
1 minute read
FACILITY OPTIMIZATION AND ENERGY EFFICIENCY
Our shared distribution facilities strive to reduce the environmental impacts of their operations. Several facilities invested in lighting upgrades and improved internal process to optimize efficiency and reduce waste. Sustainability practices that maximize energy efficiency and reduce waste and cost are incorporated into all new facilities.
In 2021, we broke ground on a new distribution center at our Eudora, Arkansas campus. This new facility, built to modern energy-efficiency standards, was completed in 2022. In addition last year we undertook a significant expansion to upgrade our existing Eudora distribution center, originally established in 1962. The facility was updated with modern LED lighting with motion detectors, as well as a new heating and air system and conveyor and box retrieval cranes with low voltage controls, to replace outdated equipment and increase energy efficiency. Plans for additional facility upgrades were developed in 2021 and will be implemented in 2022 and future years.
At our Coppell, Texas facility, in addition to improvements to overall energy efficiency, we have implemented automation into the production environment using robots that lift products. These robotic manufacturing tools enhance our employees’ production efficiency and reduce distribution costs. Through these efforts, we continue to reduce and divert waste from landfills, reduce our energy consumption, and increase overall efficiency.
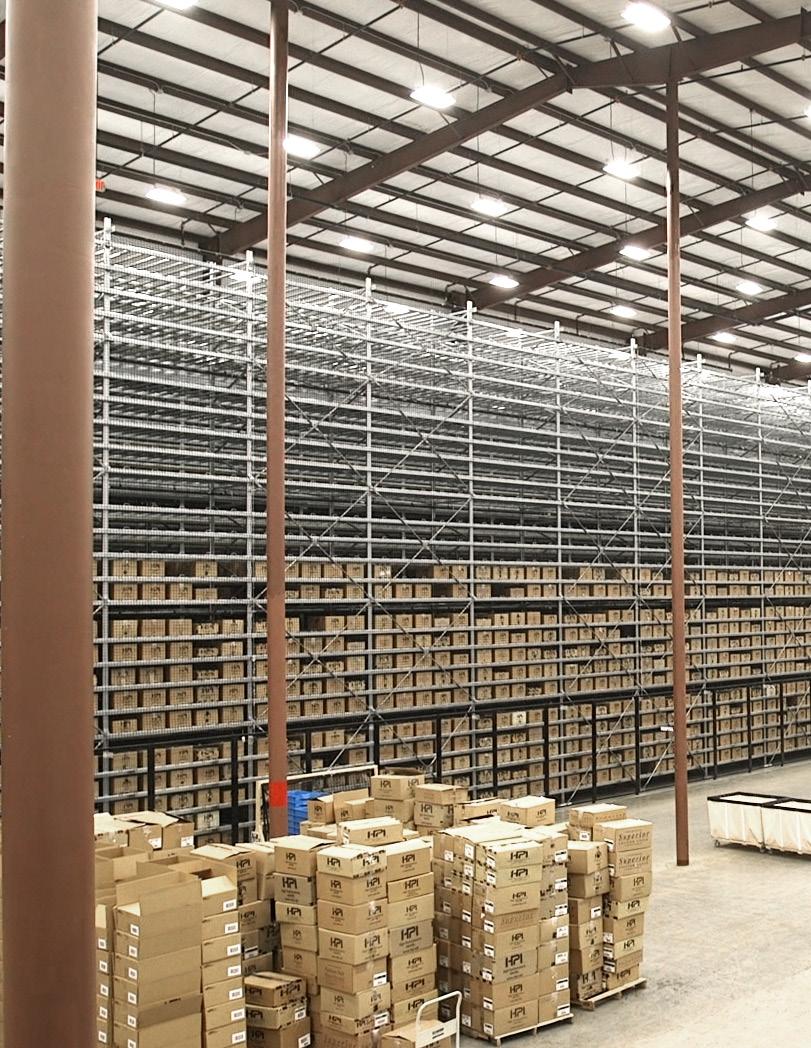
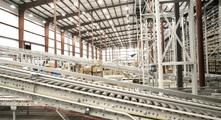
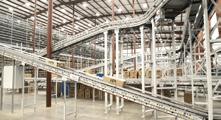
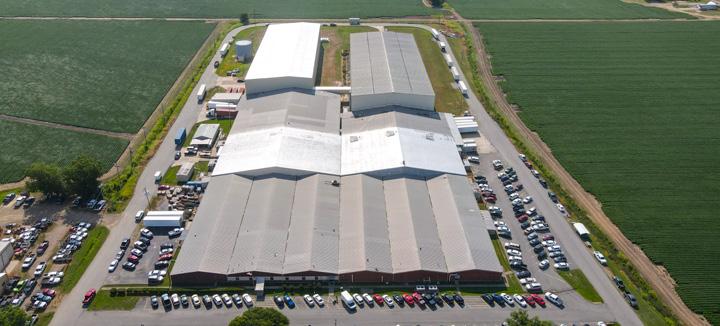