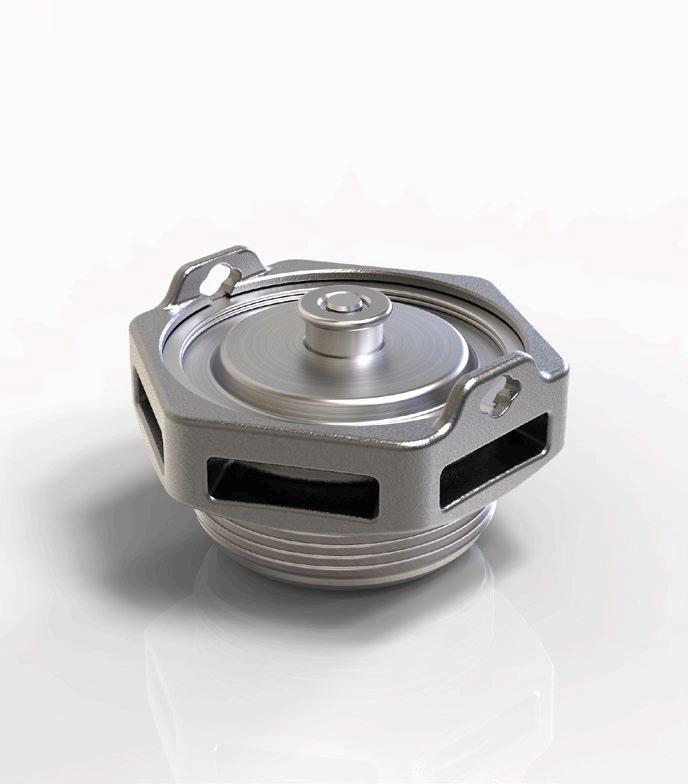
2 minute read
Fort Vale innovates IBC valve
from HCB November 2021
KEEP UP THE PRESSURE
VALVES • ADAPTABILITY, INNOVATION AND FLEXIBILITY ARE KEY ELEMENTS IN THE POST-COVID WORLD, SUGGESTS GRAHAM BLANCHARD, FORT VALE’S MARKETING DIRECTOR
QUITE A FEW of Fort Vale’s products are the result of enquiries by existing customers looking for something ‘a little bit extra’. Over the years, the Fort Vale name has become synonymous with excellence in engineering – we have a state-of-the-art manufacturing facility - having total control over all processes from research and development, design, investment casting, pressing, forging, plasma and laser cutting, to assembly, testing and certification.
We are the first manufacturer in the industry to have built a third party-approved test laboratory where we conduct air-flow and liquid-flow testing. This allows us to provide in-house testing that is suitable for a full range of products – from impact testing, air and liquid flow tests to high pressure testing for gas valves.
This facility gives us a unique insight into ‘real-life’ scenarios and enables Fort Vale to make significant and informed contributions to the safety of pressurised tanks.
NOW IN STORE One of our latest products is the new Fort Vale 2-inch BSP low profile relief valve for intermediate bulk containers (IBCs), which has been developed to radically improve flow rates and sealing performance, in the process setting a new benchmark for comparable models on the market.
The valve is perfectly suited to IBC applications where flow rates and sealing performance are key to the performance of the equipment – especially when used on low pressure, static vessels. The low profile feature increases the flexibility of the valve when space is a limiting factor and gives high flow rates with regards to pressure, while the vacuum relief offers increased vessel protection.
The potential for damaging leaks is reduced by using conical and guided seating – this significantly improves valve re-seating after relieving pressure – and CFD optimised flow rates allows balanced flow areas within the geometry of the valve, which maximises both pressure and vacuum flow rates.
A hexagonal shaped body allows for use of standard tooling to fit the valve to the pressure vessel, while a push button feature for vacuum function allows for manual venting and the integral spring design allows for greater flow rates.
The development of this valve originally came about due to enquiries from customers in the road tanker and IBC sectors – the basic premise has been around for decades and is essentially an addition to the Twinact pressure vacuum relief valve range. At Fort Vale, we’ve always prided ourselves on our ability to adapt to changing circumstances swiftly – and as we all know, this has been a skill that has proved especially useful over the last two years!
Given that we have total control of all our processes, we are able to develop a design concept through to a finished product completely in-house, quickly. This flexibility is, I think, going to be increasingly important over the next decade. We are in the middle of a period of uncertainty – social, economic and industrial – and I suspect that it will be a couple of years before things settle down. In the meantime, the companies that are able to adapt to changing circumstances, able to innovate with new technologies, and flexible enough in thought and process, will not only survive the turbulence, but prosper too. www.fortvale.com
FORT VALE’S NEW IBC VALVE OFFERS IMPROVED FLOW HAVING TOTAL CONTROL OVER THE PROCESS IS CRUCIAL,
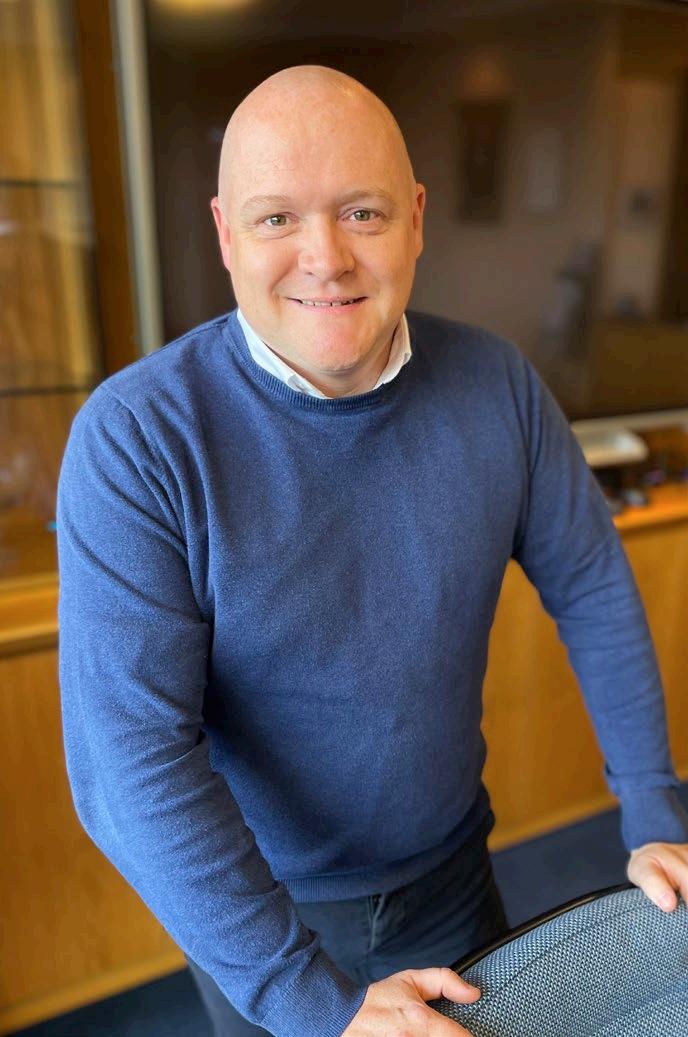
SAYS GRAHAM BLANCHARD