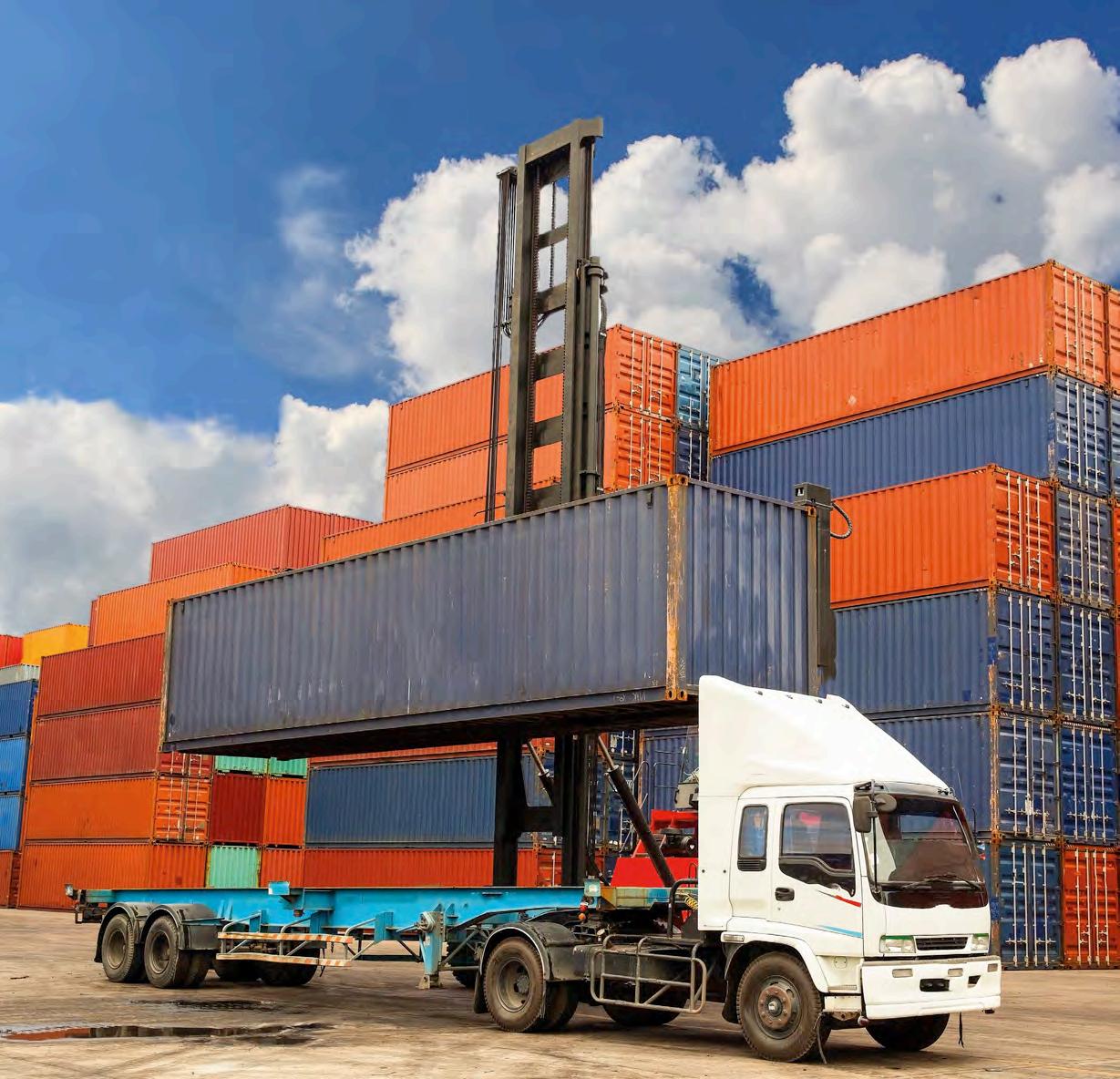
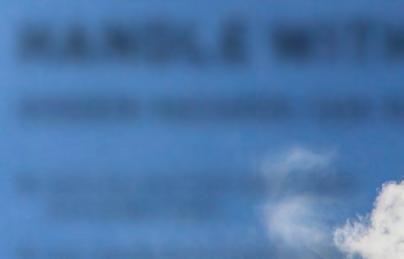
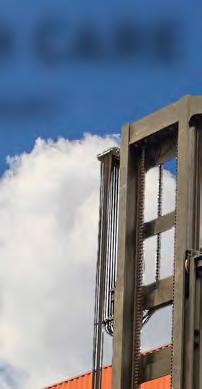
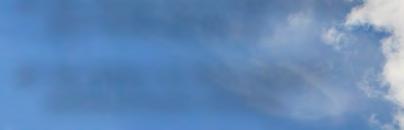
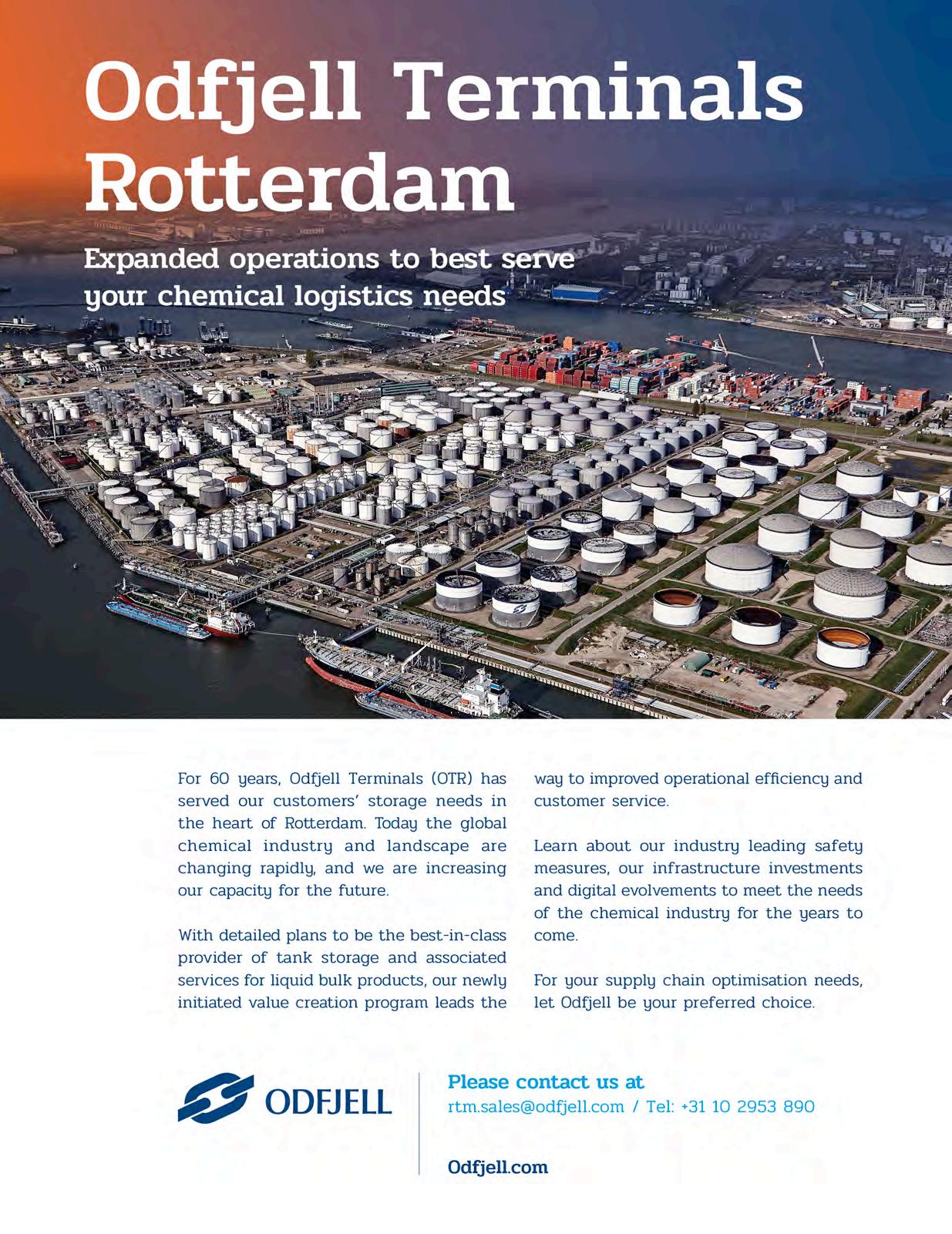
Judging by the reports we regularly refer to in these pages – and this issue is no exception – it almost seems as though occupational health and safety is a new concept and one that operators of hazardous facilities are still getting to grips with.
Nothing could be further from the truth. Even if some tools are comparatively new, particularly concepts such as process safety management or formal risk assessments, the idea of protecting personnel at work has a surprisingly long back story.
Anyone seriously interested in looking at how far back health and safety ideas go could pick up a copy of Craig Spence’s recent book, Accidents and Violent Death in Early Modern London (published by Boydell), a snappy title that immediately grabbed the attention of us thrill-seekers at HCB Towers.
In an article in the London Review of Books, Malcolm Gaskill begins with the case of Samuel Wood, whose right arm was torn off in an accident at a windmill on the Isle of Dogs in 1737; locals staunched the bleeding with sugar, which was known to have antiseptic properties, until he could be patched up by a surgeon. Despite these ministrations, he was widely expected to succumb to his injuries but in fact survived and became something of a celebrity.
The arrival of the industrial revolution, with its mechanical looms, steam hammers and any number of other potentially hazardous machines, brought new health and safety risks. Indeed, in the 1850s Charles Dickens was involved in a campaign to introduce legislation to require factory machines to be fenced off.
Gaskill also highlights the year 1665, when the population of London, the largest city in Europe, was some 400,000. In that
year around one quarter of them died, mostly from plague. Others were taken by smallpox, leprosy, shingles and a whole host of other maladies, including ‘rising of the lights’ and ‘teeth and worms’; 46 people were said to have died of grief.
Gaskill makes the point that fatal accidents were less mysterious than deadly diseases, whose causes might have been attributed to angels and demons or the alignment of the planets. On the other hand, Spence says that accidents are “communally constructed events contingent upon the social structures and cultural configurations within which they take place”.
An illustration of that is that, in some parts of the world (even in parts of the US), fatal accidents or an individual’s survival during an accident are ascribed to spirits, juju, angels or whatever. Authorities in some West African states have had to go on record to try and convince people that road accidents are caused by bad driving or poorly maintained vehicles and are not due to evil spirits.
Between 1654 and 1735, there were 12,394 fatal incidents recorded in London. Of those, 5,260 involved drowning and 1,469 involved falling. The UK Health & Safety Executive still places a great emphasis on preventing slips, trips and falls in the workplace, as these continue to cause a lot of fatalities and life-changing injuries.
On the other hand, as the Tank Storage Association heard at its recent conference, HSE is also this year focusing on low-frequency, high-outcome incidents at COMAH sites. We have not been told whether windmills are subject to COMAH.
Peter MackayCargo Media Ltd
Marlborough House 298 Regents Park Road, London N3 2SZ www.hcblive.com
Editorial Editor–in–Chief
Peter Mackay
Email: peter.mackay@hcblive.com Tel: +44 (0) 7769 685 085
Stephen Mitchell
Email: stephen.mitchell@hcblive.com Tel: +44 (0) 20 8371 4045
Brian Dixon
Designer
Tiziana Lardieri
For advertising and sales enquiries please contact Business Development Manager Daniel Rees Email: dan.rees@hcblive.com Tel: +44 (0) 20 8371 4037
Samuel Ford
Email: samuel.ford@hcblive.com Tel: +44 (0)20 8371 4035
VOLUME 38 • NUMBER 11
HCB Monthly is published by Cargo Media Ltd. While the information and articles in HCB are published in good faith and every effort is made to check accuracy, readers should verify facts and statements directly with official sources before acting upon them, as the publisher can accept no responsibility in this respect.
ISSN 2059-5735
Letter from the Editor 1
30 Years Ago 4
The View from the Porch Swing 6
Shifting sands
GPCA discusses logistics needs 8
Tying the knot
Bahri and Bolloré set up JV 12
Let’s go live
Nijhof Wassink gets connected 14
Building with boxes
Neele-Vat adds to handling capacity 16
Tanks with brains
Savvy seals deal with CIMC 18
Backing a winner
Girard reports on equipment demand 20 News bulletin – tanks & logistics 22
Platforms for growth
FECC speakers predict disruption 26
NRC buys Melrob Deal takes distributor into new markets 31
Seidler joins Maroon ranks
Further consolidation in the US 32
Consolidation in action
Azelis buys in Switzerland 34
Bodo spreads its wings
Automotive sector drives growth 35 News bulletin – chemical distribution 36
New and improved What was hot in IBCs at Interpack 38
Metalled for growth
Good prospects for metal IBCs 44
Time to talk tanks
TSA hears from the regulators 46
Let’s all make a hub
Tarragona lays Mediterranean plans 54 News bulletin – storage terminals 56
Training courses 60
Learning from training 62 Conference dairy 63
Incident Log 64 Hazards afloat
Chemtrec highlights maritime risks 67 Fire in the hold
Insurers want tighter controls 68 Hurrah for CINS
Reporting incidents at sea 70
Once more with failing CSB cites the usual problems 72
Eyes on the skies
What IATA does and how it does it 74 In the air tomorrow
DGR changes in summary 76
Border controls
Joint Meeting sees problems in the east 78 Roadside attraction
Planning for 2019’s ADR 82
THE BACK PAGE Not otherwise specified 88
Annual plastics drums survey
What’s new in gas shipping
EPCA’s Annual Meeting in review European distribution in numbers
Sometimes, when looking at copies of HCB from 30 years ago, one is struck by the distance we have travelled since then; at other times, one cannot help but think that little progress has been made. Increased computerisation has made a big difference, of course, but at the sharp end tanks still have to be welded and steel drums have to be rolled.
The front page of our November 1987 issue demonstrated just such a situation: it pictured a welder hard at work putting the finishing touches to the barrel of a tank container, much like a welder would today (though perhaps some might spot health and safety risks in the 1987 image). On the other hand, the introduction below takes us back to another world.
“In recent years European tank container builders have started to concentrate on ‘specials’ – including tanks for dedicated service and swap body tanks constructed to maximise loadings on European land and shortsea journeys,” we said at the time. “This change of direction, away from previous work on larger series of standard tanks, has been prompted by the fact that new builders are emerging outside Europe who are able to provide tanks at very competitive prices.”
How little we knew. Today there are few significant European tank container manufacturers left, and those that are still in business have mostly teamed up with counterparts in China, or are concentrating on niche business. Back in 1987 China was still largely closed off from the international market and those new volume producers were located primarily in South Africa, where investment in internationally trading assets provided a way for a country hampered by sanctions to earn foreign currency.
Those few tank container builders in the Far East in 1987 were all in Japan but were at the time suffering from a strong yen; we thought then that manufacturing might well move to South Korea – after all, the same movement was happening in shipbuilding. But the Asian currency crisis of 1988 put paid to such predictions.
We were on firmer ground with our forecast that Singapore would have an important role to play in helping develop tank container utilisation in Asia, acting as a hub for regional operations. That development had started a good decade earlier, led by Interflow, which was at that time owned by the Gallic Shipping group, although other European operators had begun to follow suit in the late 1970s, including Suttons, Leschaco, Stolt and VTG.
Development of tank container use in Asia in the 1980s was being held back by three main factors: trade imbalances and the lack of potential backhaul cargoes from Asia to Europe; a lack of tank cleaning depots outside Singapore; and a lack of awareness on the part of shippers of the potential benefits of using tank containers.
Over the years, development of the regional petrochemical industry has alleviated to some extent the problems of trade imbalance, while the opening up of tank container trades to and from North America has also offered better employment prospects. But the problems relating to cleaning and repair depot capacity and to shipper awareness are only gradually being addressed. The Asian Tank Container Organisation has done a lot in these areas in the past few years but there is still a way to go.
Busted! At the time I probably wouldn’t have used the word busted, because back then busted was common slang for arrested, as in apprehended by the police. But the sentiment was undoubtedly the same as “busted” can convey now. Caught! Discovered! My secret exposed!
It wasn’t really all that bad when my mom confronted me after a parent-teacher conference, but still…, she definitely confronted me. “Your teacher tells me you often hide a novel behind your textbook during social studies class”. During social studies class?
Heck, I tried to get away with that trick in practically every class. “What do you have to say for yourself, young man?”, my mother continued.
I couldn’t lie, in part because I wouldn’t be believed, and in part because I had made a habit of trying not to. So, I seized on a minor inaccuracy in the teacher’s observation, hoping that if I could invalidate some of what she’d said, the rest would crumble, at least in my mother’s eyes. “Mom”, I whined, “I don’t do that very often, only sometimes.” Mom wasn’t falling for it, at least not yet. “So, you admit it?” Not giving up, I tried again. “C’mon, Mom, every once in a while I’m caught up when she reviews stuff we’ve done before, and I do a little pleasure reading. If it was often, would I be getting an A?”
Bingo! My A saved me. But, honestly, I did read non-class books in class at some point almost every day. But, as long as I kept getting As, that wasn’t “often”.
I have a relative with a talent for wrecking automobiles. We were visiting, killing a little time before some family function by shooting baskets and chatting. My relative bemoaned the sad effect not having a working car was having on his social life, to which I replied that he was always wrecking his cars, and maybe that was his fault. “That’s not fair”, he said, “I don’t always do anything.”
“Okay,” I said, now upping the precision of my communication, “you often wreck your cars”, and driving the point home, “other peoples’ cars, too”. “Often,” he asked, “often, really? How can you say often?” So, we counted it up. He’d only had a license to drive for about 3½ years, but had wrecked six cars. I told him that being in a car crash
every seven months was “often”. And then he summed it up for me, albeit indirectly. “If you could only have sex every seven months, would you think that’s often?”
The light bulb went on. “Often” is relative, and “often” is subjective. And any given frequency might be often in some cases, but not often in others.
Do the DG regulations change often? In any one area (except Lithium Batteries), no, they don’t change often. But, considering all areas cumulatively together, they might be considered to change often. Added together, the changes in the last 25 years affected classification, packaging, marking, labeling, shipping documentation, acceptance, security, and most other functions, too. If you didn’t keep up with the changes, you became a DG dinosaur, and can’t do anything right now in any area.
Do CDGP questions need to be reviewed often? Compared to CHMM and a bunch of
other certifications, hell yes. Occupational safety, and industrial hygiene, and environmental protection regulations don’t change very often, at least in comparison to HazMat (DG) transport regulations. GHS based regulations change occasionally, whenever a nation (state, country) decides to make changes. But DG regulations change at least every two years, and sometimes more often. The Certified Dangerous Goods Professional (CDGP) certification exam needs to be updated at least as often as the DG regulations change.
Is a five year renewal period for DGSA or CDGP often? Five years equals five years, right? For DGSA, taking another exam every five years isn’t too often for me. But for CDGP, which can be renewed differently, five years is long enough that I sometimes forget to track the ‘renewal points’ I earn for conferences and taking training. So five years is often enough or not often enough.
The biggest DG frequency issue, though, is, IMO (wait, should that be IMHO?), the recurrent training requirements in the IMDG Code and the UN Model Regulations. Today, the way they are written, re-training could be given once a decade, or even once every other decade, and that would be compliant. Seriously, the model for our national regulations, which is also the model for our regional and international regulations, can’t come up with a better Recommendation than ‘whenever’?
“Often” is a subjective term, but really, who truly believes that every other decade DG re-training is “often enough”? Not I.
This is the latest in a series of musings from the porch swing of Gene Sanders, principal of Tampa-based WE Train Consulting; telephone: (+1 813) 855 3855; email gene@wetrainconsulting.com.
PETROCHEMICAL PRODUCERS IN the Middle East have a number of competitive advantages in the global marketplace. They have easy access to low-priced feedstock and, being newer, their facilities are generally more efficient than older plant in the mature markets. The region is also handily placed to export material both east- and westbound.
However, the distance to those markets means that producers in the region have to ensure their logistics operations are equally efficient if those cost advantages are not to
be eroded by distribution costs. That has been an increasingly important function, especially since the fall in global oil prices and the rise of shale oil and gas output in North America have changed the balance of competitivity.
More than that, changing demographics and growing pressure to reduce carbon emissions are putting something of a strain on industrial manufacturing, at the same time as customer expectations are growing. IT advances are making supply chain transparency available to more players in the chemical business,
further driving competition but also raising the potential for greater collaboration and for the capture of hidden efficiencies.
It was within that environment that the Gulf Petrochemicals & Chemicals Association (GPCA) held its ninth Supply Chain Conference this past May in Abu Dhabi.
The meeting’s stated aim was to explore the role of technology in driving agile and efficient supply chains for the petrochemical sector in the Gulf Cooperation Council (GCC) states.
Some 280 delegates from 19 countries arrived for the three-day event to hear a wide range of speakers and to network with their counterparts from other companies.
It is now generally accepted that supply chain companies have to adapt if they are going to become more agile and embrace the technology that can bring great benefits to their operations and their client industries.
But what does that mean in practice for a logistics service provider (LSP) to the petrochemical sector?
The first answer is collaboration, but this is something that many in the industry have been seeking for decades. Is it now the time to open up to partners in the supply chain? Mohammad Husain, president/CEO of Equate and chair of the GPCA Supply Chain Committee, certainly thinks so. “The industry must utilise and share common resources to ensure cost-efficiency and productivity in an increasingly competitive market environment,” he said, opening the conference.
Furthermore, supply chain efficiencies offer an excellent opportunity for the petrochemical industry to reaffirm its commitment to protecting the environment but, again, this will require industry, its LSPs and government agencies to work together to achieve sustainability goals. “The adoption and implementation of best practice initiatives, the highest industry standards, environmental programmes and rigid regulations need to be encouraged across the board,” Husain said.
Technology will play a crucial role in making sure that high-value chemicals and petrochemicals move from the manufacturing plant across roads, through ports and over the sea to their final destination in a sustainable and safe manner.
One of the largest and most modern petrochemical manufacturing plants in the GCC region is the new Sadara facility in Jubail, Saudi Arabia, whose CEO, Ziad Al-Labban, explained that the engineering of an agile supply chain was just as important to the project as the engineering of the plant itself. He described an agile supply chain as one that minimises the time from production to revenue by applying advanced work processes and systems, reduces inventory levels and relies on the building of strong partnerships.
In more quotidian terms, the need for agility in the supply chain also meant that the new
production unit should be located on the Red Sea coast, close to its suppliers, ports and logistics companies.
Al-Labban also noted the role played by various IT tools in reducing the order-torevenue period but others are still questioning whether it can generate concrete benefits. However, Nathan Scott, regional IT head for Panalpina World Transport, said that digitisation has the potential to lower production and operational costs, accelerate lead times and help in better planning and production optimisation. Scott also pointed to the potential offered by 3D printing in terms of, for example, additive manufacturing as well as the implementation of blockchain principles to simplify business processes both within and between companies. Alarmingly, though, research has indicated that, while 90 per cent of CEOs believe the digital economy will impact their industry, only 15 per cent actually have a digital strategy.
John Straw, senior adviser at IBM, had some pointers in that direction, quoting a study by Accenture that found that 58 per cent of chemical companies are already employing digital tools to get a competitive advantage. That means that established business models are being up-ended.
On a more practical level, Christian Juul Nyholm, managing director of Maersk Line’s regional operation, said that one win-win scenario could involve better forecasting by GCC petrochemical producers alongside better reliability on the part of shipping lines, through the use of digitalised collaboration.
Ralph Muessig, senior consultant at Camelot Management Consultants, said that ‘big data’ is also a game changer for the chemical logistics sector, where additional data is driving higher supply chain integration. State-of-the-art IT systems built around big data currently support typical transport management elements through order management, transport planning, transport execution, and freight cost management. With these technologies potentially disrupting the status quo, several industry experts addressed the question of how efficiency and agility could be enhanced with the new supply chain technologies.
Richard Verity, partner at McKinsey & Company, maintained that an agile supply chain is enhanced through three levels of segmentation: needs-based, asset-based and product-based. »
Needs-based segmentation reflects service requirements as well as product sophistication. Product segmentation, on the other hand, considers the variance of sales against total sales. Asset segments can employ different distribution models that cater to different product segments.
Technology disruptors such as big data can optimise the network behind the supply chain for each segment. The differentiated supply chains would drive pricing, cost, inventory, and service levels. A case study showed how Volvo has improved EBIT by 15 per cent and reduced lead times by 30 per cent through digital-enabled supply chain segmentation.
Driving efficiencies within the supply chain requires robust management of the new technology platforms. Manufacturers must use integration to extract the full efficiencies of a supply chain. At a company level, this means new organisational structures, integrative IT tools and systems that help supply chain networks work together, as well as a higher level of customer intimacy that caters to the specific needs of customers.
According to Hosnia Hashim, deputy CEO for olefins and aromatics at PIC and board chairperson at Equate, supply chain efficiency is the sum of various cross-functional collaborations. Hashim detailed how Equate’s cross-functional sales and operations teams within each business consist of people with manufacturing, sales, finance, procurement, and IT functions. They are headed by someone from supply chain.
Each team develops one integrated, tactical plan “that can direct its business to achieve competitive advantage by integrating customer-focused plans for products with supply chain.” IT serves as an enabler for people and processes and ensures continuous improvement in a measureable environment. “[IT] is your window to the world and your virtual vessel to stay ahead in an ever globalising industry,” said Hashim.
Governments can encourage this type of integration by intervening in a number of
key dimensions, Rachid Maalouli, associate partner at McKinsey & Company, explained. These include operations and maintenance upgrades alongside improved interfaces between transport modes. They could also expedite targeted expansions, enable private sector participation, provide better access to financing, assist in the adoption of disruptive technologies, and help build capabilities and attract talent.
In Saudi Arabia, Maalouli said, strong integration between different logistics assets is needed to strengthen the national supply chain infrastructure. Low levels of integration have led to diminished connectivity and lower asset utilisation. At an initial level, improved port utilisation and shorter port dwell times would help open up the supply chain.
These and other presentations made a strong case for the adoption of new technologies to improve supply chain efficiency, since a failure to take advantage of the opportunities will inevitably lead to the region falling behind.
To improve their supply chain performance, companies need to first break the circle and act in collaboration with their partners across the whole supply chain. They need to segment their supply chains; where there was one supply chain, they need to create many, but then compromise.
Customers’ demands for more and more individualised products are continuously increasing. This points to ever more microsegmentation, and finally to the
implementation of mass customisation ideas. Customers will be managed in much more granular clusters and offered a broad spectrum of suited products. This will enable customers to select one of multiple ‘logistics menus’ that exactly fits their need. At present, new transport concepts, such as drone delivery, allow companies to manage the last mile efficiently for single and high-value packages. Using big data to optimise networks for each customer segment is absolutely crucial, along with making sure that differentiated supply chain drives pricing as well as cost, inventory and service level.
While digital technologies continue to advance, the ability of people and organisations to fully use their capabilities has struggled to keep pace. Besides digital innovations in products and services, disruptive technologies may also include ways to improve human productivity. Employees should be engaged to re-think how work gets done and understand how technology can enhance rather than threaten their capabilities.
When it comes to driving efficiency, supply chain is not a solo performance. It is the sum of all cross functional collaborations. The role of IT is absolutely pivotal to achieve optimised and efficient supply chain operations as it enables processes and people, while ensuring continuous improvement in a measureable environment. IT is the new window to the world and the virtual vessel to allow companies to stay ahead of change in an ever more globalised industry. HCB www.gpca.org.ae
BOLLORÉ GROUP AND Bahri have established a joint venture, Bahri Bolloré Logistics, in Saudi Arabia, which will provide end-to-end logistics and supply chain management to local and international companies operating in the country and the wider Middle East. Bahri owns 60 per cent of the new company, with Bolloré holding the remaining 40 per cent.
Commenting on the joint venture, Abdulrahman Mohammed Al-Mofadhi, chairman of Bahri, says: “The success of this joint venture signals the importance of collaboration in creating a wider positive impact on the sector. It is only through meaningful partnerships and a shared vision that the transportation and logistics sector can break new ground and explore new horizons of growth.”
The new joint venture was celebrated and formally inaugurated at a ceremony held in the Ritz-Carlton in Riyadh in late September, attended by senior executives of the two partners as well as Éric Giraud-Telme, deputy head of mission at the French embassy in Riyadh along with other representatives of the diplomatic and military services.
“Bahri is extremely proud to be playing an active role in strengthening the Kingdom’s position as a unique global logistics gateway. Through this joint venture and other initiatives, we remain dedicated to the future growth and development of the transportation and logistics
industry in the Kingdom,” Al-Mofadhi said during the inauguration.
Ali Al-Harbi, acting CEO of Bahri, commented: “The inauguration of Bahri Bolloré Logistics will enable us to play a significant role in driving an important objective of Saudi Arabia’s Vision 2030, to further raise the Kingdom’s ranking in the global logistics market.
“The joint venture will enable us to deliver high quality logistics and supply chain management solutions as we combine Bolloré’s global footprint with our industryleading capabilities and deep understanding of the local market to meet the growing demand for these services in the regional market,” Al-Harbi added. “In doing so, we are also proud to be playing an integral role in further promoting Saudi Arabia’s credentials as a prominent logistics gateway.”
Cyrille Bolloré, chaiman of Bolloré Transport and Logistics, said: “We are particularly
honoured to conclude this strategic partnership with Bahri, one of the most recognised logistic players in Saudi Arabia. This development at the heart of a high growth potential region is an important milestone of our global network integration.”
Bolloré Logistics’ CEO, Thierry Ehrenbogen, added: “This alliance is following the development dynamic of Bolloré Logistics in the Middle East region and at the crossroads of Asia, Africa and Europe. Our joint venture with Bahri enables us to promote our expertise in our key sectors, especially in aerospace, defence, oil and gas, along with fashion and healthcare.”
Bolloré has an existing presence in Saudi Arabia, with a headquarters office and operational facility in Jeddah and another location on the Arabian Gulf coast in Dammam.
Bahri was formerly the National Shipping Corporation of Saudi Arabia (NSCSA) and remains a major player in oil and chemical tanker shipping; it has since added a dry bulk shipping operation, ship management activities, and Bahri Data, formed in 2015, which focuses on leading cross-functional initiatives to unearth the knowledge hidden inside massive amounts of data and thus create transformative impacts in the maritime industry. Last year Bahri achieved revenues of SAR 6.79bn ($1.8bn) and net income of SAR 1.76bn ($470m). HCB www.bahri.sa www.bollore-logistics.com
“OPTIMAL CONNECTIVITY 24/7 and from any location means maximum efficiency and productivity,” says Nijhof-Wassink, riding the wave of the newly digitalised supply chain. “This applies to our own processes, but primarily also for our clients. Under the name Nijhof-Wassink LIVE, we are working on the unlimited exchange of data between people and IT systems, but also between mutual systems.”
This is the basis of the latest development at the Netherlands-based bulk transport and logistics firm. Its new Transport Management System (TMS) provides its own transport planners, its clients and their customers with real-time, ‘LIVE’ information.
“Everything is about data these days,” observes Mark Burgman, Nijhof-Wassink’s business improvement manager. “The better you have set that up at the front, the better the odds of being successful on the bottom line. A large number of companies are only now starting to work with a digital plan system but at Nijhof-Wassink we have been doing this since the 1990s. We were also one of the first transport companies with onboard computers in the trucks.”
The latest iteration of the company’s digital platform provides information automatically all the way through the logistics chain. When a driver arrives to load, he presses a button and a notification is sent; the same thing happens
when he starts to load and again when he is ready to leave. This gives much more control over the process. “Approximately 150,000 status updates are exchanged between the various systems every single day,” Burgman notes.
Benno Hulzink, operations manager for Nijhof-Wassink’s dry bulk logistics division, agrees: “This system allows us to genuinely plan in real time, really LIVE. It calculates how long the expected journey time is. If there is an overnight stop, this is automatically included in the planning. In this way you know what the arrival time will be. The information is constantly kept up to date, so there is realtime shipment information. If the loading takes longer than anticipated or if the driver gets stuck in a traffic jam, this will be determined by the GPS connection and the planning will be automatically updated.”
Providing this sort of real-time information to its clients is, Nijhof-Wassink believes, a competitive advantage. “Anyone can drive from A to B,” Burgman says. “If you want to keep meeting the needs of your clients, you need more than a good truck and a driver. You also require state-of-theart automation and a far-reaching integration into the supply chain of your client.”
Hulzink illustrates what this means in practice. “We are increasingly faced with time slots that have been determined by the client. If you can plan in real time you can also plan towards such a time slot. In the old TMS there was still a lot of human thinking – subjective estimations on the basis of experience.” The new TMS provides that information quickly, objectively and in much more detail. Clients thus benefit from better delivery performance while Nijhof-Wassink optimises its own performance.
An important element of the new TMS is the way it communicates with clients’ own systems, either directly or through an intermediary platform such as Transwide or Elemica. “The client order comes to us automatically,” explains Hulzink. “Typing out information is
BETTER VISIBILITY ALLOWS NIJHOF-WASSINK TO PROVIDE BETTER CUSTOMER SERVICE AND EMPLOY ITS ASSETS EFFECTIVELY
no longer necessary and this reduces the chance of errors. This also gives our planners the time and space to set up their work differently – they can focus more on further increasing our level of service by, for example, checking whether the requirements of the transport are properly adhered to. This is crucial, in particular with chemical companies, because there even a small error in an order can lead to significant damage claims and other potentially tricky situations.
“During the implementation of the order the client constantly receives status updates, up to and including the moment the cargo has been unloaded. The client can then immediately invoice – he no longer needs to wait for a consignment note, because it has already been scanned by the driver in his truck and is already in the system.”
Such an approach also improves safety in the logistics chain. “You get more traceability,”
Burgman says. “We can get the system to also supply number plates, so the client knows which truck he can expect at the gate.”
But what Nijhof-Wassink has achieved so far is just the beginning. Hulzink explains: “We want to move towards a system that can, for instance, devise a planning proposal itself, based on orders. With such partial automatic planning, the planners can fill their time even more efficiently. It is essential, though, that they are always in control: a planner must always be able to overrule instructions from the system.
“We are already cautiously experimenting with this time of automated planning and the first results are positive,” Hulzink adds.
“With Nijhof-Wassink LIVE we can achieve the ultimate digital supply chain network, together with our clients,” Burgman says. “Thanks to 24/7 real-time information, we can offer the end client the service level that matches the modern era.” HCB www.nijhof-wassink.com
“IF YOU WANT TO KEEP MEETING THE NEEDS OF YOUR CLIENTS, YOU NEED MORE THAN A GOOD TRUCK AND A DRIVER”
IN THE FIRST half of 2017, throughput of containers at the Port of Rotterdam rose by nearly 10 per cent year on year. As many of those additional containers are carrying dangerous goods, this has meant an increase in business for specialist service providers.
Among them is Neele-Vat Logistics, which operates six facilities in and around Rotterdam, including a major warehouse on the Maasvlakte that has a total capacity of 50,000 pallet spaces and handles ADR goods, aerosols, other chemicals, electronics and goods that require temperature-controlled storage.
To handle the growing volume of inbound and – especially – outbound containers in the port, Neele-Vat has leased a further 5 ha of land opposite its existing Maasvlakte site and has already drawn up plans for another warehouse; the demand is clearly there and the company is now awaiting the award of permits from local authorities before construction can begin. It expects the warehouse to be complete late in 2018.
The second Maasvlakte facility will include drumming lines to break bulk from road tankers and tank containers. This is a new activity for Neele-Vat, reports business development manager Joost Mooijweer, as the company has traditionally focused on the transport and warehousing of packaged goods.
Another significant element of the new Maasvlakte warehouse will be an outside area devoted to the gas measurement of the atmosphere inside containers arriving into Rotterdam, which will double the company’s capacity in what Mooijweer reports is a growing activity as an increasing number of receivers are asking for a gas-free certificate before taking delivery of imported goods.
Mooijweer reports that around 15 per cent of all containers checked have gas concentrations above the acceptable limit. Only 2 per cent involve high levels of fumigants – the other 13 per cent contain gases emitted by the cargo or by the wooden pallets and dunnage inside the container. Often these gases are derived from resins and adhesives used in the manufacture of the goods.
Mooijweer says the business of gas measurement has increased rapidly from a standing start some eight years ago; it now provides a gas measurement service not only for its own clients but also for third parties, mainly other freight forwarders, which now represent some 80 per cent of activity in this business. Neele-Vat is now one of the biggest players in the market in Rotterdam and its personnel are trained and properly equipped to deal with the hazards posed by off-gassing in containers before they are delivered to the consignee.
The move into gas measurement also reflects the changing nature of Neele-Vat’s overall business since it was formed in 2014 from the merger of two long-standing family-owned companies. European land transport accounts for some 40 per cent of its business, with warehousing contributing 30 per cent, air and ocean freight services 20 per cent and customs activities 10 per cent.
This smallest sector of the business is growing fast, Mooijweer says, not least from its experience in and expertise with the ‘Delivery Duty Paid’ system required of consignments to Russia. It can only do this by maintaining its own office in the country, one of six territories covered by offices outside its Benelux base. HCB www.neelevat.com
Such a capability is already available. SAVVY Telematic Systems AG offers its customers remote temperature control and adjustment from any location at any time. Dispatchers at desktop computers or shipment staff on business trips can correct and/or adjust temperatures from a smartphone. Likewise, where temperature deviations or disturbances arise, designated persons are automatically notified. Two clicks suffice to configure the escalation workflow as needed.
was put into operation. This is not only a reliable basis for billing tank container heating costs. All of the record protocols are available retroactively as quality proofs, so taking manual – and error-prone - notes of product temperatures or pre-heating duration is no longer necessary.
A number of producers of speciality chemicals and food products are already using SAVVY’s solutions to monitor and control trace heating and cooling units remotely, including Repsol Resinas of Portugal and China-based Wanhua Chemical Group. In the event of any deviation from the target temperature or any other notable event, an automatic alarm is immediately triggered. This allows shipment personnel to intervene without delay.
The monitoring of temperature-controlled shipments is just one application for SAVVY’s telematics systems, a fact that has been recognised by the largest tank container manufacturer in the world, CIMC. David Wang, sales director for CIMC Tank, explains: “We have equipped our tank containers with the SAVVY® FleetTrac. This means we have taken the next step in further improving investment security for our customers.”
THE UNUSUAL HEA t wave in June of this year is only one of the many extreme phenomena that has characterised the weather in the last few years. The increasingly dynamic changes in the weather situation and the rise in extreme conditions pose new challenges in sectors previously unaffected by the weather. One example is the transport of temperature-sensitive goods. To ensure product quality during shipping, real-time monitoring and temperature control are increasingly important.
Ongoing temperature monitoring ensures optimum quality and safety for temperaturecontrolled shipments. SAVVY’s solution enables operators, leasing firms, and chemical companies to offer their end customers new services that reduce costs and further increase transport productivity.
For example, shipments can be automatically and precisely pre-heated or cooled depending on the conditions the goods require to arrive in good condition. Exact protocolling means there is always a record of when and how long the tank container was pre-heated, and the temperature at which it
“Thanks to SAVVY’s state-of-the-art telematics technology, uninterrupted, digital temperature protocols are not the only thing we are getting. The sophisticated alarm, diagnosis and control options offered by the SAVVY® Synergy Portal (Chinese version www.tankmiles.com) enables unprecedented real-time management for temperaturecontrolled shipments,” Wang continues.
Aida Kaeser, SAVVY CEO, adds: “For tank container operators and leasing firms, collaboration with SAVVY is not only attractive because of SAVVYs market and technology leadership. SAVVY is the exclusive telematics provider of the worldwide largest tank container manufacturer, CIMC Tank. Our customers benefit from this twofold: they get intelligent tank containers from CIMC that are already equipped with SAVVY technology ex works. This way they do not have to worry about it any more and save both installation time and money.”
SAVVY’s telematics units are built to be robust and, thanks to their very low power consumption, are also suited for long autonomous operation. The units are connected by interfaces to the container and tank wagon heating and/or cooling units. SAVVY’s intelligent interface architecture makes it possible to use the technology with a broad range of manufacturing systems.
Currently, there are SAVVY telematics units in operation with all established heating and cooling systems such as Dirac, Eltherm, Löbbe and Klinge. During operations, the unit records the current temperature and transmits the data via the SAVVY® Synergy Portal, which won the Telematic Award for the best tank container logistics solution in November 2016. This arrangement enables both real-time monitoring and, later on, seamless proof of quality. The cloud-based SAVVY Synergy Portal enables dispatchers to also have access to the individual units worldwide and maintain granular control over target values and unit parameters.
Active, non-stop shipment monitoring, with transmission every five minutes, for example, is possible with our system but does not make sense technically and economically,” Kaeser says. She puts it this way: “I don’t eat constantly to prevent feeling hunger but eat when I am actually hungry.” Similarly, SAVVY’s telematics units do not need to be in constant communication.
“Our telematics systems are hybrid and equipped with self-learning software. Instead of bombarding users non-stop with data, we notify them when there are actual deviations which are of interest for their task,” Kaeser explains. “The software takes care of the rest because it is developed to automatically recognise certain patterns, learn from them, and adjust to them accordingly.
“We are very proud of the self-learning capacity of our software, resulting from long-standing experience in the development
of highly complex algorithms. The advantage of digitisation is after all to automate flows to free employees from mindless, repetitive tasks. Valuable time is then available for tasks that truly add value.”
In addition to comprehensive transport safety and automated production of required documents, the SAVVY solution offers more cost optimisation potential. The portal provides extensive business intelligence functions to analyse the transport processes of chemical and transport companies with respect to individual indicators. These can be used to provide optimal support for capacity utilisation, asset management or to develop new business areas.
SAVVY® Telematic Systems AG, headquartered in Schaffhausen, Switzerland, is a leader in innovative telematics, sensor
and software solutions that make an important contribution to digitisation in the chemical and logistics sectors. The objective is to increase added value in these companies by means of efficient work and logistics processes, the company says.
SAVVY combines high-tech telematics system solutions for use in rail freight wagons, tank and freight containers, IBCs, vehicles or machines with sophisticated telematics technology and a process-oriented state-ofthe-art portal.
As well as its hardware and systems, SAVVY, a subsidiary of INDUS Holding Group of Germany, also offers extensive process consulting and intelligent process design services for all telematics and sensor-based applications; it is also active in digitising business processes in the chemical, industrial and logistics sectors. HCB www.savvy-telematics.com
Then in late 2014 came the slump in oil prices and, along with the opening up of new pipelines to move crude oil and NGLs, those days were suddenly over. On top of that, uncertainty during the US election year in 2016 ran into 2017 as businesses waited to see what approach the new administration would take.
jump in. That too has now calmed down although Girard says shipments are still going, particularly for stainless steel vents.
ANY MANUFACTURER SUPPLYING equipment into the hydrocarbon and petrochemical supply chain will be affected by external factors it has little or no control over. In North America, rapid development of shale oil and gas resources over the past five years generated something of a ‘gold rush’ mentality in the business, with surging demand for rail tank cars and tank trucks to move the new production and a concomitant surge in demand for safetycritical kit.
Despite all this, the market is now “picking up a head of steam,” according to Tim Girard, president of Florida-based Girard Equipment, one of the leading manufacturers of valves, vents and ancillary equipment for the oil and chemical transport sector.
In particular, Girard reports, the market for rail tank car equipment is “recovering quite nicely” with improved demand for vents for tanks handling corrosives as well as crude oil. The oil price boom in 2012 to 2014 also impacted the tank truck sector, where the big manufacturers were unable to meet demand, attracting some smaller truck builders to
Girard also says that the tank container and offshore tank sector is “pretty strong” right now. The company, now well established in this business, has carved out a significant and ever-growing share of the market, particularly in North America, where customers are realising the benefits of tank containers over other packaging formats for hazardous liquid chemicals.
Tim Girard says the company is also responding to a growing number of notable European users looking for a viable alternative to the other well known suppliers.
This is a somewhat different market with its own demands and, Girard says, aftersales service and technical support are very important. The company is being selective in
EQUIPMENT • GIRARD CONTINUES TO EXPERIENCE STRONG DEMAND FOR ITS TANK VALVES, VENTS AND OTHER EQUIPMENT AND IS INVESTING TO MAKE SURE IT CAN SUPPLY THAT DEMANDGIRARD HAS INVESTED IN A NEW FOUNDRY TO HELP KEEP PACE WITH DEMAND FOR ITS EQUIPMENT
the customers it targets, looking for niche operators for which those aspects are vital and Girard is aware that “pricing has to be good”.
In the other area of its specialities, Girard’s intermediate bulk container (IBC) business is “always pretty steady” and has not been so sharply affected by the wider market changes. Girard notes that the company offers some “great solutions” for the IBC sector, not least its sMart Vent™ pressure/vacuum relief valve, which Hoover Ferguson uses on all its metal IBCs. Girard also notes that it sells well in Europe, particularly to IBC manufacturers in Germany and Scandinavia.
Also selling well in Europe right now are Girard’s vents for road tankers. That is one outcome of the company’s reorganisation of its European operations a few years ago. Now headquartered in Barendrecht on the south side of Rotterdam, with easy access to Germany, the office is headed up by former Fort Vale sales director Anthony Malpass and has its own manufacturing facility attached.
“These are exciting times for us in Europe,” Tim Girard says. “The future looks very bright.” That outlook has been helped by recent stabilisation in exchange rates and, along with some local production, Girard is able to sell into Europe at competitive prices.
There have been changes too at Girard Equipment’s activities in the US, not least the opening a few years ago of a new foundry in Fort Pierce, Florida, some 15 miles (24 km) south along the coast from its headquarters and assembly plant in Vero Beach. Foundry capacity had always been something of a choke point in Girard’s supply chain and the addition of a dedicated plant helped the company cope with the surge in demand around 2013.
That added capacity is now coming in useful once more; Tim Girard says that new orders are coming in thick and fast now that political uncertainty has eased somewhat and that the
firm’s order backlog is “tremendous”. Nevertheless, Girard is able to keep up with demand.
And Girard Equipment is taking steps to make it easier than ever for its customers to place their orders, with a new website due to be launched before the end of this year. “A website is no longer just a billboard,” Tim Girard says. As well as an expanded and streamlined online store, the new site will offer an interactive experience with instructional videos and downloadable technical details.
In that respect, Girard is keeping up with technological developments elsewhere in the industry. It is also looking closely at the potential offered by telematics systems to add value to its customers. Tim Girard says the company is talking to RFID providers as well as to its chemical industry clients to see what they want from such systems and what is practicable. HCB www.girardequip.com
Katoen Natie has broken ground on phase II of its Specialty Chemicals Hub on Jurong Island, Singapore. The S$15m ($11m) expansion involves installation of silos, packaging lines and auxiliary equipment and is due to open in December 2018.
“ This investment represents a significant step change we offer to specialty chemical companies,” says Koen Cardon, CEO of Katoen Natie Singapore. “As Singapore is moving towards more production of high-end products, we are expanding our facilities to offer our key customers more solutions and more capacity.”
The Jurong Logistics Terminal provides a wide range of logistics and semi-industrial services to global customers, including
repackaging, sieving, grinding, blending, customising and tank container operations. “Our chemical customers are looking for total solutions that require highly skilled operators and services at the highest standards of safety, quality and environment,” Cardon notes. “We continue to innovate to develop solutions for our customers that can help them to make the difference”.
www.katoennatie.com
Gondrand expects to move into its new chemical warehouse facility in Moerdijk, the Netherlands during the first quarter of next year. “The new site will comply with the latest PGS15 guidelines for the storage of packaged hazardous and CMR substances in the area of fire safety, as well as occupational and environmental safety,” says logistics business unit manager Tom Heesakkers.
“The 17,500-m2 site, with 30,000 pallet locations, will immediately give us sufficient capacity to safely and efficiently facilitate our existing and future customers’ growth.”
Construction of the new facility, some 5 km from Gondrand’s existing warehouse, started in the second quarter of 2017. “We could have opted to upgrade our existing 16-year-old site in Moerdijk, but in the end it proved more effective and future-proof to build a completely new site,” Heesakkers says. While the current building is a steel construction with fire-resistant cladding, the new premises are being built entirely in concrete, which is “inherently fire-resistant”. The new building will have a fire compartment divided into five different temperature zones, providing a range of termperature-controlled options. “The design also includes a number of small compartments where goods that are difficult to segregate can be stored, including a room where we can safely take product samples,” Heesakkers adds.
www.gondrand-logistics.com
Hoover Ferguson has opened a new purposebuilt facility in Aberdeen, Scotland, offering tank cleaning, chemical transloading and chemical storage services. The site also has a laboratory, workshop and office space.
“Despite the challenging offshore oil and gas environment that we have been operating in, we recognised the demand in the UK market for high-quality bulk chemical storage and transloading as well as tank cleaning services,” says UK managing director Gary Wilson. “With our existing premises in Bridge of Don and Kintore, the location of this newest site perfectly positions us to further serve our customers from the north, south and centre of Aberdeen. We’re excited about what this expansion represents for Hoover Ferguson, but, more importantly, we’re looking forward to the positive impact it will have on our customers.”
www.hooverferguson.com
Finland-based LNGTainer has launched an innovative tank container concept for carrying LNG or other cryogenic liquids. The 40-foot unit has a tare weight of 9.5 tonnes and a capacity of 47.5 m3, helped by the use of Outokumpu’s Supra 16plus stainless steel.
The container looks different to other tank designs for LNG, largely because the honeycomb/perlite insulation is installed on the inside of the tank, giving a hold time of 60 days. “The most revolutionary aspect of the new tank container, and what gives a basis for the advanced design, is the fact that the insulation has been moved from the outside of the cryogenic tanks to the inside,” says Tom Sommardal, LNGTainer’s CEO. “The containers are designed as 40-foot ISO containers stackable as per international rules and regulations, and can be flexibly arranged for storage purposes at power plants when used for feeding gas turbines or engines.” www.lngtainer.com
An affiliate of the Jordan Company private equity firm has signed a definitive agreement to become the new majority shareholder in US-headquartered Odyssey Logistics & Technology. The transaction is expected to close during the third quarter, with no changes expected to Odyssey’s current management, core strategy or mission.
“ With the Jordan Company, Odyssey will continue its path of strategic growth, both organically and through acquisitions,” says Odyssey president and CEO Bob Shellman. “This transaction underscores our consistent focus on providing broader service offerings, a larger transportation network and advanced technology to enhance our global supply chain capabilities.”
“ The Jordan Company targets partnerships with established and profitable companies like Odyssey,” adds Brian Higgins, senior partner at The Jordan Company. “We are excited to partner with Odyssey’s leadership team
and to support their vision for continued growth through investment in services and technologies for their customers.” www.odysseylogistics.com
Abbey Logistics Group is to close its general haulage and Pallet Track operations to concentrate on road tanker and warehousing activities. The company has grown rapidly in the past two years through its core tanker business, which handles foodstuffs, polymers and non-hazardous chemicals. In addition, it has expanded the range of value-added services it offers to include warehousing, drumming and reprocessing.
“ This closure enables us to provide a greater focus on the markets and customers where our core skills are strongest and we can make a positive impact and bring the most value to our customers,” says CEO Steve Granite. www.abbeylogisticsgroup.com
Imperial Logistics International, which handles all of Imperial Logistics’ business outside Africa, has reported a 26 per cent increase in sales for its financial year to the end of June 2017. Revenues reached €1.64bn with EBIT up 19 per cent compared to 2015/16 at €75.4m.
“ The significant increase in turnover and profits at Imperial Logistics International is
due to positive developments at the express freight service company Palletways, which was taken over in the middle of 2016, and positive organic growth through new projects in our traditional business,” says CEO Carsten Taucke. www.imperial-international.com
Den Hartogh’s Latin America division has been presented with the Solvay Excellence Supplier Award for Maritime Logistics Services, recognising Den Hartogh’s responsiveness, execution and quality and compliance performance. Solvay’s Brazilian operation, which goes under the Rhodia name, is the largest tank container exporter in the port of Santos.
“
The award is recognition of our efforts and provides motivation for our team in Rio, especially in light of a post-integration year associated with so many changes and new processes,” says Jean Felipe Albuquerque, Den Hartogh’s general manager for Latin America. “Rhodia measures their entire supply chain, not just up to the port in Santos. So this award is not only a reward for the Rio office but for all the Den Hartogh teams that work with Rhodia around the world. Without everyone performing so well throughout the year, this award would not have been possible.” www.denhartogh.com
DIGITALISATION HAS THE potential to disrupt traditional supply chains and alter the balance between different players, with those in intermediate positions in the chain probably most at risk. It was, then, entirely appropriate that the European Federation of Chemical Distributors (Fecc) put the issue high on the agenda at its 2017 Annual Congress, which took place in Warsaw, Poland in June.
As summarised in the first part of this report (HCB October 2017, page 66), the transparency offered by digitalised systems and the demands for greater sustainability through the development of a circular economy go hand in hand, although the growing risk of cybercrime is something that all players in the market need to be aware of and guard against.
But what does all this mean for chemical distributors and their existing place in the chain? Goetz Erhardt, European head of Accenture’s Industry Consulting Practice for the chemicals, metals and mining sectors, asserted that customer and user experience will take on ever greater importance as the use of digitalisation in the supply chain increases. To succeed in this new marketplace, distributors will have to focus on developing new value propositions and “distinctive customer journeys”. As such, they will have to overhaul existing solutions and experiment cautiously with new formats of customer engagement, such as inter alia chatbots and smart phone apps.
The new business-to-business (B2B) paradigm, Erhardt continued, will be
“information abundant” and marked by dynamic networks with a “relentless focus” on customer and user experience and collective value creation. Distributors will therefore have to place ever greater store on service, knowhow and infrastructure to flourish. Moreover, the coming years will see B2B trade becoming more “consumerised”. Among other things, buyers, as well as becoming much more pricevalue sensitive will exhibit higher expectations of customer service and demand solutions more tailored to their needs. They will also expect service providers to understand their end customers’ needs and be “increasingly influenced by what they hear from others”. Buyers will also become more knowledgeable and self-directed, wanting “more specific expertise” from the seller. Additionally, they will monitor and evaluate suppliers more critically and in so doing “require ongoing engagement”.
Ralph de Haan, CEO and co-founder of Kemgo, “a B2B e-commerce platform specifically designed for the chemicals, plastics and fertiliser industries”, then described the “marketing and sales funnel”: this pictures the buyer’s mindset moving from awareness to interest, consideration, intent, evaluation and finally purchasing. In the past, he noted,
marketing was largely confined to the first two stages, with sales functions covering the rest. In an ever-connected world, though, this will change, with marketing covering everything up to and partly including evaluation while sales will largely be concerned with just the actual final purchasing stage.
While digitisation refers to creating a digital version of analogue and/or physical items, such as paper documents, images and sounds, digitalisation refers to enabling, improving and/or transforming business operations, functions and models and processes by leveraging digital technologies coupled with a broader use of digitised data “turned into actionable knowledge with a specific benefit in mind”. Digital transformation is “the profound and accelerating transformation of business activities, processes, competence and models to fully leverage the changes and opportunities of digital technologies and their impact across society in a strategic and prioritised way”, he explained.
To build a successful digitalised business, companies need to “create the right mindset” and have a shared understanding of where they want to go and what they want to achieve. They must also put the right leadership in place and “launch a group focused on digital transformation”. Meanwhile, by using an e-commerce platform, they can establish an online presence; increase exposure; allow their sales team to focus on strategic customers; and benefit from lower costs to serve. They can also gain access to much more usable information, with the platform offering them generally enhanced convenience and efficiency.
Kemgo+, he revealed, is a premium service that uses Kemgo’s “global credibility and expertise” to build a distributor’s or producer’s brand while helping them to manage their sales and optimise their operations. By using the service, companies, de Haan asserted, are able
“to increase their credibility in the chemical community” while becoming visible in new markets at a low cost. Furthermore, as well as benefitting from the fact that buyers will be able to find them based on their searches for a competitor’s products, they also gain access to “thousands of buyers across the globe”.
They can also work with Kemgo to create a global brand using its patent-pending brand recognition tool. After all, if customers remain unaware of a company and its products, they will simply buy from a competitor instead. “Information is power,” he said, asserting that “Kemgo is different”. Designed “by experts in the chemical industry for the chemical industry”, the system ensures that companies using it will only be approached by qualified members of the platform, all of whom have to first be verified to use it. At the same time, companies utilising what Kemgo has to offer can control how transparent they wish to be when it comes to prices, volumes, availability and identity. Similarly, they can easily select the countries in which they want to do business as well as whether they want to deal with producers, distributors, traders, agents or all such players.
In a similar vein, Noah’s Ark Chemicals CEO Bharat Bhardwaj asserted that his company’s
GoBuyChem.com e-commerce platform can also save companies selling chemicals significant time and money while affording them easy access to new markets. To reap the potential rewards of the digitalised market, distributors will have to “embrace 21st century buying and selling habits”, noting that even the most conservative of industries use price comparison websites. Moreover, the pressure on profits in today’s slow market is a further reason to change the way they sell chemicals, he said.
At present, Bhardwaj continued, the process of selling to a large number of buyers is time consuming, depends heavily on maintaining relationships and is complicated by the issue of different payment terms. By using the GoBuyChem platform, however, the seller has just one selling point, viz GoBuyChem, and so the whole process is “immediate”, saving sellers time while meaning they only have one payment term to contend with. As well as being assured anonymity and reduced risk, the platform also gives them “instant access to a significant client base”.
As payment is always received from GoBuyChem, administrative costs are reduced, with use of the platform doing away with the need to set up and maintain multiple clients. Similarly, companies also gain the ability to post and/or amend their »
prices “on the move” using a smart phone. The platform, Bhardwaj told delegates, offers a “user-friendly personal page layout for the seller, with the seller controlling the prices shown”. Likewise, there is also a clear layout of price comparison results.
GoBuyChem, meanwhile, maintains a full back office team so contact can be readily made by email or telephone. What’s more, by the fourth quarter of next year, both suppliers and buyers will also “be able to track the supply chain prior to the collection/delivery of cargo”. The company is also seeking to further develop the price information available to companies while also providing even more data by which buyers and sellers alike can benchmark performance in real time.
To date, said Overlack co-CEO Peter Overlack, traditional channels to market have been
“working well or even very well” and cover 95 per cent of the chemical distribution sector’s business volumes. Furthermore, he stated, “not everything we do can be standardised and handled without manual processing”. There are “three focal points of digital influence”, he continued, explaining that for distributors digitalisation has the potential to optimise in-house processes, enable the receiving of online orders and facilitate the formation of webshops.
While this poses no risk to the distributor, producers offering chemicals through their own webshops can be seen as a “conflict of channel” and thus there is a “need to clarify the position of dealers”. The third focal point, meanwhile, concerns external operators setting up “functioning platforms” that take over business from traditional distributors, resulting in a potential “loss of influence and business” for the sector.
“Without panic, hype or exaggeration, there is cause for unrest,” he told delegates, noting that such a situation can, in the best case, prove to be a creative and positive force. Nevertheless, he continued, today’s
digital developments “require our attention”, particularly those concerning what he called “the so-called platforms”.
While describing Amazon and Alibaba as “the general stores of the internet age”, Overlack pondered what exactly an industrial platform is and whether such “specialised industrial platforms make sense”. If they do, how many, he asked, will there be? “In the ideal case only one,” he said, and one that is “positioned Europe-wide and most likely related to a logistically contiguous delivery area”.
Distributors, Overlack stated, do not simply provide products, but also industry knowhow and extensive knowledge regarding the regulatory landscape. They also have an important role in handling “the whole documentation business”. External platform providers, on the other hand, “receive full data control and customer master data of the suppliers”, becoming “the absolutely essential point of contact for the end customer”.
What then, he wondered, can distributors do in response to this potential threat to their business? One possible answer, he argued, is for distributors to join together and form their own e-commerce platform that benefits the sector as a whole. “We are convinced that running a platform is not rocket science,” he told delegates, reasoning that the “only one limited input factor connected with the knowhow of the platform operators” concerns IT-based matters. This IT knowhow is not impossible to attain and execute. “It will not cost a fortune and can relatively easily be adapted to the needs of the chemicals business. We are stronger than we think,” he said.
Overlack then moved on to the subject of what such a platform, which he dubbed ‘Kemix’, might look like. In one scenario, he said, 15 to 20 per cent of Kemix shares could be held by “special purpose shareholders”, viz its management, financers and other key players. The remaining 80 per cent, meanwhile, could be distributed among the suppliers of the platform, meaning that “the suppliers of this platform [would be] its shareholders” and directly profit from its success. »
Another scenario, he offered, might see the shareholders’ rights limited to “data backup measures and methods of redistribution of the profits generated”. Under this arrangement, “a buyback of shares of the fund [could] only be performed by the fund itself”, with the fund remaining in the possession of the company operating the platform. “It’s not all that difficult. The market and organisational power rest with us. But this is not the sort of business that you can develop alone,” he said, noting that a collective and cooperative approach would be needed to ensure its fruitful development.
Hans ten Cate, European commercial director for Dow Corning’s Xiameter e-commerce business, then took the podium to give delegates a run-down of the “unique e-enabled Xiameter business model”. At the turn of the
century, he explained, Dow Corning’s offering “was becoming commoditised”. Concurrent with this, “increasing capacity in a long market” was leading to utilisation concerns. Together, these factors ultimately led to the 2002 launch of Xiameter to provide “an online business model taking advantage of the integrated back office application”.
From the start, he said, “strict and transparent business rules became the foundation of setting customer expectations”. While the Dow Corning brand bases its value proposition on the relentless pursuit of innovation in the field of speciality products and services, the Xiameter brand focuses on pursuing efficiency in the field of standard silicone products. “The two brands allow us to meet the needs of all customer segments,” he said. Moreover, the Xiameter brand “enables Dow Corning to efficiently sell high quality, reliable, standard silicone products at market-based prices” by standardising options and services. At the same time, the Xiameter business model “separates products and service, [offering] customers who know how to use these standard products
a quicker, easier and more efficient way to purchase their products”.
By offering a web-enabled brand, ten Cate argued, companies can gain an efficient way to serve customers; a new growth strategy; and a streamlined way of selling and buying. It is also a means of enabling innovation; integrating strategy with operational tactics and execution; increasing efficiency in terms of operations; and providing opportunities for automation.
To achieve all this, Xiameter adheres to a number of business rules. These include the pursuit of efficient sourcing through the use of Dow Corning’s global plant and warehouse network, whereby Xiameter chooses what it considers to be the best source location for each order. It also maintains “logical and efficient order quantities” and uses tiered volume pricing to encourage efficient ordering while placing great importance on credit term options; lead-time requirements; and picking and shipping consolidation windows.
Xiameter also provides the best available shipping dates, with its website fully integrated with SAP ERP in real time coupled with stateof-the-art capacity checking capabilities to provide accurate dates. Importantly, it also strives to make online purchasing as easy and as efficient as possible. Indeed, ease of use has been a major factor in customer acceptance, ten Cate noted, revealing that customers can check prices, source product information, place an order and check order statuses and histories around the clock, seven days a week from any location. “Just seconds after [placing an] order, confirmation of price and quantity is provided along with the freight terms, credit terms and ship date, which is based on current supply capability,” he said, adding that there is “no need to call” or wait for a response. “Most paperwork has been eliminated. The job is done the moment the customer clicks to complete the order.” HCB www.fecc.org
The next part of this report in next month’s HCB will look at major trends affecting the chemical distribution sector and the possible impact that digitalisation may have upon it.
Rassmann (NRC) has purchased 100 per cent of shares in the Melrob Group, reporting that the acquisition includes all of Melrob’s various subsidiaries in Germany, India, Japan, Korea, Singapore, Spain and the US. “Acquiring Melrob not only represents the wide-reaching and strategic expansion of Nordmann, Rassmann’s current activities in Europe, but also a decisive step towards growing our business in both the Asia-Pacific region and North America,” says NRC co-managing director Dr Gerd Bergmann. Japan, NRC says, “holds a special position” in its newly expanded geographical presence “as the company has had very successful partnerships with well-known suppliers” in the country for a number of decades. “We are especially excited to be acquiring our own subsidiary in the Japanese market and thereby be able to take advantage of new business contacts and opportunities,” Bergmann states.
“On the one hand, this acquisition is the result of our continued pursuit of Nordmann, Rassmann’s growth strategy,” he continues. “On the other, and through our now complete European and global presence – which gives the whole NRC Group a markedly higher level of visibility on the international market – we’re reaching yet another one of our strategic goals.”
“Nordmann, Rassmann is Melrob’s first choice,” says Melrob’s managing director Ian Melluish. “Strategically speaking, we’ve found the ideal partner – and the extremely close cooperation throughout the negotiating period made it very clear that our companies share a great deal in terms of corporate culture, as well as identical views on ethics. We know that the enterprise we have been building since 1995, with passion and great personal commitment, is being placed in reliable, business-savvy hands.”
Through the takeover, NRC, the company says, “will be acquiring new and important points of access to the markets for industrial chemicals as well as monomers”. Furthermore, NRC will also gain “another unique selling point” borne of Melrob’s operations within the biomaterials sphere. “Melrob represents a large number of prominent suppliers and, with its own production facility in Singapore, is one of
the world’s leading manufacturers of specialty monomers,” it says.
Commenting on the news, Irina Zschaler, NRC co-managing director and board member of Georg Nordmann Holding, states: “We look to this important development in our company’s history with great pleasure and high expectations and at the same time would like to warmly welcome all of Melrob’s staff to our NRC family.”
Subsequent to the acquisition, the two companies signed a deal to distribute Evonik’s range of standard monomers across Europe with immediate effect and its line of speciality methacrylate monomers from the start of January next year. “This is clear proof of the advantages our two companies can offer now following the merger and that together [we] will be even more successful,” Melluish says.
“Evonik is convinced that realigning our distribution business in this way will allow us to address the needs of our customers better and profit from the combined experience of the two distribution companies we’ve chosen to work with,” notes Hans-Peter Hauck, head of Evonik’s methacrylates division. “By taking this approach, we’re positioning ourselves as a leading provider of methacrylate solutions and, together with our distribution partners, ensuring the best possible support for our customers.” HCB www.nrc.de www.melrob.com
THE OHIO-HEADQUARTERED Maroon Group has acquired New Jersey’s Seidler Chemical. Established in 1896, Seidler provides speciality chemicals and ingredients as well as various value-adding services to the pharmaceutical, high-purity electronics, industrial and food and beverage sectors. Seidler’s management team, led by Richard and Martha Seidler, will remain in place and continue to actively manage the business, with Maroon stating that the transaction “is another example of successful entrepreneurs choosing to join Maroon Group”. The Seidlers’ “deep experience, differentiated market insights and value-added capabilities”, it continues, “will be instrumental in executing Maroon’s strategy”.
“We are thrilled about the opportunity to work with Rich, Martha and their team and
welcome a company with a 120-year history to Maroon Group,” says Maroon president and CEO Mark E Reichard. “This acquisition allows us to expand our value-add service offering and build additional scale in attractive end markets.”
“We’re excited to be part of an organisation like Maroon Group that shares our focus on customer success,” Richard Seidler adds. “Providing stability for our employees, customers and suppliers was a priority when Martha and I set out on this course. Maroon has a proven track record of success as it relates to acquiring businesses like Seidler. They understand the importance of servicing the customer, continue to invest in acquired companies and have a thoughtful approach to integration. Maroon Group was the right partner to continue the legacy of our family’s company.”
Meanwhile Eric Post has joined Maroon as vice-president, principal management, coatings, adhesives, sealants and elastomers (CASE).
Having held various positions with Evonik, Elementis Specialties and Emerald Kalama, Post, the company says, “will be integrally involved with the management of existing Maroon Group principals that operate in the CASE market” while simultaneously working to expand the company’s already extensive product range.
“Eric will bring a well-rounded perspective to this role and assist us in identifying additional ways to create value for our customers and principal partners, as well as drive the profitable growth of the business,” says chief operating officer Mike McKenna. “We’re excited to have him as part of our team as we continue to execute on our growth strategy.”
Meanwhile, Michael Naismith has joined Lincoln Fine Ingredients (LFI), which Maroon acquired this past March, as its new warehouse operations manager. “Mike has more than 20 years of management experience with extensive knowledge in warehouse operations and logistics,” LFI says. “Mike brings a vast knowledge of FDA, AIB and OSHA experience with him as he looks to be an integral part in bringing our customers extraordinary service and exceeding their expectations through a positive, proactive and positive team environment.”
In other news, Maroon-owned Addipel has achieved ISO 9001:2008 certification from Management Certification of North America (MCNA). “We are proud of the entire Addipel organisation for achieving this significant milestone,” says Addipel general manager Jake Reichard. “Addipel was founded to provide customised solutions to our clients and has grown to become a trusted partner with a focus on safety, quality and service. ISO certification solidifies the commitment that Addipel and Maroon Group are making to support the needs of our customers.”
Founded in 1977, the Maroon Group operates six regional customer service centres and a network of more than 35 warehouses across North America, with its various regional operating companies focusing on specific markets and geographies. “This operating philosophy has enabled Maroon Group to offer its customers, principal suppliers and employees with national capabilities while maintaining a local focus,” the company states. HCB www.maroongroupllc.com
AZELIS HAS ACQUIRED Georges Walther (GW), a Swiss chemicals distributor with a focus on the personal care, pharmaceutical and food sectors. “Combining this acquisition with existing operations from Azelis Switzerland and Azelis Germany will give us the perfect platform to strengthen our presence in the Swiss market,” says Anna Bertona, Azelis CEO and president, EMEA. “It will allow us to focus on advanced personal care products in the portfolio and will enable us to be closer to our customers’ R&D centres.”
“Market consolidation is inevitable in the industry; having access to the Azelis application labs, technical services and network will allow us to continue our growth
trajectory,” adds Jean-Michel Walther, GW’s CEO and head of sales, who will now become Azelis’ new personal care business manager for Switzerland. “We are looking forward to becoming part of a larger family – trust and personal relationships are at the heart of our culture, which will fit extremely well with Azelis’ core values.”
Azelis has also signed an agreement with Allnex to cover the distribution of liquid resins and additives (LRAs) across Thailand.
The move builds on an existing relationship the covers the distribution of Allnex lubricants across Europe and the distribution of its LRA range across France, Spain, Germany, Austria, Romania, Italy, Serbia, the Benelux countries and the Nordic region.
“Azelis and Allnex share a common ambition for growth in the region,” says
Visava Lertrojanapunya, Azelis’ managing director for Thailand. “Through our partnership at group level, Azelis has proven that our teams have a solid technical background and are well connected to our customers. The addition of Allnex products means Azelis Thailand can now offer a synergistic portfolio of resins and additives, for example in the decorative paint market.”
“As our distributor in water-based liquid resins and additives in Thailand, Azelis’ professional and experienced team has supported Allnex in expanding our business portfolio and connection to the market,” Giorgio Noli, Allnex regional business director, Asia Pacific, adds. “Azelis will be able to provide world class services beyond customer expectations and requirements. We look forward to successful and strong business growth together in the region in coming years.”
Meanwhile, Azelis Americas has combined its PT Hutchins and Ribelin businesses, with the territories covered by the newly expanded Ribelin now stretching from Florida to Seattle. This, Azelis says, demonstrates its commitment to the US coatings, adhesives, sealants and elastomers (CASE) sector. Ribelin, it continues, “is comprised of a team of highly trained, dedicated technical sales representatives, supported by application labs with degreed chemists, technical marketing and best-in-class customer service”.
“The CASE market segment is vitally important and we need to continuously improve our ability to service the market’s changing demands,” Frank Bergonzi, CEO and president of Azelis Americas, reasons. “The newly expanded Ribelin will allow our CASE segment to better serve our customers, our principals and our employees.”
Commenting on the move, CASE managing director Dan Gruber states: “We had significant success and positive feedback from our principals and customers with the integration of EW Kaufmann into the GMZ brand last year. We decided it makes perfect sense to do the same with PT Hutchins and Ribelin, especially given the fact that the Ribelin brand has been a renowned leader in the CASE market for over 80 years.” HCB www.azelis.com
IN TERMS OF global expansion, it’s been a busy time of late for Bodo Möller Chemie, having kicked off the year with the opening of a new Moroccan arm in Casablanca. “With the opening of a new branch in Morocco, we are reinforcing our presence on the African continent and after heading towards north and south Africa now follows the western region as well. We are increasingly focusing on products for applications in adhesive and sealing technology, in the composites and electrical sectors, as well as in the paint and coatings industry,” CEO Frank Haug says.
“The west African market is experiencing an exciting phase, as this country offers many development opportunities and there is a strong demand for products and industrial sectors that we serve.”
Meanwhile, on the eastern shores of the Med, the company has also now opened a branch in Tel Aviv, becoming Huntsman Advanced Materials’ sole distributor in Israel, where Bodo Möller will primarily focus on serving the needs of the local aviation and aerospace industries. “Israel is a high-tech location and there is great demand for specialised solutions in many complex industries. A suitably qualified team on site is needed to provide advice and handling,” Haug states.
Further east, Bodo Möller reports that it has taken over the distribution of Dow Automotive’s Thixon and Megum product lines from Shanghai Caraba Industrial & Trading Development.
“The automotive industry in China is the largest in the world measured by automobile unit production per year and the growth goes on,” Haug says. “Recently, as published in the Automotive News China, Dongfeng Motor Corporation in a joint venture with the Honda Motor Company announced the employment of 2,200 more people to boost vehicle output.”
The contract in China is not the only one involving Dow Chemical; closer to home Bodo Möller has been appointed to distribute Dow Automotive adhesive products across Hungary, Romania and Serbia. Bodo Möller’s Hungarian arm will act as the central location for regional support from its site in Tatabánya, distributing such brands as BetamateTM, BetalinkTM, BetacleanTM, Betaprime™, BetasealTM and BetafoamTM that are primarily used in vehicle construction. “The markets in eastern and south-eastern Europe,” says Otmar Ruhaltinger, managing director of Bodo Möller Chemie Hungary, “are characterised by high growth rates and an enormous need for specialised and application-specific specialty chemicals from the adhesives and sealants sector.”
“Our customers realise the geographic proximity as an immense advantage, in addition to our application-driven expertise about the materials,” adds Haug. “For this reason, we are present with our own branches in the Czech Republic, Slovakia, Croatia, Russia and Hungary and are constantly expanding the business from high-quality expertise and distribution in eastern Europe.”
Meanwhile, across the Atlantic, Bodo Möller has established two new subsidiaries in the US and Mexico. Based in Atlanta, Georgia and Mexico City, respectively, the new entities will similarly focus on the distribution of Dow Automotive adhesives as well as various other products. Commenting on the news, Andreas Moser, marketing director, formulated systems, states: “The American market is very exciting for us due to its absolute size and growth perspective as well as the dynamism of e-mobility products. Future-oriented manufacturers and suppliers are aware that there is a high potential for innovation and demand for modern products and services.”
“In the age of e-mobility and extreme lightweight construction, manufacturing companies from the transportation industry are faced with high demands,” Haug notes.
“They are rarely able to test products for sealing, bonding or glazing themselves comprehensively. This competence lies with us as a distributor and consultant.” HCB www.bm-chemie.com
Brenntag has officially established Brenntag South Africa following the merger of erstwhile separate operating entities Lionheart, Plastichem, Multilube and Warren Chem Specialities. Described by Brenntag as “one of the leading chemical distributors for specialty chemicals in the southern African region”, the new company employs a staff of around 180 across locations in Cape Town, Johannesburg and Durban, serving customers from the industrial, life sciences and material sciences sectors among others.
“ The new company has a focused commercial set-up, specifically tailored to customer industry sectors and leveraging on the expertise and skills of the former individual companies, ensuring that the business is strategically and operationally better positioned to realise growth,” says Brenntag Africa president Michael Thomson. “Bringing the individual companies together has allowed for the development of a customer-centred approach, aided by dedicated product management, strengthened departments for safety, quality and regulatory affairs and more streamlined and efficient operations functions.”
“
The new structure is a perfect commercial organisation, leveraging our expertise to serve our valued customers and suppliers,” adds Carl Blomme, regional president, Europe West and MEA. “It is of mutual benefit to both employees and the company. Due to our performance excellence culture, our focused organisation will create an environment where individuals can develop and where we can assure delivering the best services to our business partners.”
In other news, Brenntag Blending Solutions (BBS) has opened a state-of-the-art facility at Lutterworth in the UK. Equipped with a 25,000-litre multi-purpose vessel and a 50,000-litre storage tank, the new facility is capable of creating both liquid/liquid and liquid/solid blends. “We are delighted to announce the launch of our new facility
at Brenntag Lutterworth, offering additional scope to provide blends across the south of the UK,” says BSS business manager Andrew Ferris. “Our Blending Solutions business adds real value to our customers and the new facility reinforces our commitment to developing this key area of our business.”
Meanwhile on the financial front, Brenntag reports that is has placed a new €600m corporate bond with institutional investors. “We have taken advantage of the currently attractive market conditions to secure long-term funding at an extremely low interest rate,” says CFO Georg Müller. “The strong level of investor interest in the transaction shows once again that our company is highly attractive to the capital market. Following the successful refinancing of our syndicated loan at the beginning of the year, the new corporate bond further improves our maturity profile and supports the group’s future business development.” www.brenntag.com
Univar has acquired Tagma Brasil, a Brazilian provider of custom formulation and packaging
services for crop protection chemicals that include herbicides, insecticides, fungicides and surfactants. Commenting on the news, Univar chairman and CEO Steve Newlin states: “Brazil has agriculture and agro-food exports of more than $89bn and a domestic market that serves nearly 210m people. This acqu isition expands Univar’s agriculture business in one of the world’s fastest-growing agricultural markets. In addition, Tagma’s formulation and packaging capabilities will enhance the value proposition for several of our key global supplier partners and Tagma’s strong culture of safety, integrity and quality will be an excellent complement to Univar’s already robust agricultural business in North America.”
Meanwhile, Univar-owned ChemPoint.com has launched a new website, www.laminating adhesiveproducts.com, developed in collaboration with The Dow Chemical Company. “This project is just one example of ChemPoint’s value-added digital services that support our supplier partners by proactively making their brands a part of the customers’ online buying journey,” says ChemPoint’s North American sales director Rick Hoener. “By offering customers 24/7
access to the product, application, formulation and regulatory details that they require, we are changing chemical buying trends. In the past, this information wasn’t as readily available and easy to navigate. Now in just two minutes, customers can find the product that suits their application needs.” www.univar.com www.chempoint.com
Nexeo Solutions has signed a new deal with Cabot to distribute its speciality carbon, fumed silica, fumed alumina, dispersions and aerogel product lines across 18 eastern and Midwest US states. “This new agreement with Cabot expands our specialty chemical product portfolio and we are thrilled to offer their high-quality, highvalue products,” says Joey Gullion, Nexeo’s vice-president, chemical specialties. “Cabot’s products complement our existing portfolio and, when combined with our market reach, technical expertise and supply chain presence, we will be able to deliver superior technical support and service.”
In other news, Brian A Selmo, a partner and portfolio manager at First Pacific Advisors (FPA), has been appointed to Nexeo’s Board of Directors, bringing its total membership up to 10. “We are pleased to have Brian join the Board of Directors,” says Nexeo Board chairman Dan F Smith. “FPA’s long-term interest in the business and Brian’s vast experience across numerous industries will be invaluable to our company.” www.nexeosolutions.com
IMCD has unveiled a new coatings laboratory in King of Prussia, Pennsylvania, bringing the company’s total number of labs around the world to 35.
“Following the opening of our personal care laboratory earlier this year, we are delighted to extend IMCD’s technical capability and offering with this new dedicated coatings facility,” says IMCD US president Marcus Jordan.
“IMCD’s market-focused technical centres are an important element of the value-added proposition we offer to both our customers and supply partners and will also further enhance the knowledge and technical capabilities of the IMCD US coatings sales team.” www.imcdgroup.com
Momentive Performance Materials has expanded its distribution agreement with France’s Safic-Alcan to include eastern Europe. “Safic-Alcan and Momentive have a longstanding and successful relationship in western Europe,” says Martial Lecat, CEO of Safic-Alcan’s holding company Safinca. “We are delighted to extend our commitment with a world leader of silicone fluids and boron nitride and to offer enhanced technical solutions and added value products to our customers in personal care and industrial markets.”
Safic-Alcan UK, meanwhile, has opened a new KemCreate life-science applications lab in Haydock, Merseyside. “We aim to provide unrivalled customer support providing an outstanding formulation service,” says managing
director Barry McDonnell. “This significant investment by Safic-Alcan UK will allow us to fully explore the synergistic benefits of our principals’ raw materials in personal care formulations. We hope to inspire [companies] with marketing ideas combined with delivering innovative solutions for personal care products that meet the trends of our market.”
www.safic-alcan.com
Biesterfeld Spezialchemie (BS) has begun distributing products from Kao Chemicals Europe across Switzerland in a move that expands its offering to the local personal care and cleaning industries.
“ We value the trust that Kao Chemicals Europe has placed in us and are delighted to be able to offer their customer-focused solutions on the Swiss market,” says Sergej But, BS market manager, cleaning. “Our team is highly familiar with the extensive product range and the needs of customers in this region. As a result, we are confident that we can continue to make the collaboration a success.”
www.biesterfeld-spezialchemie.com
AS MIGHT BE expected, composite intermediate bulk containers (IBCs) were suitably well represented at Interpack in Düsseldorf this past May, with these ever more popular packagings rubbing shoulders with the numerous steel, plastics and fibre drums detailed in the first two parts of this report (HCB September 2017, page 32; October 2017, page 100). Certainly, anyone passing by the very eye-catching stand operated by Germany’s Schütz would have been hard-pressed not to notice a veritable bonanza of these units, including the new Ecobulk SX-D, a UN-approved design that, the company states, “can literally withstand ‘burning’ situations”.
“This IBC with a volume of 1,000 litres not only has a conventional [cage], it also features a complete steel coat,” Schütz explains. “Firmly welded to the steel bottom plate, the additional
coat forms its own fully sealed container around the inner bottle. This double wall construction provides effective additional leak protection, even under extreme conditions, such as fire. In exceptional conditions and emergencies, maximum safety is paramount – and that is precisely what the Ecobulk SX-D offers.”
Indeed, the fire resistance of the SX-D, it continues, was “confirmed in the UL 2368 test conducted by Underwriters Laboratories”, an independent organisation headquartered in Illinois that tests and certifies product safety. “Underwriters Laboratories awarded the IBC the UL-certified mark. This means that the container complies with the Fire Protection Directive NFPA 30: Flammable and Combustible Liquids Code of the National Fire
Protection Association in the US. It certifies that the Schütz Ecobulk SX-D is ideally suited for flammable and highly flammable liquids as well as for use in potentially explosive [Ex] zone 1 and 2 operating areas,” Schütz reports.
But certified fire-resistance is not the only benefit that the company sees this new unit as offering shippers. “For example,” Schütz states, “the SX-D can be used for hazardous goods or other sensitive filling goods, such as toluene diisocyanate (TDI). Until now, these filling products have been packed in smaller containers with a lower volume, such as steel drums, to ensure that less liquid can leak out in the event of an accident. The double wall of the SX-D greatly reduces the risk of leakage. Should the inner container leak, the additional wall prevents sensitive or flammable media from seeping out into the environment.”
“Another special safety feature of the design is that the container’s three openings are located in the top plate and are additionally protected by steel caps,” it continues, adding that an opening with a nominal width of DN 150, a G2 and a S56 bung are used for filling and discharge. “One of the bungs can be used to discharge product with a dip-tube system. In
combination with a conventional pump system, this guarantees safe and easy discharge. The second bung is located close to the edge of the container and can, for example, be used to completely empty the container by tilting it.”
Schütz has also now further developed its Foodcert and Cleancert lines of packagings intended for the transport and storage of highly sensitive filling goods, taking full advantage of the show to unveil its new Foodcert + Aseptic and Cleancert + Dualprotect offerings that it says takes things “up to the next level” when it comes to safety and cleanliness. “As a top product innovation, Schütz is now offering these IBCs with a liner system including UN approval, thus ensuring maximum quality protection with minimum effort,” it asserts.
While Ecobulk Foodcert + Aseptic IBCs aim to meet the particularly demanding requirements of the food, pharmaceuticals and personal care sectors, Cleancert + Dualprotect models are aimed at industries that handle highly sensitive non-food products, such as adhesives, for example. As with Foodcert + Aseptic units, Cleancert + Dualprotect IBCs also offer “double protection for filling products” thanks to their integrated liners. On top of this, these IBCs feature “a leakproof inner bottle”, therefore “effectively avoiding leaks even if the liner is damaged,” the company continues. “The new packaging solution for technically demanding products is extra safe and, because it is delivered ‘ready-to-fill’, is also exceptionally user-friendly. Due to its maximum quality protection, the container is ideal for transporting natural and synthetic organic compounds, inorganic compounds and silicones.”
“In most multi-use systems, there is a significant risk of accidental contamination due to product residues,” Schütz says. “This is ruled out in the two new models. Filling into the integrated liner minimises the general risk of contamination and there is no risk of the filling product coming into contact with condensate, which can form inside the inner bottle. The liner’s oxygen barrier provides additional protection against oxidation, vitamin depletion and microbial contamination. And, unlike other container types, there is no need for nitrogen blanketing.”
Another German IBC maker with plenty of new products on show at Interpack was Werit, which has further expanded its range of composite designs with the launch of the new VARIOline. While these units comprise a steel cage affixed on top of a plastics or wooden pallet, they differ greatly from traditional IBCs by housing two, three or four separate inner receptacles with filling capacities of up 490 litres rather than one large bottle.
UN-approved for the transport of dangerous goods, these new units, the company says, offer shippers a “flexible container for individual needs” and are ideally suited for transporting several different filling media in one IBC. As well as offering “easy reconditioning”, they can also be stacked with conventional 1,000-litre designs, with their proven tubular-frame cages fully protecting the inner receptacles and their contents. Indeed, the company says, they actually offer “higher safety by splitting the filling media up into several smaller containers in one packaging unit”, something it describes as the “multi-compartment principle”.
Also on display at the Werit stand was a prototype of its small-volume COMPACTline of UN-approved IBCs. Similarly utilising a galvanised tubular-framed cage, these units incorporate a single 300-litre inner bottle that is particularly suited to the handling of sensitive fluids. Offering “easy tapping and
[the] best residual discharge”, these simpleto-clean multiuse packagings can be safely stacked with 600-litre and 800-litre IBCs and offer “easy transport securing”. Moreover, with dimensions of 1,040 mm x 800 mm x 600 mm, they also facilitate “optimum use of cargo space”, with shippers able to transport a total of 64,000 litres within a single jumbo truck when employing these units.
At the same time, Werit has also unleashed a new 3” IBC piston valve that, flow-optimised for highly viscous fluids, offers 80 per cent faster discharging when handling fluids with a viscosity of 1,200 mPa. “Robust, dimensionally stable, highly load-resistant and long-lasting”, the valve, it says, also features an “ergonomic handle for comfortable use” and can be supplied either welded to an IBC or as a replaceable unit as needed.
More German IBCs were to be seen on the stand operated by Auer Packaging, which manufactures 1,000-litre composite units that it can furnish with or without UN approvals as needed. Reusable, weatherproof and boasting “low tare weight fluctuations”, these IBCs, the company says, are “the ideal storage and transportation container for liquids of all kinds”. The company also produces collapsible IBCs that can be supplied with aseptic liners for sensitive non-regulated liquids. Additionally, Auer can also readily provide shippers with »
an extensive array of plastics pails, screw-top jars, crates, boxes and pallet containers as well as numerous workplace storage accessories.
US-headquartered Greif, meanwhile, has now further enhanced its GCube range of composite IBCs with the introduction of a new co-extruded barrier layer technology that eradicates the issue of permeation that can otherwise be a problem when shipping certain types of filling goods. Available all across Europe, the new barrier layer units, the company reports, are proving particularly popular with companies operating within the agrochemical and cosmetics industries, among others.
Produced by Italy-headquartered Fustiplast, which Greif acquired in 2011 and which also operates production plants in Germany and Brazil, the GCube range includes standard models that are fully certified for the transport of dangerous goods by road, sea and air. Available with 2” or 3” valves and 150 mm or 225 mm opening lids as required, they can also be supplied with either wooden, plastics or composite pallets.
Complementing this, the GCube Elektron variant “has been expressly designed to be used in explosion-risk areas” and is able to discharge to the ground any electrostatic charges that may have built up on the bottle surface or inside the transported product. “This is possible thanks to the PE bottle with a dissipative layer and the PE conductive outlet valve, electrically connected to the pallet,” the company says, adding that such units are “ideal for [the] storage and transport of products with low flash points and which must be handled in explosion risk areas”.
Producing UN- and non-UN-approved composite IBCs, as well as various plastics drums and pails, across a network of plants spanning Europe and the Americas, MaschioPack, although founded in 2009, is able to draw on a wealth of IBC knowhow and experience thanks in no small part to the fact that its founder, Pietro Maschio, previously established and headed Italy’s Mamor from its inception in 1972 to its sale in 2003 to Germany’s Mauser. Furthermore, the company prides itself on operating “the latest high technological blow-moulding machinery” that enables it “to deliver excellent quality on the market” and meet the needs of a diverse customer base.
However, MaschioPack’s offering does not simply stop with the provision of factory-new IBCs, including food-grade and Ex units. Rather, the company also operates its Back Ticket Service, whereby, among other things, it “works out integrated recycling programmes to reuse, to rebottle and to recondition dedicated IBCs where only minor spare parts are changed”. This approach, it says, “results in several long-term projects with customers where the same IBCs are brought back and reused as ‘multiway’ because of the high quality of the MaschioPack IBC”. Moreover, it continues, “the activity of cutting and shredding used plastics containers and the manufacturing of the feet for the plastics »
“WERIT HAS EXPANDED ITS RANGE OF COMPOSITE IBCS WITH THE LAUNCH OF THE NEW VARIOLINE, WHICH HOUSES SEPARATE INNER RECEPTACLES”
and hybrid pallets and the corner protections is a 100 per cent in-house MaschioPack activity”.
While France’s Sotralentz is no stranger to Interpack, it has now undergone a change of ownership, having been acquired at the end of 2016 by the Brittany-headquartered Roullier Group. Already this has led to a number of investments, including the installation of new plant at the company’s Drulingen site, while simultaneously providing Sotralentz with what the company describes as “the oxygen and the strategic line” that it had otherwise lacked.
Now part of the Roullier Group’s Packaging Division alongside plastics packagings producer Agriplas, Sotralentz continues to produce variously sized plastics drums and jerrycans in addition to the SLX range of UN-approved composite IBCs that includes foodgrade, Ex and UV-protected designs, all of which are backed by the Sotralentz Recycling Service that has been collecting and reprocessing used units across Europe and North America since 1992.
In terms of all-plastics units, Germany’s Rikutec reports that it has further expanded its range of IBCs with the launch of a new conductive model that features a sleeve between the inner bottle and outer skin. Normally, the company says, such a unit would utilise a conductive outer layer on the inner bottle. However, by using a sleeve instead, the inner bottle exhibits “better characteristics with regard to strength” while simultaneously ensuring there will be no contamination caused by the conductive material touching the filling goods. This is of particular saliency given that a lot of Rikutec’s customers are drawn from the high-purity electronics and semi-conductor sectors where such contamination could prove very costly.
Suitable for the packing of highly flammable and UV-sensitive goods, this new UN- and
DEKRA-approved unit is designed for use in EX zones 1 and 2. With a filling capacity of 1,000 litres, the unit eschews the use of a bottom outlet and is thus dispensed and filled with dip tubes instead and can be supplied with a detachable or welded-on plastics pallet as required. Meanwhile, in a similar vein, the company has also now unveiled a new Ex-approved high-purity plastics drum capable of handling packing group I liquids, making it, the company says, one of only a few such drums currently available on the market.
Designed to have an active life of 10 years, the UN-approved Varibox from RPC Promens was another all-plastics IBC on show at Interpack that can offer the user numerous benefits, not least in terms of safety. Available in a variety of
colours for branding and product identification purposes, the unit features a sturdy doublewalled design that ensures full containment of its filling goods. Indeed, such is the level of containment offered by the system that the German DIBt, the company reports, has certified it as not requiring a sump pallet or similar extraneously means of bunding.
“The Varibox is discharged from the top,” RPC continues. As “users safely connect to a leak-free extractor” there is “no need to open caps or closures” and thus there is “no risk of contact with chemicals”. Furthermore, with the interior of the unit “shaped like a bathtub” and the extractor tube “in a sink”, the unit’s design “minimises residues” and waste. “The Varibox is the true multi-trip container,” the company says. “Its durability and reliability are proof of our many decades of expertise in this field.” HCB www.interpack.com
up from revenues of $438.5m in 2017. However, the “vastly populated region of Asia Pacific is projected for the most impressive growth rate of 4.9 per cent”, something that is “significantly higher than the global average”.
“The global metal IBC market is driven by a number of factors, but primarily owing to containerisation of consumer products that are leading to cost optimisation and ease in transportation, rapidly evolving cross-border trade between various emerging economies and growing demand for sophisticated solutions [for] bulk liquid transportation,” it reports. “Containerisation has made it possible for the shipping industry to transport products without being a financial burden. IBCs have generated a great level of productivity as they help in proper stacking and enhance the efficiency of warehouse management.”
THE GLOBAL METAL intermediate bulk container (IBC) market looks set to enjoy compound annual growth of 4.1 per cent during the period 2017-27, says a new report entitled Metal IBC Market from Transparency Market Research (TMR). “In 2017, the market had secured a valuation of $1.3bn,” TMR says. “However, by 2027, it is envisioned to reach $2bn. Containerisation has led to significant low costs for the shipping industry, which has further propelled the demand of the global metal IBC market.”
The global metal IBC market, it continues, “is highly fragmented”, with the top ten companies “collectively managing less than five per cent” of total market share in 2017. Identifying such companies as Thielmann, Hoover Ferguson, Custom Metalcraft, Transtainer and Plymouth Industries among others “as some of the notable players currently operating in the
global metal IBC market”, TMR notes that while some are looking to enhance their production capacities and product portfolios, others have been “acquiring carefully” while increasing their manufacturing locations in “the key developed economies”.
“Metal IBCs are extensively used for the transportation of hazardous industrial chemicals to minimise the snapping chances,” TMR says, stating that the industrial chemicals segment of the global metal IBC market is “expected to reach $852m” by the end of 2027.
“Among the two sub-segments based on content, metal IBCs are mainly used for the bulk transportation of liquids. [This] segment is expected to account for a market revenue share of 88.1 per cent by 2027. Technologywise, aseptic technology is highly preferred for manufacturing metal IBCs as they maintain high standards of hygiene,” it notes.
Geographically, North America “is currently the most lucrative region”, with demand there likely to hit a value of around $621.7m by 2022,
At the same time, it continues, the governments of “economic powerhouses, such as India and China, have various ongoing projects that aim to essentially double the volume of current trade in the next five years”. Moreover, the relatively low cost of manufacturing in China and India “has led manufacturers across the globe to move their production facilities to countries in Asia Pacific”. This, TMR says, “is expected to facilitate growth in trade volumes in the region” while also enabling the Asia Pacific region “to emerge [as] a global trade hub”.
“On the other hand, the availability of low-cost alternate transportation solutions, such as flexible IBCs, and the high cost of metal IBCs compared to plastic IBCs are two factors hindering the prosperity of the global metal IBC market,” TMR observes. “Nevertheless, the emergence of intermodal transportation, improving infrastructure in various emerging economies and the growing trade among them is expected to open new opportunities in this market.” HCB
Copies of the 245-page report can be downloaded from the TMR website, www.transparencymarketresearch.com, with licences starting at $5,795 for a single user.
ANALYSIS • THE HIGHLY FRAGMENTED METAL IBC MARKET IS SET FOR CONSISTENT GROWTH OVER THE COMING DECADE, FUELLED BY TRADE GROWTH AND HANDLING BENEFITS
BACK AROUND THE turn of the millennium, the UK Tank Storage Association (TSA) thought there might be mileage in opening up its annual general meeting and creating a one-day conference and exhibition for the sector. It was not a bad idea as ideas go – there was little on offer for the European storage terminal sector in those days and there was already a growing awareness of the need to have a forum to discuss regulatory and technical developments.
Those tentative steps confirmed an appetite for such an event and, over the years, the TSA conference and exhibition has outgrown two venues and is already pushing at the limits of a third. What the founders were not to know back in 2001 was that only a few years later
a devastating explosion at the Buncefield oil depot would put terminal safety well up the agenda at the national enforcement bodies and would generate a need for the use of increasingly sophisticated systems and equipment. The impact of that 2005 event is still reverberating each time the TSA conference gathers, as it did this year on 28 September, once again at the Ricoh Arena in Coventry.
The success of the TSA event is founded on simple principles: line up some relevant and interesting presentations to attract senior commercial and technical personnel from the local bulk liquids storage terminal sector, then watch as equipment and service suppliers fall over themselves to get the best pitch in the
accompanying exhibition hall. This year there were an impressive 62 exhibitors, with the hall straining at the seams to accommodate them all. And the conference sessions are organised to give delegates the maximum amount of time to get around as many of them as possible, and to offer exhibitors the maximum face time with potential customers.
Terminal operators in the UK interface with the authorities largely through the competent authorities for the Control of Major Accident Hazards (COMAH) Regulations, the UK’s implementation of the EU Seveso Directive. Those agencies are primarily the Health & Safety Executive (HSE), the Environment Agency (EA) and their equivalents in Scotland, Northern Ireland and Wales.
So it was then, after introductions by TSA’s new president, Andy Amos, projects director at the United Molasses Group, and the conference chairman, HCB’s editor-in-chief Peter Mackay, that the opening presentation was made by Dr Paul Logan, director of HSE’s Chemical, Explosives and Biological Hazards Division –which has taken over the work of the former Hazardous Installations Division.
Dr Logan’s presentation was titled: ‘Future regulation’, which may have prompted some in the audience to mutter “don’t we have enough already?”. But he was at pains to put HSE’s efforts into context: 144 people were killed at work in the UK in 2016 – this is among the lowest rates in the world, but that is no reason for complacency.
In fact, 2,515 people died in the UK from work-related illnesses and injuries last year, many of them from asbestosis, which remains a significant killer. There were also more than 72,700 ‘seven-day injuries’, many of which were life-changing for the victims. In total there were 30.4m working days lost through workplace accidents, with a cost to the country of more than $14bn.
CYBER-SECURITY IS INCREASINGLY IMPORTANT IN AN EVER-MORE CONNECTED WORLD AND SOMETHING THAT ALL INDUSTRIAL COMPANIES WILL NEED TO START TAKING SERIOUSLY, DELEGATES HEARD”
And things could easily be worse: Dr Logan presented some data that showed there are on average around 50 ‘dangerous occurrences’ every year, any one of which is “just an ignition source away from a disaster”.
A key priority of Dr Logan’s division for this year is to reduce the likelihood of lowfrequency, high-impact catastrophic impacts. This will involve working with stakeholders –including TSA and other trade associations – on strengthening safety leadership across all major hazard sectors. Working through the COMAH Strategic Forum, HSE will recommend benchmarks for effective process safety leaders but Dr Logan stressed that the regulator cannot by itself make safety management more effective – this is down to individual operators.
In addition, HSE’s other main priorities are asset integrity and cyber security, a topic that cropped up later on in the conference.
Dr Logan praised the work of the COMAH Strategic Forum, five years old this year, which is moving in “positive and constructive directions” and delivering good results. This is an excellent example of how government agencies and trade associations can work together to raise performance levels in process safety.
HSE has developed a revised strategy for its approach to safety in the chemicals sector, particularly as regards inspection and enforcement, Dr Logan reported. This will involve tighter profiling of establishments and targeting of inspections, with one-third of COMAH sites scheduled to be inspected during the 2017/18 year; most remaining sites will be covered during the 2018/19 year.
The focus of these inspections will be each site’s safety management system (SMS), which should give HSE a better understanding of the various sites and lead to what Dr Logan termed “interventions with impact”. It will also allow HSE to apply its resources most effectively, in particular through the idea of “earned recognition” that will divert intervention activity away from those sites that show themselves to be fully compliant with the relevant requirements.
One of the recommendations of the investigation into the Buncefield incident
was directed towards local authorities and related to land-use planning around highhazard sites. Dr Logan reported that this is very much on the agenda at HSE as a result not only of the expansion of industrial activity and urban sprawl encroaching on industrial areas, but also the general pressure on land, particularly for housebuilding.
Dr Logan had been asked by the organisers to speak about the potential impact of the UK’s decision to leave the EU on the storage industry. He had done his best, asking the Department for Exiting the EU for information; he showed the audience what they had told him but there was a sense that neither they nor he had much faith in the rather vague aims that were described.
There was one thing he was more sure of, though: all current health and safety legislation will remain in place after Brexit and there will be no changes in the short to medium term.
Another item in the Buncefield investigation had been the identification of the importance of effective secondary and tertiary containment in preventing the worst effects of oil and chemical spills on the environment. The COMAH competent authorities had placed great
emphasis on this, which had led to some large costs for operators of existing bulk liquids terminals, forced to replace or improve existing bunding around tanks.
However, there are ways around the issue as Mike Nicholas, senior adviser at the EA, reported in his presentation entitled: ‘When bunding costs too much’. As Dr Logan had, Nicholas began by putting things into context: between 2000 and 2011 there was at least one major accident to the environment (MATTE) every year, with four in 2010 alone. Since then, however, there has not been a single such event.
Nicholas reminded the audience that there has been a long-standing recommendation that storage tanks should be individually bunded – this was one of the outcomes of the investigation into the explosion and fire at the Regent Oil facility in Avonmouth in 1951, so it is hardly new. However, in practice terminals and depots have tended to install bunds around groups of tanks, with the bund of a sufficient size to contain 100 per cent of the largest tank within the bund.
In 2008, after the Buncefield investigation, the competent authorities’ Containment Policy »
was adjusted to require sufficient bunding to hold the contents of 110 per cent of the largest tanks or 25 per cent of all the tanks in the bund, whichever is the larger, with a caveat that, in some cases, bunds should have more capacity. Nicholas pointed out that, where bunds include more than four tanks, the 25 per cent figure would probably not be achieved with existing bunding, purely based on arithmetic.
That change to the Containment Policy in fact reflected established good practice in the industry and the 25 per cent figure was not plucked from the air – there are sound risk management principles behind it, as Nicholas explained. He also noted that France has a 50 per cent rule, though he suspected that there is not the same emphasis on tertiary containment there.
However, Nicholas said, those numbers are only there as a minimum. Good practice should involve a review of potential loss of containment scenarios and involve the calculation of the volume of bunding needed to contain all tank inventories, firewater and cooling water, rainwater and a foam freeboard.
The 2008 Containment Policy figures apply to all new establishments and also to existing establishments where significant changes to inventory or operations are being proposed. EA also required existing establishments to upgrade their secondary containment in line with the new policy as far as it is reasonably practicable to do so.
So, the question is, what is “reasonably practicable” and how is it measured? That question took the audience to the nub of Nicholas’ presentation: consideration of a case study in which the existing bund presented a level of risk falling in the category of ‘tolerable if as low as reasonably practicable’ (TifALARP). The concept of ‘ALARP’ involves weighing a risk against the trouble, time and money needed to control it.
Nicholas ran through the calculation, resulting in an expected frequency of a MATTE from a multi-tank fire involving bund overtopping at around 4x10-6 per year. The benefit of investing in bunding to achieve this predicted frequency was put at between £5m and £50m, based on property damage, harm to people and environmental recovery. »
“ALL CURRENT HEALTH AND SAFETY LEGISLATION WILL REMAIN IN PLACE AFTER BREXIT AND THERE WILL BE NO CHANGES IN THE SHORT TO MEDIUM TERM”
Given those figures, the justified spend would be in the range of £1,000 to £20,000.
What options does an operator have to enlarge the capacity of a bund? It can be extended to take up more space, but this may not be possible and, even when it is, can increase the risk posed by a pool fire. The height of the bund walls could be increased, but this is not always possible and brings with it additional risks and technical challenges. Overall, the cost of increasing the bund capacity in the case shown was put at anywhere between £100,000 and £2m – in other words, significantly more than the justified spend. EA would agree that this is grossly disproportionate, as well as technically challenging.
Being able to show figures like these would not necessarily get the operator off the hook altogether, Nicholas said. EA would look to see if the establishment risk had been adequately assessed; the operator itself might want to factor in wider costs such as business interruption and reputational harm.
Furthermore, if it is not financially practical to expand bund capacity, EA will seek assurance that the risks are no greater than those that would have been achieved through adoption of good practice. That means that the operator will need to consider other options to compensate for an under-capacity bund, such as intermediate bund walls, transfer systems to carry liquid to a remote secondary or tertiary containment, revised emergency plans or bund foam pourers. Procedures can also be adapted, such as reducing tank inventory or increasing the gap between the high level alarm and the high-high level alarm. Ultimately, the operator will need to demonstrate that all barriers are contributing to mitigation of the risk – it is all part of the safety culture.
Moving away from COMAH, TSA had taken note of its members’ increasing anxiety
over the potential for their operations to be disrupted by cybercrime and had asked the UK’s National Cyber Security Centre (NCSC) to put forward a speaker to bring delegates up to speed with the latest on the subject. Its project coordinator, known only as ‘Kevin’, arrived in Coventry with an arresting presentation.
NCSC was created in 2016 to be the national authority responsible for defending the UK from cyber attacks, deterring potential attackers and developing a national cybersecurity capability. Kevin noted the sharp increase in recent cyber attacks, although he said that most of these are just after personal data for financial gain. However, occasionally they can impact critical services, such as the recent problems encountered by the National Health Service (NHS). Although the attack was not specifically targeted at the NHS, it did have a disruptive effect.
But what if the perpetrator was actually trying to disrupt key services? This has not happened yet in the UK, although the Ukrainian energy grid has twice been the subject of an attack recently. For that reason, NCSC is concentrating on the risk posed to critical national infrastructure (CNI), which includes 13 sectors, the loss or compromising of which would lead to severe economic or social consequences or loss of life. Those
13 sectors include energy, transport, water, chemicals and civil nuclear industries. NCSC is working with industry and government agencies to assess the level of risk and to spread advice about cyber-security.
What NCSC has learned from recent incidents is that attackers generally exploit old vulnerabilities in networked systems and are increasingly displaying aggressive and confrontational attitudes. New cyber capabilities are also being exhibited, meaning companies need to ensure they are up to date with their defences.
NCSC has some basic advice on its website, www.ncsc.gov.uk, but is urging communities to share information, experiences and good practice. Kevin also pointed to the upcoming EU Directive on Security of Networks and Information Systems (NIS), which is due to be published in May 2018.
Other presentations at the TSA conference covered human factors in respect of COMAH, apprenticeships, and partnerships in port areas. HCB
All these topics are likely to be followed up next year when the TSA conference and exhibition comes round again; it is scheduled for 27 September 2018at the Ricoh Arena in Coventry. For more information, follow the TSA website, www.tankstorage.org.uk.
24 November. The aim is to bring together a range of players in the business, including chemical companies, traders, terminal operators, port authorities, bunker suppliers and shipbrokers, to discuss the options in light of rapidly changing trade flows, economic and industrial development in the region, and the need to take account of sustainability goals in energy usage and transport.
NORTHERN EUROPE HAS the ARA ports; North America has the Greater Houston area; south-east Asia has the ever-expanding Singapore; and China has Shanghai and the Yangtze ports. The Mediterranean, by contrast, lacks such a concentrated hub of port and terminal facilities for the handling of liquids in bulk and that lack affects the region’s efficiency and competitiveness.
There are many reasons for this. There is a lack of natural resources, for instance, which means there is no ‘natural’ focus of activity such as that enjoyed by Houston. There has been the political aspect, with the hydrocarbon sectors in most of Mediterranean Europe strongly controlled by their respective governments. Hinterland transport is weak, certainly compared to the obvious channel into northern Europe enjoyed by the big ports at the mouths of the Rhine. And the provision of bulk liquids storage capacity is also fragmented, with a lot of comparatively small operators involved, especially in the eastern Mediterranean region.
The Port of Tarragona in Spain’s Catalonia region is aiming to do something about this and has called a meeting to discuss what it calls the ‘regional hub challenge’ on 23 and
It is no coincidence that Tarragona has called the meeting, as it has some obvious advantages as a candidate to take on the role of a hub, at least for the western Mediterranean. Those advantages have been apparent for centuries – the Romans chose the port as their capital in Iberia – and include deepwater access, hinterland connections into central Spain, and a healthy local chemical industry.
Indeed, the Tarragona Port Authority has in recent years made more land available for
logistics service providers to the chemical industry and promoted the port under the ‘ChemMed’ banner. The local infrastructure is well set up to serve the sector, with the existing Repsol and Dow crackers linked by a common user pipeline to the port facilities and to downstream users. Vopak Terquimisa, Tepsa and Euroenergo all offer bulk liquids storage capacity at the port.
Tarragona may seem a natural choice for the establishment of a chemical hub for the Mediterranean, although ports elsewhere – particularly in the Marseille region of France and in northern Italy – may beg to differ. They will have an opportunity to make their case at the meeting, which will be held at the Tarragona Port Authority’s building and is free to attend.
The meeting will include presentations on the Port of Tarragona and its potential for growth as a hub for the chemical industry, on the changing role of the Mediterranean region in the global chemical market, and on the developing needs for bulk liquids storage. The event will also include a tour of the port’s chemical facilities. HCB
For more information and to sign up to attend the event, go to hubday2017.eventbrite.es.
STRATEGY • THE PORT OF TARRAGONA IS INVITING INTERESTED PARTIES TO HELP IT INVESTIGATE THE VIABILITY OF ESTABLISHING A MEDITERRANEAN HUB FOR BULK CHEMICAL TRADES
Malaysia-based MISC Group has reached an agreement to sell its 45 per cent equity interest in Centralised Terminals (CTSB) to its joint venture partner Dialog Group for RM193m ($46m). Through the deal, MISC is exiting its activities in the bulk liquids storage terminal sector to concentrate on its core businesses in energy shipping.
“ For MISC, this divestment will enable us to unlock the value of our investment in CTSB and take advantage of other opportunities within the energy and maritime industry,” says Yee Yang Chen, president/group CEO of MISC.
CTSB has an 80 per cent interest in the two Langsat product terminals alongside Trafiguraowned Puma Energy. Trafigura leases most of the combined 647,000 m3 capacity at the two terminals, situated in Pasir Gudang on the Malaysian site of the Johor Strait.
MISC formerly owned 50 per cent of VTTI but sold that interest to its partner Vitol in November 2015. www.misc.com.my www.dialogasia.com
Whitehelm Capital has acquired a 90 per cent stake in Vopak Terminal Eemshaven, a joint venture between Vopak and NIBC European Infrastructure Fund. Vopak will continue to manage and operate the terminal.
The 11-tank, 684,000-m3 facility is used for the strategic storage of gasoil, gasoline and other refined products and has a deepwater jetty to handle oceangoing ships. Whitehelm focuses on investing in infrastructure assets with stable long-term cash flows and, Vopak says, has a long history of investing in the tank storage sector. The Eemshaven terminal no longer fits with Vopak’s strategy, which concentrates on hub terminals and facilities linked to industrial clusters, as well as LNG opportunities. www.vopak.com www.whitehelmcapital.com
Magellan Midstream Partners and Valero Energy Partners are to expand their 50/50 joint venture petroleum product terminal currently under construction in Pasadena,
Texas. Work on the first 1m bbl (160,000 m3) of capacity and a Panamax-size jetty is currently in hand for planned startup in early 2019; another 4m bbl of tankage, a second berth capable of handling Aframax tankers and a three-bay truck rack will now be added, for completion in early 2020. Both phases are fully contracted with long-term customer commitments.
The partners say another 5m bbl of storage capacity could be built, depending on demand. The new Pasadena terminal will be linked by pipeline to Valero’s refineries in Houston and Texas city, Magellan’s Galena Park terminal and to the Colonial and Explorer pipelines.
“Demand for refined products from the Gulf Coast continues to grow and, together, we are well positioned to continue expanding our marine capabilities to meet this demand from both domestic and international markets,” says Michael Mears, Magellan’s president/CEO. His counterpart at Valero, Joe Gorder, adds: “This project provides another example of our commitment to growing our portfolio of logistics capabilities to support our long-term strategy of expanding and extending our supply chain.”
Magellan has also announced an expansion of storage capacity at three terminals in Texas to handle increased movements of gasoline, diesel and jet fuel along a new pipeline to be built between East Houston and Hearne. The 1m bbl of new refined products capacity is due onstream in early 2019. “Magellan is pleased to meet the industry’s need for pipeline capacity serving the Dallas market and other important demand centres along our refined products pipeline system with an attractive investment supported by long-term commitments from well-known, strong creditworthy customers,” Mears says. www.magellanlp.com www.valeroenergypartners.com
Valero Energy Corp and Plains All American Pipeline have dropped plans for Valero to buy two petroleum storage and distribution terminals located in Martinez and Richmond, California from a subsidiary of Plains. While the US Federal Trade Commission decided after an extensive investigation not to pursue any regulatory action with regard to the deal, the State of California filed suit to block it.
Although a motion for a temporary restraining order was denied, the two companies have decided it is not in their interests to undergo the uncertainty that a lengthy trial would entail. www.plainsallamerican.com www.valero.com
Greenergy Fuels Canada has agreed to acquire Canadian Operators Petroleum (Can-OP), a fuel marketer based in Thunder Bay, Ontario, and its wholly owned petroleum storage and supply facility, Wascan Terminals. Greenergy says it plans to upgrade and expand the terminal over the coming 18 months to make fuel supply more reliable and competitive in Thunder Bay and the surrounding region.
“O ur new presence in Northern Ontario continues our Canadian expansion and
establishes Greenergy in a region poised for economic growth and at the center of a key petroleum supply/trading intersection between western Canada, the US Midwest and southern Ontario,” says Mike Healey, director of Greenergy Fuels Canada.
“ The expertise and financial strength that Greenergy delivers will assist us greatly in the execution of our local business plan and we are excited to join the Greenergy team as it continues its fast-paced Canadian growth,” adds Bob MacMinn, general manager of Can-OP, who will remain in place along with the existing management team and will also take on additional responsibilities within Greenergy. www.greenergy.com
Gibson Energy is to expand its Hardisty terminal in Alberta, Canada with the addition of three new tanks totalling 1.1m bbl (175,000 m3). Two 300,000-bbl tanks are underpinned by a long-term contract with an oil sands customer and, along with one 500,000-bbl tank, are due to be placed in service in the third quarter of 2019.
“O ur Hardisty Terminal continues to demonstrate its commercial competitiveness and this contract affirms the ongoing demand for our strategic storage infrastructure in support of incremental oil sands brownfield development,” says Steve Spaulding, Gibsons’ president/CEO. “We will continue to focus on
the build-out of the undeveloped acreage at both our Hardisty and Edmonton terminals as our number one strategic priority.”
Af ter completion of the new tankage, total capacity at the Hardisty terminal will reach 10m bbl (1.5m m3).
www.gibsons.com
LBC Tank Terminals reports that the new upper jetty structure for its Rotterdam terminal has been delivered and installed, along with the hose tower and cranes. The arrangement will allow operators to manipulate 8-inch dock hoses using a small remote control unit.
The complete jetty is due to be ready for use this month, when the old jetty will be removed to improve access. Another jetty is to be added next year, doubling capacity and allowing efficient use of the dock space as the terminal’s capacity is expanded.
“LBC believes that it is of the utmost importance for our customers that the terminal is equipped with the best infrastructure possible,” the company states. “With the completion of this project our storage capacity will have tripled and not only will we have added seagoing and state-of-the-art barge jetties to our terminal, but these jetties will reduce waiting times at our quay to an absolute minimum such that we can safely serve our customers while maintaining optimum operational excellence standards.”
www.lbctt.com
8 Laurel Road
Hatton Vale, QLD 4341, Australia
T (+61 7) 5411 4415 www.amdg.com.au
Dangerous Goods – Initial
Air Acceptance
• December 5-7 – Brisbane
• December 5-7 – Melbourne
• December 12-14 – Sydney
Dangerous Goods – Air Transport
Recertification
• December 4 – Brisbane
• December 4 – Melbourne
• December 11 – Sydney
Dangerous Goods by Sea –
Function-Specific, Initial
• December 13-14 – Perth
• December 18-19 – Brisbane
Dangerous Goods by Sea –
Function-Specific, Recertification
• November 20 – Brisbane
• November 20 – Sydney
• December 5 – Sydney
• December 6 – Melbourne
• December 15 – Perth
• December 19 – Brisbane
Westfield Office Tower, Suite 403, Level 3, 152 Bunnerong Road Eastgardens, NSW 2036 Australia
T (+61 2) 9314 3055 www.afif.asn.au
Dangerous Goods Acceptance (Air)
• December 5-7 – Sydney
• December 12-14 – Melbourne
Dangerous Goods Re-certification (Air)
• November 22 – Brisbane
• November 27 – Melbourne
• December 4 – Sydney
• December 11 – Melbourne
Dangerous Goods Awareness (Air)
• December 1 – Melbourne
Dangerous Goods by Sea –
• November 29-30 – Melbourne
Dangerous Goods by Sea –Recertification
• November 20 – Sydney
• November 23 – Brisbane
• November 28 – Melbourne
• December 8 – Sydney
FREIGHT ASSOCIATION (BIFA)
Redfern House, Browells Lane
Feltham, Middlesex TW13 7EP, UK
T (+44 20) 8844 3625
www.bifa.org
Dangerous Goods by Air
• December 4-6 – Feltham
• January 8-10 – Feltham
• January 15-17 – Coventry
• January 17-19 – Altrincham
Dangerous Goods by Air –
Revalidation
• December 7-8 – Feltham
• January 11-12 – Feltham
• January 18-19 – Altrincham
• January 18-19 – Coventry
Dangerous Goods by Road
• January 22-24 – Feltham
Dangerous Goods by Road –Revalidation
• January 23-24 – Feltham
Dangerous Goods by Sea
• January 25-26 – Feltham
Carriage of Lithium Batteries –All Modes
• February 1-2 – Feltham
PO Box 17345
Edinburgh EH12 1DJ, UK
T (+44 131) 334 1929
www.cameon.com
Dangerous Goods Safety Adviser (DGSA)
• February 26-March 2 –Manchester
Dangerous Goods by Air
• January 15-17 – Manchester
Dangerous Goods by Air –Revalidation
• February 9 – Manchester
Dangerous Goods by Road and Sea
• February 6-8 – Manchester
Dangerous Goods by Road –Upgrade
• January 18 – Manchester
Dangerous Goods by Sea –Upgrade
• January 19 – Manchester
CARGO TRAINING
INTERNATIONAL PO Box 176
Shepperton TW17 8WP, UK
T (+44 1932) 769682
P O Box 580026 Houston, TX 77258-0026, USA
T (+1 281) 333 4672 www.cargotraining.com
Dangerous Goods by Air –ICAO (full course)
• November 27-29 – Houston
• December 4-6 – Dallas
• December 4-6 – Heathrow
• January 8-10 – Heathrow
• January 15-17 – Birmingham, UK
• January 17-19 – Manchester
Dangerous Goods by Road –ADR (full course)
• January 22-24 – Heathrow
Dangerous Goods by Sea (IMDG)
• November 30-Dec 1 – Houston
• December 7-8 – Dallas
• January 25-26 – Heathrow
IMDG – Sea – Revalidation
• December 8 – Dallas
DOT 49 CFR - Full Course
• November 30-Dec 1 – Houston
DOT 49 CFR – Recurrent
• December 1 – Houston
Lithium Batteries Multimodal
• February 1-2 – Heathrow
CHEMICAL HAZARDS
COMMUNICATION SOCIETY PO Box 899
Oxford OX1 9QG, UK
T (+44 333) 210 2427 www.chcs.org.uk
Classification for Transport
• January 31 – Manchester
Transport Labelling and Documentation
• February 1 – Manchester
Risk Characterisation and the Chemical Safety Report
• December 5 – London
The Extended SDS
• December 6 – London
An Overview of the Biocidal Products Regulation
• February 7 – Manchester
CLASS 7 LTD
9 Irk Vale Drive Chadderton Oldham OL1 2TW, UK
T (+44 161) 628 6677 www.class7.co.uk
RamMaster Level 1 –Foundation
• January 16 – Oldham
RamMaster Level 2 – Road Consignment and Transport
• January 17-18 – Oldham
RamMaster Level 2 – Rail Consignment & Transport
• February 1 – Oldham
RamMaster Level 2 – Air Consignment Upgrade
• January 30 – Oldham
RamMaster Level 2 – Sea Consignment Upgrade
• January 31 – Oldham
COGENT
5 Mandarin Court
Warrington WA1 1GG, UK.
T (+44 1925) 515 200 www.cogentskills.com
• December 7-8 – Leeds
Process Safety for Operations
• November 29-Dec 3 – Holmes Chapel
DANGO TRAINING SERVICES
169 Affric Road
Glenrothes KY7 6XA, UK
T (+44 1592) 748234
www.dangerousgoodstrainingdts. co.uk
Dangerous Goods by Air
• November 20-22 – Aberdeen
• December 4-6 – Aberdeen
• December 11-13 – Aberdeen
Dangerous Goods by Sea
• November 23-24 – Aberdeen
• December 7-8 – Aberdeen
• December 14-15 – Aberdeen
PO Box 140
Botany, NSW 1455, Australia
T (+61 8) 8234 1622 http://dgair.com.au
DG by Air – Initial
• November 27-29 – Adelaide
• December 4-6 – Perth
• December 4-6 –Sydney
• December 11-13 – Melbourne
DG by Sea – Initial
• November 30-Dec 1 – Adelaide
• December 7-8 – Perth
• December 7-8 –Sydney
• December 14-15 – Melbourne
61 New Cavendish Street London W1G 7AR, UK
T (+44 20) 7467 7100 www.energyinst.org
Hazardous Area Classification
• November 28-30 – London
Introduction to Process Safety Management
• December 5-7 – London
Human Factors Foundation
• November 20-24 – London
Natural Gas and LNG Technologies and Supply Chains
• December 11-14 – London
ASSOCIATION
Hermes House, St John’s Road
Tunbridge Wells TN4 9UZ, UK
T (+44 1892) 526171
www.fta.co.uk
ADR – Refresher
• December 5-7 – Leeds
• January 9-11 – Leamington Spa
ICC COMPLIANCE CENTER
2150 Liberty Drive
Niagara Falls, NY 14304, USA
T (+1 888) 442 9628
88 Lindsay Avenue
Dorval, QC H9P 2T8, Canada
T (+1 888) 977 4834
www.thecompliancecenter.com
Shipping Dangerous Goods by Ground in Canada: Initial
• January 8-9 – Toronto
Shipping Dangerous Goods by Ground in Canada: Refresher
• December 19 – Toronto
• January 12 – Toronto
Shipping Dangerous Goods by Ground in Canada: Initial/Refresher
• December 12 – Vancouver
• January 16 – Vancouver
Shipping Dangerous Goods by Air: Initial
• November 28-30 – Montreal
• December 12-14 – Toronto
• January 9-11 – Montreal
• January 16-18 – Toronto
Shipping Dangerous Goods by Air: Refresher
• December 20 – Toronto
• January 9-11 – Montreal
• January 16-18 – Toronto
Shipping Hazardous Materials by Ground and Air: Initial
• January 16-17 – Niagara Falls
PETER EAST ASSOCIATES
504 Centennial Park Centennial Avenue
Elstree, Herts WD6 3FG, UK
T (+44 20) 8953 6721
www.petereast.com
Carriage of Dangerous Goods by Air – Certification
• November 20-22 – Luton
• November 27-29 – Southampton
• December 4-6 – Heathrow
• December 11-13 – Stansted
• January 8-10 – Heathrow
• January 15-17 – East Midlands
• January 22-24 – Manchester
• January 29-31 – Elstree
Carriage of Dangerous Goods by Air – Revalidation
• November 23-24 – Luton
• November 30-Dec 1 –Southampton
• December 7-8 – Heathrow
• December 14-15 – Stansted
• January 11 – Heathrow
• January 18-19 – East Midlands
• January 25-26 – Manchester
Carriage of Dangerous Goods by Road & Sea
• November 20-22 – Heathrow
• December 4-6 – Stansted
Carriage of Lithium Batteries by Air, Road & Sea
• December 11-12 – Elstree
• January 15-16 – Heathrow
Carriage of Excepted & Limited Quantities by Air, Road and Sea
• January 24-26 – Elstree
88 Joo Chiat Road #02-01 Singapore 427382 T (+65) 6741 9927 www.petroedgeasia.net
Integrated Methods for Offshore LNG Transfer
• November 22-23 – Singapore
LNG Terminal Operations
• December 11-13 –Kuala Lumpur
THE REACH CENTRE
Lancaster Environment Centre, Lancaster University Lancaster, Lancs LA1 4YQ, UK. T (+44 1524) 510278 www.thereachcentre.com
Prepare for 2018 REACH Registration
• December 6 – Lancaster
Managing REACH for Downstream Users
• December 5 – Lancaster
REACH – IUCLID
• December 7 – Lancaster
3-Day Hazard Communication Package
• January 16-18 – Lancaster Classification, Labelling and Packaging (CLP) Workshop
• January 16 – Lancaster Safety Data Sheets Workshop
• January 17 – Lancaster
Extended SDS - Understanding & Implementing Exposure Scenarios
• January 18 – Lancaster
6 Venture Court
Altham Industrial Estate
Altham, Lancs BB5 5TU, UK T (+44 1282) 687090 www.specialisttraining.co.uk
ADR Initial – Packages & Tanks
• November 27-Dec 1 – Accrington
• January 8-12 – Accrington
Carriage of Dangerous Goods by Air
• January 31-Feb 2 – Accrington
The Legion, Wigshaw Lane
Culcheth, Warrington WA3 4LY, UK T (+44 151) 488 0961
www.transchemtraining.com
ADR Initial
• November 20-24 – Warrington
• December 11-15 – Wakefield
• December 18-22 – Warrington
ADR Refresher
• December 12-14 – Warrington
WARSASH MARITIME
ACADEMY
Newtown Road, Warsash Southampton SO31 9ZL, UK T (+44 1489) 556216 www.warsashacademy.co.uk
Basic Oil and Chemical Tanker Cargo Operations
• December 4-5 – Southampton
• January 8-9 – Southampton
Advanced Oil Tanker Cargo Operations
• November 20-24 – Southampton
• December 11-15 – Southampton
• January 15-19 – Southampton
Basic Liquefied Gas Tanker Cargo Operations
• December 4-5 – Southampton
• January 8-9 – Southampton
Advanced Liquefied Gas Tanker Cargo Operations
• November 27-Dec 1 –Southampton
• January 22-26 – Southampton
Crude Oil Washing
• February 1 – Southampton Jetty Operations (Petrochemicals)
• January 29-30 – Southampton
Last month I talked about teams and feedback. The last two weeks I have been working in south-east Africa teaching and training petroleum people how to build a safety culture. Much has been written on HSE but, as far as I am aware, cybernetics has not yet been applied as a useful tool for governance.
Risk prevention and risk management are methods to control risks, but often do not consider the cybernetical law of requisite variety or philosophical solutions such as a science of ethics. To prevent and control HSE risks, we have to first know ourselves. Who am I? How do I react? How do I communicate? These so-called ‘Human Factors’ are, in my opinion, insufficiently explored and understood. In Africa we spoke about narcissism, arrogance, recklessness and other human character traits and concluded that they are always dependent on the interaction with others. On an island alone, people would not have much use for such traits.
Let me first explain the Law of Requisite Variety, which was proposed by Ross Ashby in 1956. ‘A situation can only be controlled if the variety of the controller matches the variety of the situation to be controlled.’ It is impossible to prepare for every variable so most variety is absorbed through relationships with other systems. Only Variety can absorb Variety.
Every organisation generates tremendous variety and tries to control it in its own way through HSEQ rules, checklists or regulations. Human variety, environmental variety, social variety, regulatory variety change all the time and therefore cannot be controlled. A company is a living
system and needs to maintain and develop sufficient internal variety to be able to absorb (counter-balance) ‘outside’ variety. This means training people to have the combined knowledge, experience, expertise, will and influence to do so.
For HSE or risk management, only enough variety in your system can absorb, or control HSE risks originating from the outside and also the internal variety.
What an organisation can do is to insist that ‘all’ information is centralised and made available. Often management does not or cannot hear (or listen to) what is going on, because the company is managed in a top-down manner. But, as the title of this column shows, information is anything that reduces uncertainty and, next to energy and matter, it is the way our universe operates.
The solution therefore to maximise risk prevention or risk management is to make sure that all the parts of the system (the organisation) communicate constantly and are able to adapt to new situations. When outside variety changes, the organisation directly adjusts by learning and adding more counterbalancing knowledge, skills and wisdom.
This is a continuous process and can be managed by cybernetical steering of positive and negative feedback. It becomes a natural tool, not to manage or control HSE risks, but to prevent them,
This is the second in a new series of articles by Arend van Campen, founder of TankTerminalTraining. More information on the company’s activities can be found at www.tankterminaltraining.com.
NOVEMBER 11-14, RIO DE JANEIRO
37th annual Latin American petrochemical conference www.apla.com.ar/en/
NOVEMBER 13-14, PHILADELPHIA
Supply chain meeting for senior-level executives in North America http://logichemus.wbresearch.com/
NOVEMBER 13-16, ABU DHABI
33rd annual Abu Dhabi International Petroleum Exhibition & Conference www.adipec.com
NOVEMBER 13-16, MARCO ISLAND, FL
46th Annual Meeting of the National Association of Chemical Distributors www.nacd.com/meetings/am/2017annual-meeting/
NOVEMBER 14-15, SINGAPORE Conference on the prospects for LPG, ethane, NGLs and other alternative fuels in Asia www.argusmedia.com/events/argus-events/ asia/lpg-and-feedstocks-2017/home/
NOVEMBER 14-15, HOUSTON Conference on optimising polymer and liquid petrochemical supply chains www.petchem-update.com/petrochemicalsupplychain/
Annual meeting of the European Chemical Transport Association http://ecta.com/event-2408645
NOVEMBER 23-24, ST PETERSBURG
11th oil terminal congress and exhibition www.oilterminal.org/en
NOVEMBER 27-29, DUBAI
12th annual meeting of the Gulf Petrochemicals & Chemicals Association www.gpcaforum.net
NOVEMBER 28-30, AMSTERDAM
Annual trade show and conference for the container, transport and logistics industry www.intermodal-events.com
NOVEMBER 28-DECEMBER 1, LISBON
18th annual conference and awards dinner http://world.cwclng.com/
Design, Construction and Operation of LNG/LPG Vessels
NOVEMBER 29-30, GLASGOW
RINA conference on new gas shipping concepts www.rina.org.uk/LNG_LPG2017.html
NOVEMBER 29-30, HAMBURG
Fourth annual conference and trade show focused on the German tank terminal industry www.tankstoragegermany.com
DECEMBER 4-6, LONDON
Eighth annual conference on developments in the LPG sector www.argusmedia.com/events/argus-events/ europe/argus-euro-lpg/home/
DECEMBER 6, AMSTERDAM
Forum of roundtable discussions for executives from terminal operators, investors and users https://eventgrid.com/Events/34539/tankstorage-roundtable-2017
StocExpo China
DECEMBER 13-14, SHANGHAI
Inaugural tank storage expo and conference
JANUARY 8-9, HOUSTON
156th annual conference on gas storage issues in North America www.platts.com/events/americas/ gas-storage/index
JANUARY 16-18, HOUSTON
Conference on regional and global LPG market developments www.argusmedia.com/events/argus-events/ americas/americas-lpg-summit/home/
COHMED
JANUARY 29-FEBRUARY 2, GARDEN GROVE, CA
Annual conference of the Cooperative Hazardous Materials Enforcement Development (COHMED) programme http://cvsa.org/eventpage/events/cohmedconference/ International Petroleum Week (IP Week)
FEBRUARY 20-22, LONDON
Annual week of meetings, lunches, conferences and seminars in London www.ipweek.co.uk/_nocache
FEBRUARY 28-MARCH 1, RUNCORN Conference and exhibition on hazardous area operations www.hazardexonthenet.net/event. aspx?EventID=4724
MARCH 13-15, DALLAS
12th global conference on air cargo www.iata.org/events/wcs/pages/index.aspx
Date Location Vehicle Type Substance Details Source
23/7/17 Ile-Ife, road tanker diesel 14 people were burned to death when the bus they were travelling in hit a road tanker making a U-turn Premium Osun, Nigeria outside a fuel station; only two passengers survived; tank driver absconded; witnesses said response was slow Times
26/7/17 Harold, rail tank cars carbon US 90 was shut in both directions for three hours due to leak of carbon dioxide from seven CSX rail cars; WEAR Florida, US dioxide leak described as “excessive” but no evacuations necessary; warm weather though to have caused off-gassing
28/7/17 Felele, road tanker gasoline Road tanker was in head-on collision with bus on Lokoja-Abuja road; ten passengers died in crash, another Xinhua Kogi, Nigeria three died later in hospital; no indication that tanker caught fire in accident
1/8/17 Kanpur road tanker LPG Road tanker with 18 tonnes LPG overturned on NH 25 near Mati; crash damaged valve, leading to gas leak; Times of UP, India power supply shut off and locals were warned against using stoves while crew replaced valve India
2/8/17 Mbiama, road tanker gasoline Tanker driver lost control of vehicle, which overturned shortly after making delivery; tanker caught fire; Xinhua Bayelsa, Nigeria blaze spread to other vehicles; six people reported dead
2/8/17 Hyndman, freight train LPG, 32 cars of CSX train derailed in small town; one car with LPG, one with sulphur caught fire; town evacuated; Reuters Pennsylvania, US sulphur two buildings damaged; NTSB, FRA investigators on site; no injuries reported
4/8/17 Loganholme, road tanker hydrochloric Fire broke out in cab of Coogee Chemicals road tanker on M1 Pacific Motorway; driver managed to pull over SMH Qld, Australia acid at a safe location before fire spread to tanker; road closed, 1-km exclusion zone imposed
6/8/17 Raigad, road tanker gasoline Road tanker overturned on old Mumbai-Pune road, causing leak of gasoline cargo and fire; five people Times of Maharashtra, India injured in blaze; no indication of cause of accident India
8/8/17 nr Rancheria Lodge, road tanker fuel Tank truck crashed on Alaska Highway some 125 km west of Watson Lake, cause unknown; some 20,000 CBC Yukon, Canada litres unspecified fuel spilled, closing road for most of a day; driver injured in crash
8/8/17 Rowan county, road tanker ethanol Hot Z Transport tank truck overturned on Bringle Ferry Road at Davidson county line, spilling 8,000 gal Charlotte N Carolina, US (30 m3) ethanol; area closed for extended period of time for cleanup; driver charged Observer
12/8/17 Senawang, road tanker acid Road tanker with 25,000 litres “acid chemicals” collided with car at toll plaza on PLUS Highway; tanker The Seremban, Malaysia driver killed, two in car injured; acid spill caused road to be closed in both directions Star (KL)
12/8/17 Rayong province, road tanker oil Tyre blowout caused oil tanker to crash into motorcycle and run off road, overturning; tanker said to have Xinhua Thailand exploded; driver, cleaner killed before they could escape; no detail on oil cargo; accident under investigation
15/8/17 Walsleben, road tanker nitric acid Road tanker with 12 tonnes acid suffered leak on A24 Berlin-Hamburg highway, closing road; nearby buildings Focus BB, Germany evacuated; rest of cargo was transferred to second vehicle; not clear what caused damage to tank
16/8/17 nr Timber Cove, road tanker diesel Tank truck rolled over on Highway 1, spilling some 800 gal (3,000 litres) diesel and blocking road; Press California, US driver unhurt; remaining load had to be transferred before tanker could be righted; cause unknown Democrat
21/8/17 Samalkot, road tankers hydrogen Road tanker loaded with hydrogen exploded at oil ‘factory’; blast ignited two more tankers; fire spread DNA AP, India through facility; explosions spread panic among nearby residents; no injuries as plant was unoccupied
25/8/17 Indianapolis, freight trains lube oil CSX freight train collided with several cars parked on mainline; not clear what they were doing there; one Fox59 Indiana, US car with lube oil, described by CSX as non-hazardous, was ruptured, spilling oil; incident under investigation
27/8/17 Solwezi, truck sulphuric Driver lost control of truck (possibly tanker), reportedly due to speeding; sulphuric acid cargo spilled to News Zambia acid nearby river, causing extensive fish kill; lime applied to neutralise acid; locals warned against eating fish Ghana
29/8/17 Chakwal, road tanker chemical Road tanker with unspecified chemical rammed into shops on Talagang-Mianwali road, likely due to speeding, Dawn Punjab, Pakistan then caught fire; driver and helper died, street vendor injured
31/8/17 Everson, road tanker asphalt Double tanker with hot asphalt rolled over while taking turn, spilling some 5,000 gal (19 m3) asphalt to Lynden Washington, US nearby yards; road closed but no evacuations necessary Tribune
2/9/17 Kasoa, road tanker fuel Road tanker with unspecified fuel caught fire at toll booth on Weija-Kasoa road; authorities said detached Joy News Central, Ghana shaft was dragging on road, causing sparks that ignited leak from tanker; tanker burned out; driver unhurt
2/9/17 Honomu, road tanker propane Hawaii Gas tank truck with 1,750 gal (6.6 m3) propane was in head-on collision with SUV on Highway 19; Star Hawaii, US tanker overturned; leaking gas ignited, burning for two days; one killed, four injured in crash Advertiser
7/9/17 Ubeji, road tanker oil Road tanker, fully laden with unspecified oil, overturned near filling station, refinery, caught fire; responders Breaking Delta, Nigeria were slow to attend, then ran out of water; several houses, shops destroyed in blaze but no injuries Times
21/7/17 Coswig, warehouse chemicals
Source
Major fire broke out in large warehouses at Herlac lacquer plant; various chemicals on site in drums, other Sächsische Sachsen, Germany containers involved, causing difficulty for firefighters; air quality monitored but no risk to public, officials said Zeitung
22/7/17 Umm al Thoib, chemical
Fire broke out in petrochemical factory in industrial area, requiring assistance from fire brigades from other Gulf Umm al Quwain, UAE plant emirates; few details on nature of fire or identity of facility; no injuries reported News
22/7/17 Conroe, factory explosives? Fire broke out in building belonging to unidentified company that makes chemical charges for nail guns; click2 Texas, US four people working outside plant were unhurt; one car damaged; one nearby resident asked to shelter in place houston
23/7/17 Bajaura, bitumen bitumen Fire destroyed 35 drums of bitumen, 9,000 litres diesel, storage tank and other equipment at private The HP, India plant construction company; fire crews prevented blaze spreading further; cause of fire could not be determined Tribune
26/7/17 Changji Hui, chemical gas One worker killed, 31 injured by leak of high-temperature gas during pipeline maintenance at Xinjiang Xinhua Xinjiang, China plant Yihua chemical plant; incident under investigation
26/7/17 Sakaide, fireworks fireworks Two workers were badly injured by explosion at Hirao Hanabiten fireworks factory; pictures showed The Kagawa, Japan factory flattened buildings, other damage; cause of blast not immediately known Mainichi
29/7/17 Atmore, chemical sulphur Fire broke out in store of sulphur in warehouse at Tiger Sul facility; no employees on site at the time; nearby north Florida, US plant factory evacuated, local residents advised to shelter in place; fire was allowed to burn out escambia
31/7/17 Silver Peak, mine lithium Some 100 barrels of lithium stored at Rockwood mine, the only lithium mine in the US, caught fire, burning Review Nevada, US for eight hours; residents of small town evacuated from noxious smoke; safety inspectors investigating incident Journal
2/8/17 Primorskoye, arsenal munitions Around 60 people, including 35 tourists, were injured by series of explosions in munitions depot in breakaway RFE Abkhazia, Georgia province; other reports said no injuries but Russian TV showed large cloud above mountains
4/8/17 Visakhapatnam, oil refinery crude oil Fire broke out on roof of crude oil tank at HPCL refinery but was quickly extinguished; operator blamed The AP, India lightning strike, though unions cited over-dependence on contract labour, saying heavy rain extinguished fire Hindu
7/8/17 Sydney, chemical aerosols One worker badly injured by explosion at chemical waste disposal plant; fire spread to neighbouring plant; DeathRatNSW, Australia disposal plant several small explosions as blaze spread to stocks of aerosol cans; concern over gas cylinders on site tleSports
16/8/17 Kingston, oil refinery crude oil Fire broke out in tank with crude oil at Petrojam refinery; fuel supplies to the country not affected; RJR Jamaica no injuries reported; Energy Ministry to undertake investigation News
16/8/17 Benton, gas processing gas Two workers were badly hurt by explosion at Empresa Energy plant that makes refrigerant gases from LPG ArkLaTex Louisiana, US facility and methane; reports said one worker knocked a valve; leaking gas found ignition source; police investigating
19/8/17 nr Rawlins, mine uranium UR Energy’s Lost Creek uranium mine reported spill of 188,000 gal (710 m3) injection fluid; second, smaller Star Wyoming, US spill three weeks later led to UR closing operations; broken line blamed; spilt fluid not highly radioactive Tribune
19/8/17 Harrison county, sewage chlorine Stolen car crashed into sewage treatment plant, damaging tank and releasing chlorine; two people in car died WLOX Mississippi, US treatment plant in crash; several responders treated on scene; road closed, residents warned to close up their homes
22/8/17 Oklahoma City, tank battery crude oil Fire broke out on two storage tanks in south-west OKC; one tank was consumed in fire; flames began to KOCO5 Oklahoma, US die down after two hours; no injuries or threat to the public
23/8/17 Salem, gas bottling acetylene One worker injured at Western International plant when fire in acetylene tank caused explosion, fire; plant’s Citizen’s Pennsylvania, US plant suppression system helped prevent fire spreading; local firefighters had already drilled for such an event Voice
26/8/17 Erbil, weapons dump armaments Explosion reported at weapons storage facility where Peshmerga fighters stored weapons captured from Isis Rudaw Kurdistan, Iraq militants; incident not thought to be terror-related; no injuries reported
27/8/17 Khizi, arsenal munitions At least six people injured by series of explosions in military weapons and ammunition storage facility; Azeri Azerbaijan unit and nearby villages evacuated in case of further blasts; official investigation to report back on cause Daily
28/8/17 Yerevan, chemical ethanol Explosion, massive fire at Nairit’s synthetic rubber plant; not clear if the blaze started in ethanol tanks but Panorama. Armenia plant four concrete reservoirs were on fire; blaze continued for a day; no injuries reported am
29/8/17 Baytown, oil refinery oil Heavy rains from Hurricane Harvey caused floating roof at ExxonMobil refinery to sink, releasing large Washington Texas, US amount of VOCs; strong smell reported over large parts of Houston; operator did not disclose tank’s contents Post
30/8/17 DeWitt county, tank batteries crude oil Burlington Resources reported two spills resulting from Hurricane Harvey: 385 bbl nr Westhoff and 316 bbl Fox Texas, US nr Hochheim, both caused by storage tanks being dislodged by heavy rain and winds News
31/8/17 Crosby, chemical peroxides Two explosions at Arkema plant as organic peroxides self-reacted after cooling systems were put out of action Fox Texas, US plant by Hurricane Harvey; operator later conducted controlled explosions in other containers with peroxides News
31/8/17 Galena Park, oil terminal gasoline Magellan Midstream Partners reported spill of nearly 11,000 bbl gasoline from its terminal during hurricane; ABC Texas, US some spilt product reached waterway alongside Houston Ship Channel; numerous other spills during storm
WHEN IT COMES to cargo safety during transport, it is easy for shippers and carriers to be focused only on their segment of the supply chain. This approach keeps vessel operators concerned about the safety of the cargo on their ships.
Today many cargo shipments around the world are being moved by more than one mode of transport. According to statistics by the Intermodal Association of North America (IANA), annually in the US alone, there are over 60 million intermodal drayage moves, 17 million intermodal loads moved by rail, and 63 million TEUs moved through ports.
With intermodal transport playing such a huge role in the supply chain, it is important
that hazardous materials/dangerous goods transportation safety be considered for each mode. It is important for everyone in the supply chain to connect the dots to prevent accidents, injuries, and costly shipment disruptions. This is one area where CHEMTREC® becomes an extremely valuable piece of the emergency response plan.
CHEMTREC is a 24-hour emergency response information provider thatacts as a hub that connects shippers, carriers, and first responders to each other to help mitigate hazardous materials incidents around the globe. CHEMTREC also provides immediate notification to shippers as an incident occurs so that they can take appropriate action, such as arranging disposal/clean-up or notifying the customer of a disruption in the supply chain.
THE ROLE FOR CHEMTREC CHEMTREC handles approximately 300 calls
per day. Many of the incidents that CHEMTREC’s Emergency Service Specialists (ESS) help to mitigate involve intermodal shipments that have recently left a vessel or are bound for a vessel. Most incidents such as spills, leaks and fires occur during the truck or rail portion of the supply chain. Many truck incidentsoccur over the road or during load and unload. Many rail incidents occur in the rail yard or during rail movement.
These two groups are very experienced in handling hazardous materials incidents. They usually have a plan in place to contain, clean up and report an incident. In many cases that emergency response plan includes calling CHEMTREC. Information such as product-specific safety data sheets (SDSs) can be obtained, the caller can immediately be connected to the manufacturer, first responders, carriers, and expert medical information with one phone call.
On a vessel, hazardous materials cargo safety should always be a priority. Vessel operators should have a similar emergency response plan to trucks and rail that involves a way to:
• Quickly obtain a product-specific SDS
• Speak to shippers or manufacturers directly • Notify the shipper of a disruption in the supply chain
• Immediately connect with medical information providers
In 2012, CHEMTREC was asked to assist with the MSC Flaminia incident. CHEMTREC was able to use its substantial resources to help first responders identify the shippers of some containers and to identify the corresponding SDS for some products. This was a major international incident, but CHEMTREC has resources that can also help during a minor spill, leak, fire, or accident.
With so much of the world now being connected, particular attention and care should be given to intermodal hazardous materials transport. Every shipper and carrier should have an emergency plan in place. However, when things go terribly wrong, it is important to have contingencies built into the emergency response plan to ensure that the shipper, carriers and first responders stay connected, all working together to help mitigate an incident. HCB chemtrec.com
A SEAFARER’S GREATEST fear is fire aboard ship. Miles away from land and any assistance that might be provided, fire threatens the very structure that keeps the seafarer afloat. It is no surprise, then, that the prevention and extinguishing of fires aboard ships has been a critical element in the International Maritime Organisation’s (IMO) work since its inception. The International Convention for Safety of Life at Sea (Solas) includes extensive instruction on the best ways to contain and extinguish fires.
Nevertheless, the fact is that fires continue to happen and, as containerships get ever bigger and the value of their cargo increases, insurers are also getting increasingly concerned about the financial threat they pose. Events such as those that befell the
containership Hanjin Pennsylvania in November 2002 and, more recently, MSC Flaminia have led to calls for a review of fire prevention and firefighting techniques.
IMO has responded with an amendment to Chapter II-2/10 of Solas, which applies to all ships constructed on or after 1 January 2016, but insurers say that the changes do not go far enough, particularly since they do not apply to existing ships.
The International Union of Marine Insurance (IUMI) has called on IMO, maritime administrations, classification societies and other stakeholders to engage in discussions as to how fire detection, protection and firefighting capabilities can be further improved aboard containerships. In particular, IUMI highlights work that ABS has already done on the
subject and a proposal from the German Insurance Association (GDV), which could form the basis for improvements.
In remote locations and on the open sea, it can often be hours or even days after a fire has broken out before external assistance arrives. As a rule, only seagoing tugs carry the necessary equipment for effective firefighting. Until they arrive, the crew has to rely on its own resources and a fire can spread extensively.
Every ineffective attempt to put out a major fire increases the damage to the cargo, the vessel and the environment. Moreover, the crew is in great danger when a fire breaks out on board. Crew members face considerable risks when fighting such fires with the equipment currently required by law; IUMI recalls that three crew members died aboard MSC Flaminia during attempts to put out the fire.
IUMI also notes that the increasing size of containerships – up to the latest 22,000-TEU monsters now under construction – means that firefighting arrangements are falling even further behind. It also points to what it believes is a “considerable amount” of mis-declaration or non-declaration of dangerous goods in containers, which can lead to improper handling of the containers as well as an inappropriate strategy should fire break out.
The fundamental problem, as IUMI sees it, is that the legal requirements in Solas were drawn up originally to apply to fires aboard general cargo vessels and have not kept pace with the development of unitised cargo. On general cargo vessels, if a fire starts in a hold, the air space immediately fills with smoke, making the fire easy to detect. Once a fire is detected, the hold in question can be sealed off and CO2 applied to quench the fire.
That scenario is completely different on a modern containership.
IUMI says that the fire detection systems specified in Solas “do not enable effective detection of incipient fires in a container”. These systems drawn air from the hold at a point just below the deck; for a fire to be detected, therefore, smoke must have filled the hold up to this level. If fire breaks out in a
container, it will have already taken hold – and probably destroyed the container’s contents and damaged the container itself – well before the smoke reaches the fire detection system.
The effectiveness of filling the hold with CO2 is also doubtful: it cannot act directly on any burning cargo inside a container; and it will be ineffective with any fire that is generating its own oxygen, as may be the case with chemicals or other dangerous goods.
If the fire is not contained in the hold and spreads to the deck, it can have a much more catastrophic impact on a containership as there are no natural fire compartments. Furthermore, due to a lack of suitable equipment, it is practically impossible to cool the deck by using water. In addition, there is no requirement for fire detection systems on the deck.
In its paper, GDV says that, for practical purposes, firefighting operations on containerships are limited to allowing the fire to burn out in a controlled manner so
that it cannot spread further and can be contained until such time as help arrives.
“This approach is still correct,” GDV says, “but in view of the rapid pace of development towards ever larger ships, new technical solutions are also required.”
It is impractical, GDV says, for each container or even each container stack to be monitored separately and fitted with its own fire detection and firefighting system. Rather, it is necessary to separate the ship into fire compartments, using the existing division of the ship below deck. For instance, if a fire breaks out below deck, the aim would be to maintain the stability of the vessel and to prevent the fire from spreading to the deck or to adjacent holds.
On deck, the lashing structures used to secure containers can be used and extended to maintain a separation of fire compartments; additional sprinklers installed on the lashing structures can prevent or slow the spread of the fire to other fire compartments.
Furthermore, GDV says, CO2 alone is insufficient: a water-based firefighting system also needs to be installed that will allow the vessel’s structure (including hold walls, bulkheads, decks, hatch covers and so on) to be cooled. “The water supply for a fire compartment must be designed in such a way that their firefighting systems, including
the monitors on the boundary structures, are able to cool the structural elements of the fire compartment boundary sufficiently on both sides so that their stability is never in danger and the flames and heat radiation from a fire are prevented from spreading to or penetrating other fire compartments,” it says.
In addition, in order that a fire is detected as soon as possible, more sophisticated detection methods need to be applied. These could include infrared cameras, thermal sensors or similar systems below deck and infrared cameras mounted on the fire compartment boundary structures above deck.
Finally, GDV proposes, all superstructures should be protected fore and aft against the effects of flame and heat by effective water curtains, providing a refuge for the crew and protection for vital control systems. These water curtains should also extend to lifeboats and other lifesaving equipment.
“Implementation of all described measures would not only protect the lives and health of the crew members, the environment but also the vessels, their cargo and the environment. In the event of a fire, separation into fire compartments plus additional firefighting systems would enable the crew to more effectively attack and suppress fires and thus prevent them from spreading putting the hull, cargo and crew at risk,” GDV concludes. HCB
THE CARGO INCIDENT Notification System (CINS) has won the 2017 BIC Award, presented annually by the Bureau International des Containers (BIC) to recognise an individual or organisation for notable contributions to safety, security, standardisation or sustainability in containerised transport.
The BIC Award was presented to HapagLloyd’s Ken Rohlmann, vice-chairman of CINS, and Jean-Christophe Triat of the Mediterranean Shipping Company (MSC) during the annual meeting of the subcommittee on Carriage of Cargoes and Containers (CCC) at the International
Maritime Organisation (IMO) headquarters in London. It was presented by Douglas Owen, BIC secretary-general, and Giordano Bruno Guerrini, chairman of the board of BIC.
As a non-profit organisation dedicated to safety within the shipping and container industry, BIC welcomes and encourages industry-led initiatives such as CINS,” said Owen. “We have been particularly impressed with how CINS has brought the industry together to help improve safety throughout the supply chain. We are delighted to recognise this great achievement with a BIC Award.”
A ROLE IN SAFETY CINS was established in 2011 by five of the world’s biggest container lines – CMA-CGM, Evergreen, Hapag-Lloyd, Maersk Line and MSC – with the objective of highlighting the
risks posed by certain cargoes and packing failures. By collecting this data within the CINS online database, trends and incidents requiring immediate action can be more easily identified than ever before.
Maersk Line’s Uffe Ernst-Frederiksen, chairman of CINS, said: “The key driver for CINS remains ensuring safety of seafarers and all involved in the maritime supply chain across the globe, as well as protecting the environment and assets. In today’s cargo booking environment it remains key to maintain a level of vigilance where certain cargoes with potential self-reactive properties are involved.”
Rohlmann added: “CINS is a unique group of international experts, acting independently from any commercial interests, purely driven by the aim to enhance the overall safety for our colleagues, both on board our vessels and within the entire transport chain.”
By analysing trends from its database, CINS can help improve safety levels in the maritime transport chain. For example, once areas of concern are identified, information can be passed to the relevant authorities and generate guidance, advice or amendments to the International Maritime Dangerous Goods (IMDG) Code.
“CINS’s strategic efforts include producing guidelines, such as for the transport of calcium hypochlorite, steel coils and for the use of non-operating reefers,” says ErnstFrederiksen. “Currently, CINS expert work groups are developing best practice guidelines on further specific cargoes in containers, including the carriage of charcoal, lithium batteries, metal scrap, hides and skins, cocoa butter and radioactive cargo.”
By collating information concerning all incidents resulting in injury or loss of life, loss or damage of assets, or environmental concerns, CINS also supports the industry by ensuring that shipping lines have facts to rely on in the event of regulatory intervention.
There are now 14 shipping line members of CINS, representing two-thirds of the world’s containerised capacity, each of which is able to access information within the CINS database. HCB www.cinsnet.com www.bic-code.org
THE US CHEMICAL Safety Board (CSB) continues to investigate incidents in the petrochemical and oil processing sectors, despite threats to its funding, although its recommendations have a tendency to repetition. Sadly, that reflects the fact that too many operators – even the largest corporations – continue to make the same mistakes over and over again.
CSB’s latest report looks into an isobutene release and fire at the ExxonMobil refinery in Baton Rouge, Louisiana on 22 November 2016. Four contract workers were seriously injured in the fire. At the time, they were engaged in maintenance work on the refinery’s sulphuric acid alkylation unit.
The incident happened when one of the workers was removing an inoperable gearbox on a plug valve; the valve came apart, releasing isobutane that formed a vapour cloud and, very quickly, found an ignition source.
The four workers in attendance were unable to get out of the vapour cloud quickly enough and were caught in the fire.
ExxonMobil estimated that some 2,000 lb (900 kg) isobutane was released and that a nearby welding machine was the likely ignition source.
The fire was extinguished about 25 minutes after the initial ignition, once emergency responders had isolated the release.
CSB’s investigation into the incident found that there were long-standing reliability issues with the gearboxes used to operate plug valves in the alkylation unit. Furthermore, 15 of the roughly 500 plug valves with manually operated gearboxes in the unit were of an older design that had a different attachment to the others, raising the possibility that the gearbox could be removed incorrectly. The contract workers appear to have been unaware of this distinction as the refinery management failed to provide maintenance workers with a written procedure or training.
Indeed, CSB notes a list of deficiencies, including:
• A failure to identify or address reliability issues with the older model plug valve design
• A lack of human factor evaluation to determine the potential hazards with operating and maintaining these valves
• A lack of written procedures to detail the steps needed to remove different models of gearboxes
• A lack of training on the safe removal of the various plug valve gearbox models in the unit and their different hazards, and
An organisational culture that accepted the work despite the lack of detailed procedures or training.
The Baton Rouge refinery provided CSB with numerous training records, although the Board’s report states that none of them included instruction on the removal of an inoperable gearbox from a plug valve. CSB also notes that Flowserve, the manufacturer of the plug valves installed at the unit, warns in its literature that users should not remove the pressure-retaining top-cap bolts but that this warning was not communicated to workers at the plant.
In its interviews with workers at the site, CSB found that the organisational culture of the refinery acknowledged that it was “accepted practice” to remove malfunctioning gearboxes from plug vales and manually rotate the valve stem with a pipe wrench. One worker involved in the incident said that similar work had been conducted in the past without adverse consequences and described this as a “learned habit” after watching more experienced operators do the same.
CBS chair, Vanessa Allen Sutherland, says: “Our investigation found that these accepted practices were conducted without appropriate safety hazard analysis, needlessly injuring these workers. It is important to remember that good safety practices are good maintenance practices and good business practices.”
CSB’s report notes similarities between the Baton Rouge incident and a number of others that have been the subjects of recent investigations, including those at the Williams Olefin plant in Geismar, Louisiana in June 2013; the BP refinery in Texas City in March 2005; Giant Industries’ Ciniza refinery in Jamestown, New Mexico in April 2004; and, most significantly, ExxonMobil’s Torrance refinery in California in February 2015.
CSB’s report remarks that “Due to the frequency of process safety incidents at
the Torrance refinery, the CSB encouraged refinery management to consider the implementation of a process safety continual improvement program at the Torrance refinery to help prevent process safety incidents. The Baton Rouge refinery incident may suggest a similar need to strengthen the process safety focus of that refinery’s organisational culture.”
CSB identified three key lessons from the Baton Rouge incident of relevance to companies operating refineries and petrochemical manufacturing facilities.
1. Operators should evaluate the human factors associated with operational difficulties that exist in machinery and other equipment, especially when that equipment is part of a process covered by the Process Safety Management (PSM) standard. At the Baton Rouge refinery, for instance, the operator should have identified that 3 per cent of the plug valves in the alkylation unit used a gearbox attachment design that could result in inadvertent disassembly of pressure-retaining components and, had it done so, it should have applied the ‘hierarchy of controls’ to establish a mitigation strategy for those valves.
2. Operators should establish detailed and accurate procedures for workers performing potentially hazardous procedures; this is of particular important when there are different types of equipment or configurations that could cause confusion.
3. Operators should provide adequate training to ensure that all workers can perform all anticipated job tasks safely. This should include a focus on processes and equipment to improve hazard awareness and help prevent accidents.
A key safety lesson discussed in the CSB report is the hierarchy of controls. This is a method of evaluating safeguards to provide effective risk reduction. Within the hierarchy of controls, an engineering control, such as improved valve design, is more effective than a lower level administrative control, such as a sign warning workers that the gearbox support bracket connects to pressurecontaining components.
CSB’s report includes some safety guidance specific to manual gear-operated plug valves, although the learnings from the incident are of wider significance. However, since the incident, the Baton Rouge refinery has identified susceptible plug valves and either replaced them with the newer design or eliminated the support bracket and installed manual levers on the valve stem. ExxonMobil has communicated this to its other sites and has also made a presentation on the incident at an API conference. HCB
More detail on the CSB report into the Baton Rouge refinery fire can be found at www.csb.gov/csb-releases-final-report-into2016-refinery-fire-that-seriously-injured-fourworkers/. This includes a link to a detailed animation that shows how the incident happened.
questions of IATA, the most frequently heard of which is: why is the DGR updated every year, rather than every two years, as is the case with other regulations? Dave Brennan, who heads up IATA’s dangerous goods operations at its office next to the airport in Geneva, Switzerland, is clear that it is all about safety.
goods certainly raised the possibility that a catastrophic fire could take hold.
ANYONE INVOLVED IN shipping dangerous goods by air needs to be aware of and to know how to use the Dangerous Goods Regulations (DGR), published each year by the International Air Transport Association (IATA). The 59th edition is now available and will take effect promptly at 00.01 on 1 January 2018.
Those who are subject to the provisions of the DGR are justified in asking some
One good example of that is the new provisions for the segregation of lithium batteries away from other dangerous goods that present a flammability hazard; this stems from the investigation into the loss of the Asiana Airlines cargo aircraft off South Korea in July 2011. The aircraft was carrying 400 kg of lithium batteries alongside paint, resin solutions and other flammable liquids. While it was not possible to determine exactly where and how the fire started that led to the loss of the aircraft, it was felt likely that the proximity of the various dangerous
The International Civil Aviation Organisation (ICAO), whose Technical Instructions represent the legal basis for the regulation of dangerous goods in air transport, has agreed to adopt strict segregation rules but these will only take effect with the next edition of the Technical Instructions on 1 January 2019. IATA member airlines felt that this is a safety-critical measure that needs to be adopted as soon as possible, so it is making it a recommendation in the 59th edition of the DGR, becoming mandatory in the following edition to coincide with publication by ICAO.
So why not just issue an addendum to the DGR? Brennan says he knows from experience that addenda are often overlooked by personnel at the sharp end of the business, or fail to be disseminated to the people who need to know.
It is that experience that marks the IATA approach to dangerous goods regulation apart from ICAO’s. ICAO is the UN agency that oversees all aspects of the international air
AIR • A LOT GOES ON AT IATA’S GENEVA OFFICE TO GET THE DANGEROUS GOODS REGULATIONS REVISED AND PUBLISHED, BUT THAT IS JUST ONE SMALL ELEMENT OF ITS WORK
transport business; it represents UN member states so the delegates to the ICAO Dangerous Goods Panel are mostly civil servants.
By contrast, IATA represents its air operator members and its staff, particularly in the dangerous goods department, are drawn primarily from industry. They are a multinational team too, and have worked in different roles for a variety of operators, freight forwarders and other stakeholders. They have a much more practical understanding than their counterparts at ICAO, Brennan believes, and this is reflected in the difference between the DGR and the Technical Instructions.
The Technical Instructions are the legal basis for the regulations but they read like a legal text; the DGR, on the other hand, is written in such a way as to be readily understandable and usable by those who have to apply its provisions.
The annual update to the DGR also allows IATA to provide more recent information on operator variations, although others will inevitably appear during the course of the year. These variations are often frustrating for shippers, who may see them as random and unjustified obstacles to their goods. Paul Horner, IATA’s manager of dangerous goods standards, explains that they often result from a particular carrier’s experience with a certain cargo or mode of packaging, or more often these days from a risk assessment or safety management process.
IATA can, though – and often does –suggest to its members that the variations that they propose are unnecessary, badly worded or raise more problems than they solve. This has particularly been the case with variations relating to lithium batteries, the regulations on the transport of which are already complex and subject to regular change. Some airlines have proposed a total ban on all lithium batteries, including those packed with or contained in equipment, but
such a move has wider implications, such as an effective ban on the transport of medical equipment or data loggers for temperaturesensitive pharmaceuticals, which might well need to be transported urgently.
IATA usually includes an update on operator (and state) variations with each corrigendum or addendum issued during the year, but shippers and freight forwarders may find it more useful to subscribe to the electronic version of the DGR that is automatically updated whenever an addendum or corrigendum is issued and which will include the latest variations.
The idea of having the DGR in an electronic version must be getting increasingly attractive, not least from the point of view of its size. The 59th edition weighs in at 1,126 pages altogether – a far cry from the early days of the Restricted Articles Regulations in the late 1950s, when the whole matter was covered in less than 100 pages.
Indeed, as James Wyatt, assistant director of dangerous goods publications at IATA, notes, the Association’s publications are increasingly being issued and used in online versions. One exception is its Lithium Battery Shipping Guidelines, which are still selling strongly in hard copy; indeed, Wyatt says the print run was increased by 60 per cent this year in response to firm demand.
Wyatt is also involved in spreading the message about the DGR and, together with
Brennan, this month is undertaking a tour of south and south-east Asia with six one-day workshops arranged for shippers, freight forwarders, airlines, aviation authorities and other stakeholders. Getting out to meet those in the business, particularly in emerging markets, helps IATA understand what is happening in those territories and how it can assist in improving safety in the transport of dangerous goods. Such an initiative can also help bring the various players in the supply chain together so they can discuss their respective experiences.
IATA also responds to industry through a dedicated contact form on its website, which gets around 30 queries every day. Many of these are routine, Horner says, but others can also provide input to workshops and other outreach efforts or point to a need for regulatory clarification or revision.
These may end up being discussed by IATA’s Dangerous Goods Board, which next meets in March 2018 in Dallas, right after the World Cargo Symposium.
That meeting will also discuss amendments agreed by ICAO’s Dangerous Goods Panel for the 2019-2020 edition of its Technical Instructions and which will need to be reflected in the 60th edition of the DGR.
For the team at IATA’s office in Geneva, it will be back to the regulatory merry-go-round once again. HCB www.iata.org/whatwedo/cargo/dgr/pages/ index.aspx
THE INTERNATIONAL AIR Transport Association (IATA) has issued its regular useful list of the significant changes to the next edition of its Dangerous Goods Regulations (DGR). As the 59th edition will take effect on 1 January 2018, the list of changes is comparatively brief, running to just two pages. It includes addenda to the 2017-2018 edition of the Technical Instructions agreed this year by the International Civil Aviation Organisation (ICAO) as well as a
number of other amendments agreed by IATA, which represents most of the world’s airlines.
It should be noted that IATA member airlines will expect prompt compliance with the 59th edition of the DGR and that those involved in the movement of dangerous goods by air will need to equip themselves with a copy of the new edition.
The list of changes also notes that the 59th edition will include a new Appendix I to give details of those amendments already agreed by ICAO for inclusion in the 2019-2020 edition of the Technical Instructions; this gives those involved in the supply chain with an idea of some of the changes they will have to deal with in a year’s time, although it should be stressed that they remain subject to final confirmation by ICAO.
Perhaps not surprisingly, many of the changes noted by IATA involve lithium batteries. These
include new limitations in 2.3.5.9 on the number of portable electronic devices (PEDs) and spare batteries that may be carried by passengers and crew. IATA has placed a limit of 15 PEDs and 20 spare batteries per person, which is reflected in Table 2.3.A. These limits may be exceeded with the approval of the operator.
In respect of the packing of lithium batteries, 5.0.1.5.1 has been revised to include new restrictions on packages of UN 3090 or 3480 batteries being placed in an overpack with dangerous goods of Class 1 (other than Division 1.4S), Class 3, Division 4.1 or Division 5.1. Similarly, 5.0.2.11 has been revised to specify that such batteries are not permitted in the same outer packaging as dangerous goods of those classes and divisions.
Text has been added to packing instructions 965 and 968 to reflect those packing restrictions, and Table 9.3.A and
ALL THOSE INVOLVED IN SHIPPING DANGEROUS GOODS BY AIR NEED TO TAKE NOTE OF THE INCOMING REGULATORY AMENDMENTS
the provisions of 9.3.2 have been similarly amended. A note is added to 9.3.2 to identify that the segregation of packages and overpacks loaded into unit load devices (ULDs) and aircraft cargo compartments, while recommended as from 1 January 2018, will not become mandatory until 1 January 2019.
New Cargo IMP codes have been added in Appendix B.2.2.4 to facilitate the differentiation of fully regulated lithium batteries of UN 3090 and 3480 from those packed with or contained in equipment (UN 3091 and 3481). UN 3090 batteries shipped under Sections 1A or 1B of PI 968 are assigned RBM; UN 3480 batteries shipped under Sections 1A or 1B of PI 965 are assigned RBI. UN 3091 batteries are currently assigned RLM and UN 3481 batteries RLI.
Finally, text has been added to 7.1.5.5.2 to recommend a minimum size for the UN numbers on the lithium battery mark.
Several other changes relate to the newly adopted UN entries for engines and machinery. Special provision A70, which identifies the conditions under which engines may be considered as ‘not restricted’ has been revised to require that the shipper provide written or electronic documentation stating that a flushing and purging procedure has been followed for engines power by flammable liquid.
Special provision A203, which identifies that vehicles powered by an engine running on both a flammable liquid and a flammable gas must be assigned to the entry for flammable gaspowered vehicles, has been revised to clarify that in such cases the application provisions of PI 950(a) must also be met. That revision is also reflected in a new requirement added to PI 951.
There has been a restructuring of 3.9.2 to bring in all substances and articles assigned to Class 9, along with their UN numbers and
proper shipping names. These are grouped according to the hazard they pose in transport.
A note has been added to packing instruction Y960 to reinforce the face that dangerous goods of Packing Group I are not permitted.
As is usually the case, there are a large number of additions, deletions and amendments to the operator variations; this is, however, only a snapshot of variations currently in effect and IATA has noted that shippers should check with the carrier before offering dangerous goods for transport by air.
Similarly, there are changes to the contact details for competent authorities (Appendix D), the lists of UN specification packaging suppliers and package testing facilities (Appendix E) and the lists of sales agents, IATA-accredited training schools and IATA-authorised training centres (Appendix F). HCB
The list of significant changes can be found on the IATA website at www.iata.org/whatwedo/cargo/ dgr/Documents/dgr-59-significant-changes.pdf.
THE SPRING 2017 session of the Joint Meeting of RID/ADR/ADN Experts was held in Bern from 13 to 17 March; Claude Pfauvadel (France) took the chair with Helmut Rein (Germany) acting as vice-chairman. The meeting was attended by representatives of 22 full member states, a representative from DR Congo, the European Commission, European Railways Agency (ERA), Organisation for Cooperation between Railways (OSJD) and 16 non-governmental organisations.
Detailed technical proposals relating to tanks and standards were passed on to dedicated working groups and the plenary session adopted most of their conclusions. The Joint Meeting also faced a number of ongoing and new proposals for amendment. These issues were covered in the first part
of this report (HCB October 2017, page 120). Discussion then turned to reports from other informal working groups.
The European LPG Association (AEGPL) presented an informal document with an update on the progress being made by the informal working group on alternative methods for periodic inspections of refillable pressure receptacles, which had met in Paris in January 2017. The paper included three proposals for amendments to RID/ADR/ADN in response to comments made at the autumn 2016 session of the Joint Meeting.
The paper first proposed addition of a new 6.2.3.5.3 with general provisions for the substitution of dedicated checks for periodic
inspections required by 6.2.3.5.1, when the receptacle’s design prevents one or more of the checks in the periodic inspection from being successfully applied or providing meaningful results.
A second proposal laid out general provisions for destructive tests and the evaluation of their results. Finally, a more specific proposal related to over-moulded cylinders included a new definition, a new special provision and details of the required tests and acceptable results.
The paper drew many comments. In particular, some experts were worried about the mixture of guidelines and procedures that the proposals would add to the regulations, in addition to the actual technical requirements. There are also questions remaining on sampling rules and the definition of a possible service life in light of potential degradation and ageing characteristics. Some detail on acceptable confidence and risk levels should also be included.
In addition, the informal working group was invited to develop technical guidelines for the implementation of alternative control methods. As opinions differed regarding the incorporation of these guidelines into
the regulations, the issue will be considered by the informal working group for a later decision by the Joint Meeting.
France presented a report on work carried out by the National Institute for Environmental Technology and Risks (Ineris) on boiling liquid evaporating vapour explosions (BLEVEs) in the context of the informal working group on reducing the risk of a BLEVE during the transport of dangerous goods.
Ineris has developed a predictive tool to forecast the behaviour of LPG tanks when exposed to fire and the effects of the use of safety valves and thermal coatings in different tank geometries. The results of the Ineris model are consistent with experimental tests carried out in 2013 and 2014 by Germany’s Federal Institute for Materials Research and Testing (BAM) and offer a way of covering a broad range of scenarios without the need for expensive destructive tests. However, the French paper said, more tests might be necessary before final validation of the model. A number of delegates said they could provide experimental data to help with this process.
A technical discussion followed on the respective merits of the different ways of preventing BLEVEs, with some delegations expressing reservations about the use of thermal insulation, given both the possible economic drawbacks (cost and reduction in carrying capacity) and the safety concerns (risk of damage, corrosion, etc). It was, however, recalled that all the relevant elements need to be taken into account in the context of risk assessment and it would be preferable for the technical discussions to take place within the informal working group.
Interested delegates were invited to inform the representative of France of any simulations that they would like to see carried out. Results of those simulations would be presented at the autumn 2017
Joint Meeting, at which point a new mandate would be decided on for the continuation of the informal working group’s activities.
The European Railways Agency (ERA) presented a report on the eighth and ninth workshops on the roadmap for risk management in the inland transport of dangerous goods by road, rail and inland waterways, which were held in October 2016 and February 2017, respectively.
The eighth meeting was largely devoted to reviewing progress and determining further direction. It was noted that, while there is a lot of work still to be done to finalise the three guides and two user manuals that are envisaged, the principles and content of these documents have been agreed. It was anticipated that first versions of the documents could be ready by the end of 2017 and ERA was asked to consider how their ongoing maintenance would be arranged.
The ninth workshop provided an opportunity for those groups working on the three guides to discuss the interaction of the guides and to solve potential gaps and inconsistencies. It was agreed that a combination of the risk estimation method and the decision-making process will establish a versatile and transparent risk-based decision-making standard that could be applied to a variety of risk situations in the transport of dangerous goods, including those foreseen in Chapter 1.9 of RID/ADR/ADN.
During the discussions, it was noted that the framework of the guides will clearly describe the independent roles and responsibilities of the risk estimators and decision-makers in order to avoid biased risk estimations/ decisions. As a principle, it was agreed that the user of the risk estimation guide will be responsible for delivering good quality risk estimations to the decision-maker, and that the decision-maker should not intervene directly in the practical risk estimation tasks.
It was also stressed that, while the decision-making process will make use of risk estimation indicators, the decision-making guide will not define risk acceptance criteria in its first version. This will allow for more flexible use of the first version of the guide and for taking stock of user experience before this need is reconsidered.
Other discussions revolved around the need for a high-profile launch event early in 2018, the need for publication in various languages, and ownership of the guides.
ERA noted that the tenth workshop, which was to be held in June 2017, would consider a plan of action for the period 2018-2021.
Delegates at the Joint Meeting were invited to attend.
The Joint Meeting recalled that the whole process had been set up in response to a need for harmonisation of risk management procedures within the EU, and that their results could be reflected in a European »
directive. Also, in order to allow the Joint Meeting to the discuss the potential implementation of the procedures contained in the guides, it was suggested that ERA give a presentation of the guides under development at the autumn 2017 session.
The European Industrial Gases Association (EIGA) returned to the troubled issue of the mutual recognition of pressure receptacles between the US and those states party to RID, ADR and ADN. It reported that work has been slow in drawing up a petition for rulemaking in the US to allow for reciprocity but that it was anticipated that a submission would be made soon. EIGA promised to keep the Joint Meeting informed and, should the petition be successful, felt it would then be appropriate to include a new 1.1.4.7 in RID/ADR/ADN to mirror the text in multilateral agreement M299.
The International Union of Railways (UIC), the International Road Transport Union (IRU) and the European Chemical Industry Council (Cefic) reported on developments in Poland, where a new law to indicate the owner of the dangerous goods being carried on documents required in Chapter 5.4 has entered into force. This is causing problems as it introduces a disharmony in documentation, which runs counter to the aims and terms of the ADR Agreement and other transport agreements. The Polish government had noted industry concerns and that investigations would take place to find the best solution both for the industry and to facilitate international trade. The EU has also promised to initiate an official procedure.
Subsequently, as part of its Transportation Package of fiscal measures, Poland is planning further measures for certain dangerous goods for tax reasons, such as special reporting and monitoring obligations for consignors, carriers and consignees, using global positioning systems, among other things.
The Joint Meeting noted that the requirement to indicate the owner of
dangerous goods in transport documents in Poland is linked to a tax regulation and that the government of Poland does not consider it to be in contradiction with ADR, in view of article 4(1). It also noted that the European Commission was considering the legal aspects.
The Secretariat of the Intergovernmental Organisation for International Carriage by Rail (OTIF) provided an update on problems with harmonisation of RID with SMGS Annex 2, the corresponding provisions used by the Organisation for Cooperation Between Railways (OSJD). The 2017 amendments to RID have not been adopted into SMGS Annex 2, largely because of Russia’s insistence that all new and existing references to EU Directives and EN Standards should be deleted. As OSJD organs work on the principle of unanimity, this has prevented adoption of the latest amendments.
The OSJD Group of Experts on Provisions for the Carriage of Dangerous Goods and the OSJD Commission for Transport Law both met in February 2017 but once more no decision could be taken. Both Russia and China were – perhaps with some justification – concerned by the fact that EN standards do not cover the entire range of issues and urged reference to globally acceptable ISO standards. Russia also pointed out that, along with Belarus,
Kazakhstan and Kyrgyzstan, it is part of a trade bloc where there are different provisions for pressure receptacles and it would be necessary to check whether the newly referenced EN standards accord with the provisions in place in those countries.
A number of options were investigated but, as of 1 July 2017, there is disharmony between the two sets of provisions. This is of particular concern to those countries that are party to both RID/ADR/ADN and OSJD but also to those that apply ADR for road transport and SMGS for rail transport.
The Joint Meeting hoped that the OSJD member states would be able to adopt at least those amendments not related to the CEN standardisation work and EU directives.
Some OSJD stated had requested that the next meeting of the OSJD Commission for Transport Law, planned for October 2017, could be brought forward to allow the issue to be discussed.
The Council on Safe Transportation of Hazardous Articles (COSTHA) had applied for consultative status at the Joint Meeting. After some discussion that request was granted. HCB
The autumn session of the Joint Meeting took place in late September 2017; a report on that session will appear in a forthcoming issue of HCB.
ROAD • WP15 IS GETTING ON WITH THE BUSINESS OF AGREEING THE CHANGES TO ADR THAT WILL TAKE EFFECT IN 2019. DUTHYOLDERS NEED TO GO THROUGH THE NEW TEXTS WITH CARE
THE 102ND SESSION of the UN Economic Commission for Europe’s (ECE) Working Party on the Transport of Dangerous Goods (WP15) took place in Geneva from 8 to 11 May 2017. The meeting was chaired by JA Franco (Portugal) with Arianne Roumier (France) as vice-chair. It was attended by representatives of 24 contracting parties, the European Union (EU), the Intergovernmental Organisation for International Carriage by Rail (OTIF) and three non-governmental organisations.
WP15 is the body responsible for maintaining and updating the technical
annexes to the ADR Agreement, which governs the international transport of dangerous goods by road between those states that apply ADR – mostly but by no means all in Europe. The May meeting began work on agreeing the amendments that will enter into force in 2019; to do this it had to take into account the multimodal amendments adopted in December 2016 by the UN Committee of Experts on the Transport of Dangerous Goods and the Globally Harmonised System of classification and labelling of chemicals (GHS) as well as the two previous sessions of the Joint Meeting of RID/ADR/ADN experts held in autumn 2016 and spring 2017.
Before it could put its collective mind to that task, however, the Working Party heard from Eva Molnar, director of ECE’s Sustainable Transport Division, who presented the draft strategy of the Inland Transport Committee (ITC), WP15’s parent body. WP15 had already been invited to comment on the draft and Ms Molnar
reiterated that invitation, with particular emphasis on three topics:
• Facilitating implementation of the UN’s Sustainable Development Goals on issues of relevance to the Working Party
• Facilitating the implementation of and accession to ADR by new contracting parties, and
• What changes in the transport of dangerous goods can be expected by 2030, for instance in areas such as the geographical application of ADR, the use of telematics, and efforts to reduce greenhouse gas emissions.
Some delegations were at pains to point out that the Working Party has always had to deal with technological changes in the industry and they saw no problems in accommodating future changes.
The Secretariat advised the meeting that Ukraine had acceded to the Protocol amending certain articles of the ADR
Agreement; it encouraged the 13 countries that have so far not done so to follow suit so that the Protocol can enter into force.
The Working Party also noted that the corrections to ADR adopted at its 101st session had been deemed to be accepted.
The next item on the agenda was for the Working Party to review the decisions made by the Joint Meeting. These were broadly accepted, although certain amendments and transitional provisions were were still to be confirmed by the Joint Meeting at its autumn 2017 session and WP15 will await the outcome of that session before adopting them.
WP15 also noted certain corrections proposed by the Joint Meeting at its spring 2017 session; these were largely editorial in nature and the Working Party felt that they should be adopted and a second corrigendum to the 2017 text issued as soon as possible.
In the event, the Treaty Section of the UN Office of Legal Affairs expressed the view that most of the proposed corrections did not meet the strictly applied criteria; as a result, only three changes will be contained in the corrigendum [as of the end of September this document is still awaited] and the remaining corrections will form part of an official proposal from Portugal. A similar fate befell proposed corrections to Chapter 9.2 in an informal paper from Romania, which will also be part of the Portuguese proposal.
In an informal document, Germany initiated discussion of problems being experienced in that country with interpretation of the requirements in 9.3.4.2, with particular reference to the use of ‘sandwich’ panels of different materials used in the construction of EX/II and EX/III vehicles.
The discussion revealed that there is a lack of agreement on the subject and the Working Party recognised that it would be a worthwhile exercise to update and clarify the technical requirements for the construction of EX/II and EX/III vehicles. Germany offered to prepare a more detailed proposal at the next session and invited comments and technical data from other delegations.
France had noticed that, while 9.2.2.9.1 on permanently energised circuits refers to some parts of the IEC 60079 standard, the text in ADR does not refer to two parts of the standard that might be of relevance to FL vehicles. The Working Party agreed to its proposals and extended the references in 9.2.2.9.1(a) and 9.7.8.2 to cover parts 26 and 28 of IEC 60079. It also confirmed that equipment installed on vehicles in accordance with those paragraphs prior to the entry into force of the amendment could still be used.
Norway returned as promised with its proposal to extend the fastening requirements in 9.7.3, which apply to tank vehicles, batteryvehicles and vehicles carrying demountable »
tanks, to also apply to vehicles carrying tank containers, portable tanks and multiple-element gas containers (MEGCs). The Norwegian paper offered some alternatives, of which the Working Party adopted four, with some minor amendments.
As a result, 9.7.3 has been amended to extend its applicability and a new 9.7.3.3 is added:
For tank-vehicles, battery-vehicles and vehicles carrying demountable tanks, the fastenings shall withstand the minimum stresses as defined in 6.8.2.1.11 to 6.8.2.1.13, 6.8.2.1.15 and 6.8.2.1.16.
In addition, 7.5.7.4 has been amended to read: The provisions of 7.5.7.1 shall also apply to the loading, stowage and removal of containers, tank-containers, portable tanks and MEGCs on to and from vehicles. When tank-containers, portable tanks and MEGCs do not use corner castings in the patterns as defined in ISO 1496-1 Series 1 freight containers -- Specification and testing -- Part 1: General cargo containers for
general purposes, it shall be verified that the systems used on the tank-containers, portable tanks or MEGCs are compatible with the system on the vehicle and in compliance with the requirements in 9.7.3.
A transitional provision has been added at 1.6.5.22 to allow vehicles first registered or entering into service before 1 January 2021 that do not comply with the new requirements to continue to be used.
The UK reported that, following delays in processing vehicle test applications, it has allowed the first inspection on EX, FL and AT vehicles and mobile explosives manufacturing units (MEMUs) to be waived until the first anniversary test. This has been successful and the UK now proposed amending 9.1.2.1 to bring a similar provision into ADR.
After preliminary discussion, it was decided to hold this proposal for further consideration at the next session.
Sweden had noticed that the Guidelines for completing the certificate of approval according to 9.1.3 had fallen out of step with
“IN THE CURRENT ECONOMIC CONTEXT, SOME GOVERNMENTS ARE PUTTING IN PLACE WHAT AMOUNT TO PROTECTIONIST MEASURES”
the ADR provisions following amendments to the table in 9.2.1. The Joint Meeting agreed and, in the first example shown in paragraph 8 of the Guidelines, changed “Note (b)” to “Notes (f) and (g)”.
Switzerland felt that it should be clarified in 1.1.3.2(a), 1.1.3.3(a) and 1.1.3.7 that vehicles, when carried as a load, should be assigned to UN 3166 or 3171. This would help explain the additional provisions that are applicable. The feeling of the Working Party was that, as such consignments may go by rail or sea as easily as by road, this was a matter for the Joint Meeting.
A joint paper from Sweden and the International Road Transport Union (IRU) reiterated their idea that the calculated value/ transport category should be shown on the transport document when goods are carried in accordance with 1.1.3.6. The concept had received support from a number of delegations at the May 2016 session although a revised proposal submitted to the November 2016 meeting failed to find consensus, with most delegations being of the opinion that less extensive amendments to 1.1.3.6 should be made.
This time round, after a vote, the proposals were adopted for entry into force in 2019. As a result, a new table note b is added to the heading of column (b) in the table in 1.1.3.6.3:
The maximum total quantity for each transport category corresponds to a calculated value of “1000” (see also 1.1.3.6.4).
At the end of 1.1.3.6.4, after the indents, “a calculated value of” is inserted after “shall not exceed”. Note 1 to 5.4.1.1.1(f) is amended to read:
In the case of intended application of 1.1.3.6, the total quantity and the calculated value of dangerous goods for each transport category shall be indicated in the transport document in accordance with 1.1.3.6.3 and 1.1.3.6.4.
A paper from Switzerland followed up on earlier discussion of the scope of 1.1.3.1(a)
dealing with the carriage of goods by private individuals. One of the reasons for its interest in the topic was a request for clarification from a diving club, which carries out the filling and testing of its own cylinders: does this fall under the relief provided in that section? Switzerland also felt that this was a matter largely for road transport but other delegations disagreed: once the implications of the proposal were addressed it would probably affect rail transport as well.
The Working Party noted, however, that the exemptions available under 1.1.3.1(a) are being interpreted and implemented differently in different countries and that the issue is worth pursuing. The proposal was withdrawn but is likely to return in an amended form, taking note of the comments provided.
The Secretariat returned with a proposal to reference the new IMO/ILO/UNECE Code of Practice for Packing of Cargo Transport Units, the ‘CTU Code’, in ADR. It was agreed that reference to chapters 9 and 10 of the CTU Code should be made in the footnote to 7.5.7.1. Germany felt that this ought to refer to all of the CTU Code and may return with a formal proposal at the next session.
At the previous session, Spain had sought the opinion of the Working Party on the desirability of increasing the total quantities of explosives that could be carried on EX/III vehicles. It now returned with a formal proposal, pointing out that the limit of 16 tonnes has been in place since ADR first entered into force in 1968 and that there have been significant improvements in vehicle and road quality since then. However, the paper was rebuffed, with little support for the proposal. Spain nevertheless promised to return with a revised paper at the next session, taking into account comments made.
Switzerland observed that, according to 1.1.4.2.2, transport units bearing markings that do not conform to 5.3.1 are considered acceptable if the provisions of 5.3.2 are met. In effect, this relates to transport units in a multimodal shipment that do not bear orange-coloured plates. However, Switzerland contended, the reference to 5.3.2 makes it mandatory to mark transport units that would otherwise have been exempted from the requirement by 1.1.3.6. »
The Working Party confirmed that, the provisions of 1.1.4.2.2 notwithstanding, transport units not placarded in accordance with 5.3.1 but that are marked and placarded in accordance with Chapter 5.3 of the IMDG Code and that have been accepted for carriage in a transport chain that includes a maritime movement, are not required to bear orangecoloured plates. Most delegations considered that this interpretation is not in conflict with the current wording of 1.1.4.2.2 and, on a vote, it was decided that no action is necessary.
Another proposal from Switzerland sought the application of tunnel restrictions on consignments of machinery and engines of UN 3528, 3529 and 3530. The Working Party, alert to the issue, had been awaiting action by the UN TDG Sub-committee on the scope of special provision 363 before considering whether these UN entries should be assigned tunnel codes and made subject to the requirements for orange-coloured plates.
There was some discussion of the proposal but the Working Party was generally in favour
of inserting the requisite text. After some amendments to the Swiss proposal, it was decided to amend special provision 363(l) to read:
When the engine or machinery contains more than 1 000 l of liquid fuels, for UN No. 3528 and UN No. 3530, or the fuel tank has a water capacity of more than 1 000 l, for UN No. 3529:
• A transport document in accordance with 5.4.1 is required. This transport document shall contain the following additional statement “Transport in accordance with special provision 363”;
• When the carriage is known beforehand to pass through a tunnel with restrictions for carriage of dangerous goods, the transport unit shall display orange-coloured plates according to 5.3.2 and the tunnel restrictions according to 8.6.4 apply.
Tunnel codes have been assigned to the three entries, with the following codes added in column (15) of Table A in Chapter 3.2: UN 3528 (D); UN 3529 (B); UN 3530 (E).
Consequential amendments were made to 1.9.5.2.2.
Staying with orange-coloured plates, Austria had identified some conditions under which it would be possible to comply with the requirements of 5.3.2.1.4 and 5.3.2.1.6 in a manner that is not intended and that those paragraphs might benefit from
some amendment. On a vote, two changes were agreed.
In 5.3.2.1.4, “transport units” and “transport unit” are replaced by “vehicles” and “vehicle”, respectively, wherever they appear. A revision to the start of 5.3.2.1.6 was agreed but has been placed in square brackets pending confirmation at the next meeting: For transport units carrying:
• Only one dangerous substance, which requires the marking with orange-coloured plates; and
• No non-dangerous substance in fixed tanks, portable tanks, demountable tanks, tank-containers, MEGCs or in bulk; the orange coloured-plates described in 5.3.2.1.2, …
Sweden had spotted an error in 8.1.2.1(a), left over from a change to 5.4.2 made in 2015. It argued that the words “large container or vehicle packing certificate” should be changed to “container/vehicle packing certificate”. The Working Party agreed and made the change.
The government of Poland sought the Working Party’s interpretation of the list of information required on the Multimodal Dangerous Goods Form specified in Chapter 5.4 of ADR; in particular, is this list exhaustive or may contracting parties require additional information?
The question relates to the introduction of amendments to Poland’s Energy Law Act and certain other Acts that now require that the transport document shows the name and address of the entity that owns the dangerous goods being carried. As has been reported previously, this is causing problems for those consigning or carrying dangerous goods to, from or through Poland and presenting obstacles to the seamless flow of international trade.
The Working Party confirmed nevertheless that article 4(1) of the ADR Agreement does not prohibit the inclusion of additional information in the transport document, even if it is required for reasons other than safety during carriage.
The IRU representative regretted that such measures were being imposed in some countries, under the shelter of article 4(1),
and that these could be seen as trade barriers. He invited contracting parties to keep ECE informed of any such problems via its website.
The chair noted that, in the current economic context in Europe, some governments are putting in place what amount to protectionist measures involving the transport of goods in general; ADR competent authorities are not always aware of those measures, which tend not to be generated by the country’s transport ministry, and are often finding it difficult to alert dangerous goods carriers. It was suggested that those issues should be brought to the attention of ITC.
Romania had identified a difference in the English and French texts of comment c in the table in 9.2.1.1. The English text refers to “motor vehicles intended to draw trailers with a maximum mass exceeding 3.5 tonnes” while the French text has (in English) “motor vehicles with a maximum mass exceeding 3.5 tonnes intended to draw trailers”. Which is the correct version?
The Working Party confirmed that it is the English text that reflects the proposal adopted in 2015 and that the French text contains and error; it asked the Secretariat
to include a correction to the French text in the forthcoming corrigendum.
The Working Party adopted a draft programme of work for 2018-2019 as prepared by the Secretariat, while reducing the length of the planned November 2018 session from five days to four.
The next session, which was due to take place from 6 to 10 November 2017 (a report on which will be included in a forthcoming issue of HCB), was to include a discussion of the construction of the bodies of EX vehicles as well as a half-day round-table session on the transport of dangerous goods. The session will also see the election of officers for 2018.
The European Chemical Industry Council (Cefic) presented a revised version of the guidelines for application of Chapter 1.10 of ADR on the security of the transport of dangerous goods by road; these guidelines had been put together by a broad group of trade associations. The Working Party thanked the organisations concerned for undertaking the project, which many delegations have found to be of great use, and for the work to keep the guidelines updated. HCB
Emergency responders face a wide range of hazards when discharging their duties and are used to dealing with some unusual situations, but fire crews called out to a blaze in southern California at the end of September had to deal with something they had not encountered before and were not only not fully prepared but, indeed, not inoculated against.
A fire broke out at a homeless encampment in Spring Canyon Drive, just off I-125 in Spring Valley. The fire was contained in one area of the site but fire crews had to access a stream alongside the encampment. As San Miguel Fire Battalion Chief Andy Lawler explained to NBC San Diego, “The homeless population use this stream for what most of us use toilets or sinks or showers and bathtubs.”
What this meant was that, as they slid down the besmirched bank of the stream, the responders’ suits became increasingly smeared with human faeces, raising concerns over possible contamination with Hepatitis A. “We’re not talking about a small amount of contaminants there, we’re talking about a lot,” Lawler said. “We had faeces on the personal protective equipment.”
In total, 11 firefighters were contaminated and were advised to use soap and water, or bleach, to get themselves clean. “We also have a hose,” Lawler added, helpfully.
Meanwhile, over in Baltimore, four family members were injured, two severely, when a makeshift fire pit exploded. The family was sitting around a bonfire built inside the drum of an old washing machine on a Sunday evening early in October when the incident happened. Neighbours reported
hearing a loud blast “like a cannon going off”. Apparently they are used to hearing gunfire in this part of Baltimore and were not that alarmed by the explosion.
It may sound an odd thing to do, but one local news source said that plenty of people repurpose washing machine drums as fire pits and there are tips online on how to do it.
The cause of the explosion was rather more mundane, though: a spokesperson for the Baltimore County Fire Department said: “There was some kind of identified accelerant that was used and that accelerant is what exploded.” What caused the severe injuries is worth noting: the family was said to have been using a decades-old model of washing machine in which the drum contained a ring of lead shot for ballast and it could well have been this shrapnel that made things worse.
Earlier this year, residents of the town of Windsor in northern California were surprised to find their streets and cars painted pink. It emerged that a Cal Fire air tanker, returning from an aborted call to deal with a forest fire, inadvertently dropped its load of Phos-Chek fire retardant before landing at the nearby airport in Sonoma.
Once again the local fire department was called out to handle what was, in the end, a fairly harmless incident. They ended up washing vehicles and cleaning the pink stuff off the road, although care had to be taken to make sure nothing entered nearby waterways. Phos-Chek, manufactured by ICL Performance Products, contains a cocktail of phosphate and sulphate salts, along with thickening agents and a red dye to help aircrews target their drops.