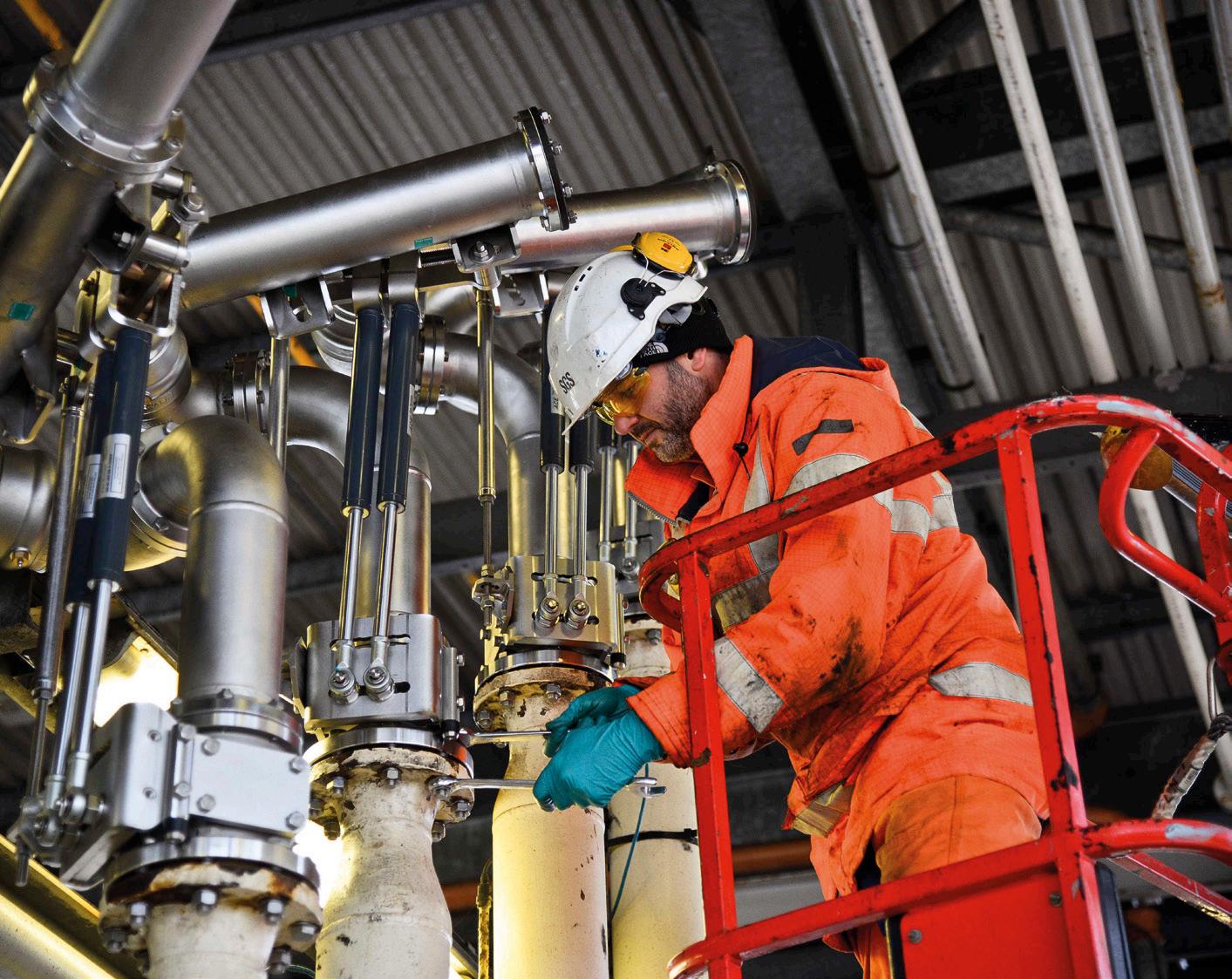
5 minute read
Fort Vale’s Safeload success
LOAD IN SAFETY
EQUIPMENT • FORT VALE’S SAFELOAD COUPLER HAS BECOME AN INDUSTRY STANDARD. TO GET THERE HAS TAKEN HARD WORK, ATTENTION TO DETAIL AND PRIDE IN THE FINISHED PRODUCT
THE DICTIONARY DEFINITION of ‘valve’ is as follows: “a device for controlling the passage of fluid or air through a pipe, duct, etc, especially an automatic device allowing movement in one direction only”. That seems pretty straightforward, doesn’t it? Of course, there’s a lot more to it than that, and especially so in the world of fuel transfer.
Fort Vale was founded in 1967 by Edward S Fort OBE, manufacturing parts for the road tanker industry. The first premises were in Colne, Lancashire and the first product was a 2.5-inch cast iron, three-way valve for tankers supplying heating oil to residential properties. In 1967 Fort Vale sold 150 valves; 50 years later, it sold 150,000.
The chief reason for this growth is the development of the Safeload range of API bottom loading couplers. First developed more than 20 years ago, the market-leading Safeload range is the first choice for many oil majors and the expanding range of Safeload products for the petroleum transfer industry now includes loading arm systems as well as four different types of couplers.
Now in its fourth iteration, the Safeload range embodies the Fort Vale culture of quality, design excellence and safety - it’s solid, it’s dependable, and is a regular but unspectacular fixture on the company sales chart. But for the terminal customers that use them, the Safeload is a prized asset, as Fort Vale’s business development manager Jonathan Parker explains.
“A big part of my professional life (before the pandemic) was attending shows and talking to customers and competitors,” Parker says. “When your customers praise products, it’s always nice, but when your competitors say the same, you know you’ve got something special. I’m fortunate in that I’ve been with Fort Vale a long time and I know the Safeload range inside out. When we began the initial design process all those years ago, the brief was to produce a coupler that would deliver the most secure connection with minimum wear to the truck adaptor, and that would be reliable and very-long lasting within the service conditions of a road-loading terminal.”
TRIED AND TESTED “We understood the rigours of the relentless usage required in the terminal environment,” Parker continues. “The product had to be robust, reliable and have been extensively tested well in excess of industry requirements, to ensure that they would be hard working, long lasting and require low maintenance.
“Thorough testing was of paramount importance. Initially, Fort Vale had intended to mimic an estimated operational working life based on one operation every twenty minutes, over a constant 24-hour day for five years (equalling 131,400 cycles). But in fact, the test continued to 250,000 cycles, which represents ten times the number of cycles called for in BS EN13083. The coupler was connected, opened, pressurised with fluid for a set period of time, closed and then disconnected. A counter was affixed to the coupler to automatically record the number of connections. On completion of the 250,000 cycles, the coupler was found to be leak-free at the MAWP and there was no significant wear or damage to any of the parts.
“It’s one of the main reasons that we are so confident in the product that we are able to offer a three-year guarantee for it - something that none of our competitors are able to do,”
Parker says. “We have unique ‘wraparound’ latches that cover over 60 per cent of the truck adaptor face. This improves the security of connection and reduces wear to the adaptor and the coupler, prolonging the life of both components. Another crucial feature is the materials we use in construction of the unit - the outer housing is hard anodised to BS5599, giving long life and durability, while treated pressure-bearing components enhance mechanical strength, especially at low temperatures.”
These features are replicated across the range, with the ‘Green’ version sporting an integrated cup to capture product loss, the ‘Manual’ with its new shaft and nut assembly that is even easier to maintain, and the ‘High Pressure’ version with strengthened collar to ensure a robust latch engagement.
CLEAN AND SHINY Long praised by many oil industry majors for its reliability and robust construction, the Safeload coupler ensures that there is only a minimal amount of residual fuel in the poppet void space on disconnection and protects against any ingress of foreign debris. The amount of liquid loss on disconnection has proven to be, on average, 75 per cent less than the permitted 5 cc. The range now includes loading arm systems and API bottom loading couplers for semi-automatic, manual, high-pressure and green requirements.
Parker continues: “We now have a range of coupler options to suit a wide variety of operating environments and a complementary range of stainless steel loading arm solutions. The Safeload loading arm has a stainless steel base swivel that eliminates corrosion, and a dual needle/ball race bearing with specialist high-resistance seals that ensure a durable fuel delivery system that gives enhanced performance and requires minimum servicing. All these things are of prime importance when considering terminal usage. Our loading arm features an integral earth system that provides electrical continuity without separate wiring and a safety device to prevent overrotation - with industry standard connections, it can be configured to suit top, bottom, left or right orientation for maximum flexibility - we do try to think of every eventuality!”
BETTER THAN ALL THE REST But it’s not all about fuel transfer - process plant systems have specific demands and Fort Vale can provide special solutions for the food, chemical and pharmaceutical sectors. These include supply access hatches with polished finishes, sight glasses or vents. The company also has an established range of specialised valves for the brewing industry as well as a variety of hygienic valve connections.
Parker concludes: “Fort Vale is synonymous with excellence in engineering and we take pride in being at the cutting edge of technology. We have a state-of-the-art manufacturing facility - having total control over all processes from research and development, design, investment casting, pressing, forging, plasma and laser cutting, to assembly, testing and certification. Multiple in-house test facilities are suitable for the full range of products from impact testing, air and liquid flow tests to high pressure testing for gas valves. This gives us the freedom to explore and experiment, to continue to push the boundaries of engineering knowledge well into the 21st century.
“We have been doing this for over 50 years now and I suppose you could basically sum up our mantra as designing the best valves that we can, refining and improving them using the finest materials, so that our customers can rely on them at all times - whatever the conditions.” www.fortvale.com
FORT VALE’S SAFELOAD API COUPLERS HAVE SET
THE STANDARD FOR THE FUEL TRANSFER INDUSTRY AND
CAN BE ADAPTED TO ALMOST ANY TYPE OF
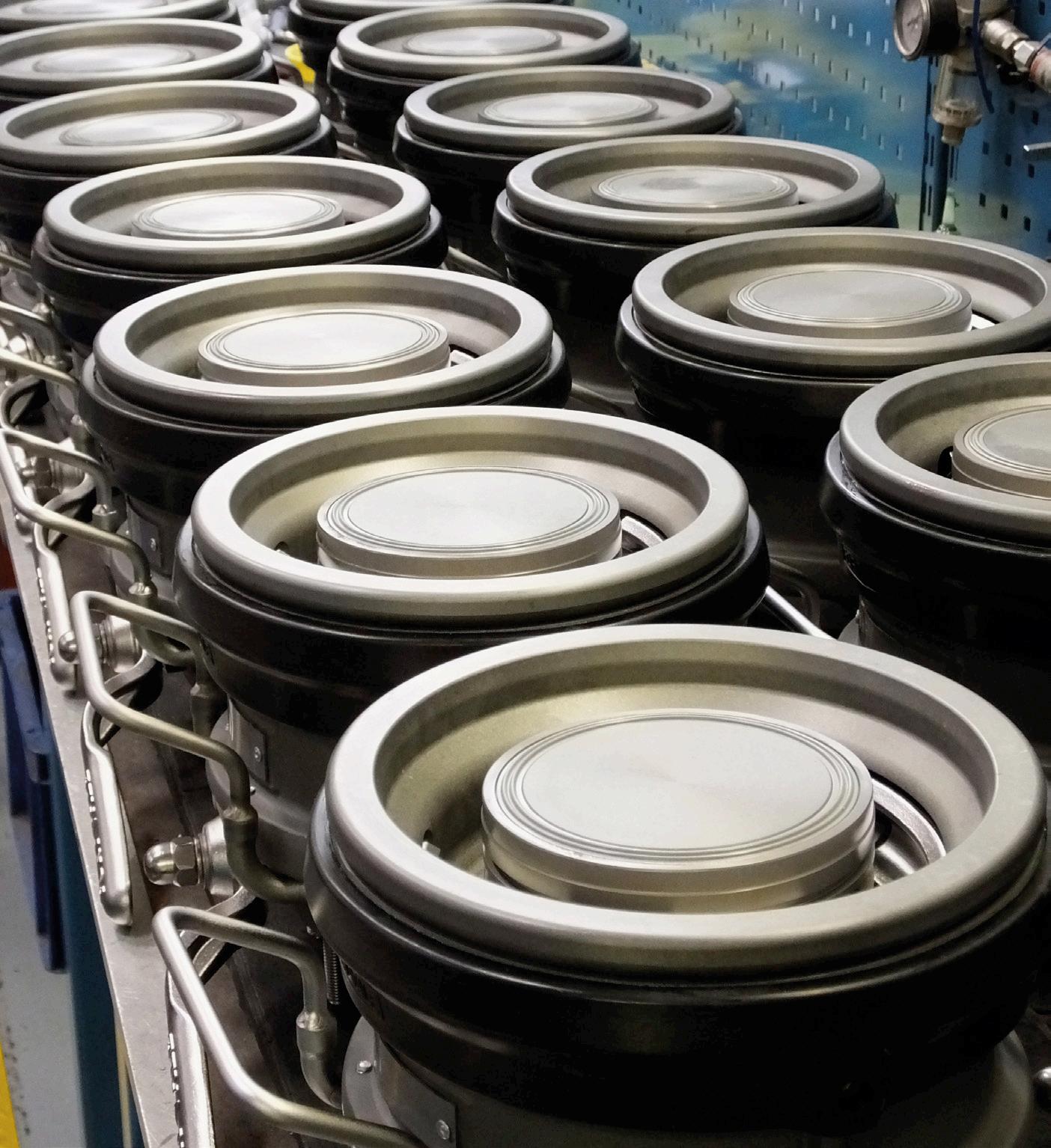