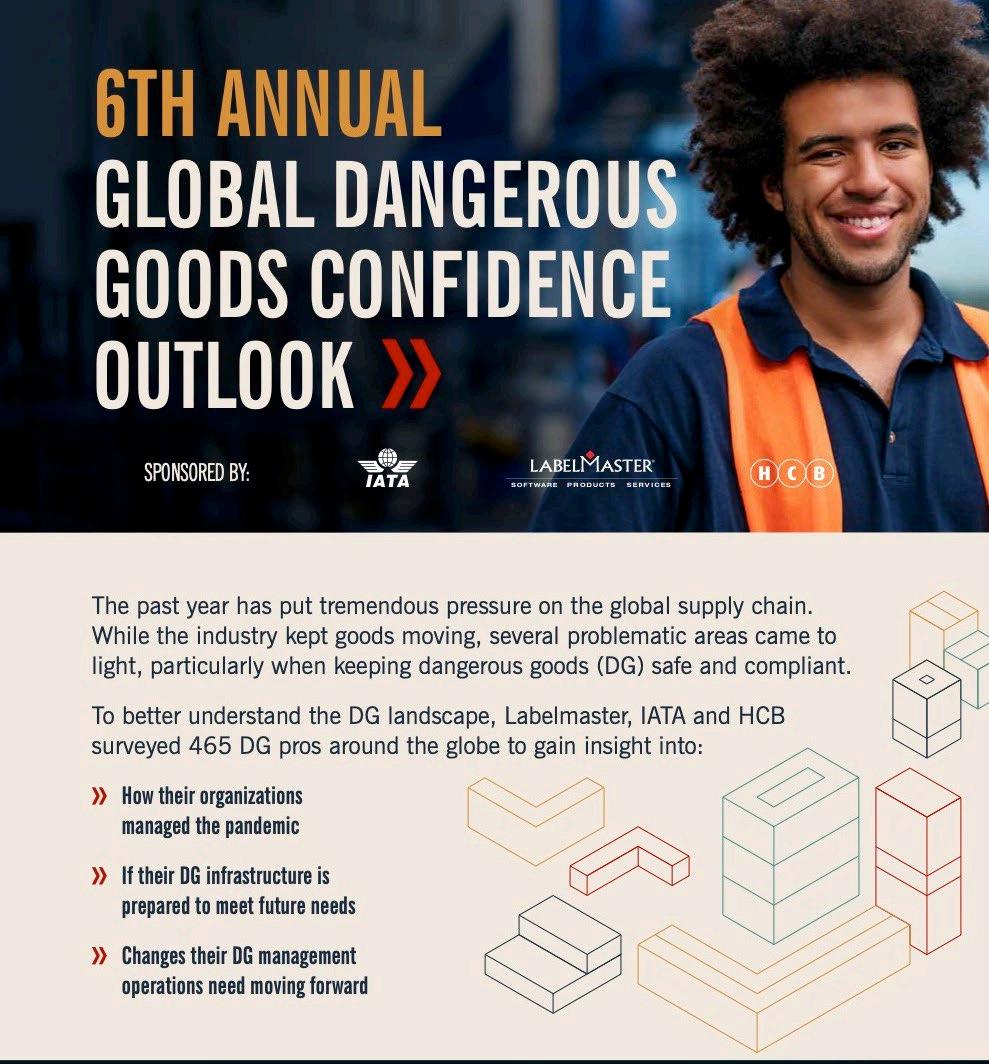
6 minute read
Survey shows the need for action
FACE THE CHANGE
CONFIDENCE • THE ANNUAL LABELMASTER DG SURVEY HAS IDENTIFIED MANY OF THE SAME FAILINGS AS IN THE PAST. BUT THERE ARE WAYS OUT OF IT, IF DG PROS TAKE CONTROL
REGULATORY COMPLIANCE IS the cornerstone of safety in the transport, storage and handling of dangerous goods. To achieve the necessary level of compliance, regulations and enforcement activity need to be transparent, balanced and consistent; all those involved in the regulated activities need to be properly trained and competent to do their jobs; and, perhaps most importantly, business owners and managers need to be aware of the hazards their activities present to workers, the public and the wider environment and to be prepared and able to provide the tools needed to ensure that their goods move safely.
Unfortunately, as Labelmaster’s annual Global Dangerous Goods Confidence Outlook survey has found over the six years it has been conducted, there is a persistent lack of confidence among a significant slice of dangerous goods professionals that they have the tools, ability and support needed to achieve consistent compliance. The results of a lack of compliance are not just fines and penalties from the enforcement agencies, but also a regular disruption to supply chains as goods are held up or returned, with a consequent impact on customer service and, if such conditions persist, a negative corporate image.
This year’s Labelmaster survey, held again in collaboration with HCB and the International Air Transport Association (IATA) this past March/ April, showed that those trends are still in place. The ‘three tribes’ identified in the 2020 survey – the best, the just good enough and the below-par – are still there too. And, as this year’s survey took place at the end of a year when supply chains were even more stressed than usual, as a result not only of the ongoing Covid-19 pandemic but also disruption in ocean freight and the longer-term impact of a shortage of drivers, it is illuminating to see that some of those questioned had managed to sail through it all, benefitting from the latest technology and the backing of their management.
HAPPY WITH PERFORMANCE When last year’s survey was carried out, in June 2020, three months into the pandemic, responders reported struggles with: • Receiving goods in a timely manner • A lack of carrier availability • Training and recertifying employees • Keeping up with the regulations.
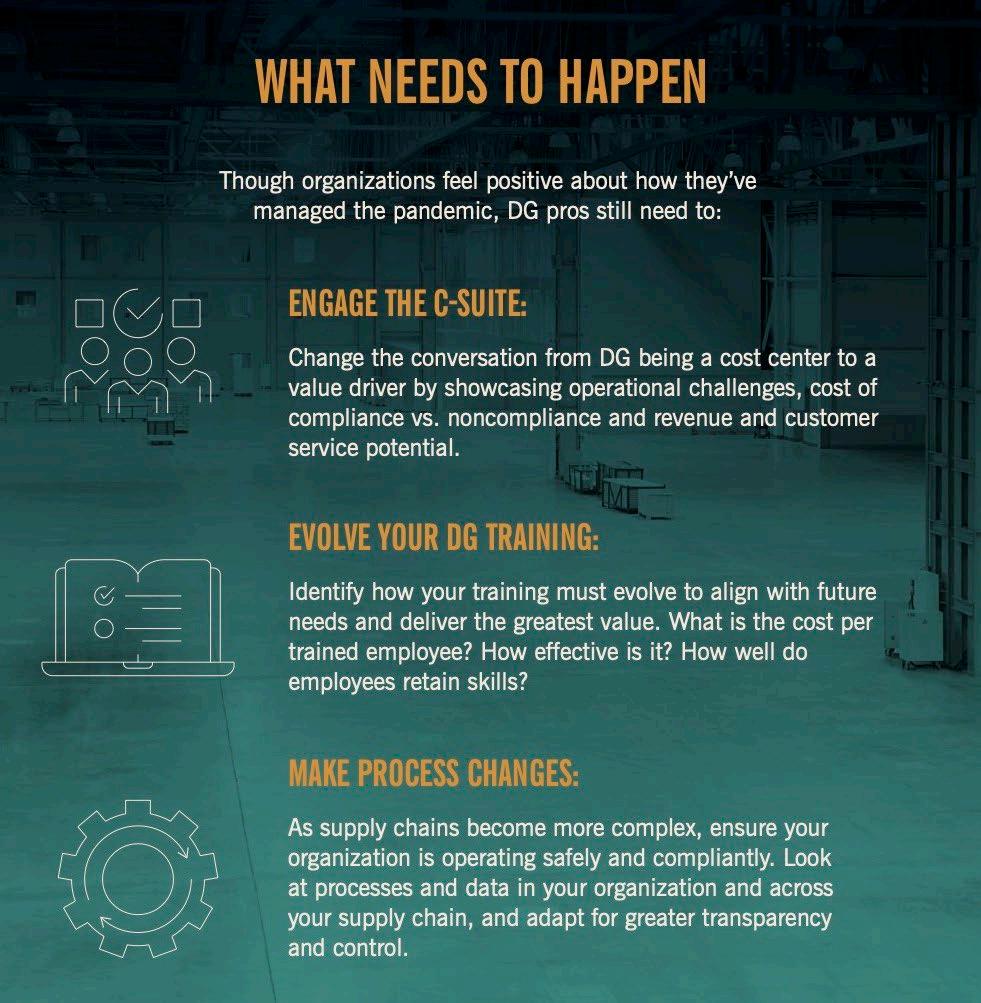
One year on and the picture is rather different: 80 per cent of this year’s respondents agreed that their companies coped well during the pandemic, with 62 per cent crediting their supply chain IT capabilities as playing a role in that performance. Indeed, 37 per cent said that their operations are already back to ‘normal’ and another 29 per cent anticipated getting back to pre-pandemic conditions within a year.
Despite that, among the 465 respondents to this year’s survey there were indications that there are still critical organisational issues that must be addressed if they are to be able to achieve compliance at a high level. Half of them pointed to inadequacies in organisation awareness of the role and its importance to the business and the lack of infrastructure with which they are provided. Nearly half were concerned about training, not least during the pandemic restrictions and the inability to conduct face-to-face training.
Other pain points are felt, as ever, in a lack of harmonisation between the various sets of regulations that must be applied, as well as their interpretation in different countries or even between different enforcement agents; the need for more investment in dedicated technology; and a lack of regulatory presence in the supply chain, which leaves the rulemaking bodies without the insights needed to develop the rules that will achieve the desired effect.
The need for greater support in terms of the provision of resources for dangerous goods compliance is well documented and something that has been flagged up over the past six years by the Labelmaster survey; nevertheless, most respondents to this year’s survey said that they are not expecting to see any growth in organisational support, with 75 per cent expecting the same – or even less – spending on dangerous goods management.
WHERE CHANGE IS NEEDED Looking at the shortcomings that dangerous goods professionals are facing, • Only 25 per cent believe their company’s current infrastructure is equipped to meet their future needs • Less than 20 per cent believe the existing technology at their disposal supports their company’s future dangerous goods needs • Just over 40 per cent feel that their current training and recertification curriculum is not equipped to meet future needs • More than 30 per cent feel their company’s senior leaders are unaware of the challenges they face in the dangerous goods supply chain • More than one-third indicated that their company only adheres to the minimum requirements.
These issues recur year after year and Labelmaster, HCB and IATA have been looking at the data to offer a way to improve the situation. So, while most organisations feel positive about how they have managed the pandemic (so far, at least), dangerous goods professionals need to do something to get attention.
Firstly, they need to change the conversation and engage the C-suite. Dangerous goods compliance needs to be seen not as a cost centre but as a value driver; make the effort to showcase the operational challenges, the costs of compliance versus non-compliance; and the opportunities for better-than-average compliance as a revenue generator and customer service tool.
Secondly, dangerous goods professionals should identify now how their training needs will have to evolve to meet future needs and to deliver the greatest value. Try and work out the cost per trained employee: how effective is it and how well do those employees retain the skills?
Finally, as supply chains become more complex, dangerous goods professionals have a responsibility to ensure that their organisation is operating safely and in compliance. Look at processes and data within the organisation and across the supply chain and adapt them, using technology if necessary, to delivery greater transparency and control.
Another area where dangerous goods professionals consistently appeal for help is for more harmonised regulation and interpretation, with only 23 per cent of this year’s respondents believing rules are well aligned across regions, industries and within their own organisation. While the regulators always have their eye on harmonisation, their work too has been disrupted by the pandemic and, when it comes to the crunch, many national or regional regulatory bodies find their own good reasons to vary from the international model. That might be fine for those companies operating only within their national borders but the dangerous goods sector is increasingly international in scope and there remain many potential pitfalls for those shipping dangerous goods overseas, or importing from other territories. Individuals will find it difficult to put pressure on their regulators to take a more harmonised view and this is where representative trade bodies can play a part. It will also help when we can all get back to meeting in person and talk to regulators at industry events.
Labelmaster’s own annual DG Symposium, taking place online this month, is another casualty of the pandemic; it is to be hoped that we will all be able to get back to Chicago next year and try and thrash these issues out in person.
For more help with compliance issues, visit the Labelmaster website, www.labelmaster.com, and keep up to date with changes at www.hcblive.com.