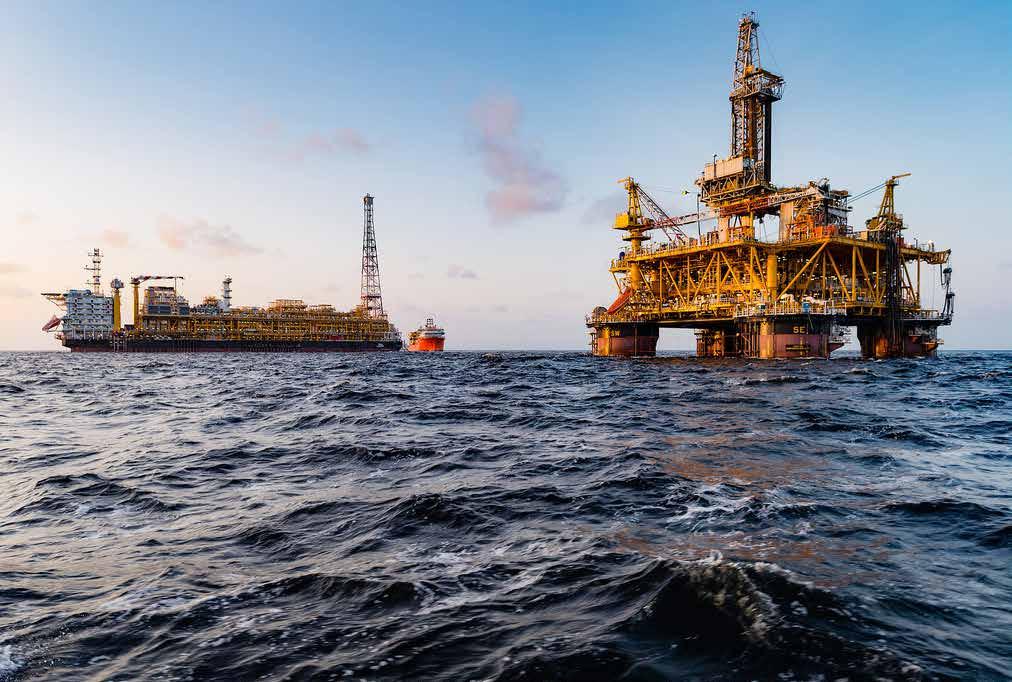
66 minute read
increase efficiency and boost production from the hundreds of thousand wells dotted across the country is gaining pace, and one of the most promising solutions is the digital wellhead
from IOG52
Moving to a cementless future for completions
By utilising an innovative cementless technology Total were able to reduce risk and increase operational efficiency for their Moho North field in The Congo.
The cementing process that isolates the various down hole formation zones as well as firmly fixing the casing in place has been core to the completion process since it was first used over a century ago. Despite its maturation as a completing technology is still presents a myriad of challenges to operators which has led them to seek new and better ways for zonal isolations.
During the drilling process, you will have to do several tests to make sure that you have correct pressure and a nonleaking well. Cementing is central to the discussion of zonal isolation and well integrity because cement typically provides at least one barrier in a well and is a component of the barrier envelope or barrier system during well construction and the operational phases of the well. Three cementing challenges in deepwater
Part of the process of preparing a well for further drilling, production or abandonment, cementing a well is the procedure of developing and pumping cement into place in a wellbore. Most commonly, cementing is used to permanently shut off water penetration into the well. Part of the completion process of a prospective production well, cementing can be
used to seal the annulus after a casing string has been run in a wellbore.
Additionally, cementing is used to seal a lost circulation zone, or an area where there is a reduction or absence of flow within the well. In directional drilling, cementing is used to plug an existing well, in order to run a directional well from that point. Also, cementing is used to plug a well to abandon it. Deepwater is one of the most challenging cementing locations where operators face a triumvirate of challenges including low temperatures, low fracture gradient and shallow flow hazards.
A new way
That all changed last year when it was announced that Total had successfully utilised an innovative cementless completion technology in the Moho North Albian field that they had developed in partnership with Welltec. The technology was Welltec Annular Isolation (WAI). Moho Nord is a deep offshore oil project situated 75 kilometres off the Congolese coast. It came on stream in March 2017 and is the largest oil project ever undertaken in the Republic of the Congo. The field will produce untapped reserves in the Moho-Bilondo license block, which covers an area of 320 kilometres and four reservoirs situated at water depths of 750 to 1,200 metres.
Given the challenges that cementing presents to operators they have long been searching for an alternative completion method that both reduces risk and saves operation expense. By using an innovative cementless technology it is possible for an operator to save up to $75 to $100m over a 15 to 20 wells deepwater field development plan can be achieved.
This solution is equally as viable for onshore and shallow offshore markets. Approaching it

from a larger scale makes the value proposition more obvious. “We like to think that we work on solutions that are best for the well and the overall project,” Gbenga Onadeko, Senior Vice President, Welltec Africa, says. “In most cases, our industry is integral to the economies of the oil and gas producing countries. We therefore believe that we are having a positive impact on the overall wealth of the nations we operate in.
“Total initially selected a cemented and perforated liner solution, the liner length was short and deep, implying the volume of cement was relatively small, which increases the operational risk of cementing the reservoir section. Because of the potential of cement contamination and also to increase the success rate of placing it behind the liner, the volume of cement pumped was increased by enlarging the hole (under-reaming) and drilling deeper i.e. a longer rat hole section, which placed the toe of the well within less preferential sections
of the formation increasing the drilling and production risks.
“With the liner deployed and cement in place, the WAB is expanded quickly under full surface control sealing against the formation rock, displacing the cement, providing a high integrity pressure isolation between zones. This in turn

ensures that even if channels or micro-annulus are present in the cemented interval, effective isolation is still achieved within the annulus.”
The long road to adoption
Even under the long-term depressed state of the price of oil that has necessitated a drive to greatly improve operational efficiency the oil and gas sector is still risk averse when it comes to adopting innovative techniques. The deployment of this project started four years ago when the Total team arrived in the Congo to prepare for the deployment. “Initially the Total team was not ready for a full cementless solution, so they used one of our products, which is called the WAB, in the wells in addition to the traditional cement,” Onadeko says. “Normally, the WABs can be used without cement to isolate several sections of the well, but in this case, because they had some technical issues, they decided to go with the WABs for their isolation properties in addition to cement.
“For most of the wells on this project, we had already deployed the WABs. But then towards the end of 2017 amidst the height of the industry downturn when the sector was really feeling the low cost per barrel, Total realised that this project was costing far too much. It had been sanctioned when the price of oil was much higher, and they urgently needed to cut costs, which provided us an opportunity to utilise this technology with its associated cost saving. In December 17 they invited all the service companies that had a contract with them on this project, to come and discuss how they could slash the well drilling costs by half.” Another reason that Total had confidence to proceed with the cementless WAI solution came about by chance. “On one of the WAB operations they put it in a long zone and accidentally put it into a well section thereby shutting off the hydrocarbon instead of water,” Onadeko explains. “Then they had to shoot some explosives into that hole to perforate it and the WAB was robust enough to withstand the shock; it did not impair their production. So that was another reason why they could go ahead and use the cementless solution, knowing now that they can perforate through and get a diversion.
“We develop cutting edge technologies and work extremely hard to convince our clients to deploy the value adding solutions. One of values we add to the industry is to assist our clients in overcoming their initial reluctance. We want to ensure that these technologies are included in their field development plans to avoid paying premiums later due to rush mobilizations.
Including the technologies in their initial plans reduces the risk of budget variation.”
The WAB and the WAI
The WAI provides long length open hole zonal isolation, significantly reducing the free annulus space between the casing and the open hole. The removal of this annular space can be beneficial in highly layered reservoirs of varying permeability, where selective production, stimulation or water shut off is required. Its metal expandable sleeve is hydraulically expanded, under full surface control using the rig pumps. Sealing on the open hole is achieved using a series of compliant, elastomeric seals, backed up by full circumferential metal to rock contact fins that prevent seal extrusion under high differential pressure.
While the WAI is suited to zonal isolation, the WAB for well completions can be utilised to provide solutions to many requirements throughout the completion phase of a well. Its leak rate capability, when set in cased hole, makes it ideal as a high-pressure production packer for both high pressure gas and oil well applications. In addition to this it can rotate and reciprocate during installation and cementing operations, and then expand and seal, on demand. In horizontal applications this allows the WAB to be incorporated as a Rapid Set Liner Hanger, reducing both risk and complexity in these often-challenging applications.
“The WAB gives us a zone of isolation,” Onadeko adds. “What we mean by that is you have a seal between a liner and reservoir and then you have a distance between that packer and the well. So, you have like an open anulus between these two packers for zonal isolation purposes. What the WAB gives you is seal integrity between the liner and the rock. Once you have established your seal then you are able to simulate, inject or produce into a certain zone.”
When cementing fails
The main competition to this technology has been cement, where liners are cemented in a well. The challenges are where the trajectories and the geometry of the wells become more difficult. In these instances, it becomes very challenging to assure the seal when using cement, despite that the bulk of wells today are completed with cement. But because cement does not always deliver the optimum seal between the liner and the anulus it makes it very difficult to compartmentalise your well.
“What the WAI gives you is cement replacement,” Onadeko continues. “Instead of leaving either cement between the packers or an open anulus, then the WAI fills the anulus with confined compartments; each WAI will be a compartment that’s isolated from the next compartment. We have no open anulus, we have no cement, but the whole of the anulus is now compartmentalised. With that achieved, you can then decide if you want to leave that compartment isolated, or whether you want to perforate it, stimulate it or produce it or inject into it. The WAI breaks down your reservoir into two metre compartments. And then you’ve got control over each two metre compartments. And each department has high integrity in relation to sealing.”
There are several things to consider when removing cement from the completion process. Cement has three functions that it is trying

to achieve for the well. The first as we have already discussed is to provide sealing which is not always possible as the well geometry becomes more challenging. For the Moho project Total had a tremendous challenge in ensuring the cement was going to seal. The second function of cement is to provide an anchor between the liner and the rock. Finally cement also supports the rock formations. If the formation is unconsolidated it provides a support to the rock to make sure it does not cave onto the liner.
“When we remove the cement, we need to be sure that we’ve addressed all three, the sealing, the anchoring and support of the rock,” Onadeko explains. “The WAB delivers two of those; it gives you the anchoring or sealing, but across the open anulus you are dependent on the rock having some sufficient mechanical properties that it won’t start to fall in onto the liner. Where the WAI will give you the sealing and the anchoring, it also gives you this mechanical support to the rock. So, WAI is really cement replacement in its full entirety, without the risk of the challenges presented by the geometry.” n
Data is king

Whether process plant, module or installation, the refinement of risk and maintenance planning is a constant process and one that involves the management of a vast set of variables.
Everything from wave conditions to wind speeds, pipeline pressure to valve performance, all must be factored in order to understand the performance and condition of an asset and its innumerable components.
Principles of risk, reliability and maintenance (RRM)
On an oil and gas producing asset there are hundreds of thousands of pieces of equipment. Just one failure can cause issues, production slow down or worse. “Safety is at the heart of all risk, reliability and maintenance (RRM) activities,” Rickard Dalman, operations manager, integrity management at Oceaneering says. “RRM frameworks help manage issues, assess reliability and schedule work using a riskbased approach to maintenance management.
“By leveraging data and expert operational and engineering knowledge, specific areas of concern can be identified, and appropriate performance standards implemented to ensure all effort and investment produces the greatest effect.”
The RRM approach involves a comprehensive review of topsides equipment on an asset. Examples include production, auxiliary and safety systems, and can also
incorporate the subsea infrastructure, the wellheads and the production facilities. RRM works by seeking to understand how critical each piece of equipment is, taking into account different perspectives and defining what’s most important for a process, system or module through criticality assessments. These assessments are followed by assignment of maintenance strategies and tasks, where runto-failure is not an option.
“The RRM project can be driven by the operator or partner however, in many instances, a specialist is brought in to help identify and work through the process to consider which pieces of equipment or systems are most important for each individual asset, with efficient and effective maintenance plans created according to particular standards,” Dalman adds. “Safety is obviously paramount throughout, as well as financial, reliability and operational factors that must also be considered.”
Driven by data
Because of the sheer quantity of equipment and parts on an asset, identifying where problems have occurred can be a costly and time-consuming task, particularly when it comes to analysing performance and understanding what equipment is the most critical.
“Today, advances in condition-based monitoring technologies and data analytics mean that huge amounts of operational information can be gathered to provide a snapshot of the performance of specific equipment,” Dalman continues. “This enables operations to make smarter decisions, and by honing in on the optimal maintenance routines they can ensure they are making the right
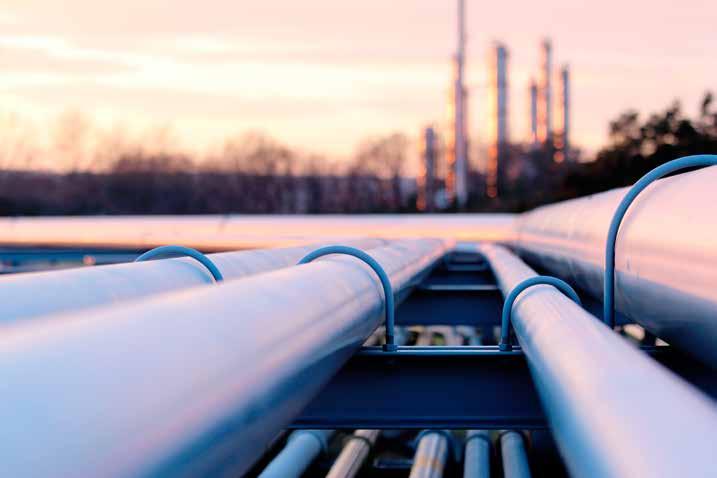
decisions, at the right time and for the right commercial reasons.
“Enhanced data gathering enables maintenance optimisation on a grand scale. The aim is for work to be carried out at the correct time from a safety and value perspective. Never too early that it’s an unnecessary cost, nor too late that an issue is missed.
“With an optimal RRM strategy, the operator has the ability to make confident, informed and optimised plans around how and where to focus maintenance efforts. In turn, optimising time spent carrying out maintenance and inspections, freeing up hours that could be focused on other critical tasks, or safely eliminating the need for certain inspections completely.”
A simplistic example of this is the adoption of a proactive spare parts strategy, which will ensure that you have the right
equipment, in the right quantities and accessible within the right time frame. It may not be necessary to keep an inventory of 5,000 bolts, however having the right amount of specified pressure safety valves (PSVs), for example, would be critical and absolutely necessary. “Reviewing and optimising your spares strategy will guarantee you are addressing and managing risk, as well as potentially saving of hundreds of thousands, or even millions of dollars, through accurate control and visibility of equipment stock,” Dalman explains.
A more complex example is the ability to use a RRM approach to assess historical data, extracted from an asset’s computer maintenance management system (CMMS) or other source. This data is then analysed by experts using customised algorithms and data analytics techniques to identify problems, reduce waste and refocus maintenance activities. “This can identify ‘bad actors’, poor performing equipment or one-off failures that often dictate the overarching schedule,” Dalman says. “These can then be uniquely identified, and a specific maintenance or replacement plan can be put in place. Thus, enabling asset owners to manage costs and efficiencies more effectively, without compromising safety and without incurring additional risk.”
Benefits to asset owners
As advances in data gathering and processing start to make their mark on oil and gas asset management, the benefits are clear. “Where the itemisation and monitoring of the otherwise overwhelming number of components on a drilling or exploration asset would once have been impossible to do manually, independent and experienced partners can now make this not only possible, but a highly efficient process,” Dalman concludes. “More so the benefits to asset owners speak for themselves. Reduced risk through enhanced risk management and increased production reliability are the holy grail of hydrocarbon production, and RRM puts this in reach for everyone. Not only now but for decades to come.” n
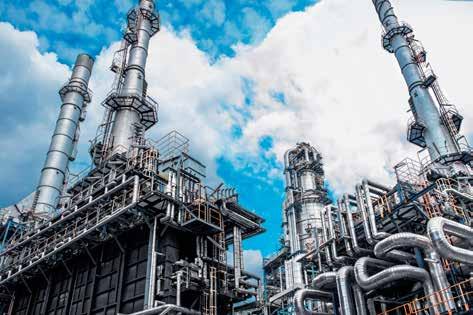
CASE STUDY – BRAZIL OVERVIEW
The RRM principle is something Oceaneering has been successfully providing its customers for many years. One example of the organisation’s approach to RRM was on an offshore installation in Brazil, which had recently changed ownership.
The customer purchasing an already operational asset and was also entering a new geography which provided various risk and unknowns. The new owner had to be sure that the maintenance and risk planning process was one they could trust and rely on for the future.
“With an acquiring asset, it is always more difficult to review and plan risk because there are many unknowns in relation to performance, reliability and condition,” Dalman explains. “There are hundreds of thousands of components to consider, have all of them been accurately maintained and inspected at the right time? Have they been replaced? Are the records accurate or, in some cases, able to be interpreted?”
There were some distinct challenges in this case. The operator approached Oceaneering as the expert service provider to translate the data into its existing company computer maintenance management system. The inherited maintenance strategy was focused on run-to-failure, whereas the new operator wanted to adopt a preventive maintenance strategy aligned with its global approach to maintenance management. It was also unsure whether data sets were complete, and it required a level of reassurance that all the relevant information was available or could be retrieved.
Oceaneering performed analysis to identify any gaps and missing information - then used its own technical experience coupled with historical data from similar assets to compensate for missing information. From there, schematics and technical databases were cleansed and updated to provide an accurate picture of the asset’s status. This included an assessment of more than 160,000 equipment tags. “As with many operators, this customer had a clear preference on how it wanted the maintenance information to be structured, so the programme was built to meet its individual requirements, recommending improvement opportunities to reduce costs along the way,” Dalma explains.
The implementation of the RRM approach has fundamentally changed the way in which the maintenance programme is now executed on the asset. It has delivered measurable benefits to the customer including: • A 50% reduction in annualised hours, leading to a year-on-year saving of $10million • Mitigated risk by providing accurate identification of safety critical equipment that was invisible in previous plans • Reclassification of more than 30,000 redundant equipment tags • Precision, control and visibility of maintenance on the asset supports efficient use of people on board (POB) resulting in less exposure to harmful activities • A uniform approach for maintenance management, in line with the customer’s global standards
Time for oil and gas to face the music on data

The maxim that data is the new oil had been floated around the oil and gas sector for several years now and while that might be overly simplistic it will play a crucial role going forwards if it can be managed effectively. To do that the sector could do worse that take a look at how the music industry handles data.
Whether or not data is the indeed the new oil, we still need hydrocarbons. With supplies diminishing, and it becomes even more expensive to get hydrocarbons out of the ground, innovation should be top of the agenda for the oil and gas industry. To find new ways of boosting efficiency and cutting costs, innovating is the only path forward. There is one significant obstacle that stands in the way of every innovation within the sector and, ironically, it is a mirror image of the traditional fear of oil and gas businesses. “It is not a shortage that threatens progress within the industry, it’s a glut; not of crude
but of data,” Simon Tucker, managing partner, energy & commodities at Infosys Consulting, says. “Until the industry can solve its data management challenges, it will be unable to deliver the new technologies that will help to keep down prices at the pump and also deliver on safety and energy efficiency. In their search for a solution, oil and gas businesses are looking to an unlikely source of inspiration.”
Taking inspiration from unlikely places
Anyone from the oil and gas industry should have an instinctive feel for the challenges of data. Like information, crude oil sits in vast lakes far from sight; it needs to be extracted and refined before it’s of any use to anyone.
But while the great oil and gas pipelines are constantly depleting reserves, data pipelines are always adding to the lakes, and therein lies the problem. “As these data lakes grow into oceans, businesses in every sector are struggling to cope,” Tucker adds. “The sheer size and complexity of oil and gas projects mean that these businesses often have to deal in petabytes, with upwards of tens of thousands of new rows of data generated every day.
“New technologies such as IoT have contributed to data volumes exploding at a far faster rate than businesses’ ability to manage and make sense of them. But, as is so often the case, technology provides answers to problems of its own making. One such answer lies in an app that will be familiar to many of the younger employees in the oil and gas industry: Spotify.
“As its users know, Spotify is much more than an online music repository. It’s a place to find the latest tracks, to find suggestions for new songs or artists, and to listen to (and create) curated playlists.
“Within a few years, we can envisage oil and gas companies using the same dashboard approach that has made the Swedish music service so popular. A Spotify-esque dashboard will enable oil and gas companies to visualise the data they work with, get suggestions, identify trends, discover new data sets, and pull all of this into one place to manipulate and report on it. This enables staff to examine realtime data, see if infrastructure such as drilling rigs, pipelines and production platforms are performing as they should, and try to maximise value based on real-time trends.”
Drilling down into data platforms
Using a music streaming service as the

model for the mind-boggling complexity of the oil and gas industry might sound like a bit of a pipedream, but the principles of good design are universal. With a dashboard-based approach, workers can easily find the data they need to work with, obtain and request information from colleagues, and discover new data sets from across their segment.
“Once they’ve got what they need, they can then pull it into one easily-managed workspace where they can analyse and manipulate the data, and report on it using advanced tools,” Tucker continues. “There’s no reason why the interface design can’t mimic the same simplicity that Spotify (or other apps) have used to drive their popularity among users.”
Tucker explains that the ability to access and visualise data is crucial for monitoring performance in real-time, as well as to match up engineering, maintenance and production data to provide an holistic view of operations. “This will have a hugely beneficial effect on the industry’s first priority, safety, by enabling workers to access up-to-the-second information about everything from corrosion to structural strength to leaks – vital for preventive maintenance projects,” he says. “Increasing the safety of operations is crucial
to the future of the sector. The more businesses can move to unmanned operations, the safer oil and gas becomes – simply put, there will be fewer people in harmful environments.
“Having the right data visualisation and management platform promises a far more efficient and timely way of maintaining equipment and infrastructure, enabling workers to spot issues in real-time, rather than spending six to nine months setting up a project to stitch together the data. In doing so, it could well prevent a major disaster – financial, environmental or both.”
The technology enabling success The benefits of data management and visualisation platforms are myriad, from enabling more unmanned operations that keep humans out of dangerous situations, to driving low-carbon operating models for the future of

energy. But these platforms are only the ‘front end’, and there are several key developments on which they rely. Not least of these is artificial intelligence, which is crucial for managing huge volumes of data 24 hours a day and extracting value from it. “It’s not humanly possible to manually manage petabytes of data, and harder still to be smart with it,” Tucker adds. “AI tools are developing to allow employees to suggest ways of using and analysing the data their business holds – and visualising the data on top of this will further improve the outcomes.”
Equally important is 5G, which is especially vital given that so many oil and gas installations are located many miles from the nearest wired networks. Only 5G can cope with the vast volumes of information generated and transmitted from these locations. “Not only will the much lower latency of 5G increase the amount of data points available, and move this data into the system faster, but the major change will be around surveillance,” Tucker concludes. “Without the latency of current networks, businesses can operate unmanned terminals using cameras and drones in real-time analysis. This means workers can remotely spot fires and leaks much faster and more safely than humans could, and they can transfer and react to this information much more quickly and efficiently.
“The oil and gas sector is undergoing a complete transformation as it moves from being focused on fossil fuels to prospecting in new fields such as mobility, battery power, electric vehicles and smarter fuels and lubricants. Data management and visualisation platforms will be central to their mission of becoming major players in creating a world that’s no longer reliant on hydrocarbons.” n
Design, digital and detail; saving millions with conductor analysis

The design, maintenance and monitoring of key components such as risers and conductors has developed significantly as the industry has matured. Today, highly developed digital technology is playing a huge part, not only in providing efficiency and cost savings, but also improving the safety of operations.
Conductor and riser systems must withstand all potential environmental conditions, but also need to be designed to contain the maximum pressure expected during operations. The new approach The obvious, but huge, benefit of analysing and testing conductor designs digitally is that it can be done very safely onshore rather than trying it out in the North Sea, waiting, and potentially dealing with disaster. Any conductor and riser system can be modelled in the virtual world, with nobody in harm’s way.
“Although this kind of data modelling has been used before, it is advances in the software
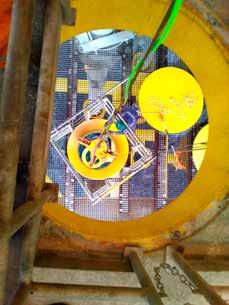
and processing power that have allowed a huge leap in its capabilities,” Martin Harrop, riser analysis manager, Aquaterra Energy, says. “Tens of thousands of numbers can be inputted, millions of calculations can be conducted, with varying loads, conditions, materials and so on all factored in, producing far more accurate and less conservative results than ever before.
“To date, the tendency has been to conduct this kind of analysis later in the development phase. With the plans drawn and the equipment ordered, it’s more often treated as a final check before work commences. Although there’s nothing intrinsically wrong with that approach, especially from a safety point of view, a significant amount of equipment expense and time can be saved if analysis is done early on in the process. Hundreds of real-world scenarios can be modelled relatively cheaply and quickly in the analytical world, pushing the boundaries which would have been too inefficient through paper-based systems.”
Harnessing this new era of high-powered computer models removes conservatism from the design stage, because impossible or inefficient options are quickly ruled out or refined. In doing so, more cost effective and streamlined designs can emerge that are still fit-for-purpose. Integrated teams and actionable outcomes
This early stage analysis approach has recently been used to tackle a design feasibility project on a platform in the Norwegian sector of the North Sea. The installation had been active for around 15 years and the owners were looking to add two more conductors in order to enhance its production.
With two available conductor slots, the solution seemed obvious - almost beyond question. Two conductors would be installed in the two spare slots, maximising the use of the pre-existing infrastructure.
One question did remain, however. These vacant slots did not have all necessary lateral guide supports installed and therefore the conductor performance could be compromised. So, a means to provide this support had to be found.
“A retrospective installation of a lateral guide support below water level was deemed very risky, as it would involve divers,” Harrop adds. “Initially, the client planned to install two supports: one above the water level and one below the water level. A hugely complicated job, not to mention in a difficult North Sea environment. Aquaterra Energy’s integrated analysis and engineering team was brought in to show how this might be possible.”
Reliable results
The analysts started by getting a comprehensive understanding of all the equipment within the plans and on-site including conductor design, water depths, environmental conditions, location of the guides and a variety of other different design specific parameters. The information was then used to build a representative computer model in specialist software, allowing the team to simulate exactly how the system could react under many different conditions.
“One of the key factors to simulate was the North Sea conditions, as when a storm hits the waves can induce significant load and movement on the conductors,” Harrop explains. “The loads were then read and compared to industry safety codes which are set by API and DNV, allowing an accurate picture as to whether they were acceptable.”
Not stopping there, the Aquaterra Energy team took this a step further, looking at higher level models, varying ideas around how the support could be designed, where it could be placed and how it could be installed at a few different elevations. Ultimately challenging the client’s idea to see if there were any better solutions available to them.
“With the analysis team being under the same roof as the offshore teams, it allowed potential solutions to be challenged on a feasibility basis, and therefore no solution was suggested that wasn’t possible to deliver,” Harrop says.
Significant savings and a new approach
Through open dialogue and collaboration between the client and analysts, a rather welcome result awaited in the data. “The outcome of this assessment was significant, and saved the client over £4million in project costs and additional untold savings on future maintenance,” Harrop continues.
As to how this was achieved Harrop explains that the analysis found a workable solution by only adding a support just above the water level. “This was achieved by optimising the conductor pipe by increasing the wall thickness and designing out the need to install a support below the water level,” he explains. “This mitigated the need for an expensive second support and significantly simplified the planned operations. Notably, divers were no longer required as the required support was above the water level, improving safety through reduced risk. As Aquaterra Energy works closely with its clients, the recommendation was made after liaising with the client to make sure they could obtain the required pipe size on time for the operations to begin.
“In providing independent advice, quickly, it gave a fresh perspective for this type of project in future. In today’s environment, where safety, efficiency and enhanced production are close bedfellows, it has been all too easy for the industry to go with what’s been done before – but new and advanced analysis supports the drive to optimisation in the 21st century.” n
Utilising flare gas to generate power for the oil and gas sector

Dynamic expansion of the oil and gas industry continues to fuel the demand for new technologies that tackle the impact of flare gas emissions globally.
While the production of oil has grown by roughly 30 per cent over the past two decades, reaching 18 million barrels per day in 2019 in the United States, the climate impact of flare gas, typically considered a waste by-product by the oil and gas industry, continues to be of concern. Globally 140 million cubic meters of natural gas are flared annually, emitting more than 300 million tons of carbon dioxide (CO2) into the environment.
According to Cummins, a lack of infrastructure to capture and sell the flare gas released when drilling for oil is a major environmental problem. “Governments, development institutions and oil companies around the world are being pressured to look at the amount of money spent in gas flaring and the damage it is causing to the environment,” Linda Nezerwe, technical specialist at Cummins,
and expert in emissions control for both diesel and gas generator sets, says. The company recently launched the HSK78G natural gas generator series, designed to provide reliable power regardless of the natural gas source or the climate, and capable of generating power from very aggressive fuels otherwise considered waste products.
“The quantity of unburned fuel that needs to be flared is usually known, but the question is what to do with it,” she added.
Flare gas and the environment
According to Cummins, billions of dollars in wasted natural gas could be used to generate reliable, affordable electricity and yield billions more per year in increased global economic output.
“The World Bank has launched an initiative called Zero Routine Flaring by 2030 which encourages investment in technologies that utilise the unburned fuel and find ways to protect the environment whilst bringing financial benefits,” Nezerwe continues. “Maximising flare gas to generate electricity would ensure that the oil and gas industries are helping nearby communities while also protecting the environment. Countries like Norway, Algeria, Canada and the United

States have made a lot of progress in limiting local oil companies on how much flare gas is allowed. More and more countries are joining the movement.”
The World Bank initiative brings together governments, oil companies, and development institutions who recognise the flaring situation is unsustainable from a resource management and environmental perspective, and who agree to cooperate to eliminate routine flaring no later than 2030. Governments and oil companies that endorse the initiative will publicly report their flaring and progress towards the initiative on an annual basis.
What to do with the unburned fuel?
Flaring of gas contributes to climate change and impacts the environment through emission of CO2, black carbon and other pollutants. It also wastes a valuable energy resource that could be used to advance the sustainable development of producing countries. For example, according to The World Bank, if this amount of gas were used for power generation, it could provide about 750 billion kWh of electricity, or more than the African continent’s current annual electricity consumption. While associated gas cannot always be used to produce power, it can often be utilised in a number of other productive ways or conserved.
In creating technologies to tackle environmental protection, Cummins says that proposed technologies for replacing gas flaring should not add additional complexity or bring added cost burdens to the operator. “Refineries will routinely flare gas during normal oil processing operations to reduce the unwanted gas in normal production. The major challenge is what to do with the excess gases.
“Current technologies such as Flaring Recovery Systems (FRS) have the goal to recover some of the flare gases and introduce them back to the refineries,” Nezerwe says. “Although these technologies have proven to be effective, they require a lot of upfront cost for equipment and management of the gas quality. However, thanks to technological advancements, today’s oil and gas companies are increasingly utilising natural gas generators
that burn raw gas instead of burning it off which is wasteful and harmful to the environment.
“This is where generator set manufacturers can play a big role,” she continued. “These generator sets can use a wide variety of fuels including low energy fuels and fuels that are often unused to produce electricity for neighbouring communities. By designing and manufacturing products that can utilise flare gasses for electricity production, lean burn combustion technologies are capable of combusting fuels of various energy levels and composition to produce power. They can produce electricity with high efficiency and very low exhaust emissions.”
How does lean burn technology work?
A lean burn engine uses excess air in the combustion chamber to have lower combustion temperatures and therefore lower NOx emissions making it an environmental friendly option. The generator’s high efficiency can be further improved by also capturing waste heat from the engine coolant as well as the exhaust gas for processes within the facility or to consumers nearby. For example, the Cummins HSK78G engine is capable of operating with high or low energy density fuel with a combined heat and electrical efficiency of around 90 per cent of the fuel input.
Utilising flare gas to generate power does present engineering challenges. Flare gas will consist of a complex mixture of different gases. The composition will depend upon the source of the gas going to the flare system, however, associated gases released during oil-gas production mainly contain natural gas which is more than 90 per cent methane with ethane and a small number of other hydrocarbons. Gas flaring from refineries will commonly contain a mixture of hydrocarbons and in some cases hydrogen. It’s important to recognise that the changing gas composition will affect the heat transfer capabilities of the gas, something which engine manufacturers will understand to ensure the performance and feasibility for their products.
“This new lean burn technology pushes new levels of efficiency, transient performance and gas variation well beyond former natural gas generators,” Nezerwe explains. “When generator set manufacturers describe features of their products, the focus is usually on the generator set outputs such as heat and electricity. But the new series of Cummins generator sets also bring the added benefit that it is able to burn flare gas, pipeline natural gas, and biogas, as well as even the lowest-BTU fuels with high efficiency and low emissions.”
A critical development for the oil and gas industry is the advancing technology in natural gas generators to utilise fuel sources that would otherwise be considered waste products. This leads to robust power solutions even with very aggressive fuels with minimal derating. These advancements in power generation applications allow operators to
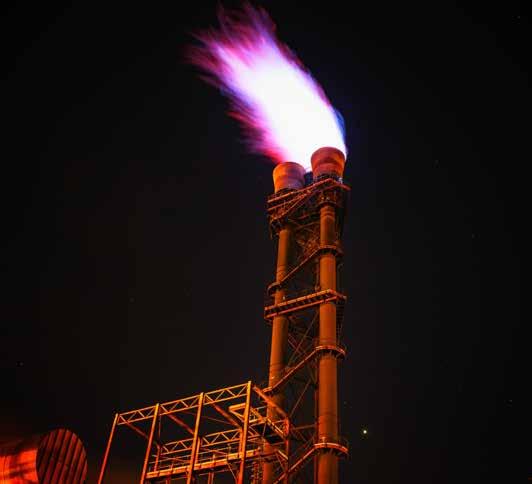
utilise environmentally harmful raw flare gas for diverse purposes instead of simply burning it, with clear benefits to the environment. The result is that routine flaring can be reduced and transformed into a more environment friendly option while also helping communities through the supply of electricity.
Investment in research and development across the industry continues to be a priority to come up with more efficient and costsaving options to cut losses, utilise the associated gases and save the environment. As governments, development institutions, manufacturers and oil companies commit to more efficient operations and implement advanced technologies to lower the environmental footprint of drilling, generator set manufacturers have a significant role to play in manufacturing products that can utilise flare gases to generate power. n

Working towards a low carbon future
Oil & Gas Technology spoke to Matthew Chinn, executive vice president of new equipment sales and customer operations for Siemens Oil & Gas, about the importance of decarbonising the entire oil and gas supply chain
OGT: How important is it that the oil and gas sector decarbonises its operations?
Matthew Chinn: There’s considerably more focus today on a lowcarbon future than there was even a year ago, so it’s critical that the oil and gas sector considers the carbon-free future world. Oil and gas continues to be the backbone of the global energy supply and natural gas will likely become even more important in decades to come. The industry’s challenge is to employ the right mix of technologies to achieve a
low-carbon world while ensuring reliable production and sustainable supply. The energy industry plays a key role in meeting this goal and taking steps to make it happen. People are seeing a tipping point for a cleaner world – with themselves, and with their customers, shareholders, and other stakeholders.
In the oil and gas industry, we clearly need to tackle our emissions, but also help our customers make low-carbon choices. While oil and gas companies remain under pressure to reduce emissions, most emissions associated with oil and gas come from consumption, rather than production. Decarbonisation truly happens with consumer choices, such as what cars we buy and how we heat, cool and light our homes.
OGT: Oil and gas companies are increasingly looking to decarbonise their activities. How can Siemens help them?
Matthew Chinn: For Siemens, sustainability is a matter of leveraging the right technologies to reduce environmental impact, improve equipment performance, and reduce both CAPEX and OPEX. We’re developing a range of cleaner technologies that support the energy transition and reduce emissions. While we’re traditionally known as a leading rotating equipment supplier, all aspects of the energy value chain fall within our remit. New transmission and distribution technologies – like high-voltage direct current (HVDC) and efficient, flexible gas turbines – are just two examples. Our all-electric oil and gas production concept based on HVDC transmission equipment can power a production plant using renewable energy from the grid, as opposed to using mid-sized gas turbine engines.
Traditionally, oil platforms have been powered by mid-size gas turbines. Equinor is one oil major that has adopted HVDC technology to cut emissions from its offshore facilities on the Norwegian continental shelf. Carbon emissions from gas turbines produce up to 80 percent of Equinor’s entire carbon emissions, leaving considerable room for massive reductions. In 2018, Equinor saved over one million tonnes of CO2 emissions from its operations by partnering with us to find smarter, more efficient and sustainable solutions and reinforced its position as a trailblazer for a cleaner oil and gas sector. OGT: Are there any particular elements of the oil and gas supply chain that you are targeting?
Matthew Chinn: A key element is our advanced gas turbine technology. Today, we can effectively recycle stored hydrogen into electricity by using it as fuel. This year, as part of our commitment toward environmental sustainability, we signed a European industry agreement that promised our new gas turbines can be operated with 20 percent hydrogen (mixed with natural gas) by 2020 and 100 percent hydrogen from 2030 onwards. Parts of these commitments have already been fulfilled, as much of the Siemens gas turbine portfolio can use fuel mixtures with hydrogen levels of 30 percent or higher, and even up to 100 percent in some turbine models.
We recently launched a performance enhancement for the SGT-800 industrial gas turbine that is used in many oil and gas applications. The upgrade – designed to provide operators with significant fuel savings and consequent CO2 emissions reductions – offers up to a 3.5 percent increase in efficiency and can be performed in conjunction with a scheduled major overhaul to minimise production impact and keep CAPEX to a minimum. Similarly, gas processing plants typically use multiple diesel engines. However, converting from diesel to gas – or even electric power – eliminates a major source of CO2 emissions.
OGT: What are the key technologies for decarbonisation?
Matthew Chinn: A key enabler is Proton Exchange Membrane (PEM) electrolytic technology for generating “green hydrogen” from water at an industrial scale. To generate green hydrogen at the scale needed to decarbonize the world’s energy, Siemens and key partners have spent the last 10 years investing in generating hydrogen from water using PEM electrolysis technology. This process uses low-cost renewable energy sources to split water (H2O) into its constituent elements without generating carbon emissions. The hydrogen can then be used as a zero-emissions fuel or combined
with other elements as a molecular component in core industrial feedstocks.
Siemens complements its PEM technology capability with carbon capture and utilization (CCU) technology required for many parts of power-to-gas and powerto-liquids processes. We can offer the CCU industry a wide range of electrification, automation, and digitalization products from our portfolio, plus global domain expertise and experience to assist operators.
OGT: How can digital technologies help?
Matthew Chinn: To make oil and gas production cleaner – producing more energy with less carbon – we also need to make it safer and smarter as well. The only way to do that is to fully embrace digitalization.
Realising the true value of data lies in knowing how to analyse it. Translating huge quantities of information into a valuable

resource can lead to better data-led operational decision-making that can be executed more quickly. More data, automation and intelligent analysis are already creating significant efficiency gains and cost savings throughout the oil and gas sector and improving safety and reliability. For example, ‘digital twin’based systems can integrate data and enable design, testing and training in virtual, risk-free environments.
Applicable from the subsurface production equipment to central processing facilities, new techniques are also creating new opportunities in operations and maintenance. Advanced data analytics maximise the value of equipment throughout its lifecycle and enable new approaches, such as predictive rather than scheduled maintenance strategies. And developments like the increased use of normally unmanned installations are also made possible by intelligent digital systems. OGT: What about Siemens Oil and Gas; how is it decarbonising its own operations?
Matthew Chinn: The use of innovative technologies such as advanced energy management and energy-efficient drives, as well as increasing automation are pillars of our emissions reduction strategy. We’ve made a commitment to become completely carbon neutral by 2030. Across the company and in every business unit, Siemens aims to be the world’s first major industrial company to achieve a net-zero carbon footprint.
In 2015, carbon dioxide emissions across the company, including the oil and gas division, were on the order of 2.2 million tonnes annually. Today, that number has been slashed by more than one-third. Cross-sector measures to improve efficiency and reduce the energy footprint of our production facilities and buildings is
expected to save about €20 million a year on energy costs from 2020 onwards.
To reduce emissions further, Siemens is using distributed energy systems at our production facilities and office buildings, deploying low-emission and e-mobility vehicles across the global vehicle fleet, and moving toward a clean power mix increasingly reliant upon natural gas and wind power.
OGT: How do you view the future prospects of the oil and gas sector amidst the drive for clean energy?
Matthew Chinn: A carbon-free world is an absolute necessity and our future reality. The Stone Age didn’t end because the earth ran out of stone or that it became too expensive to produce. Better alternatives became available. This same process is taking place right now across the oil and gas sector, but it too is a transitional process. Oil and gas will continue

to be used and will inevitably play an important role in the energy mix of the future.
As one of the many activities to decarbonize the world’s energy production and use, Siemens is active in the “Powerto-X for Applications” Working Group at the Mechanical Engineering Industry Association (VDMA), which has 3,200 member companies and is Europe’s largest mechanical engineering organization. Our involvement with VDMA is part of Siemens’ commitment to social and environmental responsibility.
Some of the world’s leading oil and gas majors are already announcing their commitment to raise performance standards in terms of energy efficiency and sustainability. Royal Dutch Shell, for example, is one of the world’s biggest oil developers but reportedly is already spending billions of dollars a year on its new energies division. Not every oil and gas company can match the resources of Shell but every company can adopt a low-carbon philosophy and adopt appropriate measures wherever possible.
Right now, considering the precise route to a carbon-free world is less important than beginning the journey by embracing energy efficiency, reducing emissions where possible, and preparing for the clean, low-carbon oil and gas business of tomorrow.
Matthew Chinn is the executive vice president of new equipment sales and customer operations for Siemens Oil & Gas. In this role, he has worldwide responsibilities for new equipment solutions and customer operations. Chinn is also the head of Siemens Oil and Gas Market Development Board which includes responsibility for leading the Siemens Corporate Account Managers (CAM) organisation responsible for managing and facilitating strategic relationships across the broader Siemens enterprise. n
Innovation Focus
Schlumberger has introduced the Ora intelligent wireline formation testing platform at the SIS Global Forum 2019 in Monaco. The platform leverages a new architecture and metrology for enhanced performance, enabling dynamic reservoir characterization in all conditions, including where previously impossible.
The Ora platform is rated to 200 degC (392 degF) and 35,000 psi and includes a new focused radial probe, a dual-inlet dual packer, laboratory-grade metrology, new measurements, and the highest flow rate pump
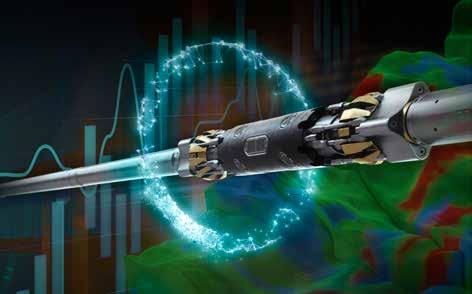
in the industry. The digitally enabled hardware can automate complex workflows, reduce operating time by more than 50 per cent and deliver the highest precision fluid analysis and zero contamination samples. Furthermore, deep transient testing is now possible on wireline.
The platform is built on a digital infrastructure, providing a new customer experience, enabling real-time decisions in a cloud-native environment.
“Characterising dynamic reservoir properties is becoming more critical and difficult than ever as drilling for hydrocarbons
Anew oilfield product to prevent one of the oil and gas industry’s most deadly situations is about to undergo field trials next week after simulator testing revealed astonishing results. Safe Influx helps avoid well blowouts by automating well control operations and removing the human risk factor is moving towards complex geologies and challenging environments,” Djamel Idri, president, wireline, Schlumberger, said. “Moreover, analysing this data to make business decisions can take weeks if not months. The Ora platform was built to address these challenges, with new wireline formation testing hardware and digital edge solutions enabling our customers to make faster and better decisions.”
The Ora platform has successfully completed more than 30 field trials worldwide in a variety of operating environments in the North Sea, US Gulf of Mexico, West Africa, Middle East, North Africa, and Central America. In Mexico for Pemex, the Ora platform was the first ever wireline formation tester to collect high-quality gas condensate samples in a challenging carbonate formation with permeability below 0.03 mD and 182 degC (360 degF) at 20,000psi pressure. This helped Pemex announce the tripling of estimated reserves for Mexico’s most important land discovery in the last 25 years.
In deepwater Gulf of Mexico for Talos Energy, the Ora platform obtained high-quality downhole fluid analysis data in a challenging well geometry, which was immediately integrated and visualized in the reservoir context. The reservoir model was then updated using a bespoke Schlumberger reservoir fluid geodynamics workflow, enabling real-time assessment of lateral and vertical connectivity
Simulator tests show life-saving potential of new oilfield product

for early completions decisions. n associated with well control.
Invented last year by Phil Hassard, head of drilling simulation at Robert Gordon University, the technology is about to get its first outing in the field at the Weatherford Land Rig at Bridge of Don Aberdeen following successful tests on a DrillSIM:6000 drilling
Innovation Focus
E&P industry intelligence gets shake-up with launch of MapStand platform
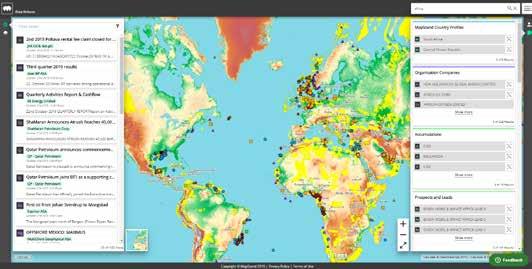
Upstream industry intelligence start-up, MapStand, has launched its disruptive go-to source to unlock essential E&P information for oil and gas professionals. The platform provides access to a free, real-time and trusted upstream industry intelligence resource. Subscribers can easily navigate comprehensive data on global E&P activities, assets and events, opening a world of project opportunities.
Enabled by powerful and geo-related simulator. Dozens of tests were carried out on the simulator replicating a huge range of well conditions from extreme to normal operations and monitoring the effects of influx flows both with and without the product.
The data test results were impressive. When Safe Influx technology was used, influx size was dramatically reduced to a safe minimum five times faster than conventional methods.
“Well control is the biggest risk in the oil and gas industry and every year we see blow search capabilities, subscribers can locate precisely the information they need on E&P projects, licenses, assets, infrastructure and planned activity as well as new exploration opportunities. Traditionally, accessing such data has involved time consuming research - often requiring specialist skills and expensive subscription commitments.
In a departure from traditional E&P industry databases, the MapStand platform will enable users to connect with peers and industry outs resulting in loss of life,” Phil Hassard, co-founder and technical director at Safe Influx, said. “Numerous studies show that up to 67 per cent of these blow outs are caused by human factors so we knew that removing these and automating well control would mitigate the risk. Although we recognised we had a potentially revolutionary product, we needed to test the concept to be sure and this is where Drilling Systems’ simulators came in.
“Using Drilling Systems’ DrillSIM:6000 we experts to share knowledge and experience. Subscribers can not only upload their profiles, but can link them to relevant projects and assets to further highlight skillsets. Geo-tagged daily news feeds keep users up to date with global E&P events, putting industry news into context on the map.
“The MapStand platform is designed specifically from the user’s viewpoint,”Francis Cram, founder and CTO of MapStand, said. “We aim to lift the barriers and frustrations involved in gaining genuinely useful insight into E&P activities, helping professionals engaging with the sector to make informed decisions and contribute to rapid innovation.”
Individual subscribers have free access to MapStand’s global activity map to search project and company information; receive live upstream oil and gas news feeds; upload their profile; and will be able to connect with other professionals. A paid professional level subscription will provide access to advanced functionality and resources.
A further fee-based subscription will enable enterprise subscribers to directly stream or download digital data layers into their own inhouse systems or to their projects, without the need for special tools or software and under
flexible data licensing terms. n were able to test how Safe Influx technology functioned in a wide range of well types and different conditions. We were thorough in our research and used widely differing variations of reservoir properties, formation pressures and mud weights. We took readings of this data and compared the results with and without using the Safe Influx system. The results were remarkable. There were huge differences with the system dramatically reducing the influx size.” n
Innovation Focus
Casing Tools develop transformational plugging and abandonment technology
Atransformational tool which could significantly reduce the cost of decommissioning is being developed by Aberdeen-based oil and gas technology company Deep Casing Tools (DCT) in collaboration with the Oil and Gas Technology Centre (OGTC) and Total.
The UK is expected to spend more than £15b on oil and gas decommissioning over next decade with the global figure for the same period estimated at £84b ($105b). Plugging and abandonment (P & A) is the complex process by which a well is closed permanently and typically accounts for about 45% of projected decommissioning costs.
Current technologies used for P & A – cut and pull; perforate and wash and, as a last resort, section milling – can create significant challenges with research revealing that around 20 per cent of all pulling operations take longer and cost more than anticipated. Early trials have shown that DCT’s Casing Cement Breaker can make these operations more predictable and reliable and can have a major impact on the length of an operation.
“Early results show that up to 90 per cent less force is required to pull a casing following a run with the Casing Cement Breaker,” David Stephenson, DCT’s chief executive, said. “One company told me

they are currently taking up to 70 days to cut and pull some casing in the Norwegian North Sea. It is too early to say how much we could reduce that by, although we hope it will ultimately be 90 per cent, but even if it were only ten per cent that would be a huge reduction given rig rates of up to £350,000 a day.”
This idea for this latest innovation came after a brainstorming session with an inventor and former colleague of Stephenson. “We started with some ideas, did some sketches and then built a small model tool to test the principle,” he said. “We built a load of samples, ran the tool, and even in those early workshop tests we reduced the force required to pull a piece of casing by 90 per cent using Casing Cement Breaker.”
DCT then built a larger workshop prototype and approached the OGTC for assistance. The OGTC canvassed members and it attracted the interest of Total who offered in-kind funding and the OGTC offered cash support.
“We now have a three-way partnership with the OGTC and Total,” Stephenson added. “The tool will be trialled early next year on wells in Total’s Alwyn and Franklin fields in the first quarter of next year, with the aim of it being fully commercial by the end of 2020.
“In the meantime, Equinor carried out a trial in the Huldra field, using the workshop prototype which confirmed the potential of what might be achieved. It reduced the force required to pull a piece of casing by about 40 per cent, which would mean a ten-day job would take six days, and that tool had really only been designed for workshop testing. We have taken the learnings from that trial, looked at how we can make it even better, addressed those issues and are now building a secondgeneration prototype. n
Innovation Focus
CGG GeoSoftware adds machine learning applications for reservoir characterisation
GeoSoftware, part of CGG’s Geoscience division, has announced that machine learning technology in Python ecosystems will be available in upcoming releases of its flagship HampsonRussell and Jason reservoir characterisation solutions. Already attracting considerable industry interest in GeoSoftware’s PowerLog petrophysical software, Python ecosystems in HampsonRussell and Jason will let experts and data scientists completely customise machine learning and reservoir characterisation workflows by using extensively available Python machine learning libraries and also their own proprietary code.
Python ecosystems allow users to efficiently research and test various state-ofthe-art machine learning workflows for proof-
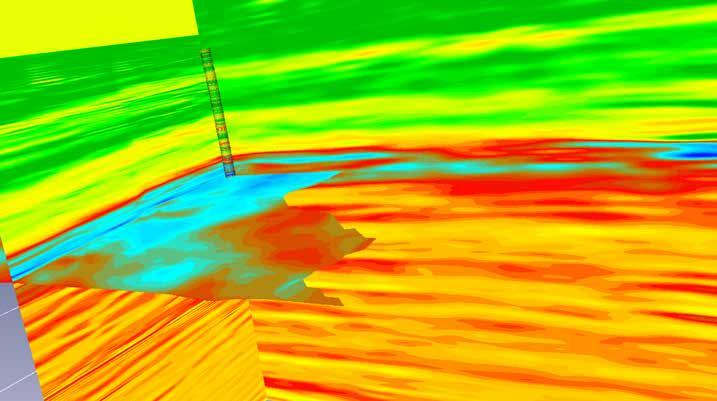
of-concept or commercial projects. Scripts and workflows directly access well, horizon and seismic data for use in machine learning, deep learning, visualization and numerical analysis. G&G experts and data scientists can use Ecosystem workflows pre-built by CGG or they can build their own new reservoir characterization workflows using the latest open source machine learning packages, such as Google’s TensorFlow.
HampsonRussell and Jason users, even those with limited expertise in machine learning or Python scripting, will now benefit from complete control over input data and analysis output. With Python ecosystems, users can process data with pre-built or client-proprietary Python scripts or Jupyter notebooks, and store input and output data in either a HampsonRussell or Jason project database or a shared directory. Python ecosystem functionality will seamlessly integrate with the application’s data stores and viewers, eliminating the need to export, reformat and reload data.
“CGG already led the market by introducing Python ecosystem technology in PowerLog,” Kamal al-Yahya, senior vice president, software and smart data solutions, said. “We are now extending its benefits to the wider community of HampsonRussell and Jason users to enable effective research and application of machine learning technologies in reservoir characterization workflows. This new capability is another example of our commitment to innovation and making new technologies accessible to the industry, for generalists and experts alike.” n
Innovation Focus
Wild Well Control has added a new 10,000 psi-rated capping stack to its Wellcontained group of subsea containment equipment. The 10,000 psi-rated (10K) stack is rated to water depths of 10,000ft, and will play a vital role in supporting quick and effective service for subsea well control events in Northern Europe. The stack’s modular design facilitates efficient deployment by crane vessel or drilling rig and regional coverage includes the following areas: North Sea; Baltic Sea; Celtic Sea; Irish Sea; Norwegian Sea; Barents Sea; and the North Atlantic waters, including Ireland and the UK.
The new stack is the third system in Wild Well’s Wellcontained program of subsea emergency response services. The 10K stack and its associated equipment package will be staged in a ready-to-deploy state from Wild Well’s Montrose facility near Aberdeen and is subject to a separate membership agreement. The full subsea well intervention systems include subsea capping stacks, debris removal shears, hardware kits for the subsea application of dispersant and inhibition fluids and other ancillary equipment.
“With the recent expansion at our quayside location at the Montrose facility, we can support both the new 10K regional stack and our global Wellcontained response capabilities,” Chris LeCompte, Wild Well’s general manager of Wellcontained, said. “The increased facility space will allow for improved efficiencies and quick mobilization for fast response from this location for our regional and global clients.” n

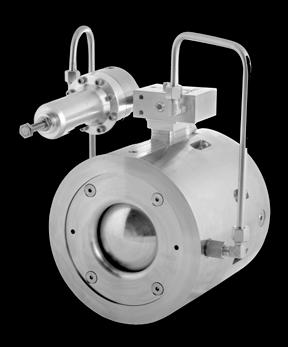
Oxford Flow has launched its IM gas regulator valve to increase reliability and reduce costs for operators in the gas distribution, power generation, industrial gases and oil and gas sectors.
The launch follows a successful ongoing trial with SGN where the valve has been installed and commissioned with ease, regulating gas pressure smoothly with rapid changing demand profiles within an accuracy class of 1.5 per cent. This accuracy the valve offers in comparison to conventional technologies enables utilities and operators to achieve faster network stability on commissioning, even where flow rates vary
Innovation Focus

Smart end position monitoring for manually operated valves
Electric actuator manufacturer Auma offers a new sensor system for signalling valve end positions which can be mounted to the company’s GS .3 part-turn gearboxes. The new solution allows plant operators to monitor the position of manually operated valves, and hence to collect crucial valve position information from all the valves in their plants – not just from motoroperated valves, which mostly use the integral limit switching functionalities of the actuators. The new sensor system adds intelligence to valves at a time when collecting and processing data from smart field devices is at the core of a rising number of significantly. In addition, the valve’s compact construction reduces weight and the need for expensive lifting equipment during installation and maintenance. In conventional valves, the diaphragm tends to be the most common failure point. Oxford Flow’s new design has eliminated the diaphragm, stem and external mechanical actuator. With only one moving part, the design minimises potential leaks and the risk of Industrial Internet of Things (IIoT) applications in process automation.
The sensor system can also be used in combination with electric valve actuators when redundant valve end position feedback is required in addition to the actuator-embedded functionality.
AUMA’s new sensor system uses inductive sensor elements which ensure contactless monitoring of the end position for 90° part-turn valves. In contrast to mechanical limit switches, AUMA’s electronic sensor system is wear-free and not subject to corrosion. It combines high fugitive emissions – maximising efficiency and reducing maintenance costs.
“This is not only a hugely exciting time for Oxford Flow, but a significant step forward for the valve industry,” Neil Poxon, CEO at Oxford Flow, said. “As many companies across the industries we serve look for ways to minimise costs, this gas regulator enables just that. Our recent valve testing and developments in the switching accuracy with robustness.
GS .3 gearboxes can be ordered with the integral sensor system as of now. Thanks to its modular design, the sensor system can also be easily retrofitted to existing GS .3 gearboxes in the field. The sensor system is available in two versions: a cost-efficient basic version and a fully-sealed premium version with aluminium housing offering enhanced IP69K protection. The premium version is particularly suitable for outdoor installation. Both versions are available with ATEX approval for use in potentially
explosive atmospheres. n UK, Germany and USA have enabled us to improve and perfect the regulator so that we can now roll the technology out to the wider industry with confidence.
“We believe this will be a pivotal moment that has a lasting impact on gas networks in the UK and beyond.” n
Innovation Focus

Trendsetter expands connector product line for 20k intervention
Trendsetter Engineering has announced that they have been awarded a contract for the design, qualification and delivery of a 20K Hydraulic Intervention Connector by HWCG.
The 20K connector is designed to interface with the HWCG 20K Capping Stack and would be utilised to conduct flowback or intervention operations after the capping stack has been installed.
“We are thrilled by this recent award from HWCG and look forward to delivering a great product,” Antony Matson, vice president of projects, said. “Trendsetter has been a market leader in developing and delivering products for HPHT applications, and this project represents yet another milestone for the Trendsetter’s subsea Connection System Product Line.”
The TC11/7 Hydraulic Intervention Connector will be the latest addition to Trendsetter’s extensive portfolio of connectors. The TC11/7 Hydraulic Intervention Connector leverages Trendsetter’s field proven hub and gasket profiles to provide 7” bore access and emergency disconnect capability for service up to 20,000psi. This order marks Trendsetter’s fifth unique connection system to be designed, qualified, and delivered to the API 17TR8 HPHT standard.
Trendsetter’s goal is to bring Innovation to Intervention by developing readily configurable, bespoke solutions. Trendsetter’s connectors have been successfully deployed and operated around the world in a variety of applications, including high pressure well intervention projects. Trendsetter offers a full range of production and intervention connectors from 2” to 16” bore, pressures up to 20,000psi, and temperatures up to 400°F. n
Innovation Focus
Weir introduces continuous duty 5000-horsepower pump
Weir Oil & Gas has introduced its SPM Quintuplex Extended Max (QEM) 5000 E-Frac Pump. This new pump is the only true continuous-duty electric or gas turbine-capable 5,000-horsepower pump in production today.
The SPM QEM 5000 E-Frac Pump builds on the proven power and durability of the SPM QEM 3000 platform, having nearly one billion field cycles with zero NPT reported. The e-frac pump delivers two worldwide firsts: a frac pump designed from the ground up for electric or gas turbine and 5,000-horsepower capacity in a single unit, rated for service at 100 per cent of rod load, 24 hours a day, even in extreme conditions.
Frac site demands have dramatically expanded in the past six years. Today, lateral lengths are 43 per cent longer, the number of stages has increased 94 per cent, sand usage is up 85 per cent and horsepower-hours per well have increased 200 per cent. These factors,

combined with operating in increasingly complex environments, pushes conventional frac fleets to their limits with longer pumping hours and less frequent service intervals to increase daily stages. This reality requires frac pumps to provide ever-increasing durability and performance, but with diesel prices at more than $3 per gallon, adding horsepower alone doesn’t fully meet operators’ needs.
The pump’s compatibility with non-standard drivers, including electric and natural gas turbines, gives operators the flexibility of tapping into the electrical grid, remote power generation or a natural gas turbine generator which reduces diesel fuel spend, emissions, overall assets on location and maintenance intervals.
The pump minimises upfront capital investment as it can reduce a frac fleet from 20 conventional pumps and 100 bores per site to just eight pumps and 40 bores per site. With only eight pumps needed to match the output of 20 conventional pumps, maintenance, noise pollution, safety hazards, emissions and overall footprint are reduced. With intentional engineering to reduce maintenance, operators can experience millions of dollars in maintenance savings per year of use and reduce maintenance personnel costs by potentially 42 per cent.
The pump achieves its horsepower with enhanced structural rigidity through an engineered skid and segmented frame plates that dramatically extend component life. It also features a dual-pressure lubrication system designed to optimise delivery and distribution of clean lubricant to provide extended life and reduced non-productive time. With a fit-for-purpose gearbox, as well as the industry’s largest bearing, the pump is capable of operating continuously at its full horsepower and higher torque applications. The high-ratio gearbox design allows for a small more efficient motor to be utilized. Furthermore, when utilising an eight-inch stroke the motor size reduction is even greater. n
2018
Professional diary
ESSENTIAL DATES FOR PROFESSIONALS WORKING IN THE OIL AND GAS SECTOR
OCTOBER
The Future of Latin America Oil & Gas Digital Transformation Summit 1st – 2nd October
Rio de Janeiro https://chameleonevents.co.uk/events/the-future-oflatin-america-oil-gas-digital-transformation-summit/
OilComm 2nd – 3rd October
Houston http://2019.oilcomm.com/
Tanzanian Oil & Gas Conference 2nd – 3rd October
Salaam, Tanzania https://www.cwctog.com/
Oil & Gas Thailand 9th – 11th October
Bangkok, thailand http://oilgasthai.com/
Kuwait Oil & Gas (KOGS) 13th – 16th October
Kuwait https://kogs-expo.com/
SPE Annual Caspian Technical Conference 16th – 18th October
Baku, Azerbajan https://www.spe.org/events/en/2019/ conference/19ctce/spe-annual-caspian-technicalconference.html
UK Onshore Oil & Gas Summit 21st – 22nd October
Birmingham https://chameleonevents.co.uk/events/the-ukonshore-gas-oil-summit/
IADC Advanced Rig Technology 2019 Conference & Exhibition 22nd – 23rd October
Amsterdam, Netherlands http://www.iadc.org/event/rig-technology-2019/
Future of Oil & Gas Canada: Digital Transformation Summit 28th – 29th October
Calgary, Canada https://chameleonevents.co.uk/events/future-of-oilgas-canada-digital-transformation-summit/
SPE Russian Petroleum Technology Conference 22nd – 24th October
Moscow, Russia https://www.spe.org/events/en/2019/ conference/19rptc/spe-russian-petroleumtechnology-conference-moscow.html
22nd International Trade Fair of Oil and Gas 22nd – 24th October
Kiev, Ukraine http://oilgas-expo.com/en/
Oil Trading & Logistics 27th – 30th October
Lagos, Nigeria https://www.otlafrica.com/about-us
121 Oil and Gas Investment 28th – 29th October
London www.weare121.com/121oilgasinvestment-london
OTC Brazil 29th – 31st October
Ro de Janeiro, Brazil OTC Brasil has been held biennially in Rio de Janeiro since 2011. The conference is organized by the Offshore Technology Conference (OTC) and Brazilian Petroleum, Gas and Biofuels Institute (IBP) and supported by 13 engineering and scientific organizations who work cooperatively to develop the technical program. http://www.otcbrasil.org/
APOGCE 2019 29th – 31st October
Bali, Indonesia https://www.spe.org/events/en/2019/ conference/19apog/asia-pacific-oil-and-gasconference-and-exhibition
NOVEMBER
Operational Excellence in Oil & Gas 4th – 6th November
Houston, Texas https://www.oilandgasiq.com/events-opexinoilandgas
Africa Oil Week 2019 4th – 8th November
Cape Town, South Africa The Summit brings together governments, national oil companies, investors, and operators, as a hub to raise capital and to take projects to final investment decisions. Africa Oil Week attracts the highest quality speakers. Over the course of the week, 200 industry leaders, including Ministers, CEOs of NOCs, Directors of Hydrocarbons, and CEOs from major and independent companies, will debate the future course of the African upstream sector. https://www.africa-oilweek.com
The Future of Petrochemical & Chemical Manufacturing Digital Transformation Summit 5th – 6th November
Manchester https://chameleonevents.co.uk/events/the-futureof-petrochemical-chemical-manufacturing-digitaltransformation-summit/
IADC Annual General Meeting 6th – 8th November
Austin, Texas http://www.iadc.org/event/2019-iadc-annual-generalmeeting/
5th Oil & Gas Africa 2019 7th – 9th November
Dar-es-Salaam, Tanzania https://www.expogr.com/tanzania/oilgas/
Oil and Gas Myanmar 2019 6th - 7th November
Myanmar http://www.oilmyanmar.com/
US-Mexico Natural Gas Forum 11th – 13th November
San Antonio, Texas http://www.usmexiconaturalgasforum.com/
ADIPEC 2019 11th – 14th November
Abu Dhabi ADIPEC brings together professionals with real buying power, with billions of dollars’ worth of business concluded at the event each year. The oil and gas industry convenes in ADIPEC to not only decide on the future of the industry, but to purchase for now, meet with existing partners and discover new business opportunities for the future. https://www.adipec.com/
Oil & Gas Vietnam 2019 13th – 15th November
Vung Tau City, Vietnam http://oilgasvietnam.com/
Algeria Oil & Gas Summit 19th – 21st November
Algiers, Algeria https://www.algeria-summit.com/
Mozambique Gas Summit & Exhibition 13th – 14th November
Maputo, Mozambique https://www.mozambique-gas-summit.com/
East Africa Oil and Gas Summit & Exhibition (EAOGS) 26th – 27th November
Nairobi. Kenya https://www.tradefairdates.com/East-Africa-Oil-andGas-Summit-Exhibition-EAOGS-M13277/Nairobi.html DECEMBER
5th International Oil and Gas Conference 2nd – 3rd December
Kuala Lumpur, Malaysia https://oil-gas.madridge.com/
Future of Middle East Africa Oil & Gas Digital Transformation Summit 3rd – 4th December
London https://chameleonevents.co.uk/events/future-middleeast-africa-oil-gas-digital-transformation-summit/
Oil & Gas Environmental Conference 3rd – 4th December
Dallas, Texas http://www.oilandgasconference.org/
8th Iraq Oil & Gas Basra Show 3rd – 5th December
Basra, Iraq www.basraoilgas.com/
7th Frankfurt Gas Forum 11th – 12th December
Frankfurt, Germany https://www.energystreamcmg.com/forums/forumsseminars/7th-frankfurt-gas-forum-2019.aspx
2020 JANUARY 2020
The 7th International Conference on Petroleum and Petrochemical Engineering 6th – 8th January
Ho Chi Minh City, Vietnam www.icppe.org/
International Petroleum Technology Conference (IPTC) 13th – 15th January
Dhahran, Saudi Arabia http://2020.iptcnet.org/
Oil & Gas IOT Summit 20th – 23rd January
Lisbon, Portugal https://www.oilandgas-iot.com/
National Biofuels Conference & Expo 21st – 24th January
San Diego https://www.biodieselconference.org/
European Gas Conference 27th – 29th January
Vienna, Austria https://www.energycouncil.com/event-events/ european-gas-conference/
LNG Bunkering Summit 28th – 30th January
Amsterdam, Netherlands https://www.oilandgasiq.com/events-lngbunkering
FEBRUARY 2020
SPE Hydraulic Fracturing Technology Conference and Exhibition 4th – 6th February
The Woodlands, Texas http://www.spe-events.org/hydraulicfracturing/ Homepage
UK CCUS and Hydrogen Decarbonisation Summit 4th – 5th February
Birmingham https://chameleonevents.co.uk/events/uk-ccus-andhydrogen-decarbonisation-summit/
Nigeria International Petroleum Summit 9th – 12th February
Abuja, Nigeria https://www.nigeriapetroleumsummit.com/
Egypt Petroleum Show (EGYPS) 11th – 13th February
Cairo, Egypt https://www.egyps.com/
Subsea Expo 11th – 13th February
Aberdeen, Scotland Subsea Expo is the world’s largest annual subsea exhibition and conference, held 11-13 February 2020 at P&J Live in Aberdeen, and also includes the industry’s prestigious awards ceremony, the Subsea UK Awards. The free-to-attend exhibition, which will see 170+ exhibitors and 6,500+ visitors, is a quality-focused event showcasing the capabilities, innovations and cutting-edge technologies of the underwater sectors. https://www.subseaexpo.com
International Petroleum Week (IPW) 25th – 27th February
London https://www.ipweek.co.uk/
Offshore Pipeline 25th – 27th February
Amsterdam https://maritime.knect365.com/offshore-pipelinetechnology/
MARCH 2020
SPE Drilling 3rd – 56th March
Galveston, Texas www.spe.org/en/events/drilling-conference/home/
CERAWeek 9th – 13th March
Houston, Texas The program of CERAWeek provides comprehensive insight into the global and regional energy future by addressing key issues—from markets and geopolitics to technology, project costs, energy and the environment, finance, operational excellence and cyber risks. https://ceraweek.com/
AUSTRALASIAN OIL AND GAS 11th – 13th March
Perth, Australia https://aogexpo.com.au/
APRIL
2nd Argentina Gas & Oil Summit 1st – 2nd April
Buenos Aires https://chameleonevents.co.uk/events/2nd-argentinagas-oil-summit/
Atyrau Oil & Gas 2020 8th – 10th April
Atyrau, Kazakhstan https://oil-gas.kz/en/
Neftegaz 2019 13th - 16th April
Moscow http://www.neftegaz-expo.ru/en/
MCEDD 21st – 23rd April
London, England http://mcedd.com/
MAY
OTC Houston 4th – 7th May
Houston http://2020.otcnet.org/
AIPN 2019 International Petroleum Summit 19th - 21st May
Bangkok, Thailand www.aipn.org
JUNE
27th International Caspian Oil & Gas Exhibition 2nd – 4th June
Baku, Azerbaijan https://caspianoilgas.az/
IIOT and Digital Solutions for Oil & Gas 3rd - 4th June
Amsterdam, Netherlands https://www.globuc.com/digitalsolutions/
EAGE 2018 8th – 11th June
Amsterdam, Netherlands http://www.eage.org
Global Petroleum Show 9th – 11th June
Calgary, Canada https://globalpetroleumshow.com/
Data Driven Drilling & Production ? June
Houston https://www.upstreamintel.com/data/
AUGUST
Machine Learning & AI for Upstream Onshore Oil & Gas 28th – 29th August
Houston http://www.machinelearning-ai-upstream-congress. com/
SEPTEMBER
KIOGE 30th September – 2nd October
Almaty, Kazakhstan https://kioge.kz/en/
All eyes on the Caribbean as replacement ratio dips to the lowest in decades
According to figures from Rystad Energy the so-called resource replacement ratio for conventional resources now stands around 16%, meaning that only one barrel out of every six consumed is being replaced by new sources.
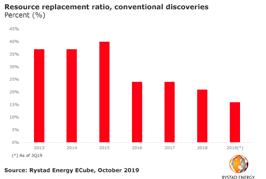

Oil and gas companies have discovered 7.7 billion barrels of oil equivalent (boe) year-to-date, according to Rystad Energy’s latest global discoveries report.
“The industry is well on track to repeat the feat achieved in 2018 when around 10 billion boe of recoverable resources were discovered,” Palzor Shenga, senior analyst on Rystad Energy’s upstream team, said.
Russia has seen the most discovered resources thus far in 2019, with the Dinkov and Nyarmeyskoye discovery announced earlier this year holding around 1.5 billion boe of recoverable resources. Guyana and Cyprus nab the other places on the podium.
The so-called resource replacement ratio for conventional resources now stands around 16%, which is the lowest seen in recent history. “This means that only one barrel out of every six consumed is being replaced by new sources. This is the lowest replacement ratio we have witnessed in the last two decades,” Shenga added.
However, the industry has high hopes after the prolific success of ExxonMobil’s Stabroek block off the coast of Guyana and more recent discoveries by other operators in the region, which have led to a surge in offshore exploration in the Caribbean. More acreage is being made available for bidding, with some countries conducting their first-ever licensing rounds in 2019 and 2020.
Offshore drilling activity has been on a steady rise in recent years, with 23 new exploration wells expected in 2019. By comparison, only seven offshore wells were drilled in 2013.
“We estimate the annual number of wells drilled could increase slightly to 25 wells in 2020, as more operators join the Caribbean exploration circuit,” says Santosh Kumar, an exploration analyst on the upstream team.
Rystad Energy expects the GuyanaSuriname basin will continue to occupy headlines with a few planned wells in both Guyana and Suriname. The basin is pinned as one of the most prospective, underexplored basins in the world and will definitely get a facelift from its current assigned volumes if hydrocarbons are established towards the east.
“Explorers have set their sights on establishing a working petroleum system and unlocking the underlying commercial prospectively of the basin. The latest update suggests that the basin could have a potential of around 13 billion boe,” Shenga said.
A wildcat exploration campaign led by Apache is currently underway in Guyana’s eastern neighbour, Suriname. Prior to this only 14 wells have been drilled in the GuyanaSuriname basin beyond water depths greater than 20 meters. n
