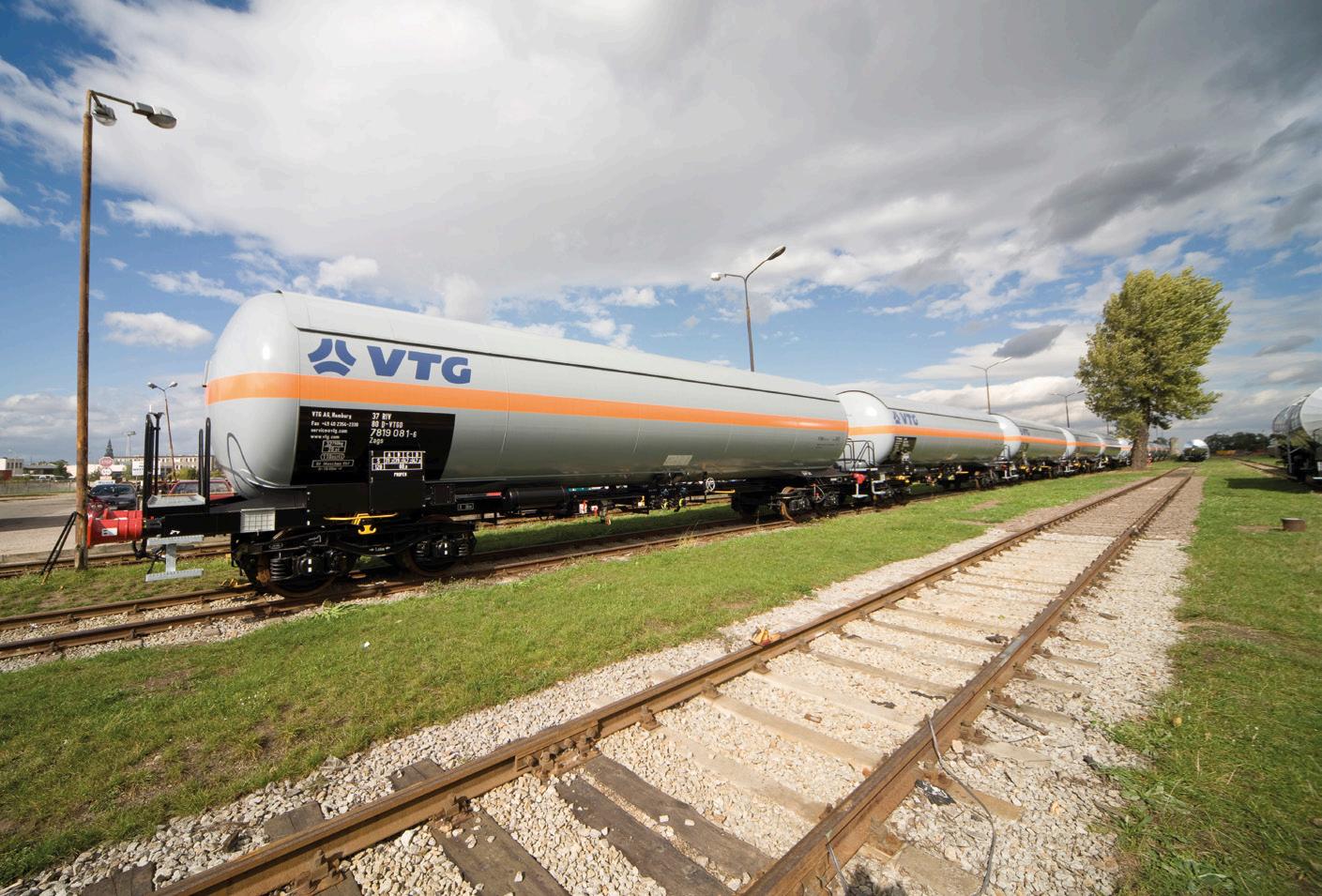
3 minute read
Cefic’s guidance on butadiene transfer
IN AND OUT CLUB
PRODUCT TRANSFER • BUTADIENE MUST BE HANDLED WITH CARE. CEFIC HAS BEEN LOOKING AT REDUCING THE RISK OF EXPOSURE DURING THE LOADING AND UNLOADING OF TANK CARS
BUTADIENE IS A starting point for a number of value chains, not least synthetic rubbers, and as such is produced and transported in large volumes. Data from the European Chemical Industry Council (Cefic) put crude C4 output from steam crackers in the EU-15 countries at some 6.4m tonnes in 2015, with production of 1,3-butadiene put at 1.9m tonnes. Of that, around one quarter of the butadiene output – 0.5m tonnes – was transported by rail.
Butadiene is considered to be carcinogenic, mutagenic and a persistent bio-accumulating toxic product. As such, the European Commission included butadiene – not just pure 1,3-butadiene but any stream containing more than 0.1 per cent by volume – in the revised Carcinogenic and Mutagenic Directive (CMD). This placed a community-wide occupational exposure limit (OEL) of 1 ppm, although some countries are more restrictive – Sweden, for instance, has an OEL of 0.5 ppm.
In the production process, butadiene is handled in closed systems to limit the risk of exposure to workers. However, operators can be directly exposed to butadiene when connecting or disconnecting rail tank cars. Cefic’s Lower Olefins Sector Group (LOSG) has been looking at the risks and, in a guidance document issued this past September, lays out some recommendations on the best types of couplings to be used during product transfer.
WHAT ARE THE OPTIONS Cefic notes that there are three types of coupling used in Europe on tank cars for butadiene. In France and Belgium, screwtype couplings (Weco-ACME) are common, whereas further east flange couplings (DN80/DN50) are typically used.
Cefic says both these couplings have inherent issues that can lead to an operator being exposed to butadiene. Flanges are a good solution if they are permanently attached but they are often installed and removed. Furthermore, they are cumbersome to handle and time-consuming to use, with each loading or unloading operation requiring up to 72 screw connections. Moreover, errors can be made in terms of bolt tension, worn gaskets and missing bolts. Such errors can result in the leakage of product and the exposure of workers to butadiene vapours. LOGS says it recommends that flange connections should not be used. Its members have committed to phase them out by the end of 2025.
Weco couplings avoid the need for bolts and connection is a simple task; in the event of leakage, it is often sufficient to tighten the coupling by screwing it in a little more. On the downside, a special wrench is required, which may not always be available. Further, there are two different types of screw connector on the market, so sometimes there is an incompatibility. The dead space between the shut-off valve and the valve on the loading arms is larger than with the flange system, so in the event of a leak more material will be released. While appropriate measures can be used to overcome these disadvantages, in the real world mistakes can be made.
A third option is to use dry-disconnect couplings; these are more expensive but are simpler and faster to use, freeing up operators for other tasks and increasing throughput at the loading station.
Cefic’s guidance advises that Weco and dry-disconnect couplings both offer advantages over flange couplings. Whichever is chosen, Cefic also recommends the use of a breakaway coupling on the loading arm.
LOSG members plan to evaluate the benefits of eliminating flanges in butadiene transport before extending the guideline to cover other C3 and C4 olefinic streams; that will also give the opportunity to take into consideration current technological developments in product transfer operations.
AS WITH MANY OTHER PRODUCTS, IT IS DURING
TRANSFER OPERATIONS THAT THE RISKS OF