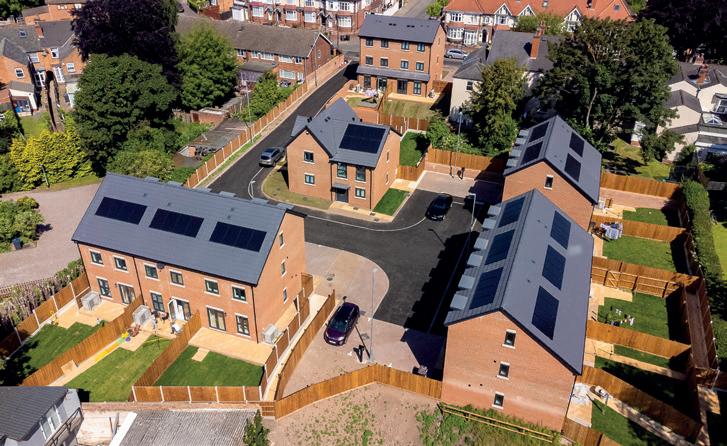
4 minute read
THE BUILDING BLOCKS OF SAFE AND SUSTAINABLE SOCIAL HOUSING
from PSBJ June 2023
Jenny Smith-Andrews, Head of Marketing at H+H, considers masonry construction as a sustainable building solution for the public sector.
asonry may not be the obvious choice for sustainable construction in the public sector, but it offers solutions to specific challenges and is a strong option for creating sustainable and durable social housing.
Advertisement
Fabric first helps tenants and landlords
Cold winters and the rising cost of energy over the last 18 months has shown us that we need to build a thermally-robust social housing stock. To achieve this, a fabric-first approach is necessary, building thermal efficiency into the structure of each building rather than relying solely on solar panels and heat pumps.
Masonry products’ inherent thermal performance makes them an excellent choice for new homes designed to meet current and future energy efficiency standards. Approved Document L recommends using the same material below DPC as in external walls for insulation continuity, making masonry the ideal choice for wall construction as it can be used in foundations.
Highly thermally efficient, masonry materials achieve excellent U-values in wall building. For example, cavity walls built with lightweight, aircrete blocks can reach a U-value as low as 0.11W/m2K, when combined with the right insulation materials.
An intrinsically-fabric-first approach to building, Passivhaus construction creates homes designed to reduce or eliminate additional heating, saving residents’ money and drastically reducing a dwelling’s operational carbon footprint. Materials like aircrete have proven success in creating the airtight structures and low U-values needed to meet the stringent building standard.
Passivhaus construction is gaining popularity in the UK, showing great promise for the public sector. In 2014, Southern Housing built a Passivhaus development on the Isle of Wight with aircrete, which has been highly successful, satisfying residents and the landlord.
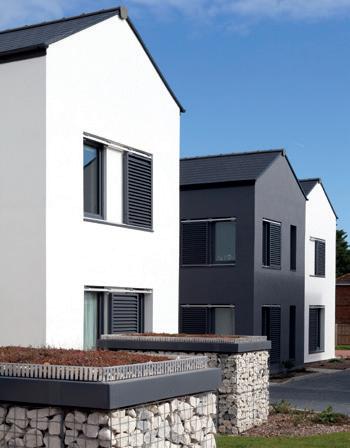
Head of Design and Technical at Southern Housing, Jack Ostrofsky, praised Passivhaus construction for social housing and called the masonry development a “phenomenal success”, citing reduced carbon emissions and lower tenant heating costs as key benefits.
Some residents reported not needing heating all year, and one tenant claimed that lighting a candle in the evening was enough to keep the living room sufficiently warm. Saving money on heating expenses made tenants more comfortable and helped secure rental income for the social landlord.
Building durability and safety into the housing stock
In late 2021, the Levelling Up, Housing and Communities Committee launched an inquiry into social housing regulation after media reports of disrepair. The inquiry found that the age and design of social housing is a principal cause of disrepair1
Much of this existing stock was only built in the 1970s using lightweight, modular construction. While the design life for homes in the UK may be 60 years, houses constructed of masonry have a life expectancy of over 100 years, lasting for generations.
After the Grenfell Tower tragedy in 2017, fire safety standards for housing have been under scrutiny, with some building materials still in question for use in affordable housing schemes. The Mayor of London, Sadiq Khan, recently reiterated his concerns about using combustible materials in his Affordable Homes Programme 2
Moreover, last December the National Fire Chiefs Council expressed concern over efforts to build homes quickly with prefabricated methods. They warned of ‘significant uncertainty’ regarding the fire performance of modular homes and called for stricter testing3
Masonry products offer excellent fire resistance. Modern construction methods, like aircrete Vertical Wall Panels, can speed up building while providing masonry’s performance benefits, helping to safely deliver the homes England needs, fast.
Moisture build up and mould growth is another serious concern for the social housing sector, with the tragic death of Awaab Ishak in 2020 highlighting the severity of the problem.
Damp and mould are some of the biggest issues currently faced by social housing associations with the number of social housing tenants in England complaining of damp and leaks on course to more than double in the years since Awaab’s death4
With damp a prevalent issue in existing social housing stock, it is imperative that we avoid building this same issue into brandnew housing. Here, building with bricks, blocks and pre-cast concrete or aircrete panels offers an immediate solution.
With masonry, interstitial condensation in buildings is less likely to cause damage. Water falling or laying on brick and block, while not ideal, will not cause structural damage and can be easily rectified, protecting residents and landlords alike.
The potential of masonry
While masonry is durable and energy efficient, the elephant in the room is embodied carbon. However, the masonry industry has enormous potential to improve and decarbonise –starting with manufacturing.
Significant advancements have already been made, of course. The UK, for example, is leading the way with the sustainable production of aircrete blocks. The H+H factory in Kent is the most efficient aircrete plant in Europe and plans are in place to further upgrade the factory later this year.
Masonry manufacturers’ scope 1 and 2 emissions will vastly improve as the nation’s electricity system decarbonises. In 2021, the Government announced aims to fully decarbonise the power grid by 2035 and earlier this year, a Climate Change Committee report voiced confidence that this goal is still very much achievable5,6 www.hhcelcon.co.uk
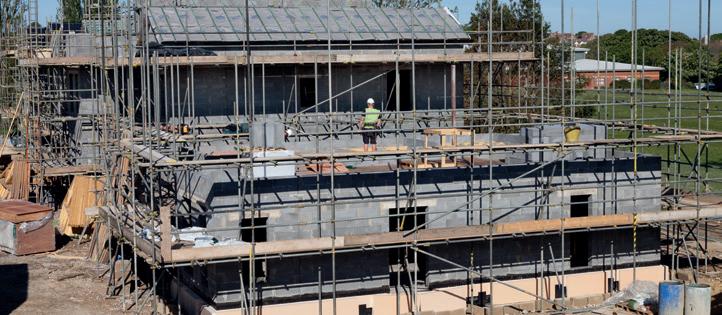
Admittedly, this isn’t the whole picture. Scope 3 emissions contribute significantly to the embodied carbon of masonry products. However, in part, these emissions may already be mitigated in a process called recarbonation.
All cement and lime-based products naturally absorb CO2 from the atmosphere during their lifespan, acting as permanent carbon sinks during the use phase of a building and continue when it is pulled down and recycled.

Recarbonation of concrete is a wellestablished science and recognised by the IPCC in its Sixth Assessment Report 7 . A recent study from AAC Worldwide has helped to quantify the process, finding that aircrete products can absorb 77kg of CO 2 per m 3, with 80% of recarbonation achieved after 50 years and 95% within 80 years 8 .
All things considered; now is the time for a step change in the way the public sector thinks about ‘sustainable construction’, and it should reconsider masonry as just that.
Sources:
1https://ukparliament.shorthandstories. com/condition-of-social-housing-in-england/ index.html?utm_source=twitter&utm_ medium=tweet&utm_campaign=social-housing
2https://www.london.gov.uk/who-we-are/ what-london-assembly-does/questions-mayor/ find-an-answer/gla-housing-funding-buildingmaterials-2
3https://www.ft.com/content/cefe4c22-fc5d4ec8-8dbd-eca71fe041cf
4https://www.theguardian.com/society/2023/ feb/02/mould-damp-complaints-social-housingombudsman-tenants-landlords
5https://www.gov.uk/government/news/ plans-unveiled-to-decarbonise-uk-power-systemby-2035
6https://www.carbonbrief.org/ccc-heres-howthe-uk-can-get-reliable-zero-carbon-electricityby-2035/
7https://eaaca.org/wp-content/ uploads/2022/08/EAACA_Net-Zero-Roadmapfor-AAC_2022-08-12.pdf
8https://www.aac-worldwide.com/category/ science-innovation/co2-absorption-during-theuse-phase-of-autoclaved-aerated-concrete-byrecarbonation-2031