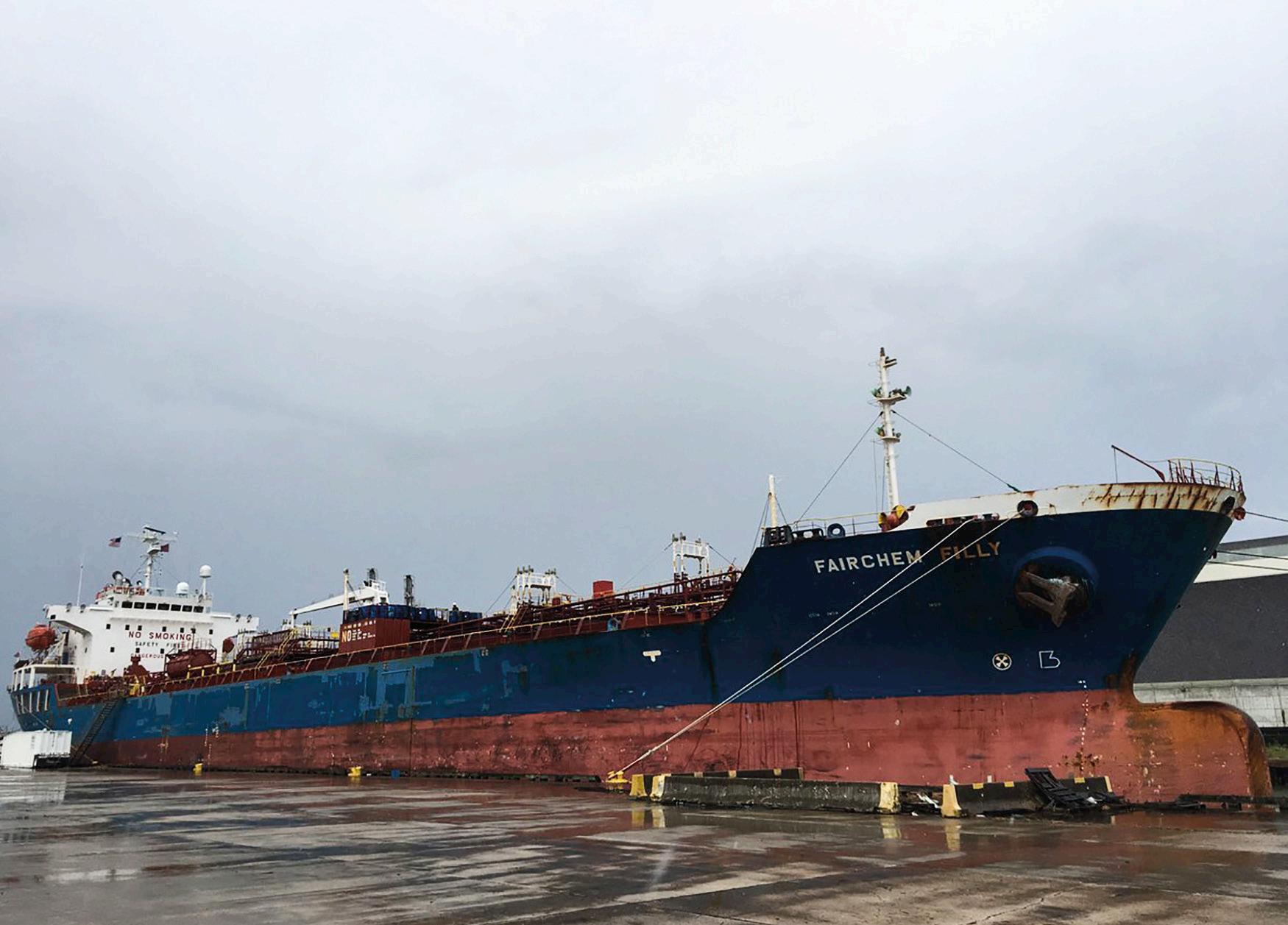
3 minute read
NTSB identifies communication issues
IT’S GOOD TO TALK
OVERPRESSURISATION • SHIP/SHORE COMMUNICATION IS VITAL TO ENSURE SAFE CARGO HANDLING. A RECENT REPORT FROM NTSB SHOWS WHAT CAN HAPPEN WHEN IT FAILS
AN INCIDENT ABOARD the chemical tanker Fairchem Filly in May 2019, during which a cargo tank suffered overpressurisation that caused damage to the ship and contaminated the cargo, was probably due to personnel failing to follow policies and procedures, combined with a lack of effective communication. This is the conclusion of an incident investigation undertaken by the US National Transportation Safety Board (NTSB), whose report on the incident has recently been released.
Fairchem Filly, a 2007-built chemical tanker with 20 stainless steel cargo tanks, arrived at Vopak’s Deer Park terminal on the Houston Ship Channel on 30 May 2019. Once the vessel was securely moored, cargo discharge operations began. Three of the ship’s crew, including the chief officer, and three shoreside personnel were involved. Only four of the cargo tanks were in cargo: one part-loaded with methyl isobutyl ketone and three full with hexene.
Hexene must be carried under a blanket of inert gas in order to prevent it being contaminated by oxygen; Fairchem Filly was using nitrogen as a blanket over the cargo. During discharge, the ullage volume increases as the cargo is pumped off, so additional blanketing must be provided. In this case, Vopak was supplying nitrogen from a shoreside system.
Vopak’s person in charge (PIC) met the chief officer onboard the ship and discussed the planned discharge; they completed the necessary paperwork and established the means of communication using UHF radio. The ship’s pumpman was assigned the task of operating the cargo manifold valves on the ship, while Vopak’s PIC was responsible for the shore valves.
At that point there was a shift change at the terminal, with the incoming dockman taking over the role of PIC. The ship was not informed of the change.
THE ACCIDENT BEGINS Discharge began from two of the tanks with hexene and, around 30 minutes later, low inert gas pressure alarms for both tanks sounded in the cargo control room. The chief officer made several attempts to contact the Vopak PIC by radio but failed to reach him. He ordered the ship’s pumpman to fully open the ship’s nitrogen valve, although he could not know whether the terminal’s nitrogen valve was open and, if open, how far. Shortly after, a further alarm indicated that the two tanks were experiencing high pressure and both pressure relief valves opened.
The crew reported that the vessel “surged” and ballast water began flowing through the vent and onto the deck. They turned off the cargo pumps to prevent the ballast water spilling over the side of the vessel.
The chief officer then re-established contact with the Vopak PIC and informed him that the vessel had experienced overpressurisation in both cargo tanks and that one had ruptured, releasing hexene into the adjacent ballast tank. All valves were closed and cargo transfer operations ceased. After the accident, the vessel’s cargo pressure monitoring system showed that the pressure had peaked at 109 kPa; the pressure relief valves were set to open at 20 kPa.
Following repairs at a nearby shipyard, damage to the vessel was estimated at $750,000. The loss of the contaminated cargo was valued at some $100,000.
WHERE IT WENT WRONG NTSB’s investigation found a number of failures on the part of both the crew and the terminal. The ship’s Quality, Health, Safety and Environment Management (QHSE) manual specified that, when receiving nitrogen from shore to blanket cargo, a 1-inch hose or orifice must be installed between the shore hose and the ship’s manifold in order to control the flow of nitrogen; during the incident, a 4-inch hose was connected directly to the manifold. The
POOR SHIP-SHORE COMMUNICATION WAS BEHIND