the QR code

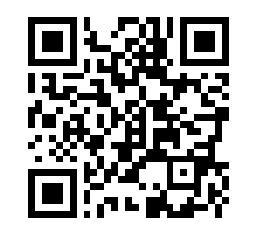
Colin’s Cee Bee Motors notches up half century
It’s not every day a Member celebrates 50 years in business but Colin Borthwick, of Cee Bee Motors in Preston, Victoria, has done just that.
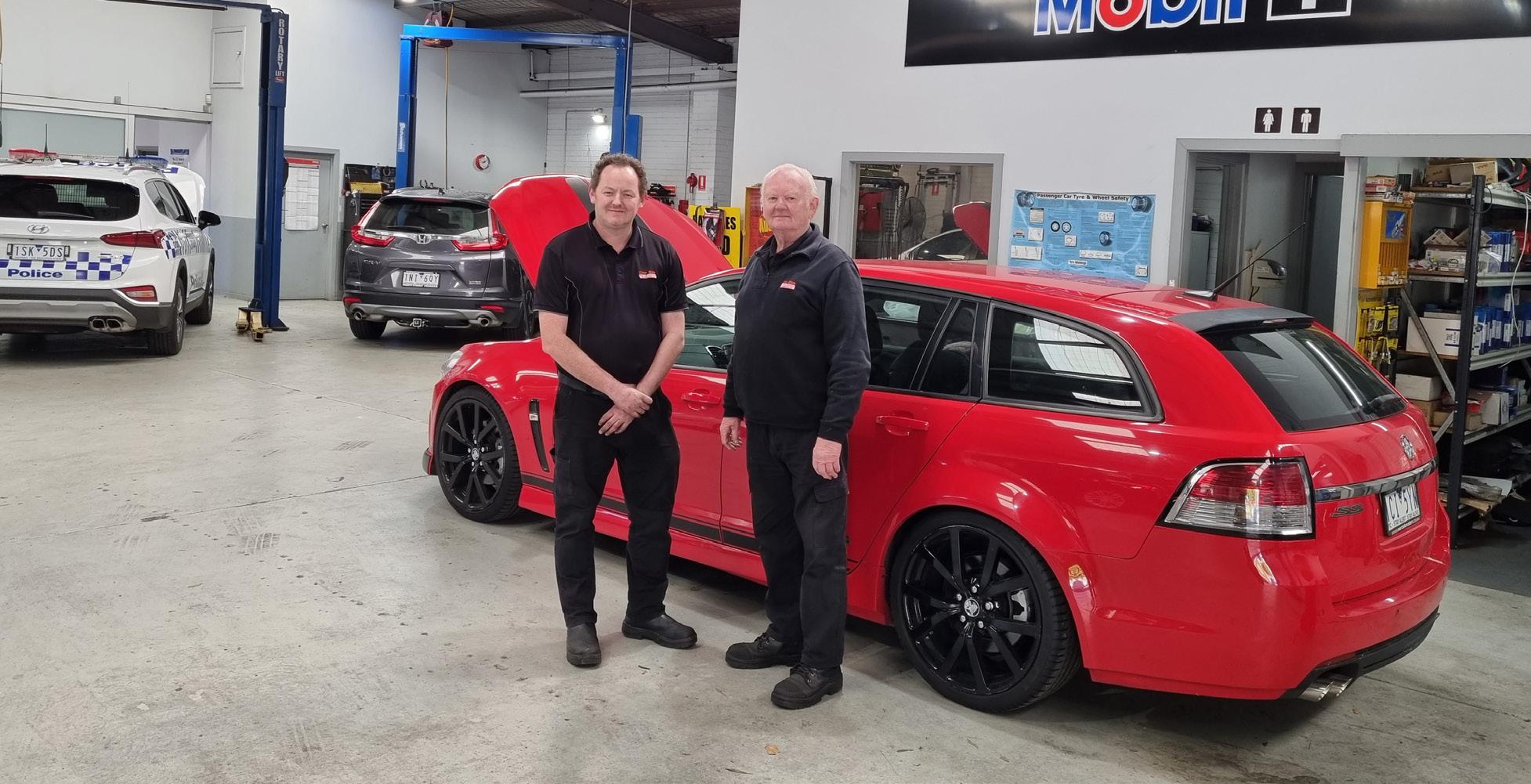
When Colin opened the doors on his first workshop in 1970, John Gorton was Prime Minister, the Beatles’ Let It Be was at the top of the pop charts, and Ford’s XY Falcon was rolling onto showroom floors across the country for the first time.
Colin had started his career in 1962 at the age of 17, joining the automotive industry because he’d always had an interest in motor vehicles as a kid.
Over the years Cee Bee Motors has moved premises a number of times, all within the Preston area, in Darebin in the northern suburbs of Melbourne. “We are now in the largest workshop we have had, due to the increase in our clientele over the years, and also feature a showroom for our used car sales,” Colin said.
The advice and opinions of anyone who has run a successful business for half a century are always worth hearing. So, what’s been the secret to Colin’s longevity in business?
“Work hard, be honest, and be polite,” he said. It’s a simple policy that’s clearly served him well. Cee Bee Motors offers a wide variety of mechanics’ services, including log book services, tuneups, road worthy certificates, air conditioning and VACC repairs. Colin has been a Capricorn Member for decades and says he enjoys the benefits of being part of a large buying group, including having access to a wide range of suppliers, getting one monthly statement, and “being rewarded for what we spend”. He likes to spend his rewards points on gift cards for his staff and family.

Colin’s promise to customers is “we are committed to delivering exceptional value and service from the moment you enter our centre”. Participation in the Capricorn Rewards is subject to the Capricorn Rewards Terms and Conditions which can be found at capricorn.coop/terms-conditions
- by Jeff Smit
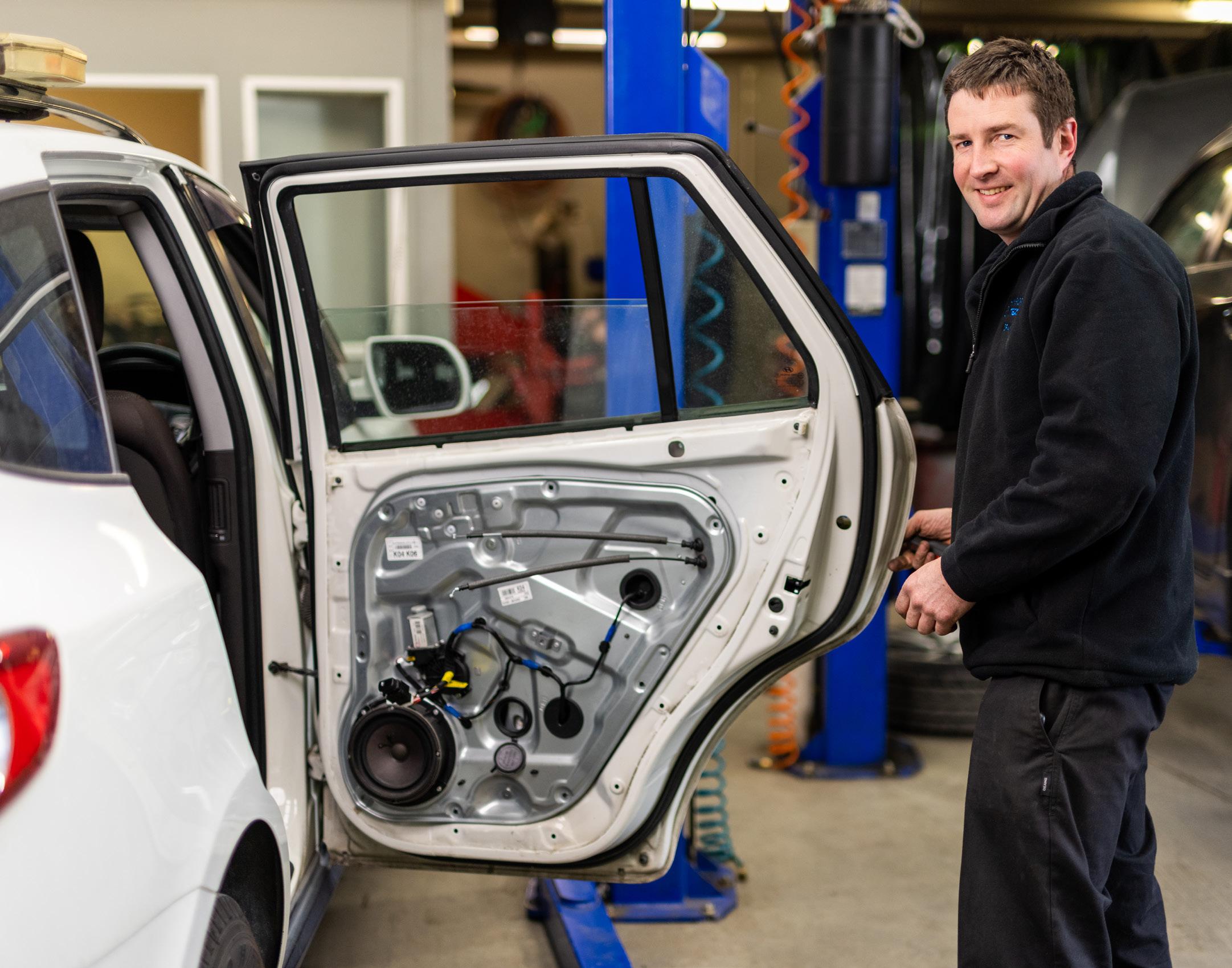
Every recurring task in an automotive workshop should have method and order to it. The kinds of vehicles being serviced in aftermarket workshops are changing all the time, but are your processes changing at the same pace? This implies that recurring tasks need to be evaluated regularly if a workshop hopes to keep up to date and run at peak efficiency.
Have you ever seen the service process involved with the servicing of an aircraft engine? It’s extremely detailed and every step is documented, for obvious reasons. We don’t need to go to that extreme, but a position somewhere in the middle would be ideal.
Revising service processes might seem like a time-consuming chore, but doing it in an orderly fashion will be worth the effort. Workshop efficiency will improve and any recurring service issues will be resolved. As a by-product, and a real bonus, the quality of work will rise, and training new technicians will become infinitely easier.
Where to start
In considering what basic service processes need to be improved, start with the jobs that irritate you the most. It might be a task that takes longer than it should or one in which mistakes consistently occur. It doesn’t really matter if at first you don’t know exactly why it bothers you – the fact that it does is enough to indicate that something isn’t working as well as it should be.
Involve your team
As a workshop manager or owner, you may not be directly involved with everything that happens on the workshop floor, so process improvement needs to involve your team. Those doing the work will have the best knowledge of the specifics, so you should involve them in any refinement of the job process.
Workshops should never be satisfied following the same process over and over if there is a better way to do the job. Routinely ask your team members to let you know if they think a job can be done better, because staff see things from a different perspective.
You can often pick up new processes through the networks you have joined or ones that you follow. Networks can be a good source of information. The best information comes from those who have made changes and have reported great improvements by doing so.
Something measured is more likely to be improved
To make sure any new process is worth adopting, you need measurements and statistics, such as the time taken for the job and the quality of the finished job. The reasons you are thinking about refining the process will give you a clue about what to measure.
By measuring routine jobs, and tracking progress on each one, patterns will emerge that will lead to the changes that will have the biggest impact on efficiency.
What’s the current process?
Mapping out the current process is the best way to visualise it and break it down into individual steps. This will give you a benchmark by which future improvements can be measured.
An easy way to do this is to write down every individual step associated with the service process on its own sticky note, then stick them on a whiteboard in the order in which they are performed.
Review each individual step
Look at each step in the process and question it. Why is it done this way? Can it be done differently? Is there a better way?
Look at the steps with fresh eyes and no bias. Think differently about what you’re doing and why you’re doing it. Just because something has been done a certain way for a long time doesn’t mean it’s the best way. Sometimes new steps might need to be added to the process, but generally speaking, it's best to cut the process down in size where possible.
Start putting together a new process
Simply rearranging the task order doesn’t help. Think about the process from the start and frame it without thinking too closely about how it has been performed in the past. New approaches to the job will often emerge and could lead to significant improvements.
Drafting up a new service process independent of the existing process will show any gaps between the two. Identify those differences so that you can measure the changes that drive the biggest overall improvements.
Time to try the new process
New processes developed by using this methodology may not be too different from your current process, and may not even be better. Before adopting it on the workshop floor, run through it with the leading technician.
Any service process should be used at least five times on the workshop floor to prove its value. If it falls short in some way, you will need to revisit the review.
Write it down and roll it out
Throughout this process you should be writing down your progress and any revisions. At the very least, the finished process must be documented because this is what will be used to implement the changes on the workshop floor.
As well as being used to apply new processes universally in the workshop, these will be the processes used for training new technicians and will serve as a constant reminder of ‘this is the way it’s done around here’.
Monitor, watch and review
Don’t stop at one process. Keep looking for the next process to improve, because technology is changing all the time. Today’s efficient process could be oldfashioned tomorrow.
Re-evaluate all your processes at regular intervals. The process of change gets easier as the workshop becomes more efficient.
Set a goal to review two service procedures in the next month and team up with a staff member to make sure the project is completed and any changes are implemented.
Don’t assume every process is the right one. Question everything and interrogate the reasons for each step in a process and why it is done that way.
Aiming for consistent improvement within the workshop, no matter how small the improvements, is really a basic management duty for survival. Every improvement you make will deliver savings in time, effort and resourcing.