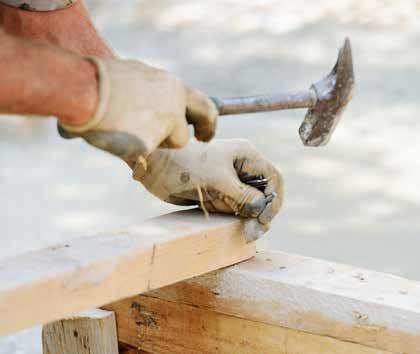
2 minute read
How can we stop hand injuries happening?
A total of 3165 incidents were notified to HazardCo in 2022 – 895 of these were finger and hand related. Given the frequency, we want to look at the impact of these injuries and how to manage them better.
Awareness is everything. You can educate your staff in the following ways:
Advertisement
Any sign of damage/wear and tear, then replace the tool. If it’s bent, don’t bend it back – replace it!
Take your time – ensure you have a firm grip on the tool and check your surroundings.
Use the correct tool for the job.
Think about the potential reaction once an action has been made – if you’re pulling a nog out, how hard do you have to pull/ hit it, do you have a solid footing, what/who is behind you.
Hand placement, hand placement, hand placement! – Ensure your free hand is as far away from the area as possible. It may be needed to hold the item steady, but ensure it is as far away from blades/hammerheads as possible.
The types of injuries
There are a fair few ways these occur on-site. The most common include:
Crushed hands and fingers
Cuts and punctures
Burns Electric shock
The causes are often the result of equipment malfunctions, falling objects, compression between objects, electrical faults, and worker errors.
Hand tools
Hand tools are a huge contributor to hand related injuries in the workplace. When using these common tools, hammers, hand saws, pliers, angle grinders etc fatigue, rushing, complacency, using faulty or damaged tools or a lack of training often leads to workers injuring themselves.
The long-term impact
The long-term impact of a hand injury ranges from minor to severe. A minor injury could mean changes in grip strength and reduced range of motion of the fingers. In more serious cases, a worker may lose the ability to use their hand.
Pre-starts to ensure that the tool is not damaged. If it is, remove it from service and either arrange for it to be repaired, or replaced.
Hold safety demos for all dangerous machinery – some tool suppliers have demo and training courses available.
When holding toolbox meetings, stress hand and finger safety awareness.
Ensure appropriate PPE is worn – gloves, hard hat, etc. This is more than just talking to your workers. As a leader you need to give your workers real-life examples of incidents that have life-changing effects on workers: their health, finances, family and livelihood.
Once workers have the knowledge, it’s up to them to maintain hand safety awareness. Team leaders, however, need to ensure they monitor and review the workplace to ensure controls are in place/being used.
Of course, reach out to HazardCo and speak to one of our expert Health and Safety experts if you have any questions or need more support on hand injuries on-site. HazardCo members get 24/7 incident support, and unlimited expert advice from our advisory team. You can contact us on 0800 555 339.