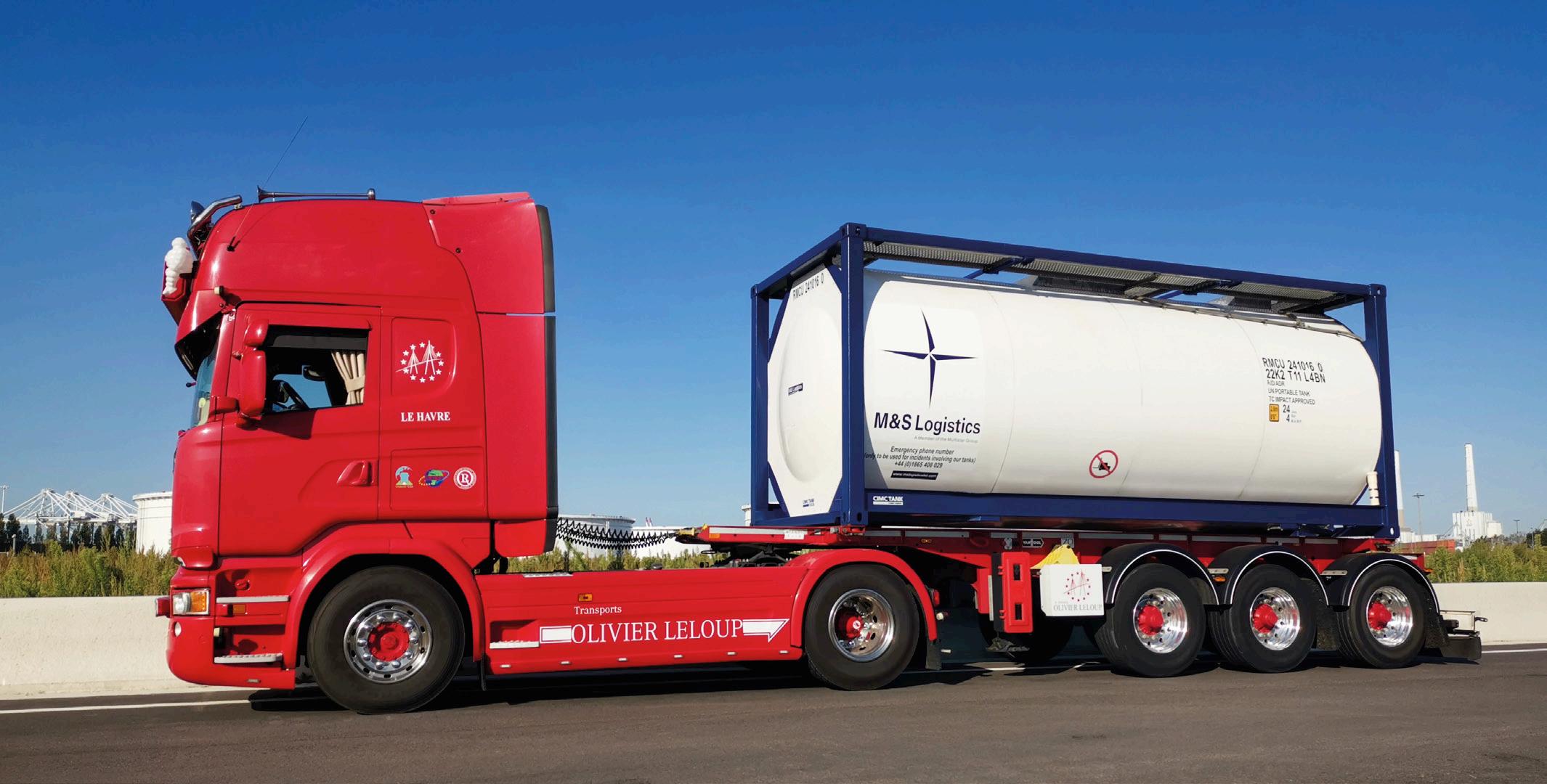
8 minute read
ITCO looks at tank container safety
CUT THE CLAIMS
TANK CONTAINERS • ALL INDUSTRIAL ACTIVITY RAISES RISKS AND DEPOT OPERATIONS ARE NO DIFFERENT. ITCO’S LATEST WEBINAR OFFERED SOME INSIGHTS AS TO HOW THOSE RISKS CAN BE MANAGED
AS THE COVID-19 pandemic shows no sign of easing, representative trade associations around the world continue to leverage the possibilities offered by online meeting apps to keep in touch with their members. The International Tank Container Organisation (ITCO) is no exception and, following the formation of four work groups in 2019, held its third webinar this past 18 November, this time concentrating on safety in the use of tank containers and in depot operations.
ITCO secretary Patrick Hicks welcomed the more than 100 registrants to the event, introducing Mike Yarwood, managing director of loss prevention at TT Club, who put things into perspective, noting that the Club has insurable interests in around half of the global tank container fleet, both owned and leased. Overall, he said, tank containers have a very good safety record, with very few claims.
On the other hand, bodily injury claims can come expensive. While they represent only 2 per cent of claims by tank operators, they are often outside their control, taking place at depots or on the road, or involving third parties. They typically involve people falling from height, being sprayed with product, or being involved in a road traffic accident. Still, TT Club has received only 21 such claims in the ten years to 2020.
Just under half of those claims represent road traffic accidents, and involve drivers or third parties being injured. Other claims show the risks that arise when people fail to follow procedures. Personnel being sprayed with product, for instance, rarely results from equipment failure; rather, such incidents happen when personnel do something they should not have done.
Two other persistent issues are injuries arising from working at height, where Yarwood said there has been no discernable improvement in the accident rate, and confined space entry; although there only a few of the latter incident, they can have significant consequences.
INFORMATION IS VALUE But, Yarwood continued, notified insurance claims give only part of the picture; what is needed is data on near-miss events. He appealed to the industry to provide information so that a clearer picture can be created, which would help to drive safety improvements. He also noted that tank container operators have a duty of care and that they could be liable if a tank is not in good condition and causes an incident, for instance at a depot. Conversely, operators should also ensure they carry
THE TANK CONTAINER SAFETY RECORD IS
out due diligence and check third-party facilities, such as depots, to ensure that their procedures comply with industry best practice.
Yarwood also warned that, in the event of a serious incident, it is vital to get insurers involved early. They need to have evidence and to be able to talk to the people involved, before they forget what happened.
Colin Rubery, ICTO’s technical secretary, asked if it would be useful to have a database of incidents. Yarwood said that knowledge drives the desire for change and, yes, such as database would be a good idea. There were no immediate volunteers to help establish such a database, however.
But there are some useful resources already available. Yarwood mentioned two of ITCO’s Technical Guidance documents on working at height (TG04) and safe tank entry (TG05); TT Club also has guidance on working in confined spaces. These are “valuable resources”, Yarwood said, summing up with some questions that tank operators need to bear in mind.
Firstly, can working at height be avoided? If not, how can it be made safer? A ‘permit to work’ system can help, especially in confined space operations – and remember that 60 per cent of fatalities in confined space incidents are would-be rescuers. During depot operations, are all the necessary pieces of equipment – ladders, breathing apparatus, etc – and personal protective equipment available? Are they fit for purpose and well maintained? Have personnel been trained in their use?
Indeed, training is vital across the board. All personnel need to be confident and competent to do their jobs. Rescue drills, especially for working at height and confined space entry activities, are also vital, as a fast response is important. VIEW FROM THE DEPOT A valuable perspective on safety in tank depots was provided by Faris Al-Shali, HSE manager for Kanoo Tank Services (Sahreej), a joint venture between YBA Kanoo and Stolt Tank Containers that operates three depots in Saudi Arabia. He has a big job on his hands, he said, to keep on top of safety procedures, and to maintain Sahreej’s ISO 45001, 14001 and 9001 certifications, as well as the provisions of ‘Gulf SQAS’, the regional version of the Safety and Quality Assessment for Sustainability audit scheme.
Al-Shali agreed that working at height is a major issue. Sahreej employs a number of different controls, including full control harnesses for its personnel and easy access to tank tops via a platform. Its workers are also issued with shoes without laces, to reduce the trip hazard, and chemicalresistant, non-slip boots.
During tank entry procedures, two people are always present: one to enter the tank and one to keep watch; both have harnesses. During tank heating, personnel do not need to spend much time on the tank, Al-Shali said, but they nonetheless are provided with a platform and harness. Sahreej facilities are also equipped with tank rotators to avoid the need for working at height during tank repair operations.
Importantly, employees must not only be physically fit but also mentally fit – it is no use expecting someone who is afraid of heights to work on top of a tank, Al-Shali said. In addition, Sahreej has a behaviourbased safety (BBS) training programme. It has also put in place a training programme that covers emergency drills, to help its workforce get used to the idea of using breathing apparatus while working at height or entering tanks – and, quite importantly, how to get in and out of a manhole while wearing such apparatus.
Continuous training aims to address unsafe behaviour during working at height, Al-Shali continues. This also gives employees the opportunity to raise problems and suggest improvements to work practices. New employees are not allowed to work at height until they have completed this
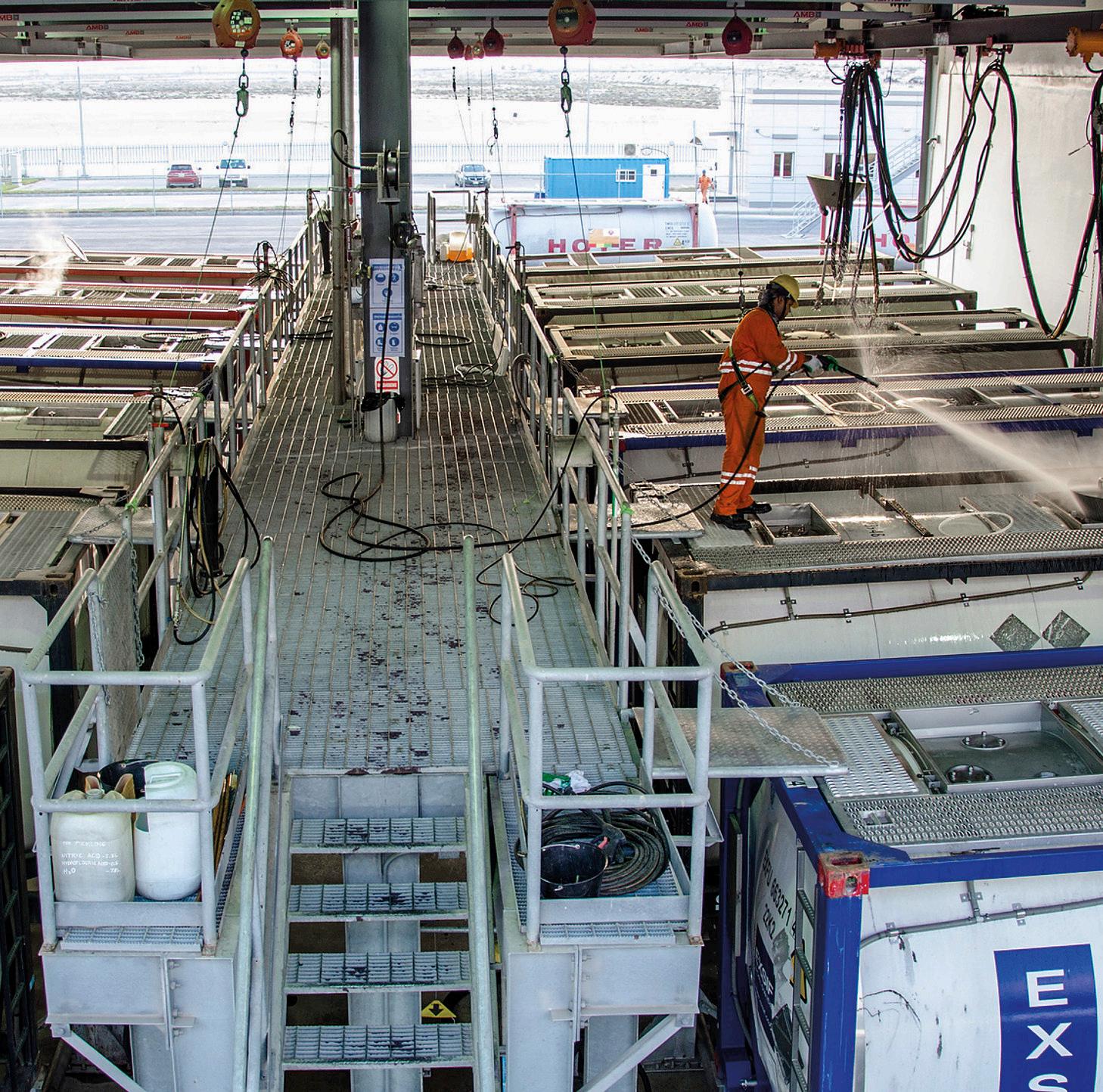
training. It is also important to remember that the trainers themselves need to be trained, and Sahreej has a programme of out-of-house train-the-trainer courses in place.
Al-Shali is often seen out and about in the company’s depots: he said it is important to observe employees in action to ensure they are complying with the established procedures. One-to-one training is offered to those who need remedial action.
“Has this programme made Sahreej more efficient?” Al-Shali asked. Management can see that its employees respond well to in-house training and, though there is a cost, it is seen as worthwhile. “We don’t take safety lightly,” he said. But tank container operators have their part to play: provide a safe tank and don’t rush the process, he urged.
THE OPERATOR’S EYE Responding to that call was James Rawlinson of M&S Logistics, who noted that cleaning stations operate daily with a certain element of risk. Tank container operators expect those risks to be managed. In general, he said, most cleaning stations have good health and safety standards in place and these standards have improved immensely over the years. Unsafe practices have largely become obsolete. It is now not unreasonable to assume that cleaning stations are operating safely – but operators cannot afford to be complacent. Tank depots vary widely in design and also in terms of their standards.
The design of the best cleaning stations is based on what has been learned from mistakes made in the past, Rawlinson said. Good facilities generally have a safety manager, a quality manager and ISO and/or SQAS accreditation.
There are, though, still some parts of the world where it is impossible to find cleaning stations that meet the standards expected, Rawlinson continued. This places the operator at risk and creates a liability. Operators need to proactively manage their use of cleaning stations and balance the need for cleaning with the risk involved. If nothing of a good standard is available, then the operator must be able to demonstrate that a full risk assessment and risk mitigation has been carried out if the liability is also to be mitigated.
Echoing Al-Shali’s closing words, Rawlinson noted that good, clear communication between the tank operator and the depot is vital. Full information, including a current and accurate safety data sheet (SDS) must be provided in advance. Responsible operators do this, and establish an open communication chain with the depot.
Operators also need to be aware that all cleaning stations have restrictions on what they can handle and, again, this information needs to be available to the tank operator. Thankfully, Rawlinson said, wilful misdeclaration of a tank’s last load to get around such restrictions is very rare.
Having established the liability that tank container operators have when it comes to depot operations, Rawlinson had this to ask: How can the operator check? All operators should carry out regular audits, he advised. Is the handling equipment – forklifts, cranes, etc – appropriate to the work to be done and in good condition? Such equipment should be inspected annually by a verification body, he noted. Operators should check and review SQAS audit reports but, Rawlinson added, be aware that these take a fairly narrow approach and may not cover all the elements relevant to each operator.
Rawlinson considered that ISO 9001 represents a good foundation but that ISO 45001 provides a better indication of a depot’s safety management procedures. The tank operator may still, though, need to carry out its own audit in order to fulfil its own risk management processes.
Bringing proceedings to a close, ITCO president Reg Lee reported that more than 4,000 tank container e-learning courses have now been delivered. ITCO members are, he said, taking the opportunity provided by Covid-19 restrictions to get their people trained remotely. Finally, wishing attendees a ‘Happy New Year’, he noted that the fourth ITCO webinar, focusing on efficiency, will be held in January; more details can be found on the ITCO website, www.itco.org.
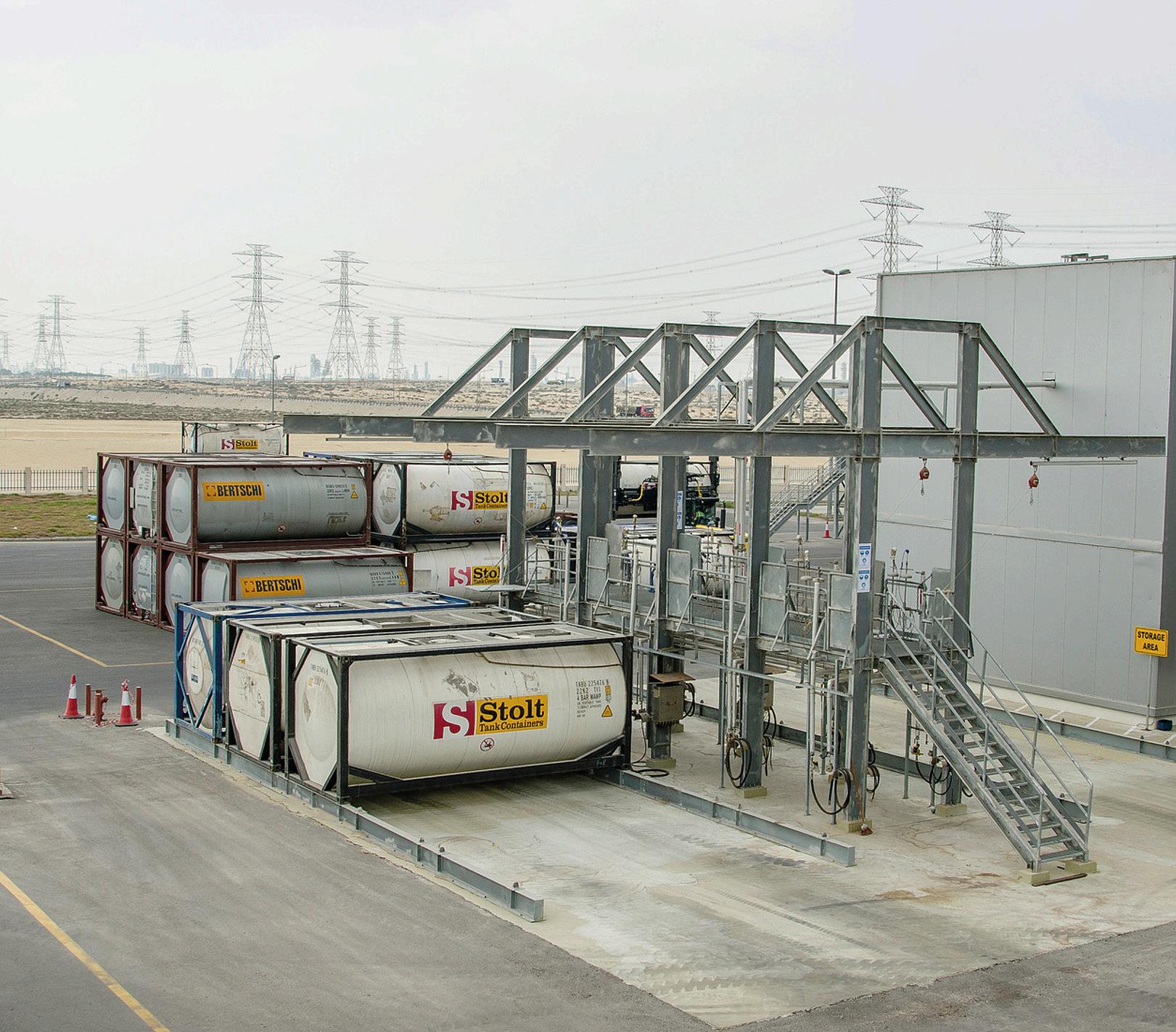