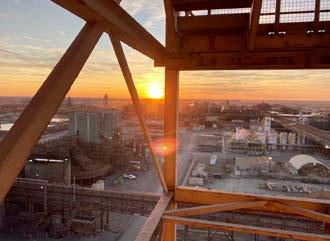
6 minute read
Trending Globally
Trending GL BALLY
For mining giant BHP, Blockchain is ‘key to supply transparency’
Advertisement
Leading global resources company BHP has proved Blockchain technology can ease concerns about sustainability and humanrights transgressions in the supply chain. Australia-based mining and metals giant BHP has been piloting Blockchain to maintain high ESG (Environmental, Social and Governance) standards across its supply chains. The technology is already being adopted by the mining industry to trace materials to the mine of origin and make precious-metal investments more transparent.
Blockchain helped with Tesla supply chain ESG targets The company recently ran a blockchain pilot in which it traced nickel shipments from its nickel operations in Western Australia to Tesla’s Gigafactory in Shanghai. Nickel is a key ingredient in the manufacture of car batteries. The pilot supported Tesla’s “due diligence on product provenance”. BHP ran a similar trial with rubber sourced for use in truck tyres. A major concern around rubber is whether it has been ethically sourced. BHP procures more than 6,000 giant tyres a year. Natural rubber carries a high-risk of modern slavery and illegal deforestation for supply chains. BHP was keen to see if Blockchain could mitigate such risks, by helping the company trace rubber from its source through the supply chain. She revealed the trials - which have been running for the past two years - were successful. BHP will use Blockchain on copper value chain. BHP will run similar trials with suppliers, focused on tracking products from manufacturing to fitment, before expanding further down the supply chain. The company also plans to use Blockchain tech to trace emissions from copper used in electric cables and wires. While ensuring a more ethical supply chain, blockchain can mitigate against supply issues, as well as supporting decarbonisation initiatives by tracking greenhouse gas emissions. A BHP spokesperson said that customers increasingly care about where products come from and to this end, traceability is a key enabler to lifting sustainability standards across the value chain.
Walmart adds science-based targets to supply chain financing option
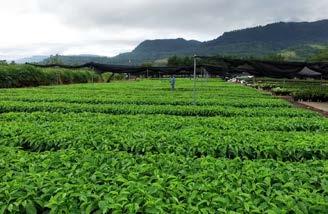
In its announcement, Walmart noted new research from HSBC and the Boston Consulting Group, which found that as much as half of the $100 trillion of investment by 2050 to achieve net-zero across global supply chains needs to come from small and mid-sized businesses. But those businesses often don’t have the in-house climate expertise and access to capital to tackle sustainability goals, the report noted.
Walmart is taking the cue from the research findings that larger corporations need to "provide liquidity and share knowledge and resources with smaller businesses."
To get access to the retailer's Sustainable Supply Chain Finance program, suppliers have two options. They can set science-based targets that will get validated by the Science Based Targets Initiative, a joint venture between CDP, the United Nations Global Compact, the World Resources Institute, and the Worldwide Fund for Nature aimed at improving companies’ work to reduce greenhouse gas emissions. Or they can meet certain score thresholds on their CDP climate change reports.
Financing for eligible suppliers with Walmart-approved invoices is linked to their CDP scores, targets and reported impacts, with lower pricing linked to more ambitious efforts, per the announcement.
Walmart has been working with HSBC since 2019 on the retailer’s Sustainable Supply Chain Finance program. The financing program announcement is the latest one by Walmart to advance its sustainability goals. The retailer is targeting zero emissions across its global operations by 2040.
Siemens has developed an ecosystem-based approach for the exchange of emission data
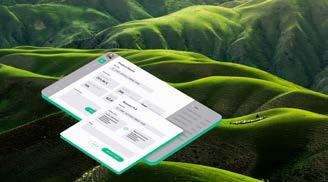
Since the supply chain accounts for the largest share of the ecological footprint of products, the decarbonization of industry is a challenge, which must be tackled by all the stakeholders together. As a leading provider of automation technology and industry software, Siemens has, for the first time, launched a solution for the efficient query, calculation, and transfer of information on the actual Product Carbon Footprint (PCF). SiGreen now makes it possible to exchange emission data along the supply chain and combine it with data from a company’s own value creation to obtain a product’s true carbon footprint. To achieve this, Siemens has initiated the open, cross-industry Estainium network with the aim of enabling manufacturers, suppliers, customers, and partners to exchange trustworthy PCF data. With SiGreen supporting companies in tracking their Product Carbon Footprint, they can take targeted reduction measures providing a quantifiable effect. CO2 management thus supports companies on their way towards carbon neutral production and helps them to transform sustainability into a decisive competitive edge.
Cedrik Neike, Member of the Managing Board of Siemens AG and CEO Digital Industries, said, “All our customers share the desire to reduce the carbon footprint of their products. But to do so, they first need to know exactly the CO2 emissions of their supply chain. And they need to know which adjustments can save them the most CO2. SiGreen and Estainium enable them to do just that. It allows us to bring much-needed transparency to supply chains while protecting the confidentiality of the data. This technology can bring us a big step closer to our goal: a carbon neutral industry.”
Precise data is a key prerequisite for effectively achieving the emission targets in the value chain. With SiGreen, Siemens has successfully developed an application for the efficient acquisition of real data collected where emissions are produced, i.e., in the corresponding steps along the supply chain. To calculate the carbon footprint, SiGreen makes use of real data rather than industrial average values. Product Carbon Footprints thus become a measurement and control instrument – and can be actively reduced by applying targeted improvement measures.
The global supply chain analytics market size is expected to reach USD 15.61 billion by 2028 according to a new study conducted by Polaris Market Research. The market is expected to expand at a CAGR of 17.5% from 2021-2028. Key factors projected to boost demand for the global market include increased adoption in sectors such as retail, consumer goods, automotive, manufacturing, and healthcare, among others. Rising government measures in supply chain management to rebuild the global economy from the covid-19 pandemic are driving market expansion globally. Moreover, the increasing presence of global leaders in the market and huge R&D investments are also positively impacting the market growth.
KEY HIGHLIGHTS OF SUPPLY CHAIN ANALYTICS MARKET
Based on solutions, manufacturing analytics emerged as the dominant segment and is projected to grow at a rapid rate over the forecast period. The growing healthcare industry and rising government initiatives in the manufacturing industry are fuelling the manufacturing segment's rise in the global supply chain analytics market. By deployment, the cloud segment accounted for most of the market and is predicted to witness exponential growth soon. The analytics in the cloud solution offers a centralized
reporting solution as well as assistance with many elements of troubleshooting, use, and optimization. It provides enterprises with improved supply chain outcomes and more detailed reporting. In terms of services, the professional service segment registered the higher revenue growth and is expected to take this lead ahead in the coming years. Professional services are required to ensure that the new systems are compatible with the existing ones and to integrate the new with the old to avoid data loss or theft.
Companies across industries are heavily spending to increase operational and supply chain efficiencies and digitize their business models. The supply chain function's emphasis has turned to sophisticated planning procedures, such as integrated sales, analytical demand planning, and operations planning, which are among most preferred business processes in many firms. Key players are adopting new growth strategies such as new technology development, product innovation, mergers, and acquisitions to gain market share, and business expansion in the global supply chain analytics market.
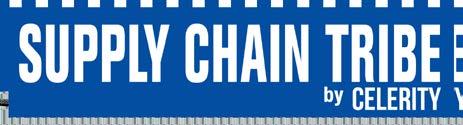
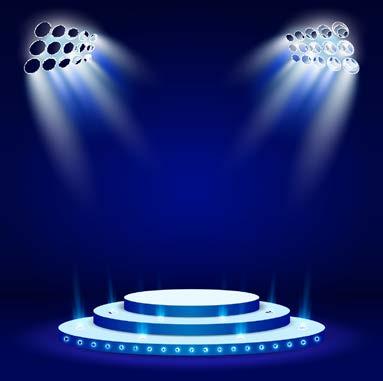
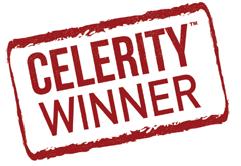