
5 minute read
MMC
from PSBJ May 2022
OFFSITE STAYS AHEAD OF THE GAME
The Government’s announcement of a ‘presumption in favour of offsite’ has helped the education sector increase the number of school places. Here, Jim Cowell, Technical Director at Elliott Offsite Solutions – soon to be Algeco – looks at some of the reasons why offsite construction of teaching spaces continues to gain favour.
Advertisement
There are signs that higher proportions of children are gaining places at their first choice of school, albeit there remains continued pressures in many areas. There are a number of reasons for this, although the Department for Education’s (DfE) push on building new teaching places using offsite has undoubtedly helped alleviate some of the issues. Encouragingly, the DfE has awarded over 20 contracts with an offsite element since the Government’s announcement. Of all the Government departments – housing, health, transport and defence – education has been the one to most fully embrace a presumption in favour of offsite, and for good reasons.
Compared to traditional construction, offsite techniques achieve a pre-manufactured value (PMV) of around 85%, whilst the work is completed in a quality-controlled factory environment, unaffected by the weather. This reduces the likelihood of the build being delayed by a shortage of skills on site or inclement weather conditions. It is a point not lost on many education providers where individual classrooms through to whole schools can be completed using offsite. Where required, this can be done within a schedule that fits around the school holiday window.
Other benefits of offsite include significantly less working at height because it is a more controlled environment. Likewise, there are fewer deliveries to site – good for the local community, less noise and safer roads. In a world where environment and sustainability feature heavily in decision making, modular and offsite builds result in significant less onsite waste compared to traditional builds.
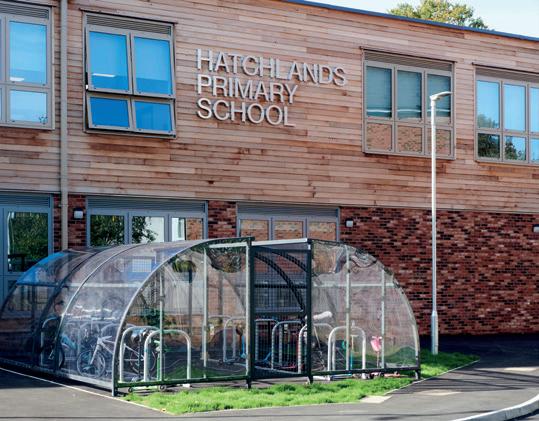
Hatchlands Primary School
A need for additional school places at Hatchlands Primary School in Redhill, Surrey, arose partly as a result of new residential developments and increasing birth rates in the area. The site is situated within an urban area where Reigate and Banstead Borough Council have a presumption in favour of sustainable development.
Planning requirements meant that making efficient use of space was a high priority on this development because the 420-place school had to be created on a similar footprint to the existing structure and within the same two-storey height restriction.
Construction of the completely new school at Hatchlands, in just 32 weeks, demonstrates the speed and versatility of permanent modular building systems on what was a complex, challenging urban brownfield site adjacent to a conservation area.
The turnkey scheme required demolition of the existing courthouse building and creation of a new, twostorey primary school using our modular system, along with parking and external landscaping. The development had to avoid being unduly prominent or detrimental to the character of the conservation area and surrounding residential community and neighbourhood.
The new school was funded by the DfE and operated by the Everychild Trust – a multiacademy trust, whose aim is to “engage, equip and empower every child”.
Development of Hatchland’s Primary School was part of the Modular-A Primary School component solution framework. Elliott was in first position on this framework, and we were awarded the first nine primary schools. Hatchlands Primary School was subsequently secured as a mini competition through this framework, along with River Mill Primary in Dartford. The Department for Education’s Modular-A covers whole primary school buildings.
Ultimately, we were awarded Hatchlands because we demonstrated value for money and an ability to provide a full turnkey solution including
demolition, externals and landscaping. As a permanent modular building system, the modules are delivered preassembled and ready for final finishing on site. This helped reduce the construction schedule at Hatchlands Primary School by around a half compared to a traditional onsite build.
The designer was DLA Architects, which worked with Elliott to develop a componentcentred solution that was based on the Elliott marketleading modular system. Hatchlands was designed in a contemporary style using brick, cedar cladding, purple panelling to complement the school’s branding, render and significant glazed elements to create lightfilled teaching spaces.
Working with DLA Architects, Elliott devoted considerable effort to siting of the building as well as its scale, height and form in order to satisfy planning and community requirements.
Height and scale of the structure was minimised by incorporating a flat-roof design, mitigating its impact on local views.
The completed school is indistinguishable to a traditional onsite build yet delivers all the benefits of offsite construction; a shorter 32-week build schedule, less site traffic, more consistent build quality and reduction of onsite waste.
Allonby House, located within the development’s footprint, was utilised as the school’s temporary facilities whilst the scheme was underway, meaning we were working within the vicinity of a live teaching environment.
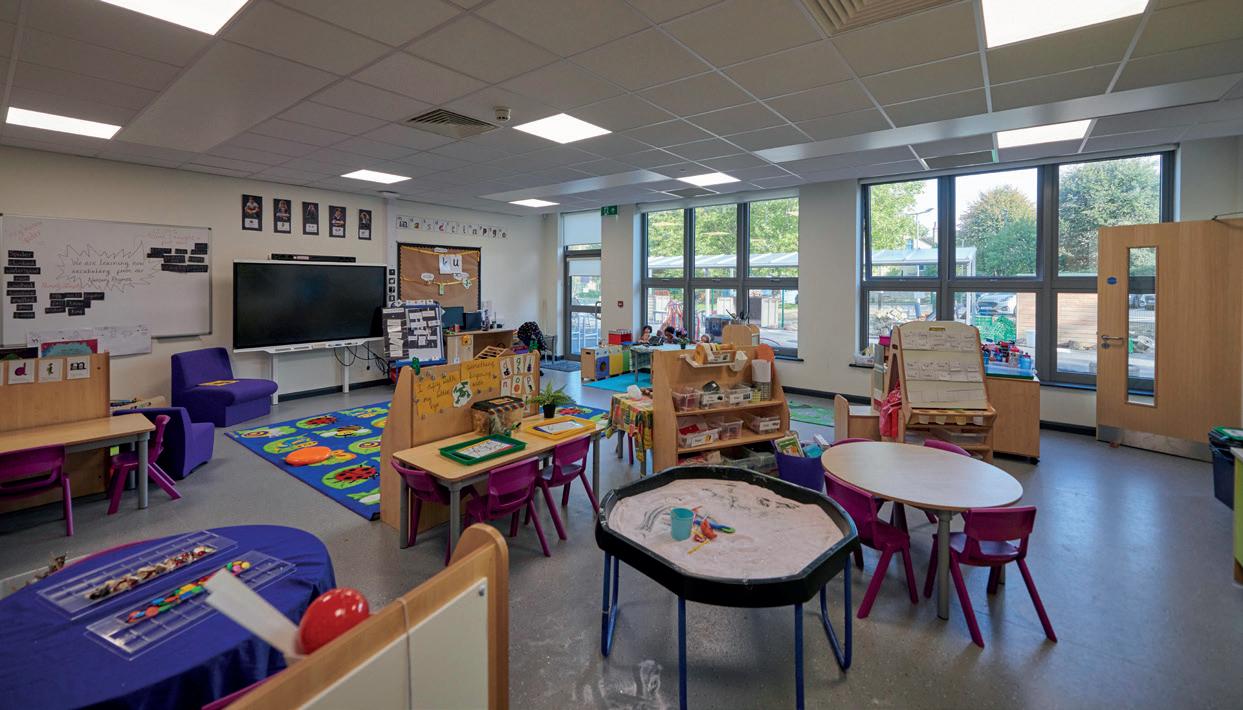
BREEAM ‘Very Good’
Construction of Hatchlands Primary School commenced on 2nd November 2020, with the school opening on 3rd June 2021 and achieved full completion on 14th August in time for the new term. Advancing to a stage of school opening in just 32 weeks demonstrates the speed, efficiency and build quality of modular systems.
The completed school was built to high sustainability standards and achieves a BREEAM ‘Very Good’ rating. This means it is within the top 25% of buildings in terms of sustainability, aligning with the goals of Reigate and Banstead Borough Council.
A large-span sports hall was created using our Hybrid system, providing the school with a valuable space that is now used for assemblies, sports and performances. The system allows incorporation of large, open atria and increased ceiling heights and can be fully integrated with the modules to provide greater design scope. The two-storey, flatroof school achieves a building massing that is sympathetic with the conservation area and avoids ‘overlooking‘ nearby residential properties.
The suspended concrete floor on the modular system helps minimise transmittance of noise, meeting minimum standards set out in The Building Bulletin 93 (BB 93) ‘Acoustic Design of Schools: A Design Guide’.
The modular system we used at Hatchlands is fully Building Regulation compliant with passive ventilation and has a 60-year design life as a minimum. Overall, the turnkey solution is considered to be one that balances design, scale and massing, resulting in an appropriate solution for the character of the area.
Once the development had been handed over, we were delighted with the comments. Moira Anderson, Headteacher at Hatchlands Primary School, said: “What a fabulous new school we now have! The children were really excited about moving into their new classroom and it is certainly very different to the temporary teaching areas we have been using. We were all really impressed with the professionalism and considerate approach of the Elliott team.” www.elliottuk.com
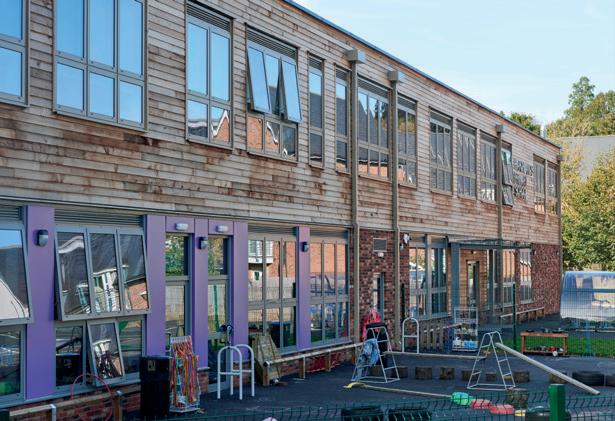