TECHNICAL DOSSIER
PETROL FUEL ADDITIVES
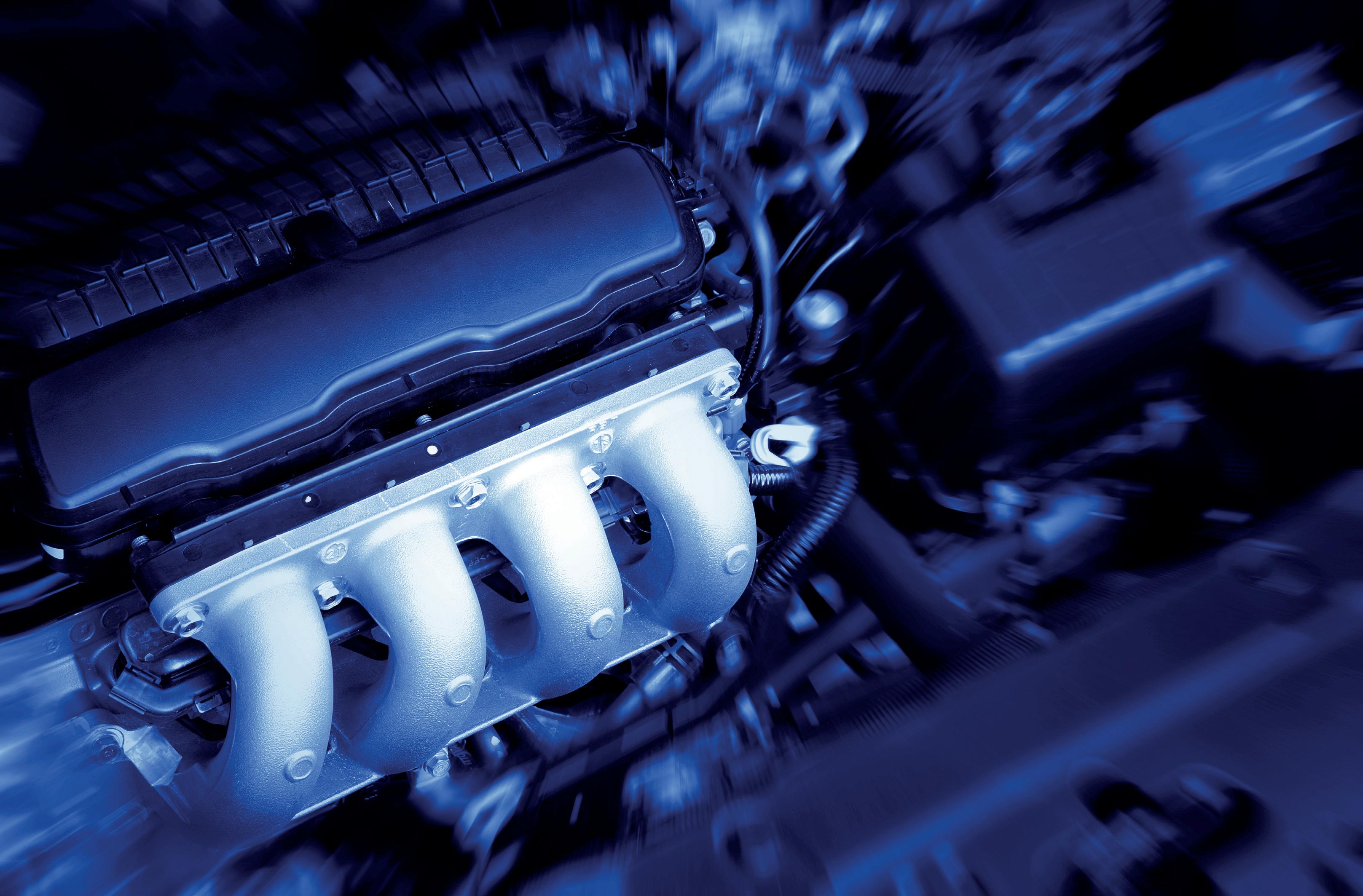
Sparco Additives is the fuel additive brand that provides more power, less fuel consumption and less pollution because it's a combination of molecules designed for more complete combustion.
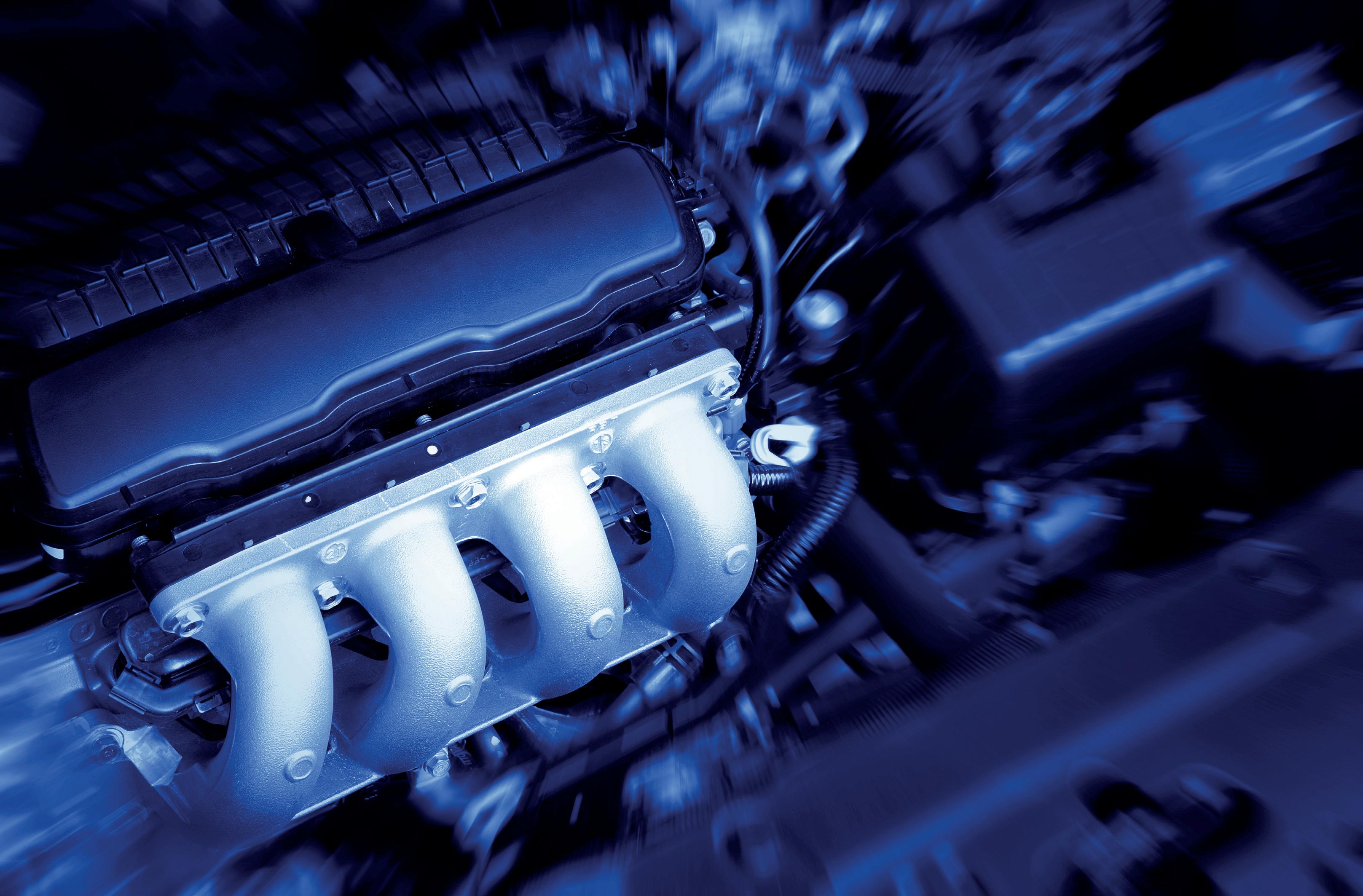
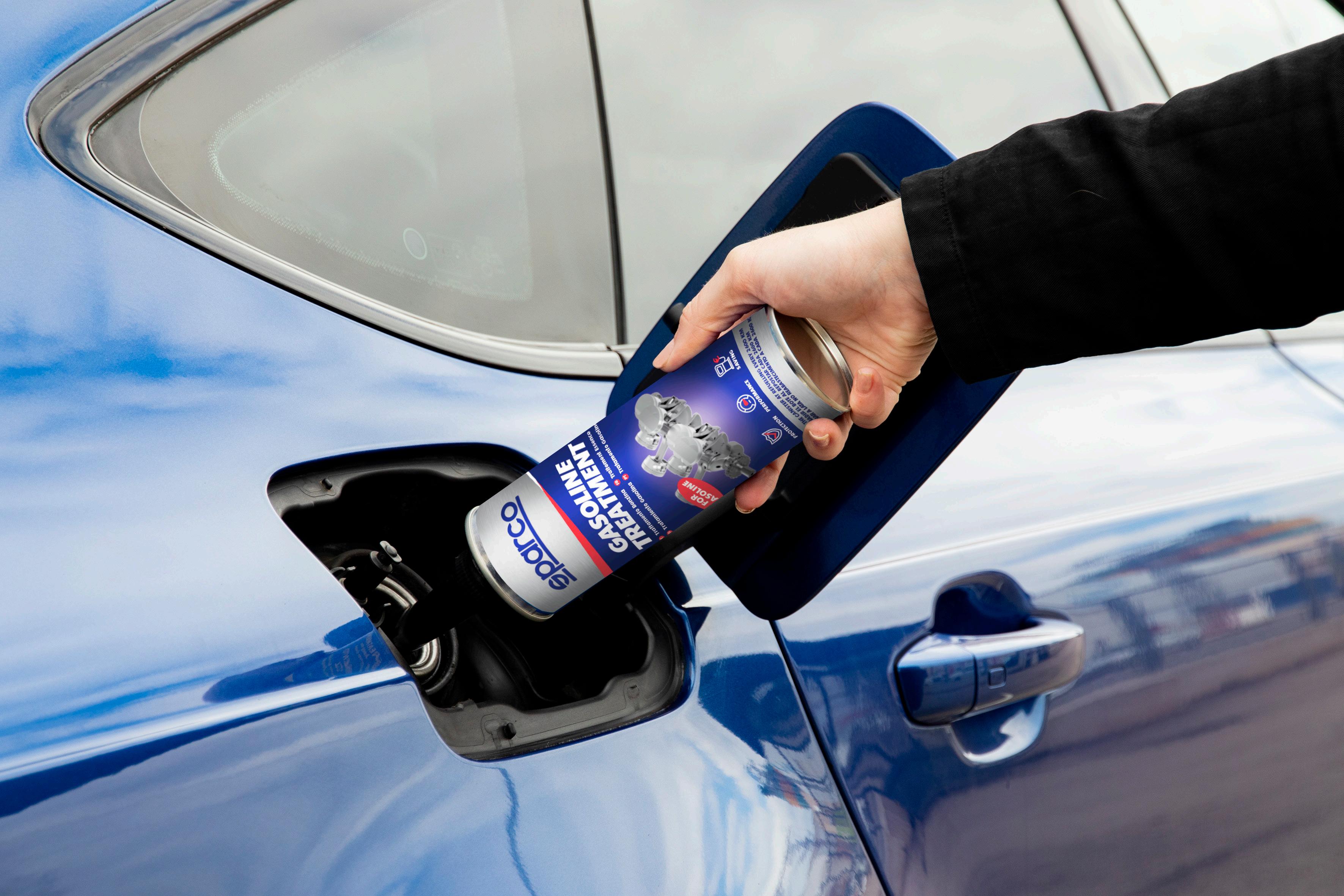
Gasoline Engine Fuel System Problem Areas
- The intake fuel system of a gasoline engine has three vital parts, namely the fuel injector, intake valve, and combustion chamber
- Injector deposits restrict fuel delivery that may cause misfire, hesitation, and rough idle
- Intake valve deposits can restrict the air flow through the intake ports. Deposits can absorb the fuel and soak up fuel spray from the injectors. This affects the mixing of the fuel and air that causes power loss and reduced performance
- Combustion Chamber Deposits can increase the compression ratio of the engine and the octane requirements of the fuel. This octane requirement increase (ORI) will cause spark knock or detonation if the fuel octane is not high enough
Product Attributes and Performance Features
- Sparco Petrol Additives are non metallic and do not contain phosphorus
- At the recommended treat rates, these detergent packages offer the following performance features:
· Control the level of deposits on injectors, intake valves and combustion chambers to keep the engine clean and maintain its optimum performance
· Provide protection against corrosion, emulsion or haze in wet fuel systems
· Decrease wear coefficient along metal surfaces inside engines resulting in increased efficiencies, improved fuel economy, longer parts life, and restored performance (for packages with friction modifier)
- All packages are completely soluble in gasoline and gasoline ethanol blends and compatible with commonly used engine and fuel system materials
Product Description
- Sparco Petrol Additives series of gasoline performance additives are detergent packages designed for both retail and aftermarket applications
- These packages are multifunctional and formulated to control deposits on injectors, intake valves, and combustion chambers
- Sparco Petrol Additives series of gasoline performance additives contain the following components:
· Polymeric dispersant
· Synthetic carrier fluid
· Demulsifier
· Corrosion Inhibitor
· Aromatic Solvent
· Friction Modifier (for some packages)
Application Benefits
Performance Features
Controls the level of deposits on injectors, intake valves and combustion chamber
Cleans up intake valve deposits
Provides excellent corrosion protection end reduces emulsion or haze formation
Reduces engine wear and instantly economises fuel
Key Benefits
Improved driveability, reduced emissions, and improved fuel economy
Restores lost engine performance
No rust, reliable engine, and longer engine life
Restored performance, longer parts life and fuel savings
- Port fuel injector deposits were first reported as early as mid 1980s
- In 2002, an auto manufacturer presented the findings related to the field problems to the Coordinating Research Council (CRC) Deposit Group
- For the injector fouling test, the test method ASTM D6421 is considered by the CRC as a quicker and much less expensive way of measuring fouling tendency (versus ASTM D5598)
Intake Valve Deposit Engine Tests
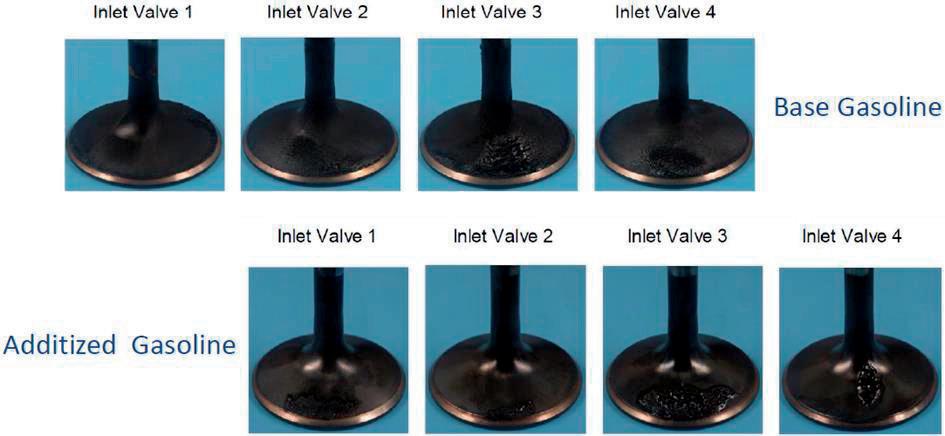
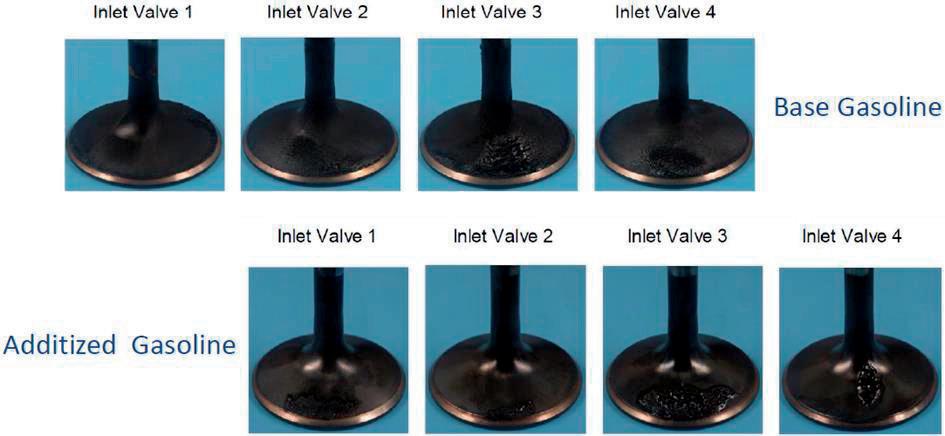
CEC-F-05-93
2.3L, 4 cylinder, 4 stroke PFI engine
Mechanical + Electronic
2 valves/cylinder
60 hours
Weight + Optical Comparison Deposits (mg/valve) + Rating Figure
M111
CEC-F-20-98
2.0L, 4 cylinder, 4 stroke PFI engine Electronic
4 valves/cylinder
60 hours
Weight Deposits (mg/ valve) + Total Combustion Chamber Deposits (mg)
Fuel quality, can

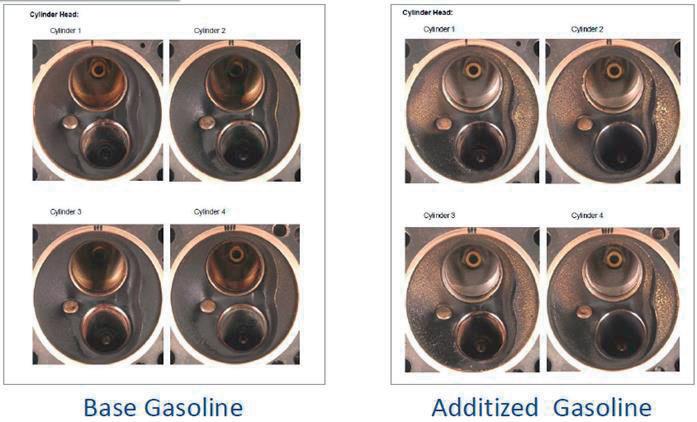
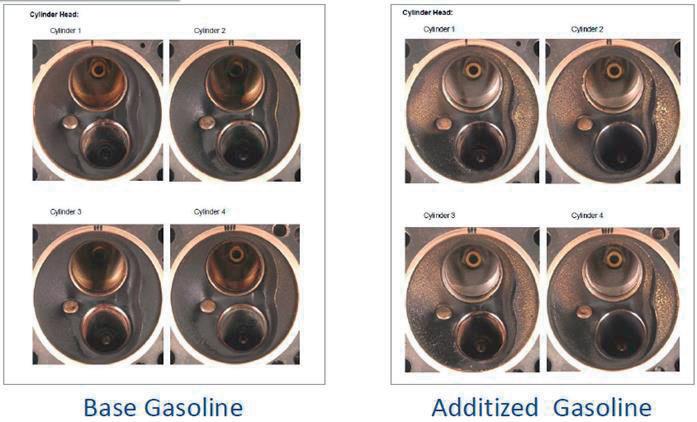
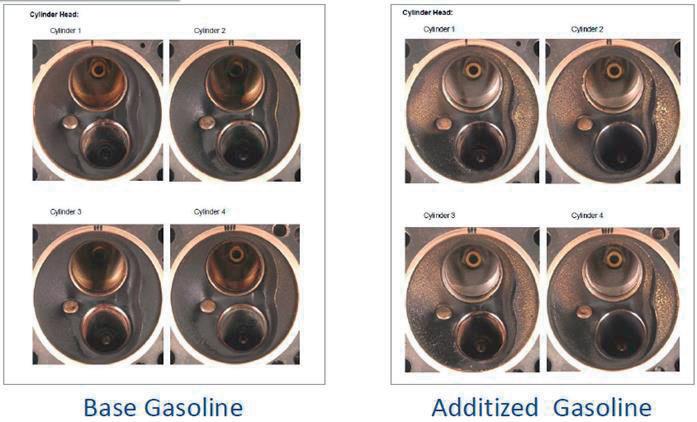
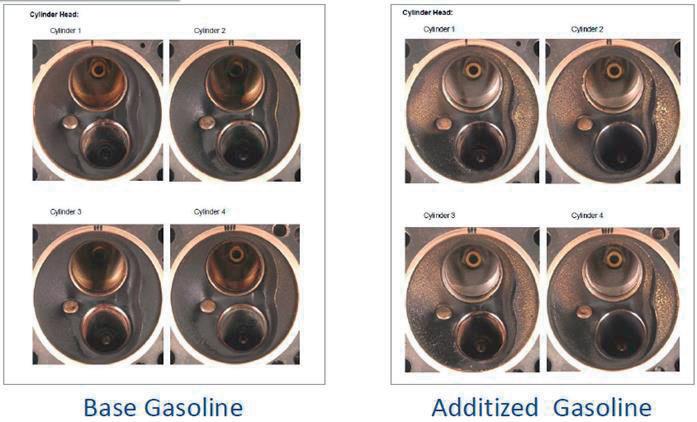
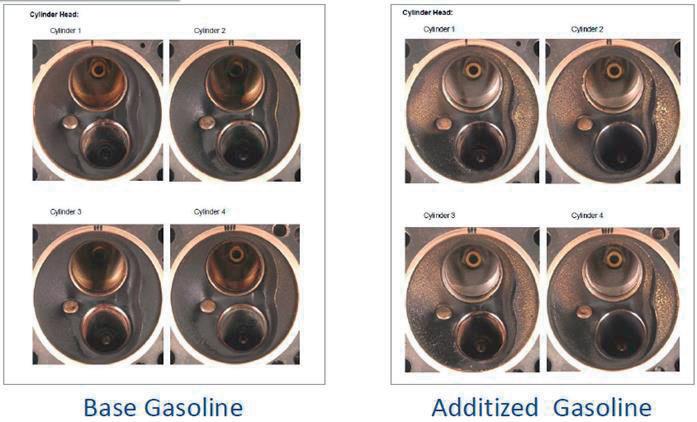
tergent addi�ves, lubrica�ng oils, engine design and opera�ng condi�ons are factors that to forma�on of deposits in the combus�on chamber nt add amber he base h min n cham om th meas
rding t
PERFORMANCE DATA - Combustion Chamber Deposits
- Fuel quality, detergent additives, lubricating oils, engine design and operating conditions are factors that can contribute to formation of deposits in the combustion chamber
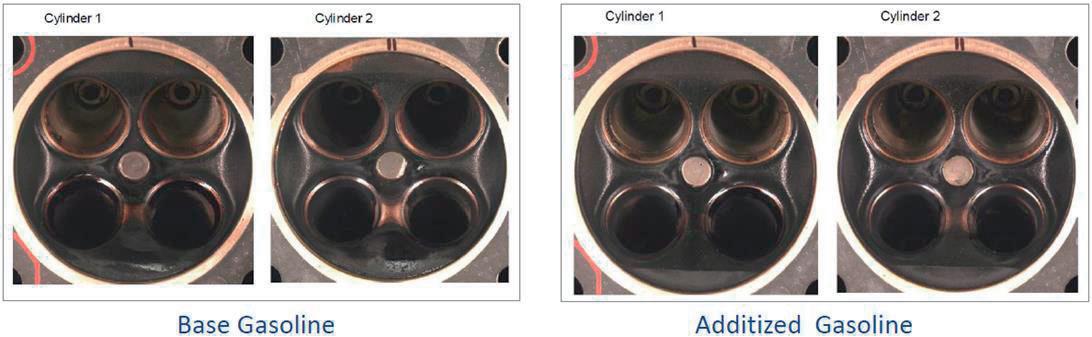
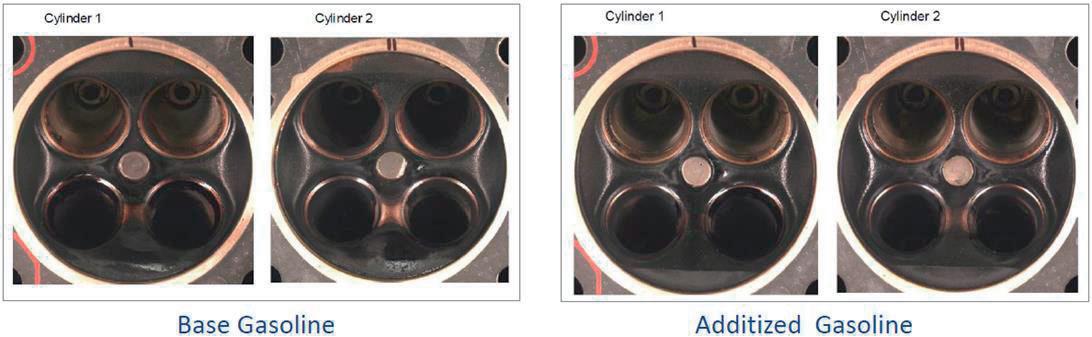
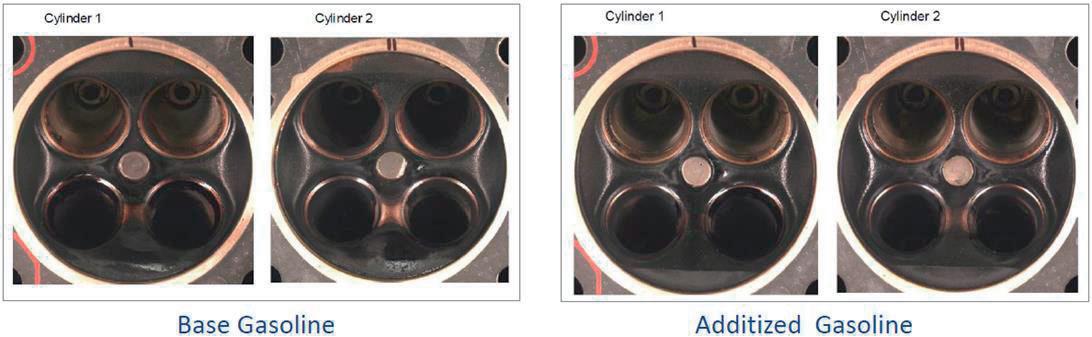
- While detergent additives are known to control deposits formation on the intake valves, it can increase combustion chamber deposits. Detergent packages have components that have higher boiling points as compared to the base gasoline that may contribute to deposit build up especially if packages are formulated with mineral oil carrier fluids
- The combustion chamber deposit (CCD) test was developed as a no harm test to ensure that the deposit contribution from the detergent additives is within acceptable levels
ding
- In Europe, CCD measurement is conducted according to CEC-F-20-98 test procedure
M102E engine according to CEC-F-20-98 procedure
there is no defined specifica�on or limit on CCD levels but anything less than 40% increase over the ddi�zed fuel is <140% of the CCD of base fuel) is considered to be acceptable
M111 engine according to CEC-F-20-98 procedure
CE DATA – Gasoline Direct Injec�on (New Engine Test)
Note: In Europe, there is no defined specification or limit on CCD levels but anything less than 40% increase over the base fuel (CCD of additized fuel is <140% of the CCD of base fuel) is considered to be acceptable
W EA111 twin charged DI engine
PERFORMANCE DATA - Gasoline Direct Injection
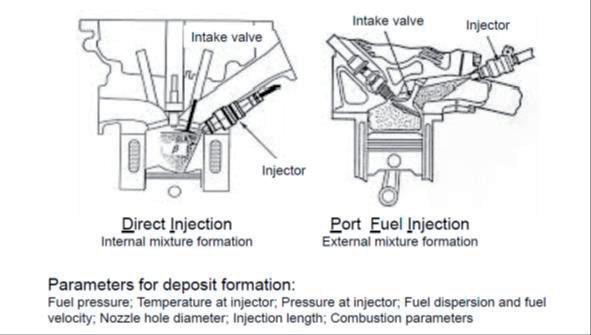
(New Engine Test)
- Test Engine : VW EA111 twin charged DI engine
- Test Cycles:
· 48 hours + 24 hours dirty up & cleanup test
· Part load at 2000rpm/56Nm
rs + 24 hours dirty -up & cleanup tes ad at 2000rpm/56Nm
- Test Status
· CEC Test Development Started 01/2017
· End of Phase 1 expected 01/2018
· Reference fuel RF 83 proposed
st Development Started 01/2017
Phase 1 expected 01/2018
nce fuel RF-83 proposed
Parameters for deposit formation: Fuel pressure, Temperature at injector, Pressure at injector, Fuel dispersion and fuel velocity, Nozzle hole diameter, injection length, Combustion parameters.
PERFORMANCE DATA - Combustion Chamber Deposits
- Fuel quality, detergent additives, lubricating oils, engine design and operating conditions are factors that can contribute to formation of deposits in the combustion chamber
- While detergent additives are known to control deposits formation on the intake valves, it can increase combustion chamber deposits. Detergent packages have components that have higher boiling points as compared to the base gasoline that may contribute to deposit build up especially if packages are formulated with mineral oil carrier fluids
- The combustion chamber deposit (CCD) test was developed as a no harm test to ensure that the deposit contribution from the detergent additives is within acceptable levels
- In Europe, CCD measurement is conducted according to CEC-F-20-98 test procedure
M102E engine according to CEC-F-20-98 procedure
FRICTION MODIFICATION
Fuel Energy Distribu�on
FRICTION MODIFICATION
Fuel Energy Distribution
Only 25% of the fuel energy is converted to u power output
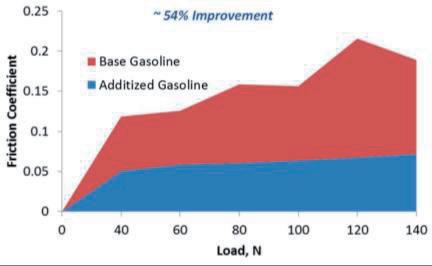
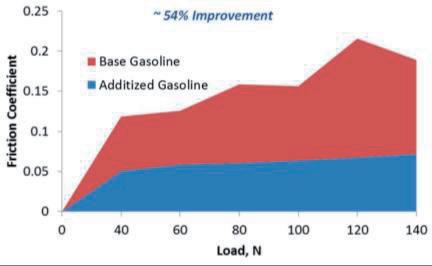
- Only 25% of the fuel energy is converted to useful power output
40 to 60% of the mechanical losses is due to ac�on of the piston assembly
- 40 to 60% of the mechanical losses is due to the action of the piston assembly
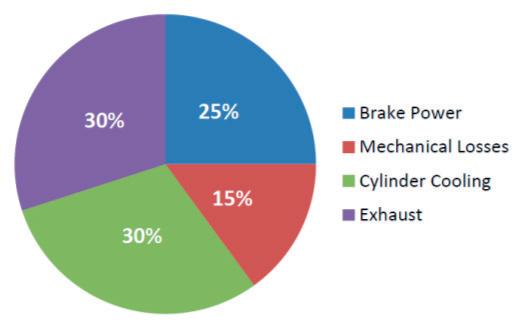
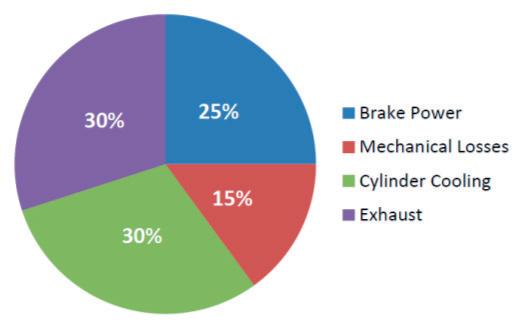
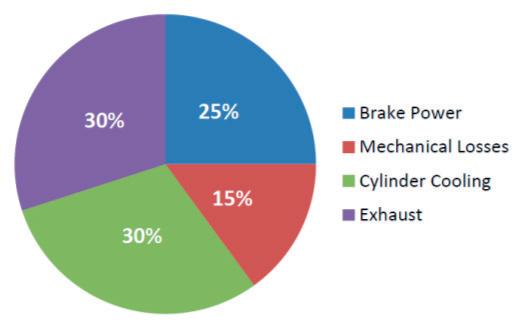
Friction Ocurrencies in the Engine
- Wear at metal to metal contact areas:
FRICTION MODIFICATION
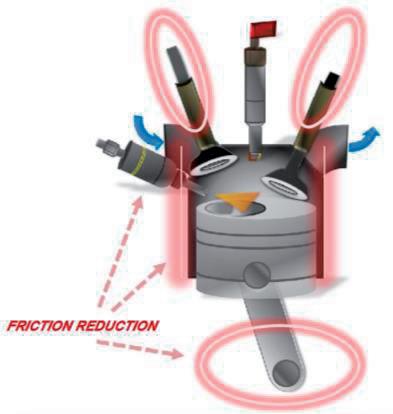
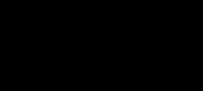
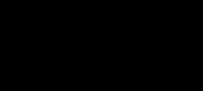
Mechanical looses
istribu�on fuel energy is converted to useful e mechanical losses is due to the ston assembly
Cylinder cooling
Fric�on Ocurrencies in the Engine
· Piston and Rings attribute to the majority of wear in an engine
· Crank and Bearings, Valve Train and Pump make up the other majority areas
· Along valve stems and valve seats
· Piston head and chamber walls
· Fuel pump and brushing
Wear at metal – to – metal contact areas: Piston and Rings a�ribute to the majority of wear in an engine. Crank and Bearings, Valve Train and Pump make up the other majority areas.
Along valve stems and valve seats
Piston head and chamber walls
Fuel pump and brushing
Newer engines have higher compression ra�os and smaller displacements
- Newer engines have higher compression ratios and smaller displacements
- Wear occurring more frequently at shorter engine lifespans
- Results in loss of efficiency
Wear occurring more frequently at shorter engine lifespans
Results in loss of efficiency
- Today’s gasoline is not as effective of a lubricant and can wear brushes in the fuel pump quicker
Today ’s gasoline is not as effec�ve of a lubricant and can wear brushes in the fuel pump quicker
Friction Modifiers and Restoration of Efficiency
Fric�on Modifiers and Restora�on of Efficiency
- Fuel wetting along chamber walls and internal surfaces allow for additive contact in these areas
- Reducing contact and prolonging parts
Fuel we�ng along chamber walls and internal surfaces allow for addi�ve contact in these areas
TE - 77 test rig is used to sim esul�ng wear as seen in an engine o
Reducing contact and prolonging parts
- Naturally occurring fuel dilution into the oil sump allows the friction modifier enhancing oil properties for longer drain intervals
Naturally occurring fuel dilu�on into the oil sump allows the fric�on modifier enhancing oil proper�es for longer drain intervals
odifiers and Restora�on of Effici
By increasing the load capaci proper�es of the fuel are tested for resist breaking down resul�n aces and a change in the Fric�on Co
Results in the restora�on of fuel economy and to the longevity of the engine life
- Results in the restoration of fuel economy and to the longevity of the engine life
TE 77 Wear Test
Characterize film efficiency a qualita�ve analysis through 3D Image Analysis. The test is done loo under magnifica�on and white light.
chamber walls and internal surfaces these areas and prolonging parts g fuel dilu�on into the oil sump allow modifier enhancing oil proper�es for longer drain inter
- TE 77 test rig is used to simulate the effects of load and resulting wear as seen in an engine over time
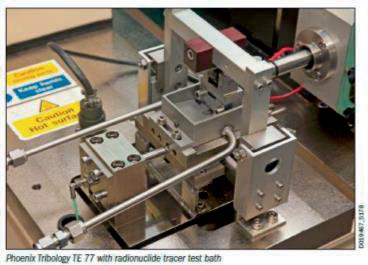
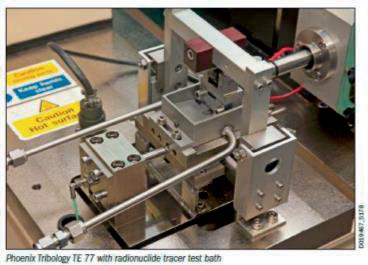
Results in the restora�on of fuel economy and to the lo the engine life
- By increasing the load capacity on specimen overtime the properties of the fuel are tested for their ability to resist breaking down resulting in a wear on the metal surfaces and a change in the Friction Coefficient
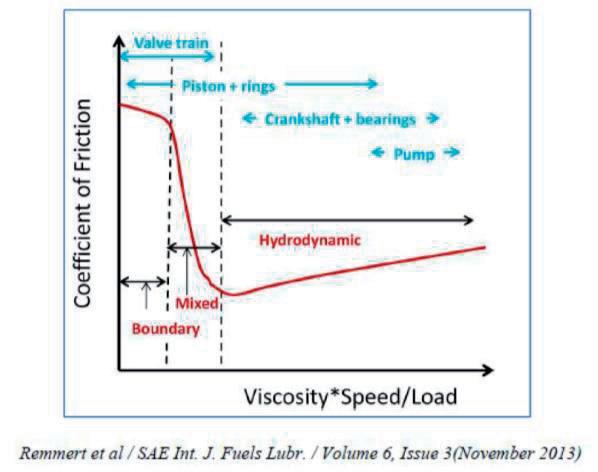
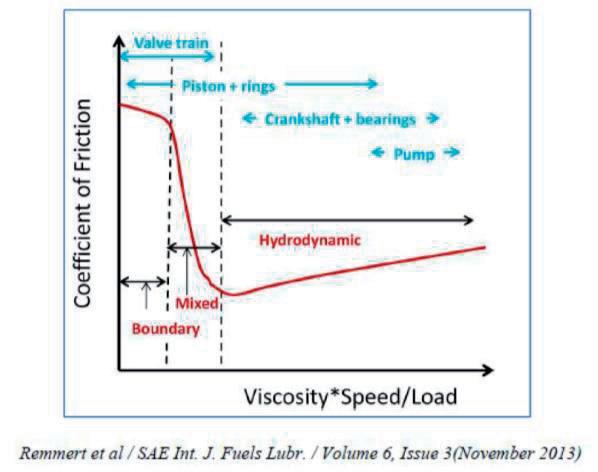
- Characterize film efficiency and surface scarring through qualitative analysis through 3D Image Microscopy Analysis. The test is done looking at surface appearance under magnification and white light
Base Gasoline
Additized Gasoline
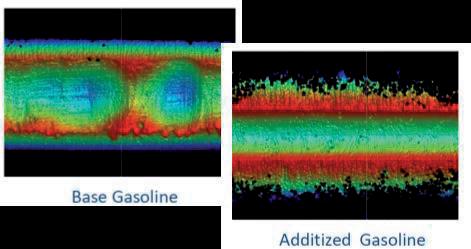
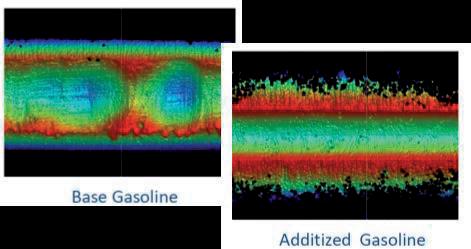
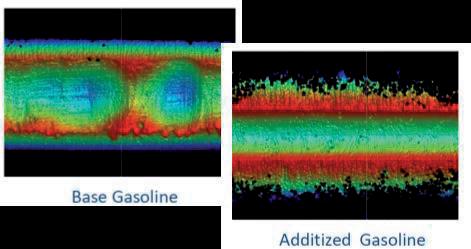
Phoenix Trilogy TE77 with radionuclide tracer test bath
hed off atures di�ve eter �cky to b pt is made to restart the engine no compression can be achieved
ADDITIONAL BENEFITS (No Harms Test) - Intake Valve Sticking Test (IVS)

- Fuel migrates to the annulus between valve guide & valve stem when engine switched off
- High temperatures can vaporize fuel leaving behind the deposit control additive
- If incorrect detergent system has been employed this can be viscous and sticky
- Causes valve to become stuck in the open position
- When attempt is made to restart the engine no compression can be achieved
- Engine will not start
Engine will not start
Intake Valve Sticking Test (GM V8 Engine SWRI Method)
- Test vehicle is a 1993 C 1500 truck with 5.0L V 8 engine and automatic transmission
- Test procedure. Test Vehicle was operated on a chassis dynamometer for four one. Hour driving cycles during each day of the evaluation. The one hour driving cycle consisted of driving the test vehicle for 56 minutes at 55 mph with a 3 minute idle period. After the driving cycles were completed, the test vehicle was cold soaked for 16 hours at 4 deg F ( 20 deg C). Following the cold soak, a cold engine compression test was performed to determine if valve sticking occurred
- The additized fuel did not cause intake valve sticking
ADDITIONAL
Ocurrencies in the Engine
BENEFITS - Water Reaction Test
- ASTM D1094
metal – to – metal contact areas: Piston and �ribute to the majority of wear in an engine. nd Bearings, Valve Train and Pump make up er majority areas.
- 20 ml water added to 80 ml fuel, shaken for 2 minutes then assessed over 5 minutes. Shake the cylinder for 2 min ±5 s, two to three strokes per second using 12 to 25 cm strokes
Separation rating are:
1 - Complete separation
Along valve stems and valve seats
Piston head and chamber walls
Fuel pump and brushing engines have higher compression ra�os and displacements curring more frequently at shorter engine s n loss of efficiency gasoline is not as effec�ve of a lubricant and r brushes in the fuel pump quicker
ADDITIONAL BENEFITS - Corrosion Test
2 - Air on water in fuel layer
3 - Emulsions, precipitates, fuel in water layer
Interface ratings are:
1 - Clear clean interface
1b - Small bubbles on <50% interface, no shreds, lace or film at the interface
2 - Shred of lace and/or film at interface
3 - Loose lace and/or slight scum
4 - Tight lace and/or heavy scum
NACE - 3.5 hours @ 38 deg C test temperature
ASTM
D665 - Pass or Fail
- Pass means no rust for both rods
- Fail means rusting on both rods
· Light Rusting: Rusting confined to not more than six spots, each of which is 1 mm or less in diameter.
· Moderate Rusting: Rusting in excess of the above but confined to less than 5 % of the surface of the test rod
· Severe Rusting: Rusting covering more than 5 % of the surface of the test rod

- Duplicate Test (2 rods)
· Procedure A – Distilled Water
· Procedure B – Synthetic Sea Water
- 4 hours @ 60 °C test
PROPOSAL
- Sparco Petrol Additives and its unique detergent system controls the level of deposits on injectors, intake valves and combustion chamber to keep the engine clean and maintain its optimum performance
· Excellent performance in M102 (Keep Clean and Clean Up)
· Excellent performance in M111 (Keep Clean and Clean Up)
· Keep Clean benefits on GDI
- Sparco Petrol Additives provides protection against corrosion and emulsion or haze in wet fuel systems
- Sparco Petrol Additives gives immediate benefit (Fuel Efficiency, Driveability ) due to the Friction Modifier
- Dosage / Performance
· Minimum dosage: 285 mg/Kg (310 ml/1000 lt of Gasoline)
· Suggested dosage 380 mg/Kg (415 ml/1000 lt of Gasoline) for a good balance among its cost, performance, clean benefits, fuel efficiency and driveability
· Maximum 600 mg/Kg (650 ml/1000 lt of Gasoline) to maximize all characteristics and functions