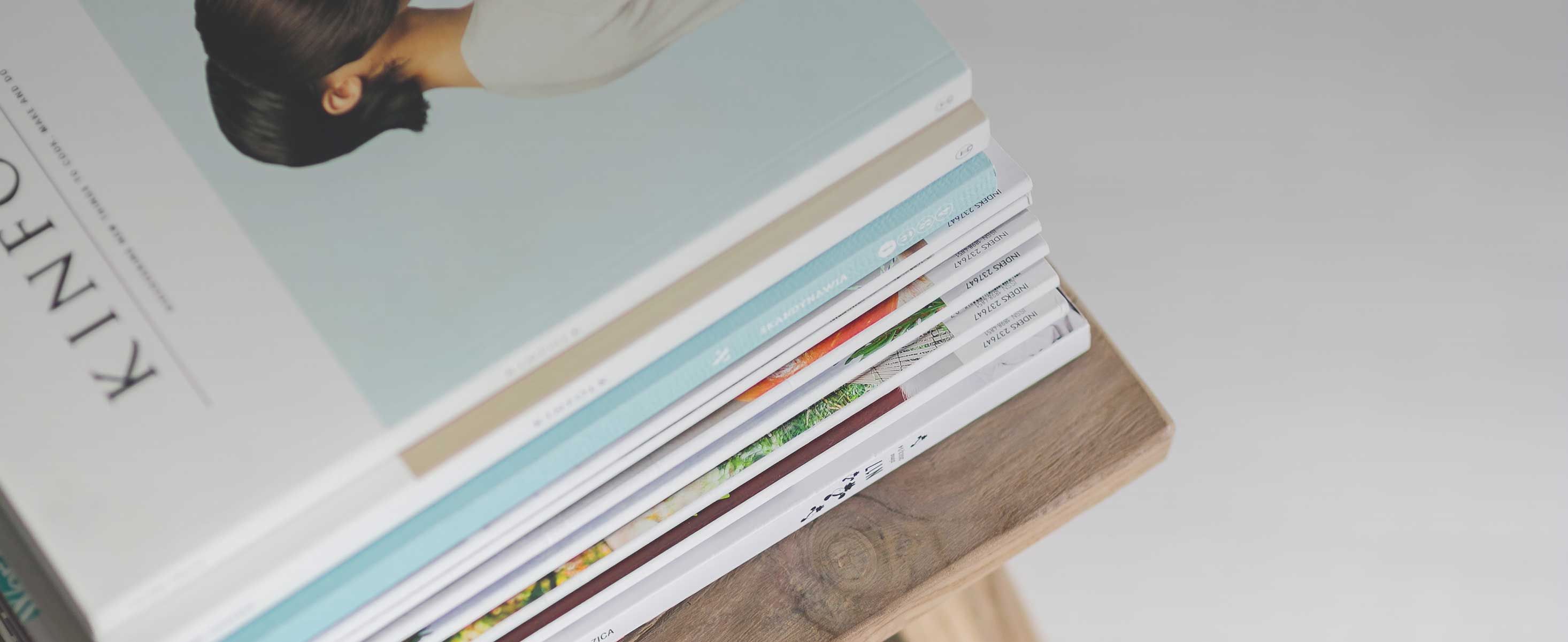
11 minute read
PERSPECTIVE
DIGITAL TWIN IN SUPPLY CHAINS AND WORK CULTURE
A digital twin is a virtual supply chain replica that consists of hundreds of assets, warehouses, logistics and inventory positions. Using advanced analytics and artificial intelligence, the digital twin simulates the supply chain’s performance, including all the complexity that drives value loss and risks. It identifies where volatility and uncertainty exist, as well as where optimization is possible. A digital twin also enables scenario planning to allow a company to make decisions on the basis of business needs, rather than resolving issues as and when they arise. Pandemic has brought great learnings for companies at large in strengthening their supply chain networks and Digital Twin is surely the way forward to thrive in such tumultuous times. The recently held Tattv’21 by SIOM, Nashik presented many such intriguing aspects where leading industry experts shared their learnings and experiences with the audience. This perspective brings out some of the most remarkable thoughts shared during the panel discussion…
Advertisement
Arindam Mukhopadhyay, VP and Global Head of Consulting COE, Gartner Virupakshappa Hovale, Country GM, Bosch Rexroth Piyush Chowhan, Group CIO, LuLu Group International
Pavan Sarda, Associate Director, Supply Excellence, Supply Chain Management, MSD Pharmaceuticals Pvt Ltd.
Can you help us understand what Digital Twin is and how can it help in enhancing supply chain efficiency?
Arindam Mukhopadhyay, VP and Global Head of Consulting COE,
Gartner: A digital supply chain twin is the digital representation of the physical supply chain, which has benefits such as end-to-end planning and execution and visual representation of the real-life supply chain, which helps us in understanding the bottlenecks, planning of time and do scenario planning. Digital Twin technology has gained traction in last few years, and Gartner in a pre-Covid study found that almost 29% of global CEOs are already in the journey of implementing IoT and Digital Twins in their organizations and another 30% CEOs are planning to implement it, which shows the significant business value it can drive.
If we talk about today, the scenario has changed due to two things and I believe we are sitting at the tipping point right now. The first one is the advent of 5G technology, which is going to be an important trigger for digital supply chain to reach to the next level. Second
one is, of course, the pandemic and it has changed the way the supply chain operates and the value proposition for digital supply chain - how technology can make the supply chains more transparent and visible. What we have seen in the past, supply chain design is primarily focused on building efficiency rather than designing for resiliency, but pandemic has shown that an efficient supply chain can often be fragile specially in the events of major disruptions like this pandemic. Therefore, the key lesson learnt during pandemic is, ‘Next generation supply chain is going to be more resilient by building redundancies and ability to monitor end-to-end supply chain digitally.’
How can digital twin improve efficiency?
Virupakshappa Hovale, Country
GM, Bosch Rexroth: Digital twin has moved from product to process set up today. In manufacturing setup, big data handling makes a huge difference. With the evolution of Industry 4.0, data availability and data transparency, we can process large amount of data clubbed with artificial intelligence and different algorithms. The digital twin for the product has evolved to a great extent now. The process must integrate backward and forward. For instance, in a manufacturing setup, there is a CNC machine in the shop floor. Assume the product gets rejected, can the machine decide on its own? No, it cannot decide because right now when you are at a stage of digital twin from a product perspective, the machine as a standalone, cannot take a decision whether to continue to produce or take a cognitive decision should I stop manufacturing now because rest of the periphery does not know what is happening there. So, what will it lead to? It will result in the stoppage of the whole line. We need to avoid that to happen and to do that, we need to bring both product and process as a digital twin where there is a good collaboration. In this way, the digital twin concept makes a big difference in ensuring availability and enhancing the agility of supply chain.
What are the advantages & challenging in implementing digitization? Virupakshappa Hovale: Though we went through disruption by health issue, the whole digital transformation is disruptive right now. Talking about India, we were already on a digital transformation journey in manufacturing. This pandemic made it accelerate further. So, it is a big advantage. Challenge is our readiness to make this happen. Do we have enough resources, technical know-how, implementation plan at the shop floor level in adding the data to the machine, machine to the network, network to the ERP system, ERP system to the interconnected plant? Do I have the scalability and the skill set to make it happen? That continues to be a challenge. Though we talk about multiplatform, multi skillset in India, we still have a long way to go in implementing this change because data plays a highly critical role in digital transformation.
(The comments expressed are of individual assessments and perspectives based on experience and may not reflect as policy guideline from Bosch Rexroth) How do you view rapid digitalization that is happening in the industry and how are we leveraging that?
Pavan Sarda, Associate Director, Supply Excellence, Supply Chain Management, MSD Pharmaceuticals
Pvt Ltd.: Every industry has its own set of supply chain challenges and pharma industry is no exception. The most important thing to highlight is the regulation. We work under strict regulations and on top of that, different countries have different regulations that we have to adhere to. We must keep track of changing regulations across the globe. Accordingly, we must adapt to it. We do not have an option of stockouts. We are in the business of life saving products. So even if there are some products, which are low volume low margin for us, we just cannot afford to be in a stock-out position. We have another problem of shelf life and cost reduction. Even some of our blockbuster medicines can come under drug control anytime, so we must still always look for an option to improve our supply chain. In that sense, we are always looking forward on improving or reshaping our supply chain.
We believe that the supply chain evolution is directly proportional to the technology evolution. Look at it like 20 years or 30 years back or even in 1980s, there was no possibility of having an ERP system because there was no technology to support that. As technology has evolved, we have actually broken that wall between the department, between the organization and that is how the supply chain has been evolving. This rapid digitization or more precisely Industry 4.0 framework is giving us an opportunity and we are very
Despite 2020 being a cash-sensitive year, as per the recent Gartner survey, 39% of manufacturing businesses indicated that they had increased their technology investment beyond pre-COVID budgeted levels. CSCOs must make sure that any investment they are proposing aligns with their CEOs’ critical priorities – growth, financial stability, cost management and risk management. CSCOs must make clear that today’s digital progress secures the options of tomorrow. For example, supply chain organizations with the right digital capabilities can act as the central nervous system of the business that senses risks and opportunities and enables real-time action.
much looking forward to improving our supply chain and address the problems. This pandemic has actually also taught us that our supply chain should not only be able to reduce the cost, but it should be also to reduce the risk now. This is where all the new technologies such as blockchains, IoT, big data and many more have the capabilities to answer all the questions, which we are seeking for. The entire industry has actually made a significant investment into this digital twin concepts or digital digitization is actually very popular since 2017. Having said that, just investing into the technology will not help, we have to start working on evolving our processes and the people around it and the pandemic has definitely given us an opportunity to do that immediately.
Help us understand the scope of digital twin in planning and assessing risk in the pharma supply chain… Pavan Sarda: As far as blockchain is concerned, we are looking for a solution to address the problem of e-leaflet. In pharma industry, we have to put leaflets in every box and that actually also leads to SKU proliferation. This means that we cannot sell the product, which is going from country A to the country B because it has different norms and different products. With the e-leaflet, we are avoiding this SKU proliferation and secondly, we are ensuring that the customer is always getting the up-to-date information by converting this leaflet from paper to the e-leaflets or digital leaflets. Second is counterfeiting. With the track & trace or the serialization requirements from the government, the blockchain is playing a big role for us. We are also working on the pilot projects on implementing the blockchains to address that. We are also looking at testing on importations with a view to reduce the lead time and improving the customer service. In terms of IoT, we are working towards building the control towers along with the different partners to get the real time data with the help of their IoT applications, which can give us the real time data immediately. We are building the visualization as well wherein we can get the visibility into the end-to-end supply chain. Now coming to big data, computational capacity allows us to run thousands and thousands of simulations in a truly short period. So, we could do the risk mitigations immediately by running the simulations and knowing where which part of the supply chain is having risk and immediately, we can take a decision on how to avoid those risks. There are various ways we are currently working on and reducing the risk on our supply chain.
How is the advancement in digital technology enhancing risk mitigation and improving the performance of supply chain? Pavan Sarda: In the year 2016-17, we encountered a major disruption in our supply chain. Even with the technology tools like ERP, it took us almost 2 weeks across the globe to understand the impact on our global supply chain as far as stock-outs are concerned. That triggered the need for real-time data in the value chain, which can help us determine the disruptions in our supply chain. Having implemented single system ERP across our manufacturing sites globally helped us in taking the digital journey forward a decade later. We started with value chain financial modeling. With big data, we are running simulations. We have a global operating model, which helps us in building SOPs for the entire group. Additionally, we are heavily investing on people. We have made training mandatory for people involved in managing supply chains. By investing in technology, we can model our supply chains better, but there’s still long way to go. We have the concept of DATA to DASHBOARD to DECISIONS, which is helping us to mitigate the risk.
What are the best practices for minimizing digital twin project risk? How do we know that any digital twin analysis is complete and comprehensive?
Piyush Chowhan, Group CIO,
LuLu Group International: Being a practitioner, I can see that these are exceedingly difficult concepts to implement. The reason is it has to be done in multiple layers. The first important aspect is how can you democratize and capture use of data. I think developed countries are also struggling as to how to consolidate data across various parts such as a unit of product or process or unit. That kind of digitalization and collection of data is happening but when you try to marry these across, we are still in the journey to derive at the exact solution. Digital twin is not a one size fits all. When the pandemic struck us in the early 2020, we actually had no idea about how the countries would react to it. Some were under the lockdown, some were open. Export imports took a big hit. We had to figure out alternate sourcing locations. If we had digital twin at that point in time, I feel we would be able to easily comprehend the situation and reduce shocks in our supply chains. But for that to happen, I would have to build data platforms, which are so efficient that we are able to replicate that in a simulation or lab environment. To me that realistically for an end-to-end digital supply chain to happen, it’s still about 7-8 years away. I feel that the amount of efforts that is needed to do it is so humongous in my view that it may take much longer than that.
What tools do you use when you go for digital twin strategy? Piyush Chowhan: This is something, which is complementary to digital transformation journey. We should not look at them as a separate initiative, otherwise it will die its own death. To go for digital transformation, I believe in S2A formula – you have to work with SENSORS, you have to work with SOFTWARE and you have to work with ALGORITHMS. These are the three building blocks or broad rules that everybody should be working on. For that to happen, you need to build a connected IoT platform. The real challenge lies in doing things at scale in a very uncontrolled environment and this is where the digitalization will help. Secondly, one needs to implement the new age cloud-based solutions rather than the age-old ERP solutions. The algorithms stage is where the differentiation lies. Have a clear understanding of what you want to achieve. Do not do a digital twin project because your competitors are doing it. This is not going to solve the problem.