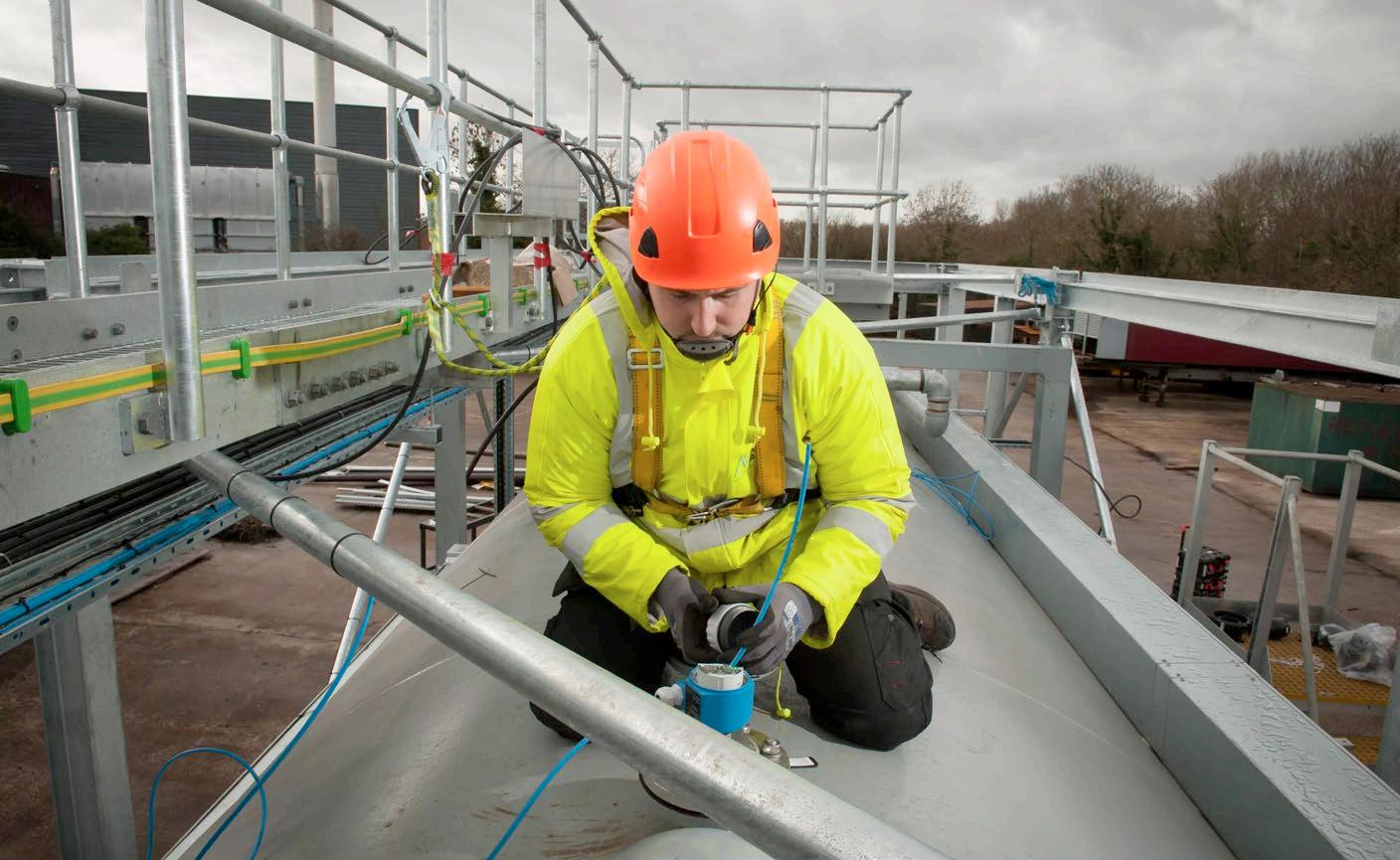
6 minute read
News bulletin – safety
from HCB November 2021
NEWS BULLETIN
SAFETY
A&A ADDS FLOTECH
Adler and Allan, the UK’s leading environmental risk reduction specialist, has acquired Flotech Performance Systems Ltd, which provides design, fabrication, consultancy, project management, planned and reactive maintenance for the storage, transfer and distribution of industrial liquids, gases and wastes. Its highly specialised services cover additive and blending, fluid transfer, access solutions, storage tank equipment and vapour recovery.
“With our already extensive capability in hazardous materials, this acquisition helps us to handle an even greater range of substances in a broader set of situations and environments, including those that will become more important in the future, such as hydrogen,” says Mike Willink, group development director at Adler and Allan. “By combining this acquisition with our existing environmental services, we are now able to be a much more strategic environmental partner to our customers.”
Thomas Sadler, managing director of Flotech, adds: “We are delighted to be joining the Adler and Allan family today. With our turnkey solutions we are already helping customers with the storage, transfer and distribution of liquid and gas products. As businesses decarbonise their processes, this move will help customers in their ability to blend contaminants into less harmful chemicals and then blend them into more useful substances such as the process for manufacturing hydrogen.” www.adlerandallan.co.uk
DGIS INTO PANDO
Labelmaster has arranged to integrate its Dangerous Goods Information System (DGIS) into Pando’s transportation management system (TMS). “The partnership provides a seamless, integrated solution for planning and executing the shipment of dangerous goods and ensure compliance with global shipping regulations,” Labelmaster says.
Chennai-based Pando helps business to digitise, monitor and optimise their supply chain operations through a networked TMS and control tower. “Shippers around the world are looking for out-of-the-box solutions for managing freight but, many of the transportation management systems lack the necessary DG management capabilities,” says Ashok Vasan, president and chief revenue officer of Pando. “By integrating DGIS with Pando’s TMS, we can now give our customers access to best-in-class DG shipping software, on a single integrated interface.” pando.ai
SARC LEVERAGES HAZCHECK
SARC, a Dutch provider of maritime software and services, has linked up with Exis Technologies to offer an EDI-IMDG validation tool for the shipping of dangerous goods by sea. The Validator uses the Hazcheck Toolkit to provide a complete check of the stowage and segregation of containers with dangerous goods aboard a vessel, alerting the user to potential conflicts and non-compliance.
“The tool is meant for ship owners, shipping lines, crew and port authorities and can assist in attaining a higher standard of safety at lower effort,” SARC says. “In summary, the EDIIMDG Validator allows for a more thorough and more efficient check of a vessel’s load, thus increasing the safety of the vessel, its crew and reducing the risk of environmental pollution.” www.sarc.nl
BATTERY GUIDE UPDATED
The US Pipeline and Hazardous Materials Safety Administration (PHMSA) has updated its Lithium Battery Guide for Shippers, designed to assist shippers to safely package lithium cells and batteries for transport by all modes according to the latest regulatory requirements, including those in the HM-215O rulemaking.
The Guide directs the reader to scenariobased shipping guides that outline the applicable requirements to ship packages of lithium cells and batteries in various configurations. Each distinct shipping guide refers to the regulatory requirements for a specific lithium cell/battery type, configuration and size, so as to make it easy for shippers to find the applicable transport provisions. The Guide can be freely downloaded from the
NCEC GOES TO SCHOOL
The National Chemical Emergency Centre (NCEC) has established the Hazmat Academy, designed to provide off-the-shelf and bespoke training solutions in the field of emergency response involving dangerous goods. NCEC hopes the Academy will help responders meet their training goals using flexible learning opportunities.
Ed Sullivan, manager of Hazmat Academy, explains: “Chemical incidents happen around the world every day. As an ex-fire and rescue service officer, I know how important it is that we have access to world-leading training to enable responders to be fully prepared to deal with incidents, as well as the opportunity to learn from each other’s experience of dealing with them. The Hazmat Academy is built on the foundation of real-life lessons leading to a safer and more competent response from all of us.” More information about the new service can be found at www.thehazmatacademy.co.uk.
CHECK YOUR VALVES
The UK Health & Safety Executive (HSE) has issued a safety alert on pressure/vacuum relief valves for road tankers. The alert follows HSE’s investigation into an incident in April 2020 when a driver noticed vapour coming from his road tanker, which was carrying nitric acid. The valve had become stuck in the open position. HSE determined that the valve had been modified by an engineer, most likely to allow it to be serviced without the use of a special tool, but the modification prevented its safe operation.
HSE is alerting users of road tankers and tank containers to inspect the pressure/relief valves fitted to ensure there have been no unauthorised modifications. It also reminds industry that those involved in the servicing of relief valves should be competent to do so.
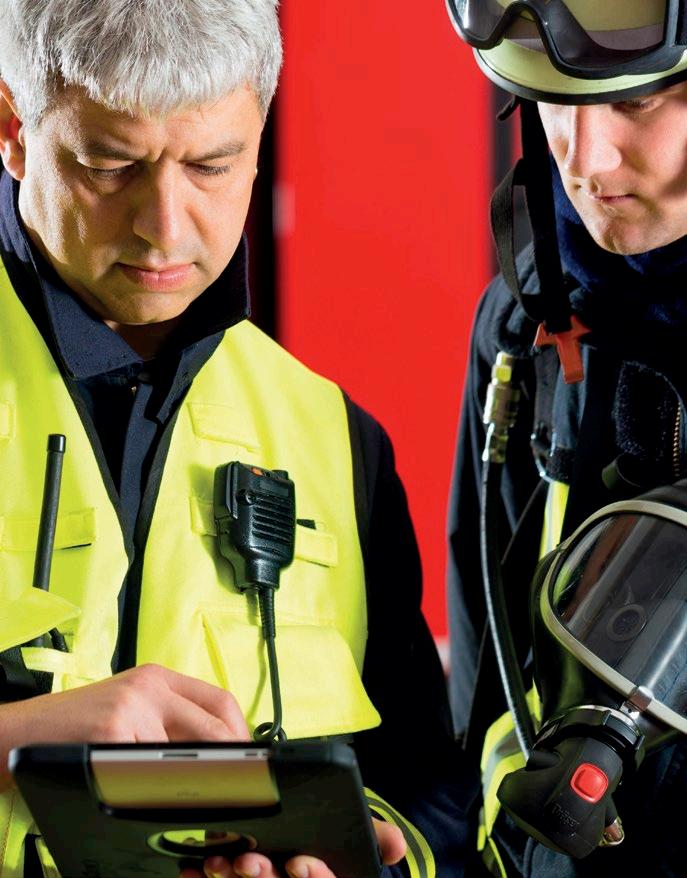
CSB REPORT FORM
The US Chemical Safety Board (CSB) has issued its new Accidental Release Form, required for all those reporting an accident involving the release of hazardous materials at a fixed facility. Those responsible must report such a release within eight hours, either by phone or by emailing the completed form to CSB. Full details of the requirement and a link to the form can be found on the CSB website at www. csb.gov/news/incident-report-rule-form-/.
NTSB COUNTS TANK CARS
The US National Transportation Safety Board (NTSB) has released information on the tank cars involved in the December 2020 derailment near Custer, Washington, which resulted in the release of some 29,000 gallons of crude oil from three of the derailed cars and the evacuation of 120 nearby residents.
NTSB’s factual report merely documents the technical details of those DOT-117 tank cars involved. Nine of the ten were originally built to DOT-111A100WI specifications with enhancements to the AAR CPC-1232 standard for tank cars in crude oil and ethanol service. Three of those nine leaked. The other tank car, which did not leak, was a DOT117j100W tank, which has a slightly thicker shell and head. NTSB has not issued any conclusions or recommendations but its report does note that this thicker tank was located among the three that did leak.
“NTSB’s intent for this investigation was to gain damage data from the DOT-117 rail tank cars involved in the derailment,” says Robert J Hall, director of NTSB’s Office of Railroad, Pipeline and Hazardous Materials Investigations. “Because our investigation was limited to data collection, we have not issued any findings or safety recommendations. The data we gathered in this investigation will assist us as we evaluate the performance of tank cars carrying flammable liquids involved in other rail accidents.”
CSB REPORTS ON HYDROGEN BLAST
The US Chemical Safety Board (CSB) has released its final report on the fatal explosion at AB Specialty Silicones in Waukegan, Illinois in March 2019. It says the blast occurred after incompatible chemicals were mixed in a tank, causing a reaction that generated hydrogen gas, which ignited. Four workers suffered fatal injuries. CSB notes that the incorrect chemical was contained in a blue plastics drum identical to that containing the chemical that should have been used.
CSB determined that the underlying causes of the incident were deficiencies in AB Specialty’s operations, policies and procedures, including its hazard analysis, methods used to store and handle incompatible materials, process safety culture weaknesses and a lack of a safety management system. CSB’s report contains a number of new recommendations for AB Specialty and reiterates some already delivered to OSHA and US EPA. The full report can be found on the CSB website at www.csb.gov/ab-specialty-silicones-llc/.