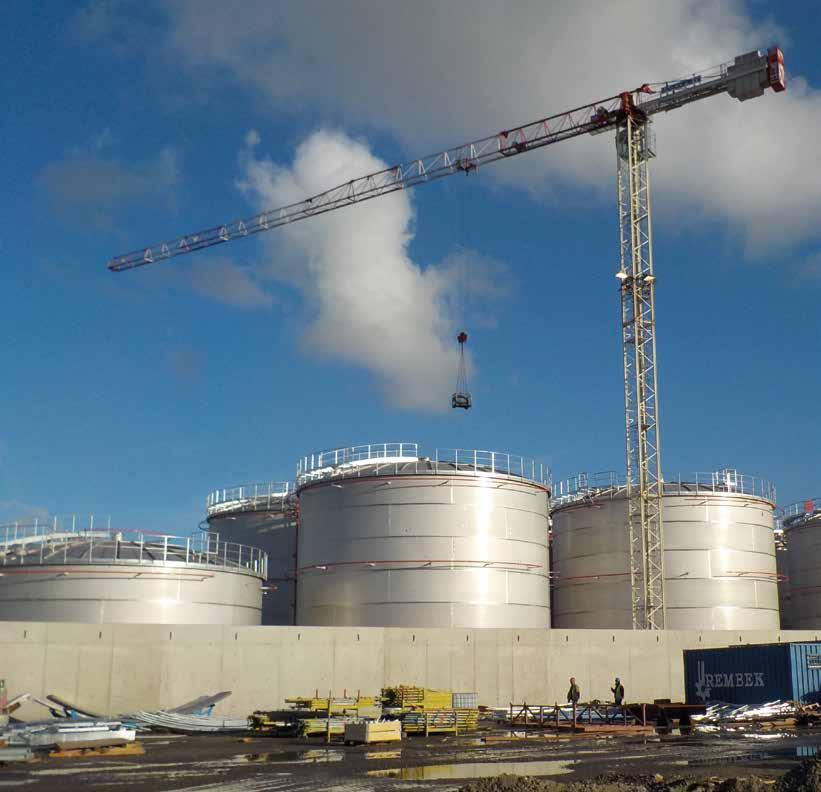
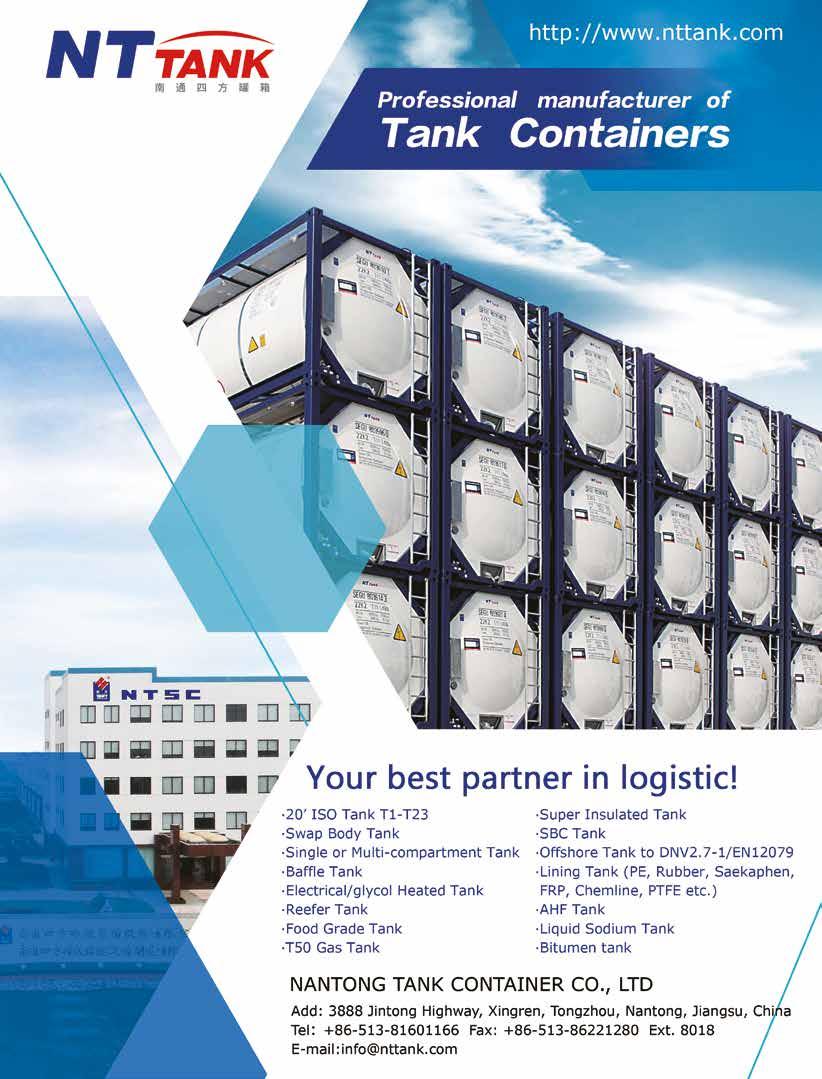
We are reminded often that the Stone Age didn’t end because humans ran out of stones, and the Oil Age won’t end because we run out of oil. Instead, many governments are pressing industry and consumers to move away from hydrocarbonbased fuel sources and switch instead to cleaner fuels.
They tell us, in fact, that within 20 years, gasoline- and diesel-powered cars will no longer be manufactured and that in perhaps 40 years there will be few left on the roads. I’m unlikely to be here to see it, but it’s clear that within a couple of generations the young will be baffled as to why we ever felt it necessary to use dirty fuels – or even to own our own cars.
The process towards a decarbonised future is likely to be gradual. Look at marine fuels, for instance. There has been an awful lot of fuss about the new IMO restrictions on sulphur levels in bunker fuels, which come into effect in 2020. There has been an increasing rush to fit new ships with engines capable of running on LNG, as there is plenty of that about at a relatively attractive price and it avoids all the sulphur (and other emissions) concerns.
But that is only one step. LNG is still a hydrocarbon – the simplest hydrocarbon of all. Ultimately the shipping industry will have to move past that and into non-carbon fuels, which probably points to hydrogen power.
It will be the same on the roads. Certainly in Europe the move towards electric-powered vehicles (including heavy goods vehicles) is well under way. Practical concerns about cost, performance, charging time and range are being overcome, and in some countries the electricity that fuels vehicles is heavily subsidised.
But that electricity has to come from somewhere, and at the moment a lot of it is generated from hydrocarbon sources. The switch to electric vehicles merely moves the emissions problem back up the fuel supply chain. It might be easier to manage emissions control at the power plant but the endto-end calculation has to take into account efficiency losses along the way.
Maybe at some time in the future alternative power sources – solar, wind, geothermal, etc – will be able to generate all the power we need. I have heard one futurologist point out that the increasing efficiency and falling cost of solar panels will mean that electricity will one day be essentially free.
But all this is still some way off. So far off, in fact, that companies that are involved in the movement, storage and handling of oil- and gas-based fuels and other liquids are still investing heavily in new assets. Our annual review of bulk liquids storage terminal construction in this issue, for instance, takes up just as many pages as ever and a further article on recent M&A activity indicates that there is still a huge appetite for opportunities in the sector among institutional investors.
It looks likely that there will be demand for this new tank capacity, at least in the medium term. But it is also certain that there will be changes in the products being handled. Refiners are already grappling with that and terminal operators will need to be ready to engineer into their assets the flexibility that will be needed as the world gradually weans itself off hydrocarbons.
Peter MackayCargo Media Ltd
Marlborough House 298 Regents Park Road, London N3 2SZ www.hcblive.com
Peter Mackay Email: peter.mackay@hcblive.com Tel: +44 (0) 7769 685 085
Sam Hearne
Email: sam.hearne@hcblive.com Tel: +44 (0) 208 371 4041
Samuel Ford
Email: samuel.ford@hcblive.com Tel: +44 (0)20 8371 4035
Ben Newall
Email: ben.newall@hcblive.com Tel: +44 (0) 208 371 4036
Craig Vine Email: Craig.Vine@hcblive.com Tel: +44 (0) 20 8371 4014
Stephen Mitchell
Email: stephen.mitchell@hcblive.com Tel: +44 (0) 20 8371 4045
Brian Dixon
Designer
Natalie Clay
HCB Monthly is published by Cargo Media Ltd. While the information and articles in HCB are published in good faith and every effort is made to check accuracy, readers should verify facts and statements directly with official sources before acting upon them, as the publisher can accept no responsibility in this respect.
2059-5735
VOLUME 39 • NUMBER 06
Letter from the Editor 01
30 Years Ago 04
View from the Porch Swing 06
Learning by Training 07
If you build it… Global terminal expansion survey 09
Value added
M&A deals show value of terminals 23
Little Rock and roll
Building a distribution hub in Arkansas 26
The key to success
Sofis helps with partial automation 28
Up the wall
Eddyfi improves NDT technology 29
Foam on tap SK firms automating foam making 30
You’re so vane
Sliding vane pumps a good fit for terminals 32
News bulletin – storage terminals 34
Fixture for fittings
Reporting back from FPS Expo 37
The vault is locked
BDP signs up for blockchain 41
Shipa to shipper
Agility moves into online logistics 42
Dutch barns
Broekman invests in warehousing 44 Alpha tanks
Thielmann designs tanks for Class 7 46
Pay it forward
Hoyer’s investments get results 47 News bulletin – tanks & logistics 48
Nice in Nice
Fecc meeting has a lot to deal with 50
The gong show CBA recognises quality 52
Brenntag invests around the world 54
Top table
New deals for Nexeo 55
To Russia with rubber
Safic-Alcan makes strategic move 56
Going for an Indian
Azelis expands in Asia 57
News bulletin – chemical distribution 58
Training courses 60 Conference diary 63
SAFETY Incident Log 64 Outside the box
New packagings for battery shipments 67
Silver safety
Changes ahead as SQAS passes 25 years 70
Pass the port
Exis moves forward with restrictions database 72
Block the blast
Welcome to CellBlock EX 73 News bulletin – safety 74
Crunch time
RID/ADR/ADN 2019 on their way 76
Testing, testing
Handling the 38.3 test report 82
Get the show on the road
Labeline Biennial Roadshow is on its way 84 News bulletin – regulations 86
Not otherwise specified 88
The HCB Tank Guide 2018/2019 –free to all subscribers
Thirty years ago the world was still trying to get to grips with the relatively new-fangled idea of intermediate bulk containers (IBCs). Indeed, a strap line on our cover seemed to be trying to reassure industry that such containers were “up to the task”.
But if potential users still needed convincing, the regulators were even further behind. As one feature in the June 1988 issue began: “The much-heralded UN recommendations on IBCs should have meant a speedy adoption of harmonised requirements at national and international level for all modes of transport. That was the theory…”
The UN experts had adopted in the fourth revised edition of the UN Model Regulations a new Chapter 16 that laid out for the first time a consistent set of recommendations, which was designed to get around the need for the lengthy case-by-case approvals process for international movements of IBCs containing dangerous goods.
However, as we said at the time, both IMO’s Carriage of Dangerous Goods Sub-committee and the RID/ADR experts had shown “an indifference verging on reluctance” to incorporate those recommendations into their respective regulations, “effectively denying chemical shippers the use of IBCs as a practical, costeffective distribution option”.
As it happened, the March 1988 meeting of the RID/ADR experts had done some more work on the topic and were prepared to begin adopting the provisions, but with a number of significant revisions compared to those in the UN Model Regulations. At the time – and not for the last time – we pondered on how such a state of affairs could come to be, seeing as most of the RID/ADR experts were among those who had drawn up the original provisions at UN level.
Despite that, we also reported that the previous 12 months had seen IBC manufacturers generally enjoying a healthy level of turnover and, with growing demand, investing in product innovation: “Most manufacturers, having examined the UN recommendations, are already making the necessary design and production changes to enable containers to be produced according to the UN criteria.”
Indeed, so intense was the level of innovation that our June 1988 survey only had room to cover developments in metal and flexible IBCs; we had to run a separate article later in the year to look at composite and all-plastics IBCs.
The situation was somewhat different in North America, where around 16 suppliers of rigid IBCs in the US and Canada had been providing units for more than 30 years. An article by Vince Vitollo noted that the safety record of IBCs in hazardous materials service had been “very good” and that, while the US Hazardous Materials Regulations had long provided construction and testing specifications, the use of polyethylene IBCs for the carriage of corrosives was gaining traction under an exemption provided by DOT.
The growth in the use of metal and plastics IBCs in North America was prompted not by the desire to maximise the capacity of shipping containers, as was the case elsewhere, but primarily by concerns over the disposal of non-bulk packagings. Chemical shippers were increasingly turning to IBCs in an effort to bring greater control over the distribution process and avoid problems associated with the disposal of used packagings. They were, perhaps, rather ahead of the rest of the world when it came to such issues.
The older of my two baby sisters loved two things (at least). She loved having her own room, which she kept private in her absence by adding a padlock to it. And she loved records, those old, flat, black circles of vinyl with spiral grooves that could play prerecorded music. One memorable afternoon after school, this sister became enraged at the rest of her siblings and took revenge. She turned the volume on her record-player up to 11, plopped one small record on it, moved the arm to the side, engaged the needle, and padlocked the door to her room.
The same song began to play throughout the house over and over and over again. My parents weren’t home from work, my sister had gone off to some sort of practice or meeting, and the weather was so lousy there wasn’t any place to go outside. Even in my own room with its door closed and a pillow over my head I could hear that damn song.
I know, it’s forty years later, and I should let it go. I assure you, I am still in the middle of the process of doing just that.
And now, I get to do it to you. At the risk of sounding like a broken record, almost exactly two years ago I wrote this: “A decade or so ago, I remarked to a former head of the UN Committee of Experts on the Transport of Dangerous Goods that I thought the Committee must be a very exciting place to be. He told me that the DG regulations were mature, and that only tweaking remained, which I took to mean that he thought the excitement was over and that only minor stewardship work remained.”
Yesterday, at a meeting of a notable DG organization, a regulator described this view to the room as “fine-tuning of a longstanding system”, although I’m not sure the second regulator necessarily agreed that it was an accurate assessment. Lots of our current system, especially the hazard communication basics are mature and only need fine-tuning, but lots needs major work, especially classification and packaging of articles. Please allow me several examples to explain.
Packaging of chemicals has long been mandated with the object of preventing exposure to the contents. Almost regardless of hazard (Class 1 the notable exception), as long as the chemical remains in the package, everything is fine. Corrosives don’t corrode if still in their packaging, flammables don’t burn, toxics don’t poison, and so on...
Now we’re changing our approach for at least some articles, to be more like Class 1, where mere containment of material isn’t enough. The most dramatic example of this is lithium battery packaging, where all the effects of burning are expected to be contained, or at least minimized. And there are murmurings that other articles, such as DG in equipment or devices or machinery should possibly be packaged with an eye toward containing any negative effects of their bad reactions.
Of course our current chemical classification system is starting to look like it needs a major overhaul. 5.2 materials are in fact oxidizers, just oxidizers that happen to also have a subsidiary hazard of flammability as well. Why should 5.2 even be its own classification? We have some (newer) desensitized liquids that won’t burn in Class 3 and some (older) desensitized liquids that won’t burn in a division we name ‘Flammable Solids’. In 4.1, our ‘Flammable Solids’ include self-reactive liquids and selfpolymerizing liquids. For flammability we put liquids and solids in different classifications, but for toxic materials we put liquids and solids in the same division. And we’ve even got issues with what is a liquid versus what is in a ‘liquid state’ and how to package and communicate the hazard of a DG that is solid by definition but often a liquid during normal transport.
And yes, I’ve moaned about some of this before. I apologize if I sound like a broken record. But, perhaps, it’s time to get things fixed.
This is the latest in a series of musings from the porch swing of Gene Sanders, principal of Tampa-based WE Train Consulting and chair of the Dangerous Goods Trainers Association; telephone: (+1 813) 855 3855; email gene@wetrainconsulting.com.
Last week I went fishing in Ireland on one of the lakes near Monaghan. The pike were biting and I was wondering why, after many millions of years of evolution, pike had not learned the difference between a lure with sharp hooks and a real fish without them. Why, I asked, were they programmed to bite first and think later?
I had to look for an answer and found that awareness of danger is usually being superseded by an innate need for survival. Eat first!
Of course when a pike gets hooked it tries everything to shake off the hook by diving, jumping and shaking its head. Sometimes he or she gets lucky and disappears into the deep without harm.
I usually use metaphors to visualise a story and this time I use pike to confirm the relationship with our human programming to survive. People, like pike, do not like to be caught. People do not like to be in danger. But when I look around in the hazardous cargo industries, I often notice that people too bite first and think later. Awareness of being in danger can sometimes be ignored when an operator looks at his watch and sees that he is late for lunch or coffee break.
Thoughts about other matters than the job at hand perhaps roam his or her mind and before he or she realises it, danger lures.
People and Dolphins, I learned recently, are equipped with a similar size brain and these two brains have been evolved to include ‘self-awareness and self-reflection’, whilst other animals, such as pike, do not possess these abilities, which can mean the difference between being caught or not. These are therefore natural, biological capabilities used to warn oneself a bit earlier and prevent dependance
on animalistic predatory behaviour. Our ‘reasoning’ capacity helps us to survive and stay at the top of the food chain. Ayn Rand, the Russian author, talked about the difference between people of character and predators by naming Reason, Purpose and Self-Esteem, as drivers for survival.
When we now apply this information in our daily HSEQ compliance struggle, we can easily conclude that it is our awareness and selfreflection that is guiding us safely through our daily routine in work or traffic. Human brain functioning gives us the edge. Therefore, I believe that HSEQ rules or regulations can only work as guidelines, but that people, through contemplation and thinking, are in charge of Health and Safety, because they are naturally inclined to do so.
According to the ISGOTT Marine Operator Program, the three levels of competency are: Awareness, Knowledge and Skill. I agree. Before I teach people how to operate a technical process, first I address so-called Human Factors and verify their thinking levels. Learning and developing HSEQ skills can only be achieved by understanding if a person is aware or not yet aware of this innately evolved survival mechanism. There, in short, I see the key to reducing HSEQ risk.
This is the latest in a series of articles by Arend van Campen, founder of TankTerminalTraining. More information on the company’s activities can be found at www.tankterminaltraining.com. Those interested in responding personally can contact him directly at arendvc@tankterminaltraining.com.
operators have been releasing financial results for the first quarter of 2018 that, on a like-for-like basis, mostly show a decline in profitability compared to a year ago. Margins are tighter and arbitrage opportunities harder to find.
Nevertheless, operating bulk liquids terminals is a long-term business. Operators need to feel confident that there will be a market for their capacity for decades to come, otherwise the investment is insecure. And given that so much of the new money pouring in to support terminal investment is coming from equity funds that demand a return, it is clear that there is plenty of confidence in the long-term viability of the sector.
FOR ALL THAT governments around the world are responding to the environmentalist lobby and a growing weight of public opinion to promote alternatives to hydrocarbon-based fuels and feedstocks, oil demand grows unabated. That is a function not just of the growing availability of crude oil and natural gas from the development of shale and other tight oil reserves, but also of a desire on the part of the populations of developing economies to enjoy the same standard of living as their counterparts in the developed world.
Such growth in global oil demand means necessarily that there is increasing world trade in crude oil, refined products, liquefied gases and other downstream products, including liquid chemicals, in bulk. That also means there is growing demand for terminalling services both in exporting and importing countries to handle the trade and to act as a balancing point to even out supply and demand inconsistencies.
This year’s annual review of terminal expansion projects reflects those trends.
Despite predictions that the shale oil and gas boom in North America would be short-lived, given the comparatively high cost of monetising these reserves, improvements in extraction techniques and the global thirst for liquid hydrocarbons has meant a lot of investment going in to build terminal capacity at each link of the supply chain. That shows both in the expansion of existing marine facilities, especially in the US Gulf Coast region, as well as plans for new export-oriented terminalling capacity for crude oil, refined products and – increasingly –LNG, LPG and other liquefied gases.
There is a concomitant expansion of terminal capacity in importing countries, responding both to growing demand from increasingly affluent consumers and to efforts to liberalise local markets. This has led to investment in crude oil and downstream logistics infrastructure in countries as diverse as Mexico, South Africa, Mozambique and Sri Lanka.
All this is happening at a time when terminal operators are feeling the pressure of adverse market developments. Major independents and North American midstream
The new Base Line Terminal in Edmonton opened for business in January 2018 with an initial crude oil capacity of 1.6m bbl (255,000 m3) in four tanks. The terminal, a 50/50 joint venture between Kinder Morgan and Keyera Corp, will expand to 4.8m bbl by the end of 2018 as eight more tanks come onstream. A further 1.8m bbl of crude oil storage may be added later, depending on customer demand.
Gibson Energy is to expand its Hardisty terminal in Alberta, Canada with the addition of three new tanks totalling 1.1m bbl (175,000 m3). Two 300,000-bbl tanks are underpinned by a long-term contract with an oil sands customer. The new capacity is due in service in third quarter 2019.
Gibsons has also added 800,000 bbl of new tank capacity at the Edmonton terminal; the tanks entered service in early January 2018.
“Our Hardisty Terminal continues to demonstrate its commercial competitiveness and this contract affirms the ongoing demand for our strategic storage infrastructure in support of incremental oil sands brownfield development,” says Steve Spaulding, Gibsons’ president/CEO. “We will continue to focus on the build-out of the undeveloped acreage at both our Hardisty and Edmonton terminals as our number one strategic priority.”
EXPANSIONS • DESPITE SHORT-TERM CONCERNS OVER TERMINAL PROFITABILITY, MONEY IS STILL COMING IN TO THE TANK STORAGE INDUSTRY TO SUPPORT CAPACITY ADDITIONS
Buckeye Partners has committed $80m to an expansion of the Chicago Complex, its key Midwest logistics hub. The project, backed by a long-term agreement with BP Products North America, will expand storage and throughput capacity, component blend and other services. It includes construction of 600,000 bbl (95,000 m3) of additional product blending tankage and expansion of an existing truck loading rack. The Chicago Complex currently has some 6.8m bbl (1.08m m3) of storage capacity, serving nearly 70 different customers. “This project will further enhance the liquidity of the Chicago Complex and continues to solidify our position as the premier storage and trading facility in the Chicago area,” says Robert A Malecky, executive vicepresident and president of Buckeye’s Domestic Pipeline and Terminals division.
Pin Oak Terminals put the first phase of its grassroots liquids terminal in Louisiana into service last year. The first 424,000 bbl of tankage is used for refined products and biofuels. Construction is continuing as Pin Oak heads for a planned total capacity of nearly 4m bbl (635,000 m3). The terminal is located at Mt Airy on the Mississippi River, and can handle up to 14 barges simultaneously, as well as Suezmax tankers.
Last year TransMontaigne Partners completed the final 800,000 bbl of its phase one 2m bbl (318,000 m3) expansion of the Collins terminal in Mississippi, with the new capacity all leased out. The company has permits to build a further 5m bbl and says it is in “active discussions” with several prospective customers.
Buckeye Partners, Texas Buckeye Partners has completed modifications to the berth at its Texas Hub terminal in Corpus Christi and has loaded the first Suezmax cargo of crude oil for export. The tanker Astra, under charter to Motiva Enterprises, was loaded on 31 March. “Buckeye Texas Hub has become a premier location providing marine terminal services, allowing growing US energy exports access to global markets,” says Khalid Muslih, executive vice-president of Buckeye and president of its Global Marine Terminals operations. “We are very excited to have reached this milestone and look forward to additional opportunities to partner with Trafigura to further expand the terminal’s capabilities and serve the region’s rapidly growing energy production.”
Contanda, Texas Contanda Terminals has secured a long-term lease on what it terms a “prime deepwater access property” on the Houston Ship Channel,
which will allow it to double storage capacity over the next five years and expand into the bulk petrochemical and hydrocarbon markets. “With this project, Contanda has the opportunity to make significant strides in achieving our corporate goals while firmly establishing our position as a leading storage provider in the growing petrochemical and hydrocarbon markets,” says Jerry Cardillo, president/CEO of Contanda. Contanda currently operates three storage terminals in the Houston area. The new facility will be built in phases to provide customers access to onsite processing, multiple ship and barge docks, and convenient tank truck and railcar accessibility.
Enterprise Products, Texas Enterprise Products Partners and Navigator Holdings are to develop an ethylene export facility at Enterprise’s existing Morgan’s Point ethane terminal on the Houston Ship Channel in Texas. The 50/50 joint venture will have refrigerated storage for 30,000 tonnes of ethylene and the capacity to export some 1m tonnes per year. The terminal, expected in service during the first quarter of 2020, is supported by long-term contracts with anchor »
clients including Flint Hills Resources and a Japanese trading company.
Enterprise Products Partners is also to further extend the Enterprise Hydrocarbon Terminal (EHT) on the Houston Ship Channel, having acquired a 65-acre waterfront site immediately adjacent to its existing facilities. The company plans to construct at least two deepwater docks capable of handling Suezmax tankers.
Howard Energy Partners (HEP) commenced operations at the new Maverick Terminals bulk liquids storage facility in Corpus Christi, Texas in May 2018, only six months after construction began. The facility currently has six 80,000-bbl tanks and is being used for the storage, blending and unit train loading of gasoline. HEP has permits to expand total capacity up to 1.25m bbl, while there is space to double that.
“The Corpus Christi terminal, with its strategic location, pipeline connectivity, efficient rail loading facilities and planned Suezmax dock, is poised to provide worldclass midstream services to clients seeking to export crude oil, refined products and NGLs from our major production basins and refining centres to the global markets,” says Brad Bynum, president and co-founder of HEP. “The completion of this facility is also
a significant step in our continued plans to develop key infrastructure for the movement of energy commodities into and out of Mexico.”
Expansion of Kinder Morgan’s Pasadena terminal was held up by Hurricane Harvey although new tankage began coming onstream in November 2017. The new Pit 11 project, costing some $186m, was completed in the first quarter of 2018, adding 2.0m bbl (318,000 m3) of capacity for refined products. Other ongoing projects have added a further 1.5m bbl of tankage at the company’s product storage terminals along the Houston Ship Channel.
LBC Tank Terminals is to build a new terminal in Freeport, Texas to serve MEGlobal’s worldscale monoethylene glycol (MEG) plant. The new facility, LBC Freeport, will be an integrated part of MEGlobal’s supply chain and linked to the adjacent production unit, currently under construction at Oyster Creek. It will mainly handle MEG and diethylene glycol.
“We are delighted to enter into this agreement and partner with MEGlobal Americas on this project. With over 30 years of historical experience in handling glycols, this project opportunity fits our portfolio and investment risk models and is aligned with our business strategy to
further optimise, build-out and expand our business,” says John Grimes, regional business president Americas at LBC Tank Terminals. Construction work has already started, with operational startup planned for 2019 to coincide with the commissioning of the new MEGlobal plant. The terminal will be located on land leased by LBC from MEGlobal Americas, a wholly owned subsidiary of Kuwait-based Equate Petrochemical.
Magellan Midstream Partners says the new dock at its Galena Park terminal in Texas is due in service later this year. Magellan is also reported to be planning a significant expansion of crude oil export capacity at its terminal in Corpus Christi. The company is looking to add four new docks, increase the draft alongside and also replace the harbour bridge to provide extra air draft. The work, due for completion in 2020, will allow tankers up to VLCC size to load crude at a rate of more than 30,000 bbl/hour.
Magellan Midstream and Valero Energy have agreed to expand their 50/50 joint venture petroleum product terminal currently under construction in Pasadena, Texas. Work on the first 1m bbl of capacity and a Panamax-size jetty is currently in hand for planned startup in January 2019; another 4m bbl of tankage, a second berth capable of handling Aframax tankers and a three-bay truck rack will now be added, for completion in early 2020. The partners say another 5m bbl of storage capacity could be built, depending on demand. The new Pasadena terminal will be linked by pipeline to Valero’s refineries in Houston and Texas city, Magellan’s Galena Park terminal and to the Colonial and Explorer pipelines.
Canada-based NOVA Chemicals and Sunoco Partners Marketing & Terminals, a unit of Energy Transfer Partners, have entered a non-binding memorandum of understanding to look at the development of an ethylene
export terminal on the US Gulf Coast. NOVA has new olefins capacity at Geismar, Louisiana and is looking at a joint-venture cracker in Texas. If the plan goes ahead, the partners will establish an 800,000 tpa terminal, fed from the Lone Star NGL storage hub in Mont Belvieu.
Energy Transfer Partners and Satellite Petrochemical USA have agreed to form a joint venture, Orbit Gulf Coast NGL Exports, to build an ethane export terminal on the US Gulf Coast that will provide feedstock for Satellite’s new ethane-fed crackers in Jiangsu province, China. The work will involve a new ethane pipeline from ETP’s Mont Belvieu fractionators, export facilities, an 800,000-bbl (127,000-m3) refrigerated storage tank and a 175,000-bpd ethane refrigeration unit. ETP will operate the Orbit assets, expected to be located in Texas. Commercial start-up is scheduled for fourth quarter 2020.
Phillips 66 commissioned 1.2m bbl (910,000 m3) of new product storage capacity at its Beaumont terminal in Texas in second quarter 2017 and by the end of the year had increased export capacity by 50 per cent to 600,000 bpd. The company is now in the process of adding 3.5m bbl (550,000 m3) of crude storage capacity, due for completion by the end of 2018, which will take overall capacity up to 14.6m bbl (2.3m m3).
Magellan Midstream and LBC Tank Terminals are adding 1.7m bbl of new tankage at their Seabrook Logistics joint venture in Houston this year. Pipeline links are also being added to Magellan’s Houston crude oil distribution system. Operations are expected to commence early in the third quarter.
South Texas Gateway, Texas
Buckeye Partners, Phillips 66 Partners and Andeavour (formerly Tesoro Logistics) have set up a joint venture to develop the planned South Texas Gateway Terminal on 212 acres of waterfront land at Ingleside in Corpus Christi Bay. The terminal will handle exports of crude oil and condensate from the Permian
Basin via the planned Gray Oak pipeline. It will have an initial crude oil storage capacity of 3.4m bbl (540,000 m3) and two docks capable of handling VLCCs. Eventual capacity could be as high as 10m bbl. The partners plan for commercial startup by the end of 2019. Buckeye owns 50 per cent of the venture, with Phillips 66 and Andeavour, which will both commit throughput, each holding 25 per cent.
Vopak is currently adding 138,000 m3 of new chemical tankage at its wholly owned Deer Park terminal. Work is due for completion by the end of the year. Current capacity stands at 1.1m m3 for biofuels, chemicals, refined products, base oils and lubricants.
Contanda is planning to build eight new storage tanks at its Grays Harbor terminal in Washington, US. The 1.1m bbl (175,000 m3) of new tankage responds to customer demand for biofuels. “We heard the community, met with our customers and developed a revised strategy involving the storage of clean products,” says GR ‘Jerry’ Cardillo, CEO of Contanda. In 2013 Contanda (then operating as Westway) sought permission to expand the terminal to handle products other than ethanol but this was turned down, largely due to local opposition to the storage and handling of crude oil. In January 2018 the company formally withdrew the application.
Odfjell affiliate Granel Quimíca is building a second tank farm in Santos. The new facility, due for completion in second quarter 2019, will have a capacity of 51,910 m3, just over half that of the existing Santos terminal.
Vopak is engaged in a significant expansion of its wholly owned Alemoa terminal in Santos, Brazil. During 2017 it announced two projects that will together add some 106,000 m3 of storage capacity and five truck loading bays, which will take total capacity up to almost 280,000 m3. The investment is underpinned by long-term customer contracts. All the new tankage is expected to be commissioned in the second quarter of 2019.
Avant Energy is planning a network of distribution terminals in the Bajio region of northern Mexico, linked by rail to a new marine terminal at Altamira, which will handle tankers of Panamax size and a storage capacity of up to 1.2m bbl (190,000 m3) for refined products. An inland terminal is planned at Querétaro, with direct connections to Kansas City Southern’s Mexican rail network. Construction work on the two terminals is expected to start shortly, with commercial operations scheduled for end 2019.
Sempra energy’s Mexican subsidiary Infraestructura Energética Nova (IEnova) has been awarded a 20-year build-andoperate contract for a marine terminal in the port of Veracruz on Mexico’s Gulf coast.
The terminal, expected to cost some $155m, will offer 1.4m bbl (222,600 m3) of capacity for the receipt and storage of gasoline, diesel and jet fuel for supply to central Mexico. Startup is scheduled in the second half of 2018.
IEnova has also announced plans to build a storage terminal at the La Jovita Energy Hub in Ensenada, Baja California.
The $130m Baja Refinados fuel terminal will have an initial capacity of 1.0m bbl (160,000 m3) for diesel and gasoline, around half of which has been contracted to Chevron to supply its service stations and other consumers in Baja California. Startup is due in second half 2020.
USD Group has begun work on a new multimodal transloading facility, Querétaro Energy Terminal, to serve the local market in central Mexico. The terminal will be serviced by Kansas City Southern’s Mexican
rail operation, with links to all major North American railroads. “Our investment in QET provides an attractive opportunity to establish a presence in the growing Mexican market while leveraging our logistics expertise in support of an existing and profitable business,” says Steve Magness, USDG’s vicepresident, business development.
USD Group is also expanding its network of refined products terminals in Mexico, through its local subsidiary USD Marketing Mexico. It is planning two facilities in the central Chihuahua area, the first of which is expected to be in service in the middle of 2018. It will include storage capacity and rail and truck transloading capabilities. Both terminals will be serviced by Ferromex, which provides access to all North American Class 1 railroads.
Vopak is currently building a new 360,000m3 terminal in Bahía Las Minas on the Atlantic coast in Panama. Once opened in second quarter 2019, the terminal’s nine storage tanks will handle bunker fuels, fuel oil and clean products and will be able to accommodate tankers of up to 80,000 dwt.
ITC Rubis has completed work on tank pit 5A as part of the Phase II expansion of its terminal in Antwerp. The new pit has a range of tanks with total capacity of 10,100 m3 Work started in September 2015 and was finished in December 2017. Phase II also involves addition of new deepwater berths and the company says it is looking at adding extra pressurised gas tanks.
Noord Natie is expanding its Antwerp terminal with 32,700 m3 of new stainless steel tankage in two tank pits, due for completion by the end of this year. The company is looking to continue expanding capacity at the site through to 2022.
To serve a contract with Total, SEA-Invest is adding eight new 20,000-m3 tanks at its Antwerp terminal, along with new loading and unloading bays and a pipeline link to the Total refinery. The Port of Antwerp is supporting the project by dredging to increase the depth alongside the terminal to 15.5 metres.
Vesta Terminals began FEED work last year on a potential 150,000-m3 expansion of its Antwerp terminal to improve vessel turnaround times. The terminal handles middle distillates, light ends and heavy fuels. The project, due for completion in early 2019, will also add two barge berths at the site.
Vopak ACS is expanding its block train loading capacity in Antwerp, primarily to handle acetyls. The terminal will consolidate rail shipments from producers in Germany for onward transport by sea. The new loading station will increase rail capacity by 400 per cent, Vopak says. “We are very pleased to be »
able to make this investment in a very modern, efficient loading station for block trains,” says Manon Bloemer, head of Vopak Belgium. “It offers further logistical benefits for our customers, and reinforces the already strong position of Antwerp as the chemical hub for North-West Europe.”
ATLHA Terminals has secured the rights to build a 70,000-m3 petroleum terminal in Duisburg, Germany. The operator says the facility, due to open in the first quarter of 2020, will handle gasoline, ethanol, biodiesel and chemicals. Amsterdam-based ATLHA was formed last year with the aim of offering terminalling and logistics services to major oil traders. It currently has a 40,000-m3 terminal in southern Spain, with expansion options, and is working on plans to build a 2.5m-m3 greenfield terminal in Europoort, Rotterdam for crude oil and condensate.
UTG Unabhängige Tanklogistik is expanding and upgrading its Kiel tank farm. After signing two long-term transhipment contracts, UTG has started work to install a rail tank wagon unloading station for heavy fuel oil and a road tanker loading station. It will also increase unloading and loading rates to improve throughput of petroleum products and lubricants.
HES Botlek Tank Terminal has put its latest expansion, totalling 277,000 m3 of new capacity, into service. Total capacity at the site now stands at some 490,000 m3. Work is expected to start soon on the next phase of construction, which will add another 130,000 m3 of tank capacity and a jetty capable of handling Suezmax tankers.
Parent HES International is also working on the new Hartel Tank Terminal at Maasvlakte 1, also in Rotterdam, which is expected onstream early in 2019.
LBC Tank Terminals last year upgraded jetty facilities at its Rotterdam terminal, enabling faster vessel turnaround. A new jetty is due
to be added this year, which will double throughput capacity ahead of planned expansion of the site’s storage capacity.
Switzerland-based Alpha Terminals is planning a €250m investment in a new liquid bulk terminal in Vlissingen. Permit applications will be entered this year for a 500,000-m3 facility, capable of handling chemicals, oil products and new energy liquids, including ammonia. Startup is scheduled for 2020.
Odfjell has completed the extension and strengthening of the jetty at its Rotterdam terminal in order to be able to handle LR2 product tankers up to 160,000 dwt. The work, undertaken in collaboration with the Port of Rotterdam, anticipates an increase in the size of vessels calling at the terminal in light of changes in product trades and the demand for distillation at the terminal’s PID unit.
“We are responding to the wishes of our customers to handle ever larger ships,” says Erik Kleine, managing director of Odfjell Terminals Rotterdam. “We appreciate that the Port Authority supports us by deepening the Petroleumhaven.”
Vopak is to expand its existing terminal in Botlek, Rotterdam. The work will involve construction of 15 new stainless steel storage
tanks, totalling 63,000 m3 capacity, for styrene and other chemicals. The work is due for completion in the second quarter 2020.
Last year Inter Terminals completed its largest development project for a decade at its Seal Sands terminal. Work included 27,000 m3 of new capacity for chemicals, additional pipeline links to local chemical plants and a new road tanker loading facility.
NuStar, UK NuStar Energy has completed the first phase of a £25m investment project at its terminal in Grays, UK. A new jetty, capable of handling tankers of up to 125,000 dwt, received its first vessel on 4 January 2018; a second jetty was subsequently added. In addition, four new road loading gantries have been commissioned, with another one being added in the second phase. On completion, the terminal will have seven retail and five separate commercial loading bays.
“This upgrade is a strategic investment for NuStar on the Thames and it will provide significant growth potential,” says David McLoughlin, UK vice-president of NuStar. “Independent supply in the south-east of England is critical to the competitiveness of the region and our clients have been fully supportive of this investment, which will enable the terminal to receive larger cargoes at a significantly faster rate than previously possible.”
Altintel completed a 24,000-m3 expansion of its terminal in Gebze in May 2017 and is considering a further similar project. The company is also looking at developing vacant land at its port, which could result in the terminal more than doubling in capacity to some 200,000 m3
Plans for the massive Raz Markaz crude oil storage terminal are moving forward after Oman Tank Terminal Company was granted usufruct rights by the Duqm Special Economic Zone Authority in July 2017. Under the 40-year agreement, OTTCO will build and operate a terminal with an eventual capacity of 25m bbl (4.1m m3). The terminal will be developed in five phases over ten years at an overall cost of close to $6bn. Third parties will be invited to take shares in the project.
Oman Oil Refineries & Petroleum Industries Company (Orpic) began operations at the Al Jefnain terminal, part of the Muscat Suhar Product Pipeline project, in March 2018.
The company is supplying fuels by truck to local marketers and is aiming to start supply aviation fuel to Muscat International Airport by the end of the year. Fuel is currently being supplied to the terminal by pipeline from Orpic’s Suhar refinery.
The Al Jefnain terminal, with a capacity of some 170,000 m3, expands Oman’s capacity for refined products storage by 70 per cent.
Orpic Logistic is a joint venture between stateowned Orpic and CLH of Spain.
Oiltanking commissioned its new terminal in Matola, Mozambique in November 2017. The terminal has an initial capacity of 58,600 m3
with land available for expansion; Oiltanking is planning another 70,000 m3 of liquids storage and a 33,000-m3 LPG facility at the site.
Oiltanking has a second terminal planned for Mozambique, which will be located in Beira. Both facilities, in which Oiltanking has an 80 per cent shareholding, are designed to improve fuel supply logistics into Mozambique and neighbouring countries. “Mozambique is one of the main transit hubs for petroleum products on Africa’s east coast. The recent transaction and the other projects will further strengthen Oiltanking’s presence in Africa and enhance our ability to serve new market segments on the east coast of the continent,” says Lo Vanhaelen, managing director of Oiltanking Matola.
Bidvest Tank Terminals is to build a 22,600-tonne LPG storage facility at its terminal in Richards Bay, South Africa, following an agreement with LPG trader Petredec Ltd. The completed facility will be the region’s largest pressurised LPG import terminal, with four mounded tanks, each with a capacity of 5,500 tonnes. Bidvest expects to have it in service late in 2019.
Burgan Cape Terminal officially opened for business in the third quarter of 2017. The new
122,000-m3 facility is a joint venture between Vitol, which owns 70 per cent, and two local firms, Thebe Investment Corp and Jicaro. It is initially being used to handle diesel and gasoline, with the option to offer blending of bioethanol and biodiesel. Product is imported by vessel, with the terminal’s jetty capable of handling ships up to 50,000 dwt, and loaded onto trucks via a fully automated rack for onward distribution.
Transnet, the South African national ports authority, last year awarded Oiltanking Grindrod Calulo a build-own-operatetransfer (BOOT) contract to develop a bulk liquids facility in the port of Ngqura, near Port Elizabeth in Eastern Cape province.
An initial 150,000 m3 of storage capacity is due to be commissioned in the third quarter of 2019. Further phases anticipate another 550,000 m3 of capacity. The first phase will replace tanks currently used for petroleum products in Port Elizabeth; those tanks will be decommissioned and the land redeveloped in line with plans to concentrate on commercial and tourism sectors. Once complete, the terminal will provide oil majors, traders and new entrants to the South African oil industry with a modern facility for handling refined products, while also supporting the local shipping industry. »
Vopak has two ongoing projects in South Africa, where it holds a 70 per cent interest in facilities in Durban and Lesedi. Work to add 130,000 m3 of new refined products capacity under the Growth 4 Project in Duban is underway and due for completion by the end of 2019. Fluor Corp was awarded the EPC contract late last year. In addition, work has started on the new Lesedi terminal, which will offer 100,000 m3 of capacity for refined products. Both facilities are part of a larger programme to help meet growing fuel demand in southern Africa.
In December 2017 Sahara Group commissioned a new 36,000-m3 fuel terminal in Dar es Salaam, Tanzania.
The facility is designed as a strategic hub for the distribution of fuels within Tanzania and other parts of East Africa. The storage capacity is split equally between automotive gasoil and gasoline; the terminal has 12 loading bays, giving the capacity to load up to 120 road tankers per day.
Pakistan State Oil and Attock Petroleum have opened a new tank farm to handle jet fuel at New Islamabad International Airport, the largest airport in Pakistan.
The tank farm can handle 10,000 tonnes of product and is equipped with the latest fire detection, alarm and firefighting systems.
VTTI has taken a 51 per cent ownership interest in a greenfield terminal currently under construction near Karachi. The 233,400-m3 terminal will be used to store a range of petroleum products. “VTTI’s expertise and knowledge of the industry as well as its international network, combined with the support of our local partners, Hascol and Fossil, will ensure the future terminal is one of the key independent regional terminals required to supply the growing domestic market,” VTTI says.
Ceylon Petroleum Corp (CPC) is to build
10 new storage tanks at its main import terminal at Kolonawwa, near the Sri Lankan capital, Colombo. The additional 11,200-tonne capacity will help CPC supply rising demand for fuel, which has been growing at 7 per cent per year since the country’s civil war ended in 2009.
Vopak and its joint venture partner PT AKR Corporindo are to expand the Jakarta Tank Terminal by 100,000 m3, taking total tank capacity to more than 350,000 m3. JTT mainly serves the greater Jakarta fuel distribution market and the expansion is needed to cope with rapidly increasing gasoline consumption and Indonesia’s biofuel blending mandate. The expansion, due to be commissioned over the course of 2019, will include eight new tanks for gasoline, ethanol and biodiesel, a new vapour recovery unit and additional in-line blending equipment.
Dialog Group has struck a deal with Johor Corp to lease additional land in Tanjung Langsat, which will allow construction of a third tank terminal. The two existing Langsat
terminals have a combined capacity of 647,000 m3, handling a range of refined products; capacity of the new terminal will be around 300,000 m3. Dialog has not yet indicated a likely date for the completion of the work.
The partners in the Pengerang Independent Terminals project, which include Dialog Group and Vopak, are to proceed with a further expansion of the project. A total of 24 new tanks for clean petroleum products are to be built, which will add 430,000 m3 of additional capacity and take the site’s total capacity up to 1.7m m3. The new tankage is due to come onstream progressively from first quarter 2019.
Funding has also been arranged for the PT2SB terminal at Pengerang, which will mainly serve the new refinery and petrochemical complex being built by Petronas. The 1.5m m3 terminal, which will handle crude oil, refined products, chemicals and LPG, is due for completion by third quarter 2019.
Dialog Group has also entered into agreements to advance Phase 3 of the Pengerang Deepwater Terminals, in which Dialog will have an 80 per cent holding. This phase will be built on reclaimed land adjacent to the second phase, and include tankage for refined products and chemicals »
and deepwater jetties; it will also have land available for downstream refining and petrochemical production.
Philippine Coastal Storage & Pipeline Corp completed the construction of 540,000 bbl (86,000 m3) of new tankage at its facility in Subic Bay Freeport Zone in third quarter 2017. The work included three new tanks and two truck loading racks, which were delivered on time and on budget by Aboitiz Construction.
Capacity at the site now stands at 5.2m bbl for diesel, gasoline, jet fuel and fuel oil.
Phoenix Petroleum has opened its ninth distribution terminal in the Philippines, a 15,000-m3 facility in Consolacion, Cebu.
The terminal will be used to store diesel, gasoline and fuel oils for the retail market in Cebu province as well as for transport and construction firms in the Visayas region.
Vopak is to build a 67,000-m3 expansion of its Sebarok terminal in Singapore, designed to
cater for growing demand for marine gasoil ahead of the arrival of the IMO global sulphur cab in marine fuels from 1 January 2020.
The new tankage is expected to be ready in the third quarter of 2019.
The new Weifang Liquid Terminal opened last year, with an initial capacity of 406,000 m3 for petroleum products and chemical storage. A second phase of 91,000 m3 was commissioned in fourth quarter 2017, while a third phase is under construction and will add a further 164,000 m3 in the first half of 2019.
“The launch of our liquid terminals is timely to capture the growing market for crude and refined oil, as well as chemicals in China. These commodities have benefitted from the gradual liberalisation of import and export policies in China,” says Timothy Lee Chi Tim, vice-chairman of Weifang Sime Darby Liquid Terminal Co. The project is a joint venture between Sime Darby Overseas and Dragon Crown Group Holdings.
Viva Energy last year put into service a 100,000-m3 crude oil storage tank at its
Geelong refinery in Victoria, Australia. The tank, the country’s largest, increases the company’s storage capacity by 40 per cent. Viva Energy has also added a new jet fuel gantry at the refinery and is planning to install a 25,000-m3 gasoline tank and construct a bitumen export facility.
Mobil Oil New Zealand is to build two new tanks at its fuel terminal in Lyttelton to replace tanks damaged in a landslide in 2014. “Construction of new tanks will restore fuel storage capacity at our Lyttelton operation, which, along with the Lyttelton-Woolston pipeline and Woolston Terminal, is an important part of the fuel supply chain in the South Island,” says Andrew McNaught, country manager for Mobil. The new tanks, which will be used to store gasoline and diesel, are due in service in 2019.
Timaru Oil Services Ltd has secured approval from the New Zealand government for a new 44,000-m3 fuel terminal at Timaru Primeport. The facility will have six storage tanks and is designed to improve fuel supplies and boost competition in the local market. HCB
new Hartel site currently under development in Rotterdam’s Maasvlakte area.
FOR MORE THAN a decade now, mergers and acquisitions involving bulk liquids storage terminal operators have been a feature of the equity investment business. Funds have been drawn to the sector by the attractive and comparatively dependable income streams that terminals can generate, especially at times when more traditional avenues have been providing poorer returns.
That process has continued over the past year, with a number of major transactions reported. In some cases, deals have been arranged with investment funds on both sides of the contract, as existing investors cash in on their assets or seek to rebalance their portfolios in light of changes to investment strategies.
A prime example of this is the interesting being shown in HES International. In April this year funds managed by Macquarie Infrastructure and Goldman Sachs announced their intention to acquire HES International from Riverstone Holdings and the Carlyle Group. HES focuses on the storage and handling of liquid and dry bulk products in Europe, with its liquids facilities including Botlek Tank Terminal and Wilhelmsen Tank Terminal, alongside the
“With the support of Riverstone and Carlyle we have become one of Europe’s most successful independent bulk handling companies providing products and services to our customers at 18 sites across eight countries,” says Jan Vogel, CEO of HES International. “Over the past 3.5 years we have implemented a focused strategy that makes optimal use of our prime real estate in Europe’s key ports and allows us to adjust flexibly to future changes and opportunities that energy transition will bring to our sector.”
Late last year HES International also signed an agreement to acquire the Valt Asphalt Terminal in Botlek, Rotterdam. The terminal, a joint venture between Vitol and Sargeant, provides storage, handling and blending services for the European and African bitumen market and is located close to HES’s existing Botlek Tank Terminal and European Bulk Services facilities. HES says it will invest to upgrade the terminal over the course of 2018 with new tanks and ancillary infrastructure.
Another change of investor happened last year at LBC Tank Terminals, when retirement funds State Super and Sunsuper sold their stakes to private investment firm Ardian, giving it a 35 per cent holding. This makes it the largest shareholder, alongside APG and PGGM, both with 32.5 per cent.
“LBC is at a significant transition point in its business strategy, in particular as the business shifts its focus toward expansion of its facilities in USA and Europe. This trend has been identified by Ardian and we value the experience and support they can provide to LBC during this period of strategic change,” LBC’s CEO, Walter Wattenbergh, said at the time.
A new name in the tank storage field is Alkion Terminals, launched in 2016 by InfraVia Capital Partners and Dutch energy firm Coloured Finches. In mid-2017 Alkion acquired eight smaller terminals in France, Spain and Portugal from LBC, as well as the partly owned Sogestran site. It then acquired a 230,000-m3 terminal in Vado Ligure, near Genova, from the Italian state energy firm ENI. Alkion now has ten terminals in five countries in Europe, with an aggregate capacity of some 1.3m m3
M&A • AS WITH CURRENT NEWBUILDING PROJECTS, MUCH OF THE INTEREST IN MERGERS AND ACQUISITIONS IN THE TERMINALLING SPHERE IS FOCUSED ON NORTH AMERICAN ASSETS
A more established investor making waves over the past year has been Warburg Pincus, lead investor in the acquisitive firm Zenith Energy. Last August Zenith agreed to acquire Arc Logistics Partners through a deal with Arc’s major owner, Lightfoot Capital Partners, marking Zenith’s first foray into the US market. “Arc Logistics’ diversified portfolio of logistics assets serves critical links between supply and demand locations in the US and we intend to further develop their existing terminals as well as pursue new developments throughout North America,” said Jeff Armstrong, president/CEO of Zenith Energy, at the time. The acquisition added some 7m bbl (1.1m m3) of storage capacity in the US to Zenith’s existing network in the Netherlands, Ireland and Colombia, which together represent more than 15m bbl of storage for crude oil and petroleum products.
Zenith Energy subsequently bought a bulk liquids storage terminal in Hamburg, Germany from Royal Dutch Shell. The Hamburg terminal is situated on 55 ha of land and has a potential storage capacity of 480,000 m³. Its acquisition in January 2018 was the third major deal for Zenith in Europe, following its purchase of terminalling assets in Amsterdam from BP in 2016 and the Bantry Bay terminal in Ireland from Phillips 66 in 2015.
Meanwhile, at the start of this year, Zenith Energy sold a 51 per cent interest in the Pawnee, Colorado crude oil terminal to Tallgrass Terminals for $31m. The Pawnee
Terminal acts as an injection point for the Tallgrass Pony Express Northeast Colorado Lateral and has 300,000 bbl of storage capacity. Tallgrass has also acquired a 38 per cent interest in Deeprock North LLC, which owns a crude oil terminal in North Cushing, Oklahoma. Deeprock North has now been merged into Deeprock Development, with a total storage capacity of some 4.0m bbl, in which Tallgrass has an overall 60 per cent interest.
ArcLight Capital Partners, which owns TransMontaigne Partners’ general partner, has set up a joint venture with BP West Coast Products covering refined product logistics in the US Pacific Northwest. The deal was anchored by the purchase of two largescale refined products terminals in Seattle, Washington and Portland, Oregon from BP, which are being operated by ArcLight affiliate TLP Management Services.
Last year TransMontaigne made a further acquisition on the US west coast, buying the Martinez and Richmond terminals in California from Plains All American Pipeline for $275m.
The established Australian investment funds have also been active lately, particularly Macquarie Infrastructure Corp, which owns International-Matex Tank Terminals (IMTT).
In August last year IMTT entered into an agreement to acquire Epic Midstream from affiliates of White Deer Energy and Blue Water Energy. The transaction valued Epic at
$171.5m. Epic operates seven terminals in the south-east and south-west US, with its main marine terminal operations in Savannah, Georgia. Aggregate storage capacity is some 3.1m bbl (492,000 m3) for petroleum products, asphalt, biofuels and chemicals.
Macquarie was also involved in the sale of Odfjell’s 50 per cent shareholding in the 377,000-m³ Oiltanking Odfjell Terminal Singapore (OOTS) last October; Odfjell received some $300m for its holding in a deal involving Macquarie Infrastructure and Real Assets (MIRA), booking a net gain of some $135m. “This divestment is in line with our strategy to focus on the terminals where we have managerial control of the assets and to further invest in growth opportunities in our core markets, such as Houston and Rotterdam,” CEO Frank Erkelens said at the time. This followed on from Odfjell’s sale of a 35 per cent indirect ownership in the Exir Chemical Terminal in Iran to Oiltanking in June 2017.
Subsequently, however, Lindsay Goldberg has suggested it may look to sell its 49 per cent interest in Odfjell Terminals BV, in which case Odfjell may seek buyers for its Rotterdam terminal.
Another Australia-based fund, Prostar Capital, acquired Socar Aurora Fujairah Terminal early in 2018. The terminal currently has 350,000 m3 of tank storage for refined products, with a further 315,000 m³ under construction and room for another 150,000 m³. Prostar already had a 40 per cent interest in the nearby Fujairah Oil Terminal.
London-based Whitehelm Capital acquired a 90 per cent stake in Vopak Terminal Eemshaven, a joint venture between Vopak and NIBC European Infrastructure Fund, in September last year. Vopak continues to manage and operate the terminal. The 11-tank, 684,000-m³ facility is used for the strategic storage of gasoil, gasoline and other refined products and has a deepwater jetty to handle oceangoing ships. Whitehelm focuses on investing in infrastructure assets with stable long-term cash flows and, Vopak says, has a long history of investing in the tank storage sector, including Oikos Storage in the UK.
Elsewhere in the North American midstream sector, SemGroup Corp has been busy, not least
with the acquisition last year of Houston Fuel Oil Terminal Co (HFOTCO) from investment funds managed by Alinda Capital Partners for a sum that could be as high as $2.1bn, depending on performance. The deal was, SemGroup says, “part of its long-term strategy to add secure, downstream cash flow to its portfolio mix”.
HFOTCO is located on 330 acres of land along the Houston Ship Channel. The business is fully supported by take-or-pay contracts with primarily investment-grade counterparties that have been customers for an average of 15 years. HFOTCO is currently executing on contractually supported growth projects, including a new ship dock, a new pipeline and connections, as well as an additional 1.45m bbl of crude oil storage that is expected to be in service mid-2018.
Following the acquisition of HFOTCO, and as part of its efforts to trim its borrowings, SemGroup sold its UK petroleum storage business, SemLogistics, to Valero Logistics
UK Ltd, a wholly owned subsidiary of Valero Energy Corp. SemLogistics’ main asset is the 1.4m-m³ Milford Haven terminal in Wales.
There has also been some activity on the part of the major international trading houses. Glencore, for instance, sold a 51 per cent interest in the newly formed HG Storage International Ltd (HGSI) to HNA Innovation Finance at the start of this year. HGSI was set up to consolidate Glencore’s petroleum products storage and logistics businesses in strategic ports in Europe, Africa, the Middle East and the Americas. The $775m transaction is being carried out in two phases as the transfer of the interest in Glencore’s three US sites is subject to regulatory approval. Glencore and HNA say they plan to expand the HGSI footprint through acquisition and organic growth.
Refiner/trader Gunvor agreed last October to sell its shareholding in the Maasvlakte Oil Terminal in Rotterdam to Aramco Overseas Co. Gunvor says the divestment is part of its strategy to invest in its Rotterdam refining operations. For Aramco Overseas, the deal will support its refining activities in north-west Europe, strengthening its export supply chain.
Many of the other newsworthy deals recorded over the past year have involved midstream assets in North America. For instance, in October last year Pin Oak Terminals acquired Gravity Midstream Corpus Christi, now renamed Pin Oak Corpus Christi, in a deal secured by financing from Pin Oak’s owners, Dauphine Midstream and Mercuria Energy. The terminal offers 737,500 bbl (117,250 m³) of storage capacity, pipeline links to nearby refineries, a crude processing unit and asphalt plant, rail loading and unloading facilities, truck racks and a dock capable of handling Aframax tankers. Pin Oak says there are long-term contracts in place that will allow it to significantly expand operations.
Delek Logistics Partners and Green Plains Partners have formed a 50/50 joint venture, DKGP Energy Terminals LLC, to invest in storage terminals for light refined products. DKGP’s first acquisition involved two light products terminals owned by an affiliate of American Midstream Partners and located in Texas and Arkansas. DKGP is understood to have paid $138m for the assets this past February. HCB
DELEK LOGISTICS PARTNERS and Green Plains Partners have formed a 50/50 joint venture, DKGP Energy Terminals LLC, to invest in storage terminals for light refined products. DKGP’s first acquisition is likely to be two light products terminals owned by an affiliate of American Midstream Partners located in Texas and Arkansas. DKGP has agreed to pay $138.5m in cash for the assets; subject to the usual conditions and approvals, the deal is expected to close in the first half.
The two acquired terminals have a total capacity of 1.32m bbl (210,000 m3). The North Little Rock terminal, which features ethanol blending facilities and the capability to unload ethanol unit trains, is adjacent to Delek Logistics’ existing terminal.
Green Plains and Delek Renewables formed another joint venture, NLR Energy Logistics
LLC, a year ago with the aim of developing another ethanol unit train terminal in the Little Rock area; this facility is expected to be in service before the end of this quarter. The partners stress that NLR Energy Logistics and DKGP will remain separate entities.
“We are excited to partner with Green Plains Partners for its potential ethanol volumes, logistics expertise and industry knowledge as the domestic markets expand blending, and look forward to the future of this joint venture,” says Uzi Temin, chairman/CEO of Delek Logistics’ general partner. “This is a great opportunity as it fits our strategy to grow through assets in markets that we are very familiar with, and by contributing our complementary existing logistics assets in east Texas and Little Rock, Arkansas, we expect to create additional synergies within the joint venture. In addition to serving third party customers, it should be well positioned to provide additional logistics support to Delek US’ Tyler, Texas and El Dorado, Arkansas refineries. Our financial flexibility should give us the ability to finance this investment under our revolving credit facility, while we continue to look for opportunities for future growth.”
“This transaction helps us start achieving our goal of diversifying Green Plains Partners
revenue and income streams,” adds Todd Becker, president/CEO of Green Plains Partners. “We believe this joint venture with Delek Logistics creates significant value for both our partnership unitholders and Green Plains Inc shareholders.
For American Midstream, the divestment of the terminal assets is part of its capital optimisation strategy; that process is likely to also see the sale of additional terminal facilities, including its marine and speciality chemical storage facilities.
Delek US Holdings, meanwhile, has reached agreement to sell four asphalt terminals in California and Arizona, as well as its 50 per cent share in another terminal in Nevada to an affiliate of Andeavor for $75m in cash plus working capital. The deal is expected to close before the end of the first half.
“We explored different options for these assets, including a sale to our affiliate, Delek Logistics Partners, and determined this transaction was the most attractive relative to other options,” says Yemin. Net cash proceeds could be returned to shareholders.
Delek US is, though, looking at other logistics assets that may be dropped down to Delek Logistics Partners, including assets at the Big Spring refinery in Texas that may also be transferred during the first half. HCB www.deleklogistics.com www.greenplainspartners.com www.americanmidstream.com
ONE OF THE biggest problems faced by tank storage operators is product contamination and its costly repercussions. Sofis, an industry leader in valve operations, was at StocExpo in Rotterdam this year, previewing its new key management system. The system aims to help eliminate the level of human error that is common alongside manual valve operation.
Sofis’s key management system comprises three main components: valve interlocks, which are permanently mounted to and lock the valve in the fully open or fully closed position unless specifically coded keys are inserted; a key management system that can authorise the removal of the keys; and finally a control cabinet that interfaces with the key management system to only allow specific keys to be removed after authorisation has been granted.
The system works to ensure that contamination risk is reduced to zero, without the need to implement a fully automated system, which is a costly and, in most cases, unrealistic solution.
Once it has been established that a valve needs to be operated, one of the operators in the control room can release the required open or close key from the cabinet. Once released, a field worker has to insert the key into the correct slot on the correct valve in order to operate the valve successfully. Since each key is coded specifically for a particular valve, it is
impossible to accidentally place an open key for valve X into the open slot on valve Y and, likewise, the system makes it impossible to insert the open key for valve X into the close slot on valve X, and vice versa.
Once valve operation is complete, a separate distributed control system (DCS) monitors the valve line-up using position feedback from the key management system.
Having a strictly regulated key management system ensures that all valve operations are performed correctly first time and there is very limited scope for human error.
Sofis’s move into the world of automation represents a significant step for the company. Frank Gielissen, marketing
director, explains how an intermediate solution like this opens up doors that had previously not been accessible to most operators. While full automation might be a preferable choice for most tank farm operators, logistically it simply isn’t an option. In order to implement a fully automated network of valves, all the valves have to be changed out, actuators need to be fitted and the farm has to be supplied with power. The latter can pose a significant problem for some, as digging up the ground to place wires may be prohibited by environmental agencies, making full automation next to impossible. Sofis’s system can be integrated into existing third-party software which makes it compatible with the current framework that the tank farm has in place or, in the case of a new farm, means no extra budget needs to be allocated to extra, more specific software.
Most tank farms around the world are currently operating with hundreds of manual valves and no realistic option to full automate. As a result, Sofis’s key management system allows a reasonable level of automation at a fraction of the cost of a fully automated system. HCB www.sofisglobal.com
EDDYFI TECHNOLOGIES HAS launched Swift™, a brand new ultrasonic testing instrument as part of its Silverwing product line. The new instrument in its line of non-destructive testing (NDT) solutions brings long-awaited efficiency improvements to remote-access applications such as storage tank inspections.
The importance of tank inspection should not be understated. Tank shell wall thickness, being an important measure of a tank’s structural integrity, requires in-depth and detailed analysis at regular intervals. Swift can be used alongside Eddyfi’s Scorpion2™, a steerable, remote-control ultrasonic
inspection crawler. Using ultrasonic testing (UT) crawlers like the Scorpion2 means inspections can occur efficiently, with all the scan data recorded in real time.
The Scorpion2 enables a deeper understanding of assets due to its unique UT analysis capabilities and software features. The unit combines a full-featured UT instrument as well as the capability to drive and control the UT crawler remotely. The latter brings a significant increase in the efficiency of tank inspection due to the fact that no scaffolding or rope access is necessary to perform checks.
Scorpion2 boasts several major features over its predecessor. For example, the drycoupled probe wheel removes the need for an external water source, usually needed for UT inspections. The Scorpion also comes
fitted with a gimballed probe holder, enabling the inspection of uneven surfaces. From a technological point of view, the Scorpion2 has the ability to programme with length and pattern of scans which gives users more flexibility and is capable of measuring thickness at speeds of up to 180 mm/s (6in/s). Finally, the 50-m (164-ft) umbilical removes the need for scaffolding and rope access, which is hugely beneficial for ease of use and for the safety of operators.
Scorpion2 comes equipped with four permanent magnet-drive wheels and two encoders. This combination makes it possible to compensate for the crawler’s drift from slippage and the weight of the cable. It also has a significantly simpler design, making it quicker and easier to set up than the original Scorpion.
“Swift and Scorpion2 are the perfect power UT inspection combo,” says Edwin van der Leden, product manager at Eddyfi Technologies. “Not only do they contribute to improve the overall efficiency of inspections, they also provide better accuracy. For example, we bring forth a unique way of processing gate information, rendering acquired data with floating gates and making postinspection processing of gate information possible. This translates to higher revenues for our customers.”
Eddyfi Technologies, headquartered in Quebec, Canada, employs more than 250 people and has customers in more than 80 countries. Eddyfi develops what it says are the industry’s most reliable test instruments, acquisition and analysis software, as well as more specialised surface array and tubing probes. The company focuses on offering high-performance non-destructive testing solutions for the inspection of critical components and assets.
Last month Eddyfi announced the acquisition of M2M, a French developer and manufacturer of phased array ultrasonic testing (PAUT) instruments for NDT. The deal extends Eddyfi’s presence in what CEO Martin Thériault terms “the much larger advanced ultrasound space” and also gives the company a foothold in China, where M2M has an office. HCB www.eddyfitechnologies.com
Saval was showing its new SmartMix® electronic foam mixing system, designed to bring added accuracy in the mixing ratio of foam concentrate to water. This is achieved by continuous monitoring of both flows using electromagnetic flowmeters and real-time adjustment of the concentrate control valve. The system employs a state-of-the-art logic specifically developed for SmartMix
The cabinet also includes an integrated touchscreen user interface, allowing the user to view system parameters, diagnostics and all process values, alarms and events. All data can be downloaded for analysis.
Saval’s partner company Knowsley SK had its new Turbinator foam mixing unit on display in Rotterdam. Developed from the company’s successful 2P and 3P foammaking systems, the Turbinator is designed specifically for the task using positive displacement technology.
The really clever thing about the Turbinator is that it is powered by water pressure – the water-powered motor and foam concentrate pump are close-coupled and integrated within a single body, so that while every revolution of the water motor delivers a fixed volume of water, the corresponding revolution of the foam pump delivers a fixed volume of concentrate. This means that the foam mixing ratio is maintained, regardless of the operating pressure.
AUTOMATION HAS COME to the tank storage sector with a vengeance in the last couple of years, changing established working practices and procedures and helping to improve safety and efficiency. That process has lately arrived in the firefighting department, promising better performance and environmental protection.
Two parts of SK FireSafety Group were on hand at last month’s Tank Storage Connect event in Rotterdam, where they each had new developments to show to visitors.
In addition to providing an accurately mixed firefighting medium, SmartMix can also reduce the environmental impact of firefighting operations. Its test procedures operate without the need to actually mix water and concentrate, avoiding the unnecessary use of concentrate stocks and eliminating the potential for concentrate to escape the system. During the test the injection point to the firewater system is isolated and the concentrate is diverted through the test outlet fitted with a pressure sustaining valve. Those test procedures also ensure that accurate proportioning is achieved every time.
The SmartMix system is housed in a powder-coated stainless steel cabinet that can be installed in the harshest environments.
That design also makes the device inherently self-priming and it also generates no wastewater. It is produced in three sizes, ranging from a nominal 4” to a nominal 8”. Knowsley SK also manufactures a unit specifically for offshore applications, in which the 431 stainless steel rotors are replaced by super duplex F55 grade steel, and the mechanical seals are Hastelloy and rubber rather than stainless steel and rubber. This allows it to use seawater as an alternative to fresh water. All products meet the requirements of the EU ATEX Directive.
Speaking to HCB at the Tank Storage Connect event, Peter Robinson, Knowsley SK’s UK sales manager, reported that the company has seen a lot of interest in the Turbinator, not least since its design and independence from a power source makes it ideal for use in a range of applications, such as foam monitors, deluge systems, foam makers and handline nozzles. HCB www.knowsleysk.com www.saval.nl
FIREFIGHTING • RECENT ADVANCES IN FOAM MAKING FROM THE SK GROUP MEAN LESS RISK OF ENVIRONMENTAL DAMAGE AND A MORE RELIABLE RESPONSE TO TANK FARM FIRES
ALL LIQUID COMMODITIES, be they refined petroleum products, chemicals or foodstuffs, will at some point pass through or be kept at a bulk liquids storage terminal. They may arrive at and depart from the terminal by oceangoing tanker, barge, rail tank car, pipeline or tank truck, in volumes that range from a few hundred to many thousands of gallons.
The job of the storage terminal in this supply chain is twofold: firstly to make sure that each parcel of cargo is in the right place at the right time; and secondly to do that in the most efficient, cost-effective, safe and reliable way.
Pumps play an important role in enabling the movement of bulk liquids between the terminal’s storage tanks and transport vessels.
Over the years, different types of pump technology have been used in bulk liquids storage terminals, with centrifugal and gear-type pumps proving popular. But terminal operators should perhaps look at the option of positive displacement sliding vane pumps as the go-to choice for the transfer of a range of fluids with varying viscosities at different flow rates and pressures.
There are three areas where sliding vane pumps can outperform centrifugal and gear-type pumps in liquids storage terminal applications.
Firstly, they offer greater energy efficiency. While terminal operators must meet the needs of their customers as regards product storage and transfer, they are also responsible for optimising energy consumption and costs at their facilities, helping create a healthy bottom line. Sliding vane pumps can assist in this area because their design and method of operation is one of the most energy-efficient among all pumping technologies.
Sliding vane pumps will help storage terminal operators gain a competitive business advantage because they offer a number of energy- and cost-saving features and benefits in liquids transfer applications, including:
• The ability to handle very thin liquids (gasoline, ammonia, LPG, etc) as well as those with viscosities of up to 50,000 cSt
• Flow rates of up to 2,000 gas/min (7,580 l/m), proportional to the pump’s speed
• Easy maintenance and vane replacement that does not require the pump to be taken out of service
• High volumetric efficiency due to selfadjusting vanes that eliminate energyrobbing slip
• Excellent suction lift and line-stripping capabilities, critical for terminal facilities that must clear lines, vessels and storage tanks of residual product
• The ability to generate high pressure in low-flow applications
• Dry-run and self-priming capabilities
• Lower overall cost of ownership compared to centrifugal pumps
A second benefit of sliding vane pumps is their sheer versatility around the terminal. Terminal operators can construct skids that allow pumps to be moved around the facility to perform multiple liquids transfer operations. For example, the skids can be placed at railcars on a siding then repositioned between a tank truck and storage tank to facilitate that loading or unloading process.
This portability makes the liquids transfer process more nimble and versatile, which results in optimised transfer operations with a corresponding reduction in operating costs.
Finally, the design and operation of sliding vane pumps make them ideal for use in a variety of applications. While shining in loading or unloading storage tanks, or transferring
liquids from one storage tank to another, the operation of sliding vane pumps can also make them a first-choice technology for other common storage terminal activities. These include the blending, mixing and packaging of raw materials or end products, which can then be loaded onto transport vehicles for further shipment down the supply chain.
Rotary vane pump technology was perfected by Robert Blackmer in 1899; the company that bears his name, based in Grand Rapids, Michigan, has taken that design forward to today’s modern sliding vane pump designs.
For almost 120 years, Blackmer® has been dedicated to providing the most efficient, safe and reliable pumping products for its customers in many of the world’s most important industries.
Today, many of those customers in the liquids storage terminal market are striving to optimise the performance of their operations in terms of delivery and storage efficiency, energy use and cost-effectiveness. These are important goals and exactly the capabilities that sliding vane pumps have been designed to offer. Blackmer recognises the needs of its customers and has taken great pains to develop and produce sliding vane technologies that play a significant role in improved operations at storage terminals.
Blackmer has a range of sliding vane pump models that fit the various liquids handling needs of storage terminals. All incorporate the sliding vane principle of operation, which employs a number of vanes that are free to slide into and out of slots on the pump rotor. When the pump driver turns the rotor, the vanes move outward in their slots and bear against the pump’s inner bore casing, creating pumping chambers that transfer a volumetrically consistent amount of liquid, essentially independent of pressure or viscosity.
According to TankTerminals.com, there are nearly 1,600 terminals in the United
Transloading – defined as the process of transferring a shipment from one mode of transport to another without intermediate storage – may be tangential to the traditional day-to-day operations at some liquids storage terminals, but there are instances where the increased use of transloading can have benefits for the terminal operator.
In essence, the main objective of transloading is to place commodities as close to the point of final processing, packaging, delivery and consumption as economically possible. It should be no surprise that moving products strictly by truck can be the most expensive form of shipping while also being the least efficient in terms of time required to complete the shipping process.
Creating a transloading operation can overcome those shortfalls by the incorporation of railcars or barges, which reduces the number of trucks or truck-miles needed.
By extension, this lowers capital costs for the shipper since smaller truck fleets, lower fuel consumption, a leaner driver pool and fewer empty trips will all reduce expenses.
Another economic advantage of transloading is that the process allows for a quick response when inventories need to be replenished, allowing companies to accelerate turnover rates, resulting in reduced inventory costs.
As noted earlier, the portability, versatility and energy-saving efficiencies inherent in the design of sliding vane pumps can play a role in improving the economic sustainability of transloading operations at storage terminals.
States that are dedicated to the storage of various types of commodities and at various capacities. All of these facilities must meet the unique needs of their customers regarding reliability and efficiency, while also satisfying internal demands that they operate at the highest level of cost-effectiveness. As shown, terminal operators who choose to outfit their sites with sliding vane pumps can create many significant competitive
advantages, all of which will play a role in building improved customer relations and a more robust bottom line. HCB
Thomas L Stone is director of marketing for Blackmer® and PSG®. He can be reached at tom.stone@psgdover.com. More information on Blackmer’s full line of pumps and compressors can be found at blackmer.com. Blackmer is a product brand of PSG®, a Dover company.
NorthStar Midstream has sold its newly built Port Arthur export terminal in Texas to a subsidiary of Colonial Pipeline. The terminal is linked by pipeline to the local refining complex and has “significant” marine loading capabilities.
“We’re pleased to announce another transaction for the NorthStar platform,” says Tim Casey, NorthStar CEO. “Our entire team is proud of the quality and capabilities of the terminal built in Port Arthur and the strong relationships we’ve developed with the local refinery community and the Port of Port Arthur. Colonial brings significant industry experience to manage the terminal over the next phase of its life cycle.” northstarmidstream.com
PBF Logistics has acquired the assets of Cummins Terminal in Knoxville, Tennessee. The East and West terminals offer tankage of some 520,000 bbl (83,000 m3) and nine truck loading bays, and receive clean products from the Colonial and Plantation pipelines.
“The acquisition of the Cummins Terminal is expected to allow PBF Logistics to leverage its growing footprint and capitalise on commercial opportunities with new customers as well as
expand opportunities with PBF Energy,” says the company.
PBF Logistics has also reached agreement to acquire a number of assets from subsidiaries of its sponsor, PBF Energy. These include the Toledo Rail Products Facility, which is to be upgraded to improve clean product distribution and exports; the Chalmette Truck Rack, which handles gasoline, distillates and ethanol; and the Paulsboro Lube Oil Terminal, which is also to be expanded. PBF Logistics is also planning to expand capacity for unloading LPG from rail tanks at the Chalmette refinery and ethanol
loading infrastructure at the Delaware City refinery’s marine terminal (below).
“These acquisitions and projects represent the first step towards executing the multi-year growth plan announced earlier this year,” says Matt Lucey, executive vice-president of PBF Logistics. “This is a unique blend of opportunities as PBF Logistics has executed on all three of its avenues for growth – third-party acquisitions, organic projects and drop-downs. By leveraging our relationship with our sponsor, the partnership is capitalising on opportunities at four of PBF Energy’s five refineries and has expanded the partnership’s geographic presence.” www.pbflogistics.com
Sempra Energy’s Mexican subsidiary, Infraestructura Energética Nova (IEnova) has announced plans to build a storage terminal at the La Jovita Energy Hub in Ensenada, Baja California.
The $130m Baja Refinados fuel terminal will have an initial capacity of 1.0m bbl (160,000 m3) for diesel and gasoline, around half of which has been contracted to Chevron to supply its service stations and other consumers in Baja California. Startup is due in second half 2020. www.sempra.com
Howard Energy Partners (HEP) (right) has commenced operations at the new Maverick Terminals bulk liquids storage facility in Corpus Christi, Texas. The facility currently has six 80,000-bbl tanks and is being used for the storage, blending and unit train loading of gasoline. HEP has permits to expand total capacity up to 1.25m bbl (200,000 m3), while there is land available to double that figure.
“The Corpus Christi terminal, with its strategic location, pipeline connectivity, efficient rail loading facilities and planned Suezmax dock, is poised to provide worldclass midstream services to clients seeking to export crude oil, refined products and NGLs from our major production basins and refining centers to the global markets,” says Brad Bynum, president and co-founder of HEP. “The completion of this facility is also a significant step in our continued plans to develop key infrastructure for the movement of energy commodities into and out of Mexico.”
www.howardenergypartners.com
Vopak has reported first-quarter EBITDA of €190.2m, 6 per cent down on last year’s figure, from revenues down 7 per cent at €316.2m. While much of the decline is due to currency movements, Vopak also notes that overall occupancy was 4 points lower at 87 per cent, as a result of “a less favourable oil market structure” that led to lower utilisation at the company’s major oil hubs.
EBITDA was lower than a year ago in all territories except the China and North Asia division, the smallest of Vopak’s four terminal divisions.
Vopak expects similar conditions for the rest of 2018 and says its full-year figures are likely to be affected by currency exchange movements, particularly the US and Singapore dollars. However, with 3.1m m3 of new capacity currently under development and with “high commercial coverage”, together with the ongoing cost-efficiency programme, Vopak is aiming to “significantly improve” EBITDA in 2019. www.vopak.com
Odfjell SE has announced that private equity firm Lindsay Goldberg is considering selling the 49 per cent stake in Odfjell Terminals BV it acquired in September 2011.
Odfjell says it “continues to consider Odfjell Terminals as core business” and that it is “committed long-term to owning, developing and operating tank terminals”. However, if Lindsay Goldberg does sell up, Odfjell will evaluate selling its indirect 51 per cent shareholding in the Rotterdam terminal.
Meanwhile, Odfjell Terminals posted EBITDA of $6.3m for the first quarter, down from $9.9m in the previous period. The decline reflected the sale of Odfjell’s share in the joint-venture Singapore terminal as well as a one-month maintenance outage at the distillation unit at Rotterdam. Underlying operations are “stable”, the company says, and it expects that to continue through 2018. www.odfjell.com
Canada-based Inter Pipeline Ltd has reported a record first quarter, with net income of C$143m, a result driven largely by its NGL processing business, which benefited from strong commodity pricing in North America.
Its European tank terminal operation, Inter Terminals, generated C$18.7m during the quarter, down from C$26.2m a year earlier, as a resulted of backwardation in certain product sectors, which led to a decline in average utilisation from 99 per cent in first quarter 2017 to 82 per cent. Inter notes that several new contracts have started since the end of the quarter, pushing up utilisation to 87 per cent for April. www.interpipeline.com
The port of Rotterdam handled 55.9m tonnes of liquid bulk in the first quarter of 2018, up 0.5 per cent on the same period last year. Within that, crude oil volumes were down 4.5 per cent, while oil products were up 4.8%, with the fall in fuel oil throughput now having ceased.
The port of Antwerp, meanwhile, handled 18.6m tonnes of liquid bulk in the first quarter of 2018, up 4.6 per cent on the same period last year. Chemicals volumes grew by 6.8 per cent and oil products by 4.6 per cent.
“These growth figures once again emphasise Antwerp’s ideal location for European distribution, with the phenomenal growth in tank storage and the general confidence in our chemical and petrochemical cluster,” says the port authority.
THE HALLS OF the Exhibition Centre Liverpool were abuzz again as the 2018 FPS Expo rolled back into town for two days in the middle of April. The event, organised by the Federation of Petroleum Suppliers (FPS), always draws an excitable crowd – which is not surprising, as there is always a lot to get excited about.
Once again, the array of new road tankers, their livery glinting under the lights, was supplemented by the rattle and hum of business going on around the stands and all manner of equipment vying to attract the eye of the visitor.
For its 38th year, the FPS Expo drew more than 120 exhibitors, including 14 first-timers, showcasing new products and services and providing an array of demonstrations and information. Those new to the event included Bunded Fuel Tanks, GreenChem Ltd, Fairfax 3D Design, Cardfox Merchant Services, Normec, Ashdowne Oil & Chemical, Close Brothers Asset Finance, REDS Group Ltd, Cavagna UK Ltd, Talent Retention Solutions (TRS) and Wirehouse Employment Services.
All those at the show were taking the opportunity offered by the showcase to
demonstrate what they could offer the fuel distribution industry at this critical time. As FPS’s recently appointed chief executive, Guy Pulham, said before the show: “The industry is on the verge of change with the government’s Clean Growth Strategy, 2050 carbon reduction targets and the introduction of Clean Air Zones. It is vital that we all work together with the government, providing information and ideas on action the government can take to meet carbon reduction targets in off gas grid buildings, including taking a stepped change approach to carbon reductions through a government supported nationwide scheme to replace older oil boilers with energy efficient condensing boilers, the development of a bio fuel and alternative research into hybrid systems.”
HCB also took the opportunity for a couple of days away from the desk to see what was new and interesting. There was plenty of that and the following pages describe just a few of the innovations we spotted among the stands.
Many innovations of interest address the desire on the part of operators to improve »
safety, efficiency and profitability – they all go hand in hand. One company to have looked at that equation with an open mind is Alfons Haar, which has built a reputation on its fuel metering systems, hose reels, pumps, overfill protection equipment and other kit used in the transfer of liquid fuels.
Alfons Haar has realised – as have others – that the most safety-critical part of the supply chain is during product transfer, and particularly in those operations where there is potential for human error. This is often the case during fuel deliveries, where drivers are expected to move back and forth between the tank, the connection and the controls. Manual operation of the transfer also opens up the potential for overfills and crossover errors.
At the FPS Expo Alfons Haar demonstrated its solution: the ‘Wireless Cockpit’ (WIPIT). This system is based around a hands-free wrist band, which allows the operator to remotely control the motor, hose reel drive, illumination and other elements of the process. At the touch of a button, the hose reel can be locked in place and the loading
process can begin automatically, eliminating the need to keep moving back and forth between the hose reel and the vehicle to lock and unlock the hose in place.
This automated process not only saves time but is also safer as it avoids human error and allows the driver’s hands to remain free, without the risk that they might drop the remote control. Switching fuels has also been streamlined to allow for safer and more efficient loading. Using the system, loading operators can switch between gasoline, kerosene and diesel, making the process more economical and environmentally friendly.
One more company leading the way in process digitalisation is US-based Scully Signal Company, which previewed two new innovations in Liverpool. The first, Scully Connect, is a quick-connect system for overfill prevention sensors. Currently, sensors are built into housings on the top of tanks, often bolted and screwed into place. While objectively secure, this method makes maintenance difficult and often costly, due to the need to strip wires and and the various tools needed to complete the job.
With no tools required and colour-coded connectors, Scully Connect offers a hasslefree maintenance solution. The housing unit uses rugged handles, meanig no tools are needed to open the sensor unit and colourcoded wires mean that the sensor can be
connected and disconnected easily. The quickconnect system is designed to cut installation time by up to 50 per cent, as well as increase safety. The system is also designed to reduce costs with its corrosion-proof, marine-grade connectors, making its patented design one of the safest on the market, Scully says.
The second of Scully’s latest innovations is the Intellitrol 2. Combining a terminal overfill prevention and a ground verification system into one unit, the Intellitrol 2 offers a complete visual diagnostic display of all overfill sensors’ statuses, as well as vehicle static grounding information. The system has the capability to monitor up to eight two-wire or fifteen fivewire vehicle sensors. The system’s ability to perform self-checks means that maximum loading safety is ensured at all times, and operational viability is guaranteed.
With full automation on the horizon, remote monitoring of tanks has become more and more desirable. Dunraven Systems, a specialist in remote monitoring, was exhibiting its Apollo Infinity line of tank monitoring products.
The Apollo Infinity SigFox ultrasonic level monitor, Dunraven’s latest system, measures fuel levels, offers a five-year battery life and remotely feeds back to an IoT cloud-based system where data can be viewed using desktop software or a smartphone app. »
Although the system is not yet ATEX approved, Dunraven does offer ATEX-approved pressure sensors and other compliant products in its range. This advanced monitoring system allows fuel distributors and multi-site organisations to remotely monitor their customers’ tanks through whatever method they see fit, whether using Apollo RMS Cloud, RMS G2, RMS Lite, or through Apollo Oil Monitoring Station.
PDI, an industry leader in enterprise management systems, was exhibiting its latest Intellifuel system aimed at automating the fuel supply chain. Using Android-based tablets, drivers can track upcoming jobs, print invoices and get signatures from clients, all on the provided app. All data can also be accessed and viewed remotely from a control room. With the utmost confidence in its products, PDI claims a demonstrable return on investment, as well as a competitive advantage for end-users. The system is also completely paperless and more environmentally friendly as a result. Systems are easily implemented and have demonstrable cost savings attached.
Archaic paper systems are slowly becoming extinct and PDI is one of many companies making the most of the opportunities for a more succinct and progressive step into the digital world.
Most would argue that full automation is an operational ideal, especially in industries where mistakes are not only costly but also potentially dangerous. Currently, however, a lot of processes on tank farms and other sites are either fully manual or only partially automated. Workers in these industries, some dealing with highly dangerous materials, require protection.
Blakläder, a Swedish producer of protective clothing, was exhibiting its range of protective clothing. Its ‘multinorm’ garments, which include protection against
multiple hazards, are a popular choice with many. New regulations mean that employers need to be able to prove that their workers’ clothing meets protection standards. All Blakläder garments have the certifications embroidered somewhere visibly obvious, so that inspection can take place without anything being removed, or any fumbling to find hidden labels.
Taking a ‘back to basics’ approach to enduser safety, AutoSock was previewing its state of the art, reusable ‘snow socks’. Woven with Kevlar for reinforcement, the slip-on, slip-off ‘socks’ increase wheel traction in the snow and can be used with almost any vehicle. The socks do not require any special training to fit and are held securely in place with elastic. The socks are currently being used by heavy goods vehicles as well as the emergency services.
AutoSock is a deceptively simple idea but its impact can be enormous. The cost of recovering heavy goods vehicles that have lost traction in snow and gone off the road can be daunting, as well as being a timeconsuming operation that is disruptive to business. AutoSock offers a low-cost and practical alternative. AutoSock is certified by TÜV Süd, ÖNorm V5121 and the French winter equipment regulations.
On a more traditional note, but still in the realm of enhancing efficiency, DP Fuel Tank Services, an industry-leading tank cleaning service provider, was previewing its nitrogen-based inerting foam. The company, with 20 years of experience in fuel tank cleaning, has produced an innovative method that can be used in lieu of standard water filling methods in a safe and legally compliant manner.
Nitro-foam inerting is not only cheaper than water filling and subsequent water disposal by tanker, DP says. Nitrogen-filled bubbles force out fuel vapour and then dissolve away to nothing, making the entire process more efficient as it requires only one process instead of two. This approach can be used to allow the re-use of a tank, or to extend its lifespan; it can also be used if a tank needs to be prepared for scrap. Inertia is guaranteed by the company’s gas-freeing specialists, making the entire process safe and reliable.
Next year marks FPS’s 40th anniversary and it is already making plans for a very special FPS Expo. The event returns to the Exhibition Centre Liverpool on 15 and 16 May 2019; full details will be available soon on the dedicated show website, www.fpsshow.co.uk. HCB
the fact and are an auditor’s nightmare. Vault by Chain.io solves this problem by providing a permanent, timestamped fingerprint derived from the data itself. If a single letter in a document or pixel in an image is changed, then the fingerprint is immediately invalid. Adding the Ethereum blockchain to this equation prevents manipulation of the fingerprint itself.”
US-HEADQUARTERED BDP International is to participate as a launch partner for Chain.io’s Vault compliance blockchain for logistics service providers (LSPs) and their customers. Vault, it explains, “is a secure, blockchainbacked digital locker for critical supply chain compliance records”. BDP’s leadership, as part of its “ongoing commitment to implementing innovative solutions”, recognised “the unique advantages offered by Vault and the enhanced security it provides against inquiries made by government auditors months or years in the future”.
“Most of the world’s commerce is managed by text-based electronic documents, like EDI and XML, or scanned images,” says Chain.io CEO Brian Glick. “Unfortunately, those records are all highly susceptible to manipulation after
The Vault system, BDP asserts, “is capable of storing archival-grade, encrypted records within the Chain.io Cloud Execution Platform while simultaneously publishing an unchangeable fingerprint on the public Ethereum blockchain”. The fingerprint, it continues, “is completely anonymous and contains no identifying information about the underlying transaction” but it can be provided to auditors, government agencies and other regulatory bodies “to prove the date and authenticity of any electronic record”.
Publishing the fingerprint on the blockchain, meanwhile, “ensures the integrity of what is stored remains intact; any attempted change is noted and the record invalidated”. Moreover, Vault “is well suited to storing highly critical compliance information,
including sourcing records, environmental chain of custody information, tariff classification support, vendor security audits, general commercial documents and more”.
“As a global logistics provider, BDP seeks to deliver innovative and dynamic service solutions to our customers, with compliance playing a major part in their evolving needs,” says BDP’s chief compliance officer Michael Ford. “The simplicity of integrating Vault with our existing platforms provides our customers with the option of having an additional level of compliance with no extra effort on their part.”
“Seeing blockchain solutions come to fruition with immediate, real-world use cases is a watershed moment for technological progress and – as Vault demonstrates – is having an immediate and powerful influence on our industry practices,” adds BDP’s chief information officer Brian Kautz. “These solutions are here today and the onus is on us to provide our customers access to these impactful product offerings.”
Shippers, LSPs and trade software providers can all integrate their existing systems with Vault using what BDP describes as “only a few lines of code to push documents to a secure FTP site”. Furthermore, Vault does not require “all-or-nothing engagement” but instead “allows companies to selectively participate with customers and documents of their choosing, easing into the blockchain without disrupting existing business processes or retraining IT staff”.
Meanwhile, in other news, Chris LoPriore has joined BDP as its new vice-president, global sales and marketing. “We are pleased to welcome Chris to the BDP International organisation,” says president and COO Mike Andaloro. “Based on his diverse background that is deeply rooted in customer relationships, securing new business opportunities and optimising process improvements, Chris will be an ideal fit to continue growing BDP’s service and solutions offerings to benefit the needs of our customers.” HCB www.bdpinternational.com www.chain.io
BLOCKCHAIN • BDP HAS TEAMED UP WITH CHAIN.IO TO OFFER LOGISTICS SERVICE PROVIDERS A VALUABLE BLOCKCHAINBACKED SERVICE FOR COMPLIANCE RECORDS
“AGILITY IS ACCELERATING a fast-moving transformation to establish itself as a digital leader in the logistics industry,” says Tarek Sultan, CEO and vice-chairman of Kuwaitheadquartered logistics giant Agility. “We are rapidly introducing new digital products, aggressively piloting and pioneering new logistics models and technologies and re-engineering our systems for speed and competitive advantage. We want to identify technology that makes logistics more efficient and lowers costs for customers.”
A prime example of this commitment is the recent launch of Shipa Freight, which Agility describes as “the first fully integrated online freight service that allows users to get rate quotes and book, pay and track ocean and air shipments around the world”. Moreover, Shipa Freight, it says, “provides instant, no-obligation rate quotes from the countries that account for 95 per cent of
global trade and allows users to manage their international shipments with a simple, easy-to-use tool accessible by desktop, laptop, tablet and mobile app”.
Commenting on the launch, Sultan states: “Shipa Freight is a simple, technologydriven answer for small and medium-size businesses trying to take the complexity out of their international shipping. It gives them the transparency, flexibility, competitive pricing and customer service that the industry offers only to multinationals and high-volume customers.”
Supporting all this, Agility reports that a recent survey it conducted of 800 small and medium-size firms found that one of the major barriers they face in terms of increasing international trade is the complexity associated with compliance, customs requirements and cross-border bureaucracy.
Shipa Freight, the company says, “helps customers overcome these issues by providing a compliance database with information on documents required on all trade lanes, helping them navigate the legal and regulatory requirements that are obstacles for many small businesses”.
Moreover, the new service is “backed by Agility’s global network of more than 22,000 experienced employees in 500 branches and over 100 countries”. This, it continues, “gives customers the support of a trusted global network and allows small and medium-size companies to access the world’s growing markets”, with Agility customer support available around the clock, seven days a week “to help them book and manage their shipments or to get rates for routes not quoted online”.
“Shipa Freight’s digital platform allows users to complete a shipment completely online,” explains Shipa Freight CEO Toby Edwards. “This includes shipment booking, a range of payment options and online tracking, which have not been widely available for small and medium-size businesses until now.”
“Shipa Freight is unique among online freight services,” Sultan adds. “It offers both air and ocean, including Full Container Load (FCL) and Less than Container Load (LCL) options. It provides users with the ability to manage their freight from start to finish via quote-book-pay-track features and 24/7 customer service. And it makes use of Agility’s existing global network and scale, which means it’s got built-in flexibility, expertise and deep understanding of how to move freight around the world.”
Meanwhile, Agility has announced a firstquarter net profit of KWD 18.9m ($62.5m) from revenues worth KWD 371.8m. This compares favourably to respective prior-year figures of KWD 14.6m and KWD 110.8m. EBITDA rose 22.6 per cent over the period to KWD 37.7m. “Agility continues to deliver results,” says Sultan. “Our double-digit EBITDA growth affirms the company’s momentum over the past three years. The Global Integrated Logistics (GIL) business continues to drive profitability gains through strong performance in Ocean and Air Freight, in addition to improving its efficiency.” HCB www.agility.com
NETHERLANDS-HEADQUARTERED BROEKMAN Logistics and Heylen Warehouses have together begun construction of a new logistics facility on the former DSM Pharma Chemicals site in Venlo on the Dutch/ German border. Broekman reports that it will use the facility for storage, logistics “and assembly activities for various products”, of which around 50 per cent will be classified as dangerous goods.
While the total warehouse surface area will come to 53,000 m2, the facility will also boast “more than 10,000 m² of mezzanine floors” and some 2,500 m2 of office space. No scheduled completion date has yet been given, but Broekman says the new site will be developed in phases, with employment rising “in parallel from 150 jobs to 300 in the end”.
“In Broekman Logistics, we have found a partner to build a new logistics facility and to contribute to our growth strategy in the Netherlands,” says Heylen CEO Ralph Caspanni. “With this triple-A visibility location, we’ll be offering the best possible accessibility by road, water and rail.”
“The Venlo site,” adds Willem Jan van Amersfoort, Broekman’s managing director, warehousing and distribution, “is ideally located, with the barge terminal and rail terminals virtually just around the corner from our terrain. The site is easily accessible from the A67 (Belgium – Germany) and the A73 (Nijmegen – Roermond). The expansion of our warehouse capacity in Venlo forms part of our growth strategy in the Netherlands.”
The news comes shortly after Broekman officially opened a new ADR warehouse in
the Maasvlakte industrial area of Rotterdam’s Europoort. “With the new warehouse at the Maasvlakte, customers can store both hazardous and safe products at a strategic location near the container terminals,” the company says. Featuring “more than 35,000 m2 of warehouse capacity”, the new facility brings Broekman’s total warehousing capacity in the Netherlands to over 310,000 m², of which one third has been specifically designed for the storage of dangerous goods.
Moreover, the opening afforded Broekman the opportunity to unveil its new BLUE4C concept, with Blue standing for Broekman Logistics Unlocking Europe combined with the four Cs of Coordinates, Combination, Customised and Compliant. As such, the new concept, it says, addresses four recent trends - “shifting modalities”; “rising product-
market combinations that require different warehouses”; “changing safety standards”; and “the globalisation of production and logistics”.
“BLUE4C perfectly complements our growth strategy in the Netherlands,” Amersfoort says. “We aim to be and remain the market leader in the field of ADR storage. We also offer warehousing capacity at strategic locations in order to continue to meet our customers’ needs.”
On the management front, Cor de Man has been named general manager of both Broekman Logistics’ Forwarding business in the Netherlands and its specialised breakbulkrelated Project Logistics operations.
“My passion is in the transformation of organisations to become and remain successful in a dynamic and competitive environment that requires a high level of client centricity,” he says. “Broekman Logistics has all the ingredients needed to succeed in this market. It boasts a great mixture of quality people and strategic assets, key elements for a logistic service provider and mandatory enablers towards the provision of optimised supply chain solutions. It is with considerable enthusiasm that I joined the team that supports Broekman Logistics in realising the transition towards a client-centric global supply chain solution provider.” HCB www.broekmanlogistics.com www.heylenwarehouses.com
FOR ORGANISATIONS OPERATING in highly regulated industries, such as chemicals, nuclear or oil and gas, the management of by-products and wastes is a key concern. In order to comply with domestic and international guidelines, wastes must be managed safely and responsibly to prevent damage to the environment and the health of employees and the general population.
The nuclear industry in particular is highly regulated, with all radioactive waste
produced during the generation of nuclear power required to be managed as hazardous material. According to the World Nuclear Association, this means waste must be isolated or diluted such that the rate or concentration of any radionuclides returned to the biosphere is harmless.
“For nuclear sector operators there are no second chances when it comes to ensuring waste and by-products are safely managed,” Bjoern Stolz, managing director of Thielmann WEW says. “Accidents can have serious consequences that can have knock-on effects for years, if not decades. For this reason, all equipment used to store and transport these products must be manufactured to stringent standards.”
The different types of radioactive waste need to be dealt with, loaded, stored and transported in different ways. Low-level radioactive waste (LLW), i.e. waste with a radioactive content that does not exceed 4 giga-becquerels per
tonne (GBq/t) of alpha activity or 12 GBq/t beta-gamma activity, does not require shielding during handling and transport.
To support its customers active in this sector, Thielmann has developed a range of specialist containers for the short and long-term storage of Class 7 liquid products (including LLW). As the cost of managing and disposing of waste is a key driver for customers operating in this sector, Thielmann aims to enhance logistics simplicity and reduce lifetime costs.
“We do this by substituting road tankers with proven intermodal technologies, so that the tank system is separated from the trailer and fitted within a standard ISO frame that is compatible with load handling systems,” Stolz says. “The hook-arm system permits rapid prime-mover redeployment and guarantees interchangeability with other civilian vehicles throughout the supply chain.”
The tank’s double-shelled module solution integrates systems to prevent settlement of ∂ and ß particulate matter, ensure accurate records of products handled are kept, and provide data logging for customer visibility.
The unit is self-filling via a vacuum pump, as this reduces the reliance on moving parts as in the case of a traditional pump, and contact with the waste product is kept to an absolute minimum. Fitted with an industrial standard self-priming pump, flow rates of up to 45 m³/h can be achieved, delivering 5.5 kW at 400 V. The system can also be integrated with an air-activated carbon filter and the valve opening/pump operation sequence is controlled by a PLC controller.
Tanks can be integrated with accessories such as electronic overfill protection, digital filling level indicator and self-retracting power cord reels, and the system can be managed via a fully integrated control box with ‘fool proof’ operation.
As with all Thielmann tank containers, every aspect of each system can be engineered to match customer requirements, to ensure that all materials, no matter how hazardous, can be safely managed throughout the supply chain. HCB www.thielmann.com
GERMANY-BASED LOGISTICS giant Hoyer has once again posted record financial figures, with group revenue in 2017 up by 1.2 per cent over 2016 at €1.20bn. Earnings before taxes rose from €40.4m last year to €40.6m, with a return on sales of 3.4 per cent. Group operational cash flow rose from €65.3m to €75.2m.
“More than 6,400 employees worldwide ensured a result in 2017 that is again above the sector average. We are very pleased with this closing figure,” says Thomas Hoyer, chairman of the Advisory Board of the Hoyer Group.
These record figures follow on from a similar story in 2016, when Hoyer celebrated its 70th anniversary with a 0.3 per cent increase in turnover and its second-highest pre-tax profit in its history. At that time, Thomas Hoyer stressed the importance the group places on investing for the future, saying: “The size of our annual investments is astonishingly high compared to other family businesses in the logistics market, as well as in manufacturing or consumer goods industries. People often talk to me about this, but it is a particular feature of bulk transport and its special requirements. These major investments will prove to be good decisions in the medium and long term.”
Those investments are continuing.
Over the past year Hoyer has strengthened its operations in North America and Asia and is now active in more than 115 countries around the world. It also last year acquired CCR, a France-based lessor of intermediate bulk containers (IBCs) and small portable tanks. That deal catapulted Hoyer to the very top of the IBC leasing field, CCR’s fleet of more than 14,000 units adding to Hoyer’s existing IBC fleet of more than 27,000 units. Along with further additions, Hoyer now boasts an IBC fleet that exceeds 43,100.
The other focus of Hoyer’s investment has been in its digitalisation strategy. The central element is the Smart Tank, which enables products in tank containers to be monitored by using innovative sensors. Over the course of 2017 Hoyer invested some €90m in innovative technology, continuing to equip its tank container fleet with complex telematics systems.
Ortwin Nast, CEO of the Hoyer Group, says: “We see innovation as an opportunity to fulfil our customers’ wishes better than others, and to design our processes to be more efficient, secure and economical.”
Hoyer says it aims to set new standards in transport and in networking customers, suppliers and goods in transit. To achieve this, the company has worked in partnership with Intermodal Telematics BV (IMT) to develop the appropriate hardware and software. This smart logistics system enables seamless monitoring of goods transported in tank containers at any defined point in time for Hoyer’s customers. This includes not only monitoring position but also the status of the transported goods with regard to their pressure, temperature, density parameters and filling level. A non-invasive filling level measuring system developed exclusively for Hoyer will solve a large number of technical challenges.
Hoyer started using its smart technology early in 2016, initially on a local basis for Bayer in Dormagen. Late last year it started working with Bayer in the US, ahead of a global roll-out. HCB www.hoyer-group.com
Raben Group has formally opened a new headquarters building and depot for its Czech and Slovak operations in Nupaky, just outside Prague, coinciding with the 10th anniversary of its presence in the countries. The new logistics centre (above) covers 27,000 m2, of which 20,000 m2 is warehousing space, including temperature-controlled areas.
The logistics centre is strategically located in CTPark Prague East, which has direct access to the D1 motorway. “I appreciate a lot the trust of Raben, which has chosen CTP as a partner for its further growth,” says Remon Vos, CEO of CTP. “CTPark Prague East is strategically located and thanks to its excellent accessibility to Prague (20 km), the airport (35 km), Dresden (170 km) and Brno (187 km), and the high quality of this built-to-suit solution, Raben also gains the advantage of fast transport service which plays an important role for logistics companies.”
www.raben-group.com
Hoyer’s Supply Chain Solutions business unit has expanded the range of services it provides for Covestro at its site in Shanghai. Formerly handling methylene diisocyanate (MDI) logistics, Hoyer is now also working for Covestro’s coatings, adhesives and specialities (CAS) division.
Services provided to CAS include the heating of tank containers prior to unloading, loading palletised finished goods and tank containers, filling IBCs and drums, and handling wastes for collection.
“Due to our experience with Covestro and the handling of many different products, we were able to start up the service quickly and reliably,” says Michelle Ding, project manager SCS Asia/Pacific at Hoyer. “The existing MDI logistics division is our advantage and makes it possible for us to also react to short-term peaks in the filling of finished goods and to deploy appropriately trained personnel in both areas.”
Hoyer is employing 24 people on the contract under the management of Jeffrey Xu, operations manager, SCS. www.hoyer-group.com
Stolt Tank Containers has reported operating revenues of $132.5m for the company’s first quarter ending 28 February, down slightly on the figure of $136.9m recorded in the previous period. Volumes held steady but freight revenue per shipment fell by 2.6 per cent in line with seasonal patterns in the product mix. Operating income slipped from $17.0m to $16.2m.
Niels G Stolt-Nielsen, CEO of parent Stolt-Nielsen Ltd, is happy with the results, which he terms “stronger than usual” in what is normally STC’s weakest quarter, and is optimistic that global tank container demand is continuing to grow. www.stolt-nielsen.com
Denmark’s Nordic Transport Group (NTG) has received full regulatory approval to acquire the Switzerland-headquartered Gondrand Group, “a full-service transportation and logistics provider” with 60 offices across seven countries and which closed its 2017 books with revenues worth €221.6m.
“It is very satisfying that all regulatory approvals now are in place for this strategically important acquisition,” says NTG chairman Morten Mathieson. “Gondrand is a perfect match for NTG in terms of business activities and geography. Not only do we add significant scale to our existing business – in an industry where scale is increasingly critical – it also paves the way to continue on our growth journey and expand our geographical footprint in both Europe and Asia.”
Gondrand is currently finishing construction of a new chemical storage warehouse and distribution facility in Moerdijk, the Netherlands. It has more than 140,000 m2 of warehouse space
around the world, bringing specialist expertise and a much bigger geographic footprint to NTG’s operations. www.ntgnordic.nk www.gondrand-logistics.com
Hakan Bicil (above) has been chosen as the next CEO of Imperial Logistics International; he will take over from Carsten Taucke, who last November announced his intention to stepping down from the management board on 1 September.
Bicil was recently chief commercial officer at CEVA Logistics and has held senior management positions at Panalpina, Toll Group and Kuehne & Nagel. “We’re delighted to have gained an experienced leader in Bicil, whose immense supply chain expertise makes him the ideal choice to drive our growth strategy in key European markets,” says Marius Swanepoel, CEO of Imperial Logistics. “Bicil is a skilled strategic thinker with a passion for true client centricity. He will be key in delivering customised solutions that keep our clients competitive and relevant in a demanding environment.” www.imperiallogistics.com
Trifleet has begun leasing cryogenic tank containers. So far it has a fleet of 20 units of 42,000 litres capacity, designed for the transport of LNG. Trifleet’s new cryogenics division is also able to provide additional equipment, such as cryogenic pumps, hoses, valves, installation systems and related technical support through the existing infrastructure, processes and expertise of its organisation.
Launch of the LNG tank service follows training of the management team that supports Jaap Kuijpers Wentink, who was engaged last year as director of cryogenics. In March this year five Trifleet underook the basic training course ‘LNG as Fuel’ offered by the STC Group, a worldwide operating educational and research institution for the shipping, logistics, transport, and process industries. The training covered the specific characteristics of LNG and the associated procedures when working with LNG and other highly flammable fuels. For this they also dealt with practical situations, such as bunkering and incident management. www.trifleet.com
Talke is adding 150 state-of-the-art Mercedes Benz Actros tractor units to its fleet; the new cabs will arrive over the next three years at its European facilities, with the first 70 due this year. The tractors are equipped with the latest generation of safety assistant systems and the cabs feature above-average levels of comfort, making them especially appealing workplaces for the drivers.
“Safety has always been our top priority. Our customers quite rightly expect and trust that Talke always uses the appropriate
equipment for transporting and handling their goods. Acquisition of the new vehicles ensures we remain faithful to our principles and keep our fleet up to date”, explains Peter Viebig, transport director at Talke.
Talke’s German operation, meanwhile, has been re-certified as a waste disposal specialist for another year. The company has held a licence for the professional transport of production waste continuously since the German Waste Disposal Specialist Regulation came into force in 1997. Talke’s fleet, equipment and storage facilities were audited by TÜV Rheinland.
Talke mainly transports wastes from chemical metal processing facilities, along with wastes associated with acid and alkali production and disused electronics. Last year the company moved more then 23,000 tonnes of wastes.
“Much of the waste so classified contains valuable raw materials that are recycled or utilised in another way. Since these substances are often hazardous, they require professional handling,” Viebig explains. “We offer our customers disposal transportation to the same high quality and safety standards and with the same transparency as when transporting finished products.” www.talke.com
THE EUROPEAN ASSOCIATION of Chemical Distributors (Fecc) meets this month for its Annual Congress at the Hyatt Regency Nice Palais de la Méditerranée Hotel on the city’s famous Promenade des Anglais and will once again give delegates much to think and talk about. “During the Fecc Congress, we will discuss digitalisation in the chemical distribution supply chain, analyse the best practices in sustainable supply chains, the trends and challenges in raw materials and discuss the future trends in the pharma distribution supply chain,” says Fecc director general Elisa Setién.
“During last year’s Fecc Congress, the chemical distribution industry explored the potential of digitalisation, exchanged
views on how to find value in social media, discussed cybersecurity and analysed the next generation of e-commerce in chemical distribution,” she continues. “Building on the success of last year’s Congress, this year we will pay special attention to blockchain technology, its potential uses in logistics and manufacturing, and we will kick-start a discussion on whether blockchain-enabled supply chain solutions could be integrated in the current business models to improve efficiencies and reduce costs for the chemical distribution industry.”
Open to both Fecc members and nonmembers alike, the Fecc Congress, Setién
states, “is the most important platform for chemical distributors to exchange experiences” while also discussing current market trends and expectations and the vital role chemical distributors play in the overall chemical supply chain. Thus, the Congress will offer “unparalleled networking opportunities” for the more than 200 highlevel chemical stakeholders that are expected to attend this year.
“Fecc aims to help chemical distributors navigate the regulatory environment in which they operate, as well as to discuss the emerging business environment in order to enable companies to consider how their business models could evolve to remain competitive,” she says. “Fecc enables members to be informed at an early stage about emerging regulatory changes, remain updated on trends in the sector and having the possibility to discuss the key issues with the industry experts in the frame of the Technical Committees [see box].”
In terms of the general European market, 2017 “was a good year for chemical distribution”, Setién reports, adding that so far this year “the months ahead look positive for the sector” as well. However, the
future is unwritten and thus the Association is well aware that there is no room for complacency. “At Fecc, we remain attentive to how geopolitical uncertainties will impact business,” she says. “At the European level, we monitor closely the evolution of the Brexit political discussions as they will impact the chemical supply chain and imply adaptations in our business. However, we remain cautiously confident that chemical distributors will be agile enough to adapt to the new situation which will emerge in 2020 after the transition period.”
December 31 2020, when the Brexit transition period ends and the UK bids a full farewell to the EU, is not the only date that’s been on the Association’s mind of late, with 31 May this year also of major importance as the final deadline under the EU’s Registration, Evaluation, Authorisation and Restriction of Chemicals (REACH) regulation. “Although the last REACH registration deadline has kept us busy and [dominated] most of the conversations these last months, for chemical distributors the real challenge remains the huge amount of information that has to be exchanged along the supply chain,” Setién says.
“Chemical distributors receive diverse information from different suppliers of the same substance, which they have to aggregate to provide their customers with a unique and consistent set of information. In 2017, Fecc published new guidelines and in January 2018
hosted a technical workshop on digitalisation of supply chain information to ensure that members are well equipped to cope with the challenge,” she explains.
Furthermore, in the next few months, Fecc will also “lead an action” of the new Exchange Network on Exposure Scenarios (ENES) Work Programme 2020. Published this past May by the European Chemicals Agency (ECHA), this updated work programme seeks to implement tools to improve chemical safety assessment and communication across the supply chain and consists, in ECHA’s words, of “24 actions until 2020 [that] will help registrants, distributors, formulators and end users to ensure the safe use of chemicals”. In order to do this, the Fecc action, Setién says, will focus on promoting “cooperation among registrants of the same substance to increase the consistency among the safe-use information communicated down the chain”.
Given the increasingly complex regime in which chemical distributors find themselves operating, it should perhaps come as no surprise that REACH is not the only blip on the Association’s regulatory radar. “Besides the ongoing work on REACH, making the implementation of the new requirements to notify hazardous mixtures to poison centres under the Classification, Labelling and Packaging Regulation (CLP) workable for chemical distributors continues to keep the Association busy,” Setién reveals.
But that’s not the only matter either. “Security is also very much in focus at Fecc these days, with the new Commission proposal for a regulation on [explosives precursors] and the continuous efforts of the supply chain to increase its robustness,” she continues, noting that in the second half of this year “the evaluation of the drug precursors regulation will also take centre stage”.
Furthermore, with ever more chemical distributors “very active in life sciences”, Fecc has also stepped up its efforts in terms of the food and feed sectors, strengthening “its collaboration and exchanges with key downstream associations” working in these fields. Meanwhile, with regard to the pharma sector, “chemical distributors
remain committed to the implementation of Good Distribution Practices (GDP) in the supply chain”, with Fecc hosting a technical workshop this past May “in order to analyse in depth the challenges and tools for the pharmaceutical excipients supply chain”. HCB www.fecc.org
Headquartered in Brussels, Fecc describes itself as “the voice of the chemical distribution industry in Europe”, a sector that currently employs more than 30,000 people and commands annual sales of around €28bn. Boasting “a growing membership of companies and national associations”, Fecc today represents around 1,600 companies, of which many are small and medium-sized enterprises (SMEs). Together, these member companies source, develop, market and distribute “a wide range of specialty chemicals and ingredients to over 1m downstream users” drawn from a broad spectrum of industries, ranging from the automotive, electronics, paints and construction sectors to pharmaceuticals, cosmetics, food and nutrition, each of which has its specialised needs.
Promoting various industry initiatives, such as Responsible Care and Good Trade and Distribution Practices, Fecc advocates at both the national and international level while continually monitoring market and regulatory changes on behalf of its members. In order to do this, the Association maintains a number of Technical and Working Committees comprised of industry experts, viz the Responsible Care (RC) Committee; the European Single Assessment Document (ESAD) Committee; the Logistics (LOG) Committee; the Precursors Committee; the Life Sciences Committee; the Safety, Health & Environment (SHE) Committee; and the International Trade Committee.
WHITCHEM, A STAFFORDSHIRE-based distributor of chemicals, minerals and polymers, has landed the UK Chemical Business Association’s (CBA) 2018 Responsible Care Award, which the Association describes as recognising “excellence by its member companies in the operation of its industry-wide programme to promote year-on-year improvements in health, safety, security and environmental management”. Moreover, Whitchem was also named as the winner of the chemical distributor with an operating site category. “The citation for the award highlights the importance of Responsible Care and product
stewardship in all aspects of the company’s business in addition to its strategy for continuous operational improvement,” CBA says.
Dakram Materials, a Bedfordshirebased distributor of inorganic metal-based chemicals, landed the Community Interaction Award. “This award aims to recognise a major contribution to community interaction made by a company, one of its employees or a group of employees,” the Association explains.
“Despite being a smaller company, Dakram Materials and its employees have fostered a long-term engagement with a wide range of initiatives in the local community as well as charitable projects overseas.”
The Awards were presented before an audience of more than 1,100 members and their guests at the CBA’s Annual Lunch his past April at the Grosvenor House Hotel in London, where, in addition to the distribution of gongs, concerns were also expressed regarding the UK’s ability to secure continued access to EU markets once the country leaves the bloc as a result of the 2016 Brexit referendum. While the CBA states that it “has no desire to engage with the politics of Brexit”, it nonetheless describes itself as being “focused on accurately representing the views of its member companies and offering an evidence-based position on the potential impact of the UK leaving the EU”.
To this extent, while addressing attendees to the Annual Lunch, the Association’s chairman, Mottie Kessler MBE, stated: “Our member surveys show a clear preference for the UK remaining part of the Single Market and Customs Union. They also show that a significant number of member companies are planning to create subsidiaries in other EU member states or have already done so.”
“The commercial rationale behind these decisions is clear,” Kessler continued. “For companies trading with EU member states, regulatory compliance is the key to market access. Authorities in these markets decide the nature and extent of the compliance required. Compliance is non-negotiable. Failure to comply is a barrier to market access. Without market access, there is no trade.”
“CBA warmly welcomed the commitment in the Prime Minister’s Mansion House speech to explore ‘associate membership’ and pay for continued access to the European Chemicals Agency (ECHA) and, by extension, to ensure that UK chemicals remain within the provisions of REACH and other key aspects of the industry’s existing regulatory framework,” he said. “This, of course, is an intention, not a certainty. Like most other business associations, CBA remains concerned about the ongoing uncertainty and its potential impact on commercial transactions, investment and jobs.”
“It is already clear that some Europeanbased companies are repatriating products
from the UK to guard against the impact of Brexit. Time is short. Decisions have to be made. Our industry requires a higher level of certainty on the commercial and regulatory framework on which its future depends,” he concluded.
CBA has also released the findings of its latest on-line Trends Survey, which was conducted during the two-week period of February 26 to March 12 this year and which is based on responses from 51 member companies. The Survey asks companies to provide information on orderbooks, sales, sales margins and employment on a ‘better–worse–same’ basis. To measure short-term trends, the analysis ignores responses answering ‘same’ and instead focuses on the positive or negative balance provided by the difference between the ‘better-worse’ responses.
“Current orderbooks and sales seem to be gathering some momentum, but the positive balance of responses is still only half the level reported in June 2017,” CBA says. “Though still representing a positive trend, member companies are less optimistic in respect of sales over the next three months. Current and future sales margins, the most
volatile aspect of these surveys, remain under pressure. The trends for industry employment and training levels are firmly positive.”
Breaking this down, CBA reveals that in terms of orderbooks, there is “a positive balance of +27 per cent”, which is “almost double” the 14 per cent level reported in November 2017. However, the Association notes, this figure still “remains low by the standards of previous surveys”. Nevertheless, when asked to compare their current sales volumes with the preceding three months and indicate their expectations for the next three months, the results were largely positive. “Current sales volumes continue to show a positive balance of +29 per cent, an improvement to the positive balance of +11 per cent reported by CBA’s last survey,” it says, adding that “future sales remain in positive territory at +18 per cent”, being “marginally higher” than the +14 per cent reported in November.
When asked to compare their current sales margins with the preceding three months and forecast their trend over the coming three months, a somewhat mixed bag emerged. “Current sales margins have turned positive, recovering from the negative balances reported in the last survey, but only to the extent of a positive response of +6 per cent,” CBA reports. Furthermore, “little improvement is expected over the next three months with member companies reporting a
positive balance of just +4 per cent”.
That said, when polled as to whether their employment levels and investment in training would be higher, lower, or remain the same over the next three months, companies remained clearly upbeat, with respective positive balances of +27 per cent and +48 per cent being reported.
Representing the UK’s independent chemical supply chain, CBA maintains a membership that includes chemical distributors, traders and warehouse operators along with logistics and transport companies. Moreover, its members, the majority of which are small and medium-sized enterprises (SMEs), “are the main industry interface with thousands of UK downstream chemical users”. Together employing more than 8,700 people, these companies distribute, pack and blend more than 4m tonnes of chemicals per annum with a market value of “almost €3bn” with CBA logistics members likewise handling an equal volume of chemicals each year.
Given the often very hazardous nature of the products at stake, the Association retains a strong and clear focus on safety. As such, it “was the first supply chain organisation in Europe to launch Responsible Care some 25 years ago” and has “published aggregate performance data for its member companies each year since 1993”. On top of this, compliance with Responsible Care has been a mandatory requirement of membership since 2002. HCB www.chemical.org.uk
BRENNTAG HAS COMPLETED its acquisition of a 65 per cent stake in India’s Raj Petro Specialities, with the German distribution giant set to acquire the remaining 35 per cent via a second tranche after a period of five years, with a possible extension of one to two years. In the meantime the business, which distributes its own-blended brands of petroleum-related products to a diverse range of industries in India as well as other countries in Asia Pacific, Africa and the Middle East, will be operated as a joint venture. Headquartered in Mumbai and Chennai, Raj, Brenntag says, is expected to close its 2017/18 books with total sales of around €180m.
“For Brenntag, the acquisition of Raj is a further step into the Indian chemical distribution market, which is the seventh largest globally for chemicals and third largest for lubricants,” says Brenntag CEO Steven
Holland. “Raj’s existing product portfolio and market presence, capability of its infrastructure and strategic locations make it a compelling investment target to expand our footprint not only in India, but also in other Asian Pacific countries, in Africa and the Middle East.”
“Raj has the widest product portfolio among its national competitors and a strong market presence with its own blended brands,” adds Henri Nejade, a member of the Brenntag Management Board and CEO of Brenntag Asia Pacific. “Its facilities are strategically placed at the west and south-east of India, in proximity to major ports, offering blending and repackaging capabilities, as well as a strong application development team.
The cooperation offers Brenntag diverse potential for synergies and future growth.”
Also in Asia, Brenntag has been appointed as ExxonMobil’s authorised distributor in Vietnam. Products covered under the deal include Mobil lubricants for vehicles and industrial applications, specifically Mobil 1
and Mobil Super for motorcycles and cars; Mobil Delvac and Mobil Delvac 1 for trucks, buses and special vehicles; and Mobil SHC and Mobil grease for industrial uses. “The demand for lubricants in the Vietnam market is increasing rapidly and [because of] those customers still demanding Mobil products, we have decided to return to the Vietnam market,” says ExxonMobil AsiaPacific CEO Yasser Al-Azzawi.
Over in the US, meanwhile, Brenntag has inked a deal with StanChem Polymers for the distribution of emulsion polymers to customers operating within the local adhesives, coatings, elastomers and sealants (ACES) market. “The StanChem product line of acrylics, styrene-acrylics and vinyl acetate acrylics resin emulsions is an exciting addition to our ACES portfolio,” says Brenntag North America’s ACES director Ted Davlantes. “Representing StanChem nationally will enable our team of technical sales professionals to meet the demands of our customers looking to develop new products and reformulate existing waterborne formulas. The addition of the StanChem line underscores Brenntag’s commitment to investing in key strategic principal partnerships and providing differentiated value to our customers.”
In other news, Brenntag-owned Multisol has unveiled a new fuels laboratory in Jankowice, Poland to serve the needs of customers across Europe, the Middle East and Africa. “The face of refining is changing and our laboratory is further proof of Multisol’s market knowledge and readiness to support its customers,” says Graham Eden, Multisol’s commercial director, fuels and specialties. “Environmental standards, such as IMO Marpol legislation, will force refiners to make changes within their operations. Multisol and Brenntag offer the technical knowledge and Infineum Fuel Additives to navigate these significant changes. Infineum additives provide our customers with an opportunity to configure their refinery to become more efficient and increase refining margins.” HCB www.brenntag.com www.rajgrp.com www.multisolgroup.com
ABOVE - HENRI NEJADE: “DIVERSE POTENTIAL FOR SYNERGIES AND FUTURE GROWTH”
executive vice-president of chemicals. “This agreement serves as another example of the strong relationship that we already share with Solvay across a broad range of markets.”
NEXEO SOLUTIONS HAS expanded its partnership with Solvay to include the distribution of a portfolio of products for the home care, personal care and agriculture markets, including Cationic Activator 671, Mackadet® EQ 112, Mackalene® 426, Mackconditioner CBC Flake, Mackpearl® 202, Miranate® LEC-80, Polycare® 133 and Rhodoclean® ASP among others. Nexeo reports that Solvay will now no longer offer these products for sale in the Americas, with Nexeo becoming the sole commercial source for these products there.
“Solvay has very attractive technologies that will help us support customers and drive product development in home care and personal care as well as agriculture,” says Joey Gullion, Nexeo’s vice-president of specialty chemicals. “It is a very attractive segment of chemistries that support products from shampoos and hair conditioning all the way into floor care. This breadth of products offers Nexeo a unique chance to interact with our customers across broad market fields. We are eager for our experienced sales and technical teams to work with our customers and help them formulate complete solutions and products, with reliable chemistries across [the] value chain and at varied price points.”
“This agreement continues our strong progress of deepening our portfolio in key markets as part of our overall chemicals strategy,” adds Brian Herington, Nexeo’s
Indeed, the deal comes shortly after Solvay selected Nexeo to distribute its home care surfactant and polymer products across North America. “We are pleased to deepen our relationship with Solvay by adding their market-leading home care products to our portfolio,” Gullion says. “The addition of home care surfactant and polymer chemistries complements Nexeo’s portfolio of products sold into the home care market. We are excited about the development opportunities the products will bring to our valued customers.”
But Solvay certainly isn’t the only company to have expanded its relationship with Nexeo of late, with DSM also appointing it to undertake the distribution of its All-Q™ Plus, BeauPlex VH®, Amphisol®, Radiance CR and Parsol® personal care lines and vitamins across the US. “DSM is recognised today as a world leader in the manufacture and supply
of ingredients for some of the world’s bestselling beauty products,” Nexeo says. “Its scientific backbone, combined with local consumer insights, results in innovative and transformational ingredients. Selecting a top distribution partner is an integral part of DSM’s channel strategy to build brands and benefit the end consumer.”
Meanwhile, Nexeo has also signed a deal with BASF to sell and distribute speciality acrylic and methacrylic monomers across the US and Canada. “At BASF, we continually look for ways to improve our customer’s experience when sourcing the raw materials we supply,” says Heather Remley, BASF’s senior vice-president, petrochemicals, North America. “We selected Nexeo Solutions to be our channel to the market because of their focus on the specialty sales process, their in-house technical capabilities and their vast logistical platform and market reach.”
“BASF’s specialty acrylic monomers are highly complementary to both our existing customers and the markets that we serve,” Gullion says. “Nexeo will carry forward BASF’s strategy of excellent customer and technical service while utilising best-in-class inventory management practices and multiple stocking points.” HCB www.nexeosolutions.com
CONTRACTS • NEXEO SOLUTIONS HAS BEEN CEMENTING ITS PLACE IN THE US CHEMICAL DISTRIBUTION SECTOR WITH A SERIES OF HIGH-PROFILE DEALS WITH MAJOR PRINCIPALS
FRANCE’S SAFIC-ALCAN has established a new Russian subsidiary. Based in Moscow, Safic-Alcan Rus will service the needs of customers from the industrial rubber and plastics manufacturing sectors across Russia and the CIS. The new subsidiary will manage warehousing locally, with Mikhail Shekhirev named as the new arm’s sales manager. A graduate of the Moscow Business School, Shekhirev will be responsible for the new subsidiary’s development and boasts, the company says, “a long experience in sales with major rubber and plastics players”.
“We are happy with the opening of this new subsidiary in Moscow,” says Safic-Alcan CEO Philippe Combette. “This initiative will enable us to support our existing local customers and to be present in high potential markets while enhancing our distribution network in eastern Europe.”
Meanwhile, Safic-Alcan has also expanded its long-standing agreement with Chemours for the distribution of Viton™ fluoroelastomers and Viton™ FreeFlow™ processing aids to cover the whole of Europe, the Middle East and Africa (EMEA). With numerous applications within the automotive, aerospace, chemical and hydrocarbon processing sectors, Viton fluoroelastomers, Safic-Alcan reports, “are high-performance elastomers with good heat and chemical resistance”. Meanwhile, Viton FreeFlow, it continues, “stands for a family of processing aids for the extrusion of films or wire and cable harnesses” that “help reduce die build-up, allowing processing to continue with consistent surface finish without impact on properties or performance”.
“We are delighted to extend our long-term partnership with Chemours to the whole EMEA region,” Combette says. “This is a great opportunity for the Safic-Alcan Group to offer on a larger scale this state-of-the-art product range to our customers.”
“We value our strategic relationship with Safic-Alcan, [which] has played an essential role in enhancing customer services in the rubber industry,” adds Chemours’ global business director Marcel Van Den Noort. “We are convinced that our customers will benefit from this change.”
At the same time, Safic-Alcan has also been appointed by Plant Advanced Technologies (PAT) to distribute its Spiraea Exudactive® C plant-based cosmetic ingredient across 20 different countries, including Bulgaria, the Czech Republic, Germany, Hungary, Italy,
Poland, Portugal, Romania, Serbia, Turkey and the UK. Spiraea Exudactive C, Safic-Alcan reports, is prepared using the PAT Plant Milking® process, a “patented technic” that produces “highly concentred actives under conditions where [the] plant’s roots are exploited in a non-destructive way” without the need to use pesticides.
“Having an efficient distribution network in Europe is crucial to market PAT’s nonexclusive products,” says PAT executive director Paul Hannewald. “We are very pleased to work with Safic-Alcan, whose team has demonstrated pertinence for promoting our first active ingredient.”
“We are happy to have been selected by PAT and to represent a key player in the cosmetics industry,” Combette states. “This new partnership will allow us to distribute natural and unique ingredients that are highly complementary to Safic-Alcan’s portfolio and to respond to our customer’s needs for natural innovative solutions.”
Headquartered in Paris-La Défense, Safic-Alcan distributes a wide range of chemicals, additives and ingredients to the international rubber, coatings, pharmaceutical and cosmetics sectors. Present “in all major countries” of the EU, it also maintains operations in Turkey and China, “with ongoing strategic development” in eastern Europe, the US and Mexico. In 2017, it posted revenues of around €565m. HCB www.safic-alcan.com
AZELIS HAS OPENED three new application laboratories in India that will focus on the needs of the local personal care; coatings, adhesives, sealants and elastomers (CASE); and food and health markets. As such, the company says it can “now offer the Indian market local support through formulation development, working on innovative concepts, analysis of products, technical training and seminars for customers and suppliers”. Furthermore, the new labs bring the company’s total number of such facilities in the Asia-Pacific region to 19, complementing a regional network that has grown rapidly over the past six years to now encompass 18 offices in 10 countries.
“Azelis entered the Asia Pacific market six years ago in 2012 and now has offices in Australia, China, India, Japan, Malaysia,
New Zealand, Singapore, Vietnam and Thailand,” the company says. “Continued investment in fully equipped laboratories, that also include existing facilities in China, Vietnam and Thailand, allows the company to meet the requirements of its customers in the Asia-Pacific region, servicing a range of applications in the personal care, food, coatings and homecare markets.”
Commenting on the news, Aparna Khurana, Azelis’ managing director for India, states: “Asia, and India in particular, represents a significant growth opportunity for Azelis and this is highlighted by the opening of three laboratories. The high quality of the staff in the new laboratories will enable us to fully support our customers at a local level. Strengthening our offering by allowing us to further develop new ideas and concepts will
aid Azelis’ potential, helping to accelerate our development and therefore better serve our principals.”
The opening of the three new labs comes shortly after Evonik named Azelis as its exclusive distributor within India, Nepal and Bangladesh for its various personal care ingredients, including actives, emulsifiers, emollients and functional ingredients. “We are delighted with the addition of the Evonik product line and are convinced this range will really enhance our current portfolio,” Khurana says.
“We are excited to now be able to offer Evonik’s full range of high-performance and quality ingredients to the Indian market. Evonik is a highly reputable manufacturing company and we are confident we will further grow business together and deliver many innovative solutions for our customers.”
“Personal Care in India is a significant growth opportunity for Azelis and this partnership will reinforce Azelis’ overall position in Asia Pacific as a leading distributor of speciality chemicals,” adds Azelis Asia Pacific CEO and president Laurent Nataf. “We both have a high focus on innovation and Evonik’s cutting-edge ingredients represent a perfect fit for both our portfolio and our strategy to focus on creating value for our customers in Asia Pacific.”
Further west on the cusp of Asia and Europe, Azelis has extended its arrangement with Clariant for the distribution of waxes, flame retardants and performance additives in Turkey. “This deal,” says Azelis group principal manager Stijn Vandevoorde, “enables us to expand our partnership in Turkey with a blue-chip partner that has an excellent reputation for quality and innovation. The product lines of waxes, flame retardants and performance additives are strongly synergetic with our current product portfolio in CASE, rubber and plastics additives and homecare and industrial cleaning. I am delighted with this new relationship, which will allow us to strengthen and broaden collaboration with our customers.” HCB www.azelis.com
UK-headquartered Blagden Specialty Chemicals has established “a fourth sector within its industrial division group” to serve the needs of customers from the graphic arts industry. “Our industrial business has grown considerably over recent years,” says Blagden CEO Graham Turton. “The addition of the Eckart pigment range to our portfolio in 2016, alongside the specialist additives we supply, makes us the ideal one-stop-shop for the digital and printing inks markets. The new sector aligns with our key supply partners’ end markets and ensures we provide the best possible service to our customers.”
The new sector will be headed by business line manager Phil Randall, who previously led the company’s coatings sector. “This is an exciting opportunity to substantially develop our business in these markets,” Randall states. “Blagden is an established supplier for inkjet and printing inks manufacturers and the new dedicated sector allows us to direct resources to develop the products and service we offer.” www.blagden.com
Airgas has acquired Ohio-based Weiler Welding Company, its 500th acquisition since it was founded in 1982 with the acquisition of Connecticut Oxygen. “Airgas is proud to mark the 500th acquisition since our inception in 1982,” says chief operating officer Andy Cichocki. “Growth through acquisition has always been a core strategy and competency for us and we remain committed to pursuing acquisition opportunities in the years to come.”
“The joining of these two companies will create tremendous value for our associates and our customers,” says Weiler president Jim Weiler. “Weiler Welding Company appreciates Airgas’ customer-centric and employee-focused culture. We feel that this culture will foster opportunities for our associates and we look forward to continuing to serve our customers as a part of Airgas.”
In other news, Airgas has been named Supplier of the Year in the Safety category by aircraft manufacturer Boeing. The gong comes in recognition of Airgas “modelling a zeroinjury mindset” while implementing a formal, measurable safety programme. “It is a true honour to receive this exceptional recognition from Boeing, particularly in the Safety category, as the safety of our customers and associates is core to our business and company culture,” says
Airgas CEO Pascal Vinet. “We are proud of our work together with Boeing to prioritise areas of improvement for injury reduction via the deployment of unique safety solutions developed by Airgas.” www.airgas.com
UK-headquartered 2M Holdings has launched what it describes as “a one-stop shop of services for new and existing customers” by which it can provide them “with flexible solutions” to meet their various outsourcing needs. “Customers can even outsource their entire supply chain to 2M Services and obtain more business with greater ease,” the company says. “The change means that in addition to the third-party sample management already on offer, 2M Services can now offer supplementary services, including toll blending, contract packing [and] bulk liquid storage.”
Meanwhile, other ancillary services offered by the company include warm rooms for the preparation of materials for subsequent processing; an onsite laboratory for retained samples and quality control testing; outside and covered warehousing for the secure storage for raw materials and finished goods with automated stock level and movement reports; and onward UK and international distribution.
“2M Services understand that [the] confidentiality of our clients is critical and enter into confidentiality agreements when negotiations with a prospective client begin,” the company states.
www.2m-holdings.com
Germany’s Biesterfeld Spezialchemie (BS) is to begin distributing Dymax Europe’s range of light-curing industrial adhesives and curing systems (right) across Germany, Austria, Switzerland, France, Turkey and Russia. The move builds on an existing arrangement that has seen Biesterfeld distributing Dymax’s products across Poland, the Czech Republic and Slovakia for a number of years.
“Dymax’s products enable us to offer our customers high-quality efficiency-boosting solutions for their manufacturing processes, from selecting the right adhesive, to questions about the right dosing or the different curing systems, to compliance with quality standards,” says BS sales director, healthcare Hartmut Zeller.
Meanwhile, BS has also extended its sales partnership with Sytheon to include the distribution of “a unique range of proprietary and patented active ingredients for the cosmetics industry” across Germany, Russia and the Benelux countries. The move follows what BS describes as a “very successful sales cooperation” in Spain. “Sytheon’s highly effective and high purity active ingredients have enriched our existing portfolio, which is already extensive and interesting,” says Bettina Heick, BS market manager, personal care.
“We are very pleased that we can now extend our existing collaboration with Sytheon to another five countries. Our sales team has the expertise needed to tell our customers about the many different ways in which these active ingredients can be used.”
www.biesterfeld.com
Netherlands-headquartered Barentz International has established a joint venture with Brazil’s Tovani Benzaquen Ingredients, a distributor of food, beverage and pharmaceutical ingredients across South America. “This is our first real entrance into Brazil, a step which fits in perfectly with our
global strategy, where Latin America is an important new market,” says Barentz CEO Hidde van der Wal.
“Brazil has recovered after some years of recession and we now see great opportunities here, both to develop the country and to grow as a company. Tovani has a wide and experienced team of dedicated technical specialists, who offer custom-made solutions developed in their technical laboratory. This is perfectly in line with our strategy to develop more custom-made solutions.” www.barentz.com
US-headquartered Hawkins has announced an unaudited record annual revenue of $504m, up 4.3 per cent on the prior year’s total, as well as fourth-quarter revenue growth of 7 per cent year-on-year. “Overall, fiscal 2018 was a challenging year with raw material cost increases and competitive pressures limiting our ability to pass the full increase in costs on to our customers,” says CEO and president Patrick Hawkins. “Those pressures, however, resulted in the entire organisation continuing to be very cost-focused while ensuring we deliver best-in-class service to our customers. This had a direct, positive impact on our results of operations, where our overall selling, general and administrative costs were flat year over year.” www.hawkinsinc.com
California-based Horn has been selected by Borregaard as its exclusive US distributor in the west and south-west for its new Exilva® line of micro fibrillated cellulose (MFC) (below).
“Exilva’s robust problem-solving capabilities are unlike other offerings on the market today, so the responsibility of choosing a partner in the US was carefully executed,” says Exilva America’s business development director Peter Orizondo.
“Horn’s industry reputation is unmatched and its market presence in the West and Southwest is key to meeting our goals for Exilva in the US. The Horn management team is always at the forefront of bringing innovative solutions to customers and Exilva fits well into Horn’s business approach in serving its industries.” www.ethorn.com
AIRSAFE TRANSPORT TRAINING PO Box 347 Cloverdale, WA 6985, Australia
T (+61 8) 9277 6968 www.airsafe.com.au
Dangerous Goods by Air –Acceptance
• June 25-27 – Darwin
• July 3-5 – Perth
• July 11-13 – Adelaide
• July 25-27 – Melbourne
• August 8-10 – Brisbane
• August 13-15 – Sydney
• August 20-22 – Perth
Dangerous Goods by Air –Refresher
• June 26 – Perth
• June 28 – Darwin
• July 10 – Adelaide
• July 18 – Perth
• July 24 – Melbourne
• August 7 – Brisbane
• August 8 – Perth
• August 14 – Sydney
• August 30 – Perth
AMSA Full Acceptance
• June 29 – Darwin
• July 9 – Adelaide
• July 23 – Melbourne
• August 6 – Sydney
• August 13 – Brisbane
• August 23-24 – Perth
Dangerous Goods by Road
• August 6 – Perth
AUSTRALIAN FEDERATION OF INTERNATIONAL FORWARDERS Westfield Office Tower, Suite 403, Level 3, 152 Bunnerong Road Eastgardens, NSW 2036 Australia
T (+61 2) 9314 3055
www.afif.asn.au
Dangerous Goods Acceptance (Air)
• July 3-5 – Sydney
• July 10-12 – Melbourne
• July 17-19 – Brisbane
• August 7-9 – Melbourne
• August 14-16 – Sydney
Dangerous Goods Re-certification (Air)
• July 2 – Sydney
• July 9 – Melbourne
• July 16 – Brisbane
• August 6 – Melbourne
• August 13 – Sydney
Dangerous Goods Awareness (Air)
• July 12 – Sydney
Dangerous Goods by Sea –
Full Acceptance
• July 10-11 – Sydney
• August 21-22 – Brisbane
Sully Moors Road Sully CF64 5RP, UK
T (+44 1446) 743 913
www.barrytrainingservices.co.uk
ADR – Initial
• July 9-13 – Barry
ADR – Refresher
• July 2-4 – Barry
BRITISH INTERNATIONAL FREIGHT ASSOCIATION (BIFA)
Redfern House, Browells Lane Feltham, Middlesex TW13 7EP, UK
T (+44 20) 8844 3625
www.bifa.org
Dangerous Goods by Air
• July 2-4 – Altrincham
• July 9-11 – Coventry
• July 9-11 – Feltham
• August 6-8 – Feltham
Dangerous Goods by Air –Revalidation
• July 3-4 – Altrincham
• July 10-11 – Coventry
• July 12-13 – Feltham
• August 9-10 – Feltham
Dangerous Goods by Road
• July 16-18 – Feltham
Dangerous Goods by Sea
• July 19-20 – Feltham
BUREAU OF DANGEROUS GOODS
4 Corporate Drive, Suite D Cranbury, NJ 08512, USA T (+1 844) 532 7634 www.bureaudg.com
49 CFR Recurrent
• July 17 – Cranbury
IATA Recurrent
• July 18 – Cranbury
IMDG Recurrent
• July 19 – Cranbury
49 CFR/IATA/IMDG Recurrent
• July 17-19 – Cranbury
49 CFR Initial
• July 17-19 – Cranbury
IATA Initial
• June 26-27 – Charlotte
• July 25-26 – Cranbury
IATA/IMDG Initial
• June 26-29 – Charlotte 49 CFR/IATA/IMDG Recurrent
• July 23-27 – Cranbury
CAMEON
PO Box 17345 Edinburgh EH12 1DJ, UK T (+44 131) 334 1929 www.cameon.com
Dangerous Goods by Air
• July 2-4 – Manchester
Dangerous Goods by Road –Upgrade
• July 5 – Manchester Dangerous Goods by Sea –Upgrade
• July 6 – Manchester
Dangerous Goods Safety Adviser (DGSA)
• September 3-7 – Manchester
COMMERCIAL OPERATOR
TRAINING SOLUTIONS Unit 6, Queensway Swansea West Business Park Swansea SA5 4DH, UK T (+44 1792) 587250 www.cotsolutions.co.uk
ADR All Classes and Tanks
• June 25-29 – Swansea
• July 23-27 – Swansea
DANGEROUS GOODS COUNCIL PO Box 7325 York, PA 17404, USA
T (+1 717) 848 8840 www.hazshipper.com
49 CFR & International AirCertification
• July 16-18 – Houston
• August 6-8 – St Louis 49 CFR – Certification
• July 16-17 – Houston
• August 6-7 – St Louis
International Air – Recertification
• July 18 – Houston
• August 8 – St Louis
DGI TRAINING CENTER
1060 El Camino Real, Suite B Redwood City, CA 94063-1645, USA T (+1 650) 306 8450 www.dgitraining.com
IATA Initial
• August 1-2 – Newark
• August 8-9 – Seattle
• August 20-21 – Chicago
• August 27-28 – San Francisco
IATA Recurrent
• July 16 – Atlanta
• July 16 – Chicago
• July 23 – Anaheim
• July 30 – Newark
• August 6 – Seattle
• August 29 – San Francisco
• August 30 – San Antonio
IMDG Initial
• July 26-27 – Anaheim
IMDG Recurrent
• July 25 – Anaheim
• August 31 – San Francisco Ground Transportation (49 CFR) Initial
• June 25-26 – Orlando
• July 9-10 – Chicago
• August 27-28 – Anaheim Ground Transportation (49 CFR) Recurrent
• July 17 – Atlanta
• July 17 – Chicago
• July 31 – Newark
• August 7 – Seattle
• August 30 – San Francisco
Multimodal Initial (49 CFR/IATA/IMDG)
• June 25-29 – Orlando
• July 9-13 – Chicago Multimodal Recurrent (49 CFR/ IATA/IMDG)
• July 16-18 – Atlanta
• July 23-25 – Anaheim
• August 29-31 – San Francisco
Ground/Air Shipping - Initial (49 CFR/IATA)
• August 1-3 – Newark
• August 8-10 – Seattle
Ground/Air Shipping - Recurrent (49 CFR/IATA)
• July 16-17 – Atlanta
• July 16-17 – Chicago
• July 23-24 – Anaheim
• July 30-31 – Newark
• August 6-7 – Seattle
• August 29-30 – San Francisco
Radioactive Materials (Multimodal)
• July 26-27 – Las Vegas Explosives (Multimodal)
• July 18-19 – Chicago
DGM TRAINING INSTITUTE
1813 Greens Road Houston, TX 77032, USA
T (+1 281) 821 0500 www.dgm-usa.com
IATA/ICAO Dangerous Goods by Air – Initial
• July 9-11 – Atlanta
• July 23-25 – Dallas
• August 6-8 – Atlanta
• August 6-8 – Houston
• August 13-15 – Miami
IATA/ICAO Dangerous Goods by Air – Recurrent
• July 10-11 – Atlanta
• August 7-8 – Atlanta
• August 9-10 – Houston Dangerous Goods by Air, including Radioactives
• July 9-12 – Houston
IMDG Code - Initial
• July 23-24 – Atlanta
• July 30-31 – Houston
IMDG Code – Recurrent
• July 24 – Atlanta
• August 1 – Houston 49 CFR Dangerous Goods by Road – Initial
• July 25-26 – Houston
• August 20-21 – Atlanta
• August 28-29 – Houston
49 CFR Dangerous Goods by Road – Recurrent
• July 27 – Houston
• August 21 – Atlanta
• August 30 – Houston
Multi-Modal (Air, Road and Sea)
– Initial
• July 16-19 – Houston
• August 20-23 – Houston
General Awareness
• June 25 – Atlanta
Transporting Radioactives
• July 12 – Houston
Transporting Batteries
• August 31 – Houston
Torquay, Devon TQ2 6NY, UK T (+44 1803) 293344
www.fremantletraining.co.uk
ADR Driver Training
• July 9-13 – Bristol
ADR Driver Training – Tanks & Class 3 Refresher
• June 25-26 – Bristol
• June 27-28 – Plymouth
Hermes House, St John’s Road Tunbridge Wells TN4 9UZ, UK T (+44 1892) 526171 www.fta.co.uk
Dangerous Goods Safety Adviser
• July 20-August 3 –Leamington Spa
ADR – Refresher
• July 31-Aug 2 – Tunbridge Wells
• August 14-16 – Stirling Dangerous Goods Awareness
• August 17 – Stirling
54 Norristown Road Blue Bell, PA 19422, USA
T (+1 215) 283 0983 www.gttstraining.com
Multi-Modal - IATA/IMDG/DOT 49 CFR – Initial
• June 25-29 – Boston
• July 9-13 – Charlotte
• July 9-13 – New York
• July 16-20 – Dallas
• July 23-27 – Cincinnati
• July 23-27 – Philadelphia
• July 30-Aug 3 – Chicago
• July 30-Aug 3 – Orlando
• August 6-10 – San Francisco
• August 6-10 – Seattle
• August 13-17 – Baltimore
• August 13-17 – Houston
• August 20-24 – Atlanta
PO Box 94449
Abu Dhabi, UAE
T (+971 2) 494 2355 www.gcas.ae
IATA DGR - Category 6 – Initial
• July 15-22 – Abu Dhabi
• August 12-19 – Abu Dhabi
Dangerous Goods RegulationsCategory 6 – Recurrent
• July 2-7 – Abu Dhabi
HAZMAT TRAINING SCHOOL SINGAPORE
146A Changi Road Singapore 419726
T (+65) 6542 5539 www.haz-mat-training.com
IATA Dangerous Goods Regulations (Initial)
• July 23-27 – Singapore
IATA Dangerous Goods Regulations (Recurrent)
• June 28-29 – Singapore
• July 26-27 – Singapore
• August 29-30 – Singapore
IATA Dangerous Goods Regulations (Awareness)
• July 23 – Singapore
IMDG Code Dangerous Goods By Sea
• June 26-27 – Singapore
• August 27-28 – Singapore
Chemical Safety Awareness
• July 12 – Singapore SCDF Hazmat Transport Driver Permit
• June 25 – Singapore
• July 11 – Singapore
• August 15 – Singapore
INTERNATIONAL AIR TRANSPORT ASSOCIATION
800 Place Victoria, PO Box 113 Montreal H4Z 1M1 Quebec, Canada.
T (+1 514) 874 0202 www.iata.org/training
Dangerous Goods Regulations (DGR) – Shippers and Packers –
Cat 1 and 2
• August 1-3 – Amsterdam
Dangerous Goods Regulations (DGR) – Initial, Category 6
• July 9-13 – Montreal
• July 30-Aug 3 – Singapore
• August 20-24 – Miami
• August 27-31 – Stockholm
Dangerous Goods Regulations (DGR) – Recurrent, Category 6
• August 20-31 – Geneva
Dangerous Goods Regulations (DGR) – Instructor Refresher
• June 27-29 – Miami
• August 22-24 – Brussels
Professional Skills for DGR
Instructors – Categories 1,2,3,6
• July 9-13 – Rome
• July 30-August 3 – Beijing
Instructional Techniques for DGR (for categories 4, 5, 7, 8, 9, 10, 11, 12)
• August 27-31 – Geneva
DGR for Auditors and Inspectors
• June 25-29 – Geneva
• August 13-17 – Singapore
Shipping Lithium Batteries by Air
• July 16-17 – Montreal
• August 20-21 – Singapore
Transport of Dangerous Goods by Sea (IMDG)
• July 18-20 – Amsterdam
570 Lafayette Road Sparta, NJ 07871-3447, USA
T (+1 888) 546 6511 www.lion.com
Multimodal Hazmat Shipper Certification (49 CFR/IATA/IMDG)
• July 9-12 – Parsippany, NJ
• July 10-13 – Boston
• July 16-19 – Hartford, CT
• July 23-26 – Baltimore
• July 31-August 3 – Atlanta
• August 6-9 – Nashville
• August 13-16 – Jacksonville
Hazmat Ground Shipper Certification (49 CFR)
• July 9-10 – Parsippany, NJ
• July 10-11 – Boston
• July 16-17 – Hartford, CT
• July 16-17 – Philadelphia
• July 19-20 – Williamsburg, VA
• July 23-24 – Baltimore
• July 25-26 – Charlotte
• July 30-31 – Orlando
• July 31-August 1 – Atlanta
• August 6-7 – Nashville
• August 13-14 – Mobile
• August 13-14 – Jacksonville
• August 16-17 – Memphis
• August 20-21 – Louisville
Hazmat Ground Shipper
Certification - Recurrent
• August 15 – Sparta, NJ
Hazmat Vessel Shipper Certification (IMDG)
• July 12 – Parsippany, NJ
• July 13 – Boston
• July 19 – Hartford, CT
• July 26 – Baltimore
• August 3 – Atlanta
• August 9 – Nashville
• August 16 – Jacksonville
Hazardous Waste in California
• July 9-10 – Anaheim
• July 12-13 – Palmdale
• July 16-17 – Modesto
• July 19-20 – San Jose Industrial & Hazardous Waste in Texas
• August 6-8 – Houston
• August 15-17 – San Antonio
• August 20-22 – Arlington
NOVADATA TAB LTD
Blackwell Drive
Springwood Industrial Estate Braintree, Essex CM7 2QJ, UK T (+44 1376) 552999 www.novadata.co.uk
ADR Core, Packages
• July 23-26 – Braintree
• August 20-23 – Braintree
OILSPILL RESPONSE TRAINING
Lower William Street Southampton SO14 5QE, UK T (+44 23) 8033 1551 www.oilspillresponsetraining.com
Oil Spill Clearance – On-Scene Commander (IMO Level 2)
• July 23-27 – Singapore
On-Scene Commander – AsiaPacific (IMO Level 2)
• July 9-11 – Johor Bahru
• July 31-Aug 2 – Makati
Oil Spill Response Management (IMO Level 3)
• June 26-29 – Singapore
• July 4-6 – Kuala Lumpur
• July 10-12 – Beijing
• July 17-19 – Goa
Oil Spill Response Refresher (IMO 1 to 3)
• July 18 – Southampton
9 Langley House
Wheatcroft Business Mark Landmere Lane, Edwalton Nottingham NG12 4DG, UK T (+44 115) 965 1888 www.safeware-int.com
Transport of Dangerous Goods Awareness
• July 18 – Nottingham EU Chemical Regulatory
Compliance in a Nutshell
• July 17 – Nottingham Authoring Safety Data Sheets
• July 26 – Nottingham GHS Professional Refresher
• July 11 – Nottingham
TRANSPORTATION TECHNOLOGY CENTER Security and Emergency Response Training Center PO Box 11130 Pueblo, CO 81001, USA T (+1 719) 584 0584 sertc.org
HazMat/WMD Technician for Surface Transportation
• August 13-24 – Pueblo Leadership & Management of Surface Transportation Incidents
• August 20-24 – Pueblo Highway Emergency Response Specialist
• June 25-29 – Pueblo
• July 16-20 – Pueblo
• July 30-Aug 3 – Pueblo
• August 20-24 – Pueblo
• August 27-31 – Pueblo Tank Car Specialist
• July 23-27 – Pueblo
Tactical Hazardous Materials Operations for Surface Transportation
• June 25-29 – Pueblo
• July 9-13 – Pueblo
• July 30-Aug 3 – Pueblo
Crude-by-Rail Response
• June 26-28 – Pueblo
• July 17-19 – Pueblo
• July 24-26 – Pueblo
• August 15-17 – Pueblo
• August 28-30 – Pueblo Transportation Container Loading and Unloading
Emergency Response
• July 10-12 – Pueblo
• August 21-23 – Pueblo UPS
55 Glenlake Parkway NW Atlanta, GA 30328, USA
T (+1 800) 634 5656 www.upshazmatseminars.com 49CFR & IATA Dangerous Goods Seminar
• July 31-August 2 – Minneapolis 49CFR Dangerous Goods Seminar
• July 31-August 1 – Minneapolis
JUNE 6-7, DAVENTRY
33rd annual regulatory update conference www.dft.gov.uk/vca/dangerousgoods/ dangerous-goods-seminar.asp
JUNE 7-10, BALTIMORE
Annual international event for response teams www. events.iafc.org/micrositeHazConf/ homeHazConf.cfm
ILTA
JUNE 11-13, HOUSTON
38th annual operating conference and trade show of the International Liquid Terminals Association www.ilta.org
JUNE 15, BERLIN
Annual event of the Federation of European Tank Storage Associations, prior to AGM www.fetsa.eu
JUNE 18-19, BARCELONA Conference on regional oil trades and logistics www.argusmedia.com/events/argus-events/ europe/argus-mediterranean-storage-andlogistics/home/
JUNE 18-21, ROME
Annual congress of the International Association of Independent Tanker Operators www.intertanko.com/News-Desk/Annual-Events/
JUNE 20-21, BRUSSELS
Round-table meeting looking at how digitalisation will affect the petrochemical supply chain www.epca.eu
JUNE 20-21, ANTWERP
Inaugural forum on best practice in chemical logistics and supply chain management www.bvl.de/en/fcl
JUNE 21-22, MARSEILLE
Annual networking event and conference for the liquids logistics sector www. events.tankbank.com.sg
JUNE 25-29, WASHINGTON, DC
Triennial summit for the global gas sector www.wgc2018.org
Hazards Australasia 2018
JUNE 26-27, PERTH Conference on process safety management in the chemicals sector www.icheme.org/events/conferences/hazardsaustralasia-2018.aspx
AUGUST 14-17, NEW ORLEANS
Conference for the North American chemical distribution sector www.nacd.com/meetings/ce/2018-chemedge/
AUGUST 26-28, SAVANNAH
Semi-annual meeting of the Petroleum Packaging Council www.ppcouncil.org/upcoming-meetings.php
AUGUST 26-29, RENO
Annual conference of the Alliance of Hazardous Materials Professionals http://ahmpnet.site-ym.com/?page=National_ Conference
AUGUST 30, SYDNEY
Annual road tanker event hosted by the National Bulk Tanker Association www.nbta.com.au/tankerday/
SEPTEMBER 4-7, HAMBURG
28th biennial exhibition and conference for the global shipping industry http://smm-hamburg.com/en
SEPTEMBER 5-7, CHICAGO
13th annual Dangerous Goods Symposium hosted by Labelmaster www.labelmaster.com/symposium
SEPTEMBER 10-14, NORFOLK
35th annual networking and training meeting sponsored by the Virginia Association of Hazardous Materials Response Specialists www.virginiahazmat.org/annual-hazmat-conference/
SEPTEMBER 12-13, LONDON
Ninth annual conference on wreck removal and salvage costs
www.wplgroup.com/aci/event/maritime-salvagecasualty-response/
SEPTEMBER 12-13, GALVESTON
11th annual event for the US aboveground tank storage sector www.nistm.org
SEPTEMBER 17-21, WHITEHORSE
Annual meeting of the Commercial Vehicle Safety Alliance http://cvsa.org/eventpage/events/cvsa-annualconference-and-exhibition/ Gastech 2018
SEPTEMBER 17-20, BARCELONA
International conference and trade show for the LNG and LPG industries www.gastechevent.com
SEPTEMBER 18-21, BUENOS AIRES
13th international exhibition for logistics technology and equipment www.expologisti-k.com.ar
SEPTEMBER 20-22, KASSEL
Biennial trade fair for the petroleum transport and logistics industry www.expopetrotrans.de
SEPTEMBER 27, COVENTRY
18th annual meeting of the UK Tank Storage Association www.tankstorage-event.org.uk
1/3/18 Kazungula, road tanker sulphuric Fire broke out in MBS Carriers road tanker with 30,000 litres sulphuric acid heading for South Africa; driver Zimbabwe Southern, Zimbabwe acid said electrical fault caused fire; most of load spilled; response focused on preventing environmental damage Daily
6/3/18 Nangarhar province, road tanker oil Magnetic bomb on tanker with unspecified oil cargo initiated on Jalalabad-Torkham road; two killed, two Khaama Afghanistan injured, several shops caught fire; no group claimed responsibility; area had hitherto been relatively calm
6/3/18 Fredericktown, road tanker hydrochloric Kuhnle Bros tank truck with 4,400 gal (16.7 m3) 36% hydrochloric acid solution was struck by freight train ObserverPennsylvania, US acid on crossing; driver, two train crew hurt; spill was kept out of nearby river; FRA investigating Reporter
7/3/18 Fort Worth, road tanker diesel Tank truck with diesel overturned, caught fire on I-20; westbound lanes closed for response; two people StarTexas, US injured; not clear what caused single-vehicle accident Telegram
8/3/18 Pflugerville, road tanker nitrogen Fire broke out in cab of tractor-trailer on Highway 18, causing grass fire; tank trailer with nitrogen not Spectrum Texas, US affected but half-mile evacuation zone imposed in case of explosion
9/3/18 Houston, truck hydrochloric Acid spilled from two damaged containers after driver braked to avoid car; police found load should not have KHOU Texas, US acid been inside the loop, load was not properly secured, incorrect paperwork; TxDOT to follow up
9/3/18 Belton, road tanker kerosene APC tank truck with aviation fuel overturned, spilled some 7,500 gal (28.4 m3) fuel; not clear what caused Indep’t S Carolina, US incident but very similar crash happened in December 2017; residents concerned at frequency of accidents Mail
12/3/18 Death Valley, road tanker slurry Driver lost control of rig, which overturned and caught fire by side of road in Death Valley National Park; KTNV California, US Highway 190 closed for seven hours; tank was carrying cyanide solution, chromatic acid slurry
13/3/18 Chyulu Hills, road tanker LPG LPG tanker exploded when it collided with another truck on Mombasa-Nairobi highway; tanker driver killed; Capital Kenya two others injured; highway closed, diversions in place FM
13/3/18 Co Tyrone, road tanker diesel Road tanker with diesel overturned on A4, causing road to be closed; small leak was found in rear end of Belfast N Ireland, UK tank; fire crews applied bar of soap, which reacted with diesel to form a temporary bung Telegraph
16/3/18 Buffalo, road tanker jet fuel Prior Aviation tank truck with 5,000 gal (19 m3) aviation fuel crashed into fence at Buffalo Niagara Int’l NYup.com New York, US Airport, spilling some 2,000 gal; nearby roads closed; no injuries reported
22/3/18 Thane, road tanker oil Road tanker with unspecified oil from JNPT to Silvassa overturned on Patlipada flyover, causing oil spill Indian Maharashtra, India that disrupted traffic; soil applied to soak up spill; no serious injuries Express
23/3/18 Miami, road tanker gasoline Crash involving tank truck on I-95 led to spillage of gasoline, closure of highway and nearby Tri-Rail Local10 Florida, US service; up to 3,000 gal (11.4 m3) believed spilt to drainage ditch; remaining fuel transferred
25/3/18 Narsinghpur, road tanker gasoline Fire broke out on tanker as it was delivering gasoline to fuel station; driver risked himself to drive tanker to OneIndia MP, India vacant plot, suffering serious burns in the process; cause of fire unknown News
26/3/18 Pretoria, road tanker gasoline Tanker driver lost control coming off N4, hit barrier and crashed into four other vehicles; significant spill Rekord South Africa of gasoline but no serious injuries or fire reported
26/3/18 Taoyuan, truck sulphuric Nine IBCs with sulphuric acid fell from truck as it rounded a corner; several containers ruptured, spilling Taiwan Taiwan acid acid to road; no immediate danger but specialised responders were despatched to clean up spill English
26/3/18 Bunnell, road tanker diesel DeFord tank truck with 1,800 gal (6,800 litres) off-road diesel overturned after driver lost control in slippery Flagler Florida, US conditions; some 1,200 gal spilled to road, storm drains; remaining cargo transferred to allow rig to be righted Live
27/3/18 Jebba, road tanker fuel Road tanker with unspecified fuel load overturned, caught fire after brake failure led to collision; five killed, Premium Kwara, Nigeria significant property damage; local paper mill’s fire unit responded Times
28/3/18 Udayapur, road tanker diesel In what was described as “Nepal’s first oil spill accident”, tanker lost 12,000 litres diesel in gorge after driver My Nepal fell asleep; two killed, three injured; accident in remote area with no risk to population República
28/3/18 Jane Lew, road tanker chemical Tank truck with unspecified flammable chemical load overturned in driveway of Southwest Energy facility, WBOY W Virginia, US leaking cargo; area evacuated until another tanker could be brought to transfer remaining cargo
29/3/18 nr Mount Isa, road tanker gasoline One person was killed when road tanker hit car and caravan on Barkly Highway, caught fire and exploded; ABC Qld, Australia two others badly hurt; responders had to let fire burn out; highway closed for some time
29/3/18 Worcester, truck oxidiser Tractor-trailer got wedged under rail bridge after driver ignored height warning signs; one drum of cumene Telegram Massachusetts, US hydroperoxide was damaged, leaked; nearby homes evacuated in case of explosion
30/3/18 Khajuri, rail tank car gasoline Major fire broke out at Bakania Bhauri oil depot, apparently during attempt to steal gasoline from parked The MP, India train; police found more than 120 containers at the site, half of them full; nearby residents evacuated Hitavada
6/3/18 Arabian Sea Maersk Honam unknown Severe fire broke out after explosion in boxes in forepeak area of ship with 7,680 containers; at least one crew FleetMon died, four missing; containership taken in tow, but took weeks to arrive in Dubai; general average declared
10/3/18 Hai Phong, Hai Ha 2 gasoline Product tanker (950 dwt, 2010) suffered explosion during discharge of gasoline cargo, reportedly due to pump VN Vietnam malfunction; responders managed to move tanker to safe area without reported injury Express
13/3/18 Tanjung Manis, Dongfang Product tanker (6,500 dwt, 2010) suffered explosion, fire in cargo tank during repair work; three injured, FleetMon Kalimantan, Malaysia Glory including master; tanker reported to be in ballast; suspected that tanks not properly gas-free ahead of hot work
15/3/18 off Oman Maersk unknown Containership ( 5,000 teu) reported fire in hold while en route from Oman to Suez; CO2 was released into hold, Maritime Kensington fire was extinguished; Maersk said no link between this and earlier explosion on Maersk Honam Executive
17/3/18 off Nishimura, Shoei Maru oil products Product tanker (1,300 dwt, 1993) with 500 t unspecified product, was disabled after collision with cargoship FleetMon Honshu, Japan No 8 Dong Kun 7; tanker understood to have been breached, some oil spilled; both towed to Tanabe Bay
25/3/18 New Orleans, barge biodiesel Wake from passing vessel caused barge to break away from towing vessel, struck concrete wharf, leaked TimesLouisiana, US 9,700 gal (230 bbl) biodiesel to Mississippi River; USCG, OMI stopped leak, started oil recovery Picayune
26/3/18 Limassol, barges petroleum Hundreds of litres of petroleum (possibly gasoline) leaked to harbour waters during transfer between two Cyprus Cyprus barges due to failed connection; company responsible expected to be fined; several police boats damaged Mail
28/3/18 Shanghai, Puelo cyclohexane Crew spotted liquid leaking during loading of container at Yangshan port; authorities alerted; leak found to FleetMon China be cyclohexane from damaged drum; container offloaded; fortunate that flammable spill was spotted
28/3/18 Civitavecchia, Golden coal Fire erupted in hold of bulker (79,500 dwt, 2010) during offloading of coal; possible that cargo had generated FleetMon RM, Italy Eclipse flammable gas in hold; fire burned all day, despite efforts of shore-based firefighters
31/3/18 Balikpapan, various crude oil Several vessels were caught up in fire, which turned out to be caused by leaking oil from damaged Pertamina Maritime Kalimanta, Indonesia pipeline; at least four people killed; severe pollution; gas masks distributed to local population Executive
Date Location Plant type Substance Details Source
2/3/18 Bolton, plastics hydrogen One worker suffered serious burns when hydrogen fluoride leaked as he tried to connect gas cylinder to piping; MEN Gtr Manchester, UK plant fluoride despite injuries, he managed to close cylinder to prevent further damage; HSE to investigate
3/3/18 nr Barrancabermeja, pipeline crude oil At least 600 bbl crude spilled from Ecopetrol pipeline at Lizama oilfield; severe impact on local wildlife, rivers; Colombia Colombia no action by operator to address leak for three weeks; nearby residents suffering medical problems Reports
3/3/18 Mullinahone, oil depot kerosene Up to 10,000 litres kerosene leaked from Mullinahone Oil facility after valve was damaged in storm; spill Extra.ie Tipperary, Ireland flowed into nearby river; affecting water supplies to 12,000 residents
3/3/18 Portland, warehouse hydrogen Fire broke out in warehouse on Airport Way, involving 16 drums of hydrogen peroxide; responders managed KOIN Oregon, US peroxide to control fire, contain leaking material; no further information
6/3/18 Okpare, pipeline crude oil Widespread fire following damage to crude oil line destroyed farmland, animals and property, and posed AfroBeat Delta, Nigeria risks to human health; locals blamed soldiers who had destroyed illegal refinery, damaging line
7/3/18 San Diego, pipeline natural gas Construction crews accidentally ruptured 22-inch gas line in Mission Valley; leaking gas forced closure of KGTV California, US nearby freeway; gas supplies to homes, businesses cut off; evacuations ordered, local mall closed
8/3/18 Boisar, pharmaceutical solvents At least three killed, 15 injured by series of explosions, fire at Novephene Specialities plant involving 25 RSOE Maharashtra, India factory 200-litre drums of solvent; nearby chemical units also damaged; operator likely to lose licence
9/3/18 Chicago, post office lithium Box of lithium batteries exploded at post office in N Broadway St; hazmat responders had been alerted to WLS Illinois, US batteries suspicious package when it went off; not clear if the batteries had been mailed or dropped off
10/3/18 Marsa el-Brega, oil refinery methanol Explosion, fire at NOC refinery after leak in methanol unit; site fire teams extinguished blaze; extent of Fire Libya damage and cause of leak not known Direct
14/3/18 Savoonga, store heating oil Some 22,000 gal (83 m3) heating oil spilled in village on St Lawrence Island during transfer of fuel between KTOO Alaska, US storage tanks; spill largely contained in bunded area but cleanup hampered by deep snow
Date Location Plant type
Substance Details Source
15/3/18 Grise Fiord, power diesel Some 4,000 litres diesel spilled from day tank at community power unit, apparently due to faulty automatic CBC Nunavut, Canada generator valve, loose plug; most of spill collected but will remain on site until island is accessible by sea again
15/3/18 Kolkata, warehouse chemicals Fire broke out in godown used to store flammable chemicals in Armenian Ghat area; blaze spread to nearby IANS India shanty homes, disrupted train services and flower market; no injuries reported
15/3/18 Cresson, chemical chemicals Series of explosions, fire at Tri-Chem Industries chemical blending plant; one person badly injured, one NBC Texas, US plant missing; suspected that static discharge from worker’s shoe ignited flammable atmosphere
18/3/18 Robersonville, meat packing fuel oil At least 1,500 gal (5,700 litres) No 6 fuel oil spilled from storage tank at rear of meat packing plant, probably WITN N Carolina, US plant as a result of vandalism; EPA found valve damaged; spill reached downstream wastewater treatment plant
20/3/18 Pulau Busing, oil terminal petroleum SCDF fire crews spent six hours battling raging fire in storage tank at Tankstore tank farm, described as Channel Singapore “quite severe”; air quality being monitored as plume of smoke rose from site; no casualties reported News Asia
20/3/18 nr Solitude, pipeline diesel Some 1,000 bbl diesel spilled from Marathon 10-inch pipeline in rural area; spill affected nearby creek; Indy Star Indiana, US booms deployed to prevent slick reaching Wabash River; not clear what caused breach in line
20/3/18 Dawsonville, chicken ferric Drum of ferric chloride was accidentally punctured at Gold Creek Foods, causing chemical to spill to stream Dawson Georgia, US processing plant chloride behind plant; significant fish kill; company criticised for late reporting of incident Co News
21/3/18 Volokolamsk, waste dump hydrogen At least 180 people were hospitalised after being affected by fumes from dump during previous two weeks; RFE Russia sulphide high levels of hydrogen sulphide recorded; dump opened in 2008 to handle waste from Moscow
22/3/18 Kralupy nad Vltavou, chemical chemicals
Six killed, several more badly injured by explosion at Unipetrol styrenics plant north of Prague; operator said BBC Czech Republic plant fire broke out in storage tank, though not clear what caused the fire or what was in the tank
29/3/18 Livorno, warehouse ethyl acetate Two workers killed by explosion during cleaning of ethyl acetate tank at Costiero Neri warehouse in port area; Huff’n LI, Italy another tank damaged in blast; unions protesting spate of industrial accidents in Italy Post
29/3/18 Richardton, ethanol plant ethanol
Some 202 bbl ethanol spilled at Red Trail Energy plant due to failure to properly close valve on transfer hose; Bismarck N Dakota, US spill contained on site; authorities monitoring cleanup Tribune
THOSE TASKED WITH dangerous goods shipping and compliance will acknowledge that one particular item classified as ‘dangerous’ has dominated the conversation for the last few years – lithium batteries (and the fire risks they pose). To protect shipments of lithium batteries and the devices that use them, restrictions and requirements have been put into place – including UN Transportation Testing (UN/DOT 38.3), which tests a battery or device’s ability to handle altitude, shock, temperature and more to determine if they are safe to transport.
While existing regulations and testing represent a significant step toward ensuring safe transport, DG shippers must still be prepared for the unexpected. For example, what if you’re shipping damaged batteries
or the batteries become damaged along the journey? What if there’s a recall on devices containing lithium batteries? How do shippers better mitigate that risk and better protect individuals who come in contact with those batteries – and do so without inflating costs? It comes down to going the extra mile to ‘think outside the box’.
Despite recent advances, one thing still rings true for most shippers – when it comes to packaging, the cardboard box almost always reigns supreme. The problem is, while manufacturing, supply chain and shipping processes have evolved and improved, until recently the actual box technology itself has remained the same. While that may be
acceptable for most shipments, when it comes to transporting dangerous goods – especially lithium batteries – it poses a significant problem.
The fact is, traditional cardboard boxes are highly flammable. If the contents of a cardboard box heat up and ignite, this type of packaging will likely fuel the fire and hasten its spread beyond the box’s confines. For this reason, the majority of lithium battery-related shipments have typically included heavy, fire-retardant liners, gel-packs, beads, metal boxes or pails, and must conform to strict exterior labelling requirements.
What if the cardboard box was engineered to protect against fire rather than promote it? What if the supply chain industry turned its attention beyond the labels placed on the outside of a box or the fillers used inside a box, and focused instead on the box itself as a way to provide improved safety?
In fact, the evolution of a better box is here. Innovative shipping materials and packaging options designed specifically to provide a thermal barrier during the transport and storage of lithium batteries are now available. Some boxes with next-generation technology even eliminate the use of gel packs, beads, liners, pellets and fillers, making the transport of lithium-related products (and other dangerous goods) safer and easier than ever before, and further simplifying critical steps in the supply chain – for both internal personnel as well as consumers.
Whether it’s shipping one damaged lithium battery or addressing a nationwide battery recall (instances of which seem to be on the rise), shippers can opt for boxes that now provide improved flame retardance/ arrestment, thermal management, pressure management, blast containment, and gas and smoke filtration. This smarter packaging translates directly to safer transport and enhanced compliance, while also addressing the added cost, package weight and complexity that come when transporting dangerous goods with the various liners and fillers necessary when using a traditional box.
Despite such innovations now being available on the market, harnessing the opportunities they can afford will require a »
basic shift in thinking across the industry –from manufacturers to shippers, and retailers to logistics providers.
As an industry, we must collectively change the way we view ‘the box’ and look at it as a strategic component of dangerous goods transport rather than simply as a container or added cost. To do this, all involved must recognise the benefits of next-generation packaging and see how they outweigh the objections:
1. Reducing risk
• Hi-tech packaging provides an added level of assurance and protection during transport
• Safer boxes help avoid negative company brand impact that could result from an incident occurring during the transport of lithium batteries
2. Promoting safe handling
• Hi-tech packaging provides an additional layer of safety across manufacturing, shipping and the supply chain as a whole
• Protects all those who come into contact with packaged lithium batteries or other DG
• Ensures damaged or recalled batteries are transported safely
• Protects against adverse shipping conditions or climate variations involved with countrywide recalls
• Simplifies the return process for everyone involved – particularly the end user
4. Gaining a competitive advantage
• Helps bolster productivity, efficiency and safety of operations
• Helps improve customer satisfaction and company reputation
When looking into alternatives to the traditional box, it is important to realise that selecting the right packaging provider is as important as choosing the right packaging solution in the first place.
Dangerous goods shippers have more riding on their shoulders than those who transport any other type of goods. To ensure they are working with the best provider and the right solution to meet their packaging needs, those responsible for shipping should keep the following key considerations in mind:
• Is the packaging solution (and its instructions) easy enough for employees (at various points of the supply chain) or even consumers to use it correctly?
• Has the packaging solution been rigorously and thoroughly tested?
• Does the packaging solution meet all the latest shipping regulations and compliance requirements?
• Does the solution offer an option for the packages to show up preassembled, saving valuable time and resources?
Given the exponential growth of e-commerce and the related rise in direct-to-consumer shipping, the pace of shipments of all kinds – including those containing lithium batteries and other dangerous goods – will only increase. Those who lag behind in the adoption of innovative packaging and modern ‘box’ options will not only expose themselves to the risks inherent in transporting flammable and dangerous goods, they will miss out on additional opportunities to streamline shipping and tracking via RFID and other next-generation technologies. In the end, this could mean losing out to the competition and, ultimately, adversely impacting the bottom line. HCB
*Pia Jala is vice-president, operations at Labelmaster, which now offers Obexion packaging to simplify the transport of lithium batteries. More information can be found at www.labelmaster.com/obexion.
“WHAT IF THE SUPPLY CHAIN INDUSTRY FOCUSED ON THE BOX ITSELF AS A WAY TO PROVIDE IMPROVED SAFETY?”
THE CONCEPT OF Responsible Care, adopted by the Canadian chemical industry in 1985, was prompted by a number of serious accidents, culminating in the Mississauga derailment in Ontario in November 1979 that caused the evacuation of nearly a quarter of a million people. Responsible Care was a pledge by industry to improve its safety and environmental performance.
The programme was rapidly adopted around the globe and is now in place in 65 countries. In many, adherence to the Responsible Care programme is now a requirement for members of national chemical industry associations.
In its early years, Responsible Care focused mainly on health, safety and environmental (HSE) performance at chemical production sites but it was soon realised that it had value to add to all elements in the chemical supply chain. Since the logistics function had become widely outsourced to thirdparty providers, there was a need to ensure that these companies too were adhering to the same high HSE standards as those chemical companies whose goods they were transporting.
This was the start of SQAS – a uniform, third-party assessment scheme to check the HSE standards of logistics service providers (LSPs). It dates back to 1992, when a working
group of the European Chemical Industry Council (Cefic) ran a pilot with three transport companies to test a new system of audits. Since its official start-up 25 years ago, SQAS has been expanding to cover the complete land logistics chain, including transport service providers, tank cleaning stations, warehouses, rail operators and chemical distributors.
The initial scope of SQAS added a ‘Q’ – quality – to the HSE elements of Responsible Care. Later on it was expanded again to cover security in the logistics chain and, more recently, added corporate social responsibility (CSR) topics.
Last year, to mark its 25th anniversary, the meaning of SQAS was extended once more, now representing Safety and Quality Assessment for Sustainability, which is matched by an expanded and revised website at www.sqas.org.
SQAS aims to achieve continuous improvement among audited companies – its assessments are regularly updated to reflect
changes in technology and the expectations of chemical manufacturers, regulators and the wider public. SQAS itself has also been the subject of continuous improvement: while its basic principles have stayed the same – the use of standardised assessments undertaken by independent auditors, for use by chemical companies as part of their risk management procedures – it has continuously adapted to changing industry requirements while also taking advantages of IT developments to make the system much more user-friendly.
None of this could have happened without the close collaboration of a number of organisations representing the logistics sectors in Europe, not least the European Chemical Transport Association (ECTA), the European Federation of Tank Cleaning Organisations (EFTCO) and the European Federation of Chemical Distributors (Fecc).
Cefic signed Responsible Care partnerships with both ECTA and Fecc, which use SQAS to verify their members’ adherence to Responsible Care.
As Victor Trapani, SQAS and transport regulations manager at Cefic (right), explains, the worth of a system such as SQAS can only be measured by the rate at which it is used, and data show that the chemical industry is making increasing use of audit reports. In 2017 there were almost 1,000 SQAS assessments carried out, including an alltime record of 572 assessments of transport companies. The number of SQAS reports being consulted by chemical companies is also rising steadily, from around 3,000 in 2012 to almost 6,000 last year.
The value that SQAS provides has not gone unnoticed in other parts of the world; Cefic has supported and helped other regional associations establish SQAS-like local schemes in the Middle East (through the Gulf Petrochemical Association), China, Taiwan, South Africa and Brazil.
One aspect of that international support has been in the area of the recruitment, training and monitoring of SQAS assessors. Cefic knows that the quality of any assessment system depends on the reliability of those carrying out the assessments and has in
place a solid management system to monitor their performance.
Indeed, Trapani says, the SQAS management committees that are in charge of the technical and strategic aspects of SQAS are permanently challenging themselves to improve the system. In December 2017, Cefic called a strategic review meeting with stakeholders to brainstorm new ideas and concepts.
As part of the continuous improvement process, Cefic is this year revising the questionnaires used in SQAS assessments. As shown in the panel below, the structure is being changed with the aim of mirroring the structure of an effective safety management system. Indeed, this should be helpful to those companies that base their in-house systems on the SQAS format. Together with other significant changes designed to improve the system, these new questionnaires will be launched in January 2019.
The new structure has five sections rather than three, which is more in line with the latest version of ISO 9001. Within that, the sub-section about IT security has been upgraded and new questions have been added concerning measures to avoid microplastics contamination in rivers and seas.
In the SQAS Transport Service questionnaire, the section relating to subcontracting has been improved and there will be a significant reduction in the total
number of questions. This is designed to allow the assessor to concentrate on areas for improvement. The SQAS Warehouse questionnaire will have a new section about bagging and an upgraded section on physical security. The SQAS Tank Cleaning questionnaire will have upgrades to its sections on effluent treatment and loaded tank heating.
“There are other important changes, not related to the questionnaires, that will be communicated in the SQAS General Assembly on 14 June,” Trapani states. HCB
THOSE SHIPPING PACKAGED dangerous goods by sea are often frustrated by unforeseen restrictions. The International Maritime Dangerous Goods (IMDG) Code is a long and complex manual to work with, although at least it does set out the provisions applicable to dangerous goods of all classes when moving by sea, and also the complex stowage and segregation provisions that carriers have to observe.
Shippers do face problems at the interface between land and sea transport, not least in the area of the placarding of containers with some dangerous goods, but even when they have classified, packaged, labelled and documented their goods in accordance with the IMDG Code they can still face delays to their shipment. Often this is to do with the specific restrictions imposed by ports around
the world; liner carriers take pains to ensure that their vessels do not get delayed simply because they have the ‘wrong’ cargo onboard, as that can prove extremely expensive.
Container lines generally collate their own lists of restrictions in relation to house policies, shipowner policies, ship constraints and restrictions applied at ports/terminals of loading, transit, transhipment and discharge. This approach is inconsistent, hugely burdensome and delivers no competitive advantage.
For many years, many of the major container shipping lines have relied on the Hazcheck software system from Exis Technologies to ensure that dangerous goods are being shipped and carried in accordance with
the IMDG Code. Recently, Exis has been working on a way to incorporate those port restrictions into the system, as well as carrier, ship and partner line restrictions, which should simplify the end-to-end management of the dangerous goods booking process.
This system, the Hazcheck Restrictions Portal, has now moved into an implementation phase, a development that was announced at the Multimodal 2018 event in Birmingham, UK at the start of May. With the support of two leading mutual insurers, the TT Club and UK P&I Club, the Portal concentrates on urging container lines, ports and terminals to upload information on their dangerous goods handling policies and restrictions, improving visibility for shippers, forwarders and others involved in the consignment and movement of such goods.
“As recent incidents of onboard fires have shown, the cocktail of dangerous goods [on a container ship] can have catastrophic effects,” says Peregrine Storrs-Fox, TT Club’s risk management director. “There are numerous issues involved, but the business case to engage with a uniform data process is clear. All supply chain stakeholders benefit from improving clarity for carriage by sea; the most urgent need is for the port/terminal community to commit to upload and maintain the relevant data via the Exis portal.”
UK P&I Club’s Stuart Edmonston is equally supportive: “We are delighted to collaborate with Exis in promoting the work on this portal. Clearer information on how dangerous goods should be correctly handled and shipped is vital in avoiding loss of life and damage to ships and cargo at sea. Our recently published guide Book it right and pack it tight also encourages best practice for packing dangerous goods for carriage by sea.”
Simple comparisons demonstrate that there are material differences in understanding and interpreting the way that port/terminal prohibitions, restrictions and additional requirements operate. Exis Technologies is encouraging stakeholders to take advantage of this new opportunity to make their own rules and regulations clearer to users of shipping and port services. HCB www.existec.com
BATTERIES • EFFECTIVE CONTAINMENT OF LITHIUM BATTERY FIRES IS NOW POSSIBLE, THANKS TO AN INNOVATIVE GRANULATE MATERIAL DEVELOPED BY CELLBLOCK FCS FOR USE IN ANY PACKAGING
CELLBLOCKEX IS AN innovative new product to aid in transporting dangerous goods. The dry material is an ideal packaging filler for shipping class D goods, including damaged or defective lithium ion batteries, as an alternative to vermiculite (see below). Its introduction is timely, given the prevalence and magnitude of lithium battery incidents.
Developed by CellBlock Fire Containment Systems in the US, the non-crystalline glass granulates that comprise CellBlockEX are offered in a number of products for various industries. The company manufactures fireand smoke-suppression systems for aircraft, fire-suppression pillows, hazmat drums,
battery storage cabinets and cases, and fire-resistant substrates.
Miami Air International, an airline with one of the highest safety ratings in the industry, was an early adopter of the products. In discussions with sports teams that were contracting with the airline, a need was identified to carry large amounts of spare lithium ion batteries and devices. This was seen as an unacceptably high risk for the airline.
Armando Martinez, senior director of safety and security for the airline, was tasked with finding a solution. During his research he developed a demanding list of requirements: the container for the batteries and devices must withstand the pressure pulse from an explosion and safely release the buildup of pressure; there must be an integral means to extinguish the fire; toxic smoke must be filtered; and the outside of the container must remain cool to the touch even if a device or battery were currently undergoing thermal runaway inside.
Armando approached CellBlock FCS with his criteria. While it already offered a product that satisfied all his requirements, it worked to fully customise a transport and storage
case that would best meet the needs of both the airline and the teams.
Underwriters Laboratories and Stress Engineering Group recently completed testing of the transport and storage cases. The test, which focused on preventing propagation in a box of twenty-five 18650 lithium-ion cells at 100 per cent state of charge, was a resounding success, CellBlock says. The cells were placed inside the case and the centre cell was heated with a cartridge heater until the battery exploded. Upon ignition the CellBlockEX granulate, which is housed in the lid of the case, deployed automatically and propagation was immediately halted. No other cell was involved in the fire and the outside temperature of the case remained ambient.
Lithium ion battery fires generate intense heat but there is also rising concern regarding distribution of toxic gases. Hydrogen fluoride can be rapidly released at the onset of a thermal event. Applying water, a frequently used way to deal with a lithium ion battery fire, can accelerate the release of gases and, according to recent research, creates a very toxic by-product of hydrofluoric acid. Because CellBlockEX is a dry medium, it combats the formation of gases by binding them to its porous surface.
CellBlockEX has a number of other advantages: it is environmentally friendly and sustainable, as it is manufactured from 100 per cent recycled glass, and is reusable; it is non-crystalline in nature, so it poses fewer health risks than vermiculite; and it has performed well in drop tests.
Dangerous goods packaging is often about the containment of contents in the event of an incident. Kevin Dougherty, a hazard goods expert and director of operations worldwide for Air Sea Containers Ltd, points out that adding CellBlockEX loose-fill as a fire suppressant very effectively raises the bar on safety standards. It can be incorporated into packaging to suit the transport of lithium batteries and any other hazardous substance or article that can cause a fire or explosion. HCB www.cellblockfcs.com
The US National Transportation Safety Board (NTSB) has released preliminary results of its investigation into a fire during the transport of high-pressure hydrogen gas cylinders in Diamond Bar, California in February 2018. The Board found that three pressure relief devices had been incorrectly set, allowing hydrogen to vent, and that some vent tubes had become detached from the assemblies, allowing the gas to vent to the interior of the trailer, fuelling the fire.
Following the investigation, Air Products has inspected the rest of its fleet and found improperly secured vent tubing in around half the lines inspected. NTSB investigators have already visited the Air Products facility in Santa Fe Springs, California and the FIBA Technologies cylinder requalification facility in Adelanto, California. Further inspections are planned for the cylinder pressure relief device manufacturing in Valley View, Ohio.
The preliminary report can be downloaded from the NTSB website, www.ntsb.gov.
The US Chemical Safety Board (CSB) has released its final report into an explosion in February 2017 at the Packaging Corporation of America’s (PGA) pulp mill in DeRidder, Louisiana (right) that killed three contract workers. Those killed were welding above a storage tank containing a flammable mixture of ‘foul condensate’ – mostly water but with a floating layer of turpentine.
Under normal operating conditions the atmosphere in the tank was not explosive but, during annual maintenance and after a period during which the turpentine had not been skimmed off (resulting from confusion as to whose responsibility it was), a flammable atmosphere had been generated in the tank, which was likely ignited by the welding operation.
“As seen in this incident, hot work conducted around tanks containing flammable materials
can be catastrophic,” says CSB chair Vanessa Allen Sutherland. “That is why it is so important for companies to effectively identify, evaluate, and control potential hazards prior to initiation of hot work.”
CSB issued a series of recommendations to PGA, including the application of effective process safety management procedures and National Fire Protection Association (NFPA) standards 69 or 68 on explosion prevention and protection. PGA was also asked to provide workers with periodic training to ensure they have an understanding of all process safety hazards applicable to areas of their responsibility and job tasks, including the safety conditions needed to permit hot work.
An illuminating animation describing the incident and its likely causes is available on the newly revamped CSB website, www.csb.gov.
CSB has also started an investigation into an explosion at the Husky Energy oil refinery in Superior, Wisconsin on 26 April 2018. The incident happened while the refinery
was being closed down for a five-week maintenance turnaround. The explosion took place in the fluid catalytic cracker unit and injured several people.
The CSB team is now narrowing its focus to determine the cause of the blast and has engaged a metallurgical expert to help identify any failings in the equipment. A large amount of debris has been recovered from a wide area and is being stored for future analysis. CSB promises further updates as its investigation continues.
The US Pipeline and Hazardous Materials Safety Administration (PHMSA) has produced a brochure to promote its hazardous materials Accident Investigation Team (AIT) pilot programme to hazmat and emergency first responder stakeholders.
Fundamentally different from traditional PHMSA Hazardous Materials Regulations enforcement efforts, the one-year AIT pilot was launched in October 2017 to develop a comprehensive investigative process for significant hazmat accidents and incidents.
This process includes identifying contributing and root causes with the purpose of learning from past mistakes to enable forecasting and mitigation of future hazmat accidents.
In addition, PHMSA expected the pilot will improve the quality of investigations by strengthening full-time investigator expertise through comprehensive training in root cause analysis, and also strengthen the agency’s stakeholder outreach and partnerships with the modal agencies under the US Department of Transportation (DOT).
Those looking for more information can email HM_Accident_Investigation@dot.gov.
The Institute of Hazardous Materials Management (IHMM) is to introduce new exam specifications for the Certified Dangerous Goods Professional (CDGP) credential on 15 October 2018. The changes follow a job task analysis completed earlier this year, which is required to ensure the exam remains relevant to current industry practice.
The new exam blueprint can be downloaded from the IHMM website, www.ihmm.org.
The Oil Companies International Marine Forum (OCIMF) has published an information paper on safety-critical equipment and spare parts. The paper provides guidance on identifying safety-critical equipment for the purpose of developing a safety management system (SMS).
“The identification of safety critical equipment and the need for safety-critical spare parts is a complicated subject”, says OCIMF director Andrew Cassels. “This paper provides guidance on the challenges that may be encountered when considering safety-critical spare parts so that a ship owner can strive to efficiently manage their risks.” The paper is free to download from the OCIMF website at www.ocimf.org/library/information-papers/.
The British Compressed Gases Association (BCGA) has produced a new guide providing comprehensive advice on the key issues surrounding the transport of compressed gases by road. Guidance Note 35 (GN35), Vehicle Selection and Transport Management, brings together for the first time key criteria and information of value to manufacturers, transport and freight operators alike.
The Note includes advice on vehicle selection, the recruitment, training and assessment of personnel, as well as the relevant elements relating to a transport management system associated with Class 2 dangerous goods. A wealth of useful associated
information, including a comprehensive listing of key contacts, agencies and organisations of relevance is also featured, signposting readers to further information in specific areas.
“GN35 is a completely new guidance document, which pulls together a wealth of information in to one place,” says Doug Thornton, chief executive of BCGA.
“The purpose of BCGA’s Guidance Notes is to recommend good practice and give information for safe procedures in the fields of production, distribution and the application of gases, or for the use of gas equipment. They take account of overarching legislation and assist in ensuring compliance through the development of controls to improve industry standards. GN35 is an important addition to the wide range of respected documents already available providing information in accordance with these objectives.”
All BCGA Guidance Notes can be downloaded free of charge from the Association’s website, www.bcga.co.uk.
The European Association of Dangerous Goods Safety Advisers (EASA) elected a new board at its eighth general Assembly in Brugge, Belgium in early May. Maria Nicopulos from the Polish DGSA association SDGSA was elected the new president, succeeding Norbert Müller, with Hersper Hornum form the Danish association FASID stepping up as the new vice-president. Gaston Zens of Luxembourg was re-elected as general secretary.
THE JOINT MEETING of the RID Committee of Experts and the Working Party on the Transport of Dangerous Goods (WP 15) of the UN Economic Commission for Europe (ECE) held its spring 2018 session in Bern from 12 to 16 March 2018. The meeting was chaired by Claude Pfauvadel (France) with Helmut Rein (Germany) as vice-chairman.
The session was attended by representatives of 22 states, the European Commission, the EU Agency for Railways (ERA), the Organisation for Cooperation between Railways (OSJD) and 12 non-governmental organisations.
The main business of the Joint Meeting is to discuss matters of relevance to the transport of dangerous goods by road, rail and inland waterway in those countries that are party to the regulations under the RID (rail), ADR (road) and/or ADN (inland waterway) agreements. That work largely, though not exclusively, involves transposition
of the amendments made to the UN Model Regulations that are common across transport modes, leaving the modal bodies to deal with issues of particular relevance.
By this stage in the biennium, the changes featured in the 20th revised edition of the UN Model Regulations had largely been dealt with. There were, though, plenty of other matters to clear up before the amendments that will appear in the texts of RID, ADR and ADN that will enter into force in 2019 can be finalised.
Documents relating to tanks were, as usual, entrusted to the Working Group on Tanks, which was chaired by Arne Bale (UK).
Poland had a question on the qualification of welding procedures, noting that EN ISO 15614-1:2017 offers two levels. Level 1 is based on the ASME standard, while Level 2, which is more severe, was contained in
earlier versions of the standard. The Pressure Equipment Directive and Simple Pressure Vessel Directive mandate use of Level 2, but does this also apply to tanks of RID/ADR?
It was noted that Level 2 is more comprehensive and therefore more expensive; however, both give sufficient proof that welding procedures are accurate. EN 12972:2018 allows Level 1 to be used for portable tanks. There was a feeling among several experts that Level 2 should apply, which should not be difficult to achieve as manufacturers and repair shops have had to meet that standard in the past. It was decided to await a comparison document from France for consideration at a future session.
The UK returned to the Working Group with a proposal to amend the provisions covering the information to be provided on the tank plate. This was based on previous discussions but at this point some experts had second thoughts, questioning what value would be provided by the change. The general feeling was that a standard would provide a good basis; EN 12561-1 already exists but is only applicable to tank wagons. It was suggested that the European Committee for Standardisation (CEN) could develop a more generally applicable standard.
The International Union of Private Wagons (UIP) proposed an amendment to 6.8.2.1.23
MULTIMODAL • THE RID/ADR/ADN JOINT MEETING IN MARCH HAD A LOT TO GET THROUGH IF THE 2019 REGULATORY TEXTS ARE TO BE AVAILABLE IN TIME FOR PROMPT IMPLEMENTATION
to clarify that, while competent authorities need to approve tank manufacturers’ welding procedures, maintenance and repair shops should be approved by an inspection body. The idea was sound but the experts felt the wording could be better. A revised version proved acceptable, leading to the first sentence of the first paragraph of 6.8.2.1.23 being changed to: The ability of the manufacturer to perform welding operations shall be verified and confirmed by either the competent authority or by the body designated by this authority. The ability of the maintenance or repair shop to perform welding operations shall be verified and confirmed by the inspection body according to 6.8.2.4.5. A weld quality assurance system shall be operated by the manufacturer or the maintenance or repair shop.
The use of austenitic-ferritic stainless steel was introduced in 6.8.5.1.2(a) for the 2019 texts of RID and ADR at the autumn 2017 session. At the time, the proposed lower temperature limit of -40˚C was placed in square brackets as further consideration was thought necessary in order to reflect the use of such tanks to carry refrigerated liquefied carbon dioxide.
France had investigated the issue and recommended a lower limit of -60˚C. While there were some questions and not all experts were totally happy, the change was adopted.
France also returned to the issue of gravity-discharge tanks and the decision made for RID/ADR 2017 that the maximum working pressure does not apply to such tanks, according to 6.8.1.14(a). However, the promised revision of EN 13094 had not yet been published, leading to an incompatibility between the standard and the regulations. It was proposed that guidance be introduced for the 2017 and 2019 editions of RID and ADR.
This has been done through the addition of some notes. The existing notes in column (2) of 6.8.2.6.1 against EN 14432:2014 and EN 14433:2014 are both amended to read: NOTE: This standard may also be used for gravity-discharge tanks.
A new note is added in column (2) against EN 13094:2015, for ADR only: NOTE: See also the guideline on the website of the secretariat of the United Nations Economic
Commission for Europe (http://www.unece.org/ trans/danger/danger.html).
That guideline for the application of EN 13094:2015 for compliance with ADR 2017 and 2019 was also agreed; it lists the amendments to the standard that are necessary. It will be posted on the UN ECE website in due course.
Germany proposed that the square brackets in footnote 4/2 to 6.8.1.18 could be removed for the 2021 editions of RID and ADR, as the latest draft for revision of EN 13094 provides for safe construction. It was not necessary to make the change for the 2019 texts as 6.8.2.7 allows the standard’s early use. The footnote now reads: However the cross section of shells according to 6.8.2.1.14 (a) may contain recesses or protrusions such as sumps, cut-outs or recessed manhole constructions. They may be constructed of flat or shaped (concave or convex) sheet metal. Dents and other unintended deformations shall not be regarded as recesses or protrusions.
France provided some legal information on the acceptance of electronic documents and signatures for tank inspection certificates, a topic that had been raised at the autumn 2017 session; several experts noted that their authorities already accept electronic documents, a position the working group supports.
A further paper from France provided more information on bursting pressure at working temperature, allowing a revision provisionally adopted at an earlier session to be completed and adopted. The second sub-paragraph in 6.8.2.2.10 is amended to read:
Except for tanks intended for the carriage of compressed, liquefied or dissolved gases where the arrangement of the bursting disc and safety valve shall be such as to satisfy the competent authority, burst pressures of the bursting disc shall satisfy the following requirements:
• the minimum burst pressure at 20°C, tolerances included, shall be greater than or equal to 0.8 times the test pressure,
• the maximum burst pressure at 20°C, tolerances included, shall be less than or equal to 1.1 times the test pressure, and
• the burst pressure at the maximum service temperature shall be greater than the maximum working pressure.
A pressure gauge or another suitable indicator shall be provided in the space between the bursting disc and the safety valve, to enable »
detection of any rupture, perforation or leakage of the disc.
In the new transitional measures in 1.6.3.49 and 1.6.4.51, “nominal pressure of the bursting disc” is replaced by “burst pressure of the bursting disc”.
The Netherlands queried the interpretation of the marking requirements in 6.8.2.5.2 and 6.8.3.5.6 and whether they should be visible during carriage; the paper also thought 4.3.3.3.2 should be reviewed, particularly the requirement to cover up the names of gases not being carried. The experts felt that the first part of the query was not an issue, as folding panels are fixed to the sides of tank wagons. However, it was agreed that 4.3.3.3.2 should be looked at and the Netherlands offered to draw up an official document.
The UK presented the report of the seventh meeting of the informal working group on the inspection and certification of tanks, which was held in London in December 2017. The group had covered a lot of ground and it was expected that formal proposals for the revision of 1.8.6 and 1.8.7 would be available in time for the eighth meeting in early May. The group was advised to concentrate on those revisions, and the revision to 6.8.
The International Union of Railways (UIC) asked whether the requirement to mark the actual holding time in the transport document, as prescribed in 5.4.1.2.2(d), applies to empty uncleaned tanks. The experts felt that it is important to do so but realised the problems faced. The European Industrial Gases Association (EIGA) is already working
on issues relating to empty tanks and it was asked to take UIC’s question into account.
UIC also brought to the table discussion of the new breed of extra-large tank containers, which are designed primarily for use in rail transport. The matter had already been discussed by the RID standing working group but the advice of the Joint Meeting was sought. The size of such tanks – capacities of up to 73,000 litres, as opposed to 36,000 litres for standard tanks – means that they are subject to increased pressures from liquid surge. It was agreed to introduce a new footnote in 6.8.2.1.2, cross-referencing 7.1.3, but the experts felt that other matters needed to be looked at in greater detail. The experts felt that this work should be carried out by the RID working group on tank and vehicle technology.
The UK raised two questions on the use of vacuum-operated waste tanks in respect of ADR but the experts were of the opinion that no action was needed.
The International Tank Container Organisation (ITCO) queried the definition of ‘operator’ in 1.2.1, which creates difficulties with leased tanks. In some countries, penalties are levied on the tank owner, which may not be the actual operator. ITCO was invited to consider a formal proposal for amendment.
CEN advised the Joint Meeting of progress made with new and revised EN and EN ISO standards that are or are intended to be referenced in RID, ADR and/or ADN. The working group on standards considered
the document and proposed several changes to the 2019 texts, on condition that the 2018 editions of the standards concerned were available by 1 June 2018.
• In 6.8.5.4, reference to EN 1252-2:2001 Cryogenic vessels – Materials – Part 2: Toughness requirements for temperatures between -80˚C and -20˚C is replaced by reference to EN ISO 21028-2:[2018]
• In 6.2.4.1, the table will include EN ISO 14246:2014+A1:2017 Gas cylinders –Cylinder valves – Manufacturing test and examinations; applicability of the 2014 text will expire on 31 December 2020
• In 6.8.2.6.1, the table will include EN 12972:[2018] Tanks for transport of dangerous goods – Testing, inspection and marking of metallic tanks, mandatory from 1 January 2021; the same revised standard is added in 6.8.2.6.2, with the existing 2007 standard only applicable to 30 June 2019 and the new version mandatory from that date
• In 6.8.2.6.1, EN 13317:[2018] Tanks for transport of dangerous goods – Service equipment for tanks – Manhole cover assembly is added after the reference to EN 13317:2002 + A1:2006, applicability of which will expire on 31 December 2020
• In the same table, EN 14025:[2018] Tanks for the transport of dangerous goods –Metallic pressure tanks – Design and construction is added after the 2013 edition, applicability of which will expire on 31 December 2020
• In the table in 6.2.5.1, EN 1442:2017 LPG equipment and accessories – Transportable refillable welded steel cylinders for LPG –Design and construction is added after the existing 2006 version, which expires on 31 December 2020.
New notes are added for EN 12245 in 6.2.4.1, one in column (2):
NOTE: This standard shall not be used for cylinders and tubes without a liner, manufactured from two parts joined together.
And a second in column (5):
31 December 2019, for cylinders and tubes without a liner, manufactured in two parts joined together.
These notes have been added to address an issue identified by the European LPG Association (AEGPL) after a number of incidents involving two-piece composite
LPG cylinders. AEGPL noted that there is a withdrawal programme in place for such cylinders and the Association was invited to keep the Joint Meeting updated on progress.
Poland sought clarification of the meaning of ‘readily flammable material’ in special provision CW24/CV24 in 7.5.11 and its allocation to substances of Class 8 with a Division 5.1 subsidiary hazard. In particular, its paper asked if organic peroxides of Division 5.2, packed in accordance with packing instruction P 520/IBC 520, can be transported on wooden pallets.
The Joint Meeting agreed that the use of wooden pallets is allowed; the term ‘readily flammable material’ is intended to address filling or cushioning materials such as a hay, paper and vegetable fibres. The European Chemical Industry Council (Cefic) offered a revised text for CW24/CV24, which received some support. Cefic and Poland were invited to work on the text and submit an official proposal at the next session.
The Joint Meeting agreed with Poland’s observation that there are discrepancies in the application of CW24/CV24 in RID and ADR. It felt that CW24 should be deleted for UN 1796 and 1826, PG II in RID and recommended the RID Committee of Experts confirm this. It also felt that CW24/CV24 should be added in column (18) of the Dangerous Goods List for the second entry under UN 2031 and invited both the RID Committee of Experts and WP15 to confirm that.
An informal document from France raised a question about the use of used packagings for the carriage of dangerous goods wastes, which it said can facilitate the waste management process by allowing incineration of the packaging along with its contents. However, in such cases it is impossible to assess the chemical compatibility of the packaging and its contents, although the risk involved is, France said, small.
It appeared that this type of operation is addressed differently in different countries. France offered to circulate a questionnaire to all contracting parties with a view to harmonising practices at international level.
UIC asked for alignment of the specifications for hazard labels and placards. At present, labels are allowed to deviate from the models, with the addition of text or numerals in the lower half. However, the same is not true for placards. It proposed some text to be added at the end of 5.3.1.7.1, which the Joint Meeting found agreeable:
The deviations specified in 5.2.2.2.1, second sentence, 5.2.2.2.1.3, third sentence and 5.2.2.2.1.5 for danger labels also apply to placards.
Referring back to discussions at the previous session, Germany came forward with a proposal to clarify the provisions regarding the language to be used on the transport document. As it stands, problems are being experienced, particularly in the return transport chain and with Class 1 articles. »
The Joint Meeting adopted the text, noting that it does not prohibit the use of other languages so long as one of French, German or English is also used. The change is found in a revised second sentence in 5.2.1.5: The mark, which shall be clearly legible and indelible, shall be in one or more languages, one of which shall be French, German or English, unless any agreements concluded between the countries concerned in the transport operation provide otherwise.
Another proposal from Germany also found favour. It spotted that UN 3132 had been omitted from the table in 1.1.3.6.3 under transport category 0, Class 4.3. The experts agreed and inserted “3132” after “3131”.
The secretariats of UN ECE and the Intergovernmental Organisation for International Carriage by Rail (OTIF) had supplied a brief list of amendments to recently adopted changes, and these were adopted by the Joint Meeting. The main changes are the addition of “bulk containers” after “large containers” in the title to 5.3.1.2. The first sentence of 5.3.1.2 in RID and the first paragraph after the Note to 5.3.1.2 in ADR are amended with similar language.
That in ADR reads:
The placards shall be affixed to both sides and at each end of the container, bulk container, MEGC, tank-container or portable tank and to two opposite sides in the case of flexible bulk containers.
Germany proposed a transitional period for the new provisions that require manufacturers and distributors to make the lithium battery test summary available, as recommended by the UN Sub-committee of Experts. This was readily adopted as a new 1.6.1.47:
Lithium cells and batteries not meeting the requirements of 2.2.9.1.7 (g) may continue to be carried until 31 December 2019.
Germany also followed up on discussions at the autumn 2017 session on the protection of valves on gas cylinders fitted with handling devices or other components. Its proposal was amended during discussion and, on the basis of a text drawn up by EIGA, 4.1.6.8 was amended with the addition of “and other components which are to remain connected to the valve during carriage (e.g. handling devices or adaptors)” in the first sentence after “Valves”.
The International Road Transport Union (IRU) proposed allowing refresher training for drivers of dangerous goods to be conducted by online means. This proposal divided opinion: some delegations felt there was no need for provisions on the topic, while others felt that ADR/ADN should at least provide minimum requirements. No agreement could be reached and IRU was asked to work intersessionally with interested parties with a
view to presenting a revised proposal at the next session.
Sweden proposed requiring wagons and containers carrying more than 8 tonnes of dangerous goods in limited quantities along with other fully regulated dangerous goods to bear the limited quantity mark. Sweden felt this would increase safety by alerting responders when there were significant amounts of limited quantity material and could be of interest on journeys passing through road tunnels. Again, opinion was divided and, after discussion, Sweden said it would take account of comments made and return with a revised proposal.
The European Aerosol Federation (FEA) proposed aligning RID/ADR/ADN with the new provisions of the EU Aerosol Dispensers Directive, 75/234/EEC, relating to the maximum allowed internal pressure. The Joint Meeting was ready to adopt the change until it was pointed out that such a move would cause disharmony and that the matter should really be taken up to the UN Sub-committee of Experts.
Spain noted that UN 2683 ammonium sulphide solution is assigned the hazard identification number 86 in column (20) of the Dangerous Goods List. This substance is corrosive, flammable and toxic; its flammability warrants the use of an FL vehicle. It should, therefore, have the
hazard identification number 836 – except this does not exist. Spain identified two other UN entries – UN 2029 hydrazine, anhydrous and UN 3484 hydrazine, aqueous solution, flammable, that have a similar list of hazards.
Opinion was once more divided; some welcomed the observation and felt that a more thorough investigation of existing hazard identification numbers would reveal further cases, while others felt that the system has been in place for a long time and should not be tinkered with. Spain was invited to submit a revised proposal, taking into account the comments made, and delegations that had identified other cases where action might be useful were invited to contact the Spanish delegate.
Germany reported that the ADN Safety Committee had agreed changes to the definition of ‘flash-point’ and suggested the same changes for RID and ADR. There was, though, no support for the proposal. Again, it was noted that any proposal for change should be taken to the UN Sub-committee of Experts.
Switzerland had had some success at the modal level with its proposal to amend CW36/CV36 to take account of the need for ventilation during the transport of gases in sheeted vehicles and those where the load compartment is not separated from the driver’s compartment. It had been asked, however, to take the proposal to the Joint Meeting, where it met with less enthusiasm. Germany noted that stakeholders can envisage problems with parcel services, and both EIGA and AEGPL wanted to seek advice from their members. Switzerland will come back with a revised version once those issues have been investigated.
Italy had been through the three official language texts and come up with a long list of discrepancies. The document was welcomed by the Joint Meeting but felt that more time would be needed to address all the issues raised; it would also be useful if the work could encompass ADN as well as RID and ADR. Delegations were invited to provide written comments to the representative of Italy.
EIGA updated the Joint Meeting on moves to harmonise provisions for UN pressure
receptacles, particularly between RID/ADR signatories and the US. It was noted that regulatory procedures in the US are still ongoing. EIGA will continue to work with its counterparts in the US and will provide more feedback at the next session.
An informal working group led by Romania and UIC had been working on new definitions for ‘danger/hazard’ and ‘risk’ and offered its suggestions. The Joint Meeting could not agree and advised the group to continue, firstly identifying ways in which those terms can be avoided throughout the regulatory texts. The results of that work will be presented at the autumn 2018 session.
The Joint Meeting also heard from the informal working group to update the architecture for dangerous goods telematics and the informal working group on the reduction of the risk of a BLEVE during transport of dangerous goods. Both groups will continue with their work.
ERA informed the Joint Meeting that the first edition of the framework guides on inland transport of dangerous goods risk management had been finalised and will be published shortly on the ERA website. Both Spain and the UK felt that further work was needed before the guides could be applied, not least since the volume of data is as yet insufficient to be reliable. ERA is to set up a group of experts that will be involved in taking the project forward.
ERA also reported on the list of parameters to be used in the harmonised risk estimation method and on the development of a Railway Common Occurrence Reporting (COR) System, something that is still at the conceptual stage. This work, ERA said, should coordinate with the work of the Joint Meeting on section 1.8.5 of RID/ADR/ADN; if not, any action ERA takes may not be fully aligned. HCB
The amendments adopted by the Joint Meeting for entry into force in 2019 require confirmation by the modal bodies, which was to take place at their respective meetings in May. HCB will report on those sessions in a forthcoming issue.
The next session of the Joint Meeting will take place in Geneva from 17 to 21 September.
A NEW REQUIREMENT relating to the transport of lithium cells and batteries has the potential to create confusion in the dangerous goods community over the coming two years.
The requirement, which involves the lithium cell and battery test summary, appears in the sixth revised edition of the Manual of Tests and Criteria as a new paragraph 38.3.5, following major reconfiguration of the testing procedures contained in section 38.3.
The intent of section 38.3 is to ensure that cells and batteries are properly tested so that
they will travel safely through the logistics chain.
The testing and subsequent documentation also ensures that counterfeit batteries that have not been tested – and that are identified as being responsible for fires during transport – are kept out of the supply chain.
The new 38.3.5 requires completion of a test summary, which must include:
• The name of the manufacturers of the cell, battery or product, as applicable
• Contact details for that manufacturer, including address, phone number, email address and website for more information
• Name of the test laboratory, with contact details as above
• A unique test report identification number
• The date the test report was completed
• Description of the cell or battery, including at a minimum:
Whether it is lithium ion or lithium metal, Its mass,
The Watt-hour rating or lithium content, A physical description, Model number(s).
A list of the tests conducted and their results (i.e. pass/fail)
Reference to assembled battery testing requirements, if applicable (i.e. 38.3.3(f) and (g))
Reference to the revised edition of the
Manual of Tests and Criteria used and to amendments thereto, if any, and A signature with the name and title of the signatory as an indication that the information provided is valid.
Paragraph 38.3.5 also states that, “The following test summary shall be made available”. The 20th revised edition of the UN Recommendations on the Transport of Dangerous Goods includes a similar requirement at 2.9.4(g): “Manufacturers and subsequent distributors of cells or batteries shall make available the test summary…”.
This raises the question: make available to whom? Paragraph 2.9.4(e)(iv) says that “Test data shall be kept and made available to the competent authority upon request” and the test summary must also be available to any enforcement officials that need to refer to it in the event of an incident involving a lithium battery shipment.
That suggests that the test summary itself will have to be passed on from the manufacturer, importer or supplier along the supply chain to initial and subsequent distributors, freight forwarders and buyers –the same requirement will apply to cells and batteries that are included in or packed with equipment, and the logistics chain of those goods, down to the retail level.
As the requirement stands, there is no need for the document to be available to carriers. As such, it cannot be seen as part of the transport document. But could that change? At some point, carriers’ insurance companies may decide that they need confirmation that the batteries being carried by the insured’s vehicles have been tested according to section 38.3 and have passed the relevant tests. The document could also be demanded by third-party logistics companies engaged in contract packing and shipping activities on behalf of their customers.
As with most regulatory changes, the key to preparedness is comprehensive and consistent training. Only that way can organisations ensure that the requirement is understood and implemented correctly, and that the
requirement is communicated properly to other parties further along the logistics chain.
Organisations need to start planning for training and implementation now. This planning process will need to include an audit of current battery inventories and manufacturers so that a document control system can be implemented. The planning process must also make sure that those responsible for procuring cells and batteries know that they must receive the test document along with the cells or batteries being purchased.
Once identified and received, the test summary documents should be sent to those responsible for record retention for other dangerous goods-related documentation to ensure the information is readily available on request. As of now, there is no record retention requirement for this document, which means that the
document should be available at all times. Lastly, training and implementation should involve an understanding of what the document is and when it is required to be supplied to the officials requesting it.
As with all the other provisions for lithium batteries over the years, this requirement for the test summary is sure to create some confusion and misapplication over the course between now and the mandatory date of January 2020. That is why it is imperative to ensure that correct and timely information is available to all stakeholders involved in the safe and legal transport of lithium cells and batteries. HCB
*Michael Bowen is president of Bureau of Dangerous Goods Ltd, a leading producer of training, technology and consulting for the dangerous goods industry; he is a certified Dangerous Goods Safety Adviser (DGSA) and
IATA Dangerous Goods Instructor. He regularly teaches and/or speaks at various industry trade associations such as COSTHA, DGAC and IATA and was the leading content developer for Hazmat University. He urges his team and clients to embrace and promote a culture of compliance for dangerous goods. For more information go to www.BureauDG.com.
MOST OF US who are involved in the transport of dangerous goods (DG) are well aware that the regulations are updated every two years. Every second autumn, DG professionals eagerly await the arrival of their new ‘regs’. The changes in the UN Model Regulations on the Transport of Dangerous Goods are issued by the UN every other year. First published in 1956, these Model Regulations - also known as the ‘Orange Book’ - set out recommendations that the regulators for each transport mode are expected to adopt
in the next round of amendments. These will, in turn, form the basis for national and international regulations.
Following that biennial publication from the UN, every two years the International Civil Aviation Organisation (ICAO) produces a new edition of its Technical Instructions for the Safe Transport of Dangerous Goods by Air and the International Maritime Organisation (IMO) publishes an amendment to the International Maritime Dangerous Goods (IMDG) Code.
For road, all EU member states and some other countries around the world are signatories to European Agreement concerning the International Carriage of Dangerous Goods by Road (ADR). Each country adopts the Agreement into its own legislation - sometimes with country-specific variations. The same applies to the regulations concerning the International Transport of Dangerous Goods by Rail (RID) and the International Carriage of Dangerous Goods by Inland Navigation (ADN).
So far so good: all the rules are updated every two years, with the aim of maintaining harmony across the modes. However, there are different timelines for implementation. The revised ICAO rules become obligatory on 1 January; there is a six-month transitional period for ADR, RID and ADN; and the IMDG Code has a one-year transition.
Elsewhere in the world, the US (in the form of the Hazardous Materials Regulations in 49 CFR), Canada (the TDG Regulations) and Australia (the ADG Code) have their own multimodal regulations based on the UN Model Regulations.
In addition, the International Air Transport Association (IATA) produces its Dangerous Goods Regulations (DGR), which incorporates the ICAO Technical Instructions as well as a raft of State and Operator variations. This is updated every year and is recognised by airlines and industry worldwide as the primary user-friendly reference for shipping dangerous goods by air.
So, as we head into the middle of 2018, DG professionals around the world are looking at how the changes that will start taking effect at the beginning of 2019 will affect their operations. One way to keep on top of those changes is to attend a regulatory update seminar such as the Biennial Dangerous Goods Roadshow, organised and hosted by Labeline International and HCB.
UPDATE • 2019 IS NOT FAR AWAY AND THE RULE CHANGES IT WILL BRING WITH IT WILL SOON BE WITH US. LABELINE AND HCB ARE OFFERING A COST-EFFECTIVE WAY TO STAY UP TO DATETHIS YEAR’S BIENNIAL ROADSHOW WILL ONCE AGAIN KICK OFF IN HEATHROW, BEFORE MOVING ON TO A SECOND SEMINAR NEAR MANCHESTER AIRPORT
Timed to coincide with the publication of the new regulations, this important international event offers an excellent training and networking opportunity for all those involved in the movement of dangerous goods: safety advisers (DGSAs), training providers, shippers, warehousing and distribution operatives, freight forwarders, administrators, procurement teams, manufacturers, fleet operators, airline service personnel, shipping lines and so on.
This year’s Roadshow will consist of two seminars, with identical content:
• 13 November at the Sheraton Skyline Hotel, Heathrow
• 15 November at the Radisson Blu Hotel, Manchester Airport.
Each venue has been chosen for its location, accessibility, excellent features and the quality of their catering. A free ice-breaker drinks reception will be held on the evening prior to each seminar. During intervals there will be the opportunity to meet with leading suppliers to the industry, including Labeline, HCB, DGOffice, Exis Technologies, Air Sea Containers, Braemar Howells, Unisto, IATA, NCEC and UL Safeware. There will also be the chance to interact with the speakers and network with delegates from around the world and across all sectors of the DG industry.
The organisers have listened to the feedback from the inaugural seminars in 2016 and have tweaked the presentations, resulting in a more interactive format. There will be a panel of world-renowned exports to discuss how the changes have been adopted into the various modal rulebooks, once more under the watchful eye of the chairman for the event, HCB’s editor-in-chief Peter Mackay.
Sitting on the multimodal panel will be:
• Jeff Hart OBE, former chairman of the UN
Sub-Committee of Experts on TDG, who currently provides advice to the Dangerous Goods Advisory Council (DGAC) on issues relating to the IMDG Code.
• Geoff Leach, former head of the UK Civil Aviation Authority’s (CAA) Dangerous Goods Office and a past chairman of the ICAO Dangerous Goods Panel, on which he still sits. He also chairs the IATA Lithium Battery
Workshops. At the Heathrow event Geoff will be replaced by Ross McLachlan, who succeeded Geoff as the ICAO DGP member nominated by the UK. He was responsible, amongst many other things, for overseeing the CAA Approved Dangerous Goods Training Scheme.
• Richard Masters, who was the on the team that created Felixstowe’s dangerous goods control system and has since worked with the UK P&I Club, for whom he wrote the IMDG Code guidance manual Book it Right and Pack it Tight, which has recently been updated and reissued.
• Gene Sanders, chair of the Dangerous Goods Trainers Association (DGTA), a director of DGAC, consultant and trainer in dangerous goods for nearly 20 years and regular contributor to HCB. Other speakers lined up for the Biennial Roadshow include:
• PC Stuart Appleton, DGSA for three police forces and chair of the UK’s CDG Police Practitioners Forum. He has responsibility for all UK enforcement operations and UK Dangerous Goods Intelligence and represents UK police at European meetings.
• Ali Karim, managing director of the Hazchem Network in Rugby – the hub and spoke pallet network specifically tailored to dangerous goods. He has more than 30 years’ experience of dealing with chemicals and gas in a production as well as sea and road transport environment at a senior management level in the UK.
• Herman Teering, managing director of DGM’s IT company that operates the specialist DGOffice software solution for all modes of transport, production, storage and handling of dangerous goods, including wastes.
• Morgan Hyson, business development manager at the Institute of Hazardous Materials Management (IHMM), which operates the vocational Certified Dangerous Goods Professional (CDGP) qualification.
• Michael Bowen, president of Bureau of Dangerous Goods Ltd, a leading producer of training, technology and consulting for the dangerous goods industry. As a DGSA and IATA Dangerous Goods Instructor, he
regularly teaches and/or speaks at various industry trade associations such as COSTHA, DGAC and IATA and was the leading content developer for Hazmat University.
Labeline International is the world’s leading supplier of the dangerous goods regulations for all modes of transport (IATA, ICAO, IMDG Code, ADR, RID etc). In early 2016, Labeline’s managing director, Keith Kingham, and key account manager Richard Shreeve decided that the industry needed a regulatory update seminar that would appeal to all those involved in dangerous goods. It was agreed that profit would not be the driver for the event and that these seminars would be geared towards enabling companies to send more than one person to attend.
HCB was asked to be the marketing partner for the Biennial Roadshow and the inaugural series in 2016 was an undoubted success. The feedback from those who attended the series was very encouraging, with comments such as: “Thanks for a great event. Excellent content and presentations…” “It was good to meet so many experts and professional in this specialist industry…”
HCB is again the main media partner for the 2018 Biennial and we are delighted to be supporting Labeline again. This not-for-profit event is priced at just £135 per person. To book your place at this important event please contact Labeline on 0870 850 5051 / +44 (0)1271 817677 or sales@labeline.com. HCB
The International Air Transport Association (IATA) has issued a guidance note advising dangerous goods acceptance staff to no longer consider the thickness of the line around hazard labels as being any more than a “minor variation”. The guidance anticipates a change in the IATA Dangerous Goods Regulations and the International Civil Aviation Organisation’s (ICAO) Technical Instructions that will take effect on 1 January 2019, which will remove reference to the thickness of the line.
The UN Model Regulations had introduced a requirement that the line should have a minimum width of 2 mm; however, while this was brought into the IATA Dangerous Goods Regulations in its 56th edition, with a two-year transition period, ADR had delayed implementation until 2019. Meanwhile, the UN Sub-committee of Experts had decided to remove the provision. IATA advises that any variation from the model labels should henceforth be regarded as “minor” in accordance with the provisions of 7.2.2.3.2(a).
The US is also to take similar action. In response to a query from the Council on Safe Transportation of Hazardous Articles (COSTHA), the US Pipeline and Hazardous Materials Safety Administration (PHMSA) has confirmed that it is looking at the provisions introduced in the HM-215M rulemaking on the inner border of labels. The transition period for this requirement expires at the end of 2018. PHMSA now plans to remove the requirement and will issue a rulemaking on the subject shortly.
The US Pipeline and Hazardous Materials Safety Administration (PHMSA) has issued a request for information, seeking opinions on the development and use of automated technologies in the transport of hazardous materials by road and rail.
“In anticipation of the role surface automated vehicles and the technologies that support them may play in transportation, the movement of freight, and commerce, PHMSA requests comments from the public and interested stakeholders - including entities engaged in the development, testing, and integration of these technologies - on the potential future incompatibilities between the hazardous materials transportation requirements in the HMR and a surface transportation system that incorporates automated vehicles,” says the Administration.
More information, including discussion of salient points, can be found here: www.federalregister.gov/documents/ 2018/03/22/2018-05785/request-forinformation-on-regulatory-challenges-tosafely-transporting-hazardous-materials-by.
PHMSA’s Office of Hazardous Materials Safety (OHMS) held a public forum last month to present the results of recent projects, during which it solicited comments on current and future work. In particular, the forum aimed to identify research gaps in the classification and transport of energetic materials, safe transport of energy products, safe containment and transport of compressed gases, and the safe packaging and transport of charge storage devices.
One focus was a discussion on the safety gaps recently identified in a 2017 cooperative research report completed by the National Academy of Sciences, Safely Transporting
Hazardous Liquids and Gases in a Changing U.S. Energy Landscape.
HCB will monitor the outcome of the public forum and any new regulatory or enforcement measures that are generated.
Transport Canada has published an updated version of TC Standard TP 14877, Containers for
The revised edition, adopted in January 2018, incorporates recent Protective Directions and the new TC117 tank car specification; it also improves harmonisation between tank car requirements in Canada and the US, and updates the dangerous goods list to align with the 19th revised edition of the UN Model Regulations.
The new standard will come into force along with publication in Canada Gazette Part II of the Regulations Amending the Transport of Dangerous Goods Regulations (Containers for Transport of Dangerous Goods by Rail); Transport Canada expects this proposed amendment will be published in Canada Gazette Part I in the third quarter with a 60-day comment period and that publication in Canada Gazette Part II will not take place until autumn 2019. In the meantime, the 2013 version of TP 14877 remains in force.
Transport Canada has also opened a 60-day consultation on a first draft of the new Canadian General Standard Board CGSB43.145 standard, Design, manufacture and use of large packagings for the transportation of dangerous goods, Classes 3, 4, 5, 6.1, 8 and 9 The standard sets out the requirements for designing, manufacturing and marking of UN standardised large packagings and for the selection and use of large packagings.
Transport Canada has also revealed something of its plans to create a Transportation of Dangerous Goods Client Identification Database (CID), which will contain details of all businesses involved in the transport of dangerous goods. CID is expected to launch in 2020 or 2021 and will change how businesses interact with Transport Canada.
Businesses that handle, offer for transport, transport or import dangerous goods in Canada will be required to give details of relevant activities, including the type and volume of dangerous goods being handled and the modes of transport used.
The European Chemicals Agency (ECHA) has opened a consultation period on draft guidance on the interpretation and application of the new Annex VIII to the CLP Regulation. The annex deals with harmonised information relating to emergency health response used by poison centres. The draft is currently being considered by the Partner Expert Group, after which a wider consultation is planned prior to publication in December 2018. More details can be found on the ECHA website at https://echa.europa.eu/ support/guidance/consultation-procedure/ ongoing-clp.
The European Commission has meanwhile published the 11th Adaptation to Technical and Scientific Progress (ATP) to the CLP Regulation, which will apply from 1 December 2019. This latest ATP includes thousands of additions and changes to the harmonised list of classification and labelling of substances and mixtures. Suppliers may choose to use the new classification and labelling criteria as from now.
Meanwhile, a recent inspection of online sales of hazardous chemical mixtures found that 82 per cent were not compliant with the CLP Regulation. According to ECHA, more than 1,300 internet advertisings were checked during 2017, of which 95 per cent were from
professional online retail outlets. The majority of non-compliant advertisements lacked information on the hazard labels, as required by Article 48(2) of CLP. Appropriate enforcement measures were taken, including written or verbal advice but in some cases fines and criminal complaints were also imposed.
ECHA has also launched a dedicated website designed specifically to provide information to consumers and to make them more aware of the benefits and risks of chemicals in their daily lives. The websitehttps://chemicalsinourlife.echa.europa.eu/is available in 23 languages and provides useful information on the role of ECHA and the EU legislation designed to protect consumers.
“Thanks to the website EU consumers can now learn more about the chemicals in everyday products and about how to use them in a safe way,” says Marco Mensink, director general of Cefic, which has welcomed the move. “It is important to continue addressing consumers’ questions and educating them about the safe use of chemicals. We hope this website will help achieve that goal.”
The US Environmental Protection Agency (EPA) has prepared three draft documents
clarifying the circumstances under which it may disclose confidential business information, as required by the revised Toxic Substance Control Act (TSCA). The three documents, which have been released for public comment, relate to the release of information to: state, local and tribal authorities; environmental, health and medical professionals; and emergency responders.
EPA anticipates publication of the final documents this month. The drafts can be found on the EPA website at www.epa.gov/tsca-cbi/ requesting-access-cbi-under-tsca.
China’s Ministry of Emergency Management (MEM) has published a guidance notice on the Safety and Risk Assessment and Grading of Manufacture and Storage Enterprises of Hazardous Chemicals. The notice requires local occupational health and safety administrations to assess all such enterprises, which will result in their grading (somewhat akin to the tiers under the EU’s Seveso system) and the allocation of levels of oversight. Higher risk enterprises will be subject to more frequent spot checks.
MEM expects the assessments to be carried out by the end of September and to be repeated every three years.
After last month’s septic tank extravaganza, we return once more to the subject – and an explosion in Linyi in the Chinese province of Shandong on 17 April. The blast happened when children were playing nearby with firecrackers and it is thought that sparks from the firecrackers ignited flammable gas seeping up from a septic tank beneath a well. One child and an adult were injured in the explosion, which was caught on CCTV cameras.
Nearby residents heard rumbling and felt the ground shake; initially they thought it was another earthquake.
Chinese CCTV has had a good time of it lately, as far as the Back Page is concerned; the day before the septic tank incident, cameras caught smoke coming from the back of a car waiting at traffic lights in Yiwu, Zhejiang province.
Within minutes, two people scrambled out of the back seats and searched for the source of the smoke under the car. They were looking in the wrong place: when they opened the boot, firecrackers shot out in all directions.
It turned out that there was a box of firecrackers in the back of the car; they were ignited when one of the passengers decided it was time for a smoke and lit up. Remarkably, despite the firework show, once the smoke had cleared the driver and passengers got back in the car and managed to drive off.
Another regular topic on this page is methanol poisoning, either of those who don’t understand the difference between methanol and ethanol (as often happens in Russia) or badly produced bootleg liquor. There has
been a spate of the latter in Java, Indonesia, where more than 60 people have died lately.
Helpfully, there is a treatment for methanol poisoning, according to Knut Erik Hovda, a medical expert from Norway’s Oslo University Hospital. He told the Jakarta Post that methanol is broken down by the liver to formic acid, and it is that that causes the poisoning to be fatal. That process is neutralised by ethanol. Those who died only did so after their bodies had dealt with the ethanol in the bootleg hooch – 12 to 24 hours after drinking it. Keeping the ethanol level up prevents that metabolisation – though reports to not say how long the patients have to remain drunk.
We should point out, though, that the UK National Chemical Emergency Centre (NCEC) says that ethanol should only be used as a last resort and that fomepizole is the preferred antidote.
Speaking of recreational drugs, seven people were arrested in April after a spate of thefts of nitrous oxide cylinders from a hospital in Staffordshire, UK. The arrests came after a failed attempt to steal more gas from Cannock Chase Hospital.
The youth of the UK are increasingly turning to laughing gas to get a recreational high. They think they’re so modern and inventive, these kids – but the practice is not new. Indeed, according to that impeccable source Wikipedia, it was first recorded in 1799 as a craze among the upper classes in England. ‘Laughing gas parties’ were all the rage for a while.
The Back Page would like to note that we don’t necessarily recommend the use of nitrous oxide to achieve euphoria and hallucinations. Other recreational drugs are available, though preferably not methanol.