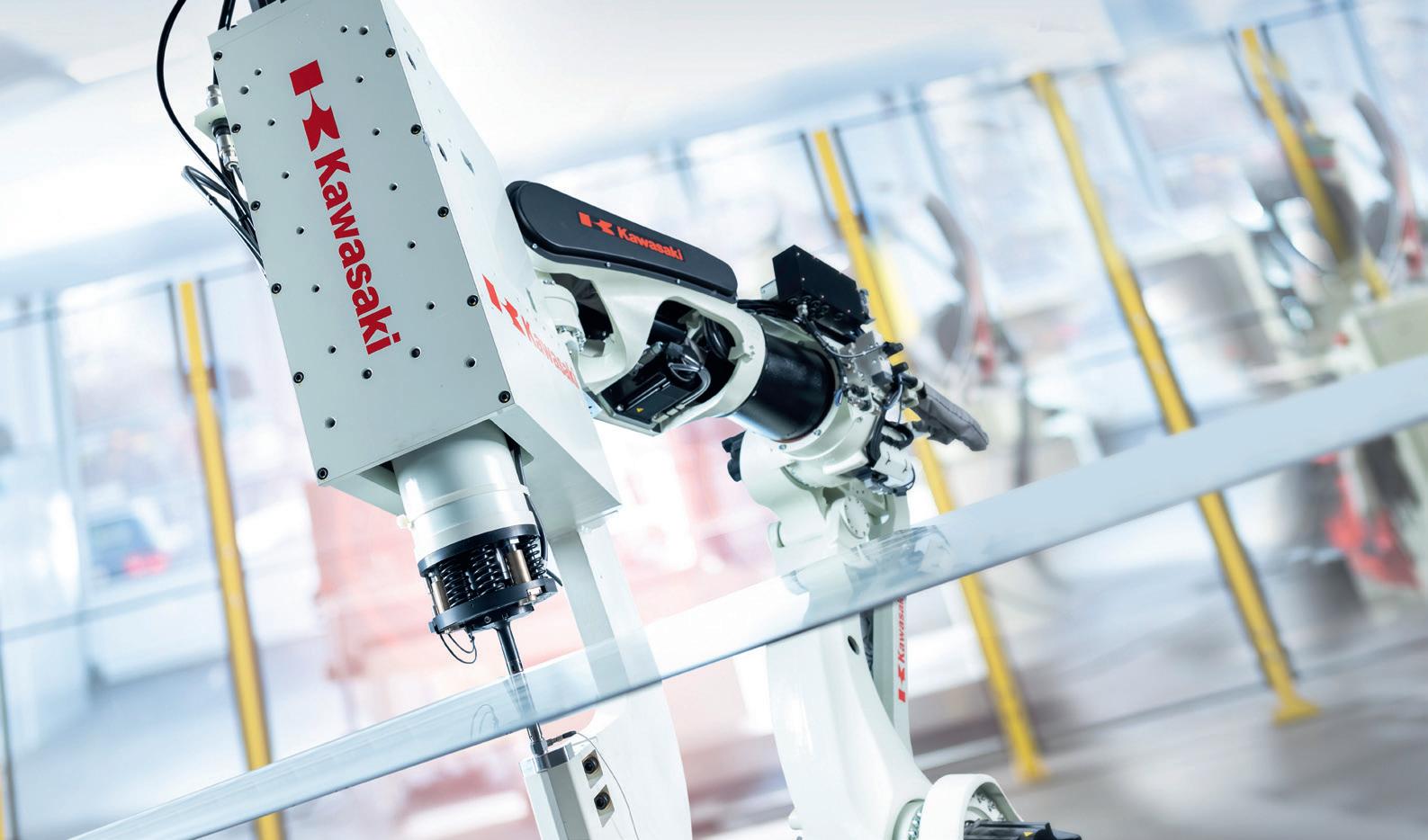
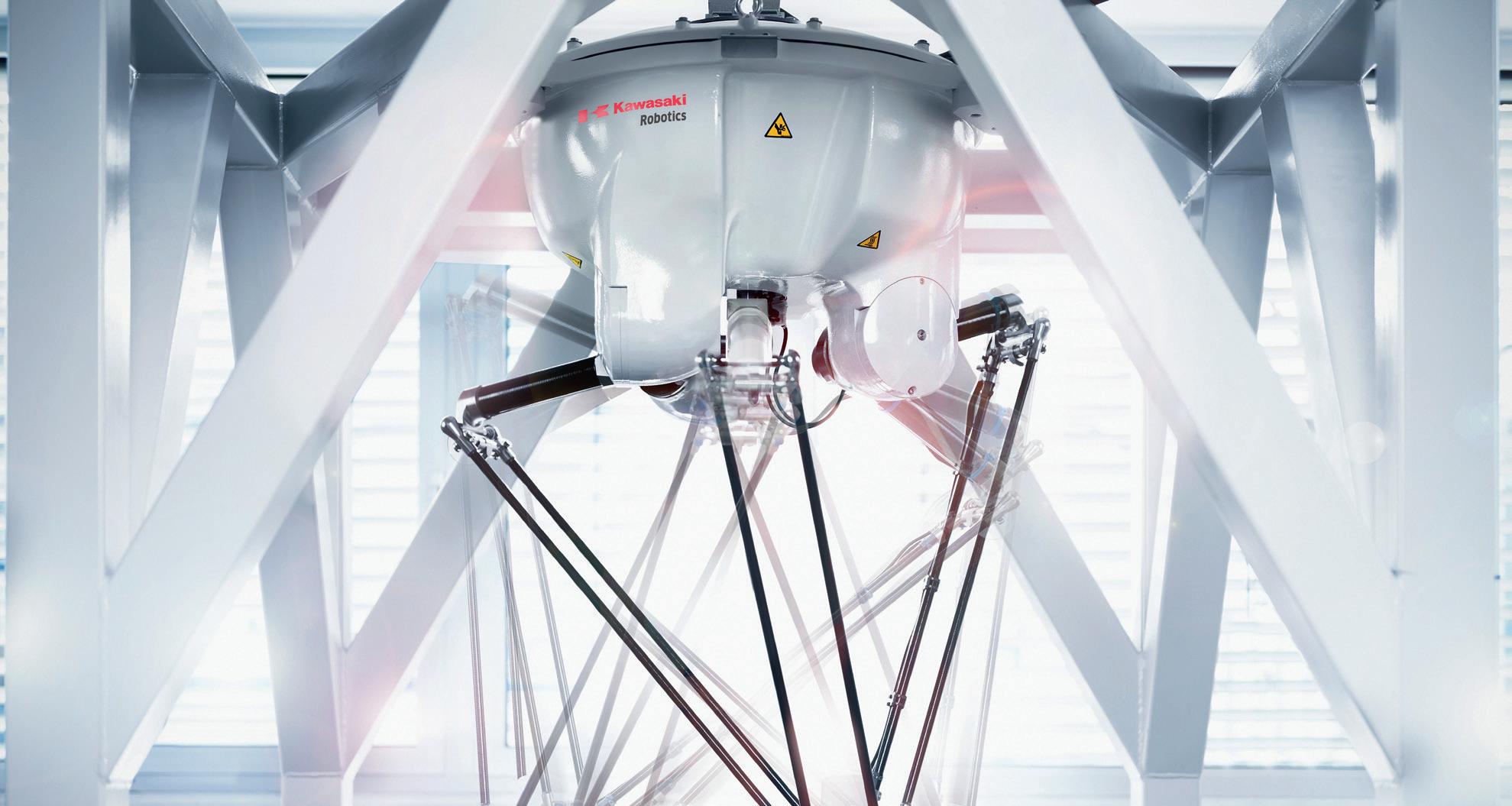
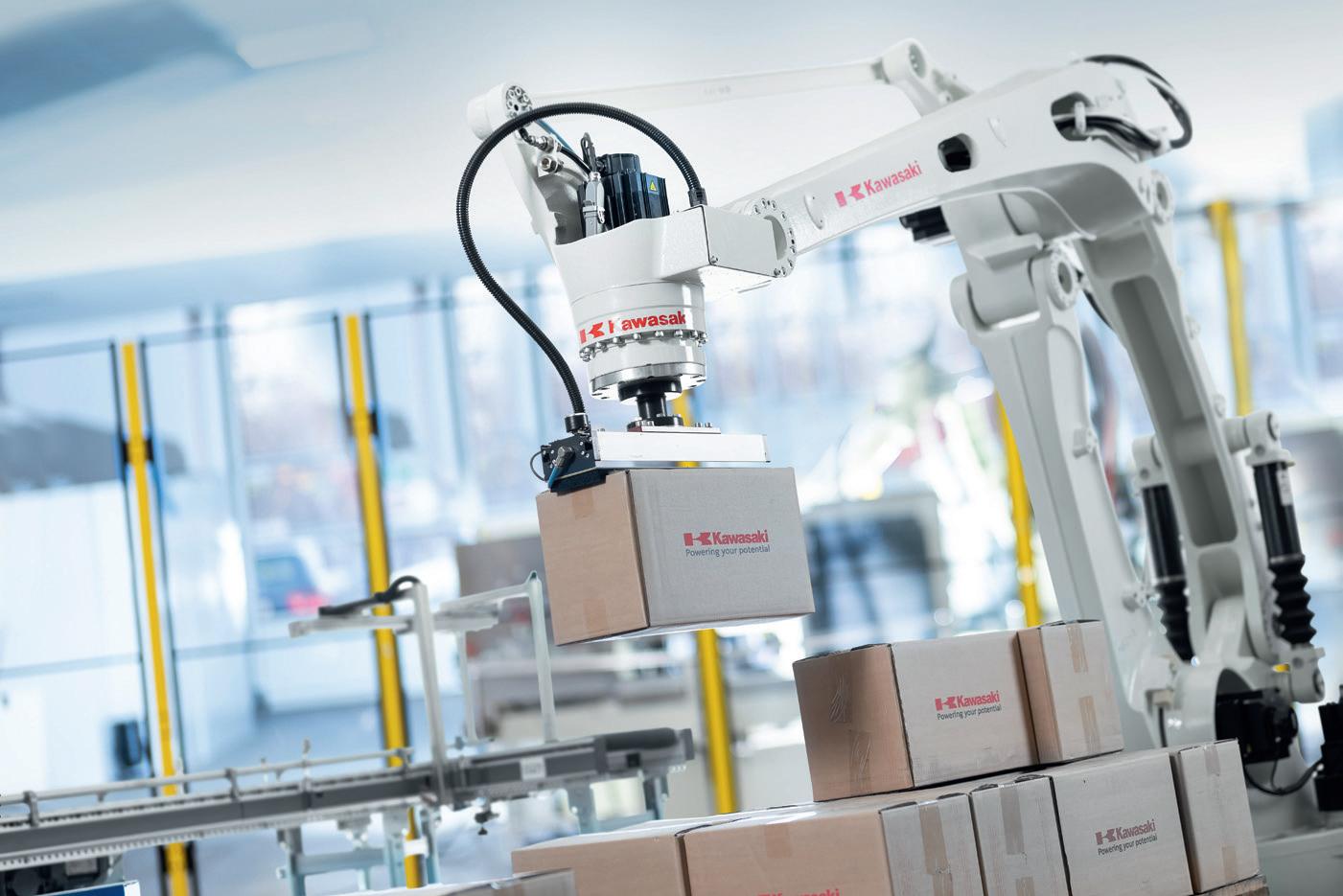
In a world of big data, our software simplifies its use.
From control systems for mobile machines to parameter setting for RFID read/write heads, we have software solutions that simplify your automation. We even have visualisation software for real time plant monitoring, from anywhere in the world.
Our software engineers remove the hassle of integrating automation solutions and ensure that you are getting all the usable data you can, providing actionable efficiency insights.
Chris Callander chrisc@cimltd.co.uk
Publication Manager
James Burke jb@cimltd.co.uk 01795 509115
Account Manager
James Davies jamesd@cimltd.co.uk 01795 509105
Design & Production
Grant Waters grant@cimltd.co.uk
James Taylor james@cimltd.co.uk
Administration Manager
Natalie Murray admin@cimltd.co.uk 01795 509103
Credit Facilities Manager
Gwen Lee creditcontrol@cimltd.co.uk 01795 509103
Marketing Manager
Lucas Payne lucas@cimltd.co.uk
Sales Director
Tom Woollin tom@cimltd.co.uk
Chief Executive
John Denning
So, the chancellor has delivered his last Spring Budget before a looming general election. As usual, moments after Jeremy Hunt stepped away from the dispatch box, my inbox started to fill with comments on his announcements from various organisations working in or with the manufacturing sector. The majority of comments welcomed those plans which affected the industry, although, as could be expected, accountants were looking for more tax breaks. But overall, it seemed the feeling was that while positive steps were taken, more could or should have been done for manufacturers.
It is clear that investment in UK manufacturing is needed. The UK has made strides towards embracing industrial automation but remains behind many of its global counterparts. In terms of robot density, the UK has traditionally lagged behind leading countries such as South Korea, Germany, and Japan. While historically, the UK’s wider investment in automation has been lower than its European neighbours and other industrialised nations.
The picture varies across manufacturing sectors. Substantial automation has occurred in the automotive industry, but other sectors, like food and beverage manufacturing, have been slower to adopt these technologies.
There are initiatives aimed at enhancing digital skills and supporting technological innovation, some of them very successfully. However, I believe the UK government, in partnership with private enterprises, should be offering more incentives for businesses to adopt advanced manufacturing technologies if the UK is to be competitive globally. And this absolutely has to be supported with skills-focused activities to equip the workforce with the necessary skills to thrive in an automated environment.
Whatever happens at the next general election, those in power must recognise and support this. And they must do so with real, meaningful action.
Enjoy the issue.
Automate UK CEO, Peter Williamson has been appointed as the new chair of the Make UK affiliate partner board. He will also represent the affiliate partner programme on Make UK’s national membership board.
Peter, who recently stepped down from his managing director role at RARUK Automation in order to focus on Automate UK, the association previously known as PPMA, is passionate about the need for the UK manufacturing sector to adopt more Automation, to empower small businesses, as well as upskilling and increasing the country’s workforce.
Peter said: “Being appointed to the Make UK affiliate partner board is a huge honour. Following on from the previous chair, Steve Brambley, who was a fantastic chair, will be a challenge but one that I welcome as we continue to be the voice of our industry.”
By welcoming Peter onto the board, the reach of both organisations has been extended to the benefit of all their members. Not only will communication between these sector leaders become smoother; they will be able to share ideas and best practices, not to mention access a wide base of resources.
Chris Corkan, Region Director –Midlands & East of England & Affiliate Partnerships at Make UK added: “I am delighted that Peter Williamson, CEO, Automate UK has accepted the role of Affiliate Partner Board Chair.”
Enginuity, the charity dedicated to supporting UK engineering and manufacturing employers by finding new ways to close skills gaps and open opportunities, is celebrating its 10th annual Skills Awards during Smart Manufacturing & Engineering Week on the 5 June at Birmingham’s NEC.
The awards recognise apprentices, pioneers of skills development, and innovative engineers who are passionately and diligently tackling some of society’s biggest challenges.
Each year, leaders from the engineering and manufacturing industry across the UK gather at Enginuity’s Skills Awards to celebrate the finest talent and commend the organisations dedicated to advancing skills development to ensure a bright future for these vital sectors in the UK economy. This year’s landmark 10th staging of the awards is no different, making Smart Manufacturing & Engineering Week an ideal backdrop for the celebration.
The Skills Awards offers an array of categories catering to various areas, ranging from the Equality, Diversity, & Inclusion award to distinctions like the Large and SME Employer Skills Champion awards and Training Partner Skills Champion award. In addition, the awards encompass specialised accolades tailored to individuals committed to enhancing their expertise in the field, such as the T Level Student award and multiple apprenticeship categories.
Pumping systems supplier Wilo UK has acquired Arfon Rewinds Limited in a move that further increases the company’s water management pump servicing capability.
The acquisition will enable Wilo UK to extend its service capability in key water management operations, including installation, repair, condition monitoring, and general pump maintenance.
Arfon has two workshops, one for dirty water pumps based in Bromborough and one for clean water pumps based in Caernarfon, with a team of circa 20 full-time engineers. The company is a major service and maintenance provider to industry in the North West of England and also numerous water utility companies, including Welsh Water and United Utilities. Arfon will continue to trade as a separate legal entity to support its existing customers and contracts, with Wilo UK having now purchased 100% of Arfon’s shares and assets.
Lee Tebbatt, Managing Director of Wilo UK, said the acquisition further strengthens Wilo UK’s servicing capability and aligns with an increased focus from customers on aftersales support and total cost of ownership.
“We already have a strong trading relationship with Arfon, which is a long-standing Wilo Service Partner. The opportunity to bring Arfon fully into the Wilo family was a good fit with our strategy of providing a full range of service capabilities across the installed pump base in the water utilities and industry sectors.
Siemens Digital Industries Software is highlighting opportunities for machine builders in the UK and Ireland to increase efficiency and boost productivity through digital transformation.
According to a benchmark report produced by the company, over twothirds of machine builders see increasing productivity and efficiency as the most significant challenge, yet 48% of companies have no strategy in place to begin their digital transformation.
“Digital transformation is coming, and it will profoundly alter the competitive landscape in the machine building industry, with smart technology greatly improving the efficiency of critical processes,” said Ben Sheath, VP and Managing Director, UK & Ireland, Siemens Digital Industries Software. “Machine builders who are digitally ready can respond to market trends and customer demands faster, better, and at a lower cost. The old objections of scalability and affordability no longer apply. Our technologies make it easy to bring production machinery online, to pilot a digitalisation initiative on a single machine and then scale across the full global
footprint of the enterprise. And the changes announced in the UK Spring Budget allow companies to write off the full cost of IT equipment, plant and machinery against taxable profits in the year of investment, instead of over the life of the asset. The firstmover advantages will be enormous. The time to act is now. And we’re here to help.”
Other highlights from Siemens’ industrial machinery benchmark report include the fact that a strategic focus on improving delivery speed and reducing time-to-market are respondents’ primary challenges.
A notably small 14% of respondents are very confident that they can measure the return on investment in digital technology and skills for their manufacturing processes and although 15% of respondents add value through the provision of remote maintenance, training and other services an alarming 48% claim to generate no value from services.
The full report can be accessed at www. siemens.co.uk/benchmark2023. Interested companies in the UK and Ireland can also benchmark their activities to their peers by taking part in the online survey and will receive feedback in the form of a personal benchmark by visiting bit.ly/SDISbench
SICK has unveiled what it believes to be the world’s first photoelectric sensor with a touchscreen display, heralding the future for universal and easy to set up sensing. The pioneering SICK W10 is a versatile all-in-one sensor that represents a major step forward in precise detection technology, adaptable for countless industrial automation applications.
The W10 photoelectric sensor’s swipe-up touchscreen technology and simple icons enable intuitive set up and teach in. The W10’s settings are pre-configured for rapid installation with common sensor functions, such as background or foreground suppression, available to select from a single device.
“It’s exciting to operate a sensor that feels as natural to use as a mobile phone,” explained David Hannaby, SICK’s UK Market Product Manager for Presence Detection.
“The touchscreen display is revolutionary. Just swipe up, select and configure. The
W10 guides you effortlessly through the operating modes needed for any installation. With just four product variants, choosing the sensor you need for your application has never been more straightforward.”
The SICK W10 is a photoelectric proximity sensor that uses intelligent onboard algorithms developed from the experience of common industry applications to achieve high repeatability across the board.
With an IP69K-rated stainless steel housing and eye-safe Class One visible red laser, the W10 adapts effortlessly to widespread uses in factory and logistics automation with built-in modes for standard, high-speed or precision operation. The robust W10 is just as resilient to harsh washdown environments as it is on fast-
moving production lines.
The W10 has a secure screen locking function and access restrictions can be set up to prevent unwanted changes to the sensor settings. The singlevalue teachin enables rapid configuration at a defined distance, while the two-value teach in enables objects of different heights to be detected without increasing the risk of errors.
The SICK W10 incorporates IO-Link connectivity so that sensor data can be shared with Industry 4.0 IoT systems, ideal for machine diagnostics and troubleshooting, as well as for edge configurations. IO-Link also provides the option of remote set-up and easy device replacement. www.sick.com
MyHARTING is a digital project platform which offers easy access to HARTING’s product data and technical information.
Users simply need to register for a free account to download and save premium content, including CAD files, technical data and whitepapers.
Visitors can also apply for an eShop account to check pricing and stock, place and track orders and manage delivery details.
Registration also gives users access to the Han Configurator, an online 3D tool which allows industrial connectors that meet exact requirements to be designed and built.
Users start by selecting three inputs (contacts, voltage and current) to generate the first possible solution. At each stage of the process, suggestions for alternative interfaces can be given, and the smart assistant feature will only allow valid configurations, avoiding numerous
combination options and saving valuable design time.
An onscreen 3D visualisation of the current configuration means users can view their creations from a range of angles. It’s also extremely easy to download all documentation (including STP files) with a single click and quickly save, load and share configurations within a team; an ideal solution if colleagues are working remotely or in a different location.
Tech Days (bit.ly/HTechDay ) are available digitally or in person to help users discover the latest in connectivity and cabling. The company’s field engineers will demonstrate and explain the latest technology, helping visitors plan out current or future projects.
bit.ly/myHAR
To create a larger-than-ever batch production mixer for a toothpaste manufacturer, advanced mixing solutions specialist EKATO had to thoroughly consider dosage and dispersion times, blend and homogenisation times, and vacuum values for the supersized design of a new toothpaste production system. NORD‘s task as the drive supplier was to configure gears and motors suited to the agitator and homogeniser specifications, with a view to high efficiency and durability.
As the agitator drives were to be installed on top of the production mixers, they also had to be kept as compact as possible, despite the extremely high performance expected of them.
UNIMIX systems consist of a vessel fitted with an agitator, a homogeniser, and various dispensing mechanisms for introducing ingredients into the process. Until recently, toothpaste batch production vessels were designed for no more than 4,000 to 5,000l. The two mixers newly engineered by EKATO hold roughly twice the volume of the largest previously available mixers, and the production system achieves at least three times the former maximum production output.
Homogeneous product quality is paramount in this application. That means the drive solution must be designed to respond quickly, unfailingly ensure continuity, and sustain the formidable forces on the agitator shaft owed to the mixture‘s high viscosity.
NORD DRIVESYSTEMS configured and supplied two motors delivering more than 150kW, with industrial gears providing nominal output torques of 242,000Nm.
NORD is the only manufacturer worldwide to produce industrial gear units as powerful as these in a single-piece cast design. Their impressive size notwithstanding, the type SK 15407 3-stage helical bevel gear units used in this process achieve a comparatively compact footprint. The one-piece housing ensures a highly reliable and leakproof construction, bearings accommodating greater torques, high resilience against axial and radial strain, low maintenance needs and a long service life. www.nord.com
Motor and drive specialist MOONS’ Industries has announced the launch of Moons’ Industries (UK) based in Reading, Berkshire. This development is the latest chapter of a journey that started nearly 30 years ago, and which the company says is building on a commitment to solving problems and meeting the needs of its customers. Shanghai-based MOONS’ Industries manufactures an extensive range of motion control products from facilities in Asia, North America and Europe.
Founded in 1994, MOONS is a global top-three manufacturer with a yearly shipment of more than 30 million motors of all types, including 10 million hybrid stepper motors. MOONS’ is acknowledged for developing high-quality motion control products and offers a range that includes over 12 types of motors and actuators, with a focus on developing innovative slotless and coreless motors.
The company’s choice of slotless brushless
DC motors includes 11 types of winding, with the ø16mm series of slotless BLDC motors available in short, long and XL versions with three different power outputs, while the latest MICRO options include slotless motor, gearbox, encoder, driver, and mechanical components.
Coreless Brushed DC motors, which provide excellent performance and are easier to control, are available in six diameters: 8mm, 10mm, 13mm, 16mm, 17mm, and 24mm. Their innovative hollow rotor design enables rapid acceleration combined with low rotational inertia, no cogging, and no iron loss, and they are housed in a compact and light package. When coupled with a gearbox, they can deliver high torque, while the encoder can be used for precise positioning applications.
product performance, improving reliability and at lower cost. With so many types of DC motors available – permanent magnet steppers, hybrid steppers, brushless DC, step servos and slotless motors – it’s tricky to know which one to choose.
MOONS’ says it understands that choosing the correct motor for a motion control application can significantly impact
However, MOONS’ believes that the combination of its extensive product range, advanced technology, and a ‘customer-first’ focus, will help UK customers to optimise the performance of their systems.
www.moonsindustries.com
The guiding theme of this year’s Hannover Messe is ‘Energizing a sustainable industry’. In line with this, the Schmersal Group will showcase new products and systems for the safe, efficient, and sustainable design of machinery and plants. With innovative safety and automation solutions, Schmersal supports companies in their digital transformation and in complying with high environmental and energy standards.
Other focus topics at Schmersal’s booth (stand D09, hall 09) will be future-proof solutions for safe food production and intralogistics.
With Schmersal’s IIoT solution, data and information can be captured in production and sent to the back office for real-time analysis. The basis of the IIoT solution is the field level, which includes networked sensors and actuators as well as safety switchgear devices. The Schmersal Cloud Solution acts as a link between the field and back
office levels. The aim is to boost the efficiency of machinery and systems with condition monitoring, predictive maintenance and the calculation of key performance indicators (KPIs).
The AZM40 solenoid interlock has a compact design and requires little space. It also has a high locking force. Schmersal will showcase new variants at Hannover Messe 2024, including escape and emergency release for enhanced user safety. The addition of the IP69 degree of protection now opens up additional potential uses. The user also benefits from reduced energy consumption with the AZM40: thanks to the bistable operating principle of the clamping device, more than 50 % of the power consumption can be saved compared to monostable locking devices.
food processing. The focus of development for the series was the requirements of hygienic design. The devices contribute to hygiene in production and thus to food safety and the health of end consumers.
The H series from Schmersal will be showcased at Hannover Messe 2024 as a full range of new command and signalling devices for hygiene-sensitive applications, particularly
The devices feature high-quality plastics for the operating surfaces, as well as stainless steel front rings, thus making them more resistant to dirt and aggressive cleaning agents and characterising their durability in the long term. Long-term use also contributes to energy savings and resource conservation.
www.schmersal.com
Cost efficient entry into automation with the LBR iisy cobot range.
Unlock hidden potential and read
between the lines of efficiency with the LBR iisy range from KUKA.
T: 0121 505 9970
E: sales.uk@kuka.com
As research carried out by the association shows that environmental, social and governance activities are an increasing focus in manufacturer’s boardrooms, Stephen Phipson, CEO of the manufacturer’s association Make UK, believes that companies who get ahead of the game will gain a competitive advantage.
The topic of environmental, social and governance (ESG) is in the spotlight for several reasons at the moment. Not only is it one of the biggest trends in financial markets, attracting hundreds of billions of pounds as investors try to do well by doing good, but it is also attracting the attention of the Government, which is looking to legislate on rating agencies that have been accused of inflating the green credentials of companies to attract investment. Make UK’s latest survey with Lloyds Bank shows that ESG is also rapidly rising up the boardroom agenda of manufacturers. According to the survey, firms said the reasons behind this increase include increasing pressures from the labour market, government, investors and customers.
A quarter of companies have responsibility for ESG at board level while a similar number have their executive reward linked to ESG performance. Furthermore, the survey shows that threequarters of companies are now including ESG conditions in their procurement strategies, a significant increase since the last survey three years ago. This shows that for many companies, this is not a ‘nice to have’ option but a cast iron pre-requisite for doing business, and for those companies unable to comply, there is a risk they will be
shut out of supply chains or have to accept discounted prices or margins to simply do business.
However, the flipside is that those companies who are ahead of the game will have a competitive advantage. This is a critical factor because the survey shows that almost half of companies, presumably the majority being SMEs, feel they do not
have the resources required to achieve the conditions set by their customers. This highlights the need for greater support for those companies as only one in four companies (27%) being asked to meet ESG requirements by their customers are getting the support to do so. Furthermore, while one third of manufacturers provide ESG support to their suppliers, firms are two and a half times more likely to provide support to suppliers in pursuit of ESG targets than they are to receive it from customers.
And the ESG requirements being stipulated are now moving beyond the traditional and expected conditions in areas such as health & safety and employment conditions into areas such as carbon emissions human slavery and biodiversity, for example wildlife habitats. Given the strains on supply chains for companies from the pandemic, the invasion of Ukraine, and the energy price shock, these increasing requirements are presenting yet another challenge for companies but one they will simply have to meet. It’s now clear that those companies who are already ahead of the game and responding to their customers will be in pole position should the Government ever get to the position where the demands of consumers and other stakeholders make mandated ESG legislation necessary.
Euchner MGB2 with safety over EtherCAT and PROFISAFE
• Modular design with submodules
• Up to six MGB2 on one bus module
• Easy to expand
• Submodule replacement in operation
• For doors hinged on the right as well as on the left
George Thompson, Chairman of BARA, the British Automation & Robot Association, outlines some of the ways automated end-of-line solutions can bring relatively easy to achieve benefits to manufacturing businesses.
In a recent article, I mentioned the relatively quick wins available from end-of-line solutions. Perhaps I should elaborate more on how this could work in a typical manufacturing environment. I have toured countless facilities in my career, and I could often see several opportunities to eliminate manual handling by introducing relatively simple automation. In some, I could see more complex solutions that would completely revolutionise their production.
If I use a typical food processing company as an example. In that case, ingredients are moved around the facility in either wheeled totes or perhaps using a manual pallet mover, where the products are manually depalletised. If we look at this first step, there are risks associated with the pushing/pulling of the product tote or pallet coupled with the bending, twisting, and lifting element of the depalletising—assuming the products are in a suitable container for a single-person lift, of course.
Another quick win is case packing, especially if this is coupled with a case or box erector and a box closer. Of course, not all boxes are created equal. However, most box styles can be loaded into an erector or closer.
Case packing is another relatively easy win for most companies. The operators who put products into boxes, generally speaking, do not add any value to this process or the product. I know it is a necessity, but it would be far better to use automation to pack the cases and use the operators to conduct more value-added operations within the business.
In an ideal world, the transfer of product to the area for depalletising could easily be accomplished using an autonomous mobile robot (AMR) or automated guided vehicle (AGV) to transfer the product, which would eliminate the risk of the push/pull action used in the manual operation. The AMR/ AGV could automatically load the pallet or tote into the depalletising cell, which could then load the ingredients into the appropriate machine. If this is a bagged item, there are existing solutions that are used in injection moulding machine loading applications that
could easily be modified to depalletise, cut and decant the bags and deposit the empty bag into a bin, shredder, or compactor ready for recycling. The AMR/AGV could collect the completed bale on the return journey as part of its overall mission schedule.
The decanted product would then be dosed into the production cycle in a measured and controlled manner to ensure the recipe is followed precisely.
If we assume that the AMR/AGV doesn’t always pick a recycling bale, which it wouldn’t, perhaps on the return journey it could collect a completed pallet or trolley of product to be taken to goods out. Before we get to that stage, there are several areas that could also be automated relatively easily.
The next stage is end-ofline (EoL) palletising, where we have manual handling concerns similar to those with depalletising. Regardless of what type of EoL solution you pick, and there are numerous options, they will undoubtedly be more efficient than manually stacking pallets. Before the AMR/ AGV collects the pallets, why not use an automatic pallet wrapper to ensure the pallets are secured and protected for transport? By the way, on average, an automatic pallet wrapper will use 30% less wrap when compared to typical manual application of stretch film. This is good for the bottom line and better for the environment.
If you would like to start your automation journey but don’t know where to start, I highly recommend visiting the BARA website (www.bara.org.uk), where we have outlined several topics under the expert advice section to give you some initial information.
8-pole bayonet locking
> 5000 mating cycles
Panel mount parts unplugged IP67
Solder and dip solder contacts
www.binder-connector.co.uk
With its double-walled underground storage tanks, German company Haase Group has been a market leader in the tank industry for over 50 years and relies on a unique combination of traditional manual work and modern automation technology. MEPCA found out how, in 2010, the company decided to enhance its tank finishing process using Kawasaki robots and safety software.
Haase was an early adopter of robotics, installing its first robot in 1991. This upgrade brought a noticeable relief for the company, so it continued down the automation path. As time went on and the robots grew older, maintenance and servicing became increasingly difficult. When it was no longer possible to guarantee reliable procurement of spare parts in the long term, it knew it was time to upgrade.
A central challenge in the construction and operation of the plant was the considerable amount of dirt and dust produced during processing. Because of this, a robot arm suitable for a dusty environment and a controller that didn’t require constant cleaning were needed.
Haase installed the Kawasaki ZT130S robot to spray glass fibre-reinforced plastic (GRP) onto the double-walled cellar and underground storage tanks during the finishing process. The robot is shelf-mounted next to a turntable where the parts are fixed, making applying an even coat of GRP easy.
The ZT130S robot provides the payload (130kg) and a horizontal/vertical reach (3,230mm/4,571mm) needed for this application. However, its wide working range and high precision capabilities make it perfect for the spraying process specifically. The robot can process single or multiple lids and bases in series, offering maximum flexibility and efficiency.
Due to the robot’s success, Haase added a Kawasaki BX100L robot to the production site to apply resin and glass fibres to a mould. The company added another ZT130L for working lids and bottoms with the automatic tool change system. This system provides it with the flexibility to manufacture approximately 100 different tank types as needed.
After interacting with the robot supplier at the Automatica trade show, Jürgen Krell, Technical Director at Haase, decided to go with Kawasaki Robotics. “For us, the attractive price, the robust design and the specific but precisely fitting requirement profile of the robot were the deciding factors,” explained Jürgen. “With a proven Kawasaki partner in the neighbouring town, the available service was also excellent for us. And the technical support provided by Kawasaki itself has quickly proven to be particularly reliable and flexible.”
A suction system ensures continuous and effective dirt extraction during the finishing process, removing 60% of airborne dirt. The robots run on Kawasaki’s E series controller, which only needs weekly cleaning for optimal performance.
Haase also developed and built a special tool change station. This allows the robot to efficiently switch between four different finishing tools. The shelf-mounted ZT130L robot is not dependent on special tools. It uses commercially available machines, such as a milling tool to prepare the tank’s manhole and an angle grinder to prepare the tank surface for lamination and further processing. The robot also uses two saws for precise cutting and grinding and a suction attachment for cleaning lids and bases.
A light barrier effectively protects the robot’s working area in combination with the Kawasaki Cubic-S safety system. Cubic-S
ensures that robots and workers can work together safely and without hesitation. The software enables the installation of particularly space-saving applications and security areas without complex external security measures. Cubic-S combines eight safety functions – including the individual definition and precise limitation of the available working space. The robot cannot exceed the specified working range limits at any time.
For this safety system to work, each axis of the robot must be electronically monitored. Predefined axis values form the limits of possible movements. If the system exceeds a predefined speed, engages previously stopped axes, or tools leave their intended orientation, Cubic-S automatically switches off the robot.
Once Haase decided to automate, it quickly restructured its plant. In less than three months, the new robot integration was completed. Since then, Haase has also successfully automated all spraying stations in production.
kawasakirobotics.com/uk
Kawasaki Robotics
Tel:+44-1925-713-000
www.kawasakirobotics.com/uk/
Flexible, modular range of high efficiency, robust gearboxes with output torques up to 250kNm.
Available on short delivery times, same
Dust zone 21 cat 2D and zone 22 cat 3D
Gas zone 1 cat 2G and zone 2 cat 3G IEC Ex, EAC Ex, CCC Ex, UKEX and specifications for North American market
MEPCA explores the latest topics relevant to industrial sensors and sensing systems
New technologies make providing accurate and reliable level sensing in hygienic applications easier than ever. There are, however, still important decisions to be made, as Andy Walker of ifm electronic explains.
Accurately and reliably monitoring and controlling levels in tanks and other vessels is a common requirement in the food, beverage, and pharmaceutical industries. There are many ways this can be achieved, but in these industries where absolute freedom from the risk of product contamination is a prime requirement, two technologies are now dominant: hydrostatic measurement and non-contact radar sensing. These technologies operate in very different ways, and each has its own set of benefits, which is important to consider when deciding on the best option for a particular application.
Hydrostatic level measurement is the more traditional option and uses a pressure sensor to determine the level. The sensor is located at the bottom of the vessel, and as the level of liquid in the vessel increases, so does the pressure the liquid exerts on the sensor. Therefore, provided that the density of the liquid is fairly constant and the shape of the vessel is properly considered, the liquid level can be calculated from the pressure measured by the sensor.
This approach can work very well and has the benefits of being relatively inexpensive and producing results that are largely unaffected by the presence of foam on the surface of the liquid or from mixing agitation. Nevertheless, it also has limitations, the biggest being changing media density as the sensor is generally calibrated to a single media/density and vessels with either dished or coned ends.
For example, the calculation relating pressure to level can be slightly more complicated and may require linearisation to provide the best accuracy for a continuous level measurement. In all applications, the
sensor is dynamically calibrated in situ to allow for the characteristics of the vessel and the density of the media. Hydrostatic level measurement can also be used if the vessel is pressurised or subjected to vacuum. But requires a second sensor to measure the top pressure, either positive or vacuum.
A final consideration, which is particularly significant in hygienic applications, is that the sensor comes into direct contact with the media, which shouldn’t present too much of a problem, as completely flush mounting pressure/level sensors, specifically designed for hygienic applications, are now readily available, and allow easy and complete cleaning via CIP/SIP. Despite this, some users have a strong preference for noncontact measurement as this minimises the risk of contamination and allows for quick and easy removal should it be required.
Fortunately, non-contact sensing is one of
the key benefits of radar level measurement, which uses FMCW (frequency-modulated continuous wave) technology.
With this, the sensor, which is mounted above the surface of the liquid, continuously sends out a microwave signal that, in the latest versions, rapidly varies in frequency from 77 to 81GHz. This signal is reflected from the surface of the liquid and returns to the sensor, but because the frequency of the transmitted signal is changing rapidly, there is a frequency difference between the transmitted and received signals. The sensor uses this difference, which is directly related to the time it takes the signal to travel to the surface of the liquid and back, to calculate the distance between the sensor and the liquid.
In addition to offering totally non-contact operation, radar sensors have many other benefits. They can work over long ranges and deliver very high accuracy – millimetre accuracy at a range of 10m is easily
achieved. They are unaffected by changing temperature or density of the media and are also unaffected in applications where the vessel is under positive or vacuum pressure. They can also be installed or removed without emptying the vessel as they are fitted above the surface of the liquid, unlike hydrostatic sensors, which need to be at the bottom of the liquid. In fact, radar sensors can often be installed above the vessel, rather than inside, in applications where vessels are constructed of plastic, such as IBC containers or chemical storage tanks.
Radar sensors clearly offer an extensive range of benefits, many of which are particularly attractive in hygienic applications, but are they always the best option?
Sometimes they are not because, like every other type of sensor, they have limitations.
Although they are unaffected by the presence of steam, vapours or condensation, radar sensors work less well with foaming media. Also, the microwave signal sent out by the sensor will only be reflected if the liquid has a dielectric constant ≥ 2. In practice, radar sensors will operate reliably with any liquid having a dielectric
constant greater than two and, in many cases, liquids with a slightly lower dielectric constant, but this does depend on the sensing range and other details of the application.
A final consideration relating to radar sensors is cost as, although prices have fallen significantly in recent times, they are still more expensive than the single sensors used for hydrostatic level measurement in vented vessels. In some applications, the extra cost is well worth paying for the benefits radar level sensors offer, and in others, the cost difference may be less than it may first appear. Radar sensors, for example, can provide continuous level information, where a single radar sensor can often provide a level measurement that would need two or more hydrostatic sensors in pressurised applications. Radar sensors are also now very easy to configure, and the reduction in commissioning time translates into cost savings.
it is hoped, make it easier for those involved with the specification of equipment for hygienic process plant to choose the best type of level sensor for their applications. In many cases, the latest radar sensors will represent the ‘gold standard’, but there are still instances where hydrostatic level measurement provides an economical and effective solution.
The information provided in this article will,
Reelliable, , eaassy y to usee, innddiccaattoors, , tootaalliisseers, , battcch controllleers s and d flow--coompputerrs Forsafeandhazardousareas
www.ifm.com
MACHINE VISION CAMERAS FOR AUTOMATION AND QUALITY INSPECTION APPLICATIONS
Scantoview thefullrange
ukflowtechnik.com
+44(0)1159017111 Seeusat onstallE56
sales@ukflowtechnik.com
For measurement, inspection and barcode verification, our cameras, lighting and software solutions prov ide the answers.
ALRAD supplies Multispectral and Hyperspectral v ision systems for ultrav iolet (UV), v isible and infrared (NIR / SWIR) wavelengths.
Do you need to monitor ‘Hot Spots’ for process control or maintenance ? Our Thermal Vision systems give you the hidden picture.
For Vision Engineers and System Integrators we prov ide a complete range of diagnostic tools and a full portfolio of machine v ision components
Tel: +44 (0)1635 937000
Email: sales@alrad.co.uk
Web:www.alrad.com
Liquid flow measuring specialist, Titan Enterprises, explains how its precision liquid flow measurement solutions support innovation and diversification in the oil, gas and energy industries.
The pressure towards sustainability is pushing the oil, gas and energy sectors to evolve innovative and diverse solutions in a move to create an energy efficient future.
Major transformations within the oil and gas industry in the form of adopting sustainable practices, developing new revenue streams and pushing the boundaries of technology, are being trialled and delivering success. Expanding into new areas such as renewable energy, advanced chemicals and biofuels, is driving innovation and diversification.
Titan Enterprises provides OEM customers in the oil, petrochemical and green energy sectors with optimised and custom-designed liquid flow measurement solutions. These have included bespoke oval gear flow meters for marine fuel flow measurement, monitoring the volume of grease lubricating wind turbine bearing mechanisms, high pressure intrinsically safe units for offshore oil drilling additive injection, and for biodiesel plants converting bio waste into sustainable biofuels.
One of the fundamental requirements for ensuring reliable and efficient wind turbine operation is to keep the heavily loaded main bearings fully lubricated in all operating conditions. Fully IP65/NEMA 4 compliant, Titan’s compact oval gear (OG) flowmeters are optimised for measuring the flow of viscous liquids. Designed to operate at pressures of up to 700 bar and temperatures up to 150°C, and with a standard flow range of 0.01 to 4.0l/min on 30Cstk oil, the OG1 or OG2 models can routinely achieve outstanding accuracy (0.75%) and repeatability (0.1%).
Titan’s OG flow meters are also an intrinsic component within Green Fuels’ biodiesel plants converting bio waste into sustainable biofuels. Green Fuels’ award-winning research and pioneering process plants have powered buildings with sustainable fuel from used cooking oil, with ongoing development to convert fish oil and sewage sludge into biofuel. Simple, accurate, and chemically resistant, Titan’s OG flow meters, with the addition of the NAMUR switch, have proved to be the ideal solution for precise chemical dosing within a potentially hazardous environment for Green Fuels’ biofuel plants.
Titan Enterprises offers special options and adaptive designs of its OG flow sensors to meet specific high-pressure requirements, aid chemical compatibility, and ensure safe operation in potentially explosive atmospheres. Titan’s OG range includes ATEX-compliant IP65/NEMA 4 protection models and devices that offer intrinsically safe options for processes that operate within harsh environmental conditions, such as explosive or corrosive atmospheres, where flowmeters are required to withstand tough environments whilst maintaining accurate
and reliable measurement.
The pivotal role of oval gear flow meters lies in controlling precise liquid dosage for efficient and economical process operations. Within the petrochemical sector, a chemical injection system employs accurate low-flow measuring sensors to inject a precision dosage of chemicals required, including antifoaming scale inhibitors and methanol, into oil wells. Accurate chemical dosing is essential for the optimal functioning of the well system, promoting efficiency and heightened productivity without excessive costs. OG flowmeters are critical in preventing overdosing that can lead to unnecessary expenses, or under-dosing that may trigger premature maintenance and suboptimal well performance.
For measuring high viscosity liquids like thick oils, bitumen and tar, precisionengineered flow meters are necessary. Titan’s standard OG flowmeters are designed to provide highly accurate flow measurement up to 1000cSt. For viscosities above 1000cSt, Titan provides high viscosity OG options specially designed with profiled gears to facilitate additional flow of the liquid and prevent hydraulic lock.
flowmeters.co.uk
When selecting an in-process system for measuring the thickness of film, plate or sheet materials, a number of challenges need to be considered, including sensor alignment, linearity and the effects of thermal changes, as Glenn Wedgbrow, Business Development Manager at Micro-Epsilon UK, explains.
There are many reasons why we need to measure thickness. All materials have a tolerance in production, so any materials that are too thin or too thick could cause a problem further down the line or at the end customer’s site. Changes in thickness during production can indicate wear of components, for example, in extrusion dies or on rolling stands. Monitoring trends can point to early warning signs.
The traditional method of checking thickness is often to take a measurement sample from the start of the production run and then again at the end. But what happened in the middle? If you find the material is out of tolerance, that’s a lot of scrap to consider. So, you might choose to take more readings during the process. If these checks are being done manually, they often require the production line to stop. Most process variability will come in the ‘start’ and ‘stop’ phases, so keeping a line running is generally key to improving consistency. Ultimately, checking the product thickness as it’s produced ensures that the end customer receives the quality of product expected.
Target material types and the production processes used all have a bearing on how the thickness of a product can be measured. Sometimes, it is based on the setting of a gap on a roller or adjustment of dies in an extrusion head. It could be liquid poured and cured, such as glass, rubber or metal. It could also be part of a secondary process where the basic material is already produced but is then combined with similar or differing materials as multiple layers or even woven strands that are then bonded, such as carbon fibre.
Let’s now consider some of the challenges of measuring thickness.
Perhaps the simplest thickness measurement is a single-sided measurement against a reference or datum surface. First, the sensor is zeroed on the datum surface, and the target to be measured is inserted. The reading of the sensor is changed or displaced by the material thickness. There are a number of uncertainties with this method. If the reference or datum moves after mastering, the reading will be incorrect. Similarly, if the target does not sit correctly on the datum surface, the air gap will also be included in the measurement. The same
issue can also occur with tilted targets. If we are only allowed to view a target from one side, we must consider if we can combine technologies to enable accurate measurements. Where we have a mix of different material types, we can utilise those different material properties to our advantage. For example, an eddy current sensor, in combination with a laser triangulation sensor, can be used to measure sprayed skin thickness. The eddy current sensor measures the distance to the nickelcoated spray mould and has an opening in the centre through which the laser sensor measures the distance to the sprayed part. Eddy current sensors only measure against metallic targets and, therefore, see straight through the non-metallic sprayed coating.
Certain fumes pose significant risks to human health, potentially leading to ailments like liver damage, kidney damage, brain damage, lung cancer, and, in extreme instances, fatalities.
Our expertise in fume and dust control makes us the ideal partner for managing hazardous substances at their source. Our industrial vacuums are versatile and can be used for various applications such as wood dust (ATEX rated), plasma cutting, laser cutting, 3D printing, chemical labs, metal grinding, and welding.
With Extractability you can breathe easy knowing your safety is at the heart of our products from our mobile fume extractors to our fitted systems.
The Health and Safety Executive estimates that 1.6 million workers are potentially at risk from not using local exhaust ventilation to control the airborne hazards.*
To book your free site survey call +44 (0)345
or email sales@extractability.eu
The use of an air coil in eddy current sensors from Micro-Epsilon makes this combination possible, as the laser sensor can look through the eddy current sensor at the same measuring point. When both signals are subtracted, the thickness of the applied sprayed skin is measured.
Another well used sensor combination is achieved with eddy current and capacitive sensors for non-metallic materials passing over a roller. Movement of the metal roller is considered by the eddy current sensor, and the capacitive sensor measures the material or coating thickness.
If the target is transparent, it is possible to make an absolute measurement of the material thickness from one side using only one sensor with interferometer or confocal technology.
The use of light refraction creates ‘edges’ or return signals that indicate the transition between the air and the material. Knowing the refractive index of a material enables the accurate measurement of the material thickness provided it stays within the measurement or working range of the sensor.
If single-sided measurement is not suitable or the challenges cannot be overcome, in many cases, customers want to know the true material thickness by measuring the material in ‘free space’, which requires having space on both sides of the material so that a measurement can be taken from both surfaces.
When you consider this set up, there are a number of challenges that must be considered and either overcome or accepted.
The sensors must be positioned so that the measuring spots coincide ‘through’ the full measurement range of the sensor. There should be no offset, tilt or inclination of the sensors in relation to the measurement object. For example, with a sensor offset of 1mm and inclination of 2°, the effective error equals 35µm, and at 10mm, the target thickness increases to 41µm.
Particularly with laser triangulation sensors, the location of the beam spot to the sensor housing should be noted. It should not be assumed that two apparently identical sensors will position the spot in the same place. Standard sensor housings are not usually precise enough for precision
thickness measurements unless time is taken to align them correctly. To help customers make their own thickness set ups, the ILD1900 sensor from MicroEpsilon uses an innovative sleeve mounting arrangement to tighten the spot spacing from housing to housing.
When you have two sensors looking at the same target, you must consider that each sensor has its own cycle time. If your target is vibrating or moving in the gap between the sensors, then it’s very easy to introduce an error. Consider a target oscillating up and down by 1mm at 20Hz (times a second). A difference in capture time of 1ms between your sensors would equate to an error of 125µm.
The next challenge is the relative position of the sensors and their measurement ranges.
Depending on how the sensors are arranged, the position of the target edges must stay within the measuring field. If the sensors are set so that the measuring zones do not overlap, then situations can arise where one sensor may not see the target. Consideration should also be given to process ‘start’ and ‘stop’ conditions; for example, is the material held in tension at all times? Speed changes in the line can induce upward or downward movement. Is the setup able to capture these events if needed? Ideally, the sensor ranges should overlap and cover the full range of material movement or at least control the movement.
The accuracy of a sensor is often referred to as its linearity. The linearity value describes the deviation from the ideal, straight characteristic curve. Each measurement sensor has its own measurement
uncertainty or non-linearity. This means that at any given point in the measuring range, the actual reading from a sensor can vary by a percentage of its measuring range. So, taking just two sensors without any additional processing means that both sensors’ uncertainties need to be considered with respect to the accuracy looking to be achieved. For example, without adjustment, just moving a target 200 microns up or down can result in errors of 8 microns. The position in the range also has the potential to affect the true value. To solve this, the sensors must be calibrated together as a whole.
Even when the sensors have been aligned and synchronised, there is still a further challenge that can affect everything –thermal changes. When measuring a target thickness in free space, the gap between the sensor and the opposite sensor is critical, as this is the constant on which the differential measurement is based. Taking a mechanical frame with a pair of sensors and cycling the temperature shows that the effective change with just a 5°C swing is up to 20 microns.
The final challenge – if the previous ones have been overcome or the errors associated have been accepted – is to prove the capability. Exactly how do you check or confirm the performance of your solution? There are two factors to consider here: the system repeatability, i.e. how much variability in the measurement system is caused by the measurement device, and reproducibility –how much variability is caused by different operators.
www.micro-epsilon.co.uk
We have the solution.
Position. Transport . Rotate
Industrial operators must embrace under-utilised IO-Link technology to enhance visibility of asset health, according to Milesh Patel, a Supplier Manager, Automation & Control, for RS UK & Ireland.
In any industrial environment, having a real-time accurate picture of asset health to keep operations moving and minimise downtime is a necessity, not a luxury. Sensors have long been used to help engineers identify potential issues, and the launch of IO-Link more than a decade ago greatly enhanced the capabilities and functionality of sensor technology by unlocking previously inaccessible sensor status information. This helps operators reduce maintenance costs and increase equipment uptime.
In the 15 years since its launch, IO-Link has duly progressed and become a standard sensor feature, but whether it is being adequately utilised by OEMs and machine builders is questionable: some may argue it isn’t being optimised in the field. IO-Link technology holds many benefits, but there are perceived barriers to this technology becoming truly mature.
IO-Link enables fast maintenance: the last metre between the field level of automation and the sensor/actuator level becomes capable of communication. This enhances the ‘normal’ capabilities of sensors from being able to simply highlight process variables, to making identification information, parameters and status of the device available. The capability to take information from sensors, self-diagnose and convey it back to the control system facilitates higher levels of predictive over preventative maintenance, increasing uptime.
The real beauty of the technology lies in the ability to utilise existing wiring. It transmits information via the sensor or actuator’s three-wire connection, making it invisible to the system and, therefore, not affecting basic sensor operations in any way. Diagnostics information can be sent
over the same line as the process data. Other benefits include reduced documentation or expert knowledge requirements thanks to the fact that device parameters are stored in the host automation system and can be automatically downloaded.
The IO-Link protocol was launched in 2009, followed by the publication of the IEC 61131-9, Single-drop digital communication interface (SDCI) for small sensors and actuators standard in 2013. The technology standard is managed by the industry association Profibus and Profinet International.
Since the 2009 launch, the number of member companies committing to the standard has grown from 41 to more than 400 in 2024.
It is estimated that during 2024 there will be over 40 million active IO-Link nodes in the field. This illustrates the technology’s growth from being a niche addition to high end sensors from sensing technology pioneers, to becoming a standard feature on many sensors and actuators, supported by a host of gateways and networking devices.
Choice may once have been considered a barrier to IO-Link adoption, but the range of IO-Link enabled sensors and actuators is bigger than ever, with virtually every global automation brand now a member of the community and adding IO-Link options into their offering. And while the cost could be
another perceived barrier – around five years ago, there was a significant premium for IO-Link capability – this situation has evolved with lower cost and entry-level sensors coming to market offering the technology. Distributors are also starting to offer their own-brand IO-Link enabled sensors: RS offers them within the RS PRO offer.
The issue of complexity has also put many off implementing IO-Link, but the tools, interface hardware and software extensions to install IO-Link are now commonplace. It’s easier than ever to implement into existing PLC or control system code, allowing existing designs to be simply upgraded to benefit from IO-Link.
Given these perceived barriers, it’s understandable that adoption of IO-Link isn’t as prolific as it should be. But it’s high time these barriers were broken down, to enable all operators to reap the rewards of embracing this technology. With the gold standard of efficiency in industrial operations being based firmly on a robust predictive maintenance strategy, those who ignore the full capabilities of IO-Link should do so at their peril.
uk.rs-online.com
In the complex symphony of industrial processes, there exists a vital but often overlooked element: the industrial gas flow meter. These unsung heroes ensure efficient, safe, and precise operation across various sectors, from chemical manufacturing to food and beverage production. Understanding their role and the diverse technologies employed is crucial for appreciating their significance.
At their core, industrial gas flow meters measure the rate at which gas flows through a pipe or conduit.
This seemingly simple function underpins a multitude of critical tasks. They optimise resource utilisation by preventing gas waste, leading to cost savings and reduced environmental impact. Additionally, they play a vital role in process control within various industries. In chemical plants, for instance, accurate flow measurement is essential for maintaining the correct ratios of reactants and ensuring product consistency and quality.
The landscape of industrial gas flow meters is diverse, offering a range of technologies catering to specific needs.
Here are some prominent examples:
• Mechanical positive displacement meters: These meters physically trap and release discrete volumes of gas, providing a direct measurement of flow rate. They are known for their simplicity and robustness, making them suitable for various industrial applications.
• Thermal mass flow meters: These meters measure the thermal conductivity of the gas, which is directly proportional to its mass flow rate. Their accuracy is less affected by pressure and temperature fluctuations compared to other types of meters.
• Coriolis mass flow meters: Utilising the Coriolis effect, these meters measure the mass flow rate of a gas by analysing the twisting motion imparted to vibrating tubes as the gas flows through them. They offer exceptional accuracy and are independent of pressure and temperature variations, making them ideal for demanding applications.
The selection of the appropriate flow
meter technology depends on various factors, including the type of gas being measured, the required flow rate range, desired accuracy, operating pressure and temperature, and cost considerations. For instance, in applications involving highly corrosive gases, special materials and designs are necessary to ensure meter longevity and safety.
Beyond their core function of measuring flow rate, modern industrial gas flow meters often offer additional functionalities. They can be equipped with data logging capabilities, allowing for process monitoring and analysis. Additionally, they can be integrated with control systems, enabling real-time adjustments to optimise gas usage and ensure process stability.
The future of industrial gas flow meters is driven by advancements in technology and increasing demands for efficiency and sustainability. The integration of Internet of Things (IoT) technology holds immense potential. By connecting flow meters to networks, valuable data can be collected and analysed in real-time, enabling predictive maintenance and remote monitoring. Additionally, the development of microfluidic technology promises miniaturised and cost-effective flow meters for wider applications.
In conclusion, industrial gas flow meters, despite their understated presence, are instrumental in ensuring the smooth operation of various industries. By providing accurate and reliable flow measurement, they contribute to efficient resource
utilisation, product quality control, and environmental sustainability. As technology continues to evolve, these unsung heroes will become even more sophisticated and integrated, playing an ever-increasing role in shaping the future of industrial processes.
www.icenta.co.uk
A leading specialty chemicals company aimed to transform its operations by enabling real-time data access and enhancing collaborative capabilities to boost operational efficiency. MEPCA discovered how using Cyzag’s no-code platform empowered the company to achieve this, implementing it across eight sites in Asia, Europe, and North America.
Streamlining operations and enhancing process analytics is a common hurdle many companies face. A leading chemical company was facing the challenges of dismantling entrenched data silos and seamlessly integrating new use cases to boost asset performance and reduce manufacturing costs. Traditionally, these efforts required significant time, money, and change management due to the reliance on fragmented digital tools, Excel spreadsheets, and paper-based processes.
The company’s selection criteria for a partner focused on functionality, user experience, IT robustness, integration capabilities, and operator engagement. Cyzag stood out for its adaptable, usercentric platform that consolidates various data streams into one workspace, leveraging a web-based, no-code approach for developing use cases.
The no-code strategy empowers citizen developers to mobilise operational improvements. It allows plant engineers and improvement experts without coding skills to quickly create, test, and deploy directly into operators daily routines. As a result, Cyzag speeds up innovation and simplifies daily operations integration, reducing extensive change management and delivering instant benefits. Process operators can also contribute, further promoting the platform’s value and operational integration.
The company initiated a proof-of-concept project at one of its sites. Within three weeks, the first version of the Cyzag platform was delivered to the shop floor, while the total deployment took eight weeks. Encouraged by the success, the full implementation began across seven sites in six countries.
The active participation of the central team and plant staff in developing solutions alongside citizen developers and Cyzag’s dual emphasis on work process improvement and process analytics facilitated the transition towards optimised operations. The impacts included the following:
Work processes
improvements: Work processes have been streamlined and standardised, simplifying management across plants and integrating key practices like shift logbooks and performance meetings. Operators now use an intuitive interface for routine organisation and task management, enhancing efficiency and managerial workflow. This has also improved communication between shifts and encouraged problem-solving.
The pilot showed a notable efficiency gain with two hours saved per shift.
Leveraging process analytics: Citizen developers’ ability to create custom use cases allowed plants to adapt processes for their unique requirements. The no-code platform’s synergy outperformed isolated tools, enabling quick solution prototyping, testing, and integration into daily workflows, facilitating sustainable improvements.
A specific initiative at one site targeting reduced variable costs saved €150k annually on steam, demonstrating the impact of a robust tool paired with a proactive and engaged team.
Motivated by this success, the company plans to roll out a shared variable costoptimisation use case across all sites, promoting a culture where innovation is routine and improvements are readily
adopted and built upon, driving operational excellence.
The Cyzag platform’s implementation transformed the chemical company’s manufacturing, streamlining operations and boosting efficiency. It democratised data, enabling informed decisions and sustainable improvements. Users across disciplines without programming skills could speed up innovation, driving cost savings.
A single, versatile tool supporting operational efficiency and process analytics offers more benefits than two or more separate tools. Having different tools complicates operators’ adoption of new use cases. Conversely, consolidating everything into one tool makes new use cases almost transparent to operators, fostering their engagement and the sustainability of the solutions.
Cyzag’s emphasis on adaptability and people nurtured a continuous improvement and innovation culture, essential for cost reduction and asset optimisation, which are critical pressure points for all manufacturers today.
www.cyzag.com
https://www.murrelektronik.uk/gb/highlights/ mq15-power-connector/
Donal Bourke, Sales Director at maintenance and asset management software specialist PEMAC, explains how mobile Computerised Maintenance Management Systems (CMMS) are becoming a critical part of modern manufacturing.
The intersection of technology and traditional manufacturing practices through the integration of mobile Computerised Maintenance Management Systems (CMMS) applications heralds a new era of operational efficiency and productivity. This leap forward is not just a matter of adopting new tools; it represents a fundamental shift in how maintenance operations are conducted, offering a beacon for industries striving towards digital transformation.
Historically, maintenance operations have been bogged down by manual processes and paper-based systems that are prone to errors, inefficiencies, and delays. The shift to digital, initiated by the advent of CMMS, laid the groundwork for a more streamlined approach, automating workflows and centralising data. The subsequent evolution into CMMS mobile applications enabled maintenance teams to access critical information and perform tasks in real-time, directly from the plant floor or field.
The ripple effects of implementing CMMS mobile applications are profound. At the heart of its benefits is the empowerment of maintenance teams with instant access to data, such as work orders, asset information, and inventory levels, enabling informed decision-making and rapid response to issues. This real-time capability significantly reduces downtime and improves the reliability and longevity of critical assets.
Moreover, mobile CMMS applications facilitate a proactive maintenance strategy, shifting away from the reactive ‘fix it when it breaks’ approach to preventive and even predictive maintenance. Through features such as predictive maintenance alerts and scheduled inspections, maintenance teams can anticipate issues before they escalate, minimising unplanned downtime and extending the life of equipment. This strategic shift not only saves costs but also improves overall plant efficiency and productivity.
The adoption of mobile CMMS also plays a pivotal role in compliance and safety management. With stringent regulatory requirements across industries, having accessible, accurate, and up-to-date maintenance records and safety information is crucial. Mobile CMMS applications ensure that all maintenance activities, safety tasks and documentation are logged and can be easily retrieved for audits.
Implementing mobile CMMS, however, is not without its challenges. It necessitates a cultural shift within organisations, from top management down to the maintenance teams. Training and change management are essential to ensure that all stakeholders understand the benefits and are proficient in using the new mobile tools. Additionally, integration with existing enterprise systems should be considered to ensure seamless data flow and maximise the utility of real-time information and performance insights.
As we look towards the future, emerging technologies such as the Industrial Internet of Things, Artificial Intelligence, and Machine Learning promise to further enhance the capabilities of mobile CMMS, making predictive maintenance even more accurate and efficient. This ongoing evolution underscores the importance of flexibility and adaptability in maintenance strategies, ensuring that organisations can leverage new technologies as they emerge.
Recently, CMMS vendors have begun to develop advancements in mobile CMMS applications’ offline functionality, allowing operations in low- or no-bandwidth areas. Verdantix, Buyer’s Guide: Computerised
Maintenance Management Systems (2023), August 2023, research highlights this as a crucial differentiator, predicting it will become standard in five years. PEMAC’s mobile application exemplifies this by allowing maintenance teams to download work for offline completion, synchronising and updating once a connection is re-established. This development highlights the innovative approaches being adopted to optimise maintenance operations and improve overall operational resilience and efficiency.
In essence, mobile CMMS applications are transforming manufacturing maintenance, driving efficiencies, enhancing strategic maintenance planning, and ensuring compliance and safety. This transformation is a testament to the power of digitalisation in the manufacturing sector, offering a glimpse into a future where technology and traditional manufacturing practices converge to create more resilient, efficient, and competitive businesses. As technology continues to advance, the role of mobile CMMS in manufacturing maintenance will only grow, solidifying its place as a critical component of modern manufacturing operations.
pemac.com
A manufacturer of custom moulded cable assemblies for the global medical and military markets has seen both compliance and productivity increase after employing the WorkfloPlus digital workflow platform from connected workforce specialist Intoware.
Carrio Cabling Corporation, based in Colorado Springs, USA, had been looking for new ways to identify assembly line bottlenecks and deliver a clear audit trail to satisfy regulatory requirements.
The company wanted to reduce wasted time due to frequent and often lengthy changeovers between multiple operations.
It needed to digitise its paper processes to achieve this, but its team was initially hesitant about moving away from existing ways of working – a common issue that many organisations face on their digital transformation journey.
Through its market research, Carrio came across Intoware’s WorkfloPlus – a mobile technology platform that enables businesses to digitise processes and tasks across industrial operations, converting them from paper to be accessible via mobile, wearable technology and desktop devices.
The technology could be used through tablets on the factory floor to help streamline Carrio’s manufacturing processes, and so the company signed up for a trial.
Miles Carrio, senior manager at Carrio Cabling Corporation, said: “Initially, our assemblers were hesitant to accept any change in their existing approach, but they quickly found using WorkfloPlus to have major benefits over the paper-based processes.”
At Carrio Cabling, 28 assemblers are working on several customer orders at any one time, and it’s common for one assembler to change between multiple operations within a particular assembly several times a day, each with its own procedures.
Because of this, it was expected to take between nine and 12 months to fully train all of Carrio’s operators on the technology and to deploy WorkfloPlus throughout the business.
However, the team took to the technology quickly and half of the assemblers were trained and using the software platform in just six weeks.
Miles added: “We quickly found that WorkfloPlus automatically compiles data faster and with greater accuracy than if our assemblers were to manually log this data themselves. Since we have thousands of lines that we can build, seeing how quickly we could digitise was key; depending on the complexity, we can migrate and digitise an assembly in just 20 to 90 minutes.”
Previously, one large paper document was shared for each assembly line at Carrio, risking the document getting lost or being subject to unauthorised modifications. Now, every assembler has a tablet, with all paperbased build procedures on the factory floor now replaced by digital workflows using WorkfloPlus.
Digitising paper-based processes has also allowed Carrio Cabling to access and analyse a wealth of data in real time. This means managers can generate hourly data reports and compare and contrast individual assembler rates to improve efficiency and prevent future production bottlenecks.
The company has also found that it ensures a thorough audit trail to satisfy both customer and regulatory needs –something crucial to Carrio Cabling as an ISO manufacturer.
Miles continued: “Before, an individual employee would gather information to track the rate of production and what assemblers had built. Automating this work in real-time simply pales in comparison to what we’d pay an operator to complete the same work, plus we wouldn’t get the information as quickly to then be able to act on it as required.”
Keith Tilley, CEO at Intoware, said: “Carrio Cabling is a great example of a manufacturing company that recognised the need to move away from paper-based processes to digital alternatives and is now reaping the benefits.
“As the business found, it is common for frontline workers to be initially hesitant about digitalisation, but when rolled out correctly and with the right training and induction provided, it can enhance productivity and make workers’ jobs much easier when it comes to audit trails and compliance.”
www.intoware.com
Industrial communication specialist, Brainboxes, explains how its Power-over-Ethernet enabled Gigabit Ethernet switches are supporting critical vision systems used in biomanufacturing facilities.
Biomanufacturing, often referred to as biotech, is a manufacturing process that utilises biological systems, such as living cells or microorganisms, to produce commercially valuable products. Commonly employed in the production of medicines, vaccines, enzymes, biofuels, and a wide range of bioproducts, biotech offers a sustainable and effcient method for large-scale production with applications in pharmaceuticals, healthcare, food and beverage processing, and various industrial sectors.
For one leading biotech company, vision systems are employed for critical tasks such as inspecting products for defects, verifying assembly processes and ensuring overall product quality. The integration of vision systems within the company’s facility enhances the capabilities of its machines, allowing them to ‘see’ and respond to the environment, ultimately improving production accuracy and reducing the need for manual intervention.
The biotech manufacturer’s vision systems, essential for stringent quality control and adherence to regulatory requirements, involve multiple cameras, sensors, and other devices distributed across a vast facility. Brainboxes’ newly developed range of Power over Ethernet (PoE) Gigabit Ethernet switches was pivotal to the system, providing the necessary network infrastructure to support communication between the various components and serving as a central connectivity hub.
Managing data transmission and power distribution for the numerous cameras and sensors distributed across the production floor became a logistical challenge. The automatic PoE negotiation and centralised power management offered by the PoE Gigabit Ethernet Brainboxes simplified the installation by allowing the transmission of both data and power over a single Ethernet cable, ensuring seamless and effcient operation.
The Gigabit Ethernet speed of the switches proved instrumental, facilitating
rapid data transmission crucial for real-time decision-making in the biotech manufacturing environment. Simple integration with image processing applications significantly elevated the manufacturer’s ability to maintain the highest quality standards in their production processes.
PoE Gigabit Ethernet switches at the core of the vision system, the biotech manufacturer witnessed a substantial improvement in operational effciency. The once complex network of cables on the production floor transformed into a streamlined system, whilst the scalability of the switch range will accommodate future growth, enabling the integration of additional devices without disrupting existing infrastructure.
Managing power for multiple devices leads to increased installation challenges and maintenance efforts. Brainboxes PoE Gigabit switches, with their automatic PoE negotiation and centralised power management, offer a solution that simplifies installations. This not only addresses power management complexities but also streamlines the overall installation and maintenance processes.
Cluttered setups, multiple plugs, and frequent maintenance checks (including EICR and PAT tests) are common issues in the manufacturing environment. The switches eliminate the need for numerous AC adapters and reduce the points of failure. Designed for easy integration, Brainboxes’ switches also ensure compatibility with various components and systems, resulting not just in enhanced connectivity but a cleaner, more effcient infrastructure.
Balancing the need for advanced features and capabilities with budget constraints is a perpetual challenge. Brainboxes PoE Gigabit Ethernet switches are a cost-effective solution, providing the necessary features without compromising on performance, aligning with the biotech manufacturer’s commitment to effciency within budget constraints.
System downtime can significantly impact overall operational effciency. Effcient power management not only ensures streamlined installations but also actively works to reduce downtime. This reliability becomes a key factor in maintaining the continuous operation of the vision system, contributing to the overall effciency of the vision systems.
For the biotech company, vision systems play a crucial role in various tasks, and the deployment of PoE Gigabit Ethernet switches has significantly improved the effciency of these systems. Addressing the challenges of power management complexity, infrastructure clutter, budget constraints, and system reliability, Brainboxes’ switches have become integral to optimising and maintaining continuous operations and contributing to the overall reliability and effciency of the vision systems.
www.brainboxes.com
FactorySmart AI provides a turnkey solution to help you leverage the power of AI in your factory. We tackle data collection, pipeline training and development, user interface design and factory communication. Once deployed, we continue to maintain and optimize the system to ensure your return on investment is fully realized.
Mondelez has chosen Festo electric drive technology for a new automated chocolate Easter egg mixing installation at its site in Herentals, Belgium.
The egg mixing line at the Mondelez facility uses an ingenious system of conveyors to ensure that everyone finds a nice mix of flavours in their pack of chocolate eggs at Easter. Electric drives were chosen over pneumatics because they offer lower energy consumption, higher safety and more flexibility in controlling speeds and positions.
Mondelez is a large, international player in the food industry with many renowned brands in its portfolio, such as Côte d’Or, Milka and Oreo. The Ergomix project was instigated to support the production of Easter eggs, with the objective of improving ergonomics for operators. Egg production runs practically all year round in order to have enough stock at Easter to meet seasonal demand. In the past, eggs were mixed by manually putting together trays of different flavours, which was labour-intensive.
In the new facility, this process has been fully automated.
Once the eggs come off the forming line and are individually packed, they go via a conveyor belt to the new plant, where they are initially sorted into large pallet bins by flavour. These trays are then prepared via a robot either for mixing or to be picked up by a mobile robot for temporary storage in a warehouse. Once all the necessary flavours for making a mix are ready, the eggs are transported via funnels to precise positions on a wide conveyor so that all the flavours are lined up next to each other. At the end, the eggs re-enter a pallet bin where the different flavours are perfectly mixed.
The first challenge in terms of drive technology was to ensure that the eggs are neatly distributed when filling the pallet bins. Otherwise, they would not be level, which
would make stacking the bins impossible. The second challenge was positioning the hoppers over the conveyor on which the mix is assembled. This required a flexible system because not every mix contains the same number of different flavours. Finally, a suitable drive also had to be found for the gripper on the robot, which moves the 150kg pallet bins.
“Our starting point for this project was not to use pneumatics,” said Bob Aerts of the Engineering Department at Mondelez. “The reasoning was that electric drives score better in terms of energy consumption, and it is also easier to implement all aspects of machine safety. We presented this to Festo and they not only understood our starting point and the applications we wanted to build, but were also able to offer all the components needed to make it all happen.”
The design of the new plant was undertaken by Betecem, with Koen
Roobaert, Application Engineer at Festo, advising on the component selection. Alax Automation was responsible for the programming.
The new Ergomix installation is located in an air-conditioned room and operates fully automatically. To fill the pallet bins evenly, the system has been designed so that the conveyor belt feeding the eggs can be moved left and right via two timing belt shafts equipped with a servo motor and torsion shaft. An electric cylinder with spindle in the extension of the conveyor belt means it can also be extended forwards and backwards. This combination means the system can position itself to drop eggs at any position in the pallet bin. The controller receives feedback from the weighing cells under the bin and the flow rate of the supply so that it can determine exactly where in the bin there is still room.
The positioning of the hoppers above the wide belt for mixing was also realised with electric axes. They allow the positions to be automatically adjusted to the number
Our products are designed around three key concepts: protection, comfort and design. Each of our solutions is challenged by our research and development experts. This allows us to offer more advanced and differentiating solutions.
of flavours which need to be brought together in a given mix. Also, the gripper on the robot that moves the pallet boxes was equipped with a Festo ESBF electric cylinder with a servo motor. All the CMMT servo motor controllers are housed in the electrical cabinet just outside the air-conditioned room. These communicate via Profinet with the PLC that controls the installation. Combining different egg flavours, therefore, no longer requires any manual handling.
“Another advantage with Festo was that they offer a full range of components,” added Bob. “That includes not only the mechanical drives, gearboxes, motors and drives but also all the necessary mechanical fittings and accessories. This has helped enormously in standardising and also ensures that all the components are perfectly matched. The flexibility we now have with this installation, we would not have
Thanks to Festo electric drives, a variety of flavour mixes can be achieved without difficulty.
been able to achieve with pneumatic drives.” www.festo.com/gb
Because we manufacture 85% of our products, through our 18 production facilities around the world, we stand behind the quality of our services.
Our offer includes systematic eco-design in each of our specifications, in order to drive our development while limiting our impact on future generations.
The common goal of our product managers and services is to offer reliable, sustainable, high-performance products in compliance with the regulations and/or standards of each territory where they are used.
Materials handling specialist Windsor Materials Handling believes that the adoption of the latest technological advancements, strong environmental credentials, and a competitive lifetime cost define the best solutions in the materials handling sector. This approach has driven the introduction of new product lines from UN Forklift and XCMG to the company’s portfolio.
Having a diverse product offering is more crucial than ever in today’s climate.
Equipment portfolios within the materials handling industry have to reflect the dynamic nature of the markets we work within and consumer behaviour more generally.
Due to market saturation, it is no longer enough to simply ‘do what we’ve always done because it works.’ To maintain a competitive advantage, product differentiation ensures that Windsor Materials Handling stands out to attain and retain new and existing customers alike.
As a company, Windsor invests heavily in conducting the appropriate levels of due diligence on the product lines it brings to market, which includes frequent reviews to ensure that what it does offer remains relevant to customer needs.
With this unique multi-brand dealer approach underpinned by a ‘local service, nationwide’ maintenance offering through its 13-branch strong network, Windsor stands proudly as the largest family-owned materials handling company in the UK.
Adaptation to market trends is without question at the top of the agenda when
deciding on the manufacturers the company partners with, and today’s directive is typically aligned to three core decision-making factors: technological advancements, environmental credentials, and lifetime cost.
Through market insights and analysis of its sales patterns, Windsor is confident that through data-driven decisions, it has optimised the product mix it offers, discontinued products with low demand and consolidated the brands available within the marketplace. The company believes it is bringing to market its best portfolio to date.
To this end, these factors have been considered ahead of the company’s recent introduction of new product lines from UN Forklift and XCMG. This launch has already spiked its customers’ interest, and by building upon Windsor’s already diverse range of products along with its tailor-made service offering, it is seeing an increase in retained and new customers.
While the initial months of 2022 witnessed a resurgence in consumer spending and increased business activity, the global energy price shock triggered by the Russian invasion of Ukraine meant the logistics sector was forced to navigate a challenging
economic climate in the second half of the year.
That along with the increasing need to decarbonise, Windsor sees both the challenge and the opportunity at a regional level. The company has been working hard over the last 24 months to prepare the businesses it works with to adopt more sustainable operations in supporting those with older IC fleets in the transition to electric or lower-carbon fuels.
Perhaps the most immediate challenge for businesses in the logistics sector is the shortage of skilled labour, particularly engineers, where recruiting and retaining good employees has been a hindrance for some time. Strong relationships are key to long-term success in any business, and Windsor is fortunate that for some years now, it has been investing in building the talent pool through the apprenticeship scheme. It also has an internal training division dedicated to upskilling engineers to keep them abreast of changing technologies, enabling the company to keep reaching the service levels that its customers choose it for.
windsor-mh.co.uk
While machinery inspections are an essential part of manufacturing, they can be complex and time-consuming to complete. MachineSafe is an all-in-one compliance platform that streamlines the entire inspection and reporting process.
The manufacturing sector is an environment where safety is non-negotiable and precision is paramount. Rigorous inspections are essential, whether assessing existing equipment or evaluating new machinery. Yet, these inspections can be time-consuming and labour-intensive.
Recognising this industry-wide challenge, safety professional, Jon Rowen, has developed MachineSafe. This one-stop digital platform streamlines inspections and transforms how the manufacturing sector approaches and achieves equipment safety.
MachineSafe simplifies the process of conducting and managing inspections by offering ready-to-go modules including PUWER, risk assessment, new machinery assessment, CE/UKCA marking, and controls, pneumatic and hydraulic systems.
With an intuitive and user-friendly design, the platform offers a suite of features to boost efficiency and close the loop on compliance, traceability and accountability.
“Equipment non-compliances are often common within a factory. By providing a comprehensive drop-down list of common issues and associated control measures, along with a comments box to add context and clarity, MachineSafe streamlines the process of identifying and managing compliance issues,” Jon explained.
“By integrating risk assessments directly into the inspection module for non-compliance items, we have created a truly optimised inspection process. Additionally, once recommended control measures are actioned, reference photos can be quickly and easily attached to the original report as implemented control measures, further enhancing traceability and compliance.”
Tailored to meet the needs of original equipment manufacturers (OEMs),
machinery end-users and safety consultants, MachineSafe offers the flexibility of conducting compliance assessments on an iPad or Android tablet, ensuring the inspection experience is as hassle-free as possible.
Inspection reports seamlessly synchronise with the secure MachineSafe cloud portal, where they can be edited and expanded upon on a PC or laptop. Completed reports can be converted to a PDF format and shared with colleagues and customers.
The Provision and Use of Work Equipment Regulations 1998 (PUWER) is a set of key regulations governing workspace safety in the UK. They are in place to ensure the proper use of work equipment through training and maintenance and to protect workers and others from harm.
PUWER regulations apply to a wide range of workplaces and equipment, including machinery, tools and appliances. Planning PUWER inspections can be daunting, especially if your historical records aren’t as thorough as they should be. This is where MachineSafe steps in.
“MachineSafe PUWER is our most indemand entry-level module, designed to
make PUWER inspections as straightforward as possible,” continued Jon. “In addition, we will set up your PUWER planning schedule, allowing you to see when PUWER inspections need to be carried out together with the status of each inspection and its risk score on your MachineSafe dashboard.”
MachineSafe’s PUWER training and support package ensures users have the necessary skills to carry out inspections and get the most benefit from the platform.
As manufacturers invest in factory equipment, carrying out a thorough new machinery audit is a reliable method to safeguard against unexpected issues.
“Performing a factory acceptance test is crucial. It serves as your final chance to identify and address any non-compliance issues before the equipment is shipped. Addressing such concerns after the equipment reaches the user’s factory can be significantly more costly and time-consuming,” continued Jon..
“Our new machinery compliance audit module is designed to ensure the right items are checked during a factory acceptance test, greatly reducing the risk of receiving noncompliance equipment.”
machinesafe.co.uk
Turck Banner explains how machine safety indication can greatly increase productivity.
In areas where machine safety systems are employed, operator timing is one of the main culprits for production loss.
Operators often alternate between being too quick to anticipate the safe (muted) part of the machine cycle causing a safety trip, or being too cautious, losing time after the safe part of the machine cycle has begun the next operation.
Safety standards have strict requirements for muting lamps and safety indicators, which cannot be ignored. However, supplemental indication that acts as guidance to the operator and other workers, can have a dramatic effect on increasing productivity.
Of course, if the operator has to change their focus to look for the indicator, or if the indicator is unclear, time and efficiency will be lost. However, the area lighting doesn’t have to be white. By changing the colour of the lighting when it is safe to perform the next task, the operator can observe this with their peripheral vision; no time is lost, and they are unlikely to jump the gun.
The choice of colours is also important. Changing between red and green to indicate unsafe and safe conditions is often a good choice. However, if the operator is required to perform intricate or complex tasks, using a green light may hinder their ability to see clearly, so a more natural white light would be a preferable indication.
If a process has long periods between safe conditions, adding an amber period before the safe time could assist the operator in preparing for the next task. Conversely, for a process with a short cycle time, adding an amber period may hinder the operation by creating a situation where the operator acts prematurely.
In the context of machine safety systems, the psychological effects of lighting are particularly significant. Workers operating heavy machinery or performing intricate tasks require focus and attention to detail. Appropriate lighting helps them see clearly and contributes to a sense of security and confidence in their work environment. When workers feel safe and comfortable, they are better equipped to perform their duties effectively, ultimately driving productivity levels higher.
Another area where production is lost due to safety systems is locating the cause of a safety activation. Sometimes, the cause is obvious if, for example, the operator has been too eager and tripped a safety light curtain. Other activations may be less obvious and much more difficult to diagnose; for example, when a door sags on its hinges and the safety device monitoring it becomes misaligned. In these conditions, choosing a safety system with good diagnostics can save time and stress in resuming production.
Turck Banner offers lighting products and safety systems ideally suited to industrial
environments. Its LED lighting and indication range includes products with IP65 and IP69K ratings, which are also resistant to harsh chemicals and cutting fluids. These products can be mounted close to where the light is required, providing bright and uniform illumination that can change colour by hard-wired connection or PLC protocols.
Turck Banner’s safety portfolio also includes illuminated E-Stops, where the whole base turns red if the button is pressed, and safety controllers with in-series diagnostics, which pinpoint the location of the safety device that has been activated and provide device monitoring to give early warning of common problems like misalignment.
The IP65/IP67 safe I/O modules with Profinet/Profisafe and EtherNet/IP/CIP Safety allow Turck Banner to provide a solution for every application scenario: full-safety I/O modules with eight safe inputs/outputs or hybrid I/O modules in which standard and safe inputs/outputs are combined in one device. All modules work independently or in conjunction with external safety PLCs and controllers. The safety configurator allows the device to work as an independent IP67 safety controller, processing safety signals and IO-Link function in a single device.
The compact hybrid controller is unique, as half of the module has safety connections, while the other has non-safety connections. Combining the two halves enables users to analyse in-series safety devices by providing in-series diagnostics via IO-Link. The device lets users control the supplemental indication and lighting via IOLink or standard I/O ports.
turckbanner.com
Beginning production of a new formulation, batch, or innovative product can often bring new challenges. Knowing which pump to use can be another. Independent pump manufacturer and distributor Northridge Pumps looks at some factors to consider when selecting the best solution.
Container emptying, batch transfer, container filling, pilot plants, and test rigs are some of the most common applications encountered when trialling a new application or scaling a process.
But what considerations should be given to such pumps, and which pump might deliver the results you need?
Containers are supplied in various sizes, from small totes to 205l Drums and 1000l tanks known as IBCs.
Such fluids are sometimes so thick that when delivered in barrels or containers, if the incorrect pump technology is chosen, fluid is not pumped – holes are made with the pump within the container of fluid, rather than it being completely emptied, with large amounts of product remaining.
Not only is the product within the centre of containers a cause for concern, but also fluids that may remain stuck to the side of the container, and the amount of wastage this can generate.
Through careful planning, versatility can be introduced into container emptying applications. By selecting differing pump lengths, a single motor can be used with multiple barrel pump types, enabling the handling of multiple fluids – from thin to viscous, safe to flammable, or inert to corrosive.
Test rig pumps are pumps used to enable testing of components, testing of concepts and also in educational machines for the understanding of engineering principles such as fluid dynamics.
As new equipment is developed, a small-
scale plant is built as a proof of concept, allowing testing and establishing limits. Often, such plants are built on a tight budget, but that doesn’t mean performance should be compromised.
A user of dielectric cooling systems contacted Northridge Pumps, wanting to test a newly developed fluid, and they sought assistance in selecting the right pump for this application. A centrifugal pump could achieve the duty, but was that the right choice?
At first glance, it met their budget and handled a duty point relatively easily, but due to centrifugal pump design, whereby flow alters with pressure as speed is reduced, it would mean that incorrect conclusions would be drawn.
After discussing the merits of a positive displacement pump, in which flow remains constant with pressure and is directly proportional to speed, the client opted for this solution as they could reach conclusions with far greater certainty than if they had chosen a centrifugal design.
Batch transfer involves the bulk transfer of set amounts of fluid within a time frame. It can be used for applications involving the filling or emptying of vessels or the mixing of ingredients.
Suppose the pump is used in a plant where mixtures change along with the fluid’s viscosity and consistency. In that case, careful attention will need to be paid to ensure that the pump can handle the characteristics of different fluids, such as increased specific gravity, which can pose challenges for some designs.
Similar to the positive displacement pump example above, having a pump where flow and pressure can be altered according to the fluid viscosity will ensure the pump meets process requirements and will not have issues during the emptying of vessels when fluid contents are low or transferred volumes change.
So, what factors should be considered when looking to scale production or conduct trials?
• Viscosity: Can differing viscosities be transferred?
• Solids: Will particles be transferred without damage to the unit?
• Sensitivity: Will the fluid be transferred without alteration?
• Flow output and pressure: Can the output be altered easily?
• Multi-use: Is the unit easily ported between tanks or processes?
• Future proof: Is the unit upgradeable for future applications?
• Personalised batches: Can the unit handle small personalised batches and be fully sanitised between fluids?
www.northridgepumps.com
Regular pump system maintenance is essential to prevent significant cost and reputational issues. Thomas Marks, General Manager at the Association for Electrical and Mechanical Trades (AEMT) looks at several issues that poor pump maintenance can lead to and outlines some of the key steps that can be taken to minimise the chance of them emerging.
Failing to adequately maintain industrial pumps can lead to various issues that can compromise the safety, efficiency, and longevity of the equipment and the wider systems the pumps are part of. One of the most immediate risks is the failure of the pump itself. Worn-out parts, clogged systems, or misalignments can cause a pump to break down, leading to potentially costly unplanned downtime. In addition, further unnecessary costs can be incurred when a poorly maintained pump consumes more energy to deliver the same output.
Inadequate maintenance can also accelerate the wear and tear of pump components, leading to more frequent parts replacement and higher maintenance costs. And pumps that are not adequately maintained tend to have a shorter operational lifespan, leading to more frequent pump replacements.
Worn-out seals or corroded parts can lead to leakages, resulting in the loss of valuable fluids, environmental contamination, and safety hazards. Without proper lubrication or cooling, pumps can overheat, damaging internal components and reducing their lifespan.
Other issues, such as misalignment or imbalance, can cause excessive vibrations, damaging the pump and its supporting infrastructure. While cavitation, which can be a symptom of poor maintenance, can damage a pump’s impeller and other components as vapour bubbles in the pumped liquid collapse, causing destructive shock waves.
Leakages, overheating, and equipment failures can pose safety risks to personnel working around the pumps. This can lead to accidents, injuries, or even fatalities. While
leaks or spills due to poor maintenance can also lead to environmental contamination, which can result in regulatory penalties and damage to a company’s reputation. And for companies that rely on pumps for critical operations, frequent breakdowns or safety incidents can also damage their reputation and customer trust. Indeed, in some industries, ensuring that equipment like pumps is adequately maintained is a regulatory requirement. Failure to comply can lead to financial penalties or legal actions.
Regularly inspecting pumps for signs of wear, damage, or corrosion is essential. This helps in identifying potential issues before they escalate. Proper lubrication is also vital for the smooth operation of pumps. It’s essential to use the correct type of lubricant and to ensure it is applied at the correct intervals.
Regularly checking and replacing wornout seals is crucial, as is ensuring that cooling systems are working efficiently to prevent overheating.
Vibration can indicate misalignment, imbalance, or other mechanical issues. Regularly monitoring and analysing vibrations can help with the early detection
of problems. Ensuring that the pump and its motor are properly aligned is also essential to prevent wear and tear and to ensure efficient operation.
As part of condition monitoring solutions, vibration sensors can now continuously monitor a pumping system to identify vibration-related issues as they emerge, and other types of sensors can track a pump’s performance and help to identify problems like reduced flow or increased energy consumption. Systems such as these can also monitor the state of bearings to enable them to be replaced as soon as any performance issues are indicated.
Keeping detailed records of maintenance activities, parts replacements, and performance metrics can help plan future maintenance and identify recurring issues.
Industrial pump maintenance is a comprehensive process that involves a combination of regular checks, timely interventions, and proactive measures to ensure the longevity and efficient operation of the pumps. But it is essential if the risks that can lead to wide-ranging consequences, from increased operational costs to safety hazards and environmental damage, are to be avoided and the smooth operation of industrial pumping systems is to be ensured.
www.theaemt.com
Connectivity specialist binder explains how high-frequency electronics integrated into the circular connector can help reduce the density of electromechanical functions inside the component’s housing, promote miniaturisation, and still create more space for optimised power transmission.
Miniaturised interfaces for signals, data, and electrical power are an engineering challenge per se. When it comes to components for medical technology, developers face even more stringent requirements. Failure protection, signal integrity, as well as functional, operator, and patient safety make their design tasks even more complex.
The increasing functional complexity places tight physical limits on the miniaturisation of interface components. In state-of-the-art M12 circular connectors, for example, which comply with the draft standard 63171-7, power pins, protective contacts, shielding, and data ports coexist in a very small space. Although this is appropriate and desirable for overall functionality, it immensely restricts freedom
in the design of individual functions. In the case of medical devices, this is particularly challenging. The compactness of the connectors is thus generally limited here, and many of these interfaces have already reached the boundaries of practical feasibility.
Traditionally, in connectors, signals, data, and power are all linked via electrical contacts, whose mechanical and chemical properties fundamentally determine the performance, quality, and efficiency of transmission. In order to keep losses to a minimum, such direct electrical connection is absolutely essential for the power supply –but is not required for signals and data.
In the world of data transmission, there are proven standards for both wired and wireless connectivity. The use of the corresponding
Hybrid connectors with NFC –developers can use the entire installation space inside the connector for the power pins, expanding the design options.
technologies depends mainly on the type and amount of data to be transferred, but also on the environmental conditions. While broadband wired Ethernet is becoming more and more established in instrumentation and automation technology, the low-energy Zigbee and Bluetooth LE – or high-speed WiFi – are good examples of widespread wireless communication standards. For data rates above this spectrum or in environments with electromagnetic interference, optical transmission methods such as fibre optics are also used.
In view of this variety of possibilities, the question arises as to what extent they can contribute to solving the problem of limited miniaturisation of interface components in combined signal, data, and power connections. For example, what if signals and data could be transmitted between the male connector and the device without
occupying space for electrical contacts? Without having to shield them from supply pins and from supply wires? What if the IP-protected installation space inside a connector housing could, in future, be used exclusively – or at least much more than before – for power transfer? What if the connector could accommodate an even wider range of functions?
With the NeaCo² technology demonstration, binder explored this question and successfully merged the two worlds of electromechanical and wireless interfaces. Using NeaCo², the engineers from Neckarsulm/Germany have shown how electromechanics and Radio Frequency (RF) electronics can be combined in a small hybrid connector. While power is transmitted via the traditional pins, they have implemented wireless Near-Field Communication (NFC). NFC has a significantly shorter range than Bluetooth or WiFi, for example, but allows the NeaCo² to be used in numerous new
applications, such as device identification, predictive maintenance, and fault prevention. In short, binder has used the integration of RF electronics to transform passive hybrid connectors into active system components, so-called micro devices.
These offer tremendous advantages. Developers can use the entire installation space within the connector for the power pins, widening their design options. And this helps them optimise the efficiency of the compact and protected power port. Electronics integration also adds options to the development of product variants. The respective connector itself can be equipped with additional features, but can also act as a communication node – or even as a controlling device.
The possible new features that can be integrated into the hybrid connector thanks to NFC include:
• Identification of approved devices; only approved devices receive power
• Identification of devices for optimised power transfer
• Counting of mating cycles and recording of
electrical resistance in order to predict faults
• Metering transmission power and temperature
• The function as an access point for live data traffic
• Safety shutdown if operating limits get overrun
• Minimised susceptibility to errors caused by contamination thanks to contactless data transmission
• The use of an additional data channel for migration systems
By integrating RF electronics, engineers are able to transform passive connectors into active system components. Thus, these receive new characteristics and distinctive features. The performance and communication capabilities of the hybrid interfaces may improve, and additional application scenarios may arise. The new connectors can be used across all industries beyond medical technology – from industrial automation to e-mobility.
www.binder-connector.com/uk
Andrew Jones, Technical Director at Axair Fans UK, looks at the benefits of outsourcing specialist engineering expertise, especially in the air moving sector.
For many years, the scarcity of inhouse engineering ability has been one of the leading workplace concerns among engineers in the public and private sectors. Post covid redundancies, economic factors including Brexit, a plagued industry perception of spanners and dirty overalls, an ageing workforce, and a new generation of Snapchat and Instagram filter lovers, have left a shortfall of up to 59,000 core engineering roles. This especially puts small to medium companies at risk.
Inefficiency in small company operations leads to reduced productivity, waste of time, and loss of resources and prevents business managers from focusing on their companies’ core services. Couple this with small and medium companies that lack the financial capability to hire professional experts; many find themselves trapped in situations where employees do not possess sufficient technical expertise to counter the advancing technology in the industry. This expertise gap puts them and the businesses they work in at a disadvantage against competitors.
Training employees with the relevant skills is an option, but an expensive and time consuming one, and as we’ve already established, those small or medium companies do not have the time or finance to invest without immediate gain.
consultants charge based on time or based on the nature of the visit, and component suppliers typically charge for the product with limited warranty periods, not extended integration support. Working with a company that offers a hybrid of both – I’ll be specific and say in air movement, specifically fan integration –small to medium companies get access to high levels of focus, years of experience and deep knowledge of motor and impeller technologies, gained from comprehensive training, certifications, and personal growth. Having one foot in with a company that has access to the latest industry advancements equally allows businesses to remain relevant and competitive in their sectors instead of sticking with what they know and getting left behind.
We see this far too often in mechanical engineering, particularly the integration of fan engineers in technical applications where the fan is predominantly the workhorse of the system. If an air movement system isn’t performing correctly, the first place to look is the industrial fan. Does it achieve the duty required for optimal performance, does the wheel type allow the right pressure development, does the motor produce enough power to drive the impeller to generate the airflow required?
Outsourcing the level of expertise is another option. The demand for outsourced technical services is rising continuously in the IT sector, with full or partial services that allow companies to obtain access to technical expertise when they need it without the hassle of full-time departments. So, what about the integration of single components, fans in this instance, where the knowledge is so niche that companies don’t need a service agreement or a monthly retainer; they simply need assistance to use the product they want to buy, to make their system better, so they can make their customers happy?
Choosing a company that offers a service and sale with a consultative approach is hard to come by. Typically, specialist
Don’t get me wrong, technical product managers, project engineers and robotics engineers are all in high demand and, in most parts, occupied. These roles would have topped the engineering position list even ten to 15 years ago, but with an ageing workforce, these roles have had to adapt, particularly as industry 4.0 technology has evolved. Upskilling and continued personal development are crucial if companies don’t want to open themselves up to skills gaps. That diamond in the rough company that offers the sale and service that larger companies don’t appreciate widens the talent pool and solves a skill-short market that smaller businesses cannot afford to overlook. The question is, are you getting that from your current supplier?
www.axair-fans.co.uk
Production areas of the chemical industry, refineries, paint shops, bulk material processing, sawmills and grain processing companies have increased risk of explosion. For these applications, Schmersal has developed the ATEX certified SLC/SLG440 safety light curtains and grids.
The Ex-SLC440 for finger, hand and body detection are available in variants with a resolution of 14 and 30mm and ranges from 0.3 to 20m. The Ex-SLG440 safety light curtains are suitable for access control in hazardous areas. The waterproof and dustproof devices achieve IP66 and IP67 protection and can also be used outdoors.
The devices can be installed in potentially explosive gas and dust atmospheres, they are used to protect hazardous areas and access points for machinery. If one or more beams are interrupted, the dangerous movement is brought to a standstill.
www.schmersal.co.uk uksupport@schmersal.com
Boosting competitiveness, protecting the climate, and promoting prosperity – are the major tasks facing the industry today. Innovative technologies are the key to mastering these challenges. But how can companies make efficient use of automation, artificial intelligence, renewable energies, and hydrogen? And what steps can be taken to counteract the impending de-industrialisation of Europe? HANNOVER MESSE 2024, which runs from 22 to 26 April, will provide answers.
In describing the environment in which this year’s HANNOVER MESSE takes place, Dr Jochen Köckler, CEO of Deutsche Messe AG, said: “Geopolitical tensions, climate change, stagnating growth, high prices for energy and a shortage of skilled workers mean that cost discipline and efficiency are currently the dominant themes in companies. At the same time, artificial intelligence is leading to profound changes in the world of work in industry. In addition, business leaders and trade associations are warning of a de-industrialisation of Europe.
“HANNOVER MESSE is more important than ever this year, because the economic environment has rarely been so volatile. In Hannover, technologies and solutions will be presented to enable industry to produce on a competitive and sustainable basis. The trade fair will be all about intelligent and carbon-neutral production, AI, hydrogen, and cross-sector energy solutions. For European companies in particular, HANNOVER MESSE will thus create a bulwark against the impending de-industrialisation of Europe,” added Dr Köckler. “Our exhibitors will show that competitive industrial production is possible in Europe. However, this will require a regulatory framework that promotes innovation and entrepreneurship.”
The solution lies in the interplay of automation, digitalisation and electrification, broad cross-industry and cross-border cooperation, and a clear political course.: “With the lead theme ‘Energizing a Sustainable Industry’, 4,000 exhibitors, high-calibre representatives from politics and industry, and with Norway as the partner country, HANNOVER MESSE 2024 is the ideal platform for this,” continued Dr Köckler. “Visitors to HANNOVER MESSE are looking for guidance on how they can
use automation, artificial intelligence, renewable energies or hydrogen in a meaningful way. This is precisely the expertise that the exhibitors at HANNOVER MESSE can provide.”
For more than a decade now, HANNOVER MESSE has been the most important trade fair for the digitalisation of industry. Artificial intelligence (AI) is now taking industrial digitalisation to the next level by revolutionising industry, making processes more efficient and adding value. By using AI, companies will be able to shorten development times while saving resources and energy.
discussed at HANNOVER MESSE,” added Dr Köckler.
“The speed at which AI solutions are finding their way into industry is breathtaking. Companies need to invest now and, above all, introduce their employees to the opportunities offered by AI. Otherwise, they will get left behind by the competition,” added Dr Köckler. “AI is the key to competitiveness and sustainability in industry.”
Specific applications will be on show at HANNOVER MESSE, including robots that can be controlled by voice, machines that automatically recognise defects and systems that cut downtime through predictive maintenance.
“In the near future, generative AI will be able to design machines. This will lead to fundamental changes in engineers’ job profiles – a subject that will also be
HANNOVER MESSE is the world’s leading trade fair for industrial technology. Its lead theme, ‘Energizing a Sustainable Industry, ‘ brings together exhibiting companies from mechanical and electrical engineering, the digital industry and the energy sector to present solutions for the future of manufacturing and energy supply. Leading topics include Industrie 4.0/Manufacturing-X, energy for industry, digitalisation/artificial intelligence and machine learning, carbonneutral production, and hydrogen and fuel cells. Conferences and forums complement the program.
The next edition runs from 22 to 26 April 2024 in Hannover, Germany, with Norway as the event’s Partner Country.
www.hannovermesse.de/en
We transform industry – innovative, sustainable and digital. 22 – 26 April 2024 Hannover, Germany hannovermesse.com
The CHEMUK 2024 EXPO will return on May 15 and 16 at the NEC in Birmingham. Running as part of the trade show, event organiser, UK Industry Events, has announced the launch of the new Process & Chemical Engineering Show Zone.
The Process & Chemical Engineering Show Zone will be the UK’s only event that brings process engineers from the chemical, food & beverage, pharma, oil & gas, and water & wastewater industries together to experience the latest innovation that is shaping and inspiring the process industries under one giant roof.
The new focused event zone will present hundreds of specialist process engineering suppliers to attending process professionals who are involved directly in the design, development, management, and maintenance of operations in the processing of liquid, solid, powder, and gas-based process engineering industries.
Managing Director of UK Industry Events, Ian Stone, explained the decision to introduce the focused show zone. “The Process & Chemical Engineering Show Zone will give attendees the ability to survey the wealth of new technology and products that are available but also to be able to share that knowledge across the various vertical industries that are the application areas for process engineering,” explained Ian.
“Process engineering is, of course, in essence, chemical engineering in as much as it is the application of chemical unit operations and unit processes. So, there is an ‘esprit de corps’ among all major process engineers, often coming through a classically chemical engineering educational base”.
Running as part of the show will be the Process & Chemical Engineering speaker programme. Highlights from this year’s show will include a series of 90-minute miniconferences, including:
• ‘Scale-Up’ challenges, towards sustainable production - IChemE Mini-Conference
• Bioprocess Scale up: From bench top to
commercialisation - IBioIC Mini-Conference
• Process Intensification Symposium: Unlocking the potential of process intensification for net zero - Hosted by Process Intensification (PI) GroupNewcastle University Mini-Conference
• Technologies that will disrupt chemical manufacturing - Hosted by Innovate UK & Biotechnology and Biological Sciences Research Council (BBSRC) MiniConference
In addition, the speaker programme will present several expert presentations and keynotes, including:
• IChemE Presidential Address
• Supporting your journey to net zeroInnovate UK KTN on behalf of Dept for Energy Security and Net Zero/ DESNZ
• Is it just yet another fieldbus? Ethernet conquers instrumentation in process industry – ABB
• Process intensification of batch chemistry production - Thermal Fluid Systems
• New technologies from the solvents industry on the road to net zero – Solvents
Industry Association
• Connecting into the UK’s innovation support ecosystem - ScotCHEM panel session
• Continuous membrane-based separation to improve batch extraction productivity –Zaiput
The Process & Chemical Engineering Show is partnered with the major trade bodies and industry associations supporting the process engineering sector, including the IChemE (The Institute for Chemical Engineers), BVAA (British Valve & Actuator Association), BPMA (British Pump Manufacturers Association), UKGSA (UK Gaskets & Sealants Association,) Process Intensification Network, NEPIC, and Chemicals Northwest, amongst others.
CHEMUK 2024 takes place on Wednesday, May 15, and Thursday, May 16, 2024, in Hall 1 at the NEC, Birmingham, and free entry badges can be secured on the event website.
www.chemicalukexpo.com
The PPMA Show is gearing up for another tremendous processing and packaging machinery event when it returns to the NEC in Birmingham on 24-26 September 2024.
Established over 35 years ago, the PPMA Show is the UK’s largest event of its kind, bringing together wellknown brands to showcase their innovative, cutting-edge processing equipment, packaging machinery, industrial robotics and machine vision systems.
The PPMA Show is organised by Automate UK, comprising the Processing and Packaging Machinery Association (PPMA), British Automation and Robot Association (BARA) and UK Industrial Vision Association (UKIVA). The three associations combine under the banner of Automate UK and have a total membership of over 550 member companies.
This annual event is renowned for representing a thriving industry made up of a vast array of sectors, including pharmaceuticals, food, beverages, household products and toiletries, microbreweries and distilleries, pet care, FMCG, and building materials and supplies.
The show attracts buyers and key decision-makers, including CEOs, MDs, directors, managers, and other key staff members who play vital roles within their companies, including engineers, production specialists, designers, buyers, processing specialists, and project managers. The PPMA Show furnishes visitors with industry knowledge, such as trends and insights, which they can take away and use to improve their businesses.
There are exciting opportunities for existing processing and packaging machinery users to discover the latest innovative processing and packaging machinery technology and solutions. The show also provides, for those new to the industry, an abundance of opportunities to learn and explore what this fascinating industry has to offer.
There are a number of reasons to visit the PPMA Show. Over 350 big brands
from the full spectrum of the industry will be showcasing the latest state-of-the-art technologies so visitors can see how incorporating these solutions can improve and boost their business. Visitors can also network and engage with a variety of impressive exhibitors in person.
The event is an opportunity for visitors to see a complete production line in action from start to finish, from labelling, filling and packaging to processing, robotics, automation and industrial vision systems.
expand professional networks, establish new business contacts and develop existing relationships.
The show boasts an impressive seminar programme led by leading industry experts. This provides a unique opportunity to not only absorb their wealth of knowledge and expertise but also to stay informed about the latest industry developments.
There are unparalleled opportunities to make valuable business connections,
The PPMA Show represents an ever evolving and fast-growing processing and packaging industry that has plenty to offer to everyone, whatever their level of expertise.
Anyone wishing to attend can register for a free ticket on the event’s website.
www.ppmashow.co.uk/visit
LiftEx 2024, the annual flagship event of LEEA (Lifting Equipment Engineers Association), will take place on 16-17 October 2024 at Olympia London’s West Hall.
Now is the time to secure exhibition space to be part of the premier, free-toattend showcase dedicated to the lifting and height safety industries – an essential event for the manufacturing and engineering sectors.
Celebrating its 19th year in London, LiftEx is a must-visit for anybody involved with procuring or using services and lifting equipment to support production and assembly lines in plants and factories around the world. It offers the perfect opportunity to network with the global lifting Industry and have face-to-face meetings to build strong working relationships.
Exhibitors can source new business by showcasing their products and services to a targeted and quality audience of lifting professionals. This will comprise end users from not only the manufacturing and engineering sectors but also from construction, oil & gas, offshore, defence, utilities and entertainment – to name a few, as well as lifting safety professionals.
Innovative new products and services that improve efficiency and reliability can provide crucial solutions for achieving successful manufacturing. A variety of cranes, hoists, platforms, cradles and their associated chains, ropes and slings will be on show alongside materials handling and height safety equipment, as well as administrative services.
There will be great examples of how the forward-looking lifting Industry is always innovating, with constantly developing technologies spreading throughout the sector to reduce risk in lifting operations. These include AI, virtual reality simulation, condition and load monitoring, remote control, and anti-collision systems.
But LiftEx is also a chance for operations to enhance safe practices, which is particularly important in busy manufacturing and production operations. It is vital that
those responsible for procuring lifting equipment and services in these operations fully understand the risks, consequences, and legal obligations and can filter good practices from the bad. The LEEA (Lifting Equipment Engineers Association) team and industry experts will share expertise and industry insights at LiftEx to help visitors in their everyday roles.
LiftEx 2024 will build on the success of last year’s event, held in Liverpool, which was the largest and most successful ever, with a record number of end-user visitors from multiple industries walking the aisles over two busy days. Here’s what some of the exhibitors at that show had to say:
Marcel Blake, Co-Founder of Core Inspection Software, said: “Our experience at LiftEx 2023 was exceptional. We were impressed by the number of genuine industry contacts and the overall quality of visitors. The event was well run and gave us a good source of new opportunities,
paving the way for some great business partnerships in the new year.”
Tessa Aindow, Marketing Manager, Modulift, said: “LiftEx 2023 was the busiest and best yet for Modulift. Our exhibition stand was buzzing from start to finish, with new and familiar faces from around the world and a significant number of end-user visitors, too. We’re already looking forward to next year’s event.”
LiftEx 2024 will be a jam-packed event, so keep an eye out for the schedule of on-site activities and show features to be announced over the next few months. Sponsorship packages are currently available for companies to raise their profile and get ahead of the competition. These packages include Headline Sponsor, Gold Sponsor, Silver Sponsor, Lanyard Sponsor and Official Water Sponsor.
Further details of exhibiting and sponsorship opportunities can be found on the event’s website.
events.leeaint.com/liftex-london-2024.
SAVE THE DATE
16th – 17th October 2024
The networking exhibition for users of lifting and height safety equipment
16th – 17th October 2024
Olympia West, London
Sponsor:
Attended by 1,500 professional visitors over 2 days. liftex.org
Hosted by:
Connect factory floor sensors to the cloud and start the digital transformation of your plant.
With the new IIoT starter kit and the user-friendly IO-Link masters from Pepperl+Fuchs, simple sensor data visualisation and analysis have become a reality. Discover the advantages of IO-Link and experience the seamless integration of IOLink sensor data into your Industry 4.0 application.
The kit includes an IO-Link master, (3) IOLink sensors, an Ethernet switch, a power supply, RFID tags and all the necessary cabling to get started. A quick start guide for connecting the IO-Link master and IO-Link devices is also provided along with software connection for various platforms such as AWS, PTC, AVEVA.
Connect your software dashboard via OPC UA or MQTT for straightforward interpretation of real-time data, and start the digital transformation of your plants now with the new IIoT starter kit from Pepperl+Fuchs.
www.pepperl-fuchs.com
C.K Tools has unveiled its new compact electric screwdriver.
The new T4930 E-Driver Electric Screwdriver allows users to quickly and accurately complete a job with ease, and in far less time than a manual alternative.
The E-Driver has been developed with a panel of tradespeople and is designed to tackle heavy-duty electrical jobs to small precision tasks, making it a versatile and portable companion to quickly and accurately drive screws and fasteners without fatigue.
Powered by a rechargeable USB-C 3.6v battery, the E-Driver offers a cordless and convenient tool with up to 200 minutes of operating time per charge. Its ergonomic design allows for supreme grip and control, and its intuitive forward and reverse buttons allow the user to change the direction of rotation, tighten and loosen screws with ease.
The E-Driver’s 6.35mm locking hex chuck retains the driver bit securely, and its torque adjustment dial, set up to 6Nm through the motor and up to 20Nm by manual rotation, allows for clear and easy adjustment to ensure screw fixings are tightened effectively. bit.ly/CKstockist
For Winn & Coales (Denso) Ltd, ensuring the longevity and cost-effectiveness of every application begins with helping customers select the most suitable Denso products for their project requirements, along with offering free product application training that’s available throughout the UK and beyond.
Its comprehensive training is available to distributors and contractors alike and can be undertaken at its dedicated training centre in London, on-site, or even virtually, to suit customer needs. The company’s highly knowledgeable Denso regional managers cover the entirety of the UK and Ireland to provide customers with training in correct and complete application methods. Recent training sessions include site visits to branches of Wolseley UK and Jewson Civils Frazer, along with Viking Johnson and Morrison Utility Services to provide training on the Denso P1 and P2 Systems – Denso’s CESWI 7th Edition compliant protection for ferrous pipes, joints and fittings in the water industry.
To register interest in free product application training, users can contact their local representative or fill in the contact form online, at: www.denso.net.
Fluke has launched a six-month buy-oneget-one-free offer.
Running between 1 March and 31 August this year, the ’Buy A Fluke, Get One Free’ offer means that anyone purchasing one of Fluke’s test and measurement tools during that six-month period is entitled to choose another product which will be free of charge. This gives technicians the ideal chance to upgrade or complete their toolbox with the latest tools available.
Fluke has set up six levels which each include five products that will be available for free, enabling customers who spend more to get greater benefit from the process. For example, those who spend between €150.00 and €599.99 (Level 1) will be offered such free products as a TPAK meter hanging kit, 1AC voltage detector or IR-450 pocketsize IR thermometer with laser pointer.
At the top of the scale (Level 6), free products available to anyone spending over €5,500.00 include a PTi120 9Hz pocket thermal camera, MicroScanner POE cable tester or a 34XRA True-RMS hand-held digital multimeter.
Customers who purchase Fluke products through authorised Fluke distributors can claim the free product through the Fluke website with the original proof of purchase, invoice, or receipt. www.fluke.co.uk/freefluke
3D Print Manufacturing
Midlands 3D Printing
T: 01785 594389
E: sales@midlands3d.com
W: www.midlands3d.com
Fibet Rubber Bonding (UK) Ltd
T: 01282 878200
E: sales@fibet.co.uk
W: www.fibet.co.uk
CEMBRE Ltd
T: 01675 470 440
E: sales@cembre.co.uk
W: www.cembre.com/en
Drives, Motors & Gears
Nord
T: 01235 534404
E: GB-sales@nord.com
W: www.nord.com
Impact Technical Services
T: 0116 244 8855
E: enquiries@impactts.co.uk
W: www.impacttechnicalservices.co.uk
Flow Meters
Titan Enterprises Ltd
T: +44 (0)1935 812790
E: sales@flowmeters.co.uk
W: www.flowmeters.co.uk
Silverson Machines Ltd
T: +44 (0)1494 786331
E: sales@silverson.co.uk
W: www.silverson.co.uk
Industrial Communications
Brainboxes
T: + 44 (0) 151 220 2500
E: sales@brainboxes.com
W: www.brainboxes.com
Intoware
T: 0115 977 8969
E: hello@intoware.com
W: www.intoware.com
Industrial Fans
Axair Fans UK Limited
T: 01782 349 430
E: sales@axair-fans.co.uk
W: www.axair-fans.co.uk
Machine Safety
Schmersal UK Ltd
T: 01684 571980
E: uksupport@schmersal.com
W: www.schmersal.co.uk
Marking Solutions
T-Mark
T: 0330 153 8320
E: sales@t-mark.co.uk
W: www.t-mark.co.uk
Pipework Systems
Jacob UK Ltd
T: 01694 722841
E: sales@jacob-uk.com
W: www.jacob-group.com/uk
Pressure Measurement Specialists
ESI Technology Ltd
T: +44 (0)1978262255
E: sales@esi-tec.com
W: www.esi-tec.com
Robotics & Automation
KUKA Robotics UK Ltd
T: 0121 505 9970
E: sales.uk@kuka.com
W: www.kuka.com
Sensors
IFM Electronic
T: 020 8213-0000
E: enquiry.gb@ifm.com
W: www.ifm.com
PLUS Automation Ltd
T: 0121 58 222 58
E: Sales@PLUSAutomation.co.uk
W: www.PLUSAutomation.co.uk
Storage Solutions
BITO Storage Systems Ltd.
T: 02476 388 852
E: Info.uk@bito.com
W: www.bito.com
Test & Inspection
AMETEK Land (Land Instruments International)
T: +44 1246 417691
E: land.enquiry@ametek.com
W: www.ametek-land.com
Simplify Complexity, Empower Efficiency
Technical excellence meets unbridled enthusiasm.
Join forces with our Hydraulic Heroes to unlock the future of industrial engineering.
sales@boschrexroth.co.uk
www.boschrexroth.co.uk