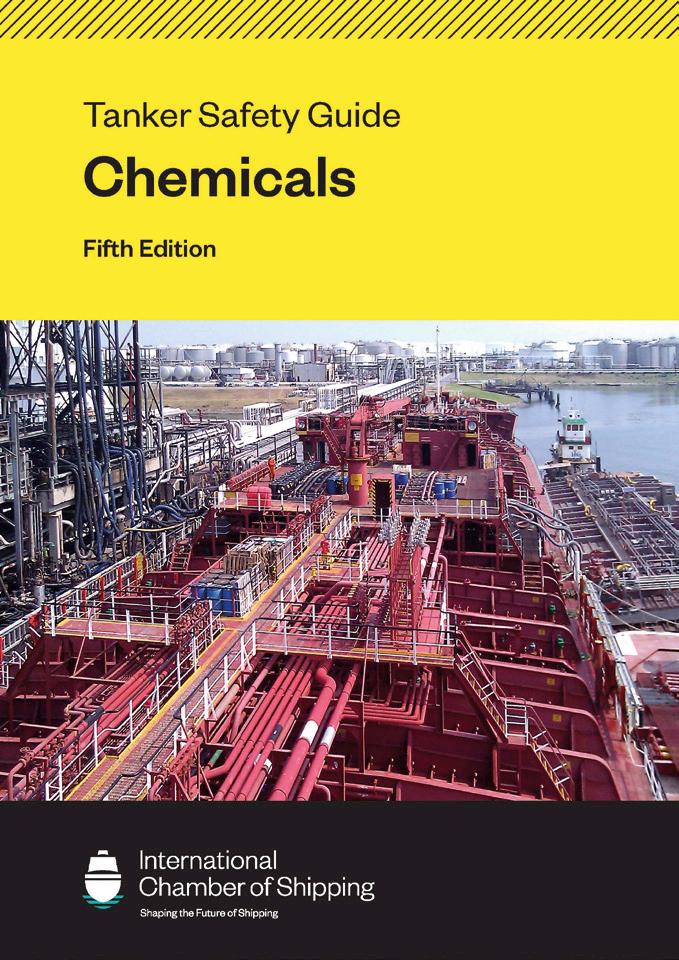
12 minute read
News bulletin – tanker shipping
NEWS BULLETIN
TANKER SHIPPING
SAFETY FOR CHEMICALS
The International Chamber of Shipping (ICS) has published a fifth edition of its Tanker Safety Guide (Chemicals). The new edition provides chemical tanker operators and crew with up-to-date best practice guidance for safe and pollution-free operations on ships regulated under MARPOL Annex II. This includes oil tankers operating in accordance with Annex II when they are carrying chemical cargoes.
“Senior industry experts have contributed their expertise and experience to the technical working group to help shape the new Guide,” says Chris Oliver, nautical director at ICS. “We have worked to simplify this new edition and to make it easier to use – and hence more likely to be used. Techniques learned in the aviation industry have been incorporated to make the checklists more effective and the industry’s greater understanding of human factors means that we can make the messaging more relevant to the user, and consequently more effective. “Sadly, the industry continues to see the same type of incidents time and time again,” Oliver continues. “We have identified these areas and expanded the guidance on key safety issues, including enclosed space entry, risk assessments and PPE. This really is the essential guide for every tanker carrying chemical cargoes.”
The ICS Tanker Safety Guide (Chemicals), which is fully aligned with the latest edition of the International Safety Guide for Oil Tankers and Terminals (ISGOTT), is available from ICS Publications or maritime booksellers. https://publications.ics-shipping.org/
AVANCE GOES FOR GROWTH
Avance Gas has ordered two 91,000-m3 dual-fuel VLGCs from Daewoo SME for delivery in fourth quarter 2022 and first quarter 2023. The contract will, Avance says, enhance its “green profile” and allow it to “take another important step towards decarbonisation while contributing to a greener shipping industry and achieving the targeted 40 per cent reduction in emissions by 2030”.
The two newbuildings will be able to burn LPG as fuel and, with the installation of shaft generators, will not need auxiliary engines, further reducing emissions.
“The outlook for the freight market remains healthy, supported by continued strong US LPG exports and growing Asian demand. The price and terms are attractive and we expect that the vessels will also secure attractive financing in line with their environmentally friendly profile,” the company states.
Meanwhile, Avance Gas Holding has appointed Kristian Sørensen as the new CEO of Avance Gas AS, with effect from 1 April. He moves from Oslo-based shipbroker Fearnleys, where he is currently CEO. “We are very pleased to get Kristian Sørensen on board. With his vast experience from the shipping and LPG markets, he will become a valuable resource to Avance Gas,” says John Fredriksen. www.avancegas.com
VLECS IN ACTION
The very large ethane carrier (VLEC) Seri Everest has successfully undertaken its first loading operation, lifting its maiden cargo of 911,000 bbl of ethane from the Orbit Gulf Coast NGL Exports terminal in Nederland, Texas on 17 January. The cargo will be delivered to Lianyungang in Jiangsu province, China, where Satellite Petrochemical has built a new ethane cracker.
Orbit is a joint venture between Satellite Petrochemical USA and Energy Transfer, which is operating the Nederland facility. Energy Transfer also carried out the first ethane export from the US in March 2016, from its Marcus Hook terminal in Pennsylvania. The Nederland terminal has a 1.2m-bbl ethane storage tank and a refrigeration unit with a capacity of some 180,000 bpd. It is supplied with ethane via a 20-inch pipeline from Energy Transfer’s fractionation unit in Mont Belvieu, Texas.
Seri Everest is owned and operated by MISC, which acquired six 98,000-m3 VLEC newbuildings under construction after an order by Satellite Petrochemical. MISC has now taken delivery of Seri Erlang, the second in the series, from Samsung Heavy Industries. “We look forward to the delivery of the remaining four VLECs as we progress into 2021,” says Yee Yang Chien, president/CEO of MISC. “Commencing the year on strong tailwinds, we remain positive for favourable developments in the industry and more opportunities in Asia, which has now become a vital demand centre for the ethane market.” www.energytransfer.com www.misc.com.my
CARBON-NEUTRAL NAVIGATOR
Navigator Holdings says that its Handysize LPG carrier Navigator Capricorn has conducted the first carbon-neutral voyage after loading an LPG cargo for Sunoco Partners at the Marcus Hook terminal in Pennsylvania for discharge in
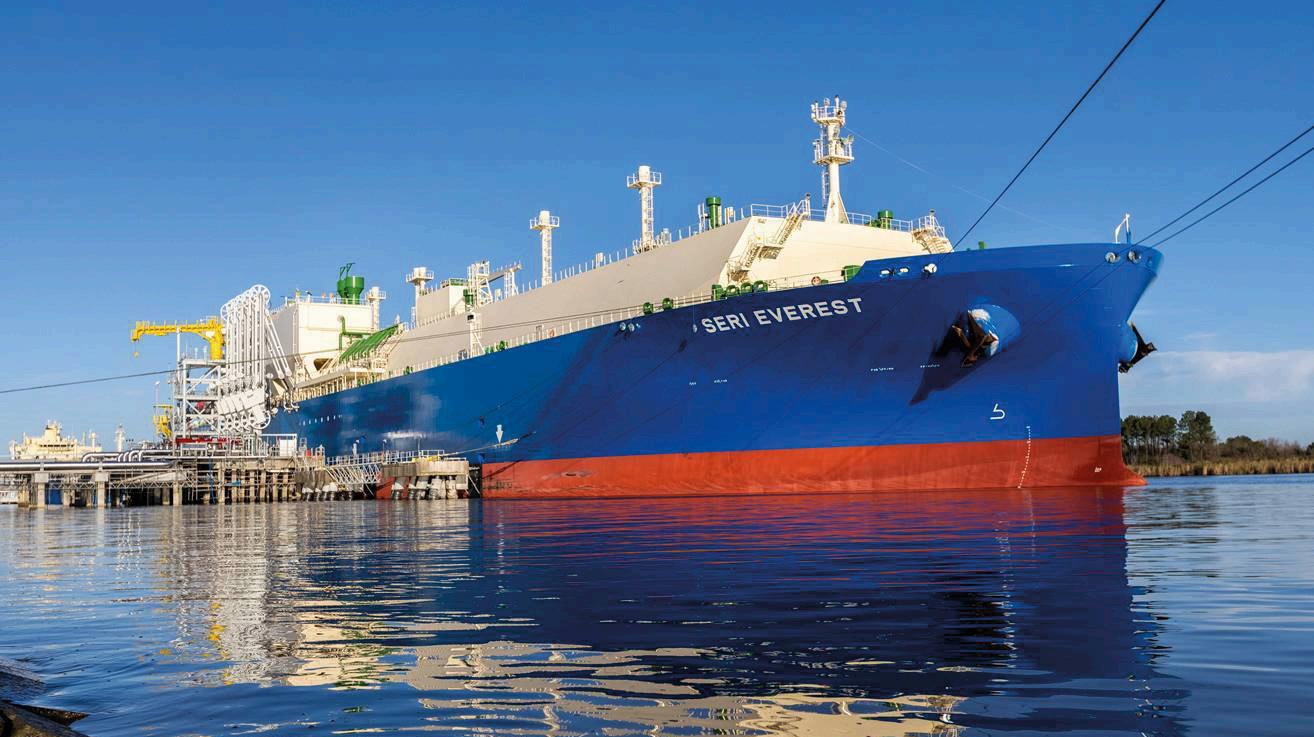
Morocco. In collaboration with the Norwegian climate and technology company CHOOSE, Navigator has committed to offsetting 1,068 tonnes of CO2 by supporting a UN-verified renewable energy project, the IslaSol Island Solar Power project in the Philippines, designed to bring daytime power to some 200,000 homes in the region.
“Carbon reduction is a key strategic objective for our company and follows our mission of connecting the world today, creating a sustainable tomorrow,” says Oeyvind Lindeman, CCO at Navigator. “We continuously strive to reduce our carbon emissions through innovations in the way we manage our company and in the way we operate our assets. Offsetting is one of several tools we choose to use in order to deliver a true carbon-neutral voyage. We are looking at ways to further promote and develop similar voyages in collaboration with our stakeholders, whilst always keeping the UN’s Sustainable Development Goals in mind.”
Navigator is also looking to use similar projects for other carbon offsetting arrangements, while future decarbonisation solutions are being developed. “Navigator is taking the lead in applying new solutions to address the existing carbon footprint associated with seagoing vessels,” notes Andreas Slettvoll, CEO and co-founder of CHOOSE. “Their effort marks a landmark change in the global maritime sector by moving from words to tangible action, and we believe many more will follow their example.” www.navigatorgas.com choose.today
ODFJELL BAGS GREEN MONEY
Odfjell has raised NKr 850 m ($98m) through a sustainability-linked bond, said to be a first in the shipping industry, issued under a newly established sustainability-linked finance framework. The bond is linked to Odfjell’s fleet transition plan, which includes the ambition to reduce the carbon intensity of its controlled fleet by 50 per cent by 2030 compared to 2008. Proceeds from the bond issue will be used to refinance existing bonds and for general corporate purposes.
“With this sustainability-linked bond, we prove our strong commitment to reduce emissions and build a more sustainable shipping industry,” says CEO Kristian Mørch. “Odfjell has for many years worked actively to drive change and reduce our carbon footprint, and we are now pleased to see that investors and banks support us through this sustainability-linked bond.” Odfjell says the unsecured bond issue was “substantially oversubscribed”.
DNB Markets, Nordea and SEB acted as joint lead managers and sustainability structuring advisors in the transaction; a joint statement from them says: “The shipping industry plays a vital role in the green transition. With Odfjell’s clear commitments, decarbonisation strategy and ambitious CO2 emission reduction targets, they show the way as a leading company in the industry. By linking their CO2 emission reduction target with their bond financing terms, they further bolster their commitments and inspire other peers to follow. We are humble and grateful for being selected as facilitators of this hallmark transaction and supporting Odfjell on their sustainability pathway.” www.odfjell.com

ELECTRIC AVENUE
EQUIPMENT • IT HAS BEEN A DIFFICULT YEAR FOR EVERYONE IN THE INDUSTRY. HCB SPOKE TO BIP PEROLO FOR SOME INSIGHTS INTO HOW THE COMPANY HAS MANAGED THE DISRUPTION
THIERRY BOURGIGNON, CEO of tank equipment specialist BIP Perolo, spoke recently to HCB about his experiences over the past year and the changes that have had to be made to operations to continue to prosper during the disruptions caused by the Covid-19 pandemic. He also brought us up to speed with what has been going on since we last spoke to him in October 2020.
HCB: How has business changed during the pandemic? Have you struggled to continue manufacturing, or had to introduce changes into the process?
TB: When Covid struck, it first affected China and there were of course consequences for our Chinese subsidiary in Rudong. However, luckily this coincided with Chinese New Year so during the holiday period our Rudong team could take the necessary measures to develop adequate health and safety protocols.
Afterwards, when the pandemic struck Europe, we had to close our French headquarters for three weeks to implement health and safety procedures and also to source protective equipment such as masks. It was really heart-warming to see all the supportive messages from customers around the world flooding in. We had the new protocol validated by the local French authorities and reopened quickly thanks to tremendous effort by our employees who adapted quickly to the new situation.
Of course, only our production unit was closed during these three weeks, all other office-based jobs were done remotely. Luckily, with all our subsidiaries and agents we already had all the remote tools and organisation in place to make this transition period go smoothly. HCB: How are you keeping in touch with your customers?
TB: We have the big advantage at BIP Perolo, in that we are a global player and have local representatives. Although international travel is limited, our sales managers and distributors still can travel in their respective countries or continents (e.g. Europe) without too much difficulty and as such keep the contact with the customer alive.
Furthermore, we also developed communication on social media such as LinkedIn, Facebook, Instagram and YouTube so that we can get direct customer contact. Obviously all exhibitions, so far, have been cancelled. Sadly, also the Transport Logistic show in Munich has gone and with that our traditional wine tasting, but we are looking into a fun way to replace this, which we will elaborate on soon.
HCB: How are you getting your products out there to the market?
TB: We still use the traditional ways of calling customers and do either a physical or virtual presentation of our products and novelties. Apart from that, we developed a newsletter to keep everybody informed of Perolo
innovations. Furthermore, we mainly use LinkedIn and our YouTube account to have short informative videos of our products showing them in action, or how their testing goes, etc. So the fact that all exhibitions are cancelled made us accelerate our digital communication.
HCB: Indeed, you mentioned last time we spoke that you were using digital communication more. Has that been successful? Have you had to re-think the way you go about your business from the commercial perspective?
TB: Yes, we received a lot of positive feedback on our new website. Also, the posts we do on social media are appreciated by our customers and allow them to interact even more with our company. We also try to publish video footage of valves in action or them being tested so the customer can get an inside look.
We recently launched a ‘Meet the team’ series, portraying Perolo employees from all subsidiaries so that our followers can meet the people behind the brand. We will also start in February/March with maintenance videos of our valve range so that repair facilities can have precise instructions of how to replace certain parts of our valves. Of course, digital communication will never replace physical travel and face-to-face meetings with customers, but it is a nice addition to already existing communication channels.
HCB: Have you had to hire people with new skills, or have you managed to re-train existing personnel to work under this different environment? TB: Covid clearly accelerated the digital transformation of our company. From a general perspective, all teams adopted a digital way of working that is fully customer-orientated.
We recruited new people in our engineering department to accelerate the planned innovations and to bring in new ideas. Other departments when they put in place new procedures always respect a digital methodology nowadays and that is the case for all subsidiaries of our group.
Of course, for the digital communication it is more difficult. After all, we are in a very specific industry that is highly regulated and requires very precise communication. Therefore, we preferred to promote an employee who has been with us for nine years and who knows the products and the customers very well. Of course, this meant offering training in communication but at BIP Perolo we find it very important to have employees grow and to offer them new challenges when possible. We are also working with external partners for some specific subjects as advertising or website architecture, but most of the work is done in-house. This way we ensure a quick and qualified reaction to customer enquiries and needs.
HCB: When you look back at 2020, was it an outright disaster or did you manage to maintain the activity levels of the previous years?
TB: Well, it is a nuanced reply. On the one hand, it cannot be denied that 2020 was a difficult year, especially when we had to shut down the production unit in France. Sadly, we had to put production staff on furlough at the time to have the new health and safety protocol approved.
Next, the tank container market was severely hit by both reduced demand and Covid-19 with a number of new built tanks dropping to an all-time low. On the other hand, 2020 was also a time in which all the investments we made in the previous years with training and innovations and widening our product range finally paid off. We are proud to say that we did not have to let go one single employee in the company and that at the end of 2020 our orderbook was full.
HCB: What is your outlook for 2021? Are you optimistic about the future of the market?
TB: The 2021 orderbook is full and we are currently recruiting new employees in different departments such as engineering, purchasing and production. As we saw in 2020 that all previous investments started to pay off, we are continuing our investment strategy by acquiring new state-of-the-art technology that will streamline our production process. We are also working on several innovations which we will communicate in due time.
Of course, Covid-19 will probably last for some time, but most of the companies that we work with seem to have adapted rather well and are confident in the future. From a global point of view, we can clearly see an ecological trend where tank containers and multimodal transport are getting more and more attention. So for us, the future looks bright. www.perolo.com
THIERRY BOURGIGNON, CEO OF BIP PEROLO, ADMITS
THAT 2020 WAS A DIFFICULT YEAR BUT NOTES THAT
INVESTMENT OVER RECENT YEARS HAS SHOWN ITS
VALUE AND THE COMPANY NOW HAS A FULL
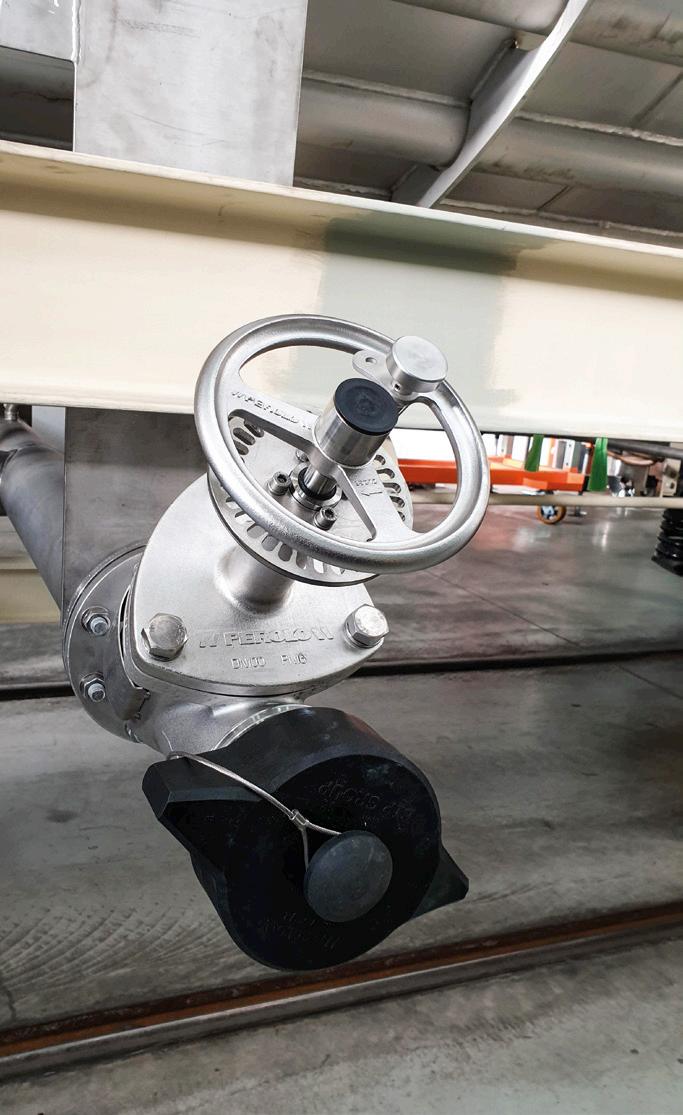