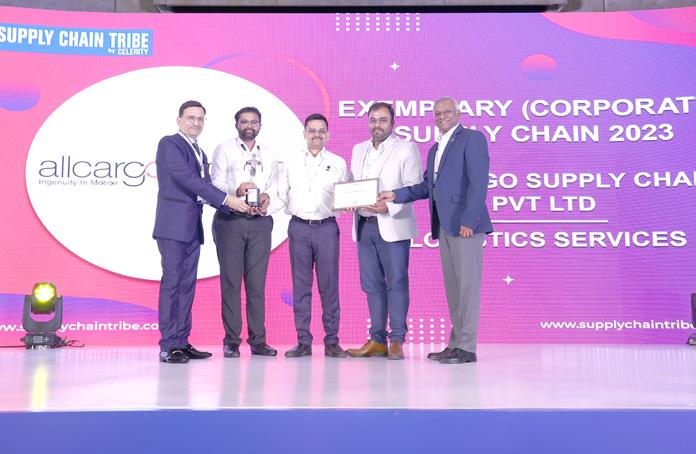
5 minute read
Allcargo Supply Chain Pvt. Ltd.
Driving Value through System Integration
Allcargo Supply Chain Pvt. Ltd. (ASCPL) team had the task of delivering optimization on costs and operations for one of India’s leading chemical manufacturers. They achieved this feat by analysing and increasing efficiency of crucial factors such as manpower, Opex, Capex and transportation network by ably integrating their in-house WMS with the customer’s SAP.
Advertisement
ONE of the biggest challenges of managing such largescale operations is efficient utilization of space and workforce within the warehouse. It requires meticulous planning to avoid any significant chunks of unutilized storage locations and at the same time, allowing ample flexibility to manage volume skewness, both forecasted and the unpredicted. It also includes employing just enough manpower to fulfil everyday KPIs and simultaneously being able to fulfil last minute volume surges. This was the key challenge ASCPL was looking to overcome. The space optimization challenge eventually led to further key operational requirements such as managing material received in mixed batches, allocate space for VAS services such as packing, labelling, stickering, challenges pertaining to manage inward and outward cut-off times, etc. Another key aspect to be looked at from optimization POV was transportation cost and network.
APPROACH & METHODOLOGY
The first step towards an efficient operation is having WMS system that can talk to the customer’s ERP in realtime. Hence, the first step ASCPL team undertook was to introduce reliable in-house WMS software and get that integrated with the customer’s SAP. This resulted in increasing quick and effective decision making by providing realtime inventory visibility to customer, reducing the dependency on Data Entry Operators, faster allocation of orders from receipt to pick list handover. This also helps in accurate location mapping and improving the picking accuracy. WMS enabled operation builds towards 100% accurate error-free picking. In addition, daily transaction and inventory report sharing helps customer plan next day orders and dispatches.
Introducing periodic inventory replenishment and consolidation activity was the next action point that enabled freeing up lots of underutilized operations space within the warehouse. WMS points to different locations which are having same SKU, and batch number products on such pallets is consolidated to eventually reduce the pallet space occupied by same SKUs. This eventually enabled freeing up critical ground space, which was in turn, utilized to conduct the value-added activities.
All these initiatives helped in creating more space inside the warehouse by going vertically high from G+3 to G+5 and G+6 racking heights. This was achieved by analysing the stacking height of similar fast-moving SKUs and clubbing them on same level. This enabled in optimizing the stack height per level and thus increasing the storage G+ levels. The capacity of the warehouse increased from approx. 2000 pallet positions to 5000 pallet positions.
The transportation cost was optimized by introducing dedicated transport coordinators to the warehouse operations’ scope. These coordinators, on daily basis, analysed the delivery locations, weight and expected TAT time and basis this called the transporters to place the required vehicle and ensured they ply on the prescribed route only. This helped in reducing the number of vehicles required and ensured fuel savings.
Outcome
“Using the above-mentioned systematic approach, ASCPL was ablet to deliver the value that customers expect when they align with us for the 3PL operations. We were able to deliver 100% stock accuracy to the customer continuously over a period. We were eventually able to bring down the warehousing and distribution cost of the customer by 28.5% by effectively maintaining the same throughput from the warehouse. At a later stage, we even delivered additional 10% increase in throughput in the same charges. The damages that plagued the operations during VAS activities effectively reduced to NIL. As a special appreciation from the customer, ASCPL team has been awarded by customer as “Best Warehouse Service Provider” measured on Operations, Safety, Sustainability, Social responsibility & Services for continuous two years now,” concluded Anubhav Srivastava, AGM –Business Development, ASCPL.
Ingram Micro
Ensuring Freight Cost saving against Budget
Our last year’s Exemplary Supply Chain winners have once again sustained their winning streak owing to their high innovative quotient and automation deployment. While there have been various success stories that make the company deserving of this accolade, here’s mentioning two of the most striking ones – Freight Cost Optimisation and Pick to Cart automation. Take a look…
FREIGHT is a crucial part of every company’s supply chain management cost. Regular fuel and maintenance cost increase, salary increase, many budgetary pressures in several directions to control freight cost against freight budget 2022-2023, as a company reducing transportation logistics costs has always been the number one priority. Becoming much more flexible and adaptable in transport modes can really help in reducing freight cost. To ensure the same, operations team had taken help of lean initiatives and Kaizen. Ingram Micro team executed various projects to reduce freight cost, some of them are:
• Shipping consolidation of multiple invoices of smaller freight for same customer into single AWB to reduce / avoid minimum freight charges against each invoice.
• Consolidation of Less-than-truckload (LTL) shipment is economical option for smaller weights consignment to FTL modes. Flexibility in choosing correct mode of freight between LTL and FTL modes results in reduction of freight cost.
• Multiple carrier options specialized Lane and geography not only provides better services but also helps in freight cost saving.
• Based on demand & load against each route for city deliveries, the team shifted from monthly fixed freight vehicle charges to Per Kg freight with same service TAT.
• Negotiations with each carrier in terms of controlling freight rates increase or no increase despite fuel rate increases.
All these initiatives not only resulted in improvement of customer deliveries TAT, they also led to freight saving of Rs14.92 million (US$188527) against forecast freight budgets without affecting customer service level.
Automation At Its Best
Besides freight cost optimisation, Ingram Micro also has been laying immense thrust on deploying automation in its processes. For instance, during a normal order picking process, materials need to be picked as per pick ticket where the pickers need to go to the respective bin location mentioned in slip, pick the SKU in the desired quantity and bring the material to the billing station for QA, serial scanning, packaging & Invoicing. The company was facing in terms of higher order processing lead time due to limitation of billing station, ultimately resulting in productivity loss as one picker support was required for scanning against each billing station.
The team came up with Pick to Cart process, which supports Picking & QA and Serial scanning through handheld device directly at stock location, picking process through Cart movement having boxes pasted with LPN Label. With change in process, picker is able to pick the SKU allocated to the cart reflecting at the handled device, performs the quality check like verification of VPN mapped in system with physical VPN on boxes and does the picking of multiple pick tickets at the same time. This process has facilitated them in reducing order process lead time, increased productivity per person, improvement in fill rate in terms of Pick-slip / Cartoon / units per Cart, and there is a clear productivity visibility through Cart management Dashboard.
These initiatives not only resulted in improvement of customer deliveries TAT, they also led to freight saving of Rs14.92 million against forecast freight budgets without affecting customer service level.
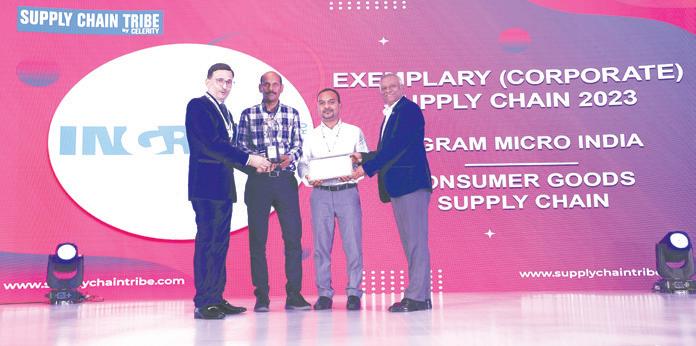