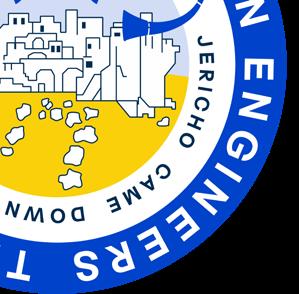

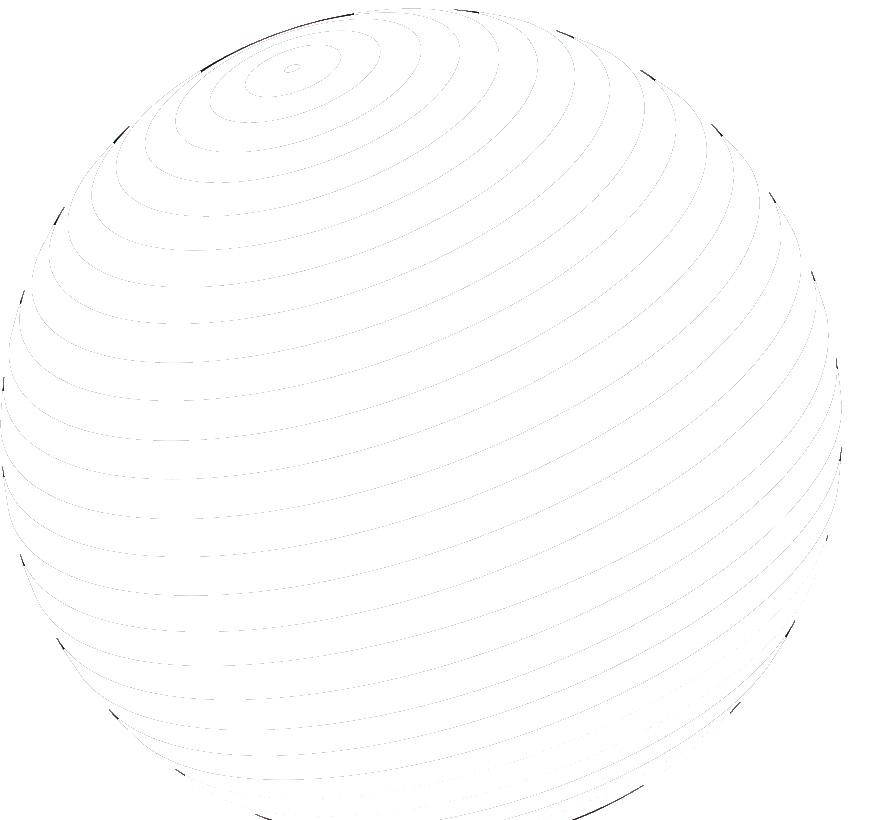
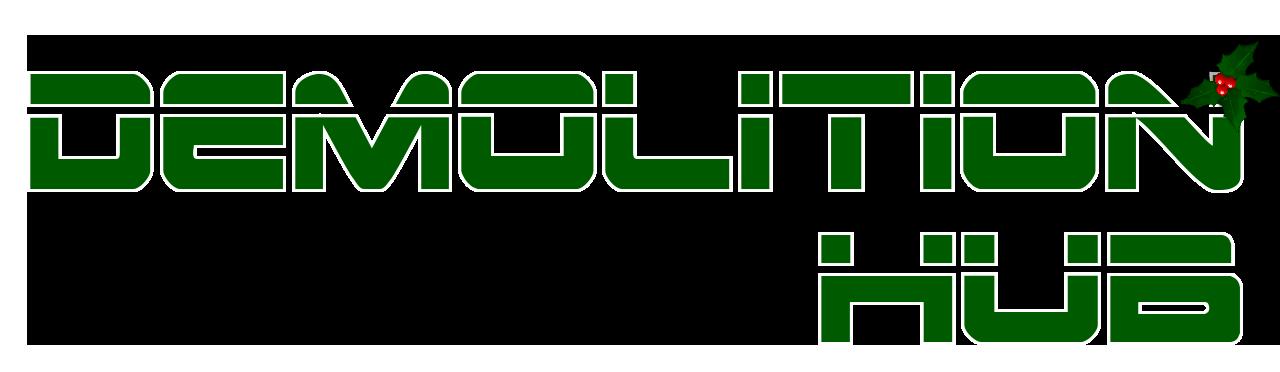
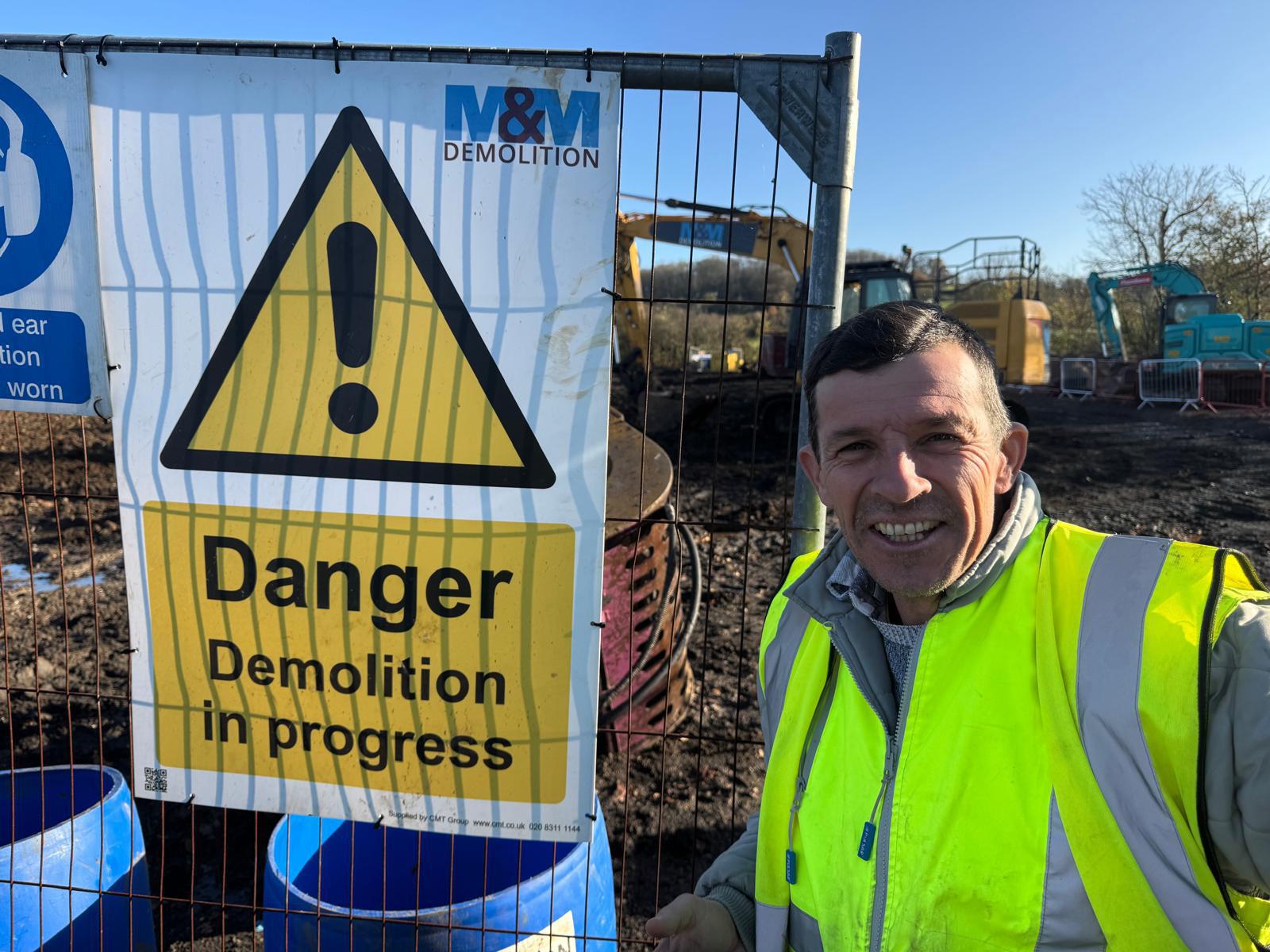
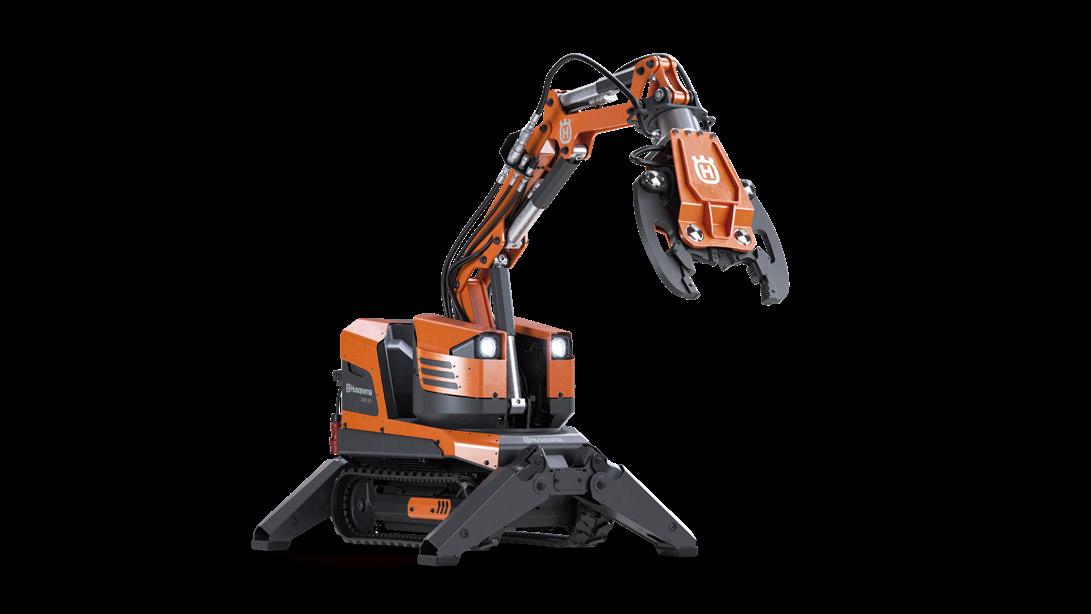
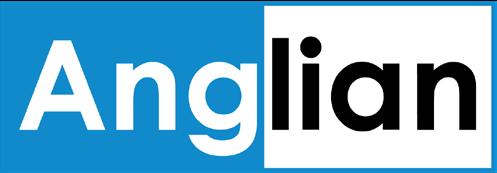
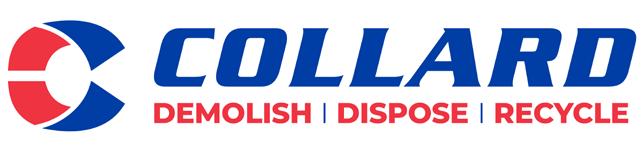
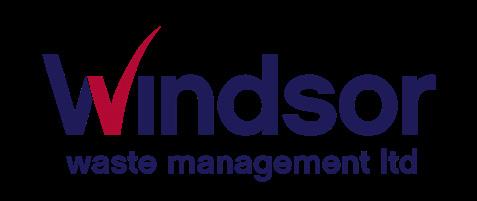
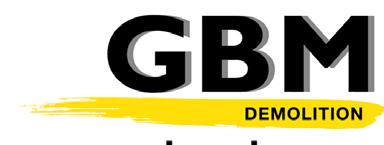
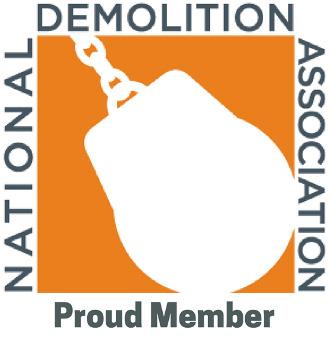

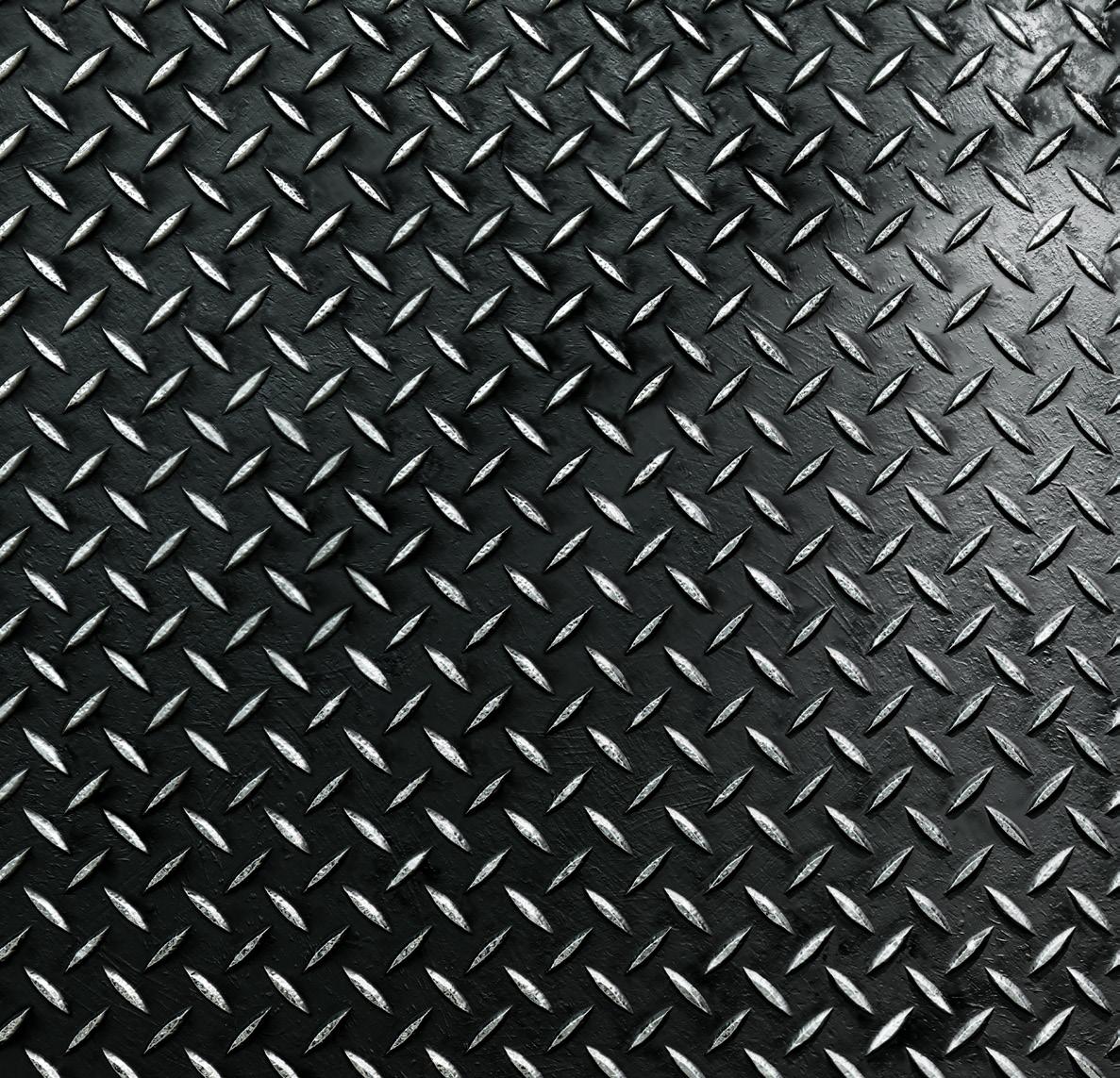

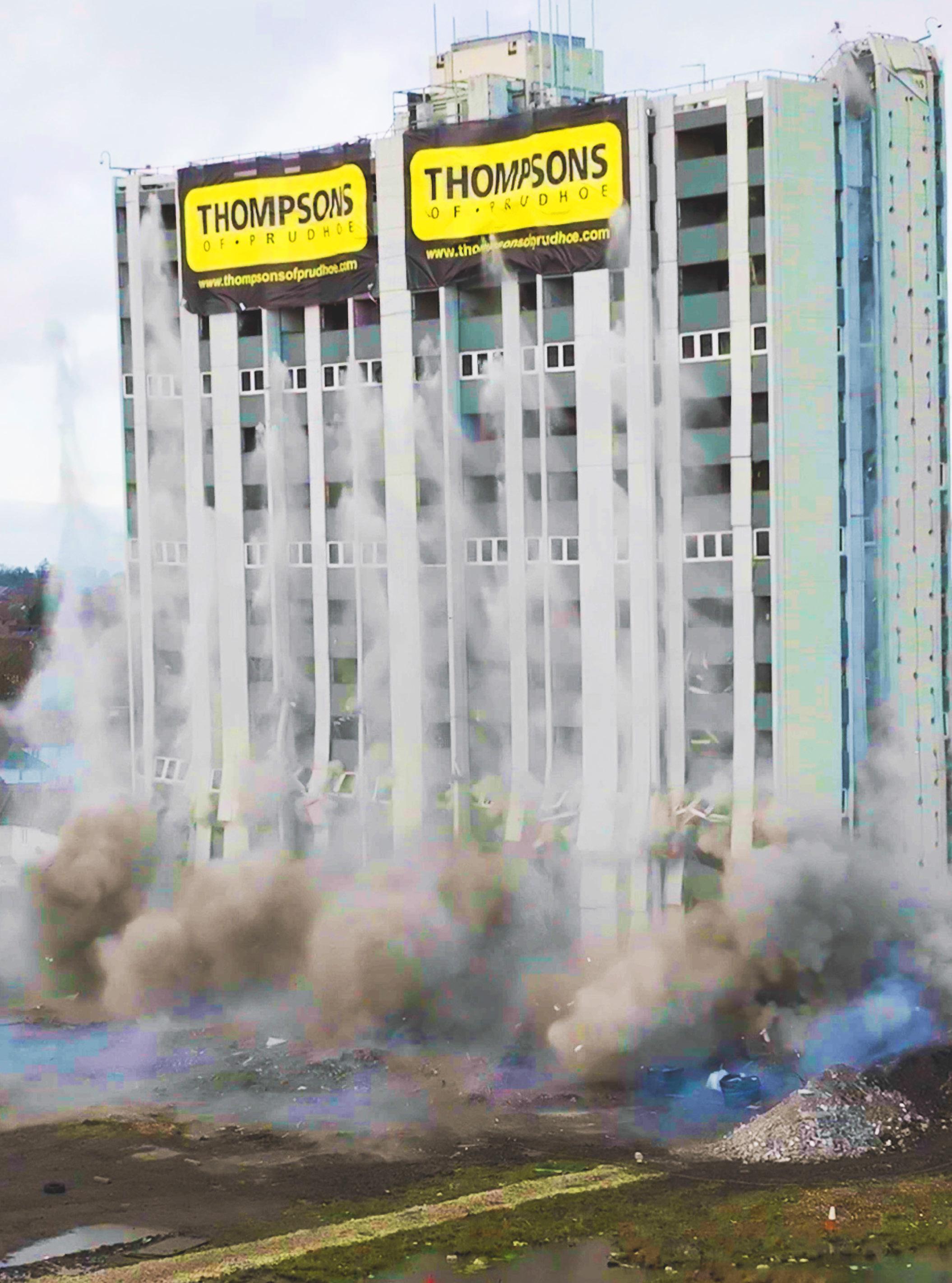
As we close out this final issue of the year –though not the last of our printed content, as we will be swiftly following this edition with the much-anticipated 2025 Demolition Directory & Yearbook – it’s the perfect time to reflect on the many successes across the demolition industry.
One notable highlight is the recent appointment of Adrian McClean as
the new President of the Institute of Demolition Engineers (IDE). His appointment has been met with widespread praise, and there is a palpable sense of anticipation about what his leadership will bring to the institute in the coming years. We look forward to collaborating with Adrian and continuing our strong relationship with the IDE as they embark on this exciting new chapter.
In November, the IDE launched a brilliant new series of online CPD sessions, beginning with an exceptional talk titled Delivering Demolition by Mike Kehoe from C&D Demolition Consultants. While there is no IDE Talk scheduled for December, we’re promised more thought-provoking sessions in the new year and I, for one, can’t wait to tune in.
On the global stage, while the Brits didn’t bring home as much silverware this year, Colemans continued to add to their collection of international accolades by winning the Recycling & Environmental Award at the World Demolition Awards in Sweden. This recognition celebrates their unwavering commitment to sustainability.
Closer to home, the British Demolition sector was well rewarded at the Sixth Annual British Demolition Awards in London. Brown & Mason earned the prestigious title of Demolition Contractor of the Year, while Worsley Plant, a Cheshire-based hydraulic attachment reseller, won Supplier of the Year. The Demolition Safety Innovation of the Year was awarded to Fireward, who treated me to a royal visit at their Essex HQ. Windsor Waste took home the Demolition Waste Provider of the Year award, and the next generation of talent was celebrated with Kayleigh Gerrietty from Brown & Mason winning Apprentice of the Year. Cawarden, a long-time leader in the industry, earned the Environmental Innovation of the Year award, while the Project of the Year awards went to Total Reclaims Demolition (Under £1m) and Downwell Group (Over £1m).
It’s been a remarkable year for the demolition industry, and we look forward to seeing what 2025 has in store. Which leaves me to wish you all a wonderful Christmas before we do this all again in February.
Ben Chambers Publisher, Demolition Hub ben@chambers.media
PUBLISHER
Ben Chambers ben@chambers.media 01903 952 648
EDITOR
Toby Wilsdon toby@chambers.media 01903 952 645
COLUMNISTS
Howard Button
Richard Dolman
Richard Vann
Terry Lloyd
ADVERTISING SALES
Ben Chambers ben@chambers.media 01903 952 648
DESIGN
Joe Chambers joe@chambers.media
PRODUCED & PUBLISHED BY Demolition Hub Ltd
Suites 5 & 6, Chapel House, 1-6 Chapel Road, Worthing, West Sussex BN11 1EX demolition@demolitionhub.com 01903 952 640
Hub is the media partner for the European Demolition Association and the Indian Demolition Association
Demolition Hub is published six times a year. The subscription rate is £60 per year. Subscription records are maintained at Demolition Hub Ltd, Suites 5 & 6, Chapel House, 1-6 Chapel Road, Worthing, West Sussex BN11 1EX
Articles and information contained in this publication are the copyright of Demolition Hub Ltd and may not be reproduced in any form without the written permission of the publishers. The publishers cannot accept responsibility for loss of, or damage to, uncommissioned photographs or manuscripts.
Joint statement on recyclable C&D materials
EU updates Construction Waste Protocol
EDA aligns with EU Pact on skills shortages
Spain’s candidate for Circular Economy Awards
German Demolition Association holds annual congress in Sweden
Launch of Explosive Demolition Working Group
EDA Think Tank 2024
Uncover the EDA Yearbook 2024
More than 100,000 occupational cancer deaths in EU annually
Farewell to Alberto Mantovani
Cutting-edge demolition techniques on the EDA 2025 Study Tour
Venice: the perfect destination for the EDA Convention 2025
Employment: Benefits trends, 2024 and beyond Legal: Managing post-accident communications
Thoughts on the NDA's Certified Demolition
Supervisor programme
Brick by brick – a remarkable dismantling project
Elevating standards with CDS certification
by Howard Button
With Tim Meaney – M&M Demolition Co. Ltd
38
GBM Demolition: The Old Tea Factory, Crewe Collard Group: Watchmoor Park, Camberley
Windsor Waste Management: A34 interchange
Burke Demolition: London Offices
54 CRUSHERS & SCREENERS
FEATURE
Arden Equipment
Crushers Consumables
MB Crusher
Omnia Machinery
Simex
Kleemann
CMS Cepcor
Red Knight 6
72 SUPPLIER TALK
Rise of the machines with Husqvarna
78 OUT AND ABOUT
Snapshots of Ben and the Demolition Hub team’s activities between issues
84 OPINION
Richard Vann: Why less is often more
Terry Lloyd: The next stage of the cycle
Richard Dolman: Getting Britain building again?
88 INDUSTRY
Komatsu integrates artificial intelligence
Anglian Demolition CamLIFE project
Kier Sub-contractor Award
Cat Command for Cat medium wheel loaders
Adrian McClean takes role as IDE President
Clifford Devlin represented at 2025 London Marathon
100 RECRUITMENT
Romax Solution
102
Bobcat Machine IQ takes security to next level
CESAR scheme exceeds 650,000 installations
AI security innovations combat site theft
Demolition Hub is the media partner for the European Demolition Association
A joint statement by the European Quality Association for Recycling (EQAR), the European Demolition Association (EDA) and the European Decontamination Institute (EDI), calls on the European Commission to ensure that recycled mineral construction materials remain exempt from the REACH regulation.
Authored by Martin Car, Secretary General of EQAR, the statement highlights the vital role of recycled materials in the circular economy and the potential negative impact if they were subjected to REACH.
Recycled construction materials, primarily derived from mineral waste like concrete, bricks and asphalt, have been successfully used for over 30 years and represent a significant opportunity to reduce reliance on
primary raw materials.
These materials meet stringent national and EU environmental and technical standards, with thorough pre-demolition audits ensuring harmful substances are removed before recycling.
The statement emphasises that subjecting recycled materials to REACH would increase costs, reduce competitiveness with primary materials and potentially threaten the EU’s target to increase recycling rates.
EQAR, EDA and EDU argue that the current system effectively safeguards health and the environment, making additional REACH requirements unnecessary and detrimental to the industry.
Recycled construction materials have proven to be safe and environmentally friendly and the statement calls for their continued classification as products, not substances, under the REACH regulation.
In 2024, the European Commission has implemented a significant update to the Construction and Demolition Waste (CDW) Management Protocol, replacing the previous version from 2017. This new version aims to further enhance the industry’s practices by promoting more efficient waste management processes, increasing the reuse of products and recycling of materials and fostering environmental, economic and social benefits.
The 2024 protocol continues to emphasise the full CDW management process with key improvements in areas such as:
Pre-demolition and prerenovation audits: Updated protocols now offer more detailed guidelines for identifying reuse potential, hazardous substances and waste streams. Improved site surveys and sampling methods are also included to help assess CDW options.
Selective demolition:
The focus remains on the safe removal and segregation of hazardous materials such as asbestos and improvements have been made in demolition planning and the separation of hazardous from non-hazardous waste.
Enhanced waste logistics:
The new guidelines provide clearer processes for managing waste transport, storage and environmental risks, aiming for better traceability and transparency throughout the waste management chain.
Waste processing and treatment:
The updated protocol highlights newer and more advanced treatment options for various waste types, including concrete, plastic, metals and insulation materials. It focuses on preparing materials for reuse through better cleaning, repairing and recycling methods.
Quality management and policy framework:
The updated protocol strengthens the need for audits, certifications and compliance with new standards to ensure confidence in the reuse of products. It also provides recommendations for regulatory authorities to develop strategies and enforcement mechanisms for CDW management.
This updated protocol addresses the growing need for cooperation between industry stakeholders, authorities and society, ensuring a more sustainable and circular approach to construction and demolition waste across the EU.
The 2024 update brings the sector closer to achieving longterm sustainability goals while providing practical solutions to overcoming regulatory and technical challenges.
In line with the European Commission’s commitment to promoting the European Pillar of Social Rights, Commissioner Roxana Minzatu has been tasked with addressing key challenges in the labour market.
Her mission includes tackling labour and skills shortages, presenting a Quality Jobs Roadmap and launching a new Pact for European Social Dialogue. She will also be responsible for occupational health and safety and labour
mobility, areas crucial to the demolition industry.
Aligned with these European goals, the European Demolition Association (EDA) has taken significant steps to promote professional development within the demolition sector. A new focus has emerged through the Working Group on Professional Development, as highlighted in a recent EDA article. This initiative is closely related to Commissioner Minzatu’s mandate, particularly in
addressing skills shortages and improving job quality across sectors.
The EDA’s Working Group will play a pivotal role in shaping the future of the industry by fostering innovation and enhancing workforce skills. The European Social Dialogue, as part of the Commission’s broader strategy, will create a platform for collaboration between employers, workers and stakeholders across Europe, ensuring that the demolition industry can meet future challenges.
By participating in these discussions, EDA demonstrates its commitment to aligning industry standards with European-level objectives, contributing to safer, more sustainable and skilled employment within the sector. The association is positioned to leverage this new pact to continue advocating for the importance of training and certification in demolition and related industries.
This concerted effort not only responds to immediate labour market needs but also enhances the demolition sector’s long-term contribution to Europe’s economic and social sustainability.
EDA proudly announces Rosnery Castillo as Spain’s candidate for the 2025 Circular Economy Awards.
Rosnery won the 2024 EMA Circular Economy Awards, organised by AEDED, the Spanish Demolition Association, for her outstanding project.
Rosnery Castillo’s nomination, titled “Design and Characterisation of Mortars with Recycled Aggregate from Construction and Demolition Waste (CDW) and End-of-Life Tires (ELT),” stands out for its innovative approach to reusing construction materials, promoting sustainability and the circular economy.
Her work focuses on designing and characterising mortars that incorporate recycled aggregates from Construction and Demolition Waste (CDW) and End-of-Life Tires (ELT). By using these materials, her project aims to reduce
environmental impact and promote sustainable construction practices. This innovative approach enhances the quality of building materials while significantly decreasing waste. This project, already recognised for its excellence at the EMA Awards, will now represent Spain on the European stage.
If the nomination reaches the finalist stage, Rosnery Castillo will be invited to the grand ceremony of the 2025 Circular Economy Awards, which will take place in Venice during the EDA’s annual convention (12-13 June). The event will bring together leaders in demolition and sustainability from across Europe to announce the final winner.
The EDA extends its congratulations to Rosnery Castillo for this significant achievement and wishes her the best of success in the upcoming competition. We are
confident that her hard work and dedication will be acknowledged internationally.
The Circular Economy Awards recognise students who develop innovative projects in circular economy and sustainability within the construction and demolition sectors.
Nominations for the awards are submitted by the national associations of each EDA member country, highlighting the best projects from their respective regions. Spain has a strong track record in the awards, being a finalist in the previous edition, underscoring the high quality of the proposals presented by the country in this important international competition.
The German Demolition Association (DA) successfully concluded its Annual Congress in Eskilstuna, Sweden, from 19-21 September. The event gathered 122 association members for three days of informative sessions, demonstrations and networking opportunities, creating a memorable experience against the scenic backdrop of Sweden’s fjords.
The congress kicked off with a welcome evening at the Munktell Museum where attendees explored an exhibition of innovative technologies. The event provided an ideal setting for networking in the unique Swedish atmosphere.
On September 20, the Member Assembly took place, where DA’s managing board and director Andreas Pocha updated attendees on the association’s activities since 2022. Viola Ridderbusch, Managing Director of DA Service GmbH, highlighted upcoming events such as the FACHKONGRESS
SPRENGTECHNIK in November and the FACHKONGRESS RECYCLING in February 2025. Attendees were also briefed on the highly anticipated FACHTAGUNG ABBRUCH 2025, Europe’s largest demolition conference, to be held in Berlin in March.
The congress featured a thrilling demo show, where participants tested new excavation equipment and explored technical innovations. An alternative city tour of Eskilstuna
was offered for those interested in local history. The evening concluded with a Swedish-themed dinner and lively celebrations.
The event wrapped up with a scenic boat cruise through the Swedish fjords, giving participants time to enjoy the stunning coastline and further connect with industry colleagues.
The next DA Annual Congress will be held in Magdeburg from 1719 September 2026.
The European Demolition Association, known for its ongoing role and leadership in the industry, has launched a new Working Group on Explosive Demolition to help clients understand the basic guidelines for implementing this methodology.
This initiative invites all EDA members interested in explosive demolition to collaborate. The group aims to identify projects where explosive demolition is the
most suitable methodology, and provide a clear explanation of the steps involved to ensure successful implementation.
Deliverable: An informative guide for clients
The main outcome will be the creation of an informative guide, designed to help clients understand the process and benefits of explosive demolition. This guide is scheduled for publication by the end of 2025.
On 9 October, the EDA Think Tank 2024 took place in Brussels. This highly anticipated event brought together leading experts and industry professionals from across Europe. They explored the latest advancements in construction and demolition waste management and pre-demolition audits.
These topics are critical as the industry seeks to adopt more sustainable practices. Moreover, they aim to contribute to a circular economy in Europe.
The first session focused on the new C&D Waste Management Protocol. Key speakers included Florian Flacheneker and Philippe Moseley from the European Commission. The discussion centred on updates to the protocol. These updates included enhanced guidelines for selective demolition. Additionally, there were improved measures for handling hazardous materials like asbestos. The incorporation of
digital building logbooks was also addressed. These advancements aim to improve overall C&D waste management. They will also increase the sector’s capacity for recycling and reuse.
In the second session, Johan D’Hooghe from TRACIMAT led a detailed presentation on predemolition audits. These audits are becoming mandatory in various regions. They apply to large-scale residential and non-residential buildings. D’Hooghe highlighted the role of these audits in ensuring safe demolition processes. Moreover, they protect both human health and the environment.
Furthermore, these audits maximise the potential for material recovery. This process enables more efficient selective demolition. Ultimately, it significantly contributes to the circular economy.
The event featured roundtable
discussions. Experts from Belgium, Germany, Italy and Austria shared their country-specific approaches. They discussed challenges in adopting these new guidelines. Networking opportunities allowed professionals to exchange ideas. Additionally, they collaborated on best practices.
The EDA Think Tank 2024 successfully underscored the importance of refining C&D waste management strategies. It also highlighted the need to apply innovative technologies. This approach aims to achieve greater sustainability in the demolition industry.
With these updates, the European Demolition Association (EDA) continues to lead the way, promoting environmentally responsible demolition practices. This effort paves the way for a greener future across Europe. EDA would like to thank all who participated in this great activity.
The EDA Yearbook 2024, a comprehensive 120-page publication is now available, offering an extensive view of the latest trends, advancements and expert insights across the demolition sector.
Among its rich content, a feature report on demolition with explosives stands out, providing in-depth coverage on the expertise required for large-scale projects using explosives. This report explores the methodologies, safety regulations and technical challenges involved in the safe and effective use of explosives in demolition, showing how these specialised techniques advance complex structural projects.
In addition to this feature, the EDA Yearbook 2024 includes numerous technical articles covering topics in demolition, decontamination and recycling (DDR), addressing innovations in sustainability, safety and efficiency that shape the future of the sector. The publication brings essential insights into how DDR practices are contributing to environmental and economic sustainability, making it a valuable resource for industry professionals.
A unique highlight of this year’s edition is the collaborative insights from national associations worldwide. Each association shares their regional expertise, showcasing the global nature of
advancements in the demolition industry and reinforcing EDA’s commitment to a knowledge-sharing environment.
For anyone in demolition, DDR, or related fields, the EDA Yearbook 2024 is a must-read, offering 120 pages of industry knowledge, trends and technical expertise. This publication, as well as previous editions, is available in hard copy and for free online consultation.
Over 100,000 people die each year in Europe from work-related cancers, primarily caused by exposure to carcinogens. Therefore, the S.T.O.P. Carcinogens at Work initiative is crucial in helping reduce these risks. It provides essential tools and resources for both employers and workers.
Occupational cancer is a major public health issue. Specifically, it affects high-risk industries like construction, manufacturing and agriculture. In addition to this, the initiative offers a searchable database of occupations. This valuable resource helps users identify specific carcinogenic risks associated with different job roles.
As a result, both employers and employees can manage workplace safety more effectively.
Moreover, the initiative focuses on preventive measures. These include risk assessments, safety protocols and safer alternatives to hazardous substances. Consequently, such solutions promote proactive safety practices. This approach ensures a safer working environment across Europe. The initiative provides important facts and statistics and aims to raise awareness about the significant impact of occupational carcinogens on worker health.
By addressing these pressing issues, the S.T.O.P. Carcinogens
at Work initiative plays a vital role. Ultimately, it helps reduce occupational cancer risks and protect workers. For more information and resources, visit the official website at https:// stopcarcinogensatwork.eu.
With deep sadness, Mantovanibenne has announced the passing of its founder and President, Eng. Alberto Mantovani. A visionary pioneer and a key figure in the industry, Mantovani marked the company’s history with unparalleled dedication and an extraordinary capacity for innovation.
Alberto Mantovani founded Mantovanibenne in 1963, taking it from a small family business to one of the leading international players in the hydraulic and recycling equipment sector. Thanks to his entrepreneurial spirit, the company has been able to stand out on the global market, offering cuttingedge solutions that have helped define the quality standards of the entire industry.
Throughout his career, Mantovani demonstrated a tireless commitment to quality and innovation, values that have
guided every step of the company’s growth. His vision has allowed Mantovanibenne to successfully face the challenges of an ever-changing market, promoting solutions that meet the needs of the sector.
Alberto Mantovani’s legacy goes beyond business success. He has passed on to his children and grandchildren the fundamental values that have guided his life and work – vision, innovation and a deep sense of responsibility towards the future of the sector. His ability to imagine tomorrow has left an indelible mark that will continue to inspire the family and all those who are part of the company, accompanying them in the continuation of a path founded on excellence and the continuous search for new solutions.
Mantovanibenne will continue its journey in the name of Alberto Mantovani’s vision and values,
with the aim of honouring his memory through commitment and dedication to excellence. His leadership will continue to inspire everyone who is part of the company.
In this moment of mourning, the Mantovani family and all the collaborators of Mantovanibenne thank those who will join them in remembering Alberto Mantovani, an entrepreneur and an extraordinary man.
Mantovanibenne has been a dedicated and longstanding member of the European Demolition Association (EDA), playing an essential role in advancing our shared goals within the demolition and construction sectors. On behalf of the EDA, we extend our deepest condolences to the Mantovani family and friends, sharing in their grief during this difficult time.
Registration is officially open for the EDA Study Tour Italy 2025. This professional trip promises an immersive experience for professionals in the demolition, decontamination and recycling industries.
Taking place on 8 to 12 June 2025, immediately before the EDA Annual Convention in Venice, the tour will offer participants a unique opportunity to gain insights into some of the most advanced demolition and recycling facilities
across Italy, bringing together experts, cutting-edge technologies and sustainable practices in one of the world’s premier regions for demolition expertise.
Participants will tour various stateof-the-art facilities that showcase innovative technologies and methods. These stops will include companies leading in demolition techniques, construction waste recycling, and sustainable practices.
Each visit will provide a detailed look at equipment, processes, and technologies shaping the future of the industry.
During the tour, you will have the chance to see live demonstrations of modern equipment and hands-on workshops with local experts.
This study tour isn’t just about learning, it’s also about building valuable connections. The itinerary includes several networking sessions where you can meet both local and international professionals. These moments provide a chance to discuss ideas, share experiences and explore potential partnerships.
Whether you’re looking to expand your technical knowledge or stay ahead of the curve in demolition and recycling innovations, this tour offers something for everyone. It’s also a great way to enhance your skills and bring back new techniques to your organisation.
The EDA is thrilled to announce that registrations are now open for the 2025 Annual Convention of the European Demolition Association. Join us from 12 to 13 June for an unforgettable event at the historic Palazzo del Casinò located within the renowned Venice Convention Centre on the scenic Lido island in the breathtaking setting of Venice.
This venue, known for its grandeur and history, offers stateof-the-art facilities and a stunning setting, making it an ideal location. In collaboration with the European Decontamination Institute, EDI and NADECO, the National Association of Demolition and Circular Economy for Construction in Italy, the convention will bring together professionals and stakeholders from the demolition, decontamination, and recycling (DDR) industries worldwide to connect, learn and collaborate, exploring the future of demolition, recycling and the circular economy.
The convention will provide unparalleled opportunities to expand your network, gain insights from global experts and participate in discussions shaping the future of demolition and deconstruction. The programme will include high-level presentations, engaging workshops and panels focusing on the latest
trends, technologies and best practices in the sector.
Whether you’re seeking to stay informed on industry updates or to exchange knowledge with like-minded professionals, this convention offers something for everyone. Participants will leave with enhanced perspectives on sustainable practices and innovations in demolition, along with valuable professional contacts.
Early registration is recommended, as spaces are limited and demand is high.
The EDA Annual Convention has built a reputation as a premier gathering for exchanging innovative ideas, addressing industry challenges and setting benchmarks for the future
and the EDA invites experts, industry leaders and researchers to submit proposals to speak at the convention in 2025.
If you have practical case studies, research findings or thought-provoking insights related to demolition and deconstruction, this is your chance to share your expertise on an international platform.
Submissions should focus on topics relevant to the EDA’s objectives and the demolition, decontamination and recycling activities, including innovations in C&D resource management, circular economy strategies, safety advancements and sustainable practices. Presenting at this convention will position you as a thought leader and allow you to contribute to shaping the future of the industry.
Papers submitted for presentation will be evaluated by the EDA Board of Directors. Selected speakers will be notified with ample time to prepare their presentations and will receive free registration to the professional programme.
Don’t miss this opportunity to contribute to a high-impact agenda and connect with industry pioneers. The deadline for submissions is 7 February 2025.
Programme
The convention’s programme includes sessions covering the latest trends, technological advancements and regulatory updates in the sector, with speakers and panel discussions featuring prominent industry experts. Attendees will have opportunities to exchange ideas, gain insights from thought leaders and participate in workshops and conferences designed to address real-world challenges and innovations in demolition and environmental management.
To foster networking and connections in more informal settings, the EDA has arranged a Welcome Cocktail on 12 June at the iconic Murano Glass Cathedral. This artistic venue, famous for its architecture and craftsmanship, will allow attendees to unwind and socialise in a unique Venetian setting. The Murano Glass Cathedral, with its rich history in glass artistry, embodies the cultural significance of Venice and offers attendees a memorable start to the convention.
On Friday 13 June, the convention will culminate with an exquisite gala dinner at the Pescheria di Rialto, a historic fish market dating back to the 11th century. The setting provides a remarkable fusion of tradition and elegance, allowing attendees to enjoy the evening by the Grand Canal in an authentically Venetian atmosphere. This event is designed to be an intimate experience, where colleagues and industry leaders can celebrate achievements, discuss future collaborations, and expand professional networks in a friendly and inviting ambiance.
Preliminary programme
Thursday 12 June – Reception and accreditation of participants
15:00 Circular Economy Awards presentations
16:30 EDA General Assembly (for EDA members only)
19:30 Welcome Cocktail at Murano Glass Cathedral
Friday 13 June – Multilingual conferences with simultaneous interpretation
8:30 Reception and accreditation of the participants
9:00 Official opening
Conference Session 1
Coffee break, networking and exhibition
Conference Session 2
Circular Economy Awards winner announcement
Lunch, networking and exhibition
Conference Session 3
Coffee break, networking and exhibition
Conference Session 4
17:00 End of professional programme
20:00 Gala Dinner at Pescheria Di Rialto
Leisure programme for companions – Friday 13 June
This guided walking tour will take you through Venice’s charming “calli” (narrow streets) and “campielli” (small squares) for an intimate look at the city’s hidden gems.
Starting with a private water taxi transfer from the Hotel Excelsior to St Mark’s, you’ll embark on a journey with a knowledgeable guide, discovering Venice’s rich history, stunning Gothic and Byzantine architecture and iconic landmarks like the Church of San Giovanni e Paolo.
The tour will wrap up with a traditional lunch in a cosy square, followed by some free time for shopping before your water taxi back to the hotel.
Leisure programme for all participants – Saturday 14 June
This guided walk will take you through Venice’s charming “calli” (narrow streets) and “campielli” (small squares), discovering hidden gems and landmarks like the Church of San Giovanni e Paolo. Start with a water taxi transfer from the Hotel Excelsior and enjoy Venice’s history and architecture along the way. The tour concludes with a traditional lunch and free time before returning to the hotel.
Marketing opportunities Unlock unparalleled visibility for your company within the industry by becoming a sponsor of the EDA Annual Convention 2025. This unique opportunity ensures your brand shines before, during, and
after the event, reaching a highly engaged audience of industry leaders and professionals.
Act fast, sponsorship slots are limited and will be allocated on a first-come, first-served basis. Gold, Silver and Bronze sponsorship packages are available.
Stand out and make a lasting impression at the EDA event by choosing from our exclusive sponsorship options. These complementary opportunities are designed to reinforce your participation and differentiate your brand.
Exclusive sponsorships: Gala dinner
Welcome cocktail Lanyard
Conference materials Delegate bag
www.europeandemolition.org/ activities/eda-annualconvention-2025
by Nicholas Ritchie
In the second half of 2024, several trends in traditional and nontraditional benefits are poised to transform the human resources and benefits landscapes.
Rapid technological advancements and shifting employee expectations have added another layer to recruiting and retaining top talent. The world of employee benefits must evolve to meet the changing needs of the workforce.
Traditional benefits like health insurance, retirement plans and paid time off serve as hygiene factors or factors that help prevent employee dissatisfaction. On the other hand, a focus on creative and non-traditional benefits can provide a valuable motivation to employees.
A combination of hygiene and motivational factors is necessary to maintain a productive workforce. Let’s look at the traditional and creative benefits trends for 2024 and beyond.
Traditional benefits typically satisfy essential employee expectations and will continue to be a cornerstone of a competitive benefits package.
Insurance
Insurance remains a cornerstone of employee benefits, with a growing
emphasis on expanding coverage and reducing costs. According to a Census.gov survey, 86% of privatesector employers offer employersponsored health insurance.
Employees value a variety of health benefits, including comprehensive health plans with vision and dental coverage. The Kaiser Family Foundation reports that in 2020, the average coinsurance rates for employersponsored health insurance plans were 18% for primary care, 19% for speciality care, and 20% for hospital admissions and outpatient surgery.
More organisations are offering customised health benefits options or cafeteria plans to enhance their benefits packages. Health savings accounts (HSAs) enable employees with high-deductible health plans to save pre-tax funds for medical expenses, with the advantage of rolling over unused funds from year to year.
Flexible spending accounts (FSAs) also contribute to a robust benefits plan. The U.S. Department of Labor notes that the percentage of private industry workers with access to flexible health care spending accounts increased from 36% in 2012 to 43% in 2021. Unlike HSAs, FSAs do not require enrolment in a high-deductible plan and provide
similar pre-tax benefits for medical expenses, although funds do not roll over and contribution limits are lower. Additionally, HSAs are portable from employer to employer, whereas FSAs are not.
Paid time off (PTO) is crucial for maintaining work-life balance and employee wellbeing. In 2024, companies increasingly offer flexible PTO policies, a move away from separate vacation, sick leave and personal time banks, allowing employees to take time off for vacation, sick leave or personal reasons.
While PTO on an accrual basis remains common and serves as an employee motivator, the added flexibility in PTO and holidays helps employees manage their time effectively, reducing burnout and promoting overall wellbeing. This, in turn, enhances job satisfaction and performance.
A Bureau of Labor Statistics study explored PTO offerings, revealing that on average, employees receive eight days of vacation after one year, 10 days after three years, 14 days after 10 years and 16 days after 25 years.
These averages show the evolving standards in PTO offerings and can be a helpful benchmarking tool. However, it’s notable that 52% of employees report working while on PTO, indicating a need for better boundaries and support during time off.
Employers must incentivise the use of PTO if it is provided, otherwise employees may feel unsatisfied and the investment in these benefits could be well-spent. Forbes Advisor says nearly a third of employees (31%) report PTO as a top benefit. Additionally, organisations in 2024 are more frequently offering
summer hours, shortened workweeks like four-day schedules, and sabbatical leave programmes to support personal and professional development.
Retirement plans are paramount for the long-term financial security of employees. Companies are strengthening their retirement benefits by modifying employer contributions or offering matching programmes to help employees save for the future.
In addition to traditional offerings, some organisations are revisiting retirement options such as the defined benefit plan to give employees more flexibility. Multiple retirement options are now being offered by some organisations.
Additionally, an upcoming regulatory change will make automatic enrolment obligatory for all 401(k) and 403(b) plans established after 29 December 2022. This change will go into effect in January 2025. Plans established before this date will be “grandfathered in” and exempt
from the automatic enrolment obligation. In theory, this change should incentivise employee financial wellness, simplify access to retirement savings and encourage higher participation rates.
A creative benefits package can be a source of competitive advantage, serving as a strong motivator toward employee satisfaction, wellbeing and performance. Here are some trends we’re seeing:
Flexible work arrangements have become popular since the Covid-19 pandemic and continue to be valued years later. While challenging, flexibility offers employees greater autonomy and work-life balance. Companies are expanding their remote work policies and hybrid work models to accommodate employee needs.
Innovative organisations are limiting burnout and improving performance by moving to a fourday workweek or making other adjustments to work arrangements.
A recent study by Upwork estimates that 32.6 million Americans will work remotely in 2025, highlighting the growing need for flexibility in work locations, environments and arrangements.
In addition to statutory benefits like maternity and paternity leave, many companies are prioritising work-life balance and family-related benefits. Offerings may include extended parental leave and childcare assistance programmes.
Organisations also recognise the need for elder care support, helping employees care for aging parents or relatives. Some companies go above and beyond with pet care, pet insurance and other subsidies for employees’ fourlegged friends.
The focus on mental health and wellbeing has intensified, driven by the recognition of its significant impact on employee productivity and satisfaction. In addition to traditional employee assistance programmes, companies are implementing comprehensive mental health initiatives, with some even staffing mental health providers to offer more extensive support than typical health insurance covers.
These programmes are designed to provide multiple levels of support, including access to therapists and counsellors in-person and through telehealth services.
Promoting physical health and wellness remains a priority in 2024, with companies incentivising healthy behaviours through various health and fitness programmes, such as subsidies for gym memberships and encouraging employees to prioritise their physical wellbeing. Demolition
by Adam R Young
Some employers will never experience a serious workplace accident involving personal injury, property damage or both. If one of these unfortunate accidents occurs, this article provides recommendations to respond in a forthright manner while avoiding potential additional legal liability and a public relations fiasco.
Scenario
An accident just occurred at one of your company’s worksites, injuring an employee. Upset employees across the country are calling and emailing each other, speculating on the root causes of the accident, the inadequacies of safety procedures and the company’s response to the accident. One email even suggests that the company knew about the hazard and wilfully exposed the employee.
Any of the unfounded speculations in these emails could
serve as a “smoking gun,” supporting a personal injury plaintiff and his attorney or an Occupational Safety and Health Administration (OSHA) compliance officer’s theory as to why the company could be liable for the accident. If the accident resulted in a fatality, a manager could face a criminal prosecution by the Department of Justice, a $250,000 personal fine and six months in federal prison. If employee interviews are not properly managed and employees provide false or untruthful information, including documents, to OSHA, there can be personal criminal liability for lying or obstruction of justice.
Advances in communication technologies (e.g., smartphones) have made communication easier and faster than ever. These communications will now be preserved digitally for future litigation, and the legal risks of miscommunications have become far more serious. Studies indicate that the period immediately following an accident is a breeding ground for workplace miscommunications – rampant communications with the lowest instances of factual accuracy and containing potential unfounded “admissions” of company or management liability in the form of “finger-pointing.”
Employers need to develop crisis management policies and train employees to restrict their communications to accurate information and avoid speculations
that could hurt the company. The company should have a crisis communication plan in place to centralise information flows through a designated company spokesperson and inform the appropriate authorities regarding crisis response. The company must regulate what statements are made and be careful to create and maintain legal privileges including attorney-client privilege and work product, where applicable.
The best way to prevent a communications mishaps following a workplace accident is to have comprehensive and effective policies in place beforehand that informs employees on how to communicate. With a careful communications policy, employers can train employees to think ahead, scrutinise their methods of communication and limit their communications to accurate and necessary information. With this policy, employees will be mindful of the need for coordinated communications that are based on whether there is a “need to know” the information before communicating it internally or to third parties. The basic elements of a careful communications policy are:
The policy should help employees evaluate whether an email is the necessary and preferable form of communication. Communications
made on social media may not be private (regardless of the employee’s privacy settings) and may not be deleted. Social media comments must be prohibited as a means of disseminating authorised company communications.
Employees are required to evaluate who will be the audience for the communications and how the sender can carefully craft the communication to be appropriate for the audience. In a crisis, this may require the sender to limit technical language and detail for a high-level audience for the communication to be effective.
Employees should be instructed to speak factually in all authorised communications and emails. Their communications should clearly state facts of which they have first-hand knowledge and therefore are credible. Relaying hearsay information that may not be credible since it may be nothing more than “gossip” and needs to be prohibited.
Employees should be instructed to avoid speculations, including unfounded “opinions” on what may have occurred or assessing “fault” or “blame” in emails, particularly on areas outside of their expertise. Absent specialised knowledge, speculations and assumptions result in inaccurate communications.
Workplace communications such as email and text should maintain a level of professionalism akin to respectful in-person communication. A professionalism provision will help prevent harassing, offensive and retaliatory communications.
Sometimes documentation is necessary to confirm that employers have timely responded and corrected or abated hazards. Employee discipline, particularly with regard to addressing potential violations of safety rules that may have caused or contributed to the accident, should be carefully scrutinised before being committed to a documentary format.
Employees should follow the company’s record-retention guidelines for maintaining documents, including those containing electronically stored information (ESI). In some cases, the documents generated may need to be retained by law, for example, those documents that may constitute ESI and may relate to potential litigation. The company will have to issue a “litigation hold” notice within the company to preserve such documentation.
Employees should consider obtaining a second opinion on communications that are questionable through the designated company spokesperson or legal counsel.
The greatest risks may come from impulsive emails sent under the stresses and strains of a workplace accident. In many cases, there is a knee-jerk reaction to a serious accident in which employees express shock, outrage or disgust about
the occurrence through internal or external communications. The policy should direct employees to consider talking through issues rather than writing an emotional email, or to save a draft and review it after the emotional environment has subsided.
For reasons outlined above, employers should have a crisis communication plan in place to manage communications during a crisis. The plan will instruct employees on how to centralise information, release verified information, deliver a pre-written initial press statement, deal with rumours, and keep accurate logs of inquiries and news coverage. The crisis communication plan will prohibit speculation on the causes of the accident or the time for resolving a crisis. The plan will prohibit the release of any information potentially placing blame for the crisis, misleading the media, and releasing information that is confidential or privileged, unless it has been cleared by the communications department or the crisis team.
With regard to the physical site of an accident, the plan will designate who will control access to the site and who will escort and monitor third parties on the site. An effective crisis communications plan will simplify information management, provide employees with a resource for accurate information and limit potential sources of miscommunications, particularly to the media or third parties.
The attorney-client privilege only protects communication between an attorney and a client in which legal advice was sought or rendered and which was intended to be and
was in fact kept confidential. This means a client cannot protect facts simply by incorporating them into a communication with the attorney. Merely cc’ing in-house counsel will not create an attorney-client privilege. Where the client also seeks business advice, the communication will only be protected so far as the communications concern the provision of legal advice. Accordingly, employers should take caution with regard to attorney-client privilege and limit emails to attorneys to legal advice. Attorney-client privileged communications should be appropriately labelled in the email or other correspondence, for example, “Privileged and Confidential Legal Matter.”
As discussed above, to be protected by the attorney-client privilege, a communication must reasonably have been intended to be confidential. This includes documents generated by or at the direction of legal counsel that are the attorney’s “work product”. Work product cannot be disseminated within the company to employees who are outside of the “control group” – that is, those employees whose job responsibilities will require them to have access to and utilise the work product to make decisions affecting the company within their area of responsibility. Dissemination beyond the control group can result in waiver of the legal privilege and make work product discoverable in litigation. The communication must not be shared with any third party, which will waive the privilege. Where an attorney seeks information, the attorney’s discussions with an employee may generally be shared with other designated non-attorney employees and still maintain
Our unique capability to repurpose virtually all construction and demolition waste from site helps our public sector, local authority, commercial and residential clients achieve zero-to-landfill targets.
Demolition
Structural alterations
Site clearance
Soft strip
Asbestos management
Remediation
Earthworks & civils
Temporary works
Joseph C. Hopewell, a project manager at NDA member company
JR Ramon Demolition, was in the first class of people to earn NDA’s Certified Demolition Supervisor (CDS) certification in 2023. We caught up with Hopewell to learn more about his experience with the programme.
What motivated you to pursue the CDS certification?
I previously worked in residential and multifamily restoration for years, and I wanted to make the transition to commercial work for a long time. A big factor in my becoming jaded with the restoration business was an overall lack of professionalism, credentialing and training in the industry. It was not typically encouraged nor were there many opportunities to certify yourself or advance your career.
When NDA’s CDS programme came around, it was exactly the kind of programme I was hoping to be a part of when I joined the demolition industry, so I was more
than enthusiastic about the chance to take part.
How would you characterise the process of obtaining the CDS certification?
I think NDA did a great job developing this programme and took the time to get it right. It was very similar to other, more established certifications and exams I have received. The process left me with the impression that if an individual is qualified and has the experience, they will justifiably receive the certification. In addition, NDA can be confident the individuals who do successfully achieve this certification are the calibre of professionals they envisioned when developing this programme.
How has the CDS certification enhanced your skills and knowledge in the field of demolition?
The process of preparing for the exam definitely helped me brush up on my knowledge and revisit
certain aspects of the work we do that perhaps I was rusty on or hadn’t thought about in some time. I have found that any time I do this, it is always a good way to get back to basics and avoid complacency. In addition, when I go through such a process, I inevitably learn something new or gain a better perspective. For this reason, I am glad to see the programme includes continuing education requirements because that will be a great way for all of us to stay up to date with the industry and continue to improve our skills for years to come.
In what ways has the CDS certification helped you in maintaining high safety standards in demolition practices?
Safety is a huge part of our industry and, in my opinion, the most important aspect of our job. Again, going back to my previous industry, safety standards and knowledge were relatively non-existent compared to what I’m accustomed to now. For this reason, I’m glad to see that safety practices constituted a significant portion of the exam, and thanks to the continuing education requirements, it will encourage me to continue taking part in further safety certifications and courses in the future.
What would you say to other professionals considering pursuing the CDS certification?
Without a doubt, if you are serious about your career in demolition, you will absolutely benefit from the process of getting certified and gain a great sense of accomplishment from doing so. I encourage all my peers to do so because the more we improve ourselves, the more we improve our industry, and that raises the tide for all of us.
MAXIMUM PERFORMANCE
LOWEST OPERATIONAL COSTS
HIGHEST RELIABILITY
The historic El Rancho Hotel in Gallup, New Mexico, is a cherished landmark with a rich history dating back to the 1930s. However, its iconic 21-metre brick chimney had begun to deteriorate, posing a significant risk to the hotel and its surroundings. Several bricks had already fallen onto the hotel’s roof and deep cracks in the chimney indicated an imminent collapse.
Demolition was needed, but the challenges were numerous. The chimney was situated just 300 mm from the historic building, a power transformer needed to remain online during the demolition and nearby utilities, including ductwork, a gas main, windows and chillers, required protection. To top it off, active overhead power lines limited access to the site.
NDA member BCS Enterprises was chosen for the project due to the company’s innovative approach and ability to address the owners’ concerns effectively. After a thorough site visit, the team produced a 3D model to develop their methodology. “We find developing these models helps minimise any potential oversights and uncertainties on the job,” says Casey Johansen, BCS Enterprises’ director of operations.
The project kicked off with initial planning in May 2023 and was awarded that same month.
Design and fabrication of the modular protection system began immediately. Demolition
commenced on 31 July 2023 and the entire chimney was removed and loaded out in just one week.
The equipment used for the project included a 275-tonne mobile crane, a Brokk 160 with a custom frame bracket, a 41-metre boom lift and a Cat 310 excavator.
The demolition strategy devised by BCS Enterprises was truly unique. The team needed to bring the chimney down within its own footprint, ensuring that materials fell in a controlled manner to avoid damaging the surrounding roof and utilities. To achieve this, a threesection modular protection box was designed and built to fit precisely around the chimney. One corner of the box was designed as a chute for the material to fall at the location farthest from all obstacles.
“The crane suspended our box in the air with the Brokk 160 robotic excavator directly mounted to the side,” Johansen says. “The crane lowered the box as we delicately hammered the chimney down. Sections of the protection box were removed as the work progressed downward.”
The demolition process began with the mobilisation of all equipment from BCS Enterprises’ yard in Phoenix. Protections were installed over windows and surrounding utilities. After the crane was set up, the protection box was lifted over the power lines and carefully guided around the chimney. The Brokk 160 was then bolted into place and the
Demolition Hub is a proud member of the National Demolition Association
crane lifted the system above the top of the chimney to begin the demolition.
The Brokk operator and a spotter worked from a boom lift at a safe distance from the chimney, guiding debris to the chute corner of the box. A Cat 310 excavator was used to load out the material, carefully working around power lines and utilities.
As demolition proceeded down the chimney, the protection box was lowered by the crane, and sections were removed. Finally, the last box section was removed, and the remaining three metres of the chimney base was carefully demolished with the Cat 310 excavator.
The demolition team consisted of nine people, including a superintendent, an operator, two spotters, a mechanic, a truck driver, a safety officer, a crane operator and a rigger. All the bricks from the chimney were recycled and brought to a nearby facility to be repurposed.
One of the biggest challenges of the project was working around utilities while avoiding any disruption to hotel operations. “Careful planning, protective measures and the use of multiple spotters helped to overcome the challenge,” Johansen says.
The project was completed safely, on time and on budget, with the chimney removed without causing any damage to the surrounding property. “Success to us means completing the project safely, efficiently and to the client’s satisfaction,” Johansen says.
BCS Enterprises’ unique approach to this challenging project exemplifies the company’s expertise and commitment to delivering innovative and safe demolition solutions. BCS Enterprises’ ability to overcome complex challenges while preserving the historic integrity of the El Rancho Hotel serves as a testament to its skill and dedication in the demolition industry.
In the demolition industry, safety, expertise and leadership are essential. The National Demolition Association (NDA) knows that deeply, and its Certified Demolition Supervisor (CDS) certification stands as a crucial measure of professional competence. The CDS validates the capabilities of supervisors in handling complex demolition projects while reinforcing a commitment to safety and efficiency.
Industry veterans, Jeff Sessler of Sessler Wrecking and Don Collier of MILBURN Demolition, offer their insights on the importance of the CDS certification and why it is becoming a standard in the industry.
For Sessler, the decision to encourage his team at Sessler Wrecking to pursue the CDS certification comes down to ensuring his workforce is equipped with the knowledge to handle the industry’s challenges. “The CDS is a thorough way to ensure you have the right people with the right knowledge running the work and leading the team safely and efficiently,” he says. With five employees already certified and more in the pipeline, Sessler Wrecking is setting a high bar for industry standards.
As a company that mandates
OSHA 30 training, Sessler is moving toward making the CDS a requirement for anyone to hold the title of superintendent. “The demolition industry is extremely complex, and some sites change conditions daily, or even faster. It’s making sure that your team is led by someone who has the experience and expertise,” he says. This focus on safety and leadership is what separates those certified through the CDS programme from others in the industry.
Don Collier of MILBURN Demolition shares similar sentiments. Having been involved with the NDA Certification Board
from the programme’s inception, Collier views the CDS certification as a badge of honour for those willing to put in the effort. “It’s a true national measurement to test their abilities to be a safe and successful, high-level field supervisor,” Collier says. He further explains that the CDS certification helps distinguish between those who simply want to lead and those who are truly qualified. “It vets out the ‘wanters’ from the qualified people,” he adds, pointing to the rigorous nature of the certification process.
Both Sessler and Collier recognise the unique challenges that come with managing demolition projects. These challenges are one of the reasons why the CDS programme has been carefully structured to address the real-world complexities of the industry. “The programme ensures that there is a thorough knowledge of all aspects of demolition and prioritises safety,” Sessler says. He acknowledges that certification is increasingly being required in job specifications, giving companies like Sessler Wrecking a competitive edge. “We’ve been awarded work by showing the additional trainings that our superintendents carry,” he says.
Collier expands on this point, highlighting the years of experience and effort that have gone into developing the CDS certification. “We really put time and effort into making it unique,” he says. “The processes that have been put in place, from the sponsorships to the way the exam content is structured, all ensure that those earning the CDS are truly qualified to lead.” According to Collier, the certification is designed to maintain a high standard in the industry, something that benefits not only the certified individuals but
the companies they work for and the industry as a whole.
For companies that may not yet be actively encouraging CDS certification, both Sessler and Collier have strong words of advice. Sessler says that the certification can advance individual careers while also benefiting the entire organisation. “If you want to advance yourself, get the certification,” he says. “It shows that you are a leader willing to take the time to become certified to be a better leader for your team and organisation.”
Collier is equally passionate about the benefits of the CDS certification, particularly when it comes to safety and profitability. “We’re trying as a group here to raise the bar and the standards in the industry, to keep all of the field workers safe and successful, and that all starts with leadership,” he says. For him, the equation is simple: “If you keep an organised project, and you run it safely and successfully, and you have a talented supervisor, you’re making money.”
For those considering pursuing the CDS certification, Collier offers practical advice. “The CDS programme is not for everybody. It’s for those high-level supervisors that want more,” he says. His key recommendation for potential candidates is preparation: “Go over the content outline, go over the reference material, and do it again.” When it comes time to sit for the exam, Collier’s final piece of advice is simple: “Relax, take a breath and choose with your gut, because those people are the people that we want.”
Sessler concurs, stressing
that the CDS certification is an investment in both individual careers and the future success of demolition companies. By obtaining the certification, supervisors can demonstrate their commitment to leading safely and efficiently in one of the most challenging industries.
As the demolition industry continues to evolve, the CDS certification is proving to be a critical tool in elevating safety standards and leadership quality across the field.
“It shows that you are a leader willing to take the time to become certified to be a better leader for your team and organisation”
I must start my column this month on a sombre note and talk briefly about prostate cancer. We have recently seen the shock news that the Olympic gold-medal-winning cyclist Sir Chris Hoy has announced that his cancer diagnosis is terminal, bringing the shocking lack of awareness under the spotlight.
Chris states: “It’s been the toughest year of our lives so far by some stretch,” with the news that he had a terminal illness in September 2023 coming “out the blue. No symptoms, no warnings, nothing. All I had was a pain in my shoulder and a little bit of pain in my ribs.”
Sadly, far too many men are affected by this silent killer and I speak from personal experience. Despite my father dying from prostate cancer at 67 I was not flagged as a possible case and it was not until I noticed blood in my urine that my doctor gave me a simple PSA test, which unfortunately returned as positive.
My personal battle against prostate cancer has been extremely hard at times and this year I took what I thought was the final solution to have my prostate surgically removed. I won’t go into details but if anyone ever wants to talk I am
always happy to try and help.
My final comment on this is, get your PSA blood test. The sooner you can, the greater chance you have of recovery.
Now back to my favourite subject, demolition.
I spotted a press release this month reporting that the prestigious RIBA Stirling Prize for architecture had been given to Transport for London ’s Elizabeth Line (Crossrail). “The Elizabeth Line is a result of a remarkable collaboration between architects, engineers and designers.” Rightly so, an outstanding achievement and a line I now use regularly.
Ironically, shortly after the announcement it was reported that another RIBA Stirling Prize winner, the 29-year-old Centenary Building at the University of Salford, which has sat empty for nearly a decade, is to be demolished.
Well, I have to ask where RIBA stands. They have openly criticised the demolition sector for the “unnecessary” demolition of buildings that could be repurposed, yet their prize was awarded to a structure that was never designed to be retrofitted and I doubt any thought was ever given to disassembly to allow the reuse of key building components.
When will the highbrow architects learn that if they want to see their fantastic designs as part of the circular hub we are all striving for, they need to listen to the demolition professionals? Perhaps joining the next IDE online talk focusing on the reuse of steel from demolition would be good place to start.
See you all online for Back to the Future; Steel Reuse in Demolition at 7.30pm on 30 January 2025. It’s FREE.
If you have something to say and would like to submit a column for publication in Demolition Hub, please email: toby@chambers.media
Interviewee:
Tim Meaney
Role: Contracts Manager
Company:
QHow did you start out in the demolition industry?
It’s been well over 20 years now since I was introduced to this rollercoaster industry and I wouldn’t change a thing. I was lucky enough to know the people I would start my journey with as my mates and what was meant to be a three-week stopgap turned out to be my life as I know it.
From having a pint in the local on darts night to standing on top of a scaffold in the middle
of London with a breaker in hand gunning concrete off steel beams and razing a building to the ground –tough work, tougher men and great times. I had to learn quick and keep up.
QHow has your career progressed?
Being from a farming background and having a little experience around various types of machinery, it was not long before I got the chance to try my hand on an excavator –the well-looked-after Daewoo 280, my supervisor’s pride and joy. He certainly could handle it and taught me well.
I loaded my first bin and was soon on my way to NVQ level operator obtaining D90 and running my own projects. Thankfully I was accepted into the company fold, we gelled well and I stayed there 17 years. I will always be grateful to these people and we remain friends to this day.
It was at this point that I decided to stretch my knowledge and experience how others worked to broaden my range of skills. After a few years of moving about I finally put in to do my Gold Supervisor card and settled in with my now close friends at M&M Demolition, where I received further mentoring and guidance and was given the opportunity to manage sites on behalf of this wonderful company. Its been a tricky road at times but I wouldn’t change anything. It led me here and I’m happy.
QHow did M&M Demolition start and how has it evolved?
M&M was started in 1964 by brothers Dave and Gary Madden. In 2014 it became available as a going concern and was bought by its current owners. All it had was a name and it needed some serious investment to make it a viable company. Rebranding and time has slowly elevated M&M from flat on the floor to its current status as a self-sustaining company with decent turnover and a great client list ranging from private developers to local government.
Constant investment in staff, training, assets and marketing has been key to raising this phoenix from the ashes.
QTell us about your team and working culture
Fundamentally M&M’s priority is to survive. Having said that, its people go hand in hand with the company on the priority list as it’s the people that make the company. Our working culture involves adopting an open book policy from senior to site management with the information highway always open.
“Onwards and upwards” has been a mantra of mine for many years and this is the positivity I promote with my colleagues in everything we do. I still get dirty from time to time with the boys and girls on site. I cannot ask anyone to do what I would not do myself.
“Fully autonomous demolition robots are expected to revolutionise the industry”
QWhat kind of projects does M&M Demolition work on most frequently?
Over the years M&M Demolition has worked on all types of projects from a solitary house to inner-city high rise. In the beginning some were as subcontractor, eventually moving into being a leading provider as Principal Contractor.
We believe that quality and service is paramount to a successful relationship with all of our clients and some testimonials can be accessed through our website.
There is not a lot we can’t do but we remain grounded and realistic in our future capabilities. We offer a full turnkey service if required from conception to full demolition and clearance.
We also carry out a varied range of enabling works, all determined by client needs. Transparency throughout every process has shown us to be exactly what it says on the tin. If we say we can do it, then we can.
QHow do you approach a project and its different aspects?
Put simply – as a team. We are lucky to have the management team capable of ensuring all requirements and needs are met before, during and after. Regular team meetings, site meetings, a million emails and whatever else can relay a message continue to keep all updated and on point. Everyone from our Demolition Principal to site management has access to information at all times.
QWhat are the standout projects from M&M Demolition’s history?
I once worked on a heritage site where an 800-year-old wall was rather too close for my liking. With great public interest and an audience every day, it took great concentration and patience for each process to be fulfilled.
The timeframe here was the biggest challenge and once I came to the realisation that the deadline was unachievable, I had to make the dreaded phone call to say I was wrong in my estimation of how long it would take. This was early in my career and you can imagine my relief when the contingency was already in place.
The lesson was measure twice and cut once. We had a site meeting and the client representatives were fantastic and I then knew we were all human.
QHow do you gain business and spread the word about your services?
Our marketing is built on fostering strong relationships, showcasing our expertise and maintaining a solid reputation within the industry.
We actively use social media platforms such as LinkedIn and Facebook to share updates about our projects, showcase our capabilities and highlight the innovative techniques we use while our website serves as a hub for potential clients, offering case studies and detailed information about our services. Sharing successful project outcomes and
client testimonials highlights our expertise and builds trust with new prospects.
Attending conferences, trade shows and NFDC events allows us to connect with key stakeholders and decision makers in construction and property development. With over 50 years’ experience, much of our business comes through wordof-mouth recommendations from satisfied clients and industry peers.
Highlighting our commitment to environmentally conscious practices and sustainable demolition methods has positioned us as a forwardthinking company, appealing to both private and public sectors.
QTell us about the tendering process
We work closely with developers, contractors and local authorities, ensuring we’re top of mind for future opportunities. Proactively reaching out to potential clients through email campaigns, targeted ads and direct networking helps us maintain a steady pipeline of projects.
We begin tenders by engaging with potential clients to understand their project requirements, goals and challenges. Then our experienced team prepares detailed and competitive tenders, focusing on efficient, cost-effective and environmentally sustainable solutions tailored to each project. We conduct in-depth consultations to present our methodology, safety measures and project plans. This ensures stakeholders are confident in our approach.
Our NFDC accreditation and track record of successfully handling complex projects often gives us a competitive edge in securing contracts.
By combining a proactive marketing strategy with a meticulous tendering process, we continue to grow our client base while maintaining our reputation as one of the UK’s leading demolition contractors.
QTell us about M&M Demolition’s memberships and accreditations
M&M Demolition is an NFDC member, Constructionline Gold, Builders Profile, Smas, CHAS Advanced and ISO 9001 accredited.
QHow do you source new talent and what can we do to attract young people into the industry?
Finding skilled labour has become increasingly challenging, particularly in the demolition industry, which currently struggles to attract younger generations. While we advertise job opportunities on social media and rely on networks within the demolition industry and wordof-mouth referrals, the majority of applicants come from these traditional sources. Occasionally, labour agencies provide excellent operatives and when circumstances align, these individuals may secure permanent positions with us.
However, with industry margins growing tighter, wages for demolition operatives have not kept pace with those in other sectors. Demolition was once a highly lucrative field, but until wage rates reflect the demands and expertise of the work, the availability of high-quality labour will remain limited as will attracting trainee and apprentices.
We engage with local schools and colleges to promote careers
in construction and demolition, inspiring the next generation of skilled professionals.
QDo you undertake any ongoing training or Continuous Professional Development?
M&M is an NFDC member, with the NDTG providing our training needs on an ongoing basis. The guidelines are clear cut as to the level of training required to keep standards high.
All those who wish to remain with us will always be kept up to date with their training. The more one progresses, the more we invest in our workforce. There is no end to the training matrix and each and every one has the freedom to go to the level they’re happy at. Needless to say, all are set at a minimum
standard as required by their job role and capabilities. Support is always close by.
Senior management are consistently keeping themselves updated on all new legislative changes and regularly attend industry meetings such as NFDC and IDE. This is transparent in our documentation when we go to tender, fill out a PQQ or simply introduce ourselves to potential future clients..
QTell us about M&M Demolition’s engagement in the community or social responsibilities?
M&M Demolition takes pride in being an active and responsible member of the communities we serve. We prioritise hiring local labour and service providers
wherever possible, supporting economic growth in the areas we work. Our commitment to health and safety extends to the communities we work in, ensuring our projects are conducted with the utmost care to protect people and the environment.
Our approach to social responsibility focuses on creating a positive impact through meaningful engagement and sustainable practices. M&M supports various community-focused organisations, contributing both time and resources to make a difference. We engage with local schools and colleges to promote careers in construction and demolition, inspiring the next generation of skilled professionals.
QWhat measures is M&M Demolition taking in regard to the climate crisis and sustainability?
M&M Demolition recognises the critical role our industry plays in addressing the climate crisis; sustainability is embedded in our operations and we continually seek innovative ways to reduce environmental impact while delivering high-quality demolition services.
Minimising waste and maximising recycling is at the heart of our operations and we prioritise recycling and reuse of materials, achieving high diversion from landfill rates. Structural components, metals and aggregates are carefully segregated into separate waste and recycling streams and repurposed whenever possible.
We invest in modern, eco-friendly plant and technologies, adopting low-emission equipment and machinery to minimise our carbon footprint and our fleet adheres to stringent emission standards to ensure compliance with the Mayor of London’s NRMM. Dust and particulate suppression systems are used during operations to minimise air pollution and advanced logistics
planning reduces unnecessary transport, cutting fuel consumption and emissions.
We engage with clients and stakeholders early in the process to incorporate sustainable practices from the outset and our teams undergo regular training to stay updated on eco-friendly techniques and regulations.
We aim to lead the demolition industry in sustainability by continuing to invest in research and development for carbonneutral demolition solutions, setting measurable goals to achieve net-zero emissions within our operations, partnering with clients to design projects that consider lifecycle impacts, encouraging reuse of entire structures or parts.
The demolition and construction industries are undergoing a green transformation. Key trends we foresee include an increased emphasis on material reuse to reduce reliance on virgin resources; more stringent regulations requiring demolition firms to measure and disclose their carbon footprint; and greater adoption of AI, drones and robotics for precision work reducing waste and emissions.
QHow do you see the demolition industry developing over the next few years?
The tried and tested methods of demolition have been around for a long time but I am always pleased to see the H&S improvements evolve and this is what keeps us safe.
It is not my belief that only the big companies will survive. If everyone believes in themselves and can see the big picture, then they will be under a little less pressure. Responsibility lying with all is how we can give ownership to our workforce.
Continued training in new innovations keeps the wheels turning. Apprenticeships for newcomers to the industry and an open mind to all nationals is the future of this country, provided all
have the right attitude towards the same goal.
We must adapt to individual needs and respect others for the person they are. We at M&M look at capabilities and build people up where we can and will continue to do so into the future. If everyone felt valued as a person, this could help relieve the shortage of trained staff.
QWhat do you envisage will be the future game changers in demolition?
Fully autonomous demolition robots are expected to revolutionise the industry by handling dangerous tasks, improving safety and delivering consistent precision while artificial intelligence will play a crucial role in optimising project planning and execution, predicting hazards and maximising material recovery.
Continued investment in electric and hydrogen-powered machinery will significantly reduce the industry’s carbon footprint. Emerging technologies will enable entire structures to be disassembled and repurposed rather than demolished, redefining “end-of-life” building strategies.
QHow do you envisage M&M Demolition in five to ten years?
We are committed to building a legacy that aligns with both our values and the needs of a changing world. Our focus is on sustainable growth, continuous innovation and strengthening our position as a leading force in the demolition and enabling works industry.
We aim to solidify our status as a top-tier NFDC-accredited contractor, expanding our portfolio of complex and large-scale projects across the private and public sectors. To remain at the forefront of the industry, we plan to broaden our range of services.
This means continuing to invest in cutting-edge technologies to enhance efficiency, safety and sustainability and recruiting and
training a skilled, diverse team while upskilling our current workforce to meet future demands. We will build on our commitment to safety and support to retain top talent while preparing for generational transitions by identifying and mentoring future leaders within the company.
Sustainability will remain at the core of our mission, aligning with global efforts to combat the climate crisis. M&M Demolition will continue to prioritise strong, long-term relationships with clients, stakeholders and regulators. Our proactive approach and adaptability will ensure we remain a trusted partner for projects of all scales. By focusing on our goals, M&M Demolition is poised to grow responsibly, deliver innovative solutions and leave a lasting positive impact on the industry and the environment.
QAnd what about you in a few years?
If only I had a crystal ball. For now the focus is on delivering to the best of my abilities. Moving forward I can only hope I keep well and can continue to serve this industry, with a little holiday treat every now and again. I’m under no illusions of greatness and simply wish to be surrounded by my family, friends and colleagues.
Who is your favourite artist?
I’m not so much into the arts although I appreciate them. I enjoy the odd trip to theatre or concert with my wife and kids.
Who do you most admire?
That’s easy, my wife. No matter what comes in life, she is steadfast, supportive and fiercely strong minded in keeping our ship afloat – not an easy job especially when I’m busy. She keeps me grounded.
What do you do for fun?
I have been known to send the odd sports car round a track. Cars are my weakness, hence I need grounding
What would be your desert island luxury?
That would be a lonely life, I’m used to hustle and bustle.
What gets you out of bed in the morning?
The need to ensure I do my part. I want to instil a work ethic in my children that says you can get what you want if you work for it. Nothing is free in life.
When and where were you happiest?
Right now – surrounded by real people and not old yet. Saying that, I wouldn’t mind having my 20-year-old body back.
What’s your bucket list activity?
Gumball rally would be really great fun. Perhaps when the kids are through university I’ll look into it.
What’s your ideal weekend?
Summertime camping with fishing rod and campfire. As long as family are there.
What would you do for a company excursion/reward, money no object?
Gumball rally of course.
What’s your favourite food/cuisine?
Home cooked red Thai curry. Love it.
What’s your tipple of choice?
Port. But not too much, its very moreish.
Title: Investing in the future
Contractor: GBM Demolition
Client: Trebor Developments
Structure demolished: The Old Tea Factory and Former Wholesale Distribution Centre, in the heart of Crewe’s established commercial area
Techniques used: Extensive Licensed and Non-Licensed asbestos abatement, mechanical demolition, GPR scanning, floor slab removal, vast foundation removal, processing to MOT Type 1 and 6F2, regrading of site
Future use: 335,000 sq ft new build distribution unit
Crewe has a longstanding reputation as a British industrial and cultural centre, with its history anchored in the railway and manufacturing industries. Its legacy is reflected in both preserved landmarks and ongoing redevelopment projects that continue to honour and build upon Crewe’s industrious past.
The town’s identity was significantly shaped in the early 19th century when the Grand Junction Railway chose Crewe as the location for a new locomotive works. This decision not only put Crewe on the map but also led to rapid industrial and population growth as workers and their families moved into the area. The Crewe Works facility, which began operating in 1843, played a vital role in producing
and maintaining steam engines, contributing to the economic prosperity of the town and solidifying Crewe’s role as a key player in the industrial era.
Crewe’s commitment to preserving its industrial roots is evident in several historical landmarks, including the Crewe Heritage Centre. Established on the original railway works site, this centre commemorates the town’s railway legacy and offers visitors a glimpse into the past with exhibits on vintage locomotives, engineering achievements and the town’s contributions to Britain’s transportation industry.
The Lyceum Theatre, dating back to 1911, also reflects the cultural side of Crewe’s heritage, hosting a variety of performances for over a century. Additionally,
Queens Park, built in 1887 to celebrate Queen Victoria’s Jubilee, is an expansive Victorianera park with ornamental gardens and historic pavilions, which continues to serve as a gathering place and source of pride for residents.
In recent years, Crewe has benefited from substantial investment in redevelopment projects aimed at enhancing the local community and creating economic opportunities. One key example is the transformation of the Old Tea Factory and Former Bargain Booze Distribution Centre, located at 1 Weston Road in Crewe’s commercial district. For years, this site served as a purpose-built distribution and production centre, strategically positioned near other distribution centres
and only ten miles west of the M6 motorway. However, with changing economic needs and the rise of new industrial standards, the site attracted the interest of developers seeking to bring modern amenities and facilities to Crewe.
The Old Tea Factory site recently secured a £25 million investment aimed at converting the former warehouse and production facility into a new distribution centre. This substantial project reflects Crewe’s emphasis on modernising its infrastructure while generating local jobs and supporting the broader economy. The redevelopment includes plans for a 30,000-square-metre warehouse space that will host office facilities on the first and second floors. This redevelopment not only revitalises a historically significant area of Crewe but also contributes to the town’s ongoing commitment to being a thriving industrial hub that continues to attract new businesses and investments. GBM Demolition was assigned to complete a PreDemolition Audit in line with the requirements of the BREEAM UK NC V6. The project targeted an Excellent certification level, and through adhering to strict protocol the required credits to assist in achieving this target were attained.
GBM Demolition was awarded the contract for the site’s demolition, a process requiring careful planning and coordination to maintain safety standards and honour environmental regulations. During the initial soft strip and site preparation phase, GBM enlisted a trusted contractor to install 200 linear metres of 2.4-meter in-ground timber hoarding. All hoarding works were treated as temporary works and dealt with in line with BS 5975. The hoarding was painted in compliance with the specifications set by Trebor Developments, the primary
developer, in preparation for sitespecific decals and notifications to be displayed, allowing the community to stay informed about the progress.
A significant part of the demolition process involved handling asbestos materials. Due to the building’s age and original construction standards, asbestos abatement was necessary to ensure safe demolition. GBM partnered with a Licensed Asbestos Removal Contractor to remove the vast amount of asbestos from site. The project involved a combination of licensed and non-licensed asbestos removal efforts, with controlled environments and monitored conditions to protect workers and prevent contamination. Licensed asbestos removals were conducted by specialised teams, which allowed for efficient handling and completion within the agreedupon timeline. The non-licensed asbestos removal, which included the removal of “Galbestos” sheeting, was carried out by GBM operatives trained in non-licensed asbestos removal procedures to reduce risks.
The physical demolition began with the dismantling of the northernmost structures, where no
asbestos-containing materials were found. Equipped with the required machinery, including the Volvo EC750 with a shear attachment, GBM systematically demolished sections of the building, recovering various metals that were sorted by type and composition for recycling.
The demolition also presented the unique challenge of safely dismantling a steel-framed tower within the structure’s centre. GBM constructed an access ramp specifically for this purpose, allowing the Volvo EC750 to reach and dismantle the tower in a single day, demonstrating the efficiency and planning involved in the project.
Dust management was a priority during the demolition to minimise the impact on the surrounding area. GBM utilised two Dust Fighter units and tool head suppression systems to control dust emissions, especially when handling materials prone to release particulate matter. These measures helped maintain air quality and protect nearby residents and businesses, highlighting the project’s commitment to responsible environmental practices.
As the demolition progressed to the substructure, GBM discovered
additional asbestos materials buried beneath the ground, including asbestos insulating boards within manholes and under the slab foundation. The GBM Site Supervisor promptly cordoned off these areas, and the Licensed Asbestos Removal Contractor was recalled to handle the abatement. This careful adherence to safety procedures ensured that the discovery of hidden asbestos did not delay the project timeline, with site grading and final preparations for redevelopment proceeding smoothly.
To process the materials on site, GBM employed a range of heavy machinery, including a Liebherr 960, Volvo EC750 and EC380 excavators and a mobile McCloskey crusher and screen. This equipment allowed GBM to process and sort the demolished materials efficiently, producing over 16,500 cubic metres of MOT Type 1 and 6F2 aggregates, which will be reused in future construction projects. Dust atomising sprays and ground hose suppression were operated to ensure substructure removal dust was minimised. GBM also utilised the built-in dust suppression
systems within the crusher and screen, which minimised dust throughout the processing works. Material transportation within the site was managed by two Volvo A30G dumpers and a Volvo L150H loading shovel, with dust suppression systems in place to minimise airborne particles during movement and crushing.
The demolition was completed ahead of schedule, with the superstructure dismantling finalised three weeks early, and substructure removals commencing two weeks in advance. Through careful planning, effective communication among all parties, and optimised use of resources, GBM was able to streamline multiple phases of demolition, recovering valuable materials for recycling and reuse. This approach minimised waste and allowed for the production of recycled aggregates on-site, contributing to the environmental sustainability of the project.
Following the completion of substructure removal and site grading, GBM provided Trebor Developments with a cleared and levelled site, ready for the construction of the new
distribution facility. This new 335,000-square-foot facility is projected to create over 150 jobs, adding significant economic value to Crewe and reinforcing its position as a centre of industrial innovation. The distribution centre will be equipped with modern amenities, including renewable energy sources and rainwater harvesting systems, reflecting Crewe’s commitment to sustainable development practices.
In summary, the transformation of the former Bargain Booze and Tea Factory site is a testament to Crewe’s adaptability and dedication to preserving its industrial heritage while embracing modern advancements. The town’s development strategy emphasises both the preservation of its rich history and the attraction of new business opportunities, underscoring Crewe’s role as a dynamic industrial and cultural hub in the UK. The redevelopment of this historic site represents a forward-thinking approach that not only benefits the local economy but also aligns with the broader goals of environmental responsibility and community engagement.
Title: Watchmoor Park
Structure type: Four office blocks within a live business park
Contractor: Collard Group
Client: Anglesea Capital and Quartz Project Services
Start date: October 2024
Completion date: Live project
Techniques: Stripout, asbestos removal, demolition, grub up of foundations, breaking up of hardstandings, crushing arisings to stockpile on site
Future use: Storage warehouses
Located just outside of Camberley, our Demolition and Enabling division is carrying out the full demolition of three office blocks within a live business park. Our works include: permanent timber hoarding, stripout and asbestos removal, demolition and grub up foundations, breaking up hardstanding and crushing arisings to stockpile on site. Our ability to carry out a one-stop-shop approach to demolition projects is in demand.
When Collard Group was appointed as the principal contractor for a demolition project at Watchmoor Park Business Park in Camberley, Surrey, our team knew they were up for a complex challenge.
This bustling business park, nestled along the A331 near the towns of Sandhurst and Camberley, posed a unique mix of logistical hurdles, environmental concerns and technical demolition demands. The job site sat between commercial offices, a nearby sewage plant and a large pond supporting local wildlife – each factor requiring specialised planning and protection strategies.
The site’s current configuration included steel-framed, two-storey office buildings, asphalt-covered car parks and surrounding access roads. Collard Group’s task was to
demolish these structures, remove all materials and prepare the area for the construction of a 10,670 m² warehouse facility with office and warehouse space, plus a parking area and loading bays.
Positioned within an active business park, the site required careful handling of foot traffic, heavy equipment logistics and environmental protections.
With entry points from the A30 and M3 and a network of surrounding A roads, the location was well-suited for construction traffic, though strict measures were implemented to manage dust, noise and vehicle flow.
A significant environmental concern involved the large pond on the western boundary, a habitat for local wildlife. To mitigate any risk of contamination from water runoff, dust suppression systems, or waste materials, Collard implemented protective barriers
and runoff controls, ensuring that demolition activities had minimal impact on this sensitive area.
From the outset, Collard Group deployed a skilled team for meticulous project planning. Collard’s approach included offering substantial value engineering to optimise the client’s resources and timeline.
Collard introduced a value engineered process across the scheme that saved the client money on multiple aspects of the project. Additionally, the use of 3D modelling for this project allowed Collard to create a detailed site plan, which assisted in designing an effective traffic management and construction phase plan, providing clear visualisations for the client and ensuring seamless planning.
A rigorous pre-demolition audit, completed in conjunction with Collard’s Construction Phase Management Plan, helped discharge planning conditions and establish clear operational guidelines. This early investment in planning and engineering set the foundation for a successful project.
With demolition on any site comes the need to prioritise safety. At Watchmoor Park, Collard’s team faced four primary risks.
• Live services: By conducting thorough inspections and service terminations, the risk from live services was minimised, ensuring safe operations as the site was prepared for demolition. The client also took the initiative to terminate all services before demolition, verified by a thirdparty M&E contractor,
• Asbestos: Although the buildings were constructed post-1992, The R&D survey identified presumed asbestos within electrical boxes. Following termination and inspection of these components, it was confirmed they were asbestos-free,
• Dust and fumes: Dust was controlled using a Dust Boss system, ensuring air quality remained safe for workers and nearby businesses. Continuous dust suppression kept levels well within the trigger points set for the site,
• Noise and vibration: Realtime monitoring systems were set up to measure noise and vibration, with site managers receiving automatic alerts if any threshold was exceeded, allowing for swift control adjustments.
The demolition itself is a phased operation. The team focused on the full demolition of buildings 1 and 2, along with the top-slab demolition of building 7 and a full stripout, back to the shell of building 9.
Following the initial strip-out of non-structural elements (such as drywall, wiring and access floor tiles), the remaining steel and concrete structures were dismantled bay by bay. Collard’s specialised 360-degree demolition excavators, fitted with rotating hydraulic grapples, methodically deconstructed these buildings. This methodical approach maintained building stability throughout the process and allowed material to be segregated on the go.
All waste materials were sorted into categories such as metal,
hardcore and non-recyclables, with an aim for 98% diversion rate from landfill. Reusable materials were either sent to Collard’s recycling plant in Wokingham or other approved facilities, while crushed concrete was stockpiled on site for later use in the new construction works.
Collard Group staffed the site with a team of qualified professionals, from contracts managers and site supervisors to specialised operatives holding CPCS, SMSTS and CCDO certifications. Health and safety protocols were managed through a competency matrix and routine refreshers, coordinated by an internal training coordinator. Each shift began with a site-specific induction, followed by a daily briefing and method statement review led
by the site supervisor. Safety protocols were strictly enforced, with controlled access, exclusion zones and clear signage, ensuring a safe environment for all on-site personnel.
All operatives on site were given comprehensive inductions and regular method statement briefings, which covered any operational adjustments.
Specialised permits, such as those for hot works, demolition and excavation, were issued and safety signage marked designated exclusion zones.
A hallmark of Collard’s approach is its commitment to sustainable demolition practices. The team prioritised recycling by stripping out valuable materials such as copper wiring and aluminium, which were sent to our Wokingham facility for processing. Flooring tiles were repurposed for future
commercial projects and structural steel was carefully removed, cut and directed to recycling plants. Concrete, bricks and other hardcore materials were crushed on-site to a 6F2 specification, ready for reuse as subbase material.
This level of resource recovery underscored Collard’s dedication to environmental responsibility, setting a standard for sustainable demolition in business parks and urban areas.
Collard Group’s demolition project at Watchmoor Park exemplifies the power of strategic planning, environmental stewardship and efficient execution in the field of commercial demolition. By combining innovative techniques like 3D modelling with comprehensive safety and environmental protections, Collard delivered a project that meets the client’s goals, adhered to strict
safety standards and minimised environmental impact.
As the project proceeds to its final stages in 2024, Collard’s team remains committed to leaving behind not only a clear construction-ready site but also a model of best practices in modern demolition. Our proactive approach – from planning through execution – sets a benchmark for how urban demolition projects can be managed with both precision and purpose.
Project: Oxford Road A34 Lodge Hill Interchange
Structure: Bridge passing over a motorway made up of steel, concrete, stone, and asphalt
Site area: The Lodge Hill junction, located between Abingdon and Oxford
Scope of works: Removing 13 mm depth of tarmac to remove bitumen and 3 mm of asbestos waterproofing over 1,300 m2. Up to 8% of asbestos waterproofing contained asbestos chrysotile
Contractors: Windsor Waste Management with AIM Environmental Ltd
Client: National Highways
Start date: 31 August 2024
Completion date: 21 September 2024
Techniques: Asbestos testing, asbestos removal during strict windows to minimise disruption to road users
Planing the road surface down to the waterproofing to remove the asbestos contaminated material and replace with new waterproofing to renew the surface and protect the integrity of the structure
Future use: Works are part of an ongoing project with Oxfordshire County Council to optimise the junction capacity at Lodge Hill, provide new access and shorter journey times and enable economic growth in the wider Science Vale area
In the autumn of 2024, Windsor Waste Management partnered with AIM Environmental Ltd to safely remove over 160 tonnes of asbestos bitumen contaminated materials from the A34 Lodge Hill interchange in Oxfordshire. This project was part of a larger bridge dismantling and infrastructure improvement initiative undertaken by National Highways. Given the strategic importance of the A34 as a key transport route for thousands of commuters daily, Windsor Waste Management was tasked with executing the asbestos disposal under strict time constraints to minimise disruption.
The A34 junction at Lodge Hill, situated between Abingdon and Oxford, currently features only north-facing slip roads. The ongoing interchange improvement project aims to enhance traffic flow and accessibility by adding new south-facing slip roads, along with traffic calming measures on the surrounding local network. These upgrades are critical to supporting the anticipated growth in the area, driven by the development of over 1,000 new homes in Abingdon by 2031, as well as the expansion of the Science Vale area. The improvements will not only increase junction capacity but also boost the overall performance and resilience of the local transport network.
The planning application for the A34 Lodge Hill scheme was
submitted in October 2022, with approval granted in September 2023. The infrastructure enhancements are expected to reduce journey times, improve access and drive economic growth in the region.
Given the hazardous nature of asbestos removal, meticulous planning was crucial. Windsor Waste Management collaborated closely with AIM Environmental Ltd and National Highways to develop a comprehensive traffic management plan. The primary objective was to minimise disruption to commuters and maintain smooth traffic flow on the A34, especially during peak hours. To achieve this, all works were scheduled over weekends when traffic volumes were lower.
• Traffic management: Special attention was given to planning vehicle movements, ensuring minimal impact on road users. Works were scheduled during off-peak hours to reduce congestion,
• Hazardous material handling: Due to the dangerous nature of asbestos, it was essential that no contaminated materials were left on site after operating hours. Windsor Waste Management developed a strategy to clear all asbestos by the end of each operating day to eliminate any risk to commuters and the environment,
• Direct communication channels: The site manager was provided with direct contact to Windsor Waste Management’s transport department outside of operating hours, allowing real-time updates and schedule adjustments. This ensured that trucks could be routed efficiently, maintaining adherence to tight deadlines.
Asbestos removal began on Saturday 7 September. On the first day, two Windsor Waste Management lorries arrived with three 20-yard roll-onroll-off (RoRo) bins. These bins were strategically positioned for quick loading, ensuring minimal downtime.
The hazardous waste was loaded into the bins and transported immediately to a licensed hazardous waste disposal facility, ensuring compliance with all relevant environmental regulations.
The project spanned three consecutive weekends, with removal works coordinated outside of Windsor Waste Management’s normal operating hours. This flexibility ensured that the project adhered to the agreed timeline without impacting commuter traffic.
Trained and authorised operatives operated the plant machines, starting by breaking out the marked 650 m² tarmac area using a breaker attachment. Once the tarmac was broken, plant drivers scraped back the material to a depth of 13 mm, taking care to avoid excessive dust generation. Bitumen and tarmac debris were carefully loaded directly into an open top 20-yard skip designated for asbestos waste. The skip was lined with polythene sheeting to prevent contamination and ensure safe disposal. This process was continued systematically until all the material had been removed.
Each 20-yard RoRo bin was filled and promptly transported off-site to reduce the risk of exposure. A total of 14 RoRo bins were utilised throughout the project.
To meet the project’s logistical demands, Windsor Waste Management stationed drivers near the site, enabling a swift wait-andload service that minimised delays and maximised efficiency.
The removal of over 160 tonnes of asbestos bitumen contaminated materials was completed successfully, with Windsor Waste Management ensuring the safe disposal of all hazardous materials. The operation was carried out seamlessly from the initial planning stages through to the final disposal, demonstrating Windsor Waste Management’s commitment to regulatory compliance and environmental responsibility.
• Efficient coordination:
Real-time communication between the site manager and Windsor Waste Management’s transport team facilitated smooth operations, with clear updates allowing for dynamic adjustments to truck routing,
• Regulatory compliance: All duty of care obligations were met, providing AIM Environmental Ltd and National Highways with assurance that the waste audit trail adhered to the highest standards,
• Minimal disruption: By conducting works over weekends and leveraging strategic planning, Windsor Waste Management successfully minimised disruption to the A34 traffic, keeping the critical transport route operational during peak hours.
This project exemplifies Windsor Waste Management’s expertise in managing complex demolition projects with hazardous waste. The collaboration with AIM Environmental Ltd and National Highways not only ensured the safe and compliant disposal of asbestos but also contributed to the successful progress of the A34 Lodge Hill interchange improvements. As the area continues to grow, these infrastructure enhancements will
play a key role in supporting local development and economic growth.
Windsor Waste Management is a market leader in asbestos disposal. It is a significant provider of total waste management services to construction, demolition and related industries across the UK. With over 20 years’ experience and an unrivalled reputation, it manages storage, collection and disposal solutions for asbestos, demolition, construction, business and hazardous waste.
AIM Environmental Ltd specialises in the safe removal and remediation of asbestos containing materials. Its knowledgeable and experienced team are extensively trained in all aspects of asbestos abatement to ensure projects are completed to the highest standard with health and safety at the core of its business. With a wealth of experience in commercial, industrial and retail sectors AIM Environmental Ltd assists in ensuring the protection and safety of buildings, staff and customers.
Project: Stripout and associated works at 7-21 Wilson Street, London EC2M 2S
Structure: 1990s reinforced concrete frame office building
Site area: 6,000m2
Scope of works:
• Act as principal contractor
• Carry out refurbishment and demolition survey
• Isolations and disconnection
• Installation of temporary site power including intruder and fire alarm
• Full internal stripout back to base build
Client: Private client
Start date: 28/10/2024
Completion date: 17/01/2025
Future use: Office building
Whether for recycling or secondary demolition, Arden Equipment’s Hydraulic Concrete Crushers bring versatility, cost-effectiveness and efficiency to construction sites.
Available for excavators from 13 to 80 tonnes, Arden Equipment Crushers offer significant toothing forces thanks to their technical characteristics and kinematics. In addition, Arden Equipment Crushers are perfectly suited to the needs of professionals thanks to their compatibility with a wide range of excavators and customisable options, such as the Arden Jet, closure plate, speedvalve or booster.
This construction equipment, with large jaw openings and moulded teeth, is used to efficiently grind concrete to the ground and pulverise
it to separate concrete rounds. In addition, interchangeable teeth are individually mounted and easily replaceable to limit maintenance costs.
Arden Equipment’s Hydraulic Concrete Crusher also meets the growing environmental demands of modern construction sites thanks to their extremely strong steels and inverted cylinders with a design focused on sustainability, efficiency and safety. By facilitating the recycling of materials directly on site, the crusher helps reduce the need for transportation and storage of waste, thereby reducing the overall carbon footprint of operations.
Whether for urban sites requiring precision and speed, or for large-scale work in demanding environments, these crushers demonstrate their
ability to meet any challenge. They embody the perfect balance of cutting-edge technology, versatility and commitment to a sustainable future.
To conclude, Arden Equipment’s Hydraulic Concrete Crushers position themselves as essential equipment to meet the current and future challenges of demolition and recycling sites. Combining robustness, innovation and respect for the environment, they offer a complete solution that optimises productivity while promoting sustainable resource management. Whether to improve operational efficiency or contribute to a sustainable economy, Arden Equipment Hydraulic Concrete Crushers are a strategic investment for demanding and visionary professionals in the industry.
In the demanding world of mining, construction, demolition and recycling, reliable equipment and high-quality parts are critical to maintaining optimal performance. As machinery is pushed to its limits day in and day out, breakdowns are inevitable. When they happen, companies need fast, dependable solutions to get their crushers and screeners back up and running. That’s where Crusher Consumables Ltd steps in. Located in the heart of the UK, Crusher Consumables is a family-owned business with over 20 years of experience, dedicated to supplying high-quality replacement parts for a wide range of crushers and screeners.
A one-stop shop for premium crusher and screener parts
Crusher Consumables stocks an extensive range of parts to fit a wide variety of machine makes and models, including those from leading brands such as Terex, Sandvik, and Metso. With our broad selection, customers can find everything they need in one place, saving both time and effort. Whether it’s jaw plates, blow bars, or hydraulic pumps, we have a solution ready for you. We also carry essential accessories and wear parts that can significantly
extend the life of your machines, keeping them performing at their best for longer.
What sets us apart is not only our wide inventory but also our commitment to sourcing only the best. Every part in our warehouse is carefully selected to ensure it meets the highest industry standards. This commitment to quality ensures that your machines benefit from enhanced durability, which translates to reduced downtime and lower long-term costs. When you choose Crusher Consumables , you’re not just buying parts; you’re investing in the reliability and longevity of your equipment.
and reliable service with a personal
In an industry where downtime can be incredibly costly, timely delivery is critical. Crusher Consumables understands this and has optimised its processes to ensure fast and efficient service. We maintain a fully stocked warehouse to meet urgent demands, meaning many orders can be fulfilled immediately, without long lead times. Our experienced team works closely with you to ensure parts are delivered quickly and accurately, reducing wait times and getting your equipment back to work as soon as possible.
What truly sets Crusher Consumables apart is our dedication to personalised service. As a family-owned business, we believe in building long-term relationships with our customers. Our team takes the time to understand each client’s unique needs, ensuring that you receive the right parts for your specific machines. With Crusher Consumables you don’t just get a supplier, you gain a trusted partner who is always ready to support you.
Expertise you can rely on
Our team at Crusher Consumables brings years of experience to the table. We understand the intricacies of crushers and screeners and we know exactly which parts are needed for different types of repairs and maintenance. Our in-depth knowledge enables us to offer expert guidance on part selection, ensuring you get the right components to optimise the performance of your machinery.
For clients who may not know precisely what they need, our team is on hand to offer advice and recommendations. We take pride in our ability to troubleshoot issues, identify the correct parts and help our customers make informed decisions. This level
of expertise, combined with our extensive product range, makes Crusher Consumables an invaluable resource for anyone in the crushing and screening industries.
Crusher Consumables is committed to sustainable practices. We understand the environmental impact of the industries we serve, and we’re actively working to promote a more sustainable approach. By supplying highquality, durable parts, we help our customers extend the life of their equipment and reduce waste. Additionally, our efficient delivery processes are designed to minimise our carbon footprint,
further supporting our mission of sustainability. We are also dedicated to providing affordable options without compromising on quality. Our strong supplier relationships allow us to source premium parts at competitive prices, passing these savings on to our customers. Crusher Consumables believes that quality and affordability should go hand-inhand, which is why we work tirelessly to offer our clients both.
For those looking for a reliable partner in the crushing and screening industries, Crusher Consumables offers a winning combination of quality products,
expert knowledge and exceptional service. We are here to help you keep your equipment running smoothly, minimising downtime and maximising efficiency. With our vast range of crusher and screener parts, fast delivery and personalised approach, we ensure that your business never skips a beat.
Crusher Consumables stands by your side, supporting your operations with dependable parts and unmatched service. Discover the difference we can make to your business by contacting us today. Let us be your trusted partner in keeping your crushers and screeners performing at their best. When it comes to quality, reliability, and service, Crusher Consumables is second to none.
Not too long ago, excavators were simply digging machines. Today, these iron giants are evolving into multifunctional tools; whether large or small, construction machines are becoming the Swiss Army knives of the building site. They transition from crushing to screening, handling to loading with ease, all with just a change of attachment. By fitting an MB Crusher attachment to their arm, they can swiftly switch between tasks, making the construction site of the future a present-day reality.
On the construction site of the future, the concept of waste will be obsolete. Every scrap material will be recovered and reused either on site or in other projects – nothing will go to waste. MB Crusher units turn waste into valuable resources, eliminating the need for material transportation and reducing the necessity to purchase new materials.
The future site is one of pure efficiency, where every action is optimised, and every resource is used to its fullest potential. MB
Crusher accessories streamline the recycling process, making resource reuse an integral, automated part of daily operations. With MB Crusher, every site becomes more efficient with less waste and faster operation.
In the future construction site, both costs and project times will be more than halved. MB Crusher’s equipment installed on a heavy machine allows multiple tasks to be managed easily while saving on maintenance and management costs. Projects thus become more affordable, and the initial investment is reduced.
The future site is also safer, as the operator remains inside the excavator’s cab, effortlessly controlling the MB Crusher attachment. A quick-coupling change system allows for smooth transitions between tasks, enhancing both safety and efficiency.
And that’s not all – soon, we may see construction sites operated remotely, with operators monitoring and controlling
machines from distant control centres.
Imagine the future – but start using it today
Some only imagine the future, while others are already living it – such as Roberto Mauro’s Italian company, which has integrated three MB Crusher attachments into its fleet to use on an eight-bucket, the MB-G600 sorting grapple and the MB-S10 screening bucket. This combo has enabled them to tackle a variety of jobs, from beach cleaning and coastal reclamation to waterpipes and road works, as well as demolition and construction.
Thanks to the versatility of MB Crusher equipment, the company has significantly reduced processing times and slashed operational costs. “I bring the machine to the site,” says Roberto, “and with the quick coupling system, I mount the MB Crusher attachments in no time, and I’m ready to work.”
The construction site of tomorrow isn’t a dream – it’s happening today. MB Crusher is leading the way with cutting-edge equipment that supercharges productivity, slashes costs, and reduces environmental impact. This isn’t about imagining the future; MB Crusher is already shaping it, one job site at a time.
Omnia Machinery Group is an international trader of used construction equipment, operating across a wide range of sectors within the construction and recycling industry.
At Omnia, we take great pride in the quality and reliability of the machinery we offer. Over the last eight years we have developed a vast network of reputable suppliers worldwide to ensure we have access to the highest quality used machinery.
The company has recently expanded its UK operations by moving into a two-acre concreted storage facility and newly developed 5,000 square foot office building,
housing up to 30 employees. This allows us to greatly increase stock on hand, in particular crushing and screening equipment for the UK market, where customers will often need a quality machine ready to go to work on short notice.
Wanting to replicate our success in the UK, we have recently opened a second location in Miami, where we can better serve our customers in the North and South American market. We have also acquired a storage facility in the US where we hold a wide range of equipment for the aggregates and road building industries, which we are always looking to expand in order to better serve our clients worldwide.
In the world of construction, demolition is a sector that demands specialised machinery to ensure precision, safety and efficiency, and this is where Omnia Machinery shines as a leading dealer of crushing and screening equipment.
Known for our extensive inventory and expertise, Omnia has become a trusted partner for contractors looking for robust and reliable crushing and screening equipment.
What sets Omnia apart is our ability to source equipment from top manufacturers known for their commitment to quality, such as
Powerscreen, Sandvik, McCloskey, Terex Finlay and Metso, all of whom are part of our extensive catalogue.
We have built a strong reputation based on customer satisfaction and successful project outcomes – clients such as D Heap Plant Hire, CW Russell, Impianti Industriali Srl and Alvajel Equipos have consistently highlighted the company’s professional approach with recent orders of a Powerscreen Premiertrak R400X, Powerscreen Warrior 1800, McCloskey R155 and Terex Finlay 883+.
Positive testimonials and repeat business stand testament to Omnia’s dedication to delivering excellence in crushing and screening solutions.
Looking to sell your equipment?
Omnia is always on the lookout for high quality crushing and screening equipment to satisfy high levels of customer demand worldwide. Depending on your requirements
and timescales, we have the following three options:
• Consignment – List your equipment through our online platform and reach a global audience of qualified buyers,
• Private sale – Keep the sale of your equipment off-market for ultimate discretion,
• Outright purchase – We are always looking to purchase quality used equipment for our own stock.
Should you decide to go down the consignment route, which consistently provides the best returns for our clients, then you will receive the following benefits:
• Sell your equipment for free – no up-front charges and no seller commission,
• Inspection report and professional photography on us*,
• Worldwide exposure with
marketing on all major selling platforms,
• US and UK bases provide unique exposure for your equipment in the US market,
• Industry-best freight rates bring international customers to your doorstep,
• Don’t waste your time on time wasters – let us do the work for you.
We don’t just post your equipment online and hope for the best.
We have a team of skilled sales professionals actively connecting with new companies to try and sell your equipment for the price it deserves.
Coupled with an established network of worldwide buyers, we go the extra mile to find your equipment a new home. We also have a market leading logistics team which offers industry best haulage and ocean freight rates, bringing potential buyers closer to your doorstep.
Simex explores the new fields of material separation directly on site, acting on the levers of savings, dynamism and environmental sustainability.
From crushing to selective separation, from volumetric reduction to screening, Simex has a range of buckets for excavators and front loaders that facilitate demolition and recycling operations, directly on site, of waste material from construction sites and excavations.
The importance of a versatile, low-maintenance and replaceable screening tool system
Finding an effective way to separate and screen materials directly on site is vital for cost and time saving-conscious construction and earthmoving fleet operators.
Available in eight models for excavators from 1.2 to 50 tonnes, Simex VSE screening buckets are specifically designed for separating different-sized materials directly on site. The VSE product range features
the rapid adjustment of output size via an instant control in the cabin. This exclusive patent allows the shafts to be instantly distanced and closed, with a maximum travel of 40 mm.
Simex’s FIT screening tool technology, another standout feature of VSE screening buckets, remains popular with customers two years after its introduction.
The low-maintenance system allows for the easy interchange of every single disc or blade without unstrapping shafts. This means up to 75% less maintenance costs than the previous system. Multiple configurations are possible, depending on the materials to be screened. FIT offers users four different setups, but many others are possible thanks to the 100% interchangeable screening elements.
Simex VSE screening buckets aim to sustainably recover and reclaim soil and aggregates resulting from demolition, helping deliver a circular economy.
In the world of construction, as well as road maintenance, the issue of recovering material deriving from demolition and scarification is becoming increasingly urgent, with the dual objective of combining environmental protection with economic savings.
Those who work in the sector are well aware of the huge costs of transporting and disposing of aggregates and material from demolition, as well as the costs for the purchase and transport of new raw materials to the site.
In the light of the above considerations, Simex is expanding the crushing and recycling approach including the regeneration of all those materials which, once volumetrically reduced, screened or scarified, can be immediately recovered on site, in a sustainable and circular perspective, with both economic and environmental advantages.
Designed to reduce the volume of aggregates directly on site, CBE
crusher buckets for excavators find their perfect application field when working with waste material deriving from demolition and excavations. Thanks to the rotor system, they don’t suffer from iron, soil (even damp or wet), wood and deformable materials.
The recycling of road paving is increasing. More and more companies are relying on the CBA asphalt granulator bucket which guarantees the production of milled asphalt with certifiable grain size.
The focus on the recycling of asphalt milling, more correctly known as bituminous conglomerate granulate by legislation (also called RA or RAP – Reclaimed Asphalt Pavement), begins from Simex’s expertise in the field of crushing and screening waste materials from
demolition, combined with the concept of milling drums with rotor crusher bucket technology.
Simex’s range of CBA asphalt granulator buckets is becoming more popular with operators in the earthmoving and aggregates field and, to date, is available in three models: CBA 20, CBA 30 and CBA 40 for excavators from 12 to 40 tonnes.
The equipment features a cylindrical drum consisting of asymmetric teeth, driven by large displacement radial piston hydraulic motors, in direct drive. The rear grid determines the grain size of the material output and is available in several configurations, to meet the different characteristics required for the milled material by the regulations in force in various countries.
The possibility of obtaining a certifiable grain size thanks to the rear grids allows the operator to
create a milled conglomerate with different grain sizes (0-25, 0-30, 0-35 or 0-40 mm), depending on the size chosen and specific local regulations.
The advantages are many. First of all, costs linked to the purchase and handling of raw materials, and to the transport and storage of waste material at disposal plants are avoided. The on-site volumetric reduction of the removed asphalt slabs guarantees full truck loads and therefore fewer heavy vehicle journeys.
Last but not least, the attention to the circular economy – recovering road bituminous conglomerate is sustainable and eco-friendly. The certifiable granulometry of the output size allows to obtain a milled material that can be reused on-site or delivered to the appropriate bituminous conglomerate production sites, thus transforming a waste product into a resource.
With the mobile impact crusher
MOBIREX MR 100(i) NEO, Kleemann (part of the Wirtgen Group) presents the first family member of the new NEO line. The machine is efficient, powerful and extremely flexible.
Regardless of whether there is limited space on the job site or if job sites change frequently, thanks to compact dimensions and a low transport weight, deployment of the MOBIREX MR100(i)NEO / NEOe is flexible, fast and highly versatile. Operation ranges from
its compactness, the machine is particularly well suited for use in urban mining – i.e. directly on site on inner-city construction sites or similar areas.
Very high product quality is expected from an impact crusher, which is precisely what this compact crusher delivers. This is guaranteed not only by the powerful crushing unit with its four-ledged rotor with large impact circle and a very wide
variety of rotor ledge options, but also by the optional four squaremetre single-deck post screening unit. This makes it possible to produce a classified final grain size.
Thanks to integrated oversize grain returning, the post screening unit is designed such that it can be easily retrofitted by plug and play. Operators can therefore be flexible with changes to application areas.
The use of an optional wind sifter can optimise the final product quality even further by removing contamination in the material such as the lightweight materials (e.g. wood and plastic). The air flow can be controlled depending on the material.
machine all-electrically and therefore free of emissions thanks to the E-DRIVE drive concept with an external power supply.
Alternatively, the machine is available with the tried-and-tested D-DRIVE concept with maximum efficiency. If the machine is operated via the diesel generator, the power and load-dependent fan reduces not only the noise emission but also the fuel consumption. Thanks to water spraying at relevant points such as the crusher inlet, the discharge conveyors and the post screening unit, dust development can be reduced considerably.
Tool-free opening of the crusher is a further positive feature that guarantees fast service and maintenance. The Lock and Turn Quick Access allows customers to open the crusher very quickly at the push of a button, within a mere 30 seconds. The operator therefore has a full view of the crushing chamber very quickly and without any manual intervention at
all. A rotor ledge replacement, for example, is extremely convenient – a clear competitive advantage that has been additionally secured through a patent application.
Additional unique features in this machine class are the fully automatic crusher gap adjustment and zeropoint determination, which have already proved their value with the Kleemann impact crushers in the EVO2 and PRO lines. The gap adjustment at the push of a button is a real gain in comfort for the operator. As a result, tedious manual measurement of the crushing gap through narrow doors on the crusher side is a thing of the past.
Thanks to the SPECTIVE operating unit specially tuned to the functions, operation of the MR100(i) NEO / NEOe is simple and intuitive. With
SPECTIVE CONNECT from Kleemann, operators have all relevant data on speed, consumption values and fill levels at their fingertips on a smartphone or tablet and prepared in a clearly arranged manner.
SPECTIVE CONNECT also offers detailed troubleshooting aids to assist with service and maintenance.
“Whether there is limited space on the job site or if job sites change frequently - the MOBIREX MR100(i)NEO / NEOe is flexible, fast and highly versatile”
Kleemann (part of the Wirtgen Group) extends its portfolio of scalpers with the new MOBISCREEN MSS 502(i) EVO, alongside the established MOBISCREEN MSS 802(i) EVO. The focus was on flexibility, operability and ergonomics.
With its compactness the MOBISCREEN MSS 502(i) EVO is optimised for lower feed capacities of up to 350 tonnes per hour. A generously dimensioned feed hopper, screening surface of 5.4 square metres and a wide crusher discharge conveyor guarantee excellent material guidance.
High flexibility in the application
The speed of all conveyor belts is easily adjustable and a simple conversion from two to three final grain sizes is possible. The wide setting range of the screen casing angle (15.4–20°), alongside the large selection of screening media available, ensures a high screening capacity combined with very high product quality.
Whether the machine has finger decks for clayey excavated earth or square mesh for classifying decorative grit (examples from a
large selection of screen media available), the screen decks of the MOBISCREEN MSS 502(i) EVO can be covered to match the individual application case. Mixed covering of the screen decks is also possible.
Overall, the new machine offers comprehensive configuration diversity to impress as a standalone machine or in conjunction with further Kleemann machines.
Intuitive machine control reduces the risk of operating errors and saves training time. In addition, all relevant functions of the MSS 502(i) EVO can be operated and viewed from a safe distance. Apart from the increased work safety, the setup and dismantling of the machine is also accelerated with the mobile operating device; the operator ultimately holds the control in his or her hands.
Automatic mode is standard in Kleemann EVO screening machines. It ensures that all subsections and belts of the screening machine are automatically started in the correct sequence when the diesel engine is switched on at the touch of a button and switched off again in reverse
order once the work is completed. Accidental misuse is ruled out.
After the actuation of automatic mode the operator can already make their way to the wheel loader or excavator to start work quickly –the machine is ready for operation as soon as the operator takes their seat.
Sustainability plays a decisive role at Kleemann even in the development and design phase. In the MOBISCREEN MSS 502(i) EVO this is demonstrated with the option of an electro-hydraulic Dual Power drive for on-site CO2 emission-free work. If a mains connection is available, the machine can be operated in allelectric mode. If there is no power supply available, the MSS502i EVO can still be used flexibly with its diesel drive. The load-controlled fan guarantees a reduction of the noise level and diesel consumption.
Water spraying at the discharge conveyors reduces the dust emissions and therefore ensures better working conditions for machine operators and higher levels of acceptance from local residents.
Specialising in crusher parts has established CMS Cepcor as a strategic partner to many operators. Our service lead offering is designed to keep your crushing equipment active and maximise production.
Trading since 1960, CMS Cepcor is a family-run business founded on expertise and consistent quality, with a heritage of delivering on promises.
Now the leading aftermarket manufacturer and supplier of crusher spare parts and liners, CMS Cepcor prides itself on delivering the trinity of non-negotiables; quality parts, exceptional customer service and quick delivery thanks to a UK stock holding of over £30 million.
Able to precision engineer parts, designed, manufactured and quality assured to be compatible with original part specifications, CMS is the alternative to the OEM for spare parts and wear liners for cone crushers, jaw crushers and impact crushers.
We’re experts for a reason. Our specialism is crushing equipment and unlike most other suppliers, we are focused on the production and supply of replacement parts and the service to fit them. Whether you need routine servicing,
scheduled liner changes or full crusher rebuilds, we are setting the standard as the go-to supplier. CMS also stands out for fast response times, something we’re able to achieve due to an expansive UKbased Global Parts Centre, along with our service team who are able to visit sites with all the required tools to do the job, including crane lorries – removing the requirement for third party crane hire. We understand that you need a provider that works as fast as you do, so we combine proactive service with reactive response times to reduce your downtime.
At CMS Cepcor we design and manufacture compatible parts for machines built by major OEMs such as Sandvik, Metso, Nordberg, Symons, Terex, McCloskey, Kleemann and Fintec. Our certified crusher technicians are available to complete on-site installation and service on a wide range of models, for the most cost-effective solution. At our Global Technical Centre in Coalville, we also have a certified crusher rebuild facility, equipped with specialist tooling – accredited by several OEMs.
CMS Cepcor’s commitment to excellence has recently earned it a prestigious King’s Award for
Enterprise, International Trade, 2024. Previous acknowledgments include the Queen’s Award in 2012 and 2019, underscoring CMS Cepcor’s long term consistency in engineering excellence, product quality and high levels of customer service.
Despite CMS Cepcor now gaining global recognition, we are still as dedicated as ever to serving home industries and supporting UK demolition customers. Our Global Headquarters in Coalville, Leicestershire is centrally and conveniently located for distribution across the whole of the UK. Here we have state-of-the-art manufacturing facilities where precision engineering turns raw materials into high-quality spare parts, as well as our Global Parts Centre – more than 6,000m2 of warehousing and storage, which ensures we can ship our parts quickly.
CMS Cepcor is redefining industry expectations and continues to lead the way in the supply of aftermarket crusher parts.
Crushing Austrian based Rubble Master is leading the impact crushing world with its range of RM crushers, available from UK distributor Red Knight 6 Ltd. The range is led by the RM120X, delivering maximum efficiency and simplicity for use on a wide range of applications.
The RM120X features a range of solutions to make the life of the operator easier and safer, whilst also delivering cost benefits back to the business through intelligent management of the machine, based on the amount and type of material being crushed.
The RM Operations Assist and RM XSMART functions enable the operator to keep track of the machine’s performance from the
cab, with live updates on engine performance, fuel consumption and machines performance all clearly visible via a lighting system on the outside of the machine.
Paul Donnelly, Managing Director of Red Knight 6 Ltd said: “The Rubble Master impact crushers are industry leading for a reason. Built to the most exacting standards, we’ve sold over 190 machines in the last five years and those customers know they can trust the RM range to get the job done. The RM120X is the next evolution in the range. The largest of the impact crushers, it also offers simplicity of use, maximum efficiency and safety for the operator via the Operations Assist.”
The Rubble Master range are highly mobile, versatile and powerful machines that are ideal for crushing natural rock (riverbed material, basalt, limestone, gypsum, granite) and for recycling rubble, asphalt, concrete, glass and production waste.
The range consists of five machines, from the RM 60 to the full spec RM120X. The hallmark of all five crushers is simplicity and efficiency, meaning short set up times and ease of use, getting RM crushers to work quickly.
Rubble Master has built its success on its market leading impact crushers, but its range of tracked scalping and sizing screens continues to gain traction in the market.
Run out of the RM Dungannon site, the factory seems to bring the expertise from their crushers to the range of screens. There remains close cooperation in product development between the RM headquarters in Linz and RM Dungannon, driving excellence across the ranges.
The range of scalping screens has four machines in total, from the incredibly compact but robust
HS3500M through to the largest screen, the HS11000M. There is also an extensive range of sizing screens with both two and three deck options, depending on your requirements. The MSC8500e also offers full hybrid drive capability, allowing you to limit fuel costs. It is something that has long been a feature of the crushing machines, but the same technology has been incorporated into the screeners, another example of the two sites working closely together for the benefit of customers.
“We completed a number of deals across both ranges and the feedback remains fantastic. Customers really see the quality of the machines, from build to operation and both ranges consistently exceeded expectations,” said Paul Donnelly, Managing Director at RK6. “Efficiency of operation is key but the ability to reduce fuel costs and have a positive environmental impact is crucial. We’ve seen a genuine improvement across both screening ranges and our customers are benefitting from that as well,” finished Paul.
A selection of the RM range of crushers and screens are available with hybrid or fully electric drive systems reducing your energy consumption and overall operating costs. As well as lower costs, reduced emissions are ideal for inner city operation as noise will also be reduced.
In addition the range is also equipped with X Smart, enabling even greater efficiency of operation.
Interviewee: Kris Whitehead
Role: Head of Sales for Contractor
Direct UK
Company: Husqvarna Construction
Kris Whitehead has been in the construction industry for over 20 years. When he joined Husqvarna Construction in 2017, he was appointed Head of Sales, Contractor Direct.
Today he is leading a dedicated sales team focusing on surface preparation, and on contractors in the sawing, drilling and light demolition business.
Q
What is your core message to our demolition contractor readership?
In construction risks are everywhere. Being responsible means proactively looking for ways to avoid and manage them. That’s why safety is a natural and essential part of everything we do. Our holistic approach includes making products that are easier to use to get the job done with less strain, offering innovative safety features that provide extra security, and training so you always know how to use our machines correctly. And we’re always looking to improve the jobsite even further, such as by helping you manage dust, minimise vibrations and reduce noise.
Similarly construction equipment has a hard life and therefore the aftersales and service element to support our contractors is what we are constantly reviewing. Knowing that support is there gives our contractors enhanced peace of mind, they know they have a trusted partner in their corner when needed.
QGive us some background on Husqvarna
Husqvarna is one of the oldest companies in the world. Swedish based we have a history spanning back over 330 years. Often remembered for our production of motorbikes in the past our current large portfolio supplies innovative products for a wide section of the construction industry as well as being a market leader in forest and garden equipment.
Husqvarna Group operates all over the globe and is a recognised brand in most major markets, in the UK we have five main sites that cover the entire UK and ROI and have a significant partnership network through our distributors to further enhance this.
Q
What do you enjoy about your role?
I love innovation and being able to help develop products that the market and our customers want and need is very satisfying. The technological advancements that are in constant motion are exciting and bringing new ideas and better processes to benefit the overall industry is where I take great pride. For me having the equipment to support our contractors to complete their projects is key and the aftermarket support as previously mentioned.
Our newest addition to our range the half tonne DXR 95 is a prime
example. It combines both impact and power but in a small footprint meaning it’s a perfect addition to demolition fleets considering its versatility to climb stairs, reach small spaces and ease of transport.
QTell us about Husqvarna’s products and how your relationship with clients works
Husqvarna Construction operates three main routes to market. We have rental partners both local and national who act as great advocates for our equipment in fulfilling the short and medium term requirements of our products.
From a sales perspective we have a split between our dealers and what we refer to as contractor direct as you note. Our dealers will cover the length and breadth of the country and both supply our products parts and accessories as well as offer additional services.
I currently look after the contractor direct channel. These
are the largest of the contractors in our industry. I have a team of very experienced people whose daily activities are to find solutions to our customers problems. We all have had projects that don’t go to plan and the industry needs to have a network to call upon to use that collective wider experience and that’s where we come in. Whether it be on demolition robots or finding the right bond of a blade for a floor saw.
Our products range from an unrivalled (in my opinion) surface prep range, through to our more traditional sawing and drilling offering, to the now well-established demolition robot range. We also now have significant concrete placement offering on trowels and compactors so we can supply the equipment to deal with concrete from start to finish.
QWhat makes Husqvarna different from its competitors?
I would say it’s a mix between innovation and people. We have a big community of colleagues many of whom have been with us for over 40 years. That’s a significant amount
of experience that money just cannot buy.
Whatever the problem we have a network of people who connect across the globe so there is rarely a situation that we cannot call on someone who has seen and can supply advice or support and I think that’s invaluable.
Innovation is a word that can be used too often but Husqvarna really does live and breathe the message. There is a constantly moving R&D department for each category of equipment.
Times change and technology is constantly advancing, we thrive on finding new solutions and engage with our customers regularly to gain insight into exactly what is they want not what we think they need.
I’ve mentioned it already but aftercare here is important. There is a significant investment from our customers in our equipment and they deserve to know that they will be supported through the life of their equipment. We have a number of mobile technicians able to support on site as well as our engineers based at our service centres.
QTell us about Husqvarna’s working culture
We have a core message for our working culture of Bold, Dedicated and Care. This means we encourage all our colleagues to dare to consider alternative and different angles to solve problems, we strive to work tirelessly for our customers and our own organisation but at the same time we consider the people element in all that we do.
Collaboratively working is critical, our teams collectively work together on a daily basis and communicate and share information across departments. Our teams are just that, teams, and as such support each other across geographical boundaries. I think we are seen as a trusted partner, ultimately business is people dealing with people and we hold strong relationships with our customer base.
QAre there any standout product developments from Husqvarna’s history?
So many it would be hard to list. Product development from our history is diverse with power cutters and floor saws to planetary grinders and now the RC Demolition Robots.
QTell us about one of your key demolition-relevant products
Our DXR range of demolition robots is what I am most proud of. We launched our first demolition robot fifteen years ago and the advancements we have made from a technological perspective since then are significant.
Today we have a range of sizes but all are operated from the same remote control platform. This gives the operator full control, whether it being able to stabilise the machine on rough ground by independently operated stabilisers or stability when on an incline such as a staircase or incline up to 30 degrees.
We use the latest electrical and hydraulic components to get the most impact or power out of each sized machine. Naturally they all fulfil third party certification around standards related to Machine Safety, “Functional Safety” and EMC.
We are quite proud of their track tensioning functions especially on the new DXR 95 and we have a variety of accessories depending on the project from breakers, crushers to shears, manual handling tools and even buckets for excavation.
The DXR range is designed to give the utmost power for the size of the machine, maximising the investment return whilst also using size to benefit in both accessibility and transport ease.
The remote control function puts real power in the operator’s hands and allows them to perform the functions of the machine at up to 300 metres away. The remote gives the operators all the access to the information required to complete the projects at hand including being able to diagnose electrical faults as power can often be a problem when on site.
The DXR range will give the most power to weight ratio when working in both tight and open spaces when needing to demolish structures. It has versatility in manoeuvrability, transport and operational advantages. What’s also often overlooked is its ability be used as a manual handling machine or an
excavator, ultimately it’s a flexible tool carrier capable of multiple functions.
Our main message when it comes to our DXR range is come and try one. We will offer either demonstrations at one of our centres or coming on site. We believe in letting the machine do the talking, they are the best advocates for themselves.
The biggest cost to any business in our industry is labour. All businesses need quality skilled and trained people but maximising their productivity by completing projects efficiently naturally improves the bottom line of any contractor.
Reliability, speed and scope of aftersales service as well as the most efficient equipment for the job will always drive growth for construction and demolition companies and this is where we feel we have a strong story. As I said, we started out fifteen years ago here and we have transformed the market already. And we aren’t stopping there. Continuous development of the products to further drive the safety of operations and the profitability of our customers is at the forefront of what we strive to do.
Who do you most admire?
Carl Jung. He was a 19th century psychiatrist, psychotherapist and psychologist and pioneered many theories on personality styles and collective behaviours of people. His work has spurred many others to bring his findings to a wider audience than just academic. For me I find it fascinating and helpful to see the world through different people’s eyes and it helps to understand what normally could be dismissed as unidentifiable behaviours.
What would you do for a company excursion, money no object?
I spent a part of my childhood in South Africa though I have not returned in many years. I would love to visit and take my team on a wildlife reserve to see such magnificent creatures that we are blessed with in their natural and protected environment, it would be exceptional. It’s also one of the most beautiful and culturally enriched countries I have ever
Snapshots of Ben and the Demolition Hub team’s activities between issues
by Richard Vann
When conducting a decommissioning survey, more information doesn’t always equal better outcomes. Richard Vann, Managing Director at RVA, advocates for a “less is more” approach, highlighting how prioritising quality over quantity can transform project safety, efficiency and cost control for the better.
is a decommissioning survey and why does it matter?
When a power plant, chemical facility, or other complex industrial site reaches the end of its
operational life, you need clear insights before dismantling begins. A decommissioning survey tells you what’s safe, what could present risks and which materials, residues and structural quirks the site holds. Ultimately, the role of this process is to gather data needed to make the decommissioning exercise safe, compliant, efficient and costeffective.
At this stage the instinct might be to gather every piece of information possible. This paints a more comprehensive picture and improves project outcomes, right? In reality, it can have the opposite effect. Gathering too much, or the wrong kind of data, can overwhelm decision making, obscure real safety issues, waste resources and complicate an already complex scope of work.
Taking a “less is more” approach –focusing surveys on complete, accurate and genuinely relevant information – is therefore crucial. And it lets contractors and engineers approach each phase with confidence, knowing they’re armed with exactly what they need, when they need it. In other words,
it’s about aiming for precision, rather than overload.
But what does this look like in practice?
The primary goal of a decommissioning survey is to establish a stringent health, safety and environment (HSE) regime. Gathering a flood of data on irrelevant risks won’t help here. Instead, you should identify the exact hazards that matter most to the plant in question and target them in the survey. By zeroing in on specific HSE issues impacting the project, contractors can develop safe systems and best practices for subsequent work packages, ensuring safety is woven into the project’s fabric from the start. From project managers to on-the-ground engineers, limiting guesswork translates into safer outcomes for everyone.
A targeted survey exposes information gaps that could lead to liabilities if overlooked. But don’t rely solely on data. To uncover
critical issues that may be otherwise missed, the knowledge of operators who have run and maintained the plant for decades becomes invaluable. These individuals possess site-specific insights that can help identify potential hazards or residues that may not be documented elsewhere. So, by leveraging their expertise during the survey process, we can address knowledge gaps before they become liabilities, ensuring no significant risks are left unexamined.
Every decommissioning project is different and technical surveys should reflect that. A one-size-fits-all approach is not only inefficient, it can also lead to misunderstandings and severely overlooked risks.
Consider a chemical facility where specific hazardous materials have been used over the years, for example; a blanket survey may fail to address unique handling and disposal requirements, leading to potentially dangerous situations down the line. When survey data aligns with the unique needs of a project, you get smarter, safer and
more efficient outcomes from start to finish. At this stage, it’s about being as dynamic and adaptable as the decommissioning projects themselves, mitigating unnecessary data distractions in the process.
Managing budgets and tender submissions can feel like a balancing act. The challenge lies in accurately predicting costs amid uncertainties that come with dismantling complex industrial sites.
When surveys are overloaded with irrelevant data, it can lead to inflated budgets and unrealistic tender prices, resulting in confusion and potential project overruns.
With more precise, targeted data from the outset, we can gain clearer insights into the real costs involved, helping project managers craft more accurate budgets and establish deliverable tender prices, reducing financial surprises further along in the project.
Perhaps the most important part of a decommissioning survey is
thoroughly identifying and recording every risk and residue. More than tick-box documentation, this step is about translating hazards into straightforward language that can be planned around, without ambiguity.
A comprehensive, precise risk assessment avoids assumptions and establishes a clear roadmap for every project stage, because nothing should be left to chance – especially where human lives are concerned.
Ultimately, clarity and relevance aren’t just preferences during the survey process – they are essential to ensuring safety, boosting compliance, streamlining decision-making and keeping budgets in check. In a field fraught with complexity, this “less is more” approach can often be the key to safeguarding success at every stage. Crucially, this doesn’t mean doing the bare minimum – far from it. It requires deeper consideration and strategic thinking to determine which information truly matters. But once pinned down, this pays dividends in the long run.
by Terry Lloyd – Head of Vendor in the SME Lending division at Paragon Bank
As we approach the end of 2024, I wanted to take the opportunity to reflect on the year we’ve had and its impact on the construction and demolition industry.
It has been an interesting 12 months, one that has seen challenges and change.
At the start of the year, we experienced some difficulties as an industry due to severe weather conditions, meaning heavy rainfall and extreme flooding in some areas. It was particularly disruptive for the construction and demolition industry, with work having to halt on site due to potentially dangerous conditions.
While health and safety is always the priority for businesses, it can
be disheartening when projects are delayed and for many, it can mean serious financial difficulty, with businesses potentially left struggling to pay their staff and for their equipment. A challenge that many in the industry will know well and have sympathy for those in that position.
Furthermore, this year we’ve also seen big political change. It was only May when then Prime Minister, Rishi Sunak called the general election for 4 July, a move that very few were expecting so soon.
Following a landslide Labour victory and the party’s promises of growth, there were announcements including mandatory housing targets and the new national wealth fund, creating a sense of excitement and anticipation.
However, this was quickly followed by a summer of rhetoric around the deficit in public finances and the nerve-racking upcoming budget – which delivered some big tax increases, as well as more commitment to house building, the latter of which has been welcomed by those in the construction industry, plus some big infrastructure projects, such as extending HS2 into Euston Station.
Insolvencies have been high this year and construction is one of the sectors hit hardest. We know there have been tough times not just in 2024 but over the past few years, but we hope we are entering a
new stage of the cycle and a more positive environment.
This can be seen in the recent construction figures for the three months to August 2024, where construction output grew by 1%, due to an increase in new work – a positive sign for the new year.
It is also worth mentioning some of the great highlights that we’ve had this year, one of which is the return of the bi-annual industry show, Hillhead.
This highly anticipated event always offers the chance to reconnect with those you haven’t seen in a long time as well as meet new people. Furthermore, it’s a great opportunity to witness first-hand the technological advancements of the machinery, demonstrating how quickly the industry is moving and the innovation of the manufacturers.
While it seems that it’s been an eventful year, as we enter 2025 there are lots of things to be positive about and we have more exciting industry events to look forward to such as PlantWorx. In addition, we are also starting to enter a lower interest rate market – something that many businesses and individuals have been waiting for.
Furthermore, we remain hopeful about plans to put housebuilding and infrastructure back at the forefront of the construction industry and expect we’ll see these plans coming to fruition as the year starts.
by Richard Dolman
There were several announcements in the budget that we may or may not have wanted to hear. Since the election of the new government they have been pledging a very positive message to “get Britain building again”, but has their first budget kick started this process?
We will all feel the effects of the increase in employer’s national insurance contributions from April, particularly SMEs. The increase in minimum wage is welcomed and a positive when attracting new people into the industry, however, this is at a slight cost but one we should embrace.
There will inevitably be an impact of an increased tax burden, this most likely be passed onto consumers through price increases leading, as the Bank of England predicts, to gradual inflation rises. We are already seeing, despite the recent point reduction on interest rates, that the major banks are increasing their fixed rate mortgages following the budget announcements.
Labour pledged to “get Britain building again” and set a very ambitious target of 1.5 million new homes to be built within their term (although the private sector has built less than 200,000 homes a year since a slight peak in 1988, with housing association properties
contributing usually no more than an additional 40,000 per year *Statista 2024), but how will this impact us?
There are some key commitments made including progressing HS2 phase 1 and “priority transport schemes” such as TransPennine route and East West Rail.
Education settings are being given a funding boost of £550 million to £1.4 billion to help rebuild more than 500 schools, although private schools may be less inclined to commit to any construction or demolition works with their imposed tax burden from April.
Hospitals are also benefiting with more than £1 billion allocated to address the problem of Reinforced Autoclaved Aerated Concrete (RAAC) and other repairs across NHS property, plus a fund is being set up for maintenance of doctor’s surgeries.
There have been increasing issues with planning backlogs and the impact on our industry and the wider construction industry over recent years, so it is good news there is going to be investment in the planning system.
The budget set aside funding for councils to recruit an additional 300 planning professionals. According to the Royal Town Planning Institute (RTPI) there are currently
approximately 22,000 planners in the UK so it is difficult to quantify how much of an impact an additional 300 will make to reform the planning system.
£80 million will fund the Brownfield Land Release Fund to support councils to develop brownfield land, which again is a positive message but is the rest of the infrastructure in place and sufficiently funded to deliver this?
The government is investing £5 billion to increase the supply of affordable homes, which is a very positive message, however, do we have the skilled labour to fulfil this?
We need, more than ever, to capitalise on the government’s commitments and ambitions to get Britain building. We should promote our industry and get more skilled workers into our sector.
There are further budgetary pledges and taxations that will have some positive and negative affects on our industry, however, the push appears to be to invest in longer term construction projects and redevelopment of brownfield land, positive messages for our industry.
Let’s take that message and get more people into our industry by inspiring our future workforce, investing in training and enabling career aspirations to be fulfilled.
Earthmoving solution expert, Komatsu, has combined artificial intelligence (AI) to modernise its Smart Construction Edge solution, in partnership with technology giant Sony as part of the EarthBrain joint-venture across Komatsu, NTT Communications, Sony Semiconductor and Nomura Research Institute, to champion digitalisation and advancement in drone surveying processes.
The innovative Edge solution is a unique device that works to enable both experts and beginners to perform accurate drone surveys and process drone flights into point clouds. The EarthBrain partnership works to optimise the construction processes through digital transformation to maximise
productivity, improve worksite safety and environmental sustainability.
With its latest Edge evolution, Komatsu Smart Construction now offers a terrain mapping tool using AI to remove obstacles such as machinery and buildings from drone surveys, reducing the need for manual amendments once the data has been captured.
Bart Vingerhoets, Senior Commercial Manager at Komatsu Smart Construction said: “I’m extremely proud to launch this new version of Edge into multiple markets. At Komatsu Smart Construction we’re committed to helping professionals within our sector increase productivity to ultimately save time and money.
“A major benefit of our updated
Edge solution is its ability to speed up data processing from drone surveys to create a fully accurate, digital twin. When connected with the Smart Construction Dashboard solution, the 3D terrain maps available will save time spent on the jobsite and the data collected including volume, percentage of progress and location on site can be collected
quickly and efficiently.”
The updated Edge solution was initially unveiled at the Intermat exhibition in Paris in April 2024 and is now available across multiple European markets Germany, France, Austria, Poland, Switzerland and the United Kingdom.
When the main surveyor of medium-sized Belgian earthmoving company CROES VS went on maternity leave the company faced challenges to maintain its surveying capabilities, making it difficult to carry out its projects with the same level of precision and efficiency.
CROES VS implemented the revised Edge technology and the workload gap was seamlessly filled without the requirement of additional training or recruitment.
The solution allows various team members, including the marketing manager, to take on drone surveying tasks and capture survey-grade earthmoving progress, identifying challenges and opportunities within seconds.
Bart Vingerhoets continued:
“Working with CROES VS has highlighted the importance of enhancing data processing speed and accuracy – serving as testament to the construction industry’s requirement of broader drone surveying adoption.
“Adopting the use of AI within the latest version of Edge means the device can eliminate the need for Ground Control Points (GCPs), which will enhance safety and efficiency on site and process data into 3D point
clouds without the requirement for internet connection. The overall goal for this enhanced Edge solution is to streamline the entire process to enable seamless terrain mapping.”
Komatsu Smart Construction experts utilise digital tools to assist clients in the earthmoving and quarry industries by finding the optimum way of using resources like machine, material and people for enhanced productivity, quicker project completion, cost savings, improved safety and reduced CO2 emissions.
smartconstruction.io
www.komatsu.eu
Anglian Demolition has undertaken a redevelopment project to help transform existing office buildings in Cambridge into a state-of-the-art 42acre parkland science campus. The project has created premises that have reduced carbon emissions by 40% compared to a new build.
The three-month project at CamLIFE (Cambridge Lab and Innovation Focused Environment) in the location formerly known as Capital Park, was undertaken for Longfellow Real Estate Partners – the largest privately held investor and developer of life science buildings in the US. Anglian acted as main contractor for building and property maintenance firm Wates.
Employing a team of 30, Anglian carried out works including partial demolition, internal demolition,
alterations and soft strip within three office buildings that were built in 2013. Once fully complete, CamLIFE will deliver approximately 170,000 square feet of best-in-class fitted lab and office space.
The aim of the redevelopment project was to utilise the existing properties and follow an adaptive redesign approach to achieve the lowest environmental impact. This has resulted in a 40% wholelife embodied carbon reduction compared to a new-build net-zero equivalent. With a long-standing commitment to sustainable development, Longfellow is targeting BREEAM Excellent and EPC A during this project.
With many different materials within the buildings that all needed to be removed, Anglian used its
expertise to complete each stage of the demolition process. This included carefully removing large panes of glass and metal spiral staircases, as well as saving 3,000 bricks to be reused in the next construction phase.
As with every Anglian demolition job, all waste created was transported back to Anglian’s 10acre facility in Attleborough to be processed. As much material as possible was reclaimed for recycling or looped back into the circular economy, including 87 tonnes of metal, seven tonnes of glass and 11.5 tonnes of rubble.
Andy Elvin, Senior Contracts Manager at Anglian Demolition and Asbestos, said: “We were delighted to undertake this latest project for Wates on behalf of Longfellow. This was a significant project for us which utilised the many skills we have within the team here at Anglian. As a business, we are committed to reducing the impact of demolition jobs on the environment by segregating and processing our waste as standard. This approach complemented perfectly the aims of Longfellow to create state-ofthe-art premises with minimal environmental impact and the highest standards.”
Norfolk based multi-service contractor Anglian Demolition and Asbestos has won a prestigious Sub-contractor Award from leading construction firm Kier.
The Positive Attitude and Conduct Award was presented by Kier Eastern and Midlands to John Bergin, Project Manager at Anglian, for his work on a demolition project at Samuel Pepys School in St Neots.
Undertaken during the summer, the project saw a range of demolition work at the school including internal soft stripping of the buildings and hand demolition and propping on a series of internal walls. Anglian had a team of four working at Samuel Pepys led by John, alongside demolition operatives Dev Blundell, Dean Nelson and Lee Beckett.
The Positive Attitude and Conduct Award was given to John in recognition of his exceptional conduct and professional attitude towards Safety, Health, Environment and Quality. The award was presented to John by Dennis Cotton, regional director at Kier – Cambridge and Midlands, at Kier’s offices in Waterbeach.
Paul Nelson, Contracts Manager at Kier, said: “This was awarded following the great work completed by John and his team at Samuel Pepys School. John kept a tight ship and despite the demolition works being tricky to complete. All activities were carried out safely, working
spaces kept spotlessly clean and the team had a positive approach to working with the Kier team and others on site.”
John Bergin, Project Manager at Anglian, said: “Health and safety is paramount to every project we undertake at Anglian and I am honoured to receive this award. This was another great job for Kier and the entire team deserve recognition for their hard work throughout.”
Anglian has been working with
Kier for many years on a range of projects. A multi-service contractor, Anglian’s divisions include Anglian Demolition and Asbestos, Anglian Scaffolding, Anglian Earthworks and Remediation and Anglian Waste Recycling.
There’s only one place you’ll find the heavy hitters of concrete and masonry this January: Vegas, baby — at World of Concrete 2025, the largest and only annual international event dedicated to your business. Be here to mix with industry giants. Get your hands on the latest technologies revolutionizing safety, performance and speed. And learn what it takes to not only claim a piece of our industry’s massive projected growth but dominate the field. Join the power players of concrete and masonry.
EXHIBITS: JANUARY 21-23, 2025
EDUCATION: JANUARY 20-23
LAS VEGAS CONVENTION CENTER
Cat Command for Loading is expanding to all medium wheel loaders, excluding the GC models. Removing the operator from the machine, Command for Loading offers semi-autonomous remote control of next generation Cat 950 – 982 wheel loaders designed to increase operating safety in hazardous environments.
• Remote operation expansion: Cat Command for Loading now supports Cat 950, 962, 966, 966 XE, 972, 972 XE, 980, 980 XE, 982, and 982 XE next generation wheel loaders,
• Enhanced safety: By allowing the user to comfortably control the machine from a safe location, Command maintains high machine productivity in operating environments like demolition, environmental remediation, stevedoring and the handling of fertiliser, chips and sawdust,
• Remote operation options: Available in both line-of-sight and non-line-of-sight configurations,
• Full integration: Integrated with the loader’s electronic and hydraulic systems for quick response and smooth control.
• Versatile control: Allows easy switching between remote and manual in-cab operation,
• Dealer-installed package: Command hardware comes in a dealer-installed package that includes a low-profile design on the roof of the loader, requiring no welding or wire splicing,
• Ergonomic console: Basic machine controls such as wheel loader startup/shutdown, bucket rack/dump and lift/lower are easily accessed through the ergonomic console control layout. Operator inputs are sent directly to the machine’s electronics from the Command console,
• Safety features: All wheel loader movements cease when the A-stop or remote shutdown switch is pressed, wireless communication is lost, a severe fault is detected or the Command console is tilted more than 45° from normal operating position,
• Command Station: For non-line of sight operation, the Command for Loading station connects to multiple machines at the same job site or different sites. The user can operate one machine at a time either on site or from miles away. It is compatible with other Command offerings for Cat equipment, including excavators and dozers.
W E A R E
C A W A R D E N
F o r m o r e t h a n 3 5 y e a r s , w e v e b e e n a
t r u s t e d f a m i l y - o w n e d a n d o p e r a t e d
s p e c i a l i s t c o n t r a c t o r , c o n s i s t e n t l y
d e l i v e r i n g e x c e p t i o n a l p r o j e c t s
L e t o u r e x p e r t i s e a n d e x p e r i e n c e
w o r k f o r y o u
c a w a r d e n . c o m
One of Birmingham’s leading demolition specialists has been appointed as President of the Institute of Demolition Engineers (IDE).
Armac Group’s Adrian McLean takes over from Vernon Watson at the helm of an organisation that boasts over 400 members and is responsible for pioneering, promoting and professionalising a sector that started 3,000 years ago.
The Operations Director, who himself has been in the industry for more than three decades, is looking to steer the IDE through one of the most exciting and challenging periods in its 48-year history, with a new focus on sustainability, the circular economy and developing the next generation of specialists.
There will also be a special focus on increasing its international
membership, with overseas demolition engineers now able to benefit from an excellent “Transforming Demolition: Rethinking Demolition Management Through Circular Economy Principles” course run online by the Perses Academy.
This is non-country specific and provides the perfect grounding for members to start their journey.
“It is a very proud moment to take over the Presidency of the Institute of Demolition Engineers, especially as it happened in my own town of Birmingham,” explained Adrian, who had the privilege of bestowing full membership on his son Cormac at the same event.
“I’m under no illusion to the challenges we face and the opportunities we must strive for. Things are changing faster than at any point, with structure
“Every new project tends to start with demolition and I want to ensure the Institute of Demolition Engineers continues to help its members pave the way for a brighter future”
and material reuse revitalising old methods and legacy issues –including RAAC and Large Panel System concrete structures –accelerating innovation amongst demolition firms.”
He continued: “As the industry changes so rapidly, the role of a demolition engineer must diversify and we have been providing more upfront material recovery feasibility assessments, which is leading to new techniques and ways of working.
“The IDE has supported this transition for some years now by creating educational routes for future members and a robust continuing professional development programme for its current members. This will accelerate under my stewardship.”
Solihull-based Armac Group has been operating in the UK for more
than 27 years and was founded by Adrian’s father Noel Snr, who left his hometown of Cork with very little in his pockets to set-out on a new potential career in demolition in the West Midlands.
It was a fruitful decision, with the company now one of the most respected in its field, employing 67 people directly and lots more in its supply chain.
Hundreds of projects have been completed throughout the years, including the high-profile removal of Axis House in Birmingham City Centre, the SAS13 bridge replacement to facilitate HS2 and the demolition of the iconic Wembley Way footbridge at the home of English football.
Adrian picked up the story: “A big focus will be on improving the IDE member experience through
even greater access to best practice seminars, more networking events and increased cross-institutional collaboration with groups outside of our own industry.
“We also want to communicate better by fully embracing the digital age and increasing the reach of our forums that are so appreciated by our members.”
He concluded: “Every new project tends to start with demolition and I want to ensure the Institute of Demolition Engineers continues to help its members pave the way for a brighter future.”
Rebecca Redmond, Clifford Devlin’s Business Development Manager is running the 2025 London Marathon for the National Federation of Demolition Contractors.
Team NFDC are running for the charity Sue Ryder. Sue Ryder is dedicated to ensuring that everyone facing the end of life or coping with grief has access to the care and support they need. There is no onesize-fits-all approach to dealing with grief or the end of life, but with Sue Ryder’s compassionate assistance, no one has to face these difficult times alone. They are there when it matters most.
Any donation will be greatly appreciated.
To donate to Rebecca, you can scan this QR code
Since being established in 2012, Romax Solutions has set a high standard when it comes to recruitment. Finding the best candidates is our driven desire and passion, we aim to meet the recruitment needs of a diverse range of clients within the construction industry. Being based just outside of London gives us easy access to service all clients throughout Essex, London, Kent and surrounding areas while also having the capabilities to support and service nationwide projects and clients.
With a depth of knowledge, our experienced and trusted staff are on hand to deliver a bespoke service to each and every client, supplying reliable and talented staff of all levels both nationally and locally. Romax Solutions
is fully accredited by the Recruitment and Employment Confederation and the National Federation of Demolition Contractors. These accreditations have enabled us to work alongside other NFDC members to meet their scope of needs on multiple projects. These projects range from small scale strip outs to large scale power station decommissions.
We are also always keen to add new talent to our current pool of candidates nationwide. These include those from management level downwards, including skilled demolition operatives and even those just starting out their demolition careers. We work effortlessly to ensure all candidates are fit for purpose, including using accredited training providers to upskill our operatives.
(Cat B Non-licensed asbestos removal)
Wandsworth, south-west London
Role: CCDO Operative with Cat B, for demolition works
Rate: £17 – £19 p/h
Requirements:
• CCDO Green/Red qualification
• Cat B Non-licensed asbestos removal
• Full PPE
• Minimum of two years’ experience in demolition
• Good timekeeping and willingness to work
What we offer:
• Ability to work through CIS / self-employed
• Weekly payments
• Assistance in regard to progression within construction
• Ongoing labourer work for the right candidate
For more information and to work on this project please contact the account manager of this specific job on 07557 196 353
Romax Solutions provides long term work for the right candidates depending on reliability and willingness to work.
Role: CCDO Operatives, work involves demolition, soft strip, long term works.
Rate: £16 – £18 p/h
Requirements:
• CCDO Green/Red Card
• Full PPE
• Minimum of two years’ experience within construction as a CCDO
• Good timekeeping and willingness to work
What we offer:
• Ability to work through CIS / self-employed
• Weekly payments
• Assistance in regard to progression within construction
• Ongoing work for the right candidate
For more information and to work on this project please contact the account manager of this specific job on 07557 196 353
Role: 360 Operator (D90) required for a demolition breaking works
Rate: £21 – £22 p/h
Requirements:
• Blue CPCS (NVQ Level 2) + D90 ticket
• Full PPE
• Minimum of three years’ experience as a 360 Operator and in demolition
• Good timekeeping and willingness to work What we offer:
• Ability to work through CIS / self-employed
• Weekly payments
• Assistance in regard to progression within construction
• Ongoing work for the right candidate
For more information and to work on this project please contact the account manager of this specific job on 07557 196 353
Romax Solutions provides long term work for the right candidates depending on reliability and willingness to work.
Role: CCDO Burner for burning works taking down structural steel works
Rate: £20 – £22 p/h
Requirements:
• CCDO/ CSCS card
• Oxy Fuel Cutting qualification
• Full PPE
• Minimum of three years’ experience within construction as a CCDO Burner
• Good timekeeping and willingness to work
What we offer:
• Ability to work through CIS / self-employed
• Weekly payments
• Assistance in regard to progression within construction
• Ongoing labourer work for the right candidate
For more information and to work on this project please contact the account manager of this specific job on 07557 196 353
Bobcat has added a new Remote Engine Disable/Enable feature on the company’s Machine IQ telematics platform. The new feature allows customers in Europe to remotely enable or disable their machine’s engine through the Owner Portal or Machine IQ app. With Remote Engine Disable/Enable, operators and owners can shut down their machine with a few clicks, deterring theft and aiding in quick machine recovery.
Machine IQ, launched last year in Europe, allows connectedmachine owners to monitor the health of their Bobcat machine and remotely track information that enhances maintenance, security and performance.
The new Remote Engine Disable/ Enable feature represents the first two-way update for the telematics system, allowing operators to both send commands to and receive data from the machine. Remote Engine Disable/Enable via Machine IQ can be activated in Bobcat skid-steer and compact track loaders, miniexcavators and compact wheel loaders connected to the system.
Tomas Plechaty, Machine IQ Senior Program Manager at Bobcat EMEA said: “Enabling advanced theft
deterrence provides critical peace of mind for our Machine IQ users and Remote Engine Disable/Enable allows our European customers to protect their equipment and allow only authorised usage.
“This feature also demonstrates our ability to interact with machines via two-way communication using telematics. Today marks another major milestone for what Bobcat continues to do – to empower our customers to accomplish more.”
Available with Premium Machine IQ subscriptions, this innovative solution empowers customers to remotely prevent theft and unauthorised use in just a few clicks. If unauthorised use is suspected, customers can log into their Bobcat Owner Portal or Machine IQ app to select the asset and click “Remote Engine Disable/Enable” in the sidebar. Only administrative users can access this feature and all Remote Engine Disable/Enable activity is tracked in the asset’s history table. Upon executing the disable command, any attempt to start an engine in an off state will fail. If the machine is in operation, the engine will shift into de-rate mode.
• Deter theft and potentially recover stolen machines: By remotely disabling engines, unauthorised use can be stopped and recovery efforts aided,
• Lower insurance rates: Demonstrating a proactive commitment to investment protection can make customers eligible for lower theft-related premiums,
• More benefits for Premium subscribers: Remote Engine Disable/Enable extends functionality for Premium subscribers, creating more value for customers,
• Boost resale value: Unlocks future-proof security making resale a more attractive and potentially higher-value investment for discerning buyers,
• Improve payment compliance for rentals: Remote Engine Disable/Enable can be used for delinquent rental accounts, encouraging prompt payment and reducing revenue loss,
• Enforce safe operating procedures and prevent potential damage: Engine
operation can be temporarily disabled in response to unauthorised use, unsafe behaviour or potential machine misuse.
With Machine IQ, customers have 24/7 access to crucial machine information on their smartphones or computers. Equipped with this information, customers can optimise machine use and plan jobs for maximum profitability by keeping idle times to a minimum and tracking fuel consumption. Service planning is made easy with maintenance notifications, saving operators time and money by allowing them to efficiently schedule machine maintenance and manage job sites during planned downtime.
Dealers and customers can choose from two options – a Standard package with basic telematics and
a Premium package with additional advanced features. According to Tomas Plechaty, the subscription options let users tailor their experiences and access the level of connectivity and insights that best suit their needs. “With a focus on simplicity for the user, we are confident that the packages will meet the needs of customers and dealers across the globe and help them grow their businesses,” he said.
Machine IQ comes factory-installed with many equipment models and can easily be installed on compatible Bobcat machines in the field. Customers should contact their local dealer to check compatibility. Bobcat customers can access Machine IQ by visiting my.bobcat.com, creating an account and logging in. Alternatively, the mobile app for Machine IQ can be downloaded from Google Play/ Apple Store. www.bobcat.com
The CESAR security scheme, owned by the CEA (Construction Equipment Association) and delivered in partnership with Datatag ID, launched in 2007, has now surpassed 650,000 installations. This milestone marks a significant achievement in anti-theft protection for construction and agricultural machinery, with the announcement at the recent CPA (Construction Plant Hire Association) conference. Steven Mulholland, the CPA’s new CEO, congratulated the scheme’s impact on improving equipment security and reducing theft risk across the industry.
Kevin Howells, Managing Director of Datatag, commented on this accomplishment: “Reaching over 650,000 installations highlights the CESAR Scheme’s success in deterring theft and aiding in recovering stolen equipment. Manufacturers, SMEs, and other companies continue placing their trust in CESAR. Our latest addition, the Ultra Tag RFID Chip, adds another layer of security, offering advanced tamper resistance and improved scanning for swift ownership verification. The multilayered security strategy CESAR employs ensures machinery is
protected through visible, covert and highly effective means.”
CESAR’s new RAPID (Registered Assets Police Information Database) tool also advances the scheme’s impact. RAPID is a web-based solution that enables officers to access the CESAR database directly from their smartphones, streamlining the identification process. Nearly 1,000 officers nationwide have already enrolled,
further accelerating investigations across the UK by enabling immediate verification of CESAR-registered assets on the spot.
The CESAR Scheme, instantly recognisable by its distinctive triangle identification plate on each registered machine, leads the UK in security for construction and agricultural equipment. This highly visible marker aids law enforcement in identifying stolen equipment and
linking it to its rightful owner. In addition to the identification plate, CESAR integrates several advanced security technologies, including a unique forensic DNA marker and microscopic data dots, ensuring that equipment can be traced even if dismantled.
With the recent addition of the Ultra Tag RFID Chip and RAPID, CESAR continues to advance its security framework. The new RFID chip, designed to be tamper-proof and equipped with a longer reading range, offers a quick, non-invasive method for authorities to identify equipment up to 18 metres away. This means an added layer of confidence in their equipment’s security for machine owners, even in challenging recovery situations. Alongside the Ultra Tag RFID Chip, the CESAR scheme’s RAPID asset protection system expands security options, combining covert marking with instant police response, further deterring theft and enhancing the likelihood of recovery. This multi-tiered security framework has positioned CESAR as the preferred choice for owners seeking dependable, industry-leading protection.
Viki Bell, Director of Operations at the CEA, emphasised the scheme’s impact: “The CESAR Scheme is central to our commitment to equipment security across the construction and agricultural sectors. With over 650,000 installations, CESAR continues to prove its value in deterring theft and building trusted protection for machinery owners. This trust and potential insurance discounts make CESAR a solid choice for safeguarding equipment. With RAPID and the tamper-proof RFID chip, CESAR sends a clear message to would-be thieves that marked machinery is well protected and harder to target.”
The scheme’s effective security features, including thousands of microscopic data dots encoded with unique identifiers visible only under ultraviolet light, ensure that even dismantled components can be traced to their origin. Each machine also receives a forensic DNA marker, embedding an unalterable identity into the equipment, in line with CESAR’s motto, “It’s in our DNA.”
For equipment owners, insurers recognise CESAR’s security benefits, often resulting in lower premiums for CESAR-registered machinery.
With over 650,000 systems in place, CESAR has set a high standard in machinery security, providing advanced, reliable asset protection for the industry.
“Reaching over 650,000 installations highlights the CESAR Scheme’s success in deterring theft and aiding in recovering stolen equipment”
In recent years, break-ins and thefts on building sites have surged, posing serious challenges for construction firms and property managers. With expensive equipment, valuable materials, and the vast, often isolated nature of building sites, securing these areas has become increasingly complex and costly.
According to a BauWatch report published in February 2024, a huge 70% of construction workers witness theft on site every year, which causes delays to at least third of construction projects.
In response, companies are turning to new security measures, with a growing emphasis on AIdriven solutions to address these risks. Here, Integrated Fencing details how traditional measures are becoming enhanced by AI technology.
Many construction companies rely on tried-and-true security measures, such as physical barriers, temporary fencing, lighting and security personnel. While these measures are essential in deterring and preventing thieves
from accessing sites and stealing thousands of pounds worth of equipment, they can be dramatically improved with the integration of technology.
That’s why construction firms are now focusing on complementing traditional methods with more advanced technologies to create a comprehensive solution that covers not only the perimeter, but also internal zones of the construction site.
AI technology is playing an increasingly prominent role in addressing the complexities of construction site security. AIpowered surveillance cameras and monitoring systems can analyse video feeds in real time, detecting suspicious behaviour before it escalates.
This means that, rather than relying on human guards to monitor every feed, AI systems can send alerts only when unusual activity is detected – making the response time faster and more precise.
For example, some AI systems can differentiate between regular
workers and intruders based on their movements or even the types of equipment they are carrying. Integrated with access control systems, these AI-powered solutions provide a layered approach to security, ensuring only authorised individuals enter specific areas, reducing the chances of internal theft as well.
Commenting on the role AI plays in construction site security, Hywel Davies, Construction Director and co-owner of Integrated Fencing, said: “The rapid development of AI over the last few years means it is now a part of almost every industry, and security is no exception. We have to embrace the advantages of this technology now readily available and quite easily at our disposal to integrate with traditional methods.
“The rapid development of AI over the last few years means it is now a part of almost every industry, and security is no exception”
“Real time video analysis and alerts for unusual activity, coupled with strong perimeter security fencing and barriers can help eliminate the possibility of thefts altogether. We strongly encourage construction firms to seek help from security professionals who will work alongside them to find bespoke solutions to prevent their valuable equipment from being stolen.” www.integratedfencing.co.uk