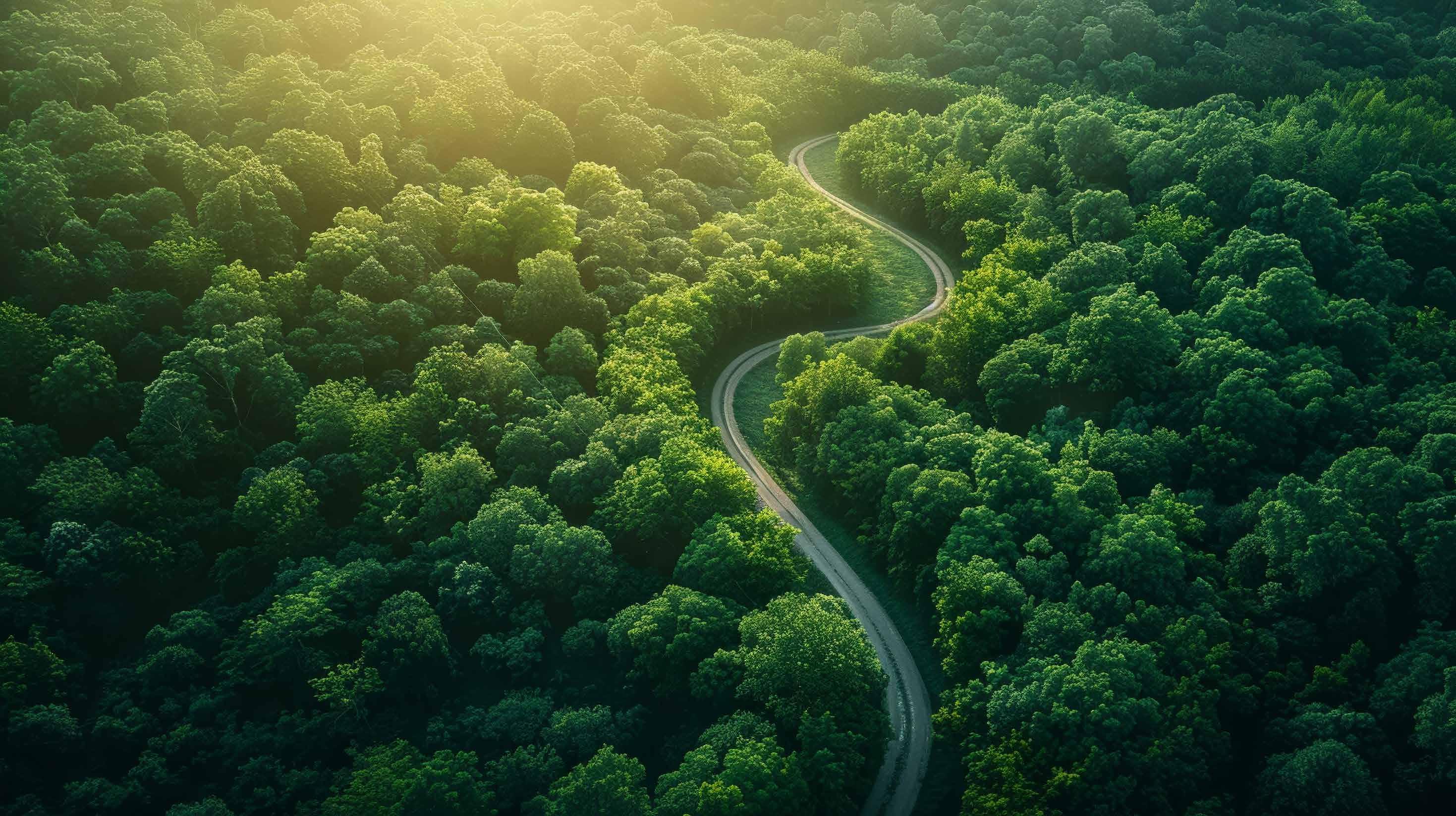

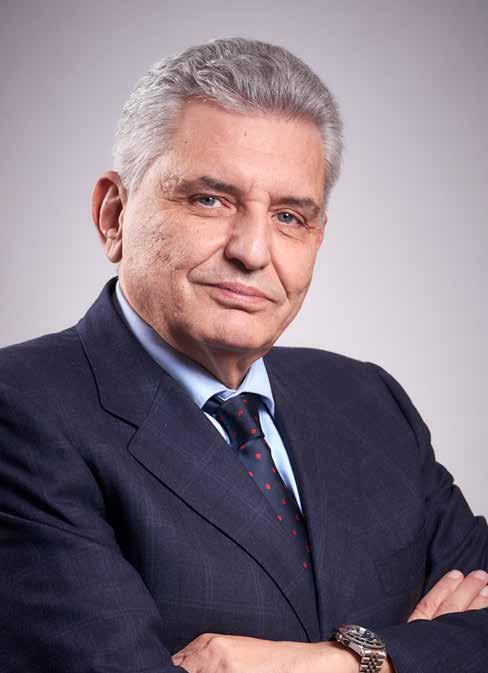
Prima Sole Components S.p.A. seventh sustainability report is affected by the actual period of uncertainty that affects all the automotive market (representing one the markets with the strongest impact on the products supplied by the companies of our group), which despite being expanding it is however affected by important changes due to the ecological transition policy that in the coming years will impose a reorganization of the market balance, with the probable acquisition of ever - increasing market shares by players from the East.
In addition to this instability, the growth in financial interest rates has reached peaks that we have not been accustomed to for decades.
All the above is included in a scenario of political tensions with war conflicts (the Israeli-Palestinian conflict, in addition to the Russia-Ukraine crisis) that have influenced the stability of the markets, especially in the early phase of Uktraine-Russia conflict, where we have experienced high volatility in the prices of raw materials, crude and fuel gas, which reached increases to record levels.
Although year 2023 has been characterized by downward rebalancing trend of raw material costs, their values did not reach the pre-crisis ones, instead stabilizing at much higher levels.
Added to this, there is the need to modernize our production processes to meet the challenges both on the decarbonisation requirements (particularly in UE, according to the Green Deal policy which sets obligations and objects for the next decades) and also in the use of artificial intelligence.
In this context we have started a process aimed at the detailed assessment of the impact of our processes with respect to the carbon footprint and the definition of a decarbonisation plan in order to achieve the objectives of reducing our GHG emissions and so also the carbon footprint of our customers.
We have also started studying how AI can optimize our production processes and improve the quality of the products our organization supply.
Plants and their organizations in BU, with their acronyms
Quality and competitiveness, but with respect for people and the environment: this is what we work for every day, by dedicating all our energy.
Prima Sole Components (PSC- Stock Company) is a Group operating since 1973 in the field of automotive plastic components, motor vehicles and household appliances. It designs, manufactures and sells innovative and sustainable products, whose goal is to live up to its customers’ expectations on a regular basis. An ambitious goal, pursued thanks to a long-term and flexible partnership, where competitiveness, quality and service achieve high standards, alongside staff work daily operating with motivation and efficiency, as well as constant research of innovative and integrated solutions.
PSC Group wants to become a global player in the Automotive & Tractor department, while continuing to oversee the supplies on the regional markets for the Appliances, Motorbike & Electric fields; it also aims to confirm itself as a reliable and efficient supplier for its customers in Europe, Brazil, the United States and the Far East.
PSC Group believes that also in the near future, market competition will be based on three fundamental variables:
Competitiveness;
Innovation;
Globalization;
In 2023, the PSC Academy&Research has been founded with the aim to provide support to all companies of the PSC Group in the promotion, coordination and implementation activities of research and project
development in the fields of human resources, training, sustainable development and circular economy.
In addition to this, in order to become a partner of the most prestigious customers, it is also important to achieve specific economic standards. For this reason and to maintain a high degree of competitiveness, in 2018 PSC introduced COBOT: collaborative robots expression of 4.0 industry, useful in those production processes, including assembly and polishing, where the human-machine interface is particularly rewarding.
It is the Group›s intention to consolidate the relationship of trust with all stakeholders and to pursue its objectives, by harmonizing the interests of each actor involved in compliance with the provisions of the law and the principles of impartiality, reliability, loyalty, fairness and transparency.
It is in this context that the objective of a shared prosperity is included, by extending the well-being generated through PSC activities to the territory.
The Group›s mission is structured on three aspects that are inseparably linked to each other:
• Economic. The management of the Group is characterized by the creation of value for the shareholders, in compliance with stringent parameters of economic and financial sustainability.
• Production and market. PSC designs, manufactures and markets advanced products from a technological point of view, capable of completely satisfying customer expectations.
• Social. PSC Group is aware of the centrality of its social role. Attentive to the local, national and international community, it is committed to improving the quality of life of all stakeholders, with the utmost respect for the environment.
The Group has identified some values that guide the effort of each worker, either when acting individually or when participating in collective initiatives:
▷ Always act with honesty and moral integrity
▷ Be critical of yourself and ask yourself how to improve yourself
▷ Be respectful of the organization, enhancing meritocracy
▷ Focus on growth and its long-term sustainability
▷ Pay attention to safety and the environment
▷ Be respectful towards customers
The annual publication of the Sustainability Report leads to the consolidation of such values and confirms the attention to the most upto-date national and international regulations, already firmly at the basis of PSC’s work practices.
Among the values that guide the Group’s activities, two in particular play a prominent role: respect for the person and for the planet that hosts us.
For this reason, the Code of Ethics - updated in 2020 and disseminated in 2021 in all the Group’s business units - makes explicit the support and respect for human rights, in accordance with the UN Universal Declaration. The organization and management model, in compliance with decreelaw 231, was also the subject of an update process in 2020.
Furthermore, over the period 2021-2023 the D.Lgs 231/2001 criteria and obligations has been implemented in all Italian PSC sites, following a step-by-step approach, starting from the PCIT business unit and then following in the SOCO; at the same time, other audits were planned by the SB in the various areas of the organisation.
The Organisational Model and the Code of Ethics, together with the appointment of the Supervisory Board (SB), are also the tools by which we ensure the prevention and mitigation of possible conflicts of interest.
In both documents, new contents were introduced, developed on the basis of the path taken by PSC towards greater sustainability of its activities
1973
PRIMA S.p.A. starts furniture accessories production.
CABLINF PRIMA is founded, active in the wiring market for Automotive.
PRIMA S.p.A. enters the field of appliances with the creation of the P.A.D. and the acquisition of ALMEC S.p.A., active in the automotive sector.
PRIMA S.p.A. acquires COLLINS & AIKMAN ITALY and its four production plants.
PSMM Pernabuco was established as a joint venture with MAGNETI MARELLI for the production of automotive plastic components based in Pernabuco (Brazil).
The production of foamed components for the automotive, aeronautic and railway sectors begins. 1980-86
PRIMA EASTERN was established in Torino of Sangro, meant to manufacture plastic products, mainly for the FVC SEVEL plant .
PRIMA S.p.A. opens its first factory abroad, PRIMA France sas.
With the sale of ALMEC S.p.A., PRIMA S.p.A. abandons the die-casting sector.
PSMM Campania A new plant was inaugurated in Gricignano d'Aversa, in partnership with MAGNETI MARELLI.
1987
PRIMA S.p.A. becomes a FIAT supplier for plastic components designed for the outside of cars.
SAPCA company was established in Modugno.
The ERIPRESS companies of Cicerale and SHANDRANI ITALY are acquired with a new name (I.VER.PLAST).
PRIMA S.p.A. acquires PLASTAL ITALIA, then SOLE S.p.A. and holdings in FINALLOY (companies (aluminum sector), OPTIMARES (aircra seats).
PSC through TWICE PS, rents a company branch o SGI,a company with plants in Italy, Austria, England, Germany and Brazil, entering the thermosetting sector.
1989
The first design and industrialization center of PRIMA S.p.A. and PRIMA I.VER, a company for painting plastic materials, was established
PRIMA S.p.A. takes over from PIAGGIO in METALPLASTI
COMPANY. In the same year, a er TECNOPRODUCT acquisition, TECNOPRIMA. was established. With the sale of CABLING PRIMA and SAPCA, PRIMA S.p.A. comes out of the wiring sector.
PRIMA S.p.A. inaugurates two production sites abroad: PRIMA GERMANY GmbH and PRIMA POPRAD sro (Slovakia), first active in the household appliances sector as well as automotive a erwards.
The internal reorganization is completed with the integration of PRIMA S.p.A. and SOLE S.p.A. as operating structures PRIMA SOLE COMPONENTS S.p.A. was established.
PSC acquires 99% ofPSMM Campania in partnership with MAGNETI MARELLI.
2020
PSC acquired the plant of Paliano by PCMA which assumed the name of Prima Components Paliano PSC acquires from PCMA the two Polish sites of Sosnowiec which take the name of Prima Sosnowiec Advanced Plastic Technologies (APT) and Prima Sosnowiec Complex Plastic Systems (CPS), and from the BATZ Group two Brazilian sites now identified as PSC Automotivos SJP e PINDA I.
PSC Automotivos acquired the PINDA II plant and started the necessary activities for its operation. The activities near the Brazilian plant of PINDA II enter to full capacity.
2023
The PSC Academy&Research, a no profit unit that develops projects for the industry, training and sustainable development, becomes operational.
PSC is a member of two prestigious trade associations:
Confindustria, the main representative organization of Italian manufacturing companies, of which Maurizio Stirpe, PSC President, is national vice president with responsibility for Labor and Industrial Relations. PSC is actively involved in several projects of the association.
Assonime, the association of Italian joint-stock companies that analyzes and addresses the prospects, developments, and criticalities of the Italian economy.
Prima Sole Components is a single member stock company, 100% owned by BS Holding, whose administrative centre and registered office are located in Torrice, in the province of Frosinone.
The government structure provides for a three-year Board of Directors (BoD) of five members. The Chairman and the Chief Executive Officer have powers of ordinary and extraordinary administration with disjoint signature.
The definition of business strategies, including economic, environmental and social issues, is one of the BoD’s competences: by monthly monitoring, through the central and individual business unit committees, and without prejudice to the responsibilities delegated to the corporate officers, the President exercises control over all activities of the company, including those related to sustainable development.
Site managers are delegated by the directors of the individual companies to ensure compliance with mandatory environmental and social standards.
The enhancement and dissemination of sustainability skills within the Group is ensured by the training plans implemented by the PSC Academy.
The CEO annually reviews the Group’s Strategic Plan, which also contains the sustainability priorities. He also reviews the contents of the Sustainability Report prior to its publication, and validates the update of the material issues identified, which are listed in Chapter 2.
The President is also a major shareholder and holds no other corporate office; therefore, there are no potential conflicts of interest in the performance of his duties.
The members of the governing body are appointed according to strategic assessments and decisions made by the Chairman and the CEO, based on the specific skills of the candidates and their ability to manage business impacts, risks and opportunities. Instead, the performance of the BoD is assessed through the monthly reporting of profit and loss accounts. To date, there are no formal procedures for managing the remuneration of the highest governing body.
5 members
Holder of management and responsibilities powers. It defines general strategic objectives and directions. It analyzes industrial and financial strategic plans.
It defines strategic guidelines in the economic, environmental and social fields.
Board of Directors
President and CEO manage ordinary and extraordinary administration, along with separate signature power. There are no subjects, except those concerning the law, transferred to the board and / or members.
Board of Statutory Auditors
Price Waterhouse Accounting control and financial statements report of the consolidated balance sheet.
3 members
Legality check:
- respect for the law and statute. - respect for the principles of correct administration, defining the nomination of auditing company.
It manages the activities, according to the objectives approved by the BoD and proposed by the AD.
The central and individual business unit committees develop action plans aimed at managing and resolving any critical issues encountered. The Supervisory Board also carries out control activities on the correct application of the 231 Organisational Model and communicates, during periodic audits, any critical issues found, also on the basis of the reports received. No critical issues were reported in the reporting year.
The companies covered by this Sustainability Report are reported in the
following diagram matching those that depend on PSC do Brazil, Sole Components, Prima Components Italia, Prima Components Europe (in 2020 called Prima East Europe Components) holding companies.
In 2023, the main change in the overall organization of the Group has been the rise of a new non-production site, the PSC Academy&Research. Based in Anagni, this new unit consist of one director and a single employee
Prima Eastern SpA
PSC plants, object of this report are present in five countries: Italy, Germany, Slovak Republic, Poland, and Brazil. Prima Poprad Sro Prima Sosnowiec CPS Prima Sosnowiec APT
Prima Components Anagni
Prima Components Ferentino
Prima Components Paliano
Prima Components Gricignano d’Aversa
Manufacturing processes concerning PSC are numerous and include many different tipologies. Such processes, divided into five categories, are listed below:
Traditional injection moulding
Bi-injection
Gas-injection
Multi-material 2K and 3K injection
Injection with fabric
Insert Moulding Decoration In-mould metal bonding Technologies for Thermosettings resins SMC (Sheet Moulding Compound)
Traditional Chrome Plating
Colored chrome
Selective chrome
Paint on chrome
In mold laser etching Carbon fiber Tampography
PVD technology covering Decorated Aluminum Painting/finishing
Robotized Painting Lines from 1 layer to body color, water and solvent Cubik Evo
Automatic gluing
US welding, Hp, Vibration
Thermoforming
PU Sphuell sealing
Complex automatic assembly
Foam for shock absorber
The products of the Group are also addressed - in different amounts - to many other fields, as shown in the following picture.
PSC products are present on the Italian, European and world market, intended for the main OEMs motor vehicle manufacturers: Stellantis, CNH, Volkswagen, Volvo, Fiasa, Daimler and BMW. In its own market
penetration policies, PSC is developing partnerships with the main OEMs also through the production site localization of its customers’ plants.
The distribution of customers, in terms of turnover, is listed in the following graph.
The geographical distribution of turnover from the sale of products and services in the last three years is as
Independent external check
With the annual drafting of this report, PSC communicates to its stakeholders the policies, commitments and strategies it applies in the field of sustainability. This document, annually updated, was prepared following the latest version of the Sustainability Reporting Standards published by the Global Reporting Initiative (GRI).
The principles followed to ensure the quality of the information and its correct presentation are:
■ Accuracy
■ Balance
■ Clarity
■ Comparability
■ Completeness
■ Sustainability context
■ Timeliness
■ Verifiability
The body of the text contains all the data related to the Group and to the three-year reporting period 2021, 2022 and 2023, in order to allow performance trends monitoring.
Appendix 1 shows the data of individual plants, reported in 2023 The Sustainability Report, which refers to the calendar year 2023 and updates the data published in previous report (July 2023), includes all companies of Prima Sole Components (stock company) Group, except for PSC Gestione Partecipazioni, since this latter is excluded from the consolidated financial statements.
The body of the text contains all the data related to the Group and to the three-year reporting period 2021, 2022 and 2023, in order to allow performance trends monitoring.
Appendix 1 shows data of individual plants, reported in 2023.
The analysis of materiality is the main reference established by the GRI standards for drawing up the Sustainability Reports. Materiality refers to the threshold when issues become important enough to be reported, since they influence the organization and its stakeholders in decision making, along with actions and performance.
In order to arrive at the identification of the material topics, it is essential to initially study one’s own reality, the context in which it operates and the competition it faces, and identify the priority sustainability issues.
This activity has been carried out for the first time in 2018 and it is updated periodically.In order to be in compliance with last updated standards of reporting, in the 2023 Report (the current one) any impacts that the organization produces towards the outside have been identified and assessed, and on the basis of the results of this assessment there have been identified the following material themes for three areas of sustainability: Economic, Social and Environmental (ESG).
The process has been re-evaluated and validated before issuing the present report.
Below, you can see the list of material topics (ordered by ESG field) and their relevant description.
Risk management
Research, development and technological innovation
Operate according to risks and opportunities in the economic, social and environmental field, for PSC operability and image.
Research and technological innovation as strategic factors to increase our products competitiveness, in line with a sustainable development and mobility
Relationships with customers (business partner)
Relate to our customers, in the role of main business partners, acknowledging value to cooperation, synergies and social responsible behavior, in order to achieve higher levels of knowledge and greater quality and to build a lasting relationship with mutual satisfaction.
Guarantee compliance with mandatory or voluntary regulations through the employees endorsement and thanks to appropriate organizational and management models, as well as to achieve performance and sustainable targets, which can be assessed and certified Compliance
Responsible management of the supply chain
Involvement of the supply chain by sharing the principles, policies and tools for the sustainability and social responsibility.
Local communities
Attention and comparison with the local community expectations, through an open, transparent and constructive dialogue.
Health and
Equal opportunities and diversity
Consider employees as a fundamental element of the company's value, and guarantee their well-being through some training appropriate for the development of individual skills, an organization and environment that will foster our commitment for quality along with personal and professional satisfaction chievement.
Guarantee processes safety and workers’ health protection throughout all procurement and production stages.
Enhance personal and cultural diversities of partners, suppliers and customers, avoiding discrimination and facilitating aggregation.
Energy
Responsible use of energy resources achieved, when possible, by technologies and energy saving activities along with renewable resources option. Emissions in the atmosphere
Carry out operations, by taking the opportunities to prevent and mitigate emissions in the atmosphere, by protecting air quality and contrasting climate change.
Apply, when possible, the most e ective practices for reduction, through prevention, and waste recycling.
Responsible use of water thanks to technologies and policy aimed at reducing its quality, when taking it, and preserving the original quality.
The identified impacts are reported in the Material Topics Management section on page 99.
The GRI disclosures reported in this document have been selected on the basis of the most relevant impacts identified during the materiality analysis.
The materiality analysis of the previous report (related to year 2022) had identified an impact due to the use of nonrenewable raw materials; nevertheless, the context analysis updated to 2023 has not highlighted any significant relevance with respect to this impact.
Principles
Analysis
Stakeholder
Independent
Although the definition of material issues has been revised, in line with the updated GRI standards, to focus on impact, the engagement of relevant stakeholders continues to be part of the process of identifying and assessing corporate priorities. This took shape through stakeholder engagement, a two-stage process:
■ Identification of different categories of stakeholders. This phase was carried out following the AA1000 Stakeholder Engagement standard (AA1000SES) 2015 and led to the identification of the categories in the following table, each accompanied by its description.
Employees working for or on behalf of PSC, including its representatives (e.g. trade unions)
Provider of products or services to PSC
Customers of PSC products
Who holds shares within PSC
The social context in which PSC sites are located. It can influence its activities
The set of institutions that can influence the PSC activities (e.g. Region, Province or Municipality in which PSC sites are located)
Non-profit associations and private organizations operating in areas that influence PSC activities (e.g. environmental associations or sector associations)
International, national and local media (e.g. television, press, radio and web) which PSC can use to communicate its initiatives
Stakeholder
■ Definition of the methods for implementing engagement. In 2023, we opted for an indirect method of involving all stakeholders. The documentation useful for reconstructing the opinions and requests on the material topics has been selected and analysed.
Below it is shown the list of material topics ordered according to the priority assigned by the company management, together with the relevant score (as more or less interest) assigned by the stakeholders.
Waste management
Energy consumption
Occupational Health and safety
Research, development and innovation
Relationships with customers (business partner)
Well-being of employees
Compliance
Risk management
Local
Responsible
Our group attaches importance to Waste Management and Energy Consumption, as demonstrated by the high scores obtained in our impact assessments. We are committed to reducing our environmental impact and optimizing the use of resources through sustainable practices.
Occupational Health & Safety are fundamental pillars for our activities, and we are committed to ensuring a safe working environment and minimizing risks for our employees.
We also recognize the importance of Research, Development and Innovation, aware that our sector is constantly evolving. Our leadership in the sector depends on our ability to invest in new ideas and technologies, developing efficient and low environmental impact solutions that respond to market needs.
We believe that it is essential to establish and maintain solid and longlasting Relationships with customers and business partners, and that investing in the Well-being and development of employees is crucial to creating a positive and stimulating working environment.
We ensure Compliance with regulations and Manage risks to identify and mitigate potential threats and vulnerabilities, to ensure the continuity of operations and the safety of our activities We actively collaborate with Local communities and promote Responsible supply chain management, ensuring that our partners and suppliers respect the same ethical and sustainable standards that we are committed to following.
We believe that the protection of Water resources, Atmospheric emissions and Equal opportunities and diversity are relevant issues, and we are committed to managing these areas responsibly to promote environmental sustainability and social inclusion.
On their side, stakeholders confirm the importance of prudent management of Energy consumption, a topic that has taken on growing importance in recent years, also due to the persistence of international conflicts. Furthermore, they attribute great importance to the topic of Research, development and innovation, aware of the crucial role it plays in addressing emerging challenges and ensuring future company competitiveness.
There is also agreement in attributing medium importance to the themes of Employee well-being and Responsible management of the supply chain. This reflection of convergence reflects a common commitment to respecting the people involved both within business processes and along the entire value chain.
Eventually, stakeholders also agree in attributing less importance to the issue of equal opportunities and diversity, however highlighting the need for further reflection and action to guarantee a more robust commitment in this area.
1 About us
and
Innovazione tecnologica:
Interessa fra le altre cose prodotti e processi, nell’intento di elevarne qualità, prestazioni e flessibilità, nonché di ridurne i costi.
Globalizzazione:
Distribuzione dell’attività scala locale e globale esigenze dei clienti.
Compliances and certifications
Responsible management of the supply chain
Relations with local communities
The Group’s vision, mission and medium- and long-term strategies are detailed in the business plan. Once the guidelines have been identified, the operational plans of the individual business units and the connected production sites are defined.
PSC management formalises functional analyses and assessments in the drafting of the operational plan with an interdisciplinary approach; For this reason, various business functions are involved in the process and external stakeholders of particular interest, including some customers and suppliers, are also taken into account.
The strategic guidelines of the business plan are:
the Group’s ability to supply competitive products and to stay in the market, facing competition.
Technological innovation:
it concerns, among other things, products and processes, with the aim of raising their quality, performance and flexibility, as well as reducing costs.
distribution of production on a local and global scale, according to customer’s needs.
Research,
Responsible
The business unit administrator identifies the activities consistent with PSC strategic guidelines by following the process described below:
• Analysis of PSC business plan: each business unit verifies the applicability of the strategic lines established at Group level to its own peculiarities.
• Identification of relevant factors thanks to the S.W.O.T. analysis (Strenghts, Weaknesses, Opportunities, Threats): a step that allows you to detail the strengths and weaknesses of the internal context, as well as external risks and opportunities. These elements are then related to stakeholders.
• Assessment of the significance of the factors identified: a risk factor is identified according to a matrix that evaluates the probability of occurrence and the impact that would have on market share, competitive advantage and reputation.
• Definition of the operational plan, by taking into account the risks involved, and in particular:
• avoid the risk by deciding not to start or continue the activity that led to its appearance
• take or increase risk to pursue an opportunity
• remove the risk source
• change the probability of the risk occurring
• change the consequences
• share the risk with a partner (also through contractual formulas for financial risk control).
The actions to cope with risks and exploit opportunities, with regard to sustainability, are the necessary inputs to carry out the operational plan in line with the company’s strategy.
The Group has also taken out policies with important companies in this department, in order to cover the main corporate risks related to industrial activities. This is a comprehensive insurance covering all material damage to buildings, plant, machinery and goods owned by the Group’s companies, whether they are present in PSC plants or as at third Parties.
Factors such as atmospheric events, criminal acts by third Parties, structural collapses, fluid leakage and mechanical failures may affect thresholds and specific allowances. Any economic losses resulting from business interruptions or factors such as those listed above are also covered by insurance. Finally, possible damages to third Parties resulting from claims covered by the policy (third Party claim and interruption or suspension of its activities) have been insured.
Group companies have taken out a policy consisting of three sections relating to indemnity obligations. In detail: third party liability, workers liability1 and product liability. Each of these covers operates with limited ceilings and deductibles.
A careful and correct management of corporate risks has contributed to making PSC a Group that creates value and wealth, by spreading part of it to its stakeholders.
1 Technical term used in the insurance industry to refer to all employees of the company
Economic value generated by
Revenues and other operating incomes
Economic value distribuited by PSC
Operating costs, remuneration of collaborators, remuneration of lenders, remuneration of the public administration and investments for the community
Economic value retained da PSC
Economic value generatedEconomic value distribuited
The economic values (generated, distributed and retained ) refer to the consolidated data of the companies included in the consolidated balance sheet of PSC.
The plants of Sole Hoergertshausen, Sole Wörth, Prima Sole Components Pinda I, Pinda II and Automotivos are not included in the reporting of
economic values because, at the end of December 2023, they had been transferred to CPM Holding S.r.l., which belongs to Stirpe family itself.
Hence, this transfer excludes the above mentioned entities from PSC consolidated balance sheet, although they are within the family group.
PSC’s five research and development (R&D) centres are located in Oderzo, Scanzorosciate, Turin and Ferentino and employ a total of 67 employees and 14 program manager. In 2023, the new PSC Academy&Research company will be added to this portfolio: a unit dedicated to developing projects related to innovation and sustainability through the management of research and development projects, In addition to the vocational training of our employees. This confirms the strategic importance of continuous progress for the Group and for this reason it is reserved for significant investments, sometimes in synergy with customers.
There is a Director in charge of this area who, in collaboration with the Program management coordinates three divisions:
■ Foreign customers ■ talian customers ■ Appliances
In order to identify and share best practices on this matter throughout the Group, PSC has equipped itself with a cutting-edge business intelligence platform.
R&D initiatives implemented by companies and business units are plenty and mixed practice.
Study and screening in the laboratory of possible options for new molding, materials, devices for TCS and their compatibility.
At the end of 2023, Sole Oderzo finalized the development of the “Sustainable Capacitive Keyboards (TCS)” project, a long-term research project financed by Sustainable Growth Fund (FCS), established by government to support businesses and investments in this sector.
The project has the aim to develop keyboards whose functions can be activated with a simple touch, similar to those used on smartphone screens. These are made using advanced super-thin over-injection plastic molding processes.
This technology allows to provide plastic components with integrated electronic circuits as a thin film, which can be adhesive-coated and/ or over-injected onto the components This integration provides new functionality, increases efficiency and reduces the use of microswitches and electrical cables, allowing the transition from traditional plastic surfaces to “smart surfaces”, i.e. intelligent surfaces equipped with interactive sensors.
The TCS project has been developed in three phases:
Development of two prototypes: one for the dashboard with color-changing backlighting and one for the rear lid opening handle. This phase ended in 2021, with the development of three prototypes, two for the internal coatings and one for the handle.
03
Full development of the technology, expected in the course of 2022/2023
Risk management
During the first reporting on the financed project, the inspector confirmed that the project was alined with the planned objectives.
• Technical-economic feasibility study on the use of Nitrogen gas as a medium carrier fluid in the painting of our main products;
3 Generated value 2 Materiality and methodology 4 Workers 5 Natural resources & environment
Research, development & technological innovation Relations with business partners and quality of products
Compliances and certifications
Responsible management of the supply chain Relations with local communities
At the end of the project, the final report has been presented and transmitted to the Ministry, and the company is now awaiting for the final evaluation visit.
We are currently carrying out further assessments and tests, even after the conclusion of the project, with the aim of developing a package of technical applications that are commercially attractive for the market.
During 2023, Sole Oderzo has been also involved in the realization of other R&D projects, for which it accrued the tax credit provided for by Legislative Decree no. 145/2013.
The involved initiatives have been the following:
• Study for the application of in-mold painting technology for our core products to evaluate green solutions economically efficient;
InMold3D3K Project:
GreenSetAut Project: GreenPriPal Project:
Productive Investments: Artificial Intelligence and Data Science Project:
• Development and application of new polypropylene materials without using primers and plasma for bioadhesive applications
A fundamental role has been also taken-on by the new unit of PSC Academy&Research, which since the very first months of activity has carried out scouting, analysis and planning and partner research activities on various financial instruments applicable to the Automotive sector. The objective of the operations have been those ones to prepare the presentation of the following projects for next year:
Initiative dedicated to industrial processes, with a particular focus on the development of new 3D-3K in-mold painting systems. This project is fundable under the EU Horizon 2021-2027 program.
Initiative focused on the development of ecological composite materials for the automotive sector. This project is fundable under the MiCS Circular Economy Spoke 4 Call of the National Recovery and Resilience Plan (PNRR).
Project for the development of an ecological pallet as a sustainable, economic and highly e icient solution for logistics and goods management. This project is fundable under the Horizon Europe 2021-2027 program.
Specific investments in production processes, with particular attention to the production of moldings and stubs, fundable through the ZES UNICA Tax Credit (DL 124/2023).
Initiative aimed at developing advanced technologies in the field of artificial intelligence and data science, fundable through the iNEST Ecosystems of Innovation Spoke 3 Call of the National Recovery and Resilience Plan (PNRR).
At the same time, PSC Academy&Research highlighted to the Group new Investment Opportunities, such as the National Military Research Plan PNRM 2024 and proposed international cooperation projects within the Erasmus Program with Istituto Tecnico Meccatronico del Lazio.
During 2023, many companies of the PSC Group requested and obtained financial assistance for a total of 19,304,149 euros.
The Group has benefited from tax reliefs and tax credits for an overall amount of 17,932,115 euros, representing almost 93% of the total financial support received.
The company that has benefited the most from this form of financial
assistance has been PSMM Pernambuco, with over 12 millions euros in tax reliefs and tax credits.
Prima Components Anagni has received 41% of the Group’s total subsidies, for a value of 67,700 euros, while Prima Eastern, with a total of 375,256 euros, has been the company that has benefited the most from investment grants, research and development grants and other types of relevant concessions.
Sole Oderzo is the only company that has benefited from financial incentives, for a total of 712,547 euros.
Risk management
Research, development & technological innovation
Relations with business partners and quality of products
Compliances and certifications
Responsible management of the supply chain
Relations with local communities
Solid: this is the adjective that best describes the relationships that PSC establishes with its customers. Indeed, it is no coincidence that several sites of the Group’s production are located in the same areas that host commercial partners of reference for PSC: Sole Suzzara is located in an IVECO district, Sole Pontedera is located in a Piaggio district, and a 50% joint venture with Magneti Marelli involves the Brazilian plant in Pernambuco.
For PSC, satisfying a customer means mainly to provide quality products and services that meet or exceed expectations. The Group’s plants are often renewed or, in any case, are subjected to constant maintenance; in addition to this, state-ofthe-art control systems have been set up which contribute to the monitoring and repeatability of processes, and to the increase in the quality of products. Statistical studies on the main variables make it possible to monitor any situations that are out of control, as well as to intervene promptly in the event of a possible recovery.
Following the precautionary approach, PSC evaluates the impact of each new product during its development. Failure Mode and Effect Analysis (FMEA) allows you to evaluate defects or problems that impact on product elements relevant to the customer, such as functionality, aesthetics and assembly, thanks to an assessment of the risk priority index, on the basis of three levels: severity, probability and detectability. The same methodology allows us to quantify the impact of products on environmental and safety aspects.
The products arriving on the market are registered in the International Material Data System (IMDS), a constantly updated platform in which all the materials used for the manufacture of cars are collected, updated, analyzed and archived. Thanks to IMDS it is possible to fulfill the obligations imposed on car manufacturers and their suppliers, complying with standards, laws and regulations in force at national and international level.
All substances and mixtures used in production by the factories are accompanied by Safety Data Sheets (SDS) with information on physicchemical, toxicological and environmental hazard properties, necessary for correct and safe handling.
Product safety and compliance with legal requirements are assessed in the FMEA by adopting the most stringent parameters. In the reporting period, no cases of non-compliance with regulations and / or voluntary codes were notified to PSC regarding the impact on the health and safety of its products and services.
PSC regularly monitors customer satisfaction with the supplied product. A process made agile also by online platforms, widespread in the automotive sector, in which reports of various types are reported in real time, including complaints and rejects, and on which assessments are carried out on a monthly basis that take into account the quality of products and services.
Information about the correct approach to environmental and social sustainability of single plans is periodically provided to customers by means of self assessments (in forms of questionnaires), such as NQC SelfAssessment-Questionnaire (SAQ), CDP and Ecovadis, on which in 2023 we obtained
of 56 out of 100.
Each production site manages any customer complaints at an operational level. The monitoring and timely review of the assessments received from customers, on the other hand, are the subject of the management committees of the business units and of the Group.
In the reporting year, no Group company was affected by legal actions in the areas of anti-competitive behavior, anti-trust and monopoly practice. Particular emphasis has been given to such aspects in the new code of ethics and conduct.
Partnership relationships with suppliers are also traditionally very strong. PSC’s strategic purchasing department signs framework agreements with large groups that produce, for example, raw materials and paints, and supports the growth of suppliers in the areas of its sites, supporting them with its own structure to achieve the highest environmental and safety standards.
Group companies strictly comply with the laws and regulations in force in the countries in which they operate. The managing directors of the business units are responsible for compliance with mandatory legislation also through their delegates (plant managers or external professionals) on all the specific issues concerned.
All the companies and production sites belonging to PCIT BU have implemented an organization and management model in accordance with Decree-Law 231/2001 aimed at preventing the commission of crimes that may involve the Company’s liability, including any risks related to corruption. In 2023, this model is therefore operational in 12 out of 18 companies.
The management and all staff received training in relation to the contents of the Organisational Model and audits in the various business areas (HSE, R&D, HR, AFC, purchasing, etc.) were organised by the Supervisory Body (SB). In 2023 the SB found no violations of any obbligation related to law 231/2001, including corruption cases: this is what emerged from audits conducted in the same year (on those sensitive activities subjected to the law) and from absence of any whistleblowing which any witness can report anonymously.
As can be seen from the following table, most of PSC plants are ISO 9001 and ISO 14001 certified, some ISO 45001. These certifications help to standardize company activities and thus ensure high performance, the achievement of predefined objectives and constant optimization, in compliance with the safety of workers and the environment.
Furthermore, almost all of our offices boast IATF 16949 certification, a quality management system for the automotive sector developed by the International Automotive Task Force (IATF).
The quality, environmental and safety policy guidelines approved at group level in January 2022 have also been confirmed for 2023.
Risk management
Relations with local communities 1 About us
Materiality and methodology 4 Workers 5 Natural resources & environment
Research, development & technological innovation
Relations with business partners and quality of products
Compliances and certifications
Responsible management of the supply chain
Prima Components Anagni
Prima Components Ferentino
In the reporting year, no remarkable cases of non-compliance with the environmental, economic and social regulations and standards were detected. The penalties exceeding 50.000 Euros are intended significant. 3 Generated value
Prima Components Gricignano
Prima Components Paliano
Prima Eastern
Sole Oderzo
Sole Suzzara
Sole Pontedera
Sole Scanzorosciate
Sole Horgertshausen
Sole Woerth
Prima Poprad
Prima Sosnowiec CPS
Prima Sosnowiec APT
PSMM Pernambuco
PSCA SJP
PSCA Pinda I
PSCA Pinda II
The strategic guidelines and general criteria related to the supply of materials and services are established by the CEO and the President of the Group. In this group, materials and services, which can have an impact on the quality of the finished product, are included. In general, materials are divided into four categories:
■ raw materials including thermoplastic resins, paints, glues and two-component resins
■ semi-finished products and components
■ products from external processes, such as molding, painting, and assembly
■ packaging
Some suppliers with the same name because they belong to the same multinational but different company names and different market (for example Europe vs Brazil) have been counted as single companies and not as a single supplier. This choice was made in consideration of the considerable differences in context, currency and strategies.
Strategic services include:
■ selections
■ rework and repairing
■ tool calibration and laboratory tests
■ sequencing
2 Materiality and methodology
3 Generated value
Risk management
Research, development & technological innovation
Relations with business partners and quality of products
Compliances and certifications
Responsible management of the supply chain
Relations with local communities
4 Workers 5 Natural resources & environment
The selection of suppliers is entrusted to the strategic purchasing department which, in order to prevent any risk in terms of supply, performs an initial assessment where the following aspects are analyzed:
■ financial stability
■ suitability of available resources, including people and infrastructure
■ turnover in the automotive sector
■ logistic process
In line with the principles of sustainability, preference is given to those suppliers who show a consistent approach to ethical standards. For this reason, the strategic purchasing management requires all suppliers to adopt a code of ethics governing matters such as respect for human rights and anti-corruption measures, as well as an ISO 9001 certified quality management system.
Moreover, the adoption of management systems for health and safety (ISO 45001) and environmental (ISO 14001) is a preferential feature in the selection of partners. In addition, all new suppliers (not imposed by customers) of outsourced processes (e.g. molding, assembly and painting) are selected by PSC taking into account also environmental criteria.
All companies that supply raw materials and components are required to enter the final information on their elementary composition directly on the IMDS. This will respect the European Directive on end-of-life vehicles (DIR 2000/53/EC) and its subsequent amendments.
If the customer has contractually defined a list of designated suppliers (the so-called “imposed suppliers”), the material or product to be used for the production is purchased from such entities. In any case, this category is also subject to monitoring, unless otherwise specified in a contractual agreement with the customer.
Finally, it should be noted that a business intelligence tool is active, adopted in 2017, which aims to promote maximum transparency and traceability of the purchase process.
Suppliers are then required to demonstrate the implementation of those measures that can improve the quality of products and/or processes, the establishment of training courses for internal staff and the development of appropriate methods for managing their suppliers.
Compliances and certifications
Responsible
Natural resources & environment
To PSC, building positive relationships with the communities of the territories where its factories are located is of fundamental importance.
In order to promptly intercept the requests of the local community, specific initiatives are active, including that of the Brazilian plants, which have established a formal procedure to improve dialogue with the territory that hosts them and the management of complaints. Furthermore, the factories of the Brazilian business unit have an action plan on the subject, based on a mapping of the interested parties, which it is periodically monitored by management.
PSC is strongly committed to monitoring and managing the environmental impact of its operations. In this context, regular monitoring is carried out in all Italian and European plants to assess the noise level generated by production activities outside the company environment. This monitoring is aimed at verifying compliance with the limits set by the acoustic zoning and taking any corrective measures.
Prima Components Paliano plant has joined the Guaranteed Mobility project coordinated by the municipality of Paliano, with the aim of ensuring better mobility for the weakest in the community, disadvantaged people, the disabled and the elderly.
The Group’s commitment to the communities that host its production sites also takes shape in other sectors. In particular, all the factories of the Sole business unit are engaged in local sponsorships in the fields of education, culture and sport. One example is Sole Suzzara, who has committed to sponsoring the local football team. 3 Generated value 2 Materiality and methodology 4 Workers
PSC’s main shareholders are involved in “Frosinone Calcio” (Frosinone Football team)’s activities. Since October 2017, this football club has had a sports facility, named after the founder of the PSC group, Benito Stirpe, at its disposal, at the international avant-garde in terms of aesthetics and construction standards. The facility can accommodate 16,310 spectators and together with the Cittadella dello Sport, and future expansion projects for musical events, it is totally for the benefit of the community.
In 2019 the Foundation of Technical Institute Superior (Fondazione Istituto Tecnico Superiore Meccatronico) in Latium region was founded in Frosinone, of which PSC is one of the founding members. Such initiative was born from the need of some enterprises in the south region of this territory to strengthen technical-specialist training in the mechanical and mechatronic field and to develop skills strictly related to their professional research. The wealth of skills that in this way are formed on the territory represents an opportunity to develop the competitiveness of this specific area, which in the case of the “Frusinate” (province of Frosinone) has a strong manufacturing vocation; there is, therefore, a strong need for adequately trained human capital capable of responding to rapid technological and digital changes. In particular, the automotive, aerospace and electrical, as well as the field of electronic components, require increasingly qualified professionals with specific and advanced skills for the management and maintenance of complex and connected mechatronic systems.
ITS Meccatronico of Lazio Foundation aims to be close to technicalscientific school training, in order to integrate and improve technical-
Relations with local communities 1 About us
Materiality and methodology
Generated value
Risk management
Research, development & technological innovation
Relations with business partners and quality of products
Compliances and certifications
Responsible management of the supply chain
practical preparation of newly graduates, both through further theoretical and technical insights, either by carrying out several hours of work placements, so as to acquire and/or improve practical skills.
The primary recipients of the Foundation’s activities are, therefore, young people, in the interest of their professional and occupational growth in the area. The training course - spanning two years in which 1800 hours of courses are planned, 700 of internship, and a final state examination - is articulated on two curricula designed in collaboration with the reference companies of the territory, in order to meet the actual employment needs in the manufacturing field.
In 2023, the third cycle of the course for Higher Technician for the Innovation of Mechanical Processes and Products ended up with the state exam which awarded the relevant diploma to 25 students who were placed both in the companies that are part of the Foundation, than at other partner companies.
Workers
5 Natural resources & environment
Over the years, the ITS foundation has expanded with the participation of approximately 50 companies from Lazio (mainly Frosinone and Latina) and with 2 locations (Frosinone and Latina): for the two-year period 20232024, 50 students will graduate.
The activated courses in 2023 for the two-year period are
■ Higher Technician for Automation and Mechatronic Systems: Specialist for the Digital Transition of the Chemical-Pharmaceutical Industry
■ THigher Technician for the Innovation of Mechanical Processes and Products: Specialist for the Digital Transition of the Manufacturing Industry
The Foundation has also evaluated additional members in the province of Rome with the aim of opening an additional office for the biennium 24-25.
In PSC the contribution of every single human resource is crucial for business success. Creating and maintaining relations based on mutual loyalty and trust are therefore vital for this Group. This is why respect for workers’ rights and the enhancement of their contribution are fundamental in the management of employees and collaborators. Not only: for PSC it is equally fundamental to foster the development and professional growth of its resources.
As at 31 December 2023, the number of employees of the companies included in the reporting boundaries was 4233, marking an increase in staff of more than 200 employees compared to previous year, of which 134 are women. This is an important sign of the Group’s growth and development, which will allow us to achieve increasingly ambitious objectives and ensure better customer satisfaction.
overall growth also involved temporary workers:
PSC promotes and respects the physical and cultural integrity of people. For this reason, it mainly guarantees also working conditions that protect individual dignity. In addition, it designs safe working environments that carefully comply with safety standards, along with hygiene protection and health at work.
During 2023 there has been a notable increase in total turnover compared to the previous year, mainly due to the increase in new entries (+50%), in the meanwhile the number of terminations decreased by approximately 16%. In the following tables it is possible to consult the details of these numbers for the last three years. The data is detailed based on key parameters (such as age, gender, and nationality).
The organization’s collaborators, including part-time and temporary workers, can take advantage of the following benefits:
• Invalidity • Parental
• Retirement provision
The details of benefits applied to specific categories of workers, in each PSC site, is shown in the appendix on page. 125.
All employees in Italy have contracts that adhere to two types of CCNL:
• Rubber and Plastic
• Metalmeccanico
When necessary, each company may enter into second-level agreements that may concern, for example, performance bonuses, shift work, etc.
At present, there are no formal procedures in addition to what is already provided for in the relevant CCNL for determining remuneration, which is linked to the individual employment relationship and to bilateral agreements between the employer and the employee.
It is also thanks to training and staff development that, year after year, PSC Group became increasingly competitive. A virtuous process not only for the company, but also for the human resources themselves who, thanks to the acquisition of new knowledge and skills, are more motivated and rewarded. In 2023, an average of 5.5 hours of training pro capite has been provided, on decrease trend compared to the previous two years.
During the year 2023, the Group’s employees attended several courses, based on a project made dynamic by a constant comparison, that one between the skills acquired and those necessary for the company’s needs of development, also strategic for our customers.
2 In order to facilitate comparability with other organizations, starting from the 2022 Report, the data by employee category has been organized differently, i.e. based on the contractual category. Therefore, for the data provided in this chapter and in chapter 4.4 (Equal opportunity and diversity), comparability with the 2021 Report data cannot be guaranteed.
• Specialist and managerial training
The company puts its employees - particularly those belonging to strategic categories - in a position to face their professional challenges with appropriate skills and tools.
• Language training
PSC has organised foreign language courses for its employees, in order to provide them with the language skills needed to cope with daily work activities.
• Specific training on occupational safety and environmental issues
In line with the provisions on health and safety at work, compulsory training courses have been organised for new employees. However, on this subject, other resources have followed updating courses.
The Group confirmed its believing on the strategic importance of human capital development by the decision to setting up PSC Academy Research, at the end of the year 2023. This new unit is dedicated, among other things, to the management and enhancement of the Group’s training projects, with the aim of ensuring the sharing of know-how and best practices. In 2023, the Academy launched a plan to expand the training modules to a group of approximately 150 middle managers of the organization, which will be concluded on 2024. Through the Academy, the annual “socialization of the Prima Sole Components Group” program (aimed at top management) has been also updated, with the aim of strengthening Human Capital, reinforcing commitments, and sharing better knowledge and experiences.
Materiality and methodology 1 About us
Since 2017, PSC has equipped itself with a computer system that, in addition to the ordinary administration of personnel, allows to manage human resources according to a very precise flow of activities. This begins with the identification of the skills required for the role, continues with a gap analysis to assess the deviation from the expected, and ends with the definition of a specific training plan.
Competence assessment is not carried out for all professional figures in the company, but is currently only a process for the resources to be developed.
In 2020, two Group procedures were implemented: Key Figures and Talent Management.
Key figures are those resources that are considered indispensable and difficult to replace for the Group (they may not even be function managers), while Talents are those resources, with relatively low seniority in the company, that have potential for growth. In the PCIT BU, which is the first BU where the process is tested, 46 key figures and 6 talents were identified in 2021 and assessed in 2022. The assessment also covered soft skills and was carried out both through the use of a system called Personal Profile Analysis and directly by HR directors and managers, with the aim of developing ad hoc training plans. Subsequently, in 2023, a training plan (based on those skills identified as to be developed) has been defined and implemented, which
will last up to end of 2025, ending with a subsequent new verification of the acquired skills and/or enhanced. Also in 2023, same project started in the Sole Components BU with a similar path.
In Italy there is a compensation system - English term that indicates a set of elements, including salary, premiums and benefits – of staff providing, in addition to fixed remuneration, for the use of variable collective remuneration instruments (result premium).
Although a structured Management By Objectives (MBO) system is not defined, since 2018 a rewarding system has been defined for working groups that propose and implement improvement projects focused on specific issues.
A performance evaluation for career development is also planned in several foreign plants, which will involve about 90% of the Brazilian BU.
Employees who received regular appraisals of their performance and career development in 2023
Total Type
Employee by gender
Average training hours per employee in 2023 decreased compared to the previous two years.
PSC companies are committed to ensuring that their employees and contractors’ employees comply with safety and health and hygiene standards at work.
In order to promote the awareness and participation of all employees, various initiatives are implemented to consolidate and disseminate the safety culture. Employees are protected by national agreements. This is valid also for plants abroad.
The Group’s Italian plants comply with Legislative Decree 81/08 through the definition of the Risk Assessment Document (DVR), which details and analyses both general and specific risks. In this respect, hierarchical principles for risk assessment and prevention shall be followed as shown below:
• Elimination of risk at source
• Replacement of what is dangerous with what is safer or less risky
• Development of large technical systems for risks protection
• Establishment of procedure and work instructions
• Spread of safety signs
• Use of Personal Protective Equipment (PPE)
The Employer, with the support of the Protection and Prevention Service Manager, the Competent Doctor, the Workers’ Representative for Health,
Safety and the Environment (RLSSA), managers and supervisors, is responsible for the application of the DVR in the processes and activities of the production sites. The results of the DVR are the basis for analysis to define improvement activities, which are then included in the Company Improvement Plan and regularly implemented.
The workers of Italian plants, through consultation and active participation of all and through their RLSSA, involved in the verification and approval of the DVR, can report risk situations, and thus make a constructive contribution. Each worker is also free to refuse to carry out an activity deemed risky, in cases where it is not properly managed by the Prevention and Protection Service.
Similar risk assessment processes are implemented in foreign plants, which monitor them periodically.
The risks deriving from the interference of the activities are, where appropriate, managed in the Italian plants through the drafting of the Single Document for the Evaluation of Interfering Risks Also in PSMM Pernambuco plant there are procedures designed to assess the risks of interference; in particular, suppliers who carry out activities in PSC are required to assess the risk of these activities at the time of taking on the assignment and thereafter on a periodic basis.
At least the minimum number of RLSSAs in line with the provisions of Legislative Decree 81/08 are present in all plants of the Italian PSC companies. In 2022, the total number of Safety Representatives is 36.
In foreign plants, the regulations in force in the specific country are applied.
In Sole Wörth plant, an external company provides to draft a report regarding daily activities on a monthly basis, in order to refer all this to the business management.
In Poprad plant, risk assessment is carried out by an external firm. Quality manager is responsible for the company and its external consultants. Likewise, factory workers who perceive risky situations shall inform their supervisors.
In the plants of Sosnowiec CPS and APT, ISO 45001 management system is active, covering all activities, workers, and workplaces. Workplace health and safety management is entrusted to an interdisciplinary group, which carries out a risk assessment, by giving priority to the identification and elimination of the most serious potential ones. The quality of this process shall be regularly checked during safety audits and daily by checking workstations. If the implemented measures give positive results, they shall be extended to other activities or departments, where possible.
In PSC do Brazil plants, risk identification and risk assessment is elaborated and managed by the “health and safety” function with the participation of area employees and/or their representatives, and is set to identify all possible dangers associated with the activities of the company, evaluating them according to the parameters of Severity and Probability. The risk assessment and prevention process follow the hierarchical principles adopted in the Italian plants. If during the assessment it appears that the measures taken are not adequate to classify the risk as “acceptable” or “moderate”, further action shall be taken to minimise the risk. The effectiveness of each action is checked from thirty to ninety days after the actual implementation, after which the risk is further assessed. In the factory there are formal committees that deal with occupational safety and health and that represent the employees of the company, such as:
Workers are encouraged to report problematic situations, in accordance with the principle of prevention, by using the appropriate safety cards (S-Tags) available in the workplace. One more time, the law protects the possibility of workers to refuse any work activity that puts their health or safety at risk.
For Sole Hörgertshausen plant, the risk assessment is carried out with the support of an external consultancy. In addition, meetings are held periodically with the RSPP in which all possible risk and danger situations are analyzed, and interventions are identified to minimize them. Employees may also communicate any security risk anonymously via a dedicated e-mail address. 5
CIPA – Internal Commission on the prevention of accidents at work. COERGO – Ergonomics Committee, which assesses the ergonomic improvement needs of the various sectors.
Workers can report risk situations by filling in a special form, analyzed by the security departments of PSMM Pernambuco and PSC Automotivos that, in collaboration with the area managers, implement the actions deemed appropriate.
Workers can also report risk situations to CIPA, which is made up of representatives from all areas of the company, which meets monthly with management and managers of the “health and safety” function. In both cases the workers do not risk any repercussions. Even in the PSMM and PSCA plants, workers can refuse an assignment that is perceived as risky, as required by national law.
PSMM Pernambuco has established a direct communication channel with the STELLANTIS group through which risk situations can be reported.
If a particular work activity is identified as hazardous to safety or health, the worker is trained to report it immediately and stop operations until the problem is resolved.
The company applies a formal procedure to prevent the occurrence or recurrence of situations of risk; this requires that the root causes, actions, and unsafe conditions that led to an accident are brought to light, and indicate and develop the countermeasures necessary to avoid similar events. Such countermeasures are monitored weekly by the “Safety” department, along with those responsible for their actions
In all the Italian PSC plants a Competent Doctor is appointed who carries out the provisions of Legislative Decree 81/08 and to whom all workers can contact according to the agreements in force. Each year this professional draws up the health surveillance plan in relation to the risks identified for each individual task, plans periodic and preventive medical examinations, carries out the on-site inspection in the workplace and participates in the periodic security meeting, as well as in the drafting of the DVR. Also in foreign plants is involved the figure of the competent doctor in the activities that aim to identify, evaluate and manage risks.
All PSC workers receive appropriate health and safety training in accordance with the legal provisions of the countries in which the establishments are located.
In some of the Group’s establishments, initiatives have been launched to promote the health of workers, including campaigns against smoking, healthy eating, the promotion of outdoor activities and flu vaccinations. In addition, many establishments have formalized agreements with local
sports facilities.
It is an example PSMM Pernambuco that, being located within Stellantis area, offers its employees, in addition to the medical service related to work, the possibility of professional medical visits (periodic or emergency) or different medical services, even if they are not related to work. This possibility is offered by direct access after programming via app. The health team at this facility also undertakes to conduct health campaigns on nonwork-related topics through the involvement of external professionals at least six times a year.
UShocks, cuts, investments and crushing: these are the main dangers identified by PC Anagni and PC Ferentino.
In order to eliminate or minimize such hazards and risks, the establishments have undertaken the actions foreseen by the DVR improvement plan, formalising precise working procedures that also include the use of appropriate PPE and appropriate training and awareness-raising of staff on the subject.
The most risky activity identified by the sites of the Sole Components business unit and the Gricignano d’Aversa plant following its evaluation process is the circulation of forklifts. In order to minimise the risk, training, information and training were provided to sensitise the trolley drivers and both internal and external traffic was improved. For the Sole Hörgertshausen plant, the risk of hand cuts in the use of machinery has been identified as significant: In order to avoid this, specific training has been carried out and regular maintenance of the machinery is guaranteed, along with adequate lighting during the operation.
The risk assessment at the Prima Eastern plant revealed that there was a danger of falling inside the press during mould change. To eliminate this
3 Generated
eventuality, the access platforms were anchored to the presses by means of bolts and special non-slip rubber mats were installed, as required by the DVR improvement plan.
For Prima Sosnowiec plants, on 2023 all the activities involving the use of extruders and those other related to fire risk have been reconfirmed as dangerous. Both technical and organizational measures have been implemented to reduce risks.
In the Brazilian factories, the main hazards identified are the cutting injuries that can occur during the finishing process and the risks of falling as a result of activities to set up new machinery, which are carried out at considerable heights. To reduce these risks, appropriate training courses for workers have been set up and they have also been equipped with Personal Protective Equipment.
In the Pernambuco plant, the risk of falling has been reduced to a minimum, thanks to the use of specific measures, such as the installation of “tension platforms” with a 45° inclination, the use of “fall arrest devices” and also the
installation of a ladder to climb for having access to the machines’ electrical panels. However, there is still a risk present on large presses, which will be contained in the coming years through the installation of additional access stairs.
The distribution of accidents that occurred in 2023 in the Group’s companies is shown in the tables below.
Number of hours worked
Rate of recordable injuries*
Rate of high-consequence injuries**
Rate of fatalities***
Number of recordable injuries
Number of high-consequence injuries
Number of fatalities
3. Due to a reclassification of the types of injuries, it was not possible to compare them with those reported in previous years, which are nevertheless shown in the appendix. In particular, from 2023 the concepts of:
• Recordable injuries: involving a temporary disability and have not caused permanent sequelae;
• high consequence injuries: resulting in a permanent sequela or that the injured person does not return to his or her health prior to the accident within 6 months of the event;
• Fatal accidents: resulting in the death of the injured person.
In all Group sites, events such as injuries, dressing and near-injuries are managed by providing an accurate assessment of possible causes, so to set up initiatives to be applied with the purpose of avoiding repetition. The types of injuries recorded in 2023 in the Group were: trauma to
the joints and from stumbling, cuts, bruises, crushing, burns, falls and accidents on the way home-to-work.
In 2023, the ratio between the number of injuries and the worked hours across the entire Group decreased, compared to same ratios of the previous two years. This figure has been calculated using data referring to permanent employees and temporary workers, all together.
PPSC is constantly committed to avoiding any form of discrimination based on age, sex, sexual orientation, health status, ethnicity, nationality, political opinions and religious beliefs. In the Group’s code of ethics, the importance of ethical and social responsibility is recognized in carrying out business activities. In this regard, PSC undertakes to respect the legitimate interests of its stakeholders.
The Group companies operate in terms of diversity. This is what customers expect and it is of vital importance for business success. It is only by valuing the specific characteristics of each and by committing to the protection of equal opportunities that PSC will be able to fully involve all human resources in its growth path Although it should be pointed out that for some of the productive activities which characterize them
in the labor market there is a greater availability of male resources, PSC is committed to providing equal opportunities in all its recruitment and employment activities. An important innovation has been the decision, promoted by the PSC Academy & Research, to check the possibility of obtaining certification on gender equality for 2023 (UNI/PdR 125:2022).
This represents a significant commitment that we intend to undertake as a Group with the ultimate aim of monitoring and reducing gender gaps and promoting equal opportunities within our organisation.
The following tables show details of human resources at the different company levels, separated by gender and age.
The following tables show the gender, age and role composition of the entire workforce for the two-year period 2022-202344
* Protected class and disabled people
4 The table above does not report statistics relating to year 2021: these data, based on a di erent classification of
(related to 2022 and 2023), so that they do not appear in the tables because inconsistent; nevertheless they are
The environment
Energy consumption
Emissions in the atmosphere
Waste management
Water resource protection
The changes affecting the climate and the environment cannot leave us indifferent and everyone belonging to our society is called to give a contribution, in order to counteract the negative effects. Being aware of this, in the interest of limiting the impact of its activities, PSC cares for it with the same passion we have for our products and with the same attention we have for our customers’ requests. PSC is constantly committed to technological systems application and operations which, not only meet legal obligation and pollution reduction, but also aims at environmental efficiency improvement.
PSC protects its resources and works in compliance with all applicable regulations. The ISO 14001 certified PSC plants evaluate the environmental impacts of their work, implementing all the necessary activities to reduce them; this type of assessment also affects the design phase of each new product thanks to the FMEA method. Some plants (17%) have also achieved
ISO 50001 certification in order to start a systematic process of monitoring the energy consumption, with the aim of improving efficiency.
It is significant to point out that the Group is strengthening some of the company’s instruments, including the prevention of accidents at work and occupational diseases, and the assessment of risks, which are not limited to existing ones, but they also include potential ones. These procedures, graphically represented in the following image, can also be extended to environmental assessments and operate in accordance with the precautionary principle. Also considering the risks for which it is not possible to carry out a scientific assessment.
In addition to these analyses, there are also assessments of the potential impacts of components produced by PSC throughout the entire life cycle (Life Cycle Assessment, LCA): Sole Oderzo has developed an LCA study applied to one of its strategic products in 2022, and at Group level, the implementation of processes and tools is being evaluated to allow all plants to systematically calculate the environmental profile of their products. These analyses will help direct ecodesign activities and identify the steps and processes that generate the greatest impact on the environment and climate, to focus reduction initiatives where it is a priority.
In the following table, it is possible to see the types of fuel used by the Group, along with the energy consumption.
Standards,
For
Some of the Group’s Italian plants self-produce energy from photovoltaic systems.
The Prima Components plants in Ferentino and Anagni and Prima Eastern have photovoltaic systems installed both on the roofs of the buildings and on the ground. These systems are managed by an external company that supplies part of the energy produced to the plants.
In 2023, energy consumption from photovoltaic sources was 2,468 GJ for the Prima Components Ferentino plant, 2,774 GJ for the Prima Components Anagni plant and 1660 GJ for the Prima Eastern plant.
Prima Components Paliano plant has a backup electricity generator, with a Customs Agency License, but without a meter. Sole Oderzo plant, through a cogeneration plant feeded by natural gas, produced 12,669 GJ of electricity in 2023; Sole Scanzorosciate plant also has a cogeneration plant, which however is managed by an external company from which Scanzorosciate purchases the electricity produced.
The responsible and sustainable use of energy is a priority for PSC, both in terms of reducing consumption to cope with the depletion of nonrenewable resources, and for aspects related to emissions resulting from the combustion of fossil fuels. It is for this reason that an Energy Manager was appointed to the workforce to support the Group in the development of an energy efficiency plan, decarbonisation and reduction of emissions into the atmosphere. For this purpose, we have developed a decarbonization plan up to 2025 that will allow us to obtain an Organization Carbon Footprint certification as Scope 1, 2 and 3 for nine sites in Italy and seven others abroad.
At the same time, we will update the strategic plan to reduce direct and indirect greenhouse gas emissions on following sites: Prima Eastern, Sole Pontedera, Sole Oderzo, Prima Components Anagni and Prima Components Ferentino.
and the
The implementation of energy efficiency initiatives adopted also thanks to the work carried out by the energy manager led to a reduction in energy consumption both in absolute terms and in comparison, to machine hours worked and value generated.
The following table summarises the use of fuels for systems and office heating, as well as emissions from refrigerant gas leaks used in refrigerators and air conditioners. In order to more comprehensively monitor the impact of the Group’s activities on the climate, as of 2022, PSC has added to the
calculation of climate-changing emissions generated by the organisation (scope 1) also the indirect emissions from the use of imported energy (scope 2), represented by electricity purchased from the grid.
GWP factors sources:
• Scope 1: CO2: DEFRA, UK Government GHG Conversion Factors for Company Reporting, 2024
Consolidation approach for emissions
Operational control.
For scope 2 emissions location based: data from Ecoinvent 3.9.1 and International Energy agency for the production of electricity in Italy, Germany, Poland, Slovakia and Brazil. Scope 1
1 About us
Generated value 2 Materiality and methodology
Workers
Natural resources & environment
environment
consumption
in the atmosphere
management
resource
Standards, methodologies, assumptions and/or calculation tools used
• For fuels, invoices
• For refrigerant gases, the FGAS declaration pursuant to Article 16 paragraph 1 of Presidential Decree No. 43 of 27 January 2012, concerning the quantities of refrigerant added in repair activities
*Significant emissions to air for each of the following compounds:
In total, considering direct emissions and Location-based indirect emissions, in 2023 our activity generated 75,880.74 tCO2e. In addition to this, our activity generates the emission of other pollutants into the air such as nitrogen oxides and fine dust. The table below shows the quantities emitted in 2023 expressed in tonnes.
emissions (PM<2,5)
* Data on NOx, SOx, PM and CO are calculated by applying emission factors. Data on VOCs are analytical and derived from direct measurements.
Source of the conversion and emission factors used to calculate energy consumption and emissions
• Ecoinvent 3.9.1 (Heat, central or small-scale, natural gas {Europe without Switzerland}| heat production, natural gas, at boiler fan burner low-NOx non-modulating <100kW | Cut-o , U)
• Gasoline, Diesel and LPG: Italian Data Banck for average emission factors on National Road Transportation: fetransp.isprambiente.it (update to 2021)
1 About us For all production sites, the amount of emissions in relation to the fuels used was reported according to the following emission factors. Since this report has been issued with updated emission factors, all emissions related to previous years have been recalculated, accordingly.
Painting is the production process in which emissions of Volatile Organic Compounds (VOCs) are more consistent. These substances, present in the power coming out from the painting booths are conveyed inside the afterburner chamber, very high efficiency equipment able to cut them from thousands of mg/Nmc to a few units. The VOC abatement process takes place by thermal oxidation (combustion) and the resulting heat
is recovered either in the same painting plant - where it is used for the heating of drying furnaces and other purposes - or in other business areas.
In the following table, you can find the details of VOC’s emissions for each plant, where the painting process, at Group level and for the last three years, takes place.
10 Assumptions:
• Total Assimilation (VOC) to solvent acetone currently present in paints and varnishes
• Lower calorific value= 28,5 [Mj/Kg] (from Prontuario dell’Ingegnere, Hoepli, 2010)
• Neglecting diffuse emissions
Sources Analyzed: Solvent Management Plan 2023 of individual plants
KPI for monitoring the Group’s performance: greenhouse gas emissions
Direct greenhouse gas emissions (Scope 1) per unit of generated value
The potential and actual significant impacts resulting from the waste from the Group’s plants are mainly related to thermoplastic moulding and, where present, painting activities. The first, in particular, produces oily emulsions that in case of accidental dispersion could be toxic to water and soil. The painting activities produce sludge that is destined for disposal or incineration. Any hazardous waste (such as material contaminated with lubricating oils) is safely stored in dedicated warehouses. The production process also results in packaging waste, waste and production waste, mostly recyclable.
The end of life of the product is regulated by Directive 2000/53/EC, which requires manufacturers of vehicles and equipment to ensure the reuse and/or recovery of at least 95% of the weight of the vehicle. The need to comply with the legislation has led over time manufacturers to reorganize the production processes and materials used. The impact of PSC products in the end-of-life phase is therefore limited as almost all of them are reused or recovered.
aimed at identifying the main sources of waste generation and the measures necessary for their reduction. The monitoring indicators are checked monthly in relation to the annual targets: if deviations from the targets are found, corrective measures are activated in a timely manner. Moreover, no waste produced by these plants is disposed of in landfills.
The waste produced in PSC plants is managed by third parties, acting in line with contractual and legal obligations. In PSMM Pernambuco disposal is instead managed by JEEP thanks to the involvement of a specialized subject. The third party companies entrusted with the collection and disposal service are all authorized to manage the waste according to the national laws in force; also the authorizations of the transporters and the recipients are periodically checked by the subjects in charge within the individual plants, both Italian and foreign.
In order to reduce waste production and thus prevent the related impacts, there are two preferred measures: the use of waste for recovery rather than disposal and the use of reusable packaging made of recyclable materials, through the selection of appropriate suppliers. In most factories, for example, waste is reused and reused in the production process.
In the Brazilian plants of PSCA and PSMM there is a constant monitoring,
Waste data are collected by filling in the loading and unloading registers, forms and the Single Model Environmental Declaration (MUD). The data are catalogued by CER code (or other waste code in non-European countries), detailing the type, characteristics, hazard classes and destination of waste; they are then recorded in special electronic databases to monitor the trend. In some plants, including all PCIT sites and the three in Brazil, monthly KPIs are set.
The following tables show the quantity, characterisation and destination of PSC waste over the last three years.
Between 2021 and 2023, there has been an increase of 5.8% in total generated waste, that is a direct consequence of the production increase. During the same period, the hazardous waste ratio sent to preparation for reuse increased by 6 percentage points. In addition, the percentage of hazardous waste sent for recycling have increased from just under 1% of total hazardous waste to 11% in 2023.
The European Directives (and their transposition at national level) propose a legal framework for the control, generation and disposal of waste, recovery and recycling, and set a number of targets to be achieved and strategies to achieve this:
• principle of prevention;
• hierarchical principle of waste;
• “polluter pays” principle;
• green economy.
In accordance with the waste hierarchy principle, management must respect an order of priority:
1. prevention;
2. preparation for re-use;
3. recycling;
4. other recovery, for example energy recovery;
5. disposal
In this context, the 5R approach is applied in the plants of the Prima Components Italia and PSC do Brasil business units.
The concept behind the tool is based on the following assumptions:
• waste does not go to landfill
• going to the top of the pyramid improves waste management;
• minimise the amount of waste produced
• the pyramid should flatten to the advantage of the inverted base with the improvement of waste management
Therefore, practical calls for action leading to better waste management are described as follows and are related to the different Rs
• Refuse/Reject: avoid producing waste thanks to a proactive approach;
• Reduce: if the first recommendation is not applicable, then the amount of waste produced and the environmental impact of the waste matrix must be reduced;
• Reuse: each material must be reused as many times as possible before being thrown away;
• Recycle: all waste that can be recycled to produce new raw material must be recovered;
• Retrieve: some waste can be exploited to produce energy, e.g. through a waste-to-energy plant.
The impact of PSC production sites on water resources is not very significant and none of the plants are located in areas with high water stress.
As for the plants of Prima Components Italia, in particular, it is divided into three categories:
1) industrial water collection and purification tanks (if the painting process is present, for the moulding phase the water is conveyed in a closed circuit);
2) civil discharges;
3) meteoric waters.
The water is mainly used for cooling the presses and, where present, for the water curtains of the painting systems, for hygienic and cleaning purposes in the common areas, and as a fire reserve.
In the plants of Prima Sosnowiec APT and in all PCITA sites water consumption and drainage in sewers are monitored through KPI, while in Prima Poprad there is an emergency plan for the management of water resources issues.
In the Brazilian plants water is taken from the aqueduct and the municipal manager also monitors the withdrawals with a meter at the entrance of the sites. In 2022, due to a water emergency, the Brazilian PINDA I plant also used water from tanker trucks. For PSMM Pernambuco, the management and monitoring of water withdrawals is carried out by Jeep.
Annual monitoring of the water resource and its impacts is foreseen in
all PSC plants. Many sites in the group aim to reduce the impact on the resource through several initiatives, including the assessment of the state of integrity of water systems to avoid losses.
All volumes taken and discharged, as described in the tables below, refer to fresh water.
5
Standard, methodologies and used hypotheses
Prima Eastern: meter reading (matching with invoices).
PC Gricignano d'Aversa, Anagni, Ferentino, Paliano e la BU PSCBR: Meter readings.
Sole Suzzara, Pontedera e Scanzorosciate: Invoices.
Oderzo: meter reading and periodic water analysis.
Sole Horgertshausen, Poprad and Sosnowiec Plants: invoices.
Prima Eastern: meter readings and estimates.
PC Gricignano d'Aversa, Anagni, Ferentino e la BU PSCBR: meter readings.
Sole Suzzara, Pontedera e Scanzorosciate: Invoice + meter reading.
Oderzo: meter reading and periodic water analysis.
Sole Horgertshausen invoices.
Prima Eastern: meter readings and estimates.
PC Gricignano d'Aversa and BU BR: meter readings.
Sole Suzzara, Pontedera and Scanzorosciate: Invoice + meter reading.
Oderzo: meter reading and periodic water analysis.
Sole Horgertshausen: invoices.
11 Data do not take into account the water withdrawals and discharges from the Sole Woerth plant as the water resource is managed externally and no information could be found on this
Total water volume withdrawn planned and not planned
Water discharged into natural water body
Water discharged into sewer
Water discharged into imho pool or biological tank/Sealed tank with periodic sampling (disposal as waste CER 200304)
Treatment and use in the JEEP/ETE process
The volumes of water discharged into the sewers are obtained from the meter reading, while those managed as waste CER 200304 are taken from the unique models of environmental declaration (MUD).
For all Italian plants the emission limits in water are defined on the basis of Legislative Decree 152/06, Table 3, Annex 5. For the plants in Brazil, however, they are fixed by reference to CONAMA Resolution number 430/201.
Other emission limits for the protection of water quality are dictated by the Integrated Environmental Authorization (AIA) for Sole Oderzo and Sole Pontedera and by the Single EnvironmentalAuthorization (AUA) for Prima Components Anagni, Prima Components Paliano and Prima Components Gricignano d’Aversa.
KPI for monitoring the group’s performance: withdrawals and discharges of water*
Volume of water withdrawn per unit of generated value
Volume of water discharges per unit of generated value
The withdrawn and discharged water volumes increased in 2023, in contrast to the trend observed in 2022, nevertheless consistent with the increased production.
* The economic value generated, water withdrawals and discharges of the companies included in the scope of PSC's consolidated financial statements were used in the calculation of the KPI.
• In 2021, the data on number of permanent female workers for the whole Group, as published in the 2022 Report, was incorrect due to a typo. The correct figure is 1.069 instead of 1.096.
• The data on man-hours worked in 2021 for the whole Group, as published in the 2022 Report have been corrected based on the adjustments made by single BUs, particularly:
• Consequently, accident rates and the KPI of the number of recordable accidents per mega-man-hour worked have been recalculated.
• The data on average training hours by employee category in 2022 for the whole Group in 2022 Report have been modified based on the adjustments made by single BUs, and particularly::
-managers: the previous value of 40.9 has been recalculated to 12.1;
- -for employees, the previous value of 6,640,883 hours has been recalculated to 6.681.123;
-for temporary workers, the previous value of 1,221,376 hours has been recalculated to 1.238.349.
Consequently, accident rates and the KPI of the number of recordable accidents per mega-hour of man-hour worked have been recalculated.
• The data on man-hours worked and accidents for 2022 for the whole Group published in the 2022 Report have been corrected based on the adjustments made by single BUs, and particularly:
- For employees:
• the previous value of 6.617.047 man-hours has been recalculated to 6.264.115;
• the previous value of 65 recordable accidents has been corrected to 59.
- For non-employees:
• he previous value of 920,854 man-hours has been recalculated to 982.374; the previous value of 10 recordable accidents has been corrected to 11. 5
-executives: the previous value of 12.1 has been recalculated to 10.1; -clerks: the previous value of 10.0 has been recalculated to 10.1.
• The data on LPG energy consumption in 2022 for the whole group in 2022 Report have been modified based on the adjustments made by single BUs, and particularly:
- The previous consumption of 37.704 GJ has been recalculated to 6.237 GJ.
• The data on natural gas consumption presented in the 2022 Report have been modified based on the adjustments made by single BUs, and particularly:
- for 2021 it was recalculated from 276.410 GJ to 243.648 GJ; - for 2022 it was recalculated from 207.333 GJ to 193.741 GJ.
As a result, direct greenhouse gas emissions caused by fuels in 2022 change from 15,496 tCO2e to 11,396 tCO2e and in 2021 change from 17,962 tCO2e to 14,389 tCO2e. The energy intensity values and KPIs related to energy consumption and greenhouse gas emissions have been recalculated, accordingly.
• The data on total electricity consumption published for the whole Group in 2022 Report have been modified following the adjustments made by single BUs, and particularly:
-For 2021 the figure of 566.692 GJ has been corrected to 605.430 GJ.
-For 2022 the figure of 684.256 GJ has been corrected to 593.872 GJ.
As a result, the Group’s scope 2 location based emissions have been recalculated, changing from 57.823 tCO2e to 55.416 tCO2e.
• In 2022, the figure on the quantity of hazardous waste intended for reuse for the whole Group, as published in the previous Report, was incorrect due to a typo. The correct figure is 2.481 instead of 2.841.
To create value for all stakeholders by designing, producing and marketing innovative and technologically advanced products, in compliance with regulations, by actively collaborating with all players in the supply chain.
• Bring all Group sites to be certified to the ISO 14001 standard.
• Bring at least 30% of all Group sites to be certified ISO 45001.
• The new integrated Quality, Environment and Safety Policies will be communicated to all Stakeholders.
• Zeroing the number of accidents at all sites.
• A webinar presenting the Sustainability Report process to new business unit managers and site managers will be repeated
• Carry out specific sustainability training for all employees by 2022, along with safety training.
Ensuring wellbeing in the workplace for all employees without discrimination, providing training and resources to ensure professional development and appropriate working conditions.
• The Academy project will be rescheduled by June 2021 to start again in September 2021 with face-to-face meetings.
• Creation of a single organisational structure for personnel assessment PSC Italy for the B.U. PCIT and Sole. Harmonisation of processes and tools used for training management, appraisal processes, job descriptions and skills is planned for 2021, with full implementation by 2022. Everything will be managed with HR management so ware.
• Target in progress: approximately 83% of the Group’s plants are certified for the 14001 standard.
• Target achieved: 67% of the Group’s plants are certified for the ISO 45001.
• Target achieved: since 2022, on the company website, a reference to the Integrated Quality, Environment and Safety Policies has been included in the 'PSC Policies' section.
• Target in prgress: in 2023, 51 minor incidents occurred among employees at all sites, and 13 has been the number of incidents among temporary workers. The average number of recordable accidents decreases from 8.5 to 7.5 expressed as total injuries per total mega worked hours. No permanent or fatal injuries have been recorded in 2023.
• Target not achieved: Due to changes in the corporate plan, the webinar had not been arranged.
• Target not achieved: no specific training course has been carried out due to di erent company’s needs.
• Target achieved: the Academy project reprised during 2021. With the launch of PSC Academy&Research, the top management “socialization” program, focused on training enhancement, has been also reconfirmed for 2023; at the same time, the number of participants (middle managers) increased and so the program will be extended to all 2024.
• Goal to be achieved soon: the harmonization of processes and tools for sta evaluation is being reorganized.
• Bring all Group sites to be certified to the ISO 14001 standard.
• Bring at least 80% of all Group sites to be certified ISO 45001
• Bring at least 20% of all Group sites to be certified ISO 50001.
• Zeroing the number of accidents at all sites.
• Define specific training for all new hires on sustainability.
• Extend the involvement of middle management in the training integration program (so-called “socialization”) up to 2024.
• Verify the requirements for obtaining the gender equality certification (Uni Pdr 125:2022) for all Italian sites.
• Finalization of the target of the harmonization of all processes.
Developing innovative solutions to improve the quality of life and the environment, protecting natural resources, reducing waste produced and emissions into the atmosphere and pursuing sustainable production processes.
• Monitor and reduce energy consumption.
• Reduce direct CO2 emissions into the atmosphere (Scope 1).
• Reduce the amount of waste.
• Increase the percentage of recovered wastes compared to disposed ones.
• Target achieved: The Group's total energy consumption per machine hours worked gradually decreased over the three-year period, achieving a total variation of 25%.
• Target to be refined: Over the three-year period, Scope 1 emissions remained substantially unchanged.
• Target to be refined: Over the three-year period, the total quantity of produce wastes increased by 5.8%, also as a result of the production increase.
• Target not achieved: Compared to 2021, in 2023 the amount of recovered wastes decreased by 5.6%.
• Monitor and reduce energy consumption.
• Reduce direct CO2 emissions (Scope 1) per unit of generated compared to 2021.
• Reduce Scope 1 and 2 emissions by 5% by 2024, in line with the objectives set in the Group's decarbonization plan.
• Reduce the amount of produced wastes per unit of value generated by production.
The material topics for PSC have been aggregated into three macro-themes that share the management approach.
Macro-themes
Material topics for PSC
Risks Management
Research, development & technological innovation
Customer relations (business partners)
Compliance
Responsible supply chain management
Relations with Local Communities
Wellbeing of Employees
Occupational Health and Safety
Equal opportunities and diversity
Energy Consumption
Emissions in the Atmosphere
Waste Management
Water Resources Protection
Processes common to all macro-themes
MOTIVATIONS AND BOUNDARIES
The material topics were identified by applying the principles for defining the contents of the Report and through the stakeholder engagement and materiality analysis processes described in detail in the second chapter of the Sustainability Report, “Materiality and methodology”.
For each material topic of PSC, the perimeter within which the potential impact may fall has been identified:
■ 1. Within company boundaries: in this case the impact primarily influences internal stakeholders
■ 2. Outside the company boundaries: in this case it is mainly external stakeholders who are affected by the impact
■ 3. Inside and outside the company boundaries: the impact concerns all stakeholders.
In the management of material issues, PSC considers both the possible impact it can cause directly and the impact that may indirectly derive from its work.
The Group is managed in the logic of recognizing the social role that the company has within the community, through the implementation of innovative solutions to improve the quality of life and the environment. PSC has developed a common policy with regard to quality, environment and safety throughout the Group, in line with the international standards ISO 9001, ISO 14001, ISO45001.
In the quality, environment and health and safety at work policy, it is stated that:
«The future of Prima Sole Components depends on the ability to establish and maintain stable and satisfactory relationships with customers.
The satisfaction of customer needs and the acquisition of new market areas are achieved through continuous improvement of the quality of products, services and cost-effectiveness.
Prima Sole Components, in carrying out its activities, considers human health, environmental protection and safety at work an indispensable duty, a continuous commitment and a constant component of its mission.»
The operational plans of the business units and the sites connected to them are then developed along these lines. In the Business Plan, the strategic guidelines are: competitiveness, technological innovation and globalization. At the level of the business unit and, in cascade, for each production site, the activities are defined in line with the strategic guidelines of PSC according to the following logical process: analysis of the business plan, S.W.O.T. analysis for the determination of strengths and weaknesses, as well as opportunities and risks, risk assessment and definition of the operating plan.
• The Business Plan covers the corporate network of all PSC Group sites.
• The last revision date of the Business Plan dates back to 2023.
Following the reorganisation of the Group in recent years, the organisation and management model, in accordance with Decree-Law 231, was subject to an updating process in 2020 and in 2023 this model was implemented in all the Italian Business Units of the Group. New content has been introduced, developed on the basis of the path taken by PSC towards greater sustainability of its activities.
With the publication of its sustainability report, PSC intends to demonstrate its willingness and commitment to embark on a new path towards sustainability in the economic, social and environmental spheres. This will and commitment originates from the company management, and is transmitted in all plants and at all company levels.
The commitment to respect the legitimate interests of its stakeholders and the community in which all PSC plants are located is enshrined in the Group’s Code of Ethics.
Also in the 2023-+2024 Prima Sole Components Business Plan, the holding company defines the vision, mission and medium and long-term strategies.
The objectives and targets that PSC sets itself on its path to sustainability are found in this Report and cover all PSC sites. The objectives are of an improving nature with respect to national regulations and will be monitored annually. Other more specific objectives are identified in the improvement plans for each company site, which are drawn up in accordance with quality, environmental and safety regulations.
The responsibility for deploying human and financial resources lies with the business unit administrator who, together with the plant manager, draws up an investment plan approved at holding company level
In the PSC sites certified ISO 9001, ISO 14001 and ISO 45001 there are complaints collection systems provided by the management systems. PSC has activated, through the recently developed 231 organizational model, a whistleblowing system: each recipient of the model is required to inform the Supervisory Body in detail and promptly about any violation of the organizational model of which it is aware, or functional anomalies or irregularities potentially relevant for the purposes of Decree 231/01. Principles of protection of employees or collaborators who report wrongdoing are defined.
Stakeholders may make inquiries and complaints at the contact point indicated in this report.
PSC publishes the Sustainability Report in accordance with the main international reference standard for sustainability reporting, the GRIStandards. PSC is also committed to keeping up to date and applied the quality, environment and safety policies that are a reference for all the
group’s plants, to pursue continuous improvement in all areas.
To monitor the effective adequacy of the management of material issues, the results of the first and third party audits carried out on the management systems will be used. In addition, the information of the GRI Standards reported in this Report, in the previous and subsequent reports, will be used as management assessments. To monitor some of the significant aspects more effectively, PSC has developed Key Performance Indicators (KPIs) that allow the performance of these aspects over the years at Group level to be assessed.
The commitment to take a more sustainable approach unites both the Chairman and the CEO and involves all business units, individual plants and all company functions and employees. Responsibility for implementing policies, delivering commitments and achieving objectives lies with the directors of each business unit and the directors of individual production units. The achievement of the specific objectives, identified in the improvement plans, is delegated to those responsible for the implementation of the specific planned activities.
Generated value
MOTIVATIONS AND BOUNDARIES
Risk Management
Research, development and technological innovation Customer relations (business partners)
To act considering economic, social and environmental risks and opportunities for PSC's operations and image.
Any related impacts could have an e ect both within and outside the Group.
Research and technological innovation such as strategic elements to increase the competitiveness of its products, in line with sustainable development and mobility.
Any related impacts could have an e ect both inside and outside the Group.
To relate to customers as key business partners, recognising the value of cooperation, synergies and socially responsible behaviour, in order to jointly achieve higher levels of knowledge and higher quality and to establish a lasting and mutually satisfying relationship.
Any related impacts could have an e ect both within and outside the Group.
• Loss of market positioning due to inadequate risk and opportunity assessment.
• Consolidation of reputation and trust relationship towards the company.
• Increased competitiveness of the company.
• Consolidation of reputation and trust towards the company.
• Contribution to the transition to a low-carbon emission economy through the development of sustainable and innovative services/products.
• Loss of customers or strategic partners.
• Increased business resilience.
• Consolidation of reputation and trust towards the company.
Responsible supply chain management Compliance
To ensure compliance with mandatory or voluntary standards through empowerment of its employees and through appropriate organisation and management models, and to achieve measurable and certifiable performance and sustainability targets.
Any related impacts could a ect both within and outside the Group
The involvement of the supply chain by sharing principles, policies and tools for sustainability and social responsibility. Any related impacts could have an e ect both within and outside the Group.
• Penalties for non-compliance with applicable socio-economic and environmental legislation.
• Contribution to the development of a more ethical society.
• Consolidation of reputation and trust towards the company.
• Consolidation of reputation and trust in the company.
• Indirect environmental damages not yet estimated.
• Indirect social damages not yet estimated.
Local communities
Attention and confrontation with the expectations of the local community, through an open, transparent and constructive dialogue.
Any related impacts could have an e ect outside the Group
• Contribution to the economic and social development of the territory.
• Conflicts with the local community due to negative perception of the productive activity carried out.
206-1: Legal actions for anti-competitive behavior, anti-trust, and monopoly practices
416-1 Assessment of the health and safety impacts of product and service categories
416-2 Incidents of non-compliance concerning the health and safety impacts of products and services 205-1 Operations assessed for risks related to corruption 205-2 Communication and training about anti-corruption policies and procedures 205-3 Confirmed incidents of corruption and actions taken 403-1 Occupational health and safety management system 308-1 New suppliers that were screenedusing environmental criteria 414-1
413-1
2 Materiality and methodology
3 Generated value
4 Workers
5 Natural resources & environment
The following commitments are central to the quality, environment and occupational health and safety policy, the principles of which are to be found at all Group sites:
■ To integrate economic objectives with stakeholder concerns and satisfaction of applicable requirements
■ To improve processes and products and system performance in general by implementing specific projects to increase performance in each area, thinking about the impact the product can have throughout its life cycle
■ To maintain constant compliance with current legislation, respecting the health and safety of workers and environmental protection.
■ To Promote sustainable behaviour in the entire production and supply chain
The guiding principles in relations with suppliers, the community and customers, to ensure the development of a responsible supply chain, high levels of customer satisfaction and open dialogue with communities, are honesty, fairness, transparency and impartiality. These principles have always animated PSC, are presented in the recently updated Code of Ethics and will be formalised with the implementation throughout the Group of the organisational model consistent with Legislative Decree 231/2001, at present, adopted by over 67% of the company..
PSC’s desire to carry out its activities in an ethical manner, respecting its guiding principles in its relations with stakeholders, is stated in the Code of Ethics.
The objectives and targets assumed for the material topics of this macrotheme are developed as described in the section ‘Processes common to all macro-themes’.
The personnel and financial resources for the management of this macroissue are allocated in an articulated manner by the entire management of the Group with coordination and control actions exercised by the chairman and managing director of PSC.
The mechanisms by which it is possible to make any complaints related to this macro-theme are developed following what is described in the section “Processes common to all macro-themes”.
Periodically, the CEO of PSC and the directors of the business unit and subsequently the Board of Directors evaluate the economic performance of the individual business units and PSC and analyze any risks and opportunities.
The evaluation mechanisms on the management of material topics related to the macro-theme “Value generated” are developed following what is described in the section “Processes common to all macro-themes”.
Responsibilities for the management of material issues related to the macro-theme “Value generated” are assigned as described in the section “Processes common to all macro-themes”.
of employees
To consider our employees a fundamental element of the company value and ensure their wellbeing through a proper training for the development of individual skills, an organization and an environment which foster the commitment to quality and the achievement of personal and professional satisfaction.
Any related impacts may have an e ect within the Group.
To ensure process safety and protecting the health of workers at all stages of supply and production.
Any related impacts may have an e ect within the Group.
Health and safety at work
• Loss of manpower and productivity due to unsatisfactory and/or overly stressful working conditions.
• Inability to attract talent due to unsatisfactory and/or overly stressful working conditions.
• Human and professional growth of collaborators.
• Di usion of a work culture that guarantees high standards of health and safety for workers.
• Damage to workers due to accidents or occupational diseases.
• Deterioration of the reputation and relationship of trust towards the company.
GRI 401: Employment 2016
GRI 404: Training and education 2016
Equal opportunities and diversity
Enhancing the personal and cultural diversity of employees, suppliers and customers, avoiding unjustified discrimination and promoting inclusion.
Any related impacts may have an e ect within the Group.
• Inadequate selection of personnel due to cultural prejudices related to gender or other personal orientations of workers.
• Contribution to the development of a more ethical society.
GRI 403: Occupational Health and Safety 2018
401-1 New employee hires and employee Turnover
401-2 Benefits provided to full-time employees that are not provided to temporary or parttime employees
404-1 Average hours of training per year per employee
404-3 Percentage of employees receiving regular performance and career development reviews
403-1 Occupational health and safety management system 403-2 Hazard identification, risk assessment and accident investigation
403-3 Occupational health services
403-4 Worker participation, consultation, and communication on occupational health and safety
403-5 Worker training on occupational health and safety
403-6 Promotion of worker health
403-7 Prevention and mitigation of occupational health and safety impacts directly linked by business relationships
403-9 Work-related injuries
GRI 405: Diversity and Equal Opportunity 2016
405-1 Diversity of governance bodies and employees
The principles set out in PSC’s quality, environment and safety policies are of reference for all the Group’s sites and are in line with the strategic guidelines of the Business Plan.
In the quality, environment and occupational health and safety policy, the central commitments include:
■ Promoting any initiative to reduce to zero, in every activity, the occurrence of accidents that can compromise the safety of employees and neighboring communities also through consultation and active participation of all workers
■ Promoting the active involvement of all staff in the process of continuous improvement, through consultation and active participation of all those who can make a constructive and innovative contribution.
PSC’s commitment to enhancing human resources, to guarantee their rights and to promote their development and personal growth is stated in the Group’s Code of Ethics.
The objectives and targets taken for the material themes of this macrotheme are developed following what is described in the section “Processes common to all macrothemes”.
Staff and economic resources for the management of workers are allocated to the individual business units through the definition and approval of the annual budget.
The mechanisms by which it is possible to make any complaints related to this macrotheme are developed following what is described in the section “Processes common to all macrothemes”.
Prima Sole Components ensures the control, monitoring and possibly the mitigation of negative impacts on the health and safety of workers according to the reference legislation. Internal and external audits and periodic reviews shall also be carried out in establishments that have implemented a management system.
The human resources of the individual business units, in collaboration with the directors of the production units, manage vocational training programs and personnel for employees, new employees and in administration at the production sites. These programs are developed according to business needs. The priorities for the individual worker are identified by the HR managers and management according to the job needs.
At sites where a management system is active at least once a year, a review is carried out involving the directors of the business units, the directors of the production units and the heads of the various business functions. Following the review, the results of the audits, the non-conformities, the corrective actions implemented, the objectives and the indicators, improvements can be implemented.
The evaluation mechanisms on the management of material topics related to the macro-theme “Workers” are developed following what is described in the section “Processes common to all macrothemes”.
The responsibilities for the management of material topics related to the macro-theme “Workers” are assigned following what is described in the section “Processes common to all macrothemes”.
Individual managers of business units, as employers of staff, have responsibility for health and safety.
In each production unit, the directors have legal power of attorney on issues related to the environment and safety and have a wide delegation regarding the management of these aspects. Each Group company has an RSPP that handles safety issues and workers elect one or more RLS (or RLSSA in companies with rubber and plastic contracts).
The responsible use of energy resources achieved, when possible, with energy saving technologies and practices and the choice of renewable resources.
Any related impacts could have an e ect both inside and outside the Group
Conduct its activities by seizing opportunities to prevent and mitigate emissions into the atmosphere, protecting air quality and combating climate change. Any related impacts could have an e ect both inside and outside the Group
• Consumption of non-renewable energy resources.
• Increased costs for energy purchase
The application, where possible, of best practices of reduction, through prevention, and recycling of waste.
Any related impacts could have an e ect both inside and outside the Group
• Direct contribution to climate change by greenhouse gas emissions during the production process.
• Indirect contribution to climate change by greenhouse gas emissions upstream and downstream of the production process.
• Contribution to the environmental impact of end-of-life waste disposal.
305-1 Direct (Scope 1) GHG emissions
305-2 Energy indirect (Scope 2) GHG emissions
305-7 Nitrogen oxides (NOx), sulfur oxides (SOx), and other significant air emissions
The responsible use of water due to technologies and practices aimed at reducing the amount taken and maintaining the original quality. Any related impacts could have an e ect both inside and outside the Group
• Water quality degradation.
• Depletion of water resources.
306-1 Waste generation and significant waste-related impacts
306-2 Management of significant waste-related impacts
306-3 Waste generated
306-4 Waste diverted from disposal
306-5 Waste directed to disposal
303-1 Interactions with water as a shared resource
303-2 Management of water discharge-related impacts
303-3 Water withdrawal 303-4 Water discharge
Among the central themes for the SGP, declared in the policy of quality, environment and health and safety at work, is the commitment to “protect and enhance the environment and take all necessary measures to prevent pollution”
The objectives and targets taken for the material themes of this macrotheme are developed following what is described in the section “Processes common to all macrothemes”.
The administrator of the business unit is responsible for allocating human and financial resources, according to the instructions of the plant manager who draws up an investment plan.
The mechanisms by which it is possible to make any complaints related to this macrotheme are developed following what is described in the section “Processes common to all macrothemes”.
Most of the plants have adopted an environmental management system certified in accordance with ISO 14001 which, thanks to an audit process and periodic reviews, provides for control, monitoring and, where appropriate, mitigation of negative impacts on the environment.
The Group adopts tools to evaluate and quantify energy and environmental loads and the potential impacts of products and processes through:
• External analysis laboratories for the assessment of the main environmental impacts (emissions, discharges, noise, waste), dedicated internal resources and external consultancy for the energy assessment of individual sites
• Involvement of all professional skills necessary for the development, management and control of activities
• Adoption and maintenance of an environmental management system.
The evaluation mechanisms on the management of material issues related to the macro-theme “Natural resources and environment” are developed following what is described in the section “Processes common to all macrothemes”.
Responsibility for the management of natural resources and environment issues is also entrusted to the business unit administrators.
As part of the management system, the issue is addressed by entrusting management responsibility to the site manager who is accompanied by a manager of the management system and an operational structure.
Workers 3 Generated value 2 Materiality and methodology
5 Natural resources & environment 1 About us
Employees diversity on 2021 STAFF13 (Managers and White Collar)
Number of hours worked
Rate of Recordable work-related injuries*
Rate of High-consequence work-related injuries**
Rate of fatalities (as result of work related injuries)***
Number of Recordable work-related injuries
Number of High-consequence work-related injuries
Number of fatalities (as result of work related injuries)
Number of hours worked
Rate of Recordable work-related injuries*
Rate of High-consequence work-related injuries**
Rate of fatalities (as result of work related injuries)***
Number of Recordable work-related injuries
Number of High-consequence work-related injuries
Number of fatalities (as result of work related injuries)
13 Employee classification carried forward to 2021
(Workers)
Those people who are not directly involved on production activities or not directly working on any machinery
Direct economic value generated: revenues; (PRODUCTION VALUE)
Economic
Economic
Direct economic value generated: revenues; (PRODUCTION VALUE)
Economic value distributed: operating costs, employee wages and benefits (TOTAL PRODUCTION COST)
Economic value retained: "direct economic value generated" less "economic value distributed".
Direct economic value generated: revenues; (PRODUCTION VALUE)
Economic value distributed: operating costs, employee wages and benefits (TOTAL PRODUCTION COST)
Economic value retained: "direct
Rest
Nationality: Italy
Nationality: Europe (excluding italy)
Nationality: Rest of the world
Total temporary employees women
Men
Nationality: Italy
Nationality: Europe (excluding italy)
Nationality: Rest of the world
Total non-guaranteed hours employees women Men
Nationality: Italy
Nationality: Europe (excluding italy)
Nationality: Rest of the world
Total full-time employees
women
Men
Nationality: Italy
Nationality: Europe (excluding italy)
Nationality: Rest of the world Total
Nationality: Italy
Nationality: Europe (excluding italy)
Nationality: Rest of the world
Totale Permanent employees
employees
Nationality: Italy
Nationality: Europe (excluding italy)
Nationality: Rest of the world
Total temporary employees women
Nationality: Italy
Nationality: Europe (excluding italy)
Nationality: Rest of the world
Total non-guaranteed hours employees women Men
Nationality: Italy
Nationality: Europe (excluding italy)
Nationality: Rest of the world
Total full-time employees
women
Men
Nationality: Italy
Nationality: Europe (excluding italy)
Nationality: Rest of the world
Total Part-time employees
Nationality: Italy
Nationality: Europe (excluding italy)
Nationality: Rest of the world
Totale Permanent employees
Temporary employees
Nationality: Italy
Nationality: Europe (excluding italy)
Nationality: Rest of the world
Total temporary employees
women
Men
Nationality: Italy
Nationality: Europe (excluding italy)
Nationality: Rest of the world
Total non-guaranteed hours employees
Men
Nationality: Italy
Nationality: Europe (excluding italy)
Nationality: Rest of the world
Total full-time employees
women
Men
Nationality: Italy
Nationality: Europe (excluding italy)
Nationality: Rest of the world
Total Part-time employees
Nationality: Italy
Nationality: Europe (excluding italy)
Nationality: Rest of the world
Totale Permanent employees
Nationality: Italy
Nationality: Europe (excluding italy)
Nationality: Rest of the world
Total temporary employees women
Men
Nationality: Italy
Nationality: Europe (excluding italy)
Nationality: Rest of the world
Total non-guaranteed hours employees
women
Men
Nationality: Italy
Nationality: Europe (excluding italy)
Nationality: Rest of the world
Total full-time employees
women
Men
Nationality: Italy
Nationality: Europe (excluding italy)
Nationality: Rest of the world
Total Part-time employees
Nationality: Italy
Nationality: Europe (excluding italy)
Nationality: Rest of the world
Totale Permanent employees
Nationality: Italy
Nationality: Europe (excluding italy)
Nationality: Rest of the world
Total temporary employees women
Men
Nationality: Italy
Nationality: Europe (excluding italy)
Nationality: Rest of the world
Total non-guaranteed hours employees
women
Men
Nationality: Italy
Nationality: Europe (excluding italy)
Nationality: Rest of the world
Total full-time employees
women
Men
Nationality: Italy
Nationality: Europe (excluding italy)
Nationality: Rest of the world
Total Part-time employees
Italy
Nationality: Europe (excluding italy)
Nationality: Rest of the world
Totale Permanent employees
Nationality: Italy
Nationality: Europe (excluding italy)
Nationality: Rest of the world
Total temporary employees
women
Men
Nationality: Italy
Nationality: Europe (excluding italy)
Nationality: Rest of the world
Total non-guaranteed hours employees women Men
Nationality: Italy
Nationality: Europe (excluding italy)
Nationality: Rest of the world
Total full-time employees
women
Men
Nationality: Italy
Nationality: Europe (excluding italy)
Nationality: Rest of the world
Total Part-time employees
Man hours worked
Number of recordable injuries
Number of high-consequence injuries
Number of fatalities as a result of injury
Rate of recordable injuries
Rate of high-consequence injuries
Rate of fatalities as a result of injury
Man hours worked
Number of recordable injuries
Numebr of high-consequence injuries
Number of fatalities as a result of injury
Rate of recordable injuries
Rate of high-consequence injuries
Rate of fatalities as a result of injury
Man hours worked
Number of recordable injuries
Number of high-consequence injuries
Number of fatalities as a result of injury
Rate of recordable injuries
Rate of high-consequence injuries
Rate of fatalities as a result of injury
Man hours worked
Number of recordable injuries
Numebr of high-consequence injuries
Number of fatalities as a result of injury
Rate of recordable injuries
Rate of high-consequence injuries
Rate of fatalities as a result of injury
Man hours worked
Number of recordable injuries
Number of high-consequence injuries
Number of fatalities as a result of injury
Rate of recordable injuries
Rate of high-consequence injuries
Rate of fatalities as a result of injury
Man hours worked
Number of recordable injuries
Numebr of high-consequence injuries
Number of fatalities as a result of injury
Rate of recordable injuries
Rate of high-consequence injuries
Rate of fatalities as a result of injury Employees
Man hours worked
Number of recordable injuries
Number of high-consequence injuries
Number of fatalities as a result of injury
Rate of recordable injuries
Rate of high-consequence injuries
Rate of fatalities as a result of injury
Man hours worked
Number of recordable injuries
Numebr of high-consequence injuries
Number of fatalities as a result of injury
Rate of recordable injuries
Rate of high-consequence injuries
Rate of fatalities as a result of injury
Man hours worked
Number of recordable injuries
Number of high-consequence injuries
Number of fatalities as a result of injury
Rate of recordable injuries
Rate of high-consequence injuries
Rate of fatalities as a result of injury
Man hours worked
Number of recordable injuries
Numebr of high-consequence injuries
Number of fatalities as a result of injury
Rate of recordable injuries
Rate of high-consequence injuries
Rate of fatalities as a result of injury
Man hours worked
Number of recordable injuries
Number of high-consequence injuries
Number of fatalities as a result of injury
Rate of recordable injuries
Rate of high-consequence injuries
Rate of fatalities as a result of injury
Man hours worked
Number of recordable injuries
Numebr of high-consequence injuries
Number of fatalities as a result of injury
Rate of recordable injuries
Rate of high-consequence injuries
Rate of fatalities as a result of injury
Governing body CDA
< 30 years old
30-50 years
> 50 years old
Women
Men
Vulnerable categories
Total governing body
< 30 years old
30-50 years
> 50 years old
Women
Men
Vulnerable categories
Total executives
< 30 years old
30-50 years
> 50 years old
Women
Men
Vulnerable categories
Total Middle managers
< 30 years old
30-50 years
> 50 years old
Women
Men
Vulnerable categories
Total Clerks
< 30 years old
30-50 years
> 50 years old
Women
Men
Vulnerable categories
Total Workers
< 30 years old
30-50 years
> 50 years old
Women
Men
Vulnerable categories
Total governing body
< 30 years old
30-50 years
> 50 years old
Women
Men
Vulnerable categories
Total executives
< 30 years old
30-50 years
> 50 years old
Women
Men
Vulnerable categories
Total Middle managers
< 30 years old
30-50 years
> 50 years old
Women
Men
Vulnerable categories
Total Clerks
< 30 years old
30-50 years
> 50 years old
Women
Men
Vulnerable categories
Total Workers
< 30 years old
30-50 years
> 50 years old
Women
Men
Vulnerable categories
Total governing body Executives
< 30 years old
30-50 years
> 50 years old
Women
Men
Vulnerable categories
Total executives
< 30 years old
30-50 years
> 50 years old
Women
Men
Vulnerable categories
Total Middle managers
< 30 years old
30-50 years
> 50 years old
Women
Men
Vulnerable categories
Total Clerks
< 30 years old
30-50 years
> 50 years old
Women
Men
Vulnerable categories
Total
< 30 years old
30-50 years
> 50 years old
Women
Men
Vulnerable categories
Total governing body
< 30 years old
30-50 years
> 50 years old
Women
Men
Vulnerable categories
Total executives
< 30 years old
30-50 years
> 50 years old
Women
Men
Vulnerable categories
Total Middle managers
< 30 years old
30-50 years
> 50 years old
Women
Men
Vulnerable categories
Total Clerks
< 30 years old
30-50 years
> 50 years old
Women
Men
Vulnerable categories
Total Workers
Governing
Executives Middle
< 30 years old
30-50 years
> 50 years old
Women
Men
Vulnerable categories
Total governing body
< 30 years old
30-50 years
> 50 years old
Women
Men
Vulnerable categories
Total executives
< 30 years old
30-50 years
> 50 years old
Women
Men
Vulnerable categories
Total Middle managers
< 30 years old
30-50 years
> 50 years old
Women
Men
Vulnerable categories
Total Clerks
< 30 years old
30-50 years
> 50 years old
Women
Men
Vulnerable categories
Total Workers
< 30 years old
30-50 years
> 50 years old
Women
Men
Vulnerable categories
Total governing body
< 30 years old
30-50 years
> 50 years old
Women
Men
Vulnerable categories
Total executives
< 30 years old
30-50 years
> 50 years old
Women
Men
Vulnerable categories
Total Middle managers
< 30 years old
30-50 years
> 50 years old
Women
Men
Vulnerable categories
Total Clerks
< 30 years old
30-50 years
> 50 years old
Women
Men
Vulnerable categories
Total Workers
First
Treatment
First
t
t
t
t
t
t
About us
Materiality and methodology
Generated value
Workers
Natural resources & environment
Waste
Other disposal operations
Other recovery options
Landfillingwaste disposal
Inceneration with energetic recovery
Inceneration without energy recovery
Preparation for re-use
Riciclyng
Total Hazardous Waste
Other disposal operations
Other recovery options
Landfillingwaste disposal
Inceneration with energetic recovery
Inceneration without energy recovery
Preparation for re-use
Riciclyng
Total No-Hazardous Waste
Other
Landfillingwaste
Inceneration
Inceneration
Other
Other
Landfillingwaste
Inceneration
Inceneration
Preparation
Riciclyng
Other disposal operations
Other recovery options
Landfillingwaste disposal
Inceneration with energetic recovery
Inceneration without energy recovery
Preparation for re-use
Riciclyng
Total Hazardous Waste
Other disposal operations
Other recovery options
Landfillingwaste disposal
Inceneration with energetic recovery
Inceneration without energy recovery
Preparation for re-use
Riciclyng
About us
Materiality and methodology
Generated value
Workers
Natural resources & environment
Other disposal operations
Other recovery options
Landfillingwaste disposal
Inceneration with energetic recovery
Inceneration without energy recovery
Preparation for re-use
Riciclyng
Total Hazardous Waste
Other disposal operations
Other recovery options
Landfillingwaste disposal
Inceneration with energetic recovery
Inceneration without energy recovery
Preparation for re-use
Riciclyng
Other disposal operations
Other recovery options
Landfillingwaste disposal
Inceneration with energetic recovery
Inceneration without energy recovery
Preparation for re-use
Riciclyng
Total Hazardous Waste
Other disposal operations
Other recovery options
Landfillingwaste disposal
Inceneration with energetic recovery
Inceneration without energy recovery
Preparation for re-use
Riciclyng Total No-Hazardous Waste
content index
Prima Sole Components has reported the information in this GRI content index for the period 01/01/2023 - 31/12/2023 in accordance to the GRI Standards
GRI 1: Foundation 2021 GRI 1 used
2-1 Organisation details
2-2 Entities included in the organization’s sustainability reporting
2-3 Reporting period, frequency and contact point
2-4 Restatements of information
2-5 External Assurance
2-6 Activities, value chain and other business relationships
2-7 Employees
2-8 Workers who are not employees
2-9 Governance structure and composition
2-10 Nomination and selection of the highest governance body
2-11 Chair of the highest governance body
2-12 Role of the highest governance body in overseeing the management of impacts
2-13 Delegation of responsibility for managing impacts 2-14 Role of the highest governance body in sustainability reporting 2-15 Conflicts of interest
2-16 Communication of critical concerns
2-17 Collective knowledge of the highest governance body
2-18 Evaluation of the performance of the highest governance body
2-19 Remuneration policies
2-20 Process to determine remuneration
2-21
2-22
Intertek Italia SpA Via Miglioli, 2/A 20063 Cernusco sul Naviglio (MI) Italia
Tel +39 02 95383833 Fax +39 02 95383832 intertek.it
Torino, July 18th , 2024
To the Board of Directors of P.S.C. - Pr ma Sole Components S.p.A and to all interested parties
Intertek Italia S.p A. (Intertek) was mandated by P.S.C. - Prima Sole Components S.p.A (P.S.C.) to carry out an independent assessment of the Sustainability Report for the year 2023, in order to verify the correct application of GRI Standards 2021 including the relevance and reliability of its contents with respect to stakeholders' expectations.
Intertek has not played any direct or indirect role in the preparation o the document, whose contents are the sole responsibility of P.S.C.
Intertek declares its independence and absence of conflicts of interest with regard to P.S.C. and its stakeho ders.
The assessment was accomplished considering in particular the international standard ISAE 3000 (Revised), in "limited assurance" mode.
Our task involved:
- a completeness and consistency analysis of the Sustainability Report under assessment with respect to the standards adopted by P.S.C
- the investigation of qualitative and quantitative aspects deemed to be significant for stakeholders;
- the interview on a sample basis of P.S.C. staff and interested parties' representatives.
Based on the above activities and selected sample, no contrary evidence arose to let us conclude that:
- the Sustainability Report of P.S.C. - Prima Sole Components S.p.A for the year 2023 has been prepared in accordance with GRI Standards 2021;
- the data and information included in the Report are consistent with the assessed documents.
We therefore believe that the Sustainability Report of P.S.C. - Prima Sole Components S.p.A for the year 2023 contains an adequate representation of impacts, strategies and sustainability performances of the company, with respect to GRI reporting principles and stakeholders' expectations.
Best regards.
A essandro Ferracino
Marco
Zomer Regiona Director ECA Business Assu rance Project Leader (excl. UK and Iberia)