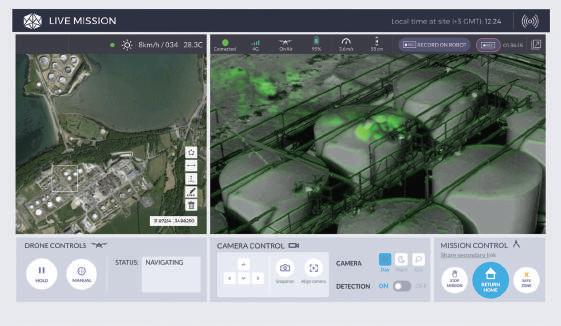
2 minute read
EYES IN THE SKIES
generally done about once every few months, letting any small leaks that arise between inspections go unnoticed.
OGI provides an affordable and accurate way to visualise escaping plumes of gas that would otherwise be invisible. The real magic happens when OGI is combined with autonomous drone inspection solutions.
THE CURRENT WAR in Ukraine has only served to accentuate the growing demand for oil and gas products across the globe. This increasing need, combined with efforts worldwide to reduce methane emissions, is placing more focus on leak detection and repair.
The new game changer in the industry is use of infrared cameras, spectrally filtered to pick up volatile organic compounds (VOCs) by optical gas imaging (OGI). This technology has been transforming the way oil and gas players are detecting leaks and fugitive emissions. But now, using these infrared sensors as the payload for autonomous drones marks a new era in leak detection, making it safer, more frequent, and thoroughly documented. The new technology is here to stay and here’s why.
Whether refinery emissions are seen as a carbon footprint issue or a product loss issue – it’s an issue. And with such large quantities of emissions, optimising emissions inspections has the potential to transform industry. According to the US Environmental Protection Agency (EPA), a typical refinery or chemical plant can emit 600 to 700 tpa of VOCs from leaking equipment, such as valves, connectors, pumps, sampling connections, compressors, pressure-relief devices, and open-ended lines. It is estimated that valves and connectors account for more than 90 per cent of emissions leaking from equipment, with valves being the most significant source.
Out Of The Box
Older inspection options entail an elaborate and often hazardous process that requires specialised staff to take measurements by walking through the equipment. This technique can only conduct spot measurements and cannot pinpoint where the leak is coming from or where the gas is flowing. Further, the complexity and risk of these manual inspections means they are
Percepto’s drone-in-a-box solution augments manual inspections with autonomous on-site inspections, for increased safety and reliability. The data collection and analysis is automated by the Percepto AIM software, which includes a sophisticated cloud backend for AI-powered site inspections, monitoring, surveillance, and visual data collection and management. The inspection data is automatically captured, unified, analysed and visualized to provide actionable insights that are based on high quality information.
Using autonomous drones equipped with OGI cameras and Percepto’s AIM software algorithms for inspections offers several distinct advantages over those done with handheld cameras. There are the obvious benefits, such as more frequent inspections that are unaffected by inclement weather, hazardous physical conditions involving heights, or the lack of an available crew. AIM also solves the challenge of upcoming US regulations by saving leak videos and keeping a historical timeline of emission inspections and leaks. All this translates directly into better productivity and lower costs by minimizing environmental infractions and product loss.
When automated, scanning for large emissions takes less time and can be performed more often, to find leaks before they turn into something more difficult to repair and more dangerous. This makes it much easier to catch the 1 per cent of leaks that account for 99 per cent of emissions. In other words, automating emission inspections with drones means never missing the big leaks—ever.
This article is an edited version of a piece written by Mark Fishburn, director of sales, North America at Percepto. More information on the Percepto system can be found at https:// percepto.co/