
11 minute read
VOLUME 42 • NUMBER
from HCB November 2021
Following on from the high-level panel session, Dr Christian Kohlpaintner, CEO of Brenntag, had some comments in a brief interview. He noted that, through the pandemic, people have been key, although the adaptability of the wider chemical industry has been vital. He added that innovation is largely taking place within smaller companies and start-ups, advising larger companies to keep an eye on what is going on there and tap into the possibilities.
As head of one of the world’s largest chemical distributors, Dr Kohlpaintner was keen to point out the role that such players in the market can offer, providing a link and possibly a market for ideas.
LINKS IN THE CHAIN For HCB readers, a core aspect of the EPCA Annual Meeting is always the supply chain session and this year was no different, with conversations following on from the topics covered in previous meetings. Dirk Verstraeten, chair of EPCA’s Supply Chain Programme Committee (SCPC) and senior expert logistics at Covestro Deutschland, described how the group was “continuing our journey on digitisation and sustainability” in the chemical supply chain. This year it has held two workshops, which were designed to bring in expertise both from the digital world and from sectors outside the chemical supply chain.
Those workshops also involved the participation of Professor Ann Vereecke from Vlerick Business School, who has been working with EPCA on the topic for some years now. She offered some insights gained from the meetings on the progress of the journey to create a sustainable petrochemical supply chain through digitisation. “Climate change is hitting so many people,” she observed. “There is a duty to reduce the impact of the supply chain.” Furthermore, natural disasters are becoming more frequent and often have impacts on the supply chain that can raise costs.
Pressure for change is coming from consumers – especially the young – but also from downstream customers, regulators and investors. “The time has come to reimagine the supply chain,” Prof Vereecke said, laying out some pointers.
The petrochemical supply chain needs to become more eco-effi cient; gains can be made by “connecting the dots” between partners in the chain. What does it mean for the petrochemical supply chain to change from linear to circular? It certainly implies more recycling – but does taking used plastics back into the chain threaten production? Probably not, Prof Vereecke said: it should in fact deliver more opportunity, more jobs and more profi t.
Digital technologies can provide a way towards a smarter and more circular supply chain, as the two workshops agreed. Firstly, a smart emissions simulator/calculator can allow carbon emissions to be calculated along with time and cost, so as to accurately refl ect the environmental cost of transport. Ovinto has helped develop this idea with a pilot that can help supply chain buyers make informed decisions – but it has also raised some questions. Primarily, to roll this out in the real world will need data. “Operators need to be willing to share their data,” Prof Vereecke said.
Secondly, to build some circularity into the supply chain will involve the participation of consumers and they will need to be helped to fi nd ways to easily have their used goods returned and recycled. Workshop participants had envisioned a social media platform through which consumers could signal that they have goods to be collected and then taken into the correct recycling stream. To do this will take artifi cial intelligence, governance and, quite possibly, legislation.
Reimagining a future supply chain that is sustainable and circular highlights the need for data to be shared in order to create visibility. “If we don’t measure, we don’t know,” Prof Vereecke said. A reluctance to be open and share data is a major barrier to progress. Secondly, trust needs to be there along the supply chain; tools will be needed to help build that and create an environment in which transparency can be provided.
One thing that came out of the SCPC’s workshops was that there is a lot going on downstream of the chemical industry in these areas. Companies operating in the textiles, construction, packaging and retail sectors feel more pressure from consumers and can provide the chemical sector with inspiration for improvements in eco-effi ciency and the creation of very different ecosystems. What will be needed to make this happen? Prof Vereecke was clear: investment and leadership.
AWAY FROM CHEMICALS The themes described by Prof Vereecke were picked up in the panel session that followed, which again brought in speakers from a range of fi elds outside the immediate confi nes of the chemical industry. And it was evident that things are already moving. Mark Noordhoek
DIGITAL TECHNOLOGIES CAN HELP LOGISTICS
Hegt, CEO of NxtPort International, said that more and more companies are collecting data to provide themselves and their customers and supply chain partners with real-time information to help reduce their environmental footprint. “Data is the new oil – or, rather, sunlight: it can be enjoyed by all,” he said. However, everyone wants their data to be kept secure and controlled: this is getting more difficult.
If data is to be shared and offer transparency, then the system needs to be open to all, with low barriers to entry, especially for SMEs. The data platform needs to be neutral and separate from any application that uses it. Systems like this are already in place and being scaled up globally, Hegt added.
The industrial packaging sector is in many ways well ahead of the pack in terms of the circular economy and it was interesting to hear from Marc Löffler, head of technical sales and service at Mauser Packaging Solutions, who describe the intermediate bulk container (IBC) as the “perfect packaging for a circular economy”. Mauser has been collecting and remanufacturing its IBCs for decades and has now also started recycling the polymer in used bottles, turning it into new pallets for the next IBCs it manufactures. Indeed, Löffler said, Mauser now collects and recycles more than 10 million plastics drums and 4 million IBCs a year.
Laura Nieboer, specialist in business model innovation at Sabic, described a rather more complex recycling project it has become involved in, alongside major UK retailer Tesco. The UK is a large consumer of plastics packaging but has a low rate of plastics recycling, so the project offered a lot of opportunity, she explained. The project focused on plastics used for wrapping cheese and involved not only Sabic and Tesco but also the manufacturer of the plastics packaging, cheese producers, consumers and Plastic Energy, which is using used plastics as a raw material for new fuels.
At the moment this sort of scheme is difficult to justify on the grounds of cost but, after the introduction of a plastics packaging tax for packagings with less than 30 per cent recycled material, due to appear in 2022, it will make it viable to apply the closed loop concept.
Another innovative project was described by Julie Lietaer, founder of Ariadne Innovation, which is looking to apply circular concepts in the textiles business and is behind the #HackYourJeans project. This is designed to act as a connector and accelerator for sustainable textile products.
Lietaer’s story had some particularly relevant learnings for the petrochemical sector. There are a lot of SMEs in the textiles business and it requires a lot of work to bring them all together to collaborate and innovate. Using a digital platform for all players in the ecosystem to share their knowledge and bridge gaps has now attracted more than 250 partners, each now better placed to make a difference to their environmental impact.

BECOMING CLEARER Summing up the supply chain session, Prof Vereecke noted the clear enthusiasm for change. “It’s a dream – but dreaming is good,” she said, urging the sector to start small but scale fast. “It takes vision and courage to move away from the traditional focus on operational performance in the supply chain towards designing supply chains that serve the world better,” she said, echoing others who highlighted the need for strong leadership to move the transition forward. “But,” she added, “it doesn’t have to be an either/or between cost and benefit.”
Kate Johnson, general manager of Shell Chemicals Europe, had been invited to wrap up the first day of EPCA’s 55th Annual Meeting. “We are beginning to talk about how we’re going to do what’s needed,” she said, citing the key requirements as partnerships, collaboration, technical solutions, innovation and data. These will lead to efficiency gains that will generate a more sustainable industry.
Financial risks will need to be taken, Johnson admitted, and there are lot of things that need to be got right. Different value chains will need to change in different ways to line all those up – there are a lot of paths each
CHEMICAL MANUFACTURERS ARE FOCUSING ON
organisation can take and some wrong decisions are going to be taken.
Johnson also noted that she is getting a lot of support from Shell’s employees for the transformation, “and we need to get more young talent into the organisation to help drive that,” she said.
Leadership has to change, become more agile and learn to recognise the risks that are being taken. Building new supply chains will also require new partnerships with service providers and regulators, which points to a need for new skill sets.
Those ideas were pursued in more detail on the second day by Diederick Samsom of the European Commission and one of the architects of the EU Green Deal, who reiterated that industry is looking for leaders who can change the world. “A sustainable future means changing behaviour today,” he stressed. In part that will be driven by new regulation, which will require goods to be made from non-toxic products, be repairable and be recyclable at the end of their life. “We need expertise, knowledge and – hopefully – ambition from industry,” he said. Samsom was quite clearly channelling Prof Vereecke’s urge to “dream big” by saying that Europe has the power to determine how things are made all over the world.
US AND THEM When it comes down to it, though, business is still business, and Samsom was challenged by Dr Martin Brudermüller, who said that industry is aware that the world is changing and that profit-and-loss is no longer the only metric. But how can companies maintain economic success while meeting the EU’s emissions targets? Getting to net-zero, circularity and non-toxic products all at the same time is going to be very costly. Speaking as a father, Dr Brudermüller said he could not argue with the aims of the EU Green Deal, “but there is a lot of change to deal with”. Industry desperately needs more collaboration with politics. “We need to sit down at the table and get smelly,” as he put it, and figure out how to deliver on ecological targets while remaining competitive.
Neil Carr, president EMEA & India of Dow Chemical, noted that investment cycles in the petrochemical industry are long; any investment made now won’t pay off for generations. Furthermore, the industry has not invested in Europe in recent years as it has in Asia, which is its focus for growth, so where is the money coming from? Public funding is needed across the EU, Carr said, returning to the idea of establishing a mechanism to prevent “carbon leakage” and establish a globally level playing field.
Samsom agreed that the role of governments is to provide clarity and the resources needed to help the transition. But he disagreed that Europe should join a level playing field at a lower level, saying: “The idea is to bring the rest of the world up to European standards on the environment.”
Samsom also took issue with Carr’s point about long lead times. “The best time to plant a tree is 30 years ago,” he said. “The second best time is today.”
More regulation is on its way, though Samsom noted that “uncertainty produced by democracy” may hold things up. However, he said he is glad that we now witness a society where all actors are moving in the same direction.
One of those pieces of regulation is likely to be the Carbon Border Adjustment Mechanism (CBAM), under which the carbon emissions caused by goods produced elsewhere in the world will have to be recognised on entry into the EU. Dr Brudermüller foresaw a bureaucratic nightmare if everything had to be checked at the border, though Samsom reassured him that the idea is to apply this only to raw materials. He also acknowledged that this might put Europe at a competitive disadvantage but noted that Europe has always regulated more strictly than the rest of the world (“ever since the abolition of child labour”) and it hasn’t hurt yet.
“I understand we can’t run way ahead of the rest of the world, but by running a little faster it gives us an advantage,” Samsom suggested. “Europe has a role to take the rest of the world along on this journey.”
CHEMICAL PRODUCERS MUST INVEST TODAY More discussion of finance came later in the programme; HCB will return to the topic in next month’s issue.
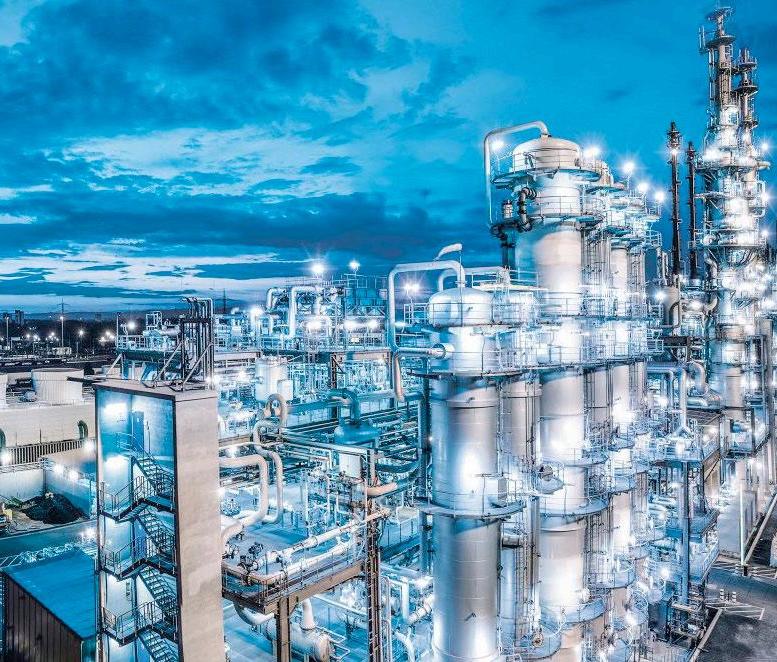