
5 minute read
Scanjet’s integrated tank management
DESIGN TO REALITY
TANK MANAGEMENT • NIKLAS FALKMER, MANAGING DIRECTOR OF SCANJET, EXPLAINS HOW SMART SYSTEMS CAN HELP TANKER OWNERS MEET INCREASINGLY COMPLEX REQUIREMENTS
LEGISLATION REQUIRES THAT hazardous cargoes are tracked and monitored at every stage both on land and at sea. In addition to the comprehensive data capture and recording requirements carriers face, stringent new laws and regulations have been introduced in the past ten years aimed at offsetting incidents arising at sea and during loading and unloading. Continuous monitoring is essential to prevent and control leaks and spills and to avoid the build-up of toxic substances in holds and tanks that could affect the quality of the products and could be life-threatening.
Going forward, the pressure is on to deliver smarter, more flexible monitoring solutions to achieve cost-effective ship management. For shipbuilders, scalability and adaptability are vital in meeting changing market demands. For owners and carriers, the synergies among the related products are key to achieving operating economies and maintaining vessel compliance with new regulations as they emerge. The growing move towards ship autonomy, although still some way off, has placed additional emphasis on the digitisation of ship systems
Unique in the market, the Intelligent Tank Management (ITAMA) approach provides direct, real-time monitoring and measurement covering all aspects of tank management to ensure safe operations and control at sea and in port. Central to the ITAMA system is the integration between marine tank management and key aspects of tank maintenance such as tank cleaning machines to improve safety and achieve faster turnaround times.
MADE IN MODULES Quality control was a pre-requisite in bringing the new end-to-end solution to the market. Manufactured in-house by Scanjet to assure product reliability and performance, ITAMA creates advantages for ship owners and operators alike by taking advantages of the synergies between products while achieving 100 per cent compatibility.
Developed to provide reliable operation in harsh marine environments. ITAMA has been designed as a modular platform, bringing together embedded proprietary software, operating system and hardware to create a fully integrated system that delivers information direct to the ship’s automatic systems.
The system supports multiple PC Workstations (master and/or slave). Userfriendly touch-screen system display units show only active tanks ‘in action’ while local indicators and a new handheld ATEX-certified Wireless Tank Monitoring and Alarm Unit provide additional viewing options. ITAMA additionally provides support for ship-to-shore transmissions and remote support via ship’s internet connection.
Adding in flexibility was also an important outcome for this next-generation approach. ITAMA provides the capability to add or remove monitoring points, accommodating a virtually unlimited number and types of instruments. This includes full connectivity and data transfer with third-party products and automation systems. The system has been designed to be future-proof, offering lifetime full reverse compatibility of parts and components – allowing for ease of upgrading to meet new standards and regulations, as well as changing requirements.
MULTI-FACETED CONTROL ITAMA covers a wide scope of operational areas, comprising automatic tank monitoring alarm and control and measurement, fixed and portable tank cleaning, and inert gas systems.
The Scanjet tank measurement technology is based on high frequency non-contact radars or high-accuracy temperature compensated absolute pressure sensors, or both in combination, to measure liquid density measurement online. Temperatures can be monitored at multiple points, with readings used to automatically recalculate the specific gravity of the liquid as a function of the temperature.
Proprietary mathematical algorithms integrated within the system filter out instrument fluctuations and compensate for the effects of tank liquid movement arising from pitch and roll, additionally avoiding false alarms. Temperatures can be measured at multiple points, with readings used to automatically recalculate the Specific Gravity of the liquid as a function of the temperature.
A separate service for non-contact tank calibration ensures accurate tank volume charts. The system thus enables reliable reconciliation between level (ullage) and weight measurements at any trim or list.
Tank level gauging is provided by an electro pneumatic system offering continuous, fast measurement, transmitting data to the relevant systems via with DC 4-20 mA or digital Modbus serial line.
Suitable for permanent submersed operation, ITAMA’s pressure sensors measure absolute pressure. The system control panel features continuous and simultaneous digital readout of each measuring point as well as user-defined visual and audible fixed and user-defined alarms. Continuous corrections of the level readings for the vessel’s trim and list and a transmitter for system atmospheric pressure compensation are included with the system. Serial line communication to other systems is available via RS485, RS422, RS232 and TCP/IP.
Providing additional safety for inland and chemical carriers and offshore supply vessels, Scanjet’s Feen IGS Nitrogen Generator System creates a pure, dry and contamination-free nitrogen gas membrane for the protection of cargo, eliminating the risk of tank explosions during tank cleaning and cargo discharge.
NIKLAS FALKMER (ABOVE): THE PRESSURE IS
ON TO DELIVERY SMARTER, MORE FLEXIBLE
MONITORING SOLUTIONS TO ACHIEVE COST-
EFFECTIVE SHIP MANAGEMENT INTEGRATING OPERATIONS Scanjet has its roots in the supply of tank cleaning equipment and offers fixed and portable tank cleaning equipment to suit a wide variety of installations, with numerous installations for chemical tanker operators including Stolt Tankers, Odfjell and Utkilen. Integrating tank cleaning with cargo tank monitoring optimises cleaning process times and reduces the use of tank cleaning water and boiler fuel. It also provides automated tank cleaning reports. Tank cleaning machines may be equipped with a sensor that connects to the tank radar gauge, which transfers data to the central workstation via a Supply and Communications unit. Providing information in real time, this also eliminating the need for extra cabling.
Designed as a dedicated concept to support all types of vessel and offer maximum flexibility, continuous improvement and development ensures ITAMA is constantly evolving to meet changing market demands and issues as they emerge.
For vessels due for upgrades, integrated solutions like ITAMA offer a fast, economic alternative to replacing individual elements, where issues with compatibility or obsolescence can lead to unexpected extra costs. In most cases, upgrades and refits are done without the need for hot work onboard. For newbuilds also, installing an integrated system eliminates problems from the outset while offering the added benefit of automation and seamless integration. With compatibility assured, and all interfaces accommodated in the system design, there is minimal or no need for specialist engineering input, saving time and money.
Integration has also been shown to minimise lifetime maintenance costs, with single source supply providing a faster response for spares and service support and evidence of compliance with all recognised class requirements – often a condition of contract for oil companies. HCB www.scanjet.se
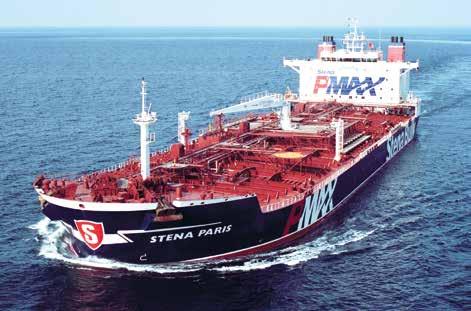
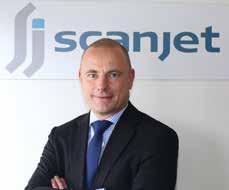
