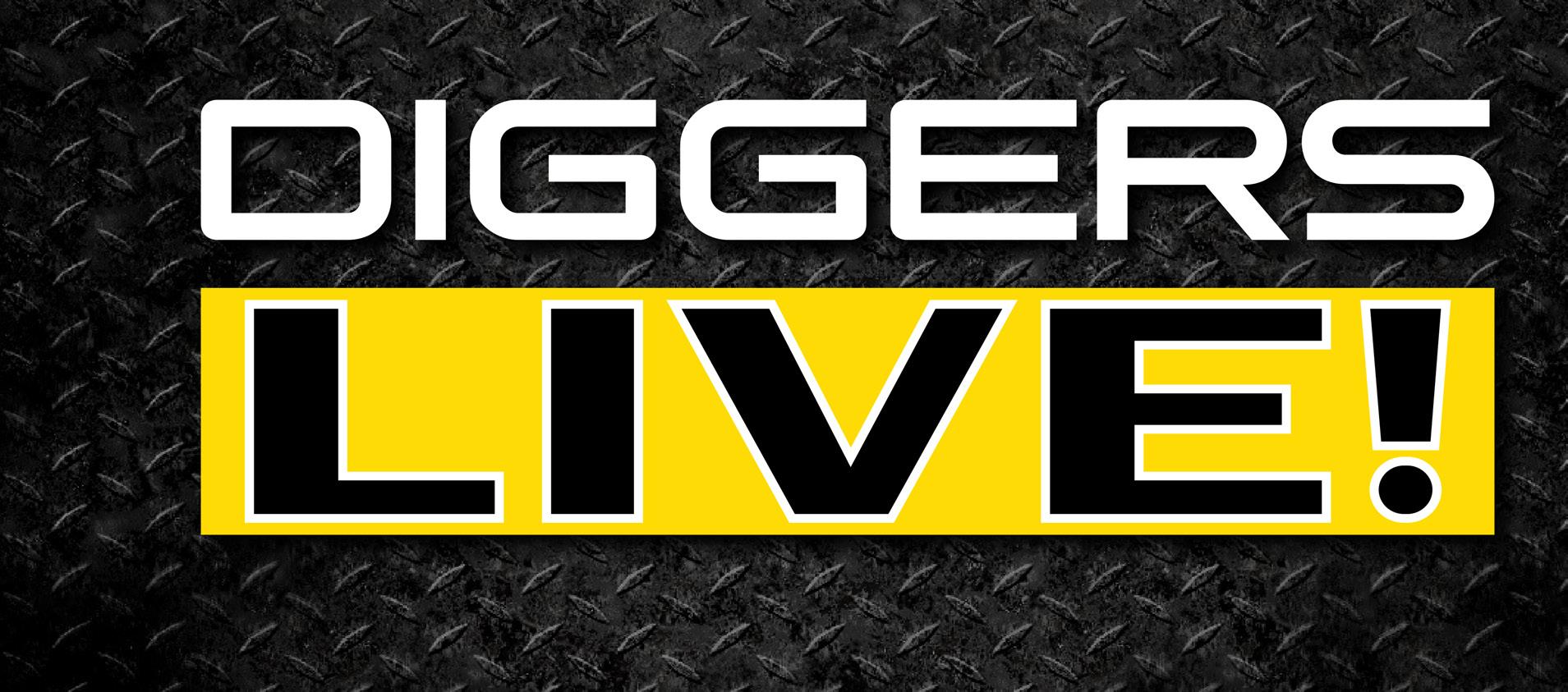





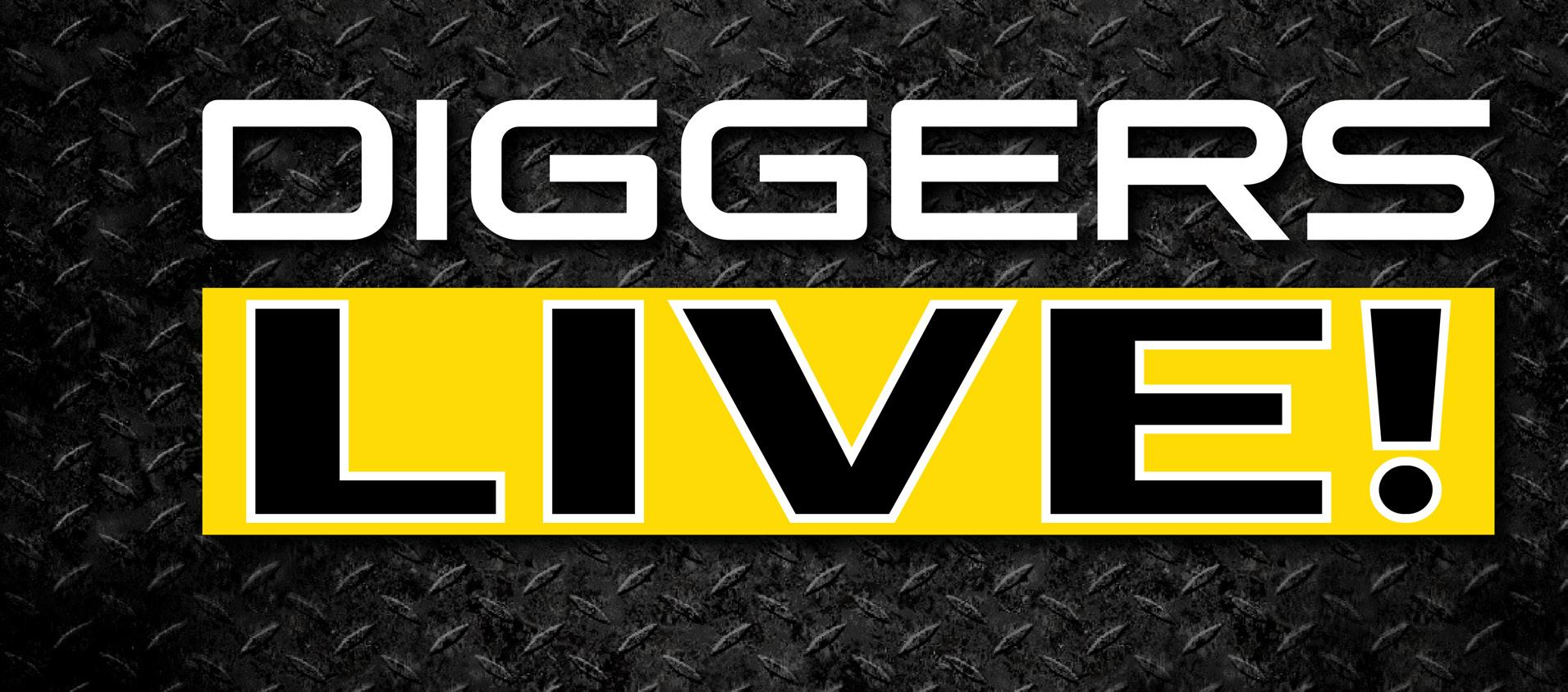
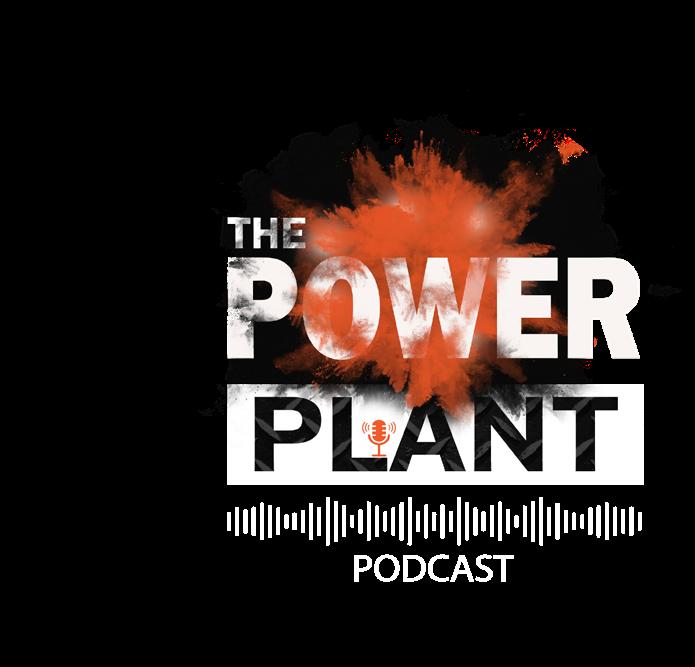
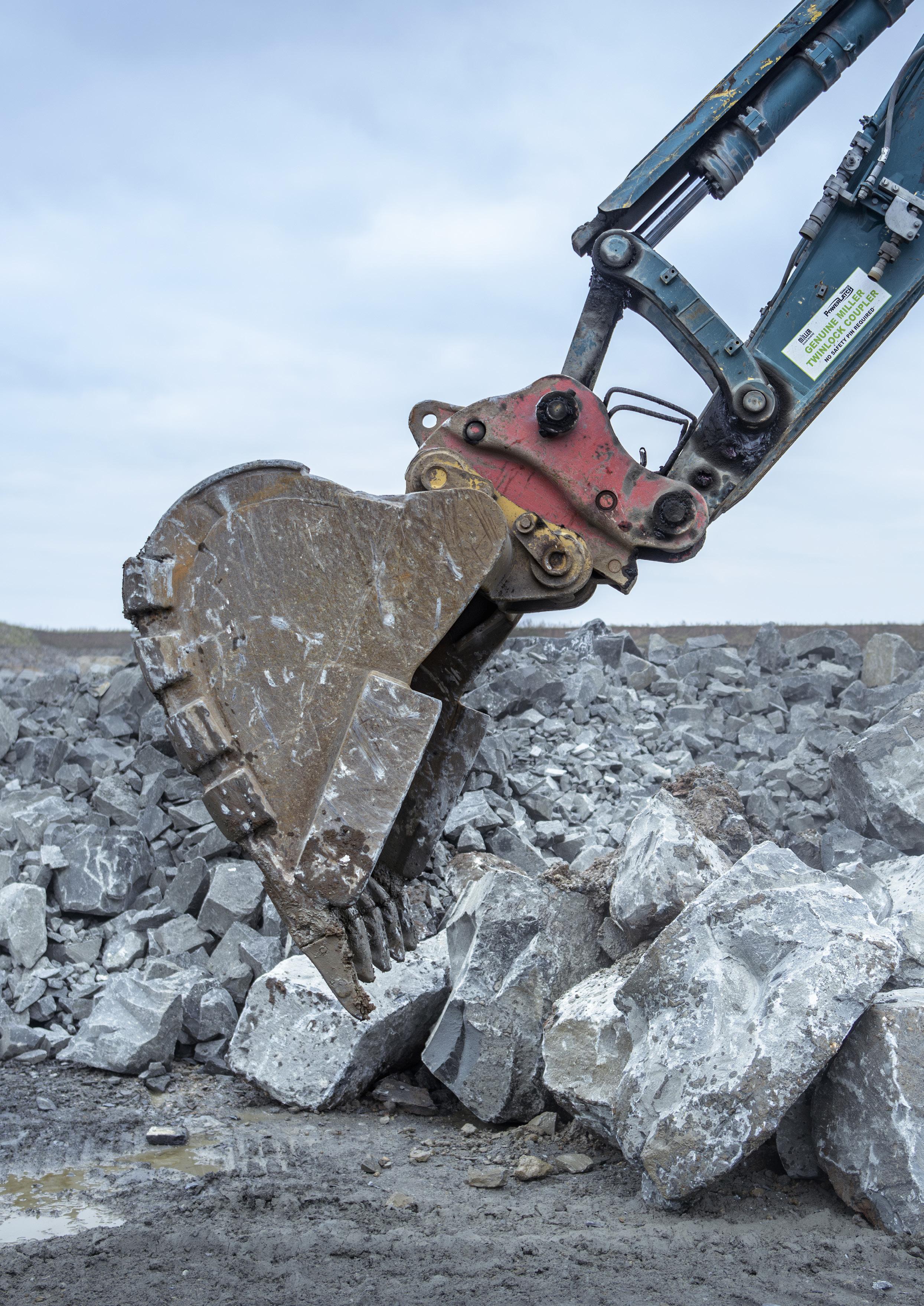
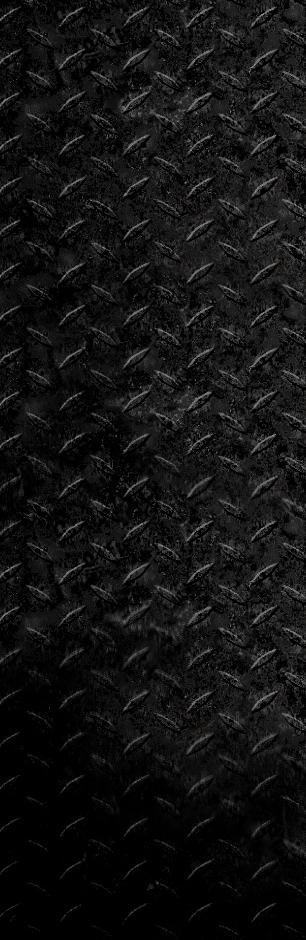
FROM 1.8 TO 95 TONNES THE ALL NEW F-SERIES BREAKS THE MOULD.
Happy new year and welcome to the first issue of 2025 from the team at Diggers LIVE!
2025 is the fifth anniversary year for us and with an output of 27 published bimonthly magazines we launch ourselves into this year at World of Concrete, the 51st staging of the event at the Las Vegas Convention Center, where we really aim to utilise our social media avenues with video bigger and better than ever before. Keep an eye on the socials later on this month.
In 2024 many changes took place globally. Particularly of note to us was the change in government in the UK, the election of the soon to be President across the pond and now Justin Trudeau standing down in Canada. These and many more metrics will make 2025 an interesting year for global manufacture and therefore I wanted to run through the biggest innovations in construction equipment in 2024. Here are some of the most notable trends:
Electric and hybrid machinery: As sustainability takes centre stage, fully electric and hybrid construction machines have gained significant traction. Companies like Volvo and JCB have unveiled new electric excavators and wheel loaders that offer zero-emissions performance, reduced noise pollution and lower operational costs. These machines are especially suited for urban projects with strict environmental regulations.
Autonomous equipment: The rise of autonomous construction equipment has reached a new level. Self-driving bulldozers, excavators and haul trucks now operate more efficiently on job sites. These machines, equipped with GPS, sensors and AI, can perform repetitive tasks with minimal human intervention, increasing productivity and safety.
Telematics and IoT Integration: Telematics systems have become ubiquitous in construction equipment. IoT-enabled machines now provide real-time data on performance, fuel consumption, and maintenance needs. This connectivity allows fleet managers to optimise equipment use, reduce downtime and perform predictive maintenance.
Robotic Automation: Robotic systems have made significant strides in construction, including robotic bricklaying and 3D printing. These innovations reduce labour costs and improve construction speed, particularly in complex or hazardous environments.
These breakthroughs are transforming how construction projects are executed, pushing the industry towards greater efficiency and sustainability.
We wish you a brilliant 2025, you are in safe hands here.
Ben Chambers, Publisher
ENQUIRIES info@chambers.media 01903 952 640
952 648
952 640
2024 YEAR IN REVIEW
The state of the construction equipment industry
With Max Lytle, CEO of FuelActive
Executive Hire Show
World of Concrete Baumag
The UK Concrete Show
Jake Soulsby, General Manager of Mount Machinery Group
• The need to embrace alternative fuel
• Decarbonisation
• Hydrogen infrastructure solutions
• SANY
• Hydrogen fuel cells
• BMC Buckets
• Caterpillar supplied by Finning
• Hardlife Group
• Hill Engineering
• Bucket Design
• Ulrich Attachments
Caterpillar invites world’s most-skilled operators to forge their legacies through third Global Operator Challenge
Specsavers launches stylish new safety eyewear range
Exclusive new Cat® Track Wear Sensor provides remote, no-touch wear monitoring and alerts
Transforming safety and efficiency
Develon and Leica Geosystems Expand 3D Machine Control Options for DD130-7 Dozer
North of England hirer Fairfax takes delivery of 750th Thwaites dumper
Bobcat presents expanded range at Executive Hire Show
The search is on for the UK’s most promising plant apprentices
Rokbak gears up for North American growth at 2025 AED Summit
AUREOS launched as new name and brand for Keltbray Infrastructure Services Limited
by Ben Chambers
As the construction sector faces the twin challenges of increasing demand for infrastructure projects and ever-evolving technology, the construction equipment industry has experienced a year of rapid transformation in 2024. The sector has had to balance heightened market demand, labour shortages, sustainability initiatives and a shifting regulatory environment. These factors, along with innovations in machinery design and smart technology integration, have reshaped the landscape of the global construction equipment market.
In 2024 the construction equipment industry saw a robust recovery, driven by large-scale infrastructure projects, housing developments, and commercial constructions.
The UK saw growth as its construction sector rebounded, bolstered by government-backed initiatives such as HS2 and large urban renewal programmes.
In the United States, the bipartisan infrastructure bill passed in 2021 continued to fuel demand for heavy machinery, particularly for road building and public works projects.
However, this growth was not without its challenges. While demand surged, a lingering shortage of key materials such as steel and semiconductors – fuelled by disruptions from the Covid 19 pandemic and geopolitical tensions – created significant supply chain bottlenecks. Manufacturers were forced to contend with delays in production and escalating costs. Even
as demand outstripped supply, many construction firms found it difficult to secure the necessary machinery on time. Despite these issues, the global construction equipment market is projected to grow at a steady rate in coming years.
One of the most notable developments in the construction equipment industry in 2024 has been the acceleration of technology adoption. The integration of automation, AI, and the Internet of Things (IoT) into construction machinery has drastically transformed how projects are managed and executed.
Autonomous construction equipment, including self-driving bulldozers, excavators and haul trucks, has become increasingly common. These machines use GPS, sensors, and advanced software to carry out repetitive tasks without the need for a human operator, improving safety and productivity.
Companies like Caterpillar, Komatsu
and Volvo CE have been at the forefront of this shift, releasing next-generation machines that incorporate both remote operation capabilities and real-time performance tracking.
The integration of IoT in construction machinery has also led to a boom in telematics and fleet management systems. These innovations enable construction firms to monitor equipment performance, track fuel consumption, schedule maintenance, and optimise machine usage remotely, leading to reduced downtime and cost savings. For example, sensors embedded in construction equipment can now provide detailed diagnostics, predicting when maintenance is needed before a failure occurs.
Additionally, the development of virtual and augmented reality tools for equipment training and project visualisation has taken hold. These technologies have enhanced safety protocols and operational efficiency, allowing workers to simulate hazardous environments and improve their skills without risk.
The focus on sustainability has been one of the defining themes of the construction equipment industry in 2024. As governments and private sector players continue to commit to net-zero goals, manufacturers are increasingly developing greener, more energy-efficient equipment.
Electric construction machinery has seen a breakthrough in 2024, with several manufacturers releasing fully electric and hybrid versions of bulldozers, excavators, and wheel loaders. Companies such as Volvo, JCB, and Liebherr have unveiled new models designed to reduce carbon emissions, noise pollution, and fuel consumption. These machines are particularly wellsuited for use in urban construction projects, where environmental concerns are increasingly at the forefront of planning.
Additionally, alternative fuels such as hydrogen and biofuels have garnered attention in the heavy equipment sector. These fuels offer a way to reduce reliance on diesel and lower emissions while maintaining the power and performance needed for demanding tasks. The adoption of such eco-friendly technologies is expected to accelerate, especially as governments introduce stricter regulations on emissions and sustainability in construction projects.
The construction equipment industry is not immune to the labour shortages that have plagued the broader construction sector. In 2024, the industry continued to face difficulties in recruiting skilled workers, particularly machine operators, technicians, and engineers. The aging workforce and lack of younger talent entering the industry have compounded this issue, leading many companies
to invest heavily in training and development programmes.
The rise of automation has, in some respects, eased the burden on human labour, particularly in tasks that are repetitive or dangerous. However, these technological advancements have also created a need for a new type of workforce – one that is skilled in managing and maintaining advanced machinery. The demand for workers proficient in robotics, AI, and machine learning has skyrocketed, leading to the creation of specialised training programmes and certifications.
Furthermore, with the adoption of remote operation technologies, companies have been able to hire workers in regions where there is less physical infrastructure, creating new opportunities for remote-based operations and digital skills development. This has provided a potential solution to labour shortages while addressing the need for greater efficiency.
Supply chain disruptions: navigating global challenges
Global supply chains continued to face turbulence in 2024, affecting everything from raw material availability to delivery timelines. The construction equipment industry was not immune to these disruptions, particularly regarding the availability of critical components such as semiconductors, steel and rubber. The ongoing geopolitical tensions, supply chain bottlenecks and natural disasters had ripple effects across the industry, causing delays in manufacturing and delivery schedules.
As a result, many construction firms and equipment rental companies turned to alternative suppliers and diversified their procurement strategies to mitigate risks. Manufacturers, in turn, are investing in localised production and assembly to reduce their dependence on global supply chains and ensure they can meet demand in a timely manner. This diversification of supply sources is expected to continue in the coming years as companies seek to create more resilient and agile supply networks.
As the industry looks ahead to the next decade, digital transformation and AI integration are poised to continue reshaping the landscape. The next wave of construction machinery is expected to feature even more advanced AIdriven capabilities, including predictive analytics for performance optimisation, enhanced machine learning algorithms for improving operational efficiency, and deeper integration with project management software.
The trend toward fully connected construction sites is expected to accelerate, with machines, materials, and workers all communicating in real-time to streamline operations. This “smart construction” ecosystem will not only enhance efficiency but also improve safety by providing managers with real-time data on site conditions, equipment health, and worker performance.
Additionally, the increased focus on circular economy principles will drive
innovation in equipment design and lifecycle management. Manufacturers are expected to explore new ways to extend the life of machinery through refurbishment, repurposing and recycling, reducing the environmental impact of construction projects.
In conclusion, 2024 has been a year of adaptation, growth, and innovation for the construction equipment industry. While challenges such as supply chain disruptions and labour shortages continue to test the resilience of the market, technological advancements and a strong focus on sustainability have provided both solutions and opportunities.
As the industry embraces digitalisation, automation and greener practices, it is well on its way to shaping the future of construction. The coming years will likely bring even more exciting developments as the sector continues to evolve and adapt to the changing demands of a dynamic global marketplace.
FuelActive offers a patented floating fuel pickup system for diesel tanks that draws fuel from the top of the fuel level, reducing water contamination and improving engine efficiency. This leads to a 3-5% fuel saving and corresponding CO2 emissions reduction, with a payback period of less than a year. The company has grown 70% year-on-year since Covid and operates in various sectors including construction plant. Toby Wilsdon spoke to CEO Max Lytle to find out more.
Interviewee: Max Lytle
Role: CEO
Company: FuelActive
Toby Wilsdon
Tell us about FuelActive and its offering
Max Lytle
So FuelActive is a floating fuel pickup system, and what differentiates it is that it’s globally patented, so it is the only one of its type.
In standard diesel tanks there is a tube or pipe at the bottom drawing fuel into the engine. FuelActive has a floating pickup that sits at the top of the fuel level. The difference in the quality of fuel is substantial because diesel or biofuel (which is also hygroscopic) carries an element of water, that separates out (free water). Water’s about 20% heavier than diesel, so it sits at the bottom of the tank and with a standard pickup it’s always drawn into the fuel line.
Some filters and water separators can remove an element of that water, but some of the contamination will get to sensitive engine components. As we’ve gone through the tiered engine progression up to Euro 6, or Stage V for construction equipment, the injectors are
incredibly sensitive and manufacturers are putting on very high levels of filtration. So what we’re seeing is filters don’t get to their service life. But even if they do, the sensitive engine, the sensitive injectors are degrading. If they degrade the efficiency of the engine is not what it should be.
Really, all FuelActive is doing is serving the cleanest possible fuel to sensitive engine components, protecting them to the OEM standard. That protects your fuel consumption, which has a direct correlation to sustainability. Every litre of diesel you save is 2.62 kg of CO2.
Most of our customers fit FuelActive to protect their engines, so they get guaranteed uptime. They get a fuel
“Really, all FuelActive is doing is serving the cleanest possible fuel to sensitive engine components”
economy saving of between 3 and 5% in the UK, which is a financial benefit to a company, but it will also be a 3 to 5% saving of CO2. Most customers advertise the sustainability credentials of FuelActive.
How about the history of the company and the product?
The company has actually been around for a long time. The product was designed by our chief engineer in the early 2000s and he worked hard at trying to market the product, but I think it would be fair to say that while he invented an extremely clever product, we struggled to scale the product. Just before Covid we received some investment from a private equity group. That allowed the company to bring in a professional sector-based sales team. So we now operate in mining, rail, construction, transport, power generation; those are our main sectors. We have individuals who have worked in those sectors so they can speak the specific language, understand the market and the customer. That has allowed the business to grow approximately 70% year on year for the last three years.
That’s just the start for us.
The floating fuel pickup is the core product, but what our design and engineering teams are working at is taking the concept and making it appropriate for all those sectors. You’ll appreciate the difference between a 400-tonne haul truck and a three-tonne mini excavator. The challenges are very different. We have over 100 products, but the basic premise of a floating fuel pickup is the constant that sits within them.
TW
Had there been any floating fuel pickups before?
Not that we’ve ever experienced. The closest we’ve come to finding something similar is in wine, drawing off the clean wine and leaving the dregs at the bottom.
The reality is since the invention of the diesel engine in 1897 the tank has been abandoned by everybody. It is the thing people think of last in the design process.
There is huge consideration of the latest engine technology, hydraulics, gearboxes, transmissions, everything you would think engineers are engaged with, but no one thinks about the tank. It’s a dumb box, and increasingly, it’s a plastic injection-moulded box, but no one has considered how to revolutionise
the delivery of fuel into an engine. They just put more filters on, more water separators.
If you can start the process by sending clean fuel to those components, they last longer, and they operate better.
TW
You were saying the business structure has been very important to the success.
Mike James, our Chief Engineer, invented the product for a friend who worked in diesel water pumps but lost a very important contract because he suffered from water in diesel. And Mike said there must be a solution, but he found there wasn’t. He came up with the idea and solved that. That customer was Hydrainer, they’re still our customer 20 years later.
But taking that value proposition is sometimes a question of commercialisation. Do you know the right people? It’s also a matter of time and place, because we now can prove categorically that FuelActive provides customers with a fuel economy benefit. It also may be a question of timing, because we’re sitting in the market across a number of sectors, it’s a necessity for transition technology. So if they switch to full electric or full hydrogen, or whatever the green the total green solution is,
it is complicated and expensive, and an infrastructure may not be viable at the moment, and therefore relatively modest incremental gains on the road to Net Zero is a much more focused discussion, I would say, today, than it was three years ago.
Timing may also be playing into our hands. I’ve spoken to the Head of Engines at a very senior OEM and he said they believe that there will still be a necessity for diesel engines beyond 2050, and therefore people are looking for these incremental savings across transport, power, rail, mining. A 5% fuel saving – and therefore CO2 saving – is a really significant step forwards for the sustainability and innovation teams that most of these large organisations run. That’s what we’re able to deliver.
Going back a few years, red diesel provided very few challenges for customers with unsophisticated engines, but as we’ve gone for cleaner diesel – B7, B10, HVO – some of these fuels present engines with a number of challenges. They cure quicker, they go off quicker, they can carry more water into the diesel tank even before the buildup of condensation inside the tank.
So some more environmentally friendly fuels have presented engine manufacturers with greater challenges for their sensitive components, which helps the value proposition of FuelActive.
So for the readers of Diggers LIVE!, the heavy plant operators, how do they get their product?
If you have anything between a 10 and 30 tonne excavator or more, FuelActive has a product that could be installed less than an hour. It is a one-time fit and forget unit. There is no additional service or maintenance required.
Based on fuel economy alone, it will have a payback of less than a year. If customers are also faced with the challenges of early filter changes, or they suffered from injector failures as a result of their day-to-day operations, we would also protect against that and there’s evidence behind it.
One of the challenges we have in the excavator market is proving the future economy saving, because it is very difficult to build a control group of excavators that have the same duty cycle over a protracted period of time. You can have 10 excavators on a site and not one will be doing the same job. This is why we focus on Haul Trucks and ADTs.
The reason I can tell you categorically it works is that in mining, a 400-tonne haul truck produces hundreds of data points on one journey. Precise engine and OEM telematics provide huge volumes of load, distance, fuel economy data – we’ve
got the exact weight, we’ve got the exact journey, we’ve got the exact speed, and we can break that journey up into various different segments. And when you compare those across a mine of 60 haul trucks, half of which are fitted with FuelActive, you begin to have enough suitable data to prove these things categorically. We have proved a minimum of 3.65% fuel economy saving on ADTs with a tier one tier one rental company in the UK. Overseas with market-leading mining companies the savings are closer to 5%.
ADTs have that ability to run the same cycle. Excavators don’t, but we have a number of customers in the UK who have also reported a fuel saving and better protection from contaminated fuel.
TW
So on fuel consumption, it would be a year, and then on total cost of ownership, better than that.
ML
Customers are able to report the CO2 benefit in their sustainability reports and people are now putting it into tenders and contracts as well. People acknowledge the effort made towards achieving sustainability goals as part of the tender process and the contract process.
We’ve worked with Colas rail, who are responsible for about 40% of the UK’s maintenance and they work very closely with Network Rail. They’re seeing between 4 and 7% fuel economy saving and they’ve published today that they’ve been selected for an eight-year contract for rail maintenance. Some of that submission was focused on Colas Rail’s commitment to sustainability and innovation.
The value proposition of FuelActive goes up depending on the harshness of the environment in which machines operate. In an African mine there are some really challenging factors, not least the quality of the fuel, but also airborne dust and particles. And we know from working in a number of waste and recycling applications, those are pretty challenging as well and the latest technology provided by manufacturers doesn’t necessarily align with them. Some machines can struggle in those environments, so that is a particularly good fit for FuelActive.
T W
Tell a us little more about the company and the team
M L
The business currently has 19 employees, split into two groups. Primarily, we have
“There is NO additional service or maintenance required. Based on fuel economy alone, it will have a payback of less than a year”
a field service engineering team and a design team, which is constantly coming up with new and innovative, easy to install methods for all the sectors.
And then we have a sector sales and commercial team. It’s a very flat organisation. We don’t need multiple layers of management. We’re beginning to build a network of trusted distributors but FuelActive itself can remain relatively small so long as we maintain the excellence of our team.
So the team of 19 includes manufacturing?
We maintain our own manufacturing capability for R&D and Test and valuation small production runs. We also have some UK based external manufacturers for volume orders, because the magic of FuelActive is in its design team, its patent and the ability to sell into the sectors.
I don’t believe manufacturing is something we need to keep in house. As we grow overseas (quite aggressively at the moment), it’s likely there will be a necessity to build locally to those customers. There are commercial benefits, avoiding tariffs for example, but a lot of consumers just want to buy product that has been built in their own country.
TW
Is it fair to say, it’s quite a simple product or idea?
M L
It’s very simple, Toby. A lot of our customers say that to us when we demonstrate it and I take that as a badge of honour. We always almost receive the same feedback. “Why has no one ever thought of this before?” We’re lucky, because Mike James did and then we protected that idea with our patents.
TW
What’s it like working at working at FuelActive?
ML
It’s great. FuelActive is fundamentally a start-up business. It should be viewed in that context. What I particularly enjoy is that as a small organisation, we can be agile, make decisions and implement them very quickly. We’re able to respond to the needs of our customers and help solve their challenges.
The reality is that large organisations are naturally more bureaucratic by nature and I enjoy smaller scale, more dynamic businesses. And that’s what drew me to FuelActive.
TW
How did you come to where you are now?
ML
I spent 20 years as a helicopter pilot and an officer in the British Army, and then I took a job at JCB, and worked for them for seven years in a number of roles. The two key roles for me were running global major accounts. Then I took responsibility for running Asia, living in Singapore. I was Managing Director of Southeast Asia and that was fantastic. But when Covid struck it was clear that there were going to be challenges in Asia, so I brought my family home, at which stage I received an opportunity to join FuelActive.
I looked at the product during the interview process and as I drove home my mind was spinning on all the opportunities and I thought it was everything that I wanted – a British company with a superb product that had an environmental benefit, to which I thought I could add value.
TW
How much of what you do is down to transferable skills in running a business, and how much is down to your sector knowledge?
M L
I absolutely subscribe to the view that if you get the right people who have the right emotional intelligence, particularly with a commercial side, then you can pick up the language of various
“If you have anything between a 10 and 30 tonne excavator or more, FuelActive has a product that could be installed less than an hour. It is a one-time fit and forget unit”
sectors. For the most part, we’ve recruited people who have the right fundamental qualities and then assigned the sectors to them.
I don’t think you want to go too specific in terms of that and certainly for myself, while I have an understanding of construction equipment, I think it’s more of a fundamental understanding of engines and design. Being sat underneath an engine in a helicopter for 20 years has certainly been as useful to me as anything. But it’s more to do with understanding people and trying to grow the business that way.
Turning to the future, is there scope for diversifying FuelActive?
We take a lot of feedback from customers about other things they would like to do. We’re exploring bulk tank solutions. We’re exploring AdBlue warning in fuel detection. We’re also exploring fuel active solutions that are seamless in terms of their integration into the tank, so they can be fitted using almost OEM components, or certainly some of the access holes that are provided by OEM.
There are different aspects that our R&D team are working on. We continue to look at different sectors. Given my own background, I’m convinced there’s a good fit for the military. I know the procurement cycle in the military takes a very long time, so we have to be patient for that.
Everywhere there is a diesel engine, there is an opportunity for FuelActive, possibly with the exception of the automobile industry, because there’s not the return on investment and access to the tank within the car is incredibly complex.
TW
Where do you see the company in five years?
M L
We’ve just completed an investment round. We’ve got some very exciting opportunities with new investors who are well connected in the market globally and that should help propel us forward. But we’re also on the verge of being able to announce at least three testimonials from customers who are market leaders in their sectors. That will help make FuelActive less of an industry secret.
T W
if you try to switch to electric tomorrow you blow the London grid. There’s just not enough power and that’s before you consider the fact that you’re looking at a jump from about £150,000 to around £400,000. Who’s bearing the cost for that increment? The supermarket can’t, so it’s passed to the consumer.
And you’re in it for the long term?
M L
Absolutely. I love it. There’s a great team of people that I work with and everybody shares the same passion for the company, wants to see it grow and a brilliant idea from our inventor, Mike James, turn into something that everyone has access to. I believe it has this place, until true green is available for everybody I think we’ve all got to do something in terms of smoothing the transition into true green, and FuelActive can be part of that.
TW
And there’s a good few years to go in that respect.
ML
Some of the deadlines look quite challenging for a number of reasons. The power required to electrify a fleet of 1,000 HGVs, as well as the expense, is of a scale that few people have really
The acid test for all of us is, how much appetite do we have if it comes with that sort of cost increment? So we need to work hard on the cost. We need to work hard on the infrastructure and in the interim we need to look at incremental savings.
M L
We’re based just outside Cardiff and it’s a super place to be. We’re really well supported by the Welsh government. They’ve really helped us with some of our growth and continue to do so. We’ve received a number of Innovate UK grants as well to help with our product design and development.
We’re at a really exciting stage where we’ll be able to publish some very exciting results very soon. In January 2025 I’d expect to be able to announce results from a top five rental company in the UK proving the fuel savings and CO2 savings we’ve been talking about.
Dates:
Wednesday 12 - Thursday 13 February 2025
Opening hours:
Wednesday 9am to 5pm; Thursday 9am to 4pm
Venue:
Coventry Building Society Arena www.executivehireshow.co.uk
On Wednesday 12 and Thursday 13 February 2025, the CBS Arena in Coventry will transform into the centre of the tools, plant, and equipment hire industry. With every one of the 145 stands booked, the event promises two unmissable days of inspiration, innovation, and connection.
The show is a trade-only event open to hire executives throughout the UK and Ireland and it has also attracted hire industry visitors from Europe and beyond. Senior executives from the procurement and purchasing departments of the national hire operations attend the show, along with large numbers of independently owned entrepreneurial hire outlets. At the 2024 show, 86% of visitors were from independent hire companies.
Who is exhibiting?
For manufacturers, suppliers, dealers or importers of tools, equipment and plant looking to target the
hire industry, there is no better opportunity to promote their products and services to this vitally important market.
For the full list of exhibitors, go to www.executivehireshow.co.uk/ visiting/2025-exhibitor-list.
Where is the venue?
The popular Coventry Building Society Arena is located at the heart of the UK motorway network and is within two hours’ drive of 75% of England. The Coventry Building Society Arena is justifiably proud of its new tag as the “Home of Hire”. Visit www.executivehireshow.co.uk now to register for fast-track entry and start planning your visit with the online floor plan Executive Hire Show 2025 Registration. Both registration and attendance are free. With just two days to experience the best in hire, early registration guarantees visitors more time on the show floor to secure the best in ‘show deals’.
“There’s only one place you’ll find the heavy hitters of concrete and masonry this January”
Dates:
Exhibits: Tuesday 21 – Thursday 23 January
Education: Monday 20 – Thursday 23 January
Venue: Las Vegas Convention Center, Las Vegas, USA
Opening hours: Daily from 9:30am to 5pm
www.worldofconcrete.com
There’s only one place you’ll find the heavy hitters of concrete and masonry this January: Vegas, baby – at World of Concrete 2025, the largest and only annual international event dedicated to the commercial concrete and masonry construction industries. Get your hands on the latest technologies revolutionising safety, performance and speed and learn what it takes to not only claim a piece of our industry’s massive projected growth but dominate the field.
World of Concrete has been serving the global concrete and masonry construction industries for more than 50 years. It connects and educates buyers and sellers through live and digital events throughout the year, facilitated via worldofconcrete.com, and WOC360. Its goal is to provide this important community with the connections, intelligence and opportunities that help customers grow, do business and make better informed business decisions
The 2025 World of Concrete Education Program will offer more than 180 sessions of solid, in-depth learning options for every concrete/ masonry professional including technical applications, business best practices, project management and safetyrelevant topics for every skill level from beginner to experienced, every level of responsibility from office and field personnel to business owners. Over
40% of our educational offerings will be brand new for 2025. We’re also pleased to bring back several of our most popular technical seminar series, industry certifications, sessions for emerging leaders, interactive workshops, and industry training courses/forums, plus a full track presented in Spanish!
Please be advised, there is no on-site registration. You must register online before coming to the show to receive your printed badge on site.
Dates: Thursday 23 – Sunday 26 January
Venue: Messe Luzern, 6005 Lucerne, Switzerland
Opening hours: Daily from 9am to 5pm
www.baumaschinen-messe.ch
Experts and decision-makers from the construction and ancillary industries can look forward to the premier Swiss construction machinery trade fair, Baumag 2025, from 23 – 26 January in Lucerne.
Over the four days the trade fair becomes a showcase for the construction industry and presents the approximately 18,000 visitors to the modern Lucerne exhibition centre with a concentration of innovative power.
Digitalisation and the shift from fossil to renewable energy sources are important topics at Baumag 2025. Automation of construction processes using construction software, flexible and functional excavator controls, electric construction machines with zero emissions and low noise, surveying with drones and self-sufficient
and environmentally friendly storage systems are just a few examples.
Preparations are in full swing and the anticipation is clearly evident in Exhibition Director Andreas Hauenstein: “The exhibition is once again fully booked. We are very proud of that. This shows that Baumag is the most important Swiss sales, presentation and communication platform for the industry and a guarantee for sustainable customer contacts.
“The unbeatable added value of the exhibition is the personal exchange in a harmonious environment and nowhere else works better. The positive atmosphere and the high level of visitor interest always make it clear that Baumag is an indispensable meeting place for the construction industry.”
“The unbeatable added value of the exhibition is the personal exchange in a harmonious environment and nowhere else works better”
ELECTRIC
KHD Brokk Hire is the ‘one stop shop’ for all things electric plant, with a sustainable twist too! From electric diggers & dumpers to Brokk machines – we do it all! WE OFFER:
Dates: Wednesday 26 – Thursday 27 February
Venue: The NEC, Birmingham
Opening hours: Wednesday 9am to 5pm; Thursday 9am to 4pm
www.concreteshow.co.uk
Visit The UK Concrete Show, taking place from 26 – 27 February 2025 at the NEC Birmingham. There’s something for everyone at the show, from civils, to groundworks, ready mix, volumetric operators, block manufacturing, precast, batching plant operators and more.
Exhibitors will showcase the latest launches and innovative technology from the sector. Tools, equipment, and services to improve your business’s productivity and keep ahead of the competition. From admixtures and beautiful concrete to pumps and volumetric trucks, The UK Concrete Show is guaranteed to provide something new that your business will profit from for years to come.
Whether you’re a supplier and have noticed one of your customers performing above and beyond, or if you have a younger member of your own team who is starting out positively in their career, you may wish to put them forward for one our Emerging Talent Awards.
Concrete is a broad church, so job roles vary including site managers, concrete polishing contractors, volumetric truck and mixer operators, batchers, sales and marketing roles, floor screeding, junior civil engineers and many more.
All winners will receive a £500 John Lewis voucher at the show on Thursday 27 February.
Visit the new “Find Your Community” area – the go-to hub for industry connections and support. This dedicated space showcases our partner organisations, each offering valuable insights, expert advice, and tailored guidance to attendees. It’s an excellent opportunity to explore the advantages of joining these organisations, from professional development and networking, to exclusive resources and industry updates. Whether you’re seeking collaboration, career growth, or simply want to stay informed about the latest in concrete innovation, the Find Your Community area is the perfect place to connect, explore professional opportunities and strengthen your ties within the concrete industry.
“The UK Concrete Show is guaranteed to provide something new that your business will profit from for years to come”
Interviewee:
Jake Soulsby
Role: General Manager
Company: Mount Machinery Group
Fleet size: More than 100 excavator attachments
Brands: Mount Machinery, Steelwrist
Tell us a little about the background and current circumstances of Mount Machinery
Mount Machinery is a family run business based in Leeds since 1994, delivering excavator attachment sales, short and long-term hires and repair services. We are committed to a simple, honest, quality service delivered on time.
Which sectors do you predominantly supply?
The construction, demolition, plant hire, quarrying, remediation, recycling, utility, civil engineering and groundwork industries.
What is the scope of your hire offer?
We offer the following attachments for excavators from 1 to 50 tonnes:
• Hydraulic breakers
• Crusher buckets
• Screening buckets
• Dedicated shears
• Hydraulic pulverisers
• Concrete cutters
• Compactor plates
• Selector grabs
• Augers
• Pallet forks
• Riddle buckets
• Ripper teeth
• Thumb buckets
• Land rakes
• Rock grabs
• Tilting buckets
What is your geographical reach?
Being centrally located in the UK, Mount Machinery covers from the Scottish Borders to the Midlands and from the Wash to the Wiral. We also have strong relationships with Cross Hire Partners and have delivered buckets to Bristol and crusher buckets to London.
What are your most popular products?
Rock breakers, crusher buckets and augers
What is the average age of your machines?
Mount Machinery is committed to providing some of the newest excavator attachments to our customers. In 2024 we’ve spent more than £150,000 upgrading the hire fleet, with a target of replacing each piece of equipment every three years.
Our Mount Machinery Brands are built to test the test of time. One of our customers bought a breaker in 2010 still has it on their hire fleet 14 years later.
Do you have any preferred manufacturers or brands?
We favour our own Mount Machinery brand, known for durability and performance. Our focus is on quality, low maintenance and strong aftermarket support, all of which enable us to maintain high availability and quick servicing.
What is your service offering?
We have a fully equipped workshop and
can repair most makes and models of attachments fast. Our team at Mount Machinery is fast paced and dynamic. Most of our hires are delivered the same day. We emphasise flexibility and quick replacement in the case of malfunctions, prioritising uptime for our client.
What are your thoughts on the hire market and the needs of contractors? Where does hire stand in relationship to ownership? The hire market has been expanding as contractors seek flexibility and avoid the upfront costs of ownership. We’re observing an increasing preference for hire solutions driven by the need for cost efficiency and evolving project requirements.
Do you have any expansion plans?
In 2025 we are introducing temporary fences and crowd barriers, muck tipping skips and concrete pouring buckets into our fleet and have an expansion target of four depots by 2030.
Why HVO is the alternative fuel that the construction industry needs to embrace
by Ollie Bradshaw, Sustainability Manager at Certas Energy
The construction industry is one of the United Kingdom’s major emitting sectors. Accounting for roughly 2.5% of the country’s total carbon emissions, it heavily contributes to the emissions related to our built environment (residential and commercial). According to the government’s data, the built environment is responsible for around one quarter of the UK’s total emissions. This means that embracing alternative and more sustainable fuels is essential to the country’s efforts to meet its ambitious net zero targets.
We can expect government regulations to further tighten, so embracing new methods and solutions needs to be highup on the agenda for leaders across the construction industry.
The sector is currently under pressure to move away from petroleum diesel and to support the transition to lower emissions. One alternative power source the sector is increasingly embracing for Non-Road Mobile Machinery (NRMM) like dump trucks, excavators and generators, which ran on red diesel until the repeal of the government rebates in 2022 and then on white diesel, is Hydrotreated Vegetable Oil (HVO).
HVO is a liquid renewable alternative to diesel composed of hydrocarbon molecules with a chemical structure and energy density similar to fossil diesel. It is a drop-in solution that does not require alternative infrastructure and can be mixed with white diesel during the transition, blending the two.
The market has shown robust growth in the past year, with the total volume doubling from 262 million litres to roughly 523 million litres. We anticipate growing demand for HVO for at least the next 10 to 15 years.
For construction companies that are apprehensive about switching from white diesel to biofuels, understanding which sustainable options will work for their plant will be crucial in making the transition to an alternative power source like HVO confidently.
As the UK’s leading supplier of HVO, Certas Energy is spearheading the transition from diesel to this biofuel to facilitate the journey towards net zero emissions.
How HVO compares to other alternative fuels
Gas-to-Liquid (GTF) Fuel is a FAME-
free alternative to regular diesel which, like HVO, is a drop in fuel that can instantly reduce some harmful emissions. However, GTF does not lower lifecycle GHG emissions, making HVO more suited to businesses looking to reduce their carbon footprint.
Compressed natural gas can reduce carbon dioxide emissions by up to 25% and nitrogen oxide up to 80%. New tanks are required for this fuel which can be a costly transition, whereas HVO can be dropped into current infrastructure.
Liquified natural gas is another alternative fuel made from gas cooled to liquid form. This is a safer alternative to pressurised gases and popular in the marine sector. However, it is a lower energy density fuel and does not deliver the same efficiency benefits as HVO.
FAME, or biodiesel, is made from vegetable oils, animal fats or recycled greases. Whilst this biodegradable fuel can reduce emissions, there are maintenance issues such as clogged filters which can impact machinery and vehicle downtime. HVO is practically FAMEfree, meaning it does not experience the same operational difficulties.
Why use HVO on your next project?
Manufactured from 100% renewable raw materials and sustainable waste, HVO produces 90% fewer carbon emissions than traditional options.
HVO can be dropped straight into any engine currently running on diesel, making the transition seamless, and the environmental benefits immediate, meaning it is a simple switch.
The alternative fuel produces fewer residues and lower particulate emissions because of its a higher cetane number. This makes for more efficient combustion, which not only reduces pollution to the atmosphere but extends the lifespan of diesel particulate filters.
Virtually free from aromatics, metals and sulphur content, HVO can improve the cleanliness and efficiency of engines, reducing the need to renew or repair and cutting maintenance costs.
HVO also has a shelf life of up to ten years, which is beneficial for long-term storage when working on longer projects.
In comparison to standard diesel, which has a shelf-life of six to 12 months, HVO allows for planning projects far in advance and enabling work to continue without the risk of interruption. The
www.certasenergy.co.uk
nationalaccounts@certasenergy.co.uk
0345 600 4040
biofuel is ideal for winter conditions, withstanding temperatures as low as -30C.
As the country continues to make progress to net zero by 2050, the construction industry now faces a critical juncture. Adopting alternative fuels such as HVO aligns with supply chain decarbonisation objectives and presents businesses with an immediate way to minimise their carbon footprint, reduce operating costs and prepare for a sustainable future.
By embracing short and mediumterm solutions like HVO promptly, construction firms will be able to play a crucial role in shaping a more sustainable, decarbonised industry.
by Luis Bassett,
Construction plant-hire is an exceptionally difficult sector to decarbonise. It includes powerful machinery with challenging duty cycles operating on sites that have minimal existing infrastructure, if any.
Machines are often designed to be a particular size, weight, reach or work in particular environments, such as on rail. For some tasks it is already challenging to get hold of a machine with the right specifications, even without restricting yourself to hybrid, Stage V, hydrogen or fully electric models.
Commercial road fleets are moving towards electric, but there are challenges with public charging infrastructure. Fleet operators are being advised to focus on electrifying the shortest and most predictable routes first, and in the case of vans, considering whether employees are able to charge at home. This being the case, how far are we from charging infrastructure that works for HIABs and truck-mounted cranes, which not only need to travel to multiple sites, but carry out work once they get there?
For most types of equipment the only option is to bring the power to the machine. You can’t track a 100-tonne electric crawler crane down the road to the nearest charge point. Plant-hirers rarely have any control over the grid capacity on site, and sites often express frustrations in getting a connection. Even if you can get a sufficient grid connection, how green is the tariff?
Plant-hirers cannot always afford to invest in the latest kit, especially in cases where they do not qualify for full expensing. Residual value is another crucial consideration. How much a machine can be sold for determines how much money it needs to bring in before then to be profitable.
In a battery-electric machine, the battery is usually the most expensive component, but also the quickest to depreciate in value. Customers are equally mindful of price, and although there are fuel savings to be had with new state-ofthe-art equipment, this does not always cancel out the difference in weekly hire cost.
Electrification of smaller machines, hand-held items and equipment suitable for tethering (concrete pumps for example) shows promise, along with hydrogen combustion engines for the larger and mobile kit. However, the infrastructure will take time and government support to evolve, as will tackling the higher investment cost.
Drop in alternative fuels are commercially available and can reduce greenhouse gas (GHG) emissions by as much as 90%, as long as they are sufficiently high blend and sustainably sourced. This can be verified through the use of certified suppliers under the Renewable Fuels Assurance Scheme (RFAS).
HVO is the most well-known, though not yet manufactured in the UK. High blend biofuels are another option, but
“Reductions in carbon emissions should not be vilified simply because they contain a degree of fossil fuel use”
these may require modifications to the engine and/or fuel storage. Fuel additives that improve fuel efficiency are also commercially available.
Diesel-electric hybrid offers significant benefits through improved fuel efficiency, utilising battery power during periods of low demand. Being much less dependent on infrastructure, it is a more flexible, scalable and incremental solution.
Battery storage units are also widely available to hybridise diesel power generation on site, or enhance existing grid supplies to avoid diesel power generation entirely, acting as a buffer between the site and the grid to cover peak demand without the need for expensive infrastructure upgrades. There are also smaller transportable options designed to replace the traditional trolley generator.
General efficiencies like anti-idling practices, eco-operator modes and power management (including renewable energy generation on site) can also reduce carbon emissions significantly.
Climate targets must recognise sector-specific challenges and allow scope for these approaches while the goldstandard technology gains momentum. Reductions in carbon emissions should not be vilified simply because they contain a degree of fossil fuel use. Less carbon tackled today, is more carbon to tackle tomorrow and less time to do it in.
The plant-hire sector has proven time and time again that it will do what it can, when it can, but it cannot do it alone. Substantial visible progress in infrastructure and financial incentives like fuel rebates and full expense allowance will be required. These necessaries do however carry a hefty price tag, and what remains to be seen is how far the UK taxpayer can afford to run in this race to Net Zero. www.cpa.uk.net
The UK’s hydrogen industry has been given a transformative boost following the unveiling of HYKIT, a joint venture between investment company HYCAP, green pioneer HydraB Group and JCB, which will manufacture key products for the clean economy.
Starting in 2025 from a state-ofthe-art unit in Oxfordshire, HYKIT will build a suite of products to assist hydrogen distribution, including mobile compressors, storage solutions and refuelling systems.
Developed in tandem with JCB’s hydrogen engineering division, the products will provide vital infrastructure for operators of hydrogen machinery and vehicles in the construction and transportation sectors.
Jo Bamford, Executive Chairman of the HydraB group, which owns a suite of companies in the net zero space, including zero-emission bus manufacturer Wrightbus, hydrogen distributor Ryze Power and H2 producer Hygen Energy, said the new company was a vital stepping stone to further hydrogen adoption.
“I first started talking about hydrogen in 2019 and ever since then we’ve been steadily building a network of companies who can get this industry on its feet,” Jo Bamford explained.
“Between us we’ve delivered hydrogen buses and hydrogen diggers; now we are focusing on the infrastructure to bring it all together.
“Our commitment to the industry is clear – we are putting the ecosystem
in place to help businesses realise that hydrogen is a vital part of the UK’s energy mix.”
Neil Tierney, previously of NanoSun, will serve as CEO of HYKIT, leading the initiative to ensure the successful development of these crucial hydrogen solutions.
JCB Chairman Lord Bamford said: “JCB has proven that hydrogen can be a fuel of the future for construction and agricultural machinery, without any of the carbon emissions associated with fossil fuels.
“Machines powered by JCB’s pioneering hydrogen combustion engines are set to revolutionise how building sites and farms of the future operate. A key ingredient in this hydrogen revolution is getting the right infrastructure in place to support the deployment of this clean fuel.
“HYKIT’s launch shows that we are serious about the hydrogen economy and serious about getting UK-engineered equipment to get this industry moving.”
James Munce, CEO of HYCAP, an investment fund dedicated to energy transition investments added: “Our view is that the integration of JCB’s industrial expertise into HYKIT will lead to new standards of reliability and affordability in equipment to distribute and dispense hydrogen.”
“Between us we’ve delivered hydrogen buses and hydrogen diggers; now we are focusing on the infrastructure to bring it all together”
As a global leader in construction engineering, SANY is dedicated to delivering high-quality, sustainable and emission reduction initiatives, introducing more than 40 new electric products globally in 2023 and remaining committed to supporting the energy transition in Europe.
The UK product range includes two fully electric excavators, the smaller 2-tonne SY19E launched in 2023 and the 23-tonne SY215E, which launched earlier this year.
With its electric machines, SANY sees the advantages that high voltage can give in terms of efficiency and performance and has designed technology that offers industry changing benefits and a number of environmental benefits too.
Automotive standard components meet the highest safety requirements and regulations, the performance is much greater than comparable industrial components and they are more readily available to purchase which effects the total cost of ownership for plant hirers. The CCS2 charging socket of the SY19E and SY215E is also automotive standard, therefore these electric excavators can be charged at any public charging station, including fast chargers, which helps to support the charging infrastructure being developed by the government and companies within the UK.
The fully electric SY19E and SY215E are both powered by a state-of-theart lithium iron phosphate battery, providing the best solution to both customer and operator alike. Lithium iron phosphate batteries not only have superior operating characteristics compared to lead-acid batteries, they’re also far less toxic to produce and recycle. They do not contain any toxic/hazardous chemicals or rare metals like cobalt, nickel or lead and are made of more common elements like graphite, iron and copper instead, eliminating the biggest environmental impact factor in standard lithium-ion batteries and improving recyclability.
The lithium iron phosphate battery offers the customer different methods to recharge the machine including a fast charge of 1.5 hours. Unlike other batteries, the depth of discharge behaviours will not affect the overall life of the battery. This allows the customer to tailor the charging needs to each day and different site/ job being undertaken, minimising logistics and maximising business efficiency.
Lithium iron phosphate batteries also offer lifetime periods for instance up to 3,500 full charge cycles for the SY19E which will cover the machine for more than the standard lifetime, this reduces environmental impact compared to other batteries which will need to be changed throughout the machine life.
The SY19E and SY215E excavators are produced within a light house factory company (as recognised by the World Economic Forum) so material waste, energy and greenhouse-gas emissions are hugely reduced throughout the production and manufacturing process, minimising the environmental impact compared to standard manufacturing processes.
The SANY SY215E has also been tailored specifically for the European market, featuring the latest generation cab including a large 10˝ HD touchscreen, LED lighting, improved air suspension seat, enhanced air ventilation, intelligent fault self-diagnosis and a low noise working environment, all designed specifically with the operator in mind.
SANY’s electric machines offer state of the art design, coupled with a high voltage system and automotive standard components that ultimately offers the best environmental benefit, performance and economy in the market.
www.sanyuk.com
+44 (0) 330 2021 318
Battery:
Rated Voltage: 268.8 V
Operating weight: 1,965 kg
Max. power: 15 kW / 2,000 RPM
Max. bucket capacity: 0.04 m3
Max. digging depth: 2,360 mm
Max. travel speed: 3.6 km/h
Battery:
Rated Voltage: 618 V
Operating weight: 23,200 kg
Max. power: 150 kW / 1,800 RPM
Max. bucket capacity: 1.1 m3
Max. digging depth: 6,255 mm
Max. travel speed: 5.4 km/h
by Greg Harris, Chief Commercial Officer of
In the search for alternative, emissionfree power sources for plant machinery, hydrogen fuel cells might seem an exotic option, but the technology is proven, practical, and already in use throughout the construction industry.
Hydrogen fuel cells might not be the first things that come to mind when discussing alternative fuels for the construction industry, but the race to net zero is on and in light of the need to reduce greenhouse gas emissions, many industries are looking to alternative fuels to power their operations.
Hydrogen fuel cell systems have emerged as a greener and impressively viable alternative to fossil fuels, particularly within the construction industry, which occupies the unenviable position of being a major polluter.
Hydrogen fuel cells are an emissionfree technology. They generate electricity through an electrochemical reaction, producing only water and heat as byproducts. Compared to diesel generators, which emit particulates, nitrogen oxides and carbon monoxide, fuel cells are totally clean when using green hydrogen.
They also have a significant edge over battery-electric power systems due to their rapid refuelling capabilities. Systems can be refuelled in a matter of minutes, much like refilling a diesel tank, eliminating the lengthy, and productivity-sapping,
recharging cycles battery-powered machines require.
The number of fuel cell variants available makes them suitable for a range of construction-related applications including powered access, material handling, welfare cabins, lighting towers and standby power.
For instance, the fuel cell modules within the IE-POWER range are compact and robust, and have the capability to deliver clean, near-silent power from 1 kW to 32 kW.
Migrating to a new source of clean
power can be a daunting step. But fuel cells are already in use within the construction industry, demonstrating that this technology is a viable alternative to traditional power sources.
In 2023, we collaborated with machinery manufacturer Niftylift to develop the world’s first hydrogenpowered Mobile Elevating Work Platform (MEWP) known as the ‘H2E’ (Hydrogen-Electric).
Our IE-POWER 1 fuel cell modules were integrated into the battery-powered vehicle, to enable continuous zeroemission operation even when charging facilities are unavailable. The H2E model can run for up to 4-5 days on a single charge. Niftylift represents a real-world example of how hydrogen can revolutionise powered access equipment while cutting lifetime costs and carbon emissions.
However, the potential of Intelligent Energy’s fuel cell technology goes beyond Niftylift. The same operational principles and benefits can be applied to a wide range of material handling and construction equipment powered by fuel cell technology including forklifts, diggers and cherry pickers.
And the benefits are not all about extended run times. Noise pollution is a significant issue on construction sites when diesel generators and engines are in use. Hydrogen fuel cells operate almost silently, improving on-site safety and comfort.
One of the challenges to widespread hydrogen adoption remains the UK’s
limited refuelling infrastructure. While hydrogen-powered machinery like the Niftylift platform is ready for use today, a more widespread hydrogen supply network is required to unlock its full potential.
Both policy and financial incentives will have a part to play in the adoption of hydrogen, and initiatives like the Government’s Clean Power 2030 Action Plan and support to green hydrogen projects across the county are encouraging signs.
In summary, hydrogen fuel cells are far from a futuristic dream, they are a present-day solution for a greener, more efficient construction industry. For companies looking to reduce emissions, enhance efficiency and future-proof their operations, hydrogen offers a compelling path forward. The shift from diesel to clean energy is not just achievable – it’s already happening.
JCB X-Series excavators are leading the way in lowering fuel consumption. The 145XR now uses up to 10% less fuel than our previous model, the JZ140. We’ve made this possible by reducing the working speed of the engine from 2050rpm to 1700rpm, whilst maintaining performance by optimising the hydraulic system. We’ve also improved slew control and increased bucket tearout by 13% for smoother operating. Start saving today.
* £2000 saving is versus the JZ140 Stage V and is based on an
Wayne Ridings, Managing Director
Well ladies and gents, the festive period is upon us once more and I take this opportunity to wish everyone a prosperous New Year. It has been a hard year for British engineering so let us hope 2025 brings some welcome relief to you all. Here at BMC we have had some exciting news to assist us in becoming a far more comprehensive bespoke supplier in excavator attachments. With the help of some esteemed suppliers from Italy, Lameter and Idrobenne we are now poised to start the New Year with a bang.
While we still construct standard buckets for all machines up to 50 tonnes, we were getting several enquiries for some bigger products so, it made sense to join forces with
two excellent Italian worldwide suppliers. They will enable BMC to assist and quote to anyone requiring attachments above and beyond our usual restrictions, while being able to offer a solution to a client’s predicament in sourcing a suitable product on a one stop-basis.
Covering the heavy end of the market we have Lameter. They have spent 40 years supplying made to measure buckets and attachments to both the mining and quarrying sector throughout the world, producing frontal excavator buckets for machines of 120 to 400 tonnes for example. As you can well imagine, spends on products of this magnitude need to be custom made to suiting their needs such as, brand of GET required, lubrication kits, dust guards, etc. Their mining loading buckets include a range of underground profiles, side dump range and high dump etc. This leaves our bucket supply range limitless, and we look forward to getting involved in any mining or quarry work we can assist with.
BMC has been making mechanical grabs for years and we find ourselves busy with hydraulic thumbs at present, which the US market loves by the way. We have noticed a steady rise in sales recently but again we were restricted to what we could provide to our customers regarding size and type.
With Idrobenne supplying an endless range of grabs for all environments including, railway, forestry, demolition, waste, clamshell and ever-popular selector grabs, it’s provided us with vast choice to pick from and I have no doubt we could provide the right tool for our customers.
www.bmc-buckets.co.uk
sales@bmc-buckets.co.uk
Inspecting and replacing bucket tips regularly is essential to avoid machine damage while maximising output. However, it’s important to match the right tool to both the machine and the work it is doing to optimise performance and machine longevity. Here, Cheryl Griffith, Wear Parts Product Manager at Finning, the world’s largest dealer of CAT equipment, parts and services shares her expert view on selecting the right type of tip and what signs to look for when it comes to replacing them.
Work tools are an important part of any machine. Not only do the tools protect the most expensive machine components, but they also have a direct effect on the productivity, fuel consumption and maintenance costs of your machine. Choosing the right tips at the right time enables operators to achieve the lowest cost per tonne, whilst also safeguarding the engine and powertrain life of your machine.
These tools have a direct effect on the machine’s ability to perform effectively. A worn-out work tool can also increase operator fatigue, for example an increase in cab vibration caused by resistance on the system, means it takes more time to move material, as worn tips lead to less penetration into the pile.
Checking your bucket tips regularly as part of a wider check of all your wear components is essential. The kind of environment the machine is working
in affects the rate of wear. For example, if a machine is operating in a quarry and working with granite, which is an incredibly hard material, the bucket tips will wear at a quicker rate.
Visual checks – what to look for:
• Excessive wear on bucket tips – tips worn through on the bottom or cracked in the pocket area should be replaced,
• Damage to the bucket tip adapters –badly worn bottom straps worn into the bottom cavity should be replaced,
• Damaged or missing retainer pins –tap lightly on each pin and if it moves easily replace the retainer,
• Cracks on the base edges beside adapters and corner welds,
• Cracks on base edges on the top and bottom of the rear weld.
Generally, the tip should look like a triangle shape to the side, but if the tip has a blunt end rather than a sharp end it can really affect the efficiency and impact of
the digging process. This means you get less penetration, less efficiency and it’s not possible to get the full force of the machine into the load to lift the maximum capacity.
Another thing to check is that you can shake the tip as there should be some play in it rather than it being completely rigid. However, if there’s too much play in the tip, this means the adapter is starting to wear and will make the machine less efficient and reduce tip retention.
When a tip is wearing it can also mean the fuel burn will increase because the machine is having to work harder to break up the same material. This leads to wear to the adapter at the back of the tip, which is why not replacing tips regularly can quickly escalate machine costs as these are more expensive to replace.
Which product type and tip type to use is something Finning supports customers with because it has a huge Cat product range to choose from to find the best fleet solution for both Cat and non-Cat machines. Our inspection team can also conduct ground engaging tool inspections, so customers have complete peace of mind that they are getting the best out of their wear parts.
There’s only one place you’ll find the heavy hitters of concrete and masonry this January: Vegas, baby — at World of Concrete 2025, the largest and only annual international event dedicated to your business. Be here to mix with industry giants. Get your hands on the latest technologies revolutionizing safety, performance and speed. And learn what it takes to not only claim a piece of our industry’s massive projected growth but dominate the field. Join the power players of concrete and masonry.
EXHIBITS: JANUARY 21-23, 2025
EDUCATION: JANUARY 20-23
LAS VEGAS CONVENTION CENTER
At Hardlife Group, we have spent more than two decades redefining durability, quality, and affordability in the construction industry. From our humble beginnings to where we stand today, our story is one of innovation, growth, and a commitment to providing excavator attachments that truly go the distance.
Where it all began
Our story started in 2001, when our founder, Frode Iversen, began exporting used excavators from the UK back to his home country of Norway. To date, more than 3,500 machines have been exported to the region. Scandinavia’s rugged terrain and harsh conditions demand equipment that’s up to the challenge. Customers began asking for excavator attachments to match their machines, so Frode worked with a designer to develop the first sketches of what we now know as Hardlife attachments.
Before Bucket Warehouse was even established, we were already introducing Scandinavian design into the UK market. The Scandinavian Tilt Bucket was one of our very first products and remains a key part of our history. Frode developed the design based on Norwegian requirements, ensuring it could tackle the toughest terrain.
By 2012, we had a full range ready and launched into the Norwegian market. After recognising demand in the UK, we established Hardlife UK, focusing on providing “new buckets at second-hand prices.” We quickly gained traction with customers who wanted durability and performance without the premium price tag. In any industry, there are leaders and followers. At Hardlife, we’ve always been proud to lead the way, and the UK market has taken notice. Over the last 15 years, we’ve seen many UK suppliers start copying the very models we pioneered – especially our Scandinavian designs.
The Scandi bucket range
Our Scandinavian roots remain at the core of our attachment designs. Over the years, we’ve developed a versatile and durable range of Scandi buckets tailored for extreme terrains:
• Scandinavian Tilt Buckets –Precision-engineered for tiltrotator use and inspired by Norwegian requirements,
• Cable Buckets – Skinny trenching buckets with elongated flat bases and no teeth, ideal for trench work and utilities,
• Scandi Digging Buckets –Narrower than standard bulking buckets for better penetration, with elongated bases for increased volume,
• HD Scandi Digging Buckets – For eight-tonne+ machines, featuring high-grade steels and additional wear plates,
• Rock Buckets – Built for 20-tonne+ machines, using the highest-grade steels, delta cutting edges for penetration and wear shrouds for
• Grading Buckets – Optimised for tiltrotators, with tapered backs to prevent corners from catching during rotation,
• Rock Riddle Buckets – Scandi Digging Bucket design with horizontal riddle bars for sorting materials,
• Grading Riddle Buckets – A wide-mouth, low-profile bucket with riddle bars, ideal for sorting without teeth,
• Finishing Buckets ‘Renskeskuffer’ –Perfect for cleanup work, with elongated cutting edges for a smooth, tidy finish.
Our Scandi range is built to a higher standard, using HB500 and HB450 abrasion-resistant steels alongside S355 and Q690 structural steels. This combination ensures superior performance, extended durability, and reliability in the most challenging conditions.
In 2014, we moved into our first UK
Buzzard, allowing us to hold stock and operate a workshop. Soon after, we expanded into Bergen, Norway, to better serve our Scandinavian customers.
Our success saw us relocate to a larger facility in Bletchley, Milton Keynes by 2017, where we doubled our capacity within 18 months and launched the Hardlife Utility range of storage tents and container shelters.
To meet demand for the Utility range, we secured an additional 1.5-acre plot for demonstrations and dedicated storage while expanding workshop space to refine and grow our excavator attachment range.
Introducing Scandinavian design to the UK market more than 12 years ago was a milestone for us. We brought with us a commitment to durability, performance and precision engineering – values rooted in Norway’s unforgiving landscapes and challenging work environments.
Whether it’s our Scandi Digging Buckets for ground penetration, Rock Buckets for maximum breakout force,
to deliver unmatched reliability and
excavators to leading the way with innovative attachments and storage solutions has been incredible – but we’re not done yet. As we expand our range and refine our designs, we remain committed
construction, earthmoving,
Hill Engineering celebrated its 30th anniversary in 2024, and while it was the first attachments manufacturer to create the double-locking hydraulic Tefra coupler, its range of buckets is equally impressive.
The aptly-named Titan range of buckets is used across a diverse range of industries, including construction, demolition and materials handling, ground care and landscaping, civils and utilities, and quarrying and aggregates.
The preferred supplier to OEMs such as Hitachi, JCB, Komatsu, Volvo and Caterpillar also works closely with hire companies and end users to continually develop and improve its products to work smarter and safer, focusing on quality, innovation and reliability.
The Titan bucket range features two options – the HD and HDX style – with the further option of fixed pin or bossed attachment points.
The HD range is available in widths between 450 mm and 3,000 mm. While it is Hill’s standard duty bucket, it is built to a higher specification than normal standard buckets, enabling the user to
enjoy a longer bucket lifespan. These HD buckets can be ordered with teeth, blade or BORCE.
The HDX models, which are available between 450 mm and 2,000 mm, exploit the superb qualities of high tensile, wearresistant steels such as Hardox, Weldox and Hi-Tuf. These buckets have a minimum 35% high strength steel content and can be designed to suit specific applications.
A unique feature of the HDX is the full-width internal secondary beam, located inside the box beam head section, for extra strength and improved torsional rigidity.
The HDX buckets sport a greater use of wear bars and drop forged wear plates to create added strength and durability depending on the terrain and environment the excavator needs to work in.
Titan buckets can be ordered with heel shrouds, lip shrouds and side cutters.
Hill Engineering produced one of its biggest bespoke buckets – a 4.9-tonner strengthened with 20, 30, 40 and 50 mm Hardox – for Irish neighbours Loughran Rock Industries in 2021 and it’s still going strong.
The design and build by Hill Engineering took a month and the bucket has now been in operation, digging greywacke for PSV chips, tar and concrete, 10 hours a day and six days a week for three years.
The bucket is a 2,250 mm-wide monster (narrowing to 1,769 mm at the back), which features six FC600 teeth, six F40 heel shrouds and six side cutters.
Weighing in at 4,882 kg itself, it has a cutting edge of 70 mm and capacity of 4.9 m 3 – slightly larger than the 4.6 m 3 bucket that would normally be supplied by OEM Doosan.
You wanted a versatile electric jobsite solution to dig, load and carry, inside or outside. We’ve delivered a super quiet, zero emissions, no heat, plug and play solution allowing you to work in even the most restricted environments with ease.
Build your cleaner and greener business with us.
In this era of fast-moving technology and ever-changing construction sites, the humble bucket is something contractors may take for granted. But, like all attachments, buckets have changed dramatically over the last two decades. Driven by the demand for increased safety and efficiency, buckets have evolved to give users more options and selecting the right bucket for the task is vital, as Barry Robison, Group Sales and Commercial Director at leading earthmoving attachments manufacturer Miller UK, explains
Often, users will look at specifying a bucket and think the only consideration is size. However, bucket technology has developed to meet the needs of precise project specifications, driven by the requirements of contractors to carry out work without compromising on safety or economy, so it’s not necessarily a case of bigger being better.
Instead of simply looking at the biggest bucket, matching buckets to the specific requirements of each application and the environment in which it will be used – whether that’s building, earthmoving, mining or quarrying – is essential. The right bucket should complement and
enhance the machine and make each task as smooth and efficient as possible, saving contractors fuel, time and money. Put simply, specifying the wrong bucket will cost more in the long run.
For decades, Miller has been committed to innovation, listening to its customers to design and develop high performance buckets tailored to their needs, whether that’s reacting to new safety legislation or finding ways to improve efficiencies on site. These precision-engineered buckets are a far cry from the first generation of buckets and are designed to cut through the ground with minimal resistance and drag to release the full potential in terms of digging power and bucket capacity.
When a bucket is more than just a commodity
There is a danger that contractors may consider a bucket as a simple commodity to be replaced when it’s worn out, with little impact on the overall project. But buckets have evolved hugely and high-end designs are proven to have a significant impact on the speed a project can be completed.
Buckets can be manufactured to meet specific performance design objectives. For example, where there are reduced power requirements but contractors are under pressure to make fuel savings, buckets can be designed to ensure the maximum digging force is employed with the minimal pressure. By creating a compact
bucket design with a shorter pin-to-point diameter, it allows operators to break the ground with more force – without adversely affecting the fill capacity of the bucket.
It’s not just the capacity of the bucket that can be altered to create a more efficient process. Buckets designed to mirror the natural geometry of the excavator and shaped to match the natural arc of the digger arm will reduce strain on the excavator itself, maximising digging force, reducing power requirements and fuel usage.
With greater variety in standard bucket design than ever before, specialised buckets can be relied on for all manner of tasks, from channel clearing and grading to house building and quarrying. Where space is restricted, for example, a tilt bucket provides greater versatility and is ideal for side-angled trenches or landscaping works. With rock buckets for face or bank loading in mining or quarry applications, ripper buckets for heavy-duty excavation applications and riddle buckets for sorting applications, there is a bucket for every application – without the need to opt for a completely bespoke projectspecific design.
With over 45 years’ experience in bucket build and design, Miller is recognised as the UK’s largest bucket manufacturer, offering a vast portfolio from mini, heavy duty, rock and extreme rock through to tilt, hi-tip and wheel-loader buckets.
At Miller’s headquarters in the north-east of England, the company has recently invested in a state-of-the-art robot production line – capable of welding attachments for machines over 100 tonnes – to cater for its increasing demand for its buckets delivered across the globe. With stock widely available, Miller’s buckets are known for their high quality and safety and are trusted by leading earthmoving manufacturers worldwide including SANY, LiuGong, Volvo, Hitachi, JCB and CASE.
Ulrich Attachments can count clients as demanding as the waste industry among its customer base of a wide range of end users who nevertheless have a common purpose – to seek a specialised solution for their handling needs.
Following its 1998 management buy-out from Boughton’s, the premium producer of buckets and winches, Ulrich has become one of UK leading manufacturers of mobile plant equipment and thanks to sole production in the UK, offers possibly the highest quality bespoke products in the industry. Its product portfolio now encompasses
a wide range of standard and bespoke attachments, including forks, couplers, winches and other specialist handling equipment that increases the versatility of mobile plant machinery for OEMs such as Volvo, Hitachi, JCB, DEVELON, Liebherr and CASE Construction.
The company’s buckets portfolio is particularly standout with products to suit every model and make of machine in a wide range of applications. This includes general purpose and rehandling buckets which can be manufactured to a specification recommended by Ulrich’s sales specialist to suit each application. Multiple bespoke options include steel specification to specific rollback and dump
solutions, even down to how narrow or wide the bucket is required to suit each working condition.
Heavy duty also features on Ulrich’s refuse clamp buckets which feature a clamp assembly designed to withstand the rigours of waste transfer duties. Multiple styles of clamp are available dependent on the type of waste or material in the application. Ulrich’s traditional solution is its ¾-width single clamp, which is suitable for most waste applications, but the company also offers bespoke solutions including full-length, twin clamps and integrated heavy-duty clamps.
Ulrich rock buckets are designed for the very toughest of jobs, with heavy duty
construction and Hardox reinforcements designed for handling hard compacted material and blasted rock in mining or quarrying applications as well as foundries and fabrications. They offer superb breakout capability and are designed to work with all brands of wheeled loaders in arduous applications, with wear-resistant teeth and segments fitted as standard.
Ulrich also manufactures high-capacity bulk handling buckets, including High Tip variations designed specifically to maximise capacity and productivity for each job. The High Tip bulk handling buckets provide extra reach and dump heights for loading high-sided bulk trailers.
At the other end of the scale, Ulrich manufactures bespoke buckets for grain handling. These are light in weight but large in capacity.
For additional versatility, the Ulrich Simplex bucket range is designed to undertake a range of front-end loader tasks and is available for all major loading shovel brands from 0.6m³ to 6.5m.
Designed for general earthmoving duties in restricted conditions, the
Ulrich side dump bucket gives additional discharge height over a conventionally mounted bucket on a carrying cradle, with the side dump action activated by a single hydraulic cylinder.
But it is at the forefront of the design and manufacture of High Tip buckets that Ulrich really shines.
During 2024, the UK’s largest privately-owned landfill operators, Valencia, purchased five High Tip buckets from Ulrich ranging from 10 m 3 to Ulrich’s largest-ever High Tip highdischarge bucket – a 14 m 3 capacity bucket. This was required to complement the larger dumper trucks the operators had been acquiring due to an expansion in their recycling facilities.
Designed for light material rehandling into high sided trucks and hoppers, capacities for Ulrich’s High Tips start at 0.7 m³ and give an additional discharge height of up to 1.7 m above that obtained with a conventionallymounted standard bucket.
The bucket is mounted on a carrying cradle with a pivot located
behind the cutting edge which enables high discharge, while the dump action is achieved by two hydraulic cylinders mounted in the bucket sides which allow forward dumping of the load while the cradle and loader linkage remain in the high-carry position.
Ruggedly, yet simply constructed, the High Tip is manufactured from high-quality materials for long life, with the option of Hardox for more aggressive applications. The buckets can be direct pin-mounted to the loader arms or via a quick coupler bracket on the loader.
Caterpillar has launched its third Global Operator Challenge, inviting thousands of machine operators worldwide to put their agility, resilience and versatility to the test on a wide range of construction equipment and technology.
“For nearly 100 years, our customers have been pushing the limits with our machines,” said Caterpillar Construction Industries Group President Tony Fassino. “This challenge helps showcase and celebrate the exceptional skills of the expert men and women in this important profession as they forge their legacies of being the best operators in the world.”
More than 140 Cat® dealer competitions were held during the 20222023 challenge, which attracted more than 10,000 operators from 32 countries. The 2025-2026 challenge aims to include more events, countries and operators than previous programmes.
Invitation for operators
Operators are invited to compete in local challenges facilitated by Cat dealers around the globe during the first round, being held from January to September 2025. The competitions will feature at least three different challenges on at least three separate pieces of equipment. Scoring is based on the operator’s skills, safety, efficiency and competence in using integrated technology such as payload, grade control and operator ease-ofuse features to enhance the machine’s performance.
Winners from local dealer events will advance to regional semi-final competitions during the autumn of 2025. Nine finalists will emerge from the regional semi-finals and participate in the final competition in March 2026 at Caterpillar’s outdoor Festival Grounds exhibit during CONEXPO-CON/AGG in Las Vegas. The winner receives either a $10,000 cash prize or an equal value trip for two where Caterpillar has a location worldwide.
For more information and official rules about the Global Operator Challenge, including how to participate, visit www.cat.com/operatorchallenge
Specsavers has launched its newly enhanced safety eyewear range, co-created with Stryder Eyewear. This collaboration combines decades of expertise with innovation to deliver a collection designed to meet the diverse needs of industries and PPE requirements.
With more than 50 years of experience and over 100 patents, Stryder Eyewear has worked closely with Specsavers to ensure the range adheres to rigorous production standards, offering exceptional durability while meeting all necessary safety regulations.
The new safety eyewear collection is available in three tiers – classic, specialist, and premium – priced at £90, £100 and
£130 respectively. Each tier has been carefully designed to cater to varying workplace needs, blending robust safety features with contemporary, stylish designs.
Safety frames will also now be included in our 2-for-1 offer for most customers nationwide in stores, allowing everyone to make the most of these style options, or to have different frames for different jobs.
The range is made using materials and processes that offer customers more sustainable choices says Dona McLafferty, Corporate Account Manager for safety eyewear at Specsavers: “The new range combines materials and
“Carefully designed to cater to varying workplace needs, blending robust safety features with contemporary, stylish designs”
processes that offer customers more sustainable choices, plus comfort and style.
The range includes some frames which are made using high-performance raw materials. These raw materials, traditionally sourced from fossil fuels, have a proportion of their content replaced with materials from plant-based sources. This allows customers to reduce their consumption of non-renewable materials without compromising on performance. We’re also excited to introduce new features, including titanium frames and coloured styles, to meet the preferences of a wider audience.”
Designed with both comfort and
functionality in mind, the eyewear range uses state-of-the-art injection moulding methods, enabling features such as adjustable temple tips with overmoulded soft parts for enhanced comfort. Various frames also include an indirect venting system and seamless side shield integration, improving visibility and significantly reducing lens fogging.
Each frame is engineered to deliver optimal safety and style and is suitable for a broader range of prescriptions. They include adjustable metal-free nose pads for unparalleled grip and over-moulded wire-core temples designed to fit any head size. Customers can choose from an array of colours, including black, grey, crystal,
burgundy, green, and silver.
Specsavers’ latest safety eyewear range represents a significant step forward in workplace protection, combining industry-leading safety standards with user-focused design.
The classic range is now available to corporate customers with a safety eyewear voucher, included in the Specsavers Corporate Safety Eyewear scheme. This allows employees to select and try frames with personalised service, ensuring a seamless experience and consistent quality. By providing employees with Specsavers Safety Prescription Glasses, businesses are choosing tailored, safe and durable eye protection.
With 120 years of undercarriage experience, Caterpillar continues to innovate, so customers get the most from their investment. Exclusive to Cat machines and undercarriages, the proprietary Cat Track Wear Sensor (CTWS) remotely monitors undercarriage wear to better predict wear out, plan maintenance and increase machine uptime.
Monitored within the Cat Wear Management System, the new CTWS wirelessly communicates critical track link wear information from the machine to the dealer for monitoring. Timed alert intervals – a 40% wear alert for possible bushing turns, 70% to signal for measuring and replacement part ordering, and 100% for required replacement – improve inspection scheduling and streamline ordering of
replacement parts. The real-time track wear status enables no-touch track link measurements, increases fleet coverage by automating inspections, provides visibility to track wear when operating in remote locations and allows for prioritised timing of service visits by helping optimise manual inspections.
Field tested for proven reliability throughout the expected track life, more than 2,000 Cat machines have been shipped with the innovative sensor technology. The small electronic sensor installs in a
customised pocket in the track link for protection. Each link assembly includes a smart link, resulting in two sensors on a machine, one on each side. The CTWS survives high frequency shock loads and meets sensor functional and environmental tests. Subject to operating conditions, sensor battery life has been shown to last up to seven years.
The wear sensor is standard on new Cat D5, D6 and D8 dozers, and 953 and 963 track loader models in select regions with planned expansion to models in the dozer line in the future. It can be retrofitted on eligible dozer undercarriages.
www.cat.com
THE DEMOLITION, ASBESTOS,
FOOTBALL, BOXING, TRAVEL, GENERAL KNOWLEDGE, SCIENCE, WRESTLING,
CONSPIRACY THEORIES, LITERATURE,
#01 Get Involved... The PowerPlant Podcast
Managing machine hours, tracking fuel usage and monitoring load capacities no longer rely on manual processes or on-site checks. PVS Data (Plant and Vehicle Services Ltd) has transformed fleet management for plant and construction companies worldwide, encompassing brands from all OEMs. With the installation of the new D2 unit, businesses can access over 300 real-time data parameters, including live engine reports, precise machine locations through the w3w (What 3 Words) app integration, and safety metrics, including height, slew, and RCI (Rated Capacity Indicator) data from Xwatch Safety Solutions.
Xwatch Safety Solutions, part of the Hexagon Group, is redefining on-site and in-cab safety standards. Operators can now set precise height, slew, and RCI limitations directly from their excavator’s cab, providing a new level of control and assurance. Safety has always been a cornerstone of the construction industry and Xwatch builds on this legacy with advanced in-app telematics across its product range. This innovation enables live, global visibility of key safety data, ensuring the highest levels of protection for operators, machines and ground personnel.
Dan Leaney, Xwatch Safety Solutions, Sales Director, commented on the new technology, saying “The telematics system for the D2 units from PVS, branded as XW-Insite by Xwatch, represents our most advanced safety and telematics solution to date. Currently being trialled with a leading plant hire firm, a tier-one contractor, and through PVS’s own trials, this system integrates Xwatch’s precise height, slew, and RCI data with PVS Data’s cloud-based platform. It delivers seamless telematics access across fleets,
covering all major equipment brands.
“Operators can configure and monitor critical safety parameters directly from the cab, while managers gain real-time visibility into machine performance and safety metrics, whether on-site or working remotely. This innovation is designed to prevent accidents, reduce downtime, and enable smarter, data-driven decisions.
“At Xwatch, we are proud to collaborate with PVS to lead the industry in making construction sites safer and more efficient, and we look forward to seeing comparable data emerge from these
trials in the coming months.”
This collaboration between PVS Data and Xwatch Safety Solutions brings powerful functionality to fleet management. PVS Data’s cloud-based computing and live reporting provide seamless access to telematics across an entire fleet, covering all major brands, including JCB, SANY, Hitachi and Takeuchi to name a few. Site managers gain a clear visual overview of their machinery equipped with Xwatch Safety Solutions. They can monitor height and slew settings, view the exact weight on the hook, confirm whether stop and creep controls are active, and analyse overall capacity utilisation – all in real time.
Combine this safety information with real-time data such as fuel usage, engine performance, fault reporting, idle and productive hours and carbon dioxide emissions. The result is a construction site that operates more efficiently, ensures greater safety for ground personnel, meets zero-emissions goals, reduces costs and downtime, extends machinery life and encourages smarter machine operation.
Scott McCabe, Owner and Director of PVS Data, commented on the
partnership: “Heightened safety on site has been at the heart of the industry for decades. Our partnerships with innovators like Xwatch make the platform the logical all-in-one solution for fleet health and safety. We’re excited to see where our current trials take us, advancing the platform to show a greater number of meaningful data parameters, and growing our partnership with the Xwatch team.”
Hitachi Construction Machinery UK has been at the forefront of this partnership by delivering connected technology to its customers when purchasing new machines. Its custombranded platform, created by PVS Data, is CTFleet Link® and it has changed the way its customers all over the country see their fleets of mixed-brand machinery.
Stephen Creaser, Director of Product Support for HCMUK, shared his thoughts on the intuitive platform and its capabilities: “At Hitachi UK, we’ve always been proud to take the first step to a more connected industry, a safer industry
for operators and ground personnel and a wider network of opportunities by innovative organisations.
“PVS, the D2 units and their platform showcasing Xwatch’s safety solutions are the logical solution for fleets worldwide, connecting OEMs in a single sign-on solution. Giving users on and off-site the ability to check on machine status and driver controls for designated safety equipment is logical and works. We’ve seen no end of evidence that the more eyes on what’s going on in the operator’s cab, the safer the construction site becomes.”
A safer site has more eyes on the machines and the controls their operators are using. A more efficient site is wellconnected, with pools of analysed data readily available to support decisions about an organisation’s economic growth and future investments. Construction sites can unlock significant potential by embracing the expertise, knowledge and safety improvements offered by Xwatch Safety Solutions and PVS Data.
DEVELON and Leica Geosystems, part of Hexagon, have announced a new aftermarket 3D machine control solution tailored for the DEVELON DD130-7 dozer.
The DEVELON DD130-7 dozer is designed to excel in earthmoving tasks, providing superior power and efficiency. Now, with the addition of the Leica MC1 3D machine control system, this dozer will further enhance operator accuracy and overall project productivity.
The Leica iCON iGD3 3D machine control solution integrates seamlessly with DEVELON’s advanced hydraulic controls, allowing operators to execute precise grading and earthmoving tasks with minimal rework.
“We are thrilled to collaborate with Leica Geosystems to bring the latest 3D
machine control technology to our dozer lineup,” said Stephane Dieu, Product Manager for DEVELON in Europe. “This innovative solution boosts efficiency and operational excellence for our customers, enabling them to tackle more complex projects with confidence.”
The Leica MC1 3D machine control system simplifies grading by providing real-time data and feedback. The system is displayed on the robust Leica MCP80 control panel, offering user-friendly navigation that allows operators to visualise the design and reference models directly from the cab. With the dual GNSS configuration, the DD130-7 dozer benefits from precise blade control and automatic adjustments for optimal cut/fill
“We are thrilled to collaborate with Leica Geosystems to bring the latest 3D machine control technology to our dozer lineup”
operations. This reduces operator fatigue and improves site productivity.
“We are excited to introduce the Leica MC1 3D solution for the DD1307 dozer. This collaboration offers unparalleled precision and sustainability for construction professionals,” said Neil Williams, President of the Machine Control division at Leica Geosystems.
“Our shared vision of innovation and efficiency in earthmoving is transforming job sites into more productive, safe and sustainable environments.”
To mark the occasion the Fairfax Plant Hire team and BTE Plant Sales were invited to Thwaites to tour the factory and meet the team. A special 750th dumper decal was commissioned, this anniversary edition celebrates the relationship of Fairfax Plant Hire and Thwaites distributor BTE Plant Sales with whom the dumper deals, over the decades, have been done.
Mark Love, Fairfax Plant Hire Director said “Thwaites manufactures the best dumper on the market, their brand values of safety and quality both aligned with our own. Our customers ask for Thwaites machines by name, knowing they will be getting a quality machine that will not let them down and get the job done.”
Accompanying Mark was BTE Plant Sales Managing Director Rebecca Bryson, Fairfax Service Manager Martin Hazelwood, Social Media Creator Michaela Love and Service Engineer Adam Taylor.
Hosting the party was General Sales Manager Andy Sabin and Distributor Manager Will Redman.
Rebecca Bryson said: “This really is
a special occasion as we mark the sale of the 750th Thwaites dumper to Fairfax Plant Hire. It remains my, and my team’s pleasure to have developed over the past few decades a relationship that is built on trust, understanding and communication. I would like to thank Mark and the Fairfax team for their continued loyalty and support.”
Fairfax Plant Hire took delivery of its first Thwaites dumper back in 1990 and since then the company has grown rapidly to cover as it does today the north of England, East Midlands and Warwickshire.
Concluding, Thwaites Distributor Manager Will Redman said: “We were so grateful that the Fairfax team and Rebecca were able to accept our invite to the Thwaites factory. While I have not been involved in all the machines sold, I am proud to have been involved in the 750th, I look forward to seeing the special edition on site.
By way of perspective, if you were to place each of the 750 dumpers ‘skip to skip’ you would have to walk the length of twenty-eight football pitches to get from the first to the 750th.
“Thwaites manufactures the best dumper on the market, their brand values of safety and quality both aligned with our own”
We have the largest central stockholding in the UK, which is supported by a finely tuned stock control program, a highly organised warehousing system and carefully selected logistics partners. This allows Astrak to have the undercarriage parts that you need available when you need them, minimising machine downtime.
Once it’s on the machine, our extended warranty is the most comprehensive in the market place. Each of our rubber tracks come with an extended 24 month warranty as standard.
All of our undercarriage and wear parts are manufactured in IS0 9001 and OEM approved production facilities with rigorous quality control procedures.
Place your order prior to 4.30pm and it will be despatched for delivery on the next working day.
Our wide range of heavy-duty components will keep your excavators, dozers and tracked machinery working harder, for longer. Every hour of machine downtime incurs avoidable costs! This is why you need a reliable partner you can rely on. Stocking the widest range from bucket teeth, cutting edges and OEM quality undercarriage components through to custom made wear parts. Astrak providing you complete undercarriage and wear part solutions. The right part, to the right place, at the right time!
Bobcat will be presenting the company’s expanded range of products for the rental industry at the sold out Executive Hire Show 2025 (EHS) at the Coventry Building Society Arena in Coventry from 12-13 February.
As can be seen on the company’s stand, number A72, Bobcat offers one of the widest ranges of products on the market for the rental industry. The Bobcat product portfolio has grown significantly over the past five years, launching more machines during this period than previously in its entire history.
For the rental industry, Bobcat offers extensive lineups of compact machinery (including loaders, excavators, telehandlers, compact tractors and mowers) and material handling equipment (including forklifts and warehouse solutions), plus a broad range of attachments, parts and services. All Bobcat products are backed by a worldwide network of independent dealers and distributors.
Among the latest additions to the Bobcat range are a complete line of generators, portable compressors and light towers, building on decades of success and experience in the portable power market.
The very latest portable power products are the new PG40 and PG50 models (pictured), providing a leap forward in portable generator design.
Powered by Stage V D24 engines and Stamford alternators, the new PG40 and PG50 ecoconscious models replace the previous generation Stage IIIA G40 and G60 units, delivering a combination of increased power output and lower
fuel consumption compared to their predecessors.
The D24 engine in the new generators is a very impressive unit – more powerful than those in other machines of this size on the market and with a higher capacity. This has allowed Bobcat to offer a true 50 kVA prime unit on the market in the new PG50 model and still be below the Diesel Exhaust Fluid system requirement. Alongside the PG50, the PG40 delivers a prime power output of 40 kVA.
In addition, both generators have a new sleek, compact design, with a selection of novel features including optional factory-mounted running gear, with either fixed or variable height, for easy transportation such as towing behind a car. This upgrade provides unmatched convenience, ensuring mobility on and off the job site.
The new generators also have ‘Liquid Heat’, a low-load management system designed to reduce downtime and deliver peace of mind. Their versatile capabilities allow the new generators to manage lighter loads while preserving engine life, making them the perfect investment for the rental industry.
The EHS is firmly established as the only annual national event in the UK aimed at tool, equipment and plant hirers and the suppliers serving this dynamic industry. The EHS enables hire professionals to not only see key suppliers they already do business with, in one place, but also to get in front of new companies from around the world who are looking to serve this important market.
A nationwide search is on for the most promising apprentices and trainees in the construction plant industry who, in the eyes of their employers, are likely to become tomorrow’s leaders of the sector.
The Construction Plant-hire Association (CPA) – the largest trade association for the plant-hire sector in the UK – has opened entries for the CPA Stars of the Future Awards 2025.
The awards are free to enter and are open to both CPA members and non CPA members. Nominations are welcome from all employers including plant-hire companies, manufacturers, contractors, suppliers and others operating in the construction plant sector with apprentices and trainees in their workforce. Nominees need to be on an approved apprenticeship scheme or an employer in-house learning programme.
To make a nomination, employers can download a nomination form from the CPA website at www.cpa.uk.net/ skills-training/stars-of-the-future and complete and return it to the CPA by the nomination deadline of 21 March 2025.
The winners will be announced at a prestigious awards ceremony at the Heart of England Conference and Events Centre in Fillongley, near Coventry, on Thursday 10 July 2025. The event will be hosted by construction industry journalist and vlogger Peter Haddock.
Awards will be made for the well-
established categories of Plant Mechanic of the Year (Level 2), Plant Technician of the Year (Level 3), Young Plant Operative of the Year, Plant Operative of the Year, Plant Installer of the Year, Lifting Technician of the Year, Hire Controller of the Year, Apprentice Mentor of the Year and College of the Year. All nominees are also eligible for special awards including the Judges’ Special Award and the Best Personal Statement Award.
In recognition of the growth of the awards over the last 12 years, a new awards category has been added for 2025 for Technical Support Person of the Year. This award is for apprentices or trainees who are in a role that has a plant technical focus and who are supporting other plant-focused operations of their business such as data handling and supply, hiring activities, sales and marketing activities, parts and/or resources/ equipment supply, machine/equipment systems programming/maintenance, site operational planning, supporting external customers, etc.
Steve Mulholland, CPA Chief Executive Officer said: “We urge employees – both small and large – to nominate apprentices and trainees who they see as being the industry’s future leaders, as it means the world to them to be nominated for an award. The awards are open to all employers across the industry, so nominating organisations needn’t be a CPA member to put someone forward.
“Stars of the Future is becoming more high profile every single year and last year’s winners received national recognition and won some fabulous prizes, including tool kits, machine training courses, iPads, an overseas trip to visit a Liebherr crane manufacturing plant in Germany, another overseas trip to one of Wolffkran’s manufacturing facilities in Luckau, Germany and a VIP day courtesy of JCB. We know that many previous Stars of the Future winners have been fasttracked to supervisory and management positions.
“At the CPA, one of our primary objectives is to encourage new blood into the construction plant sector, and Stars of the Future helps us to achieve this. The standard of entries gets higher every year and last year we received 80 nominations from across the industry. We anticipate even more this year,” he added.
Stars of the Future has a two-tier judging process – the CPA selection panel
and a panel of external judges from across the industry who decide the eventual winners of each category.
The national winners for Stars of the Future 2024 were Bethan Whittaker of KJ Services and Bridgend College (National Plant Mechanic of the Year); Morgan Wardle of Banks Plant Solutions and Askham Bryan College (National Plant Technician of the Year); Millie ScottYoung of Sunbelt Rentals (Hire Controller of the Year); Josh Jones of L Lynch Plant Hire & Haulage (Young Plant Operative of the Year); Reece Stray of L Lynch Plant Hire & Haulage (Plant Operative of the Year); Zac Bradshaw of Commhoist (Lifting Technician of the Year), and Hayden Chappell of Southern Hoist Services (Plant Installer of the Year).
Steve Gwynn of Sunbelt Rentals won Individual Apprentice Mentor of the Year, Dave Rogers of L Lynch Plant Hire and Haulage won Group Apprentice Mentor of the Year, Shannon Weiss of Finning UK and Finning Academy won the Best Personal Statement Award and the Judges’ Special Award was awarded to Tom Williams of CBL and Bridgend College.
Sponsorship opportunities are available for Stars of the Future 2025. For further information, please contact Lisa Collins on 07968 840 390 or email lisa@lisacollinscommunications.co.uk.
Scottish articulated dump truck (ADT) manufacturer Rokbak is preparing to kick off another promising year in North America at the 2025 AED Summit, taking place on 15-17 January in Orlando, Florida.
Organised by Associated Equipment Distributors (AED), an international trade association representing companies involved in the distribution, rental and support of equipment across construction, quarrying, mining and other industrial applications, this annual gathering is a cornerstone event for Rokbak in North America.
The manufacturer will use the AED Summit to hold face-to-face meetings with a significant portion of its North American dealers, who are AED members. This will enable Rokbak senior executives, regional sales and service teams and marketing specialists
to connect with dealers directly.
“The AED Summit provides a fantastic opportunity for us to strengthen relationships with our North American dealer network, gather their valuable feedback from the market and collaborate on strategies to achieve our shared goals,” says Robert Franklin, director of sales for the Americas at Rokbak.
new market opportunities
At AED Rokbak won’t only be meeting with existing dealers. The manufacturer will also be looking to connect with potential new partners who share the brand’s commitment to providing reliable equipment and exceptional service.
“Over the last few years, Rokbak has established a solid dealer footprint in states such as Texas, the Carolinas and Florida, where our robust and versatile RA30 and RA40 ADTs are ideally suited to the many housing, infrastructure and
energy projects,” Robert explains. “As we move into 2025, we also see significant opportunities to support the housebuilding and aggregates sectors in the central and north-western regions of the USA and so we’re actively recruiting for new dealers in those areas too.”
In addition to dealer meetings, Rokbak staff will also attend various conference sessions to stay at the forefront of industry developments. This will help ensure Rokbak remains aligned with dealer and customer priorities in North America and is well equipped to overcome emerging challenges.
“We are optimistic about 2025,” Robert concludes. “While we acknowledge there may be challenges ahead, infrastructure investments are expected to continue, inflation is showing signs of slowing down and the overall industry mood is positive.
“From Rokbak’s perspective, we have a strong product lineup, strong dealer partnerships and a shared commitment that positions us to deliver success for even more customers across North America this year.”
Leading Infrastructure services provider, Keltbray Infrastructure Services Limited (“KISL”) has renamed and rebranded to AUREOS.
In August 2024 KISL was acquired by EMK Capital and embarked on a process to rename and rebrand itself, epitomising its role providing infrastructure services in the energy security and decarbonised transport sectors. The process was highly inclusive, involving employee engagement and customer feedback.
The new contemporary name, which broadly translates as ‘a new dawn’, reflects the company’s ambition to deliver
sustainable energy and transport networks carbon future whilst improving societal connectivity.
Darren James, CEO, AUREOS, said: “This is an important time in the evolution of our company. As AUREOS we commit to all our stakeholders to always strive to be their first choice as ‘The leading infrastructure engineering services provider for the energy security and decarbonised transport sectors.’
“I am particularly pleased with the engagement of our extended team in choosing the new company name as we enter the next exciting phase of growth.”
“I am particularly pleased with the engagement of our extended team in choosing the new company name as we enter the next exciting phase of growth”
Over the last 12 months, the European construction industry has undergone many significant changes. Driven by advances in technology, the increasing emphasis on sustainability and evolving safety standards – it has never been more integral for businesses in the sector to adopt new and emerging trends.
With updates to European legislation also coming into play in 2025, including both the EU Data Act and the Corporate Sustainability Reporting Directive, rapid change and adoption of technology has become paramount to the success of construction companies and their projects.
Komastu Smart Construction experts offer insight on the biggest digital and technological changes set for the construction industry this year and how to be ahead of the curve.
In March 2025 the EU Data Act will create access to industry data that businesses can utilise to make informed decisions across research and development to create innovative technology that will grow the construction sector across Europe.
Coupled with existing data acts and funding opportunities, this change will contribute to the establishment of an EU single market for data, making the European construction economy stronger.
The new act will drive innovation in operations, production and supply chain management as it identifies the gaps in the sector. Construction companies must harness the power of this data to unlock new efficiencies, improve project management and enhance decisionmaking processes.
Additionally, the EU sustainability
reporting requirements will push companies to disclose carbon emissions data, encouraging the adoption of environmentally responsible practices and further integrating data-driven solutions, requiring the sector to become a greener industry.
In 2025, artificial intelligence (AI) will be at the forefront of construction innovation. AI is already transforming project management by predicting timelines, identifying risks and recommending real-time adjustments.
As legislation comes into play to make construction a safer sector for all, tools to support actions such as virtual terrain mapping will be integral to practices in 2025. Bart Vingerhoets, Senior Commercial Manager at Komastu
Smart Construction, also expects the adoption of digital tools to increase, particularly through programmes such as the latest Komatsu Smart Construction Edge evolution, which enables users to remove obstacles – such as machinery and buildings – from drone surveys, reducing the requirement for site visits that could potentially be time consuming and hazardous.
Drones and robotics will play a defining role in major construction projects, making surveying faster, safer, and more accurate. Technology such as AI-powered robots, satellites and cameras will monitor job sites remotely, improve safety and streamline quality control. Design automation and resource management solutions will also help cut delays and cost overruns.
Pairing drone technology with
advanced software like Dashboard and Edge boosts decision-making, productivity, and cost efficiency by quickly processing data and providing actionable insights.
Smart Construction’s recent project with HB Golf, a specialist construction company in the Czech Republic, has improved the businesses outputs by delivering key data and information in an easy-to-use format.
Technology Manager at HB Golf, Chris Horn, explains how Smart Construction’s Dashboard has allowed his team to work more efficiently and operate on budget: “Drone technology has prevented costly mistakes and saved time from potential reworks. I previously found that a huge portion of my time was spent on surveying which I can now delegate to site managers. My team uses drone data pulled through to the Dashboard system
to get an accurate overview of the site and all survey data.”
The construction industry faces a significant skills shortage, with an estimated 1.5 million additional workers needed to fill construction jobs in Europe by 2030. Upskilling initiatives in digital project management, robotics operation, and data analysis are essential for businesses to meet the evolving needs of the industry.
As the construction sector continues to adapt to new and emerging trends, the workforce’s skill set will continue to shift into 2025, making it crucial that construction workers are able to effectively understand and use digital tools. The adoption of automation, AI, and digital tools is driving demand for a more techsavvy workforce.
Caterpillar
kicks off next 100 years of innovation and industry leadership: Company celebrates its centennial anniversary with employees, founders and communities
Caterpillar Inc. marked its 100th anniversary with celebrations throughout the US that commemorate a monumental moment in the company’s history. The iconic manufacturing company officially turns 100 on 15 April, marking a century of customer-centric innovation and industry-leading transformation.
The Holt Manufacturing Company and the C.L. Best Tractor Co. merged to form what was then known as the Caterpillar Tractor Co. in 1925. From the company’s first track-type tractor designed to pull combine harvesters in Northern California to autonomous construction and mining equipment and engines that power the world today, Caterpillar products and services have helped its customers complete infrastructure projects that have shaped the modern world.
“Our success over the last 100 years is a testament to the hard work and dedication of our employees, the continued trust of our customers and the support of our dealers and business partners,” said Caterpillar Chairman and CEO Jim Umpleby. “I am proud to lead such a
strong team, and I’m confident Caterpillar will continue to help our customers build a better, more sustainable world over the next 100 years.”
Celebrations took place in Sanford, North Carolina and Peoria, Illinois. At the company’s global headquarters in Irving, Texas, the families of company founders C.L. Best and Benjamin Holt will gather with company leaders and employees to celebrate the first 100 years of innovation as Caterpillar begins its journey into its next century.
The Centennial World Tour has nnow embarked on its journey to visit Caterpillar facilities around the world and provide an interactive and immersive experience for employees and visitors. The company is also commemorating the milestone with limited-edition “Centennial Grey” painted machines available for purchase in 2025.
Caterpillar invites its global employees, customers and all of its stakeholders to join in its 100th anniversary celebrations all year long. To learn more about Caterpillar’s 100th anniversary, please visit caterpillar.com/100.
“Our success over the last 100 years is a testament to the hard work and dedication of our employees, the continued trust of our customers and the support of our dealers and business partners”
Operators of Mecalac’s new Revotruck can now rotate the entire cab to keep their vision and focus on the job and a view of potential obstacles on the site The exclusive chassis with central oscillation ensures stability and traction in all conditions. The infinite cab positions of the Revotruck open up visibility in all directions