
13 minute read
FOCUS
KNIGHT In SHINING ARMOR
The COVID-19 pandemic has shone a bright spotlight to the field of humanitarian logistics and the wider global & local economies, and the supply chain associated with it. The outbreak has majorly impacted global manufacturing capacities and distribution of products & services locally and across borders. The response to the pandemic has been varied with some organizations having been able to quickly adapt and adjust to the new reality, while some have found it hard to survive. The dominant focus on minimizing costs, while following lean, just-in-time, and zeroinventory approaches while being hugely effective in normal times have several deficiencies in operating during a disaster or pandemic setting. Much can thus be learned from humanitarian supply chains for managing pandemic or disaster related supply chain disruptions, shares Sunil Banthiya, Chief Operating Officer, Aliaxis India, during the recently held Tattv’21 conclave by SIOM, Nashik.
Advertisement
THE World Economic Forum estimates that in the decades to come, epidemics will, on an average, cause an annual economic loss of ~ 0.7% of the global GDP, equal in scale to the global economic loss caused by climate change (WEF, 2019). The current coronavirus disease (COVID‐19) pandemic constitutes a global healthcare crisis with far‐reaching consequences on livelihoods and economies. The pandemic has had direct and indirect impacts and cascades on the supply chain.
Going by such striking estimates, this could not have been a more opportune time to talk about the importance of humanitarian logistics. What exactly is humanitarian logistics? The basic task of humanitarian logistics comprises planning, acquiring, and delivering requested supplies and services, at the places and times they are needed for the purpose of alleviating the suffering of vulnerable people. Humanitarian supply chains focus on saving lives and on responding to disasters and emergencies and are therefore geared toward dealing with turbulence, uncertainties, and a complex dynamic environment.
The key difference between humanitarian logistics versus any business supply chain is in their strategic objectives. A business supply chain is centered around the fact that you want to achieve the most optimal cost to serve along with great customer satisfaction. The objective of humanitarian logistics is to deliver a certain throughput in a race against time in most situations. The emphasis is more on throughput and not so much on optimizing the cost of service.
COMPLEXITY OF MANAGING SUPPLY CHAIN DURING A PANDEMIC
Let me share some of the challenges that we faced in managing our supply chain during this COVID-19 pandemic. A) Volatile Demand: The most talkedabout example of demand spike, toilet paper, is ironically usually the go-to example of a perfectly forecastable product, since the end consumption, as you would imagine, is rather stable. The one thing which one quickly realized was that in this pandemic situation, no historical based statistical algorithms, the mainstay of most demand forecasting tools, are of much use. A combination of “shortage gaming” and the “bullwhip effect”, results in unprecedented volatility in demand.
B) Supply Bottlenecks: The other challenge that we faced during the pandemic were the painful supply bottlenecks. Trade channels and our vendor operations got closed for a variety of reasons – shortages of labor, sickness, travel bans, or simply because they fell in containment zones. What this meant was that the ecosystem of suppliers, which you could rely on to support your manufacturing process was not
available. Further the frequent plant start-up and shut down due to erratic material supply created a risk on operational performance and safety of the plant. All these factors along with availability of only a skeleton staff, due to COVID-19 infections, adversely impacted product supply.
C) Logistic Disruptions: The other key disruption was in terms of transport because the sudden lockdown meant that truckers in some cases abandoned their vehicles on highways. In many cases, import cargoes were stuck in customs due to the sheer amount of port congestion. Container shortages led to close to ~ 40 to 50% increase in ocean freight costs and all of this had truly little forward visibility, which meant that one hardly had the time to react, adjust and plan before the next crisis was on to you.
D) Working Capital Crunch: What happens during any of these humanitarian disaster settings is also that there follows a working capital crunch, as businesses prioritize cash preservation in an uncertain world. This translates to delayed vendor payments and therefore the inability of many small and mid-size vendors to stay afloat and be able to provide their services, resulting in a cascading impact of shortages and rising costs.
E) Managing Inventory: This is more acute, if your product is shelf life managed and you happen to have warehouses closed because of their being in containment zones or otherwise - managing product shelf life and obsolescence further adds to the distribution complexity.
WHAT KIND OF SOLUTIONS SHOULD WE BE THINKING ABOUT?
In a world accustomed to instant coffee, instant messaging and “click of a button” deliveries, there is, in this case, unfortunately no easy quick-fix solutions. One needs to build a unified playbook where you can set parameters, standardize with easy to replicate steps, which one could follow in a situation like this. This requires careful preparation; people capability build and an organizational ability to think and respond in an agile manner. As the old saying goes, “Amateurs study tactics, but professionals study logistics”.
CRITICAL IMPORTANCE OF REVERSE SCHEDULING
Let us look at the challenge of the biggest public health undertaking of our times that we need to solve to mitigate the COVID-19 pandemic – getting needles to shoulder in the shortest period. In my point of view, what would make our journey from vaccine to vaccination successful is the implementation of some of the time-tested concepts of supply chain.
A) Reverse or Backwards Scheduling: The place to start would be the point of delivery or care and stretching back
Facing and managing supply chain disruptions can be considered the new norm, considering other disruptive forces such as climate change, or financial or political crises. The lessons learned from humanitarian supply chains can help us to mitigate and overcome supply chain disruptions more effectively and help organizations, supply chains, and societies at large, to manage current and future disruptions.
Sunil Banthiya is a versatile supply chain and operations leader with more than 25 years of experience across Plan, Source, Make & Deliver. A passionate believer and practitioner of Supply Chain Excellence, Sunil has led several initiatives using appropriate technology & Lean Six Sigma tools across diverse product categories to achieve significant improvement in supply chain performance. Sunil holds a B.Tech in Chemical Engineering from Indian Institute of Technology Kanpur, India.
to the supply point of vaccine. Based on say what our goal on the number of vaccinations that we need to carry out per day or per week are, demand would get set. We now need to work backwards to map out the end-toend supply chain “flow” to fulfill that demand. The next step is to identify where the bottlenecks in the “flow” of vaccines is and to monitor and resolve them in real time. There are of course additional complexities – managing the vaccine shelf life, the requirement of a cold supply chain, reshuffling supplies based on fluctuating demand from one area to another, recording and managing a follow up schedule and delivery to the prioritized target group for vaccination, etc. The concept of “Reverse scheduling” is central in thinking through the capacity or throughput requirement in terms of volume, time and skill.
B) Debottlenecking Constraints: Most of us would be familiar with the theory of constraints. Simply put, you resolve one bottleneck, and another will get uncovered in the end to end supply chain. Organizations need to work towards eradicating those bottlenecks and see how they can manage all the pieces together be it sourcing, operations, logistics, and try to get a perfect “flow” from
the point of origin to the point of delivery.
LESSONS FOR BUSINESS SUPPLY CHAIN
Let me share some of our own experience as we went through the pandemic and the lessons that we have learned from it… A) Build redundancies in the supply chain: While it seems counterintuitive, one of the key learnings emerging from the pandemic is that one cannot afford to be only focused on Just in time deliveries, reducing inventory and taking costs out of your supply network. There is a tradeoff with these “lean models” and the level of preparedness or inventories required to combat a pandemic. Redundancy in terms of number of supply or distribution nodes becomes hyper critical to ensure business continuity and customer service. The reason I am saying this is that one of the key industry trends across the board, post the GST implementation has been one of consolidation of the distribution network footprint – merging or closure of warehouse operations in multiple states to sometimes a single large distribution center in a central location to prioritize scale synergies and reduce inventories and costs. Just imagine however if this single distribution center fell into a containment zone, what it would mean in terms of business continuity. Therefore, one of our key learnings was that some redundancies in the supply chain and the incremental cost because of it is essential as it can prove immensely useful to mitigate disruption in an emergency or a pandemic situation.
B) The Case for Diversification: A lot of companies have painfully learned the lesson of having all their “eggs in one basket” in how their supply chains are configured. Historically, large companies have sometime chased the cost arbitrage available of lower tax or labor rates and offshored a large part of their supply chain into a certain geography or country. For whatever reason, if that country or region suffers a disaster or a health pandemic, you are looking at a large disruption in your supply chain. Companies with diversified supply chains during this COVID-19 pandemic were far better placed to mitigate the disruption due to the pandemic in one region by quickly ramping up production in a less impacted geography.
Let me give you an example of 3M, the industrial giant, which in no small way, was able to meet the spike in demand of their N95 masks because of their global manufacturing footprint and not being constrained by a single source of supply. For large organizations therefore, even if the complexity and costs are more, it makes sense to have a global footprint.
C) Agility: What the pandemic also taught us is the criticality of being nimble – operating systems which enable flexibility are the rights ones to invest in. Employees, being able to navigate and manage ambiguity, identify, and cope with workarounds (ramping up on virtual meetings for example!) and above all be resilient in the face of adversity. Adaptability is required whether it be in terms of a small change in being able to say ship directly from the plant to the customers or in managing a large
change of reformulating a product to accommodate an alternate source of supply. Again, when you build in flexibility to work in multiple ways in your supply chain, you also incur an additional cost. However, this flexibility may just be the critical difference to being able to survive and thrive or perish. C) End-to-end Visibility: Having realtime visibility of your supply chain is key to agility. If there is one thing that this pandemic has taught us, it is the importance of digitization and being able to have an end-to-end visibility – right from where your raw materials are to the inventory your distributors are carrying. If you are running a cross-border supply chain, having visibility becomes even much more critical for you to be able the manage that entire flow of material from your vendors, logistic partners, to manufacturing and finally to your distributors and customers.
Digitizing the supply chain improves speed, accuracy, and flexibility and the ability to respond in real-time.
D) Collaboration & Innovation: The COVID‐19 pandemic has accelerated business model innovations and brought it to the forefront. There are abundant cases of organizations donning a new avatar, for example, automotive and aerospace manufacturers producing
One must communicate both upstream and downstream in terms of managing your internal and external stakeholders, employees, suppliers, and customers to ensure alignment. Pandemics and disaster settings are fertile grounds for rumormongering, fueled by easy accessibility to social media. As in anything, nature abhors vacuum – an absence of transparent communication from you would quickly get filled with speculation and conspiracy theories. In most cases, it is better to OVERCOMMUNICATE than to COMMUNICATE LESS.
ventilators; distilleries producing hand sanitizers, or, in transportation, stranded passenger planes being converted to cargo planes. The latter was important as much of medical transportation uses belly cargo; thus, stranded passenger planes hugely improved the overall cargo capacity.
For our organization as well, soon after the lockdown, we realized, that we could leverage our existing as well as forge new collaborative relationships with academia, hospitals and vendors to innovate in repurposing our manufacturing facilities in response to the pandemic.
Using our core manufacturing competency and expertise in plastic processing, we could initiate design and manufacture of PPEs such as face shields, safety goggles and hand sanitizers. By collaborating with academia & hospitals, we improved on our initial product design, developed rapid prototypes to be able to scale up quickly for mass production. In all of this, an important part is the relationship with your suppliers and customers. Relationships are critical if you need quick access to more products from your vendor, for example, working capital support from your customers and given the fact that all suppliers and customers were facing a difficult time, such relationships became even much more critical.
ABOVE ALL, EXECUTION IS THE KEY…
All this finally boils down to one simple fact of EXECUTION. As the saying goes, “Ideas are everywhere, it's finally the implementation which matters”. Good execution capability is a key characteristic of any great supply chain and let us look at some of the key enablers for good execution...
A) Centralized Co-ordinated approach: Executing in a dynamic fast changing external environment requires a centralized coordinated approach. A patchwork approach rarely works. This is even more critical when there are multiple stakeholders you are having to deal with. One needs to co-ordinate both horizontally and vertically. Let me explain what I mean by horizontal and vertical coordination. When it comes to horizontal coordination, it’s all about suppliers in manufacturing and distribution, you need to get that coordination right. Vertical co-ordination is essentially from a strategic or tactical point of view – what's the inventory required say at a certain point, where do you think the demand would emerge and how would you service that? Making choices, therefore in terms of what to prioritize is a key decision. One of the things, for example, that we did during the pandemic, knowing that we were constrained in terms of capacity due the fewer number of lines that we could run and the limited number of people we could get into our plants, we carefully chose which part of the product portfolio we should focus on and the SKUs that we should make and deliver.
B) Crisp & Clear Communication:
The last thing that I cannot stop emphasizing is the importance of clear messaging in a crisis. One must communicate both upstream and downstream in terms of managing your internal and external stakeholders, employees, suppliers, and customers to ensure alignment.
Pandemics and disaster settings are fertile grounds for rumormongering, fueled by easy accessibility to social media. As in anything, nature abhors vacuum – an absence of transparent communication from you would quickly get filled with speculation and conspiracy theories. In most cases, it is better to overcommunicate than to communicate less.
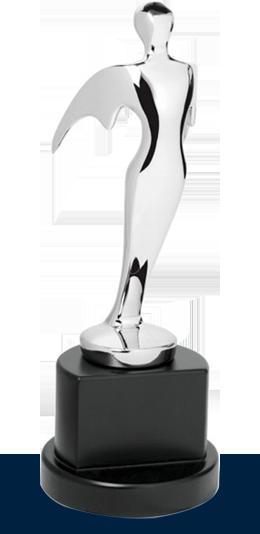
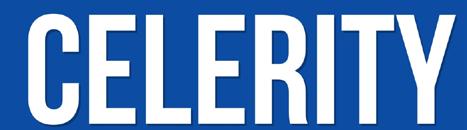