
3 minute read
Revolutionising public transport operations with remote monitoring and control capabilities
Thales Group’s Remote Secured Operation Control Center wins at the HKB Technology Excellence Awards 2022.
In our increasingly digitalised world, public transport operators and solution providers are also amongst those that look toward innovations in this domain to increase the quality of service to their end customers, the passengers.
Thales Group develops, manufactures, and sells products, systems, and services in high-technology fields. The development of this large offer relies on strong capabilities in terms of R&D, including both upstream (R&T: research and technology) and in engineering.
To this extent, Thales has established a network of innovation hubs to foster and promote innovative initiatives locally. An Innovation Hub is designed as a creative platform geared towards customer-centric collaboration with three main missions:
• Bridging Thales R&T centres to support new Thales businesses in a country and its neighbouring region;
• Implementing fast prototyping & evaluation of advanced technology concepts to complement Thales Solutions portfolio.
• Complementing Thales R&T competence with the local eco-system (Universities, Start-ups, etc.)
Design Thinking, Lean Start-Up, and Minimal Viable Products (MVP) methodologies are applied in order to deliver innovative and user-centered products in short cycles.
Design thinking is the primary methodology used for discovering each customer’s major problem and proposing solutions, which leads to rapid prototyping followed by the development and testing of MVPs.
Thales, for example, has developed consistent expertise in the simulation environment, video analytics, and big data analytics in Hong Kong since the establishment of the Innovation Hub.
Remote Secured Operation Control Center (OCC) is an innovation of the integrated control centre.
A control centre allows transport operators to monitor their entire network and systems and take action to ensure smooth operations. What about the staff away from the control centre? time to key operation indicators to analyse the current situation and validate corrective actions proposed by his team.
The objective of the Remote Secured OCC is to minimise the physical dependency of staff on site or in the operation control room. With remote working with a secured device, it provides safe working conditions in unsecured environments, for example, triggered by weather (typhoons), traffic (road gridlock), and health (virus outbreaks). It also enables monitoring assets remotely from home or from the working sites (stations, wayside, depots, maintenance centres, etc.). This solution can also serve as a backup control centre, and allow managers to access the operation KPI in real time.
To summarise, the Remote Secured OCC is an innovation that extends the supervision out of the operation and control room to any remote location with the same level of security in order to keep the system running smoothly in all circumstances.
This innovation was made in Hong Kong and won the Hong Kong Business Technology Excellence Awards 2022 in the Information and Communications TechnologyEngineering category. It will be first delivered for the Grand Paris Project in France and is proposed to all our customers.
It is not the first innovation to come out of the Innovation Team of Ground Transportation Systems Team in HongKong. Our team focuses on building digital and data-related prototypes for multiple customers.
It allows access to a broader range of parties to the information like the maintenance team, the station supervisors, or third parties like cleaning services or fire dept. Accessible from mobile devices, for example, smartphones, tablets, and laptops, and the solution is fully secured and tightly controlled.
Remote Secured OCC ensures the constant global awareness of all the concerned teams, wherever they are, and promotes collaboration.
As simple examples:
• The station staff can more easily switch an escalator direction to manage the incoming or outgoing flow of passenger.
• A technician in the depot can access the history of the ventilation system in front of him, and take control of the equipment through the same channel as the operator in the control centre, to diagnose and fix a control issue.
• A manager off-site can access in real-
That team also produced NAIA, the passenger flow analytic solution that provides customerfocused key indicators, like waiting time and crowdedness, to measure the quality of the service offered to the public. This solution is in constant evolution. It started as a retrospective analysis for planning and marketing using an algorithm and now proposes predictions and alerts for operations.
The selling point is that NAIA relies only on data already produced by the existing operating systems—the fare collection and the train schedule—and uses machine learning to augment the value of those data by providing needed indicators.


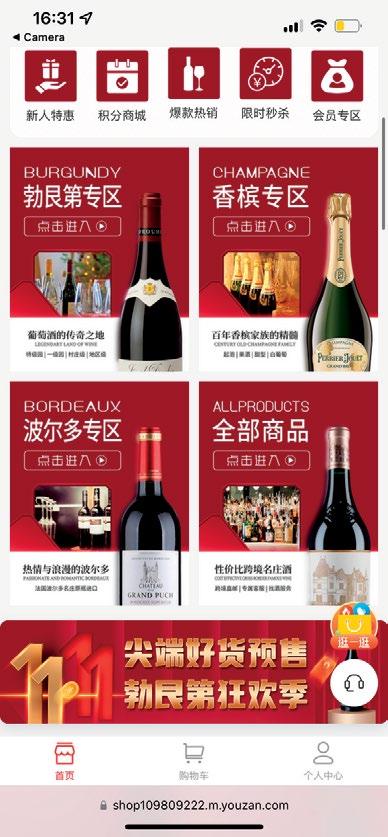
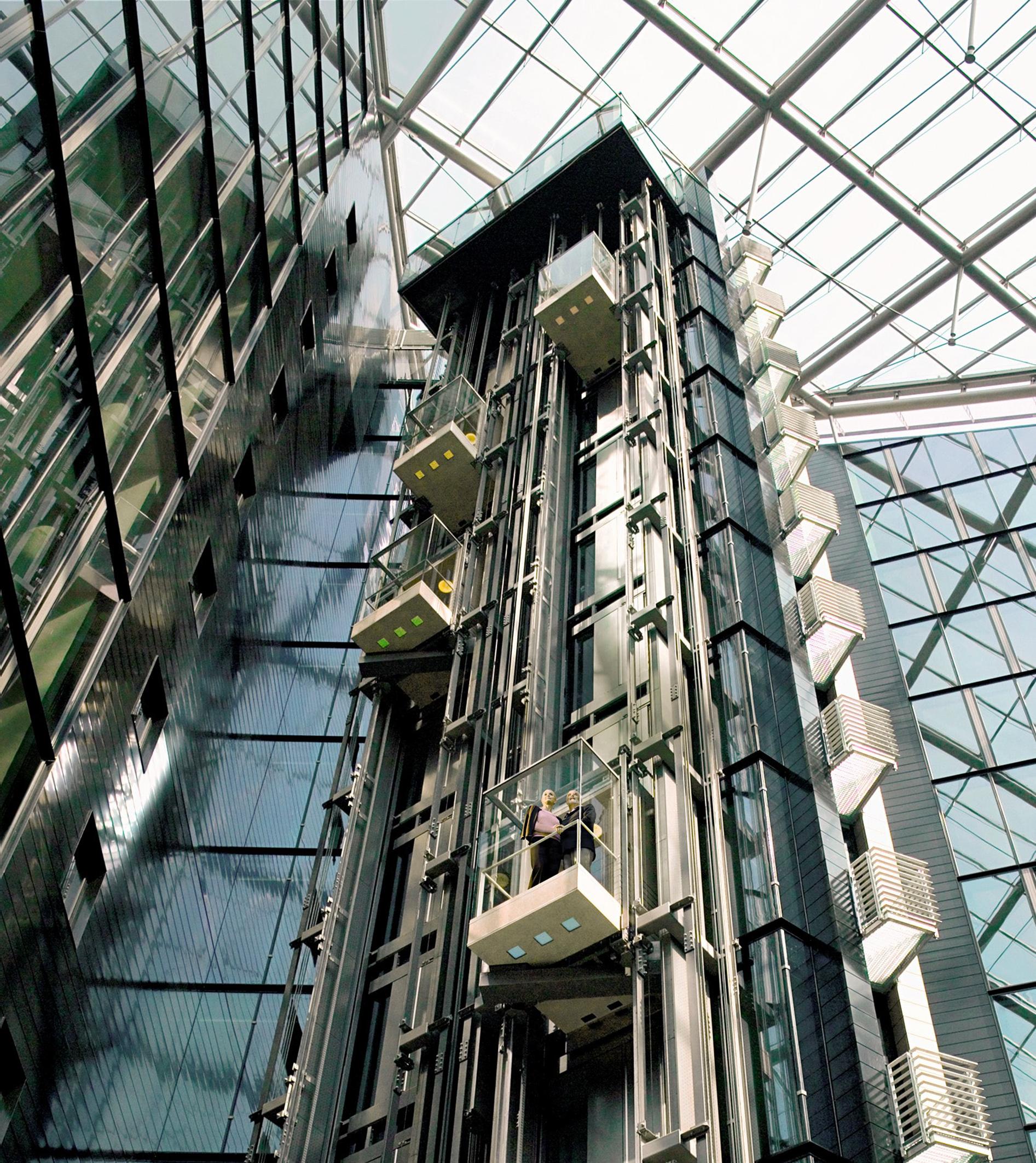
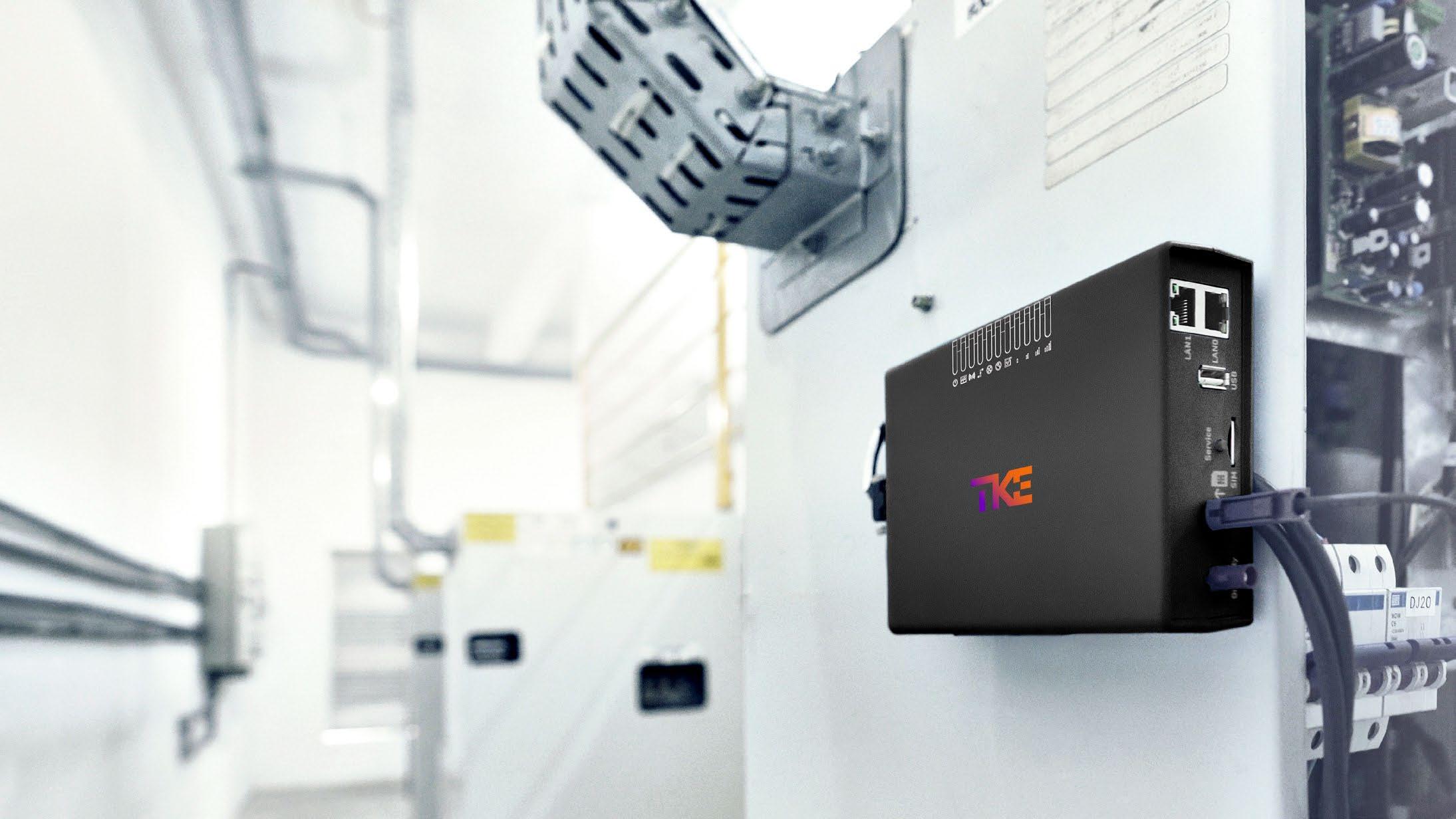
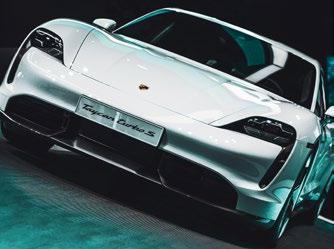
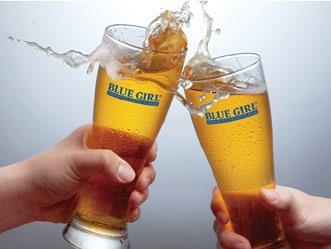
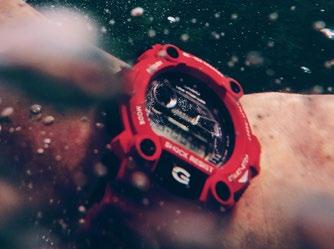
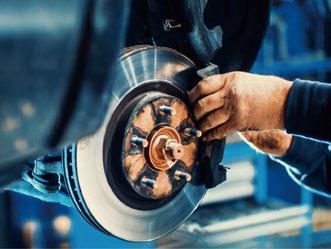

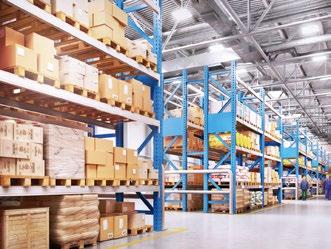
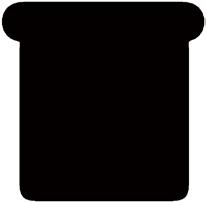