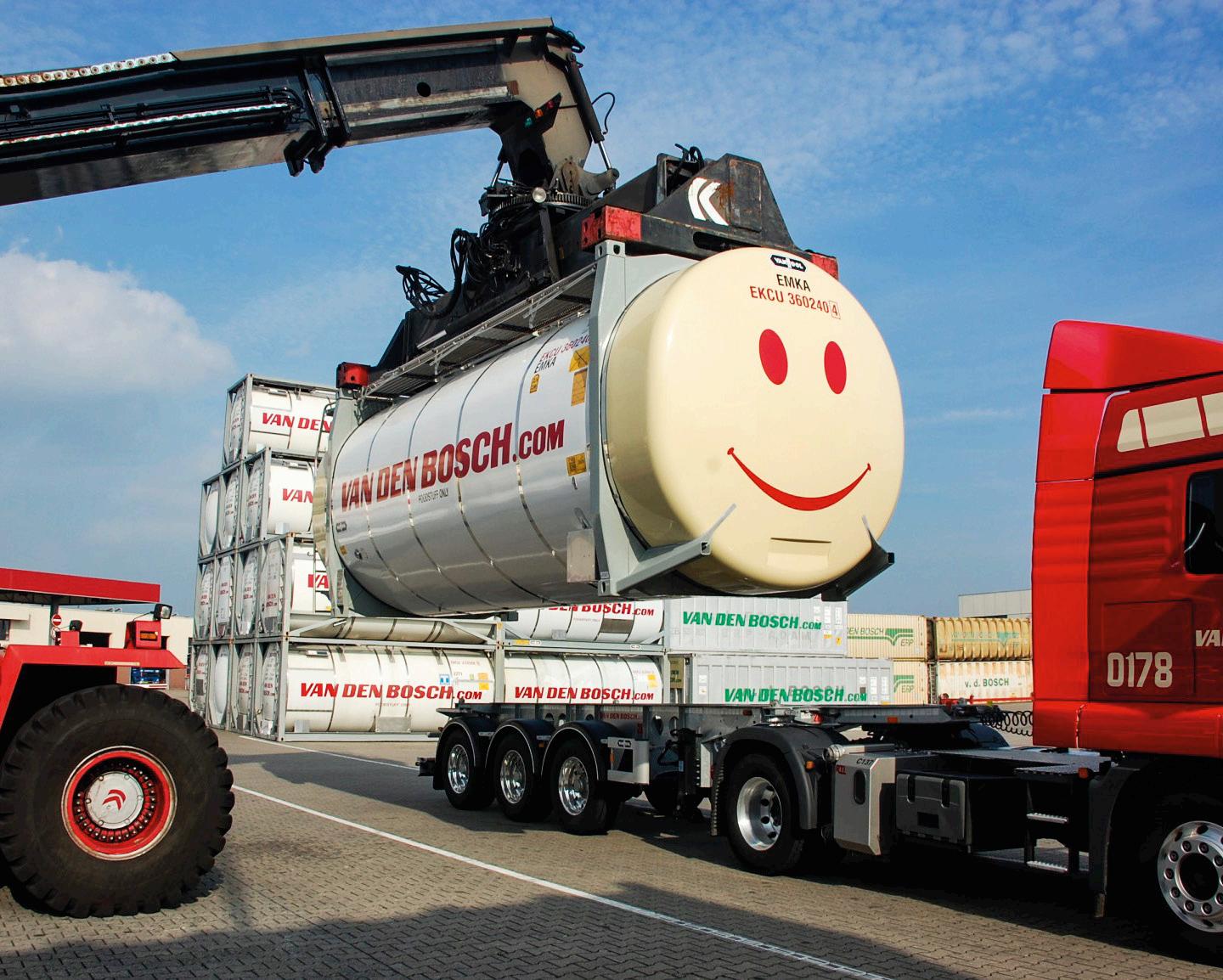
3 minute read
A lighter tank from Van den Bosch
TREAD LIGHTLY
DESIGN • VAN HOOL HAS COME UP WITH A NEW, LIGHTER TANK CONTAINER FOR VAN DEN BOSCH, DESIGNED TO HOLD MORE PRODUCT AND IMPROVE THE SAFETY OF PERSONNEL
VAN DEN BOSCH has begun the introduction of a new design of High Volume Ultra Light tank container, developed in collaboration with manufacturer Van Hool. The first series of 50 new tanks are arriving and are being deployed by Van den Bosch in its foodgrade transport operations
The new tanks have a capacity of 35,500 litres and weigh just 3,180 kg. When transporting products such as sunflower oil, soybean oil, palm oil and coconut oil, which have a relatively low density, this allows them to carry up to 30 tonnes of product. “This results in a maximum payload, savings on logistics costs and fewer transport movements,” says Emiel van Haren, operations director of Van den Bosch’s liquid food division. “The high insulation makes the container also ideal for conditioned transport.”
The design of the new tank builds on a design developed by Van den Bosch and Van Hool in 2014. “Where we took a huge step in the field of payload optimisation back then and developed a ground-controlled mechanism, we’re now going one step further,” says Van Haren.
The new pressurised tank container is equipped with a single point of sealing, connected to the ground control mechanism so that the valve and airline can now be operated at ground level via a tap in the outlet box. Van Haren says: “Developing ground level controlled equipment is a new step to prevent unnecessary working at height and all the associated risks. We also optimise sealability by going from two to just one sealing point on the container.”
VAN DEN BOSCH AND VAN HOOL HAVE BEEN WORKING CONSTANT IMPROVEMENT The latest design is part of a longer continuum. Van Haren says that, ten years ago, 28 tonnes was the standard load capacity. “That was improvable. Together with our partner Van Hool, we developed it up to 30 tonnes. In the meantime we have been continuously looking for ways to make our containers even better. For example, through the development of a single point of sealing and switching to a pressurised container to increase deployability. This also includes a higher insulation value, which helps maintain product temperature and prevents solidification.”
Van den Bosch’s chemical division, meanwhile, has recently undergone its three-yearly audit under the Safety and Quality Assessment for Sustainability (SQAS) programme, achieving a ‘score’ of 94 per cent, compared to 82 per cent in its last audit in 2017. “We are extremely proud of this result, which once again underlines that quality and safety are woven into every part of our organisation,” says Michiel van Kessel, director of staff services.
The auditor was impressed, Van den Bosch says, by the business operations and the outcomes achieved, particularly as SQAS was expanded in 2019 and there were new aspects to be audited. “It is the ultimate proof that quality and safety run like a red thread through our organisation,” van Kessel notes. “I am also impressed by the cooperation between all departments, with this excellent score as the end result.”
“The chemical sector sets high standards for quality and safety in the transport of chemical products. These requirements have been translated into the SQAS standard,” van Kessel continues. “This high score once again underlines that our customers can always trust that their raw materials are transported safely and that the quality is optimal.” www.vandenbosch.com
