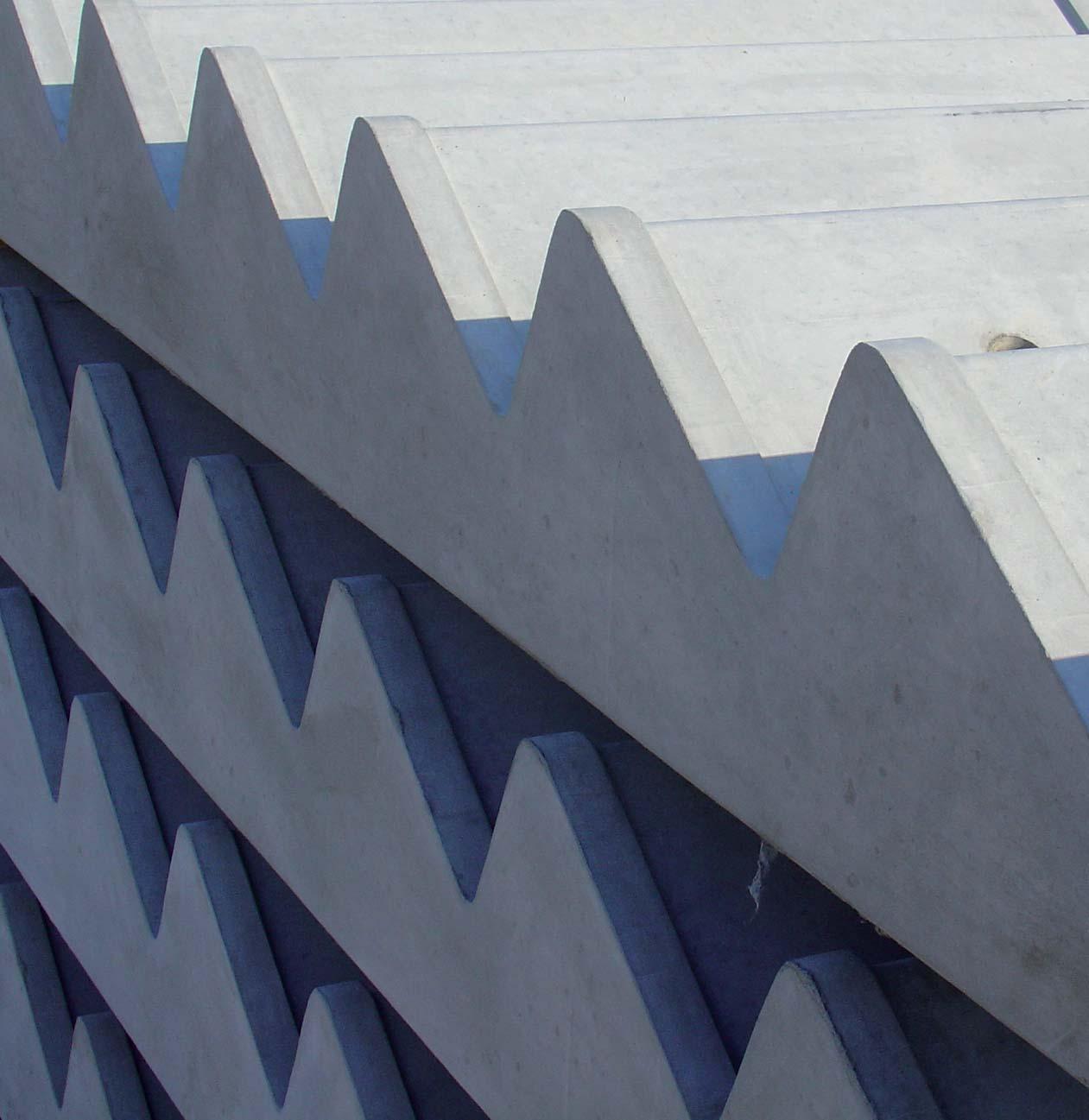
4 minute read
Prevailing strategies in architectural construction – Product structures
PREVAILING STRATEGIES IN ARCHITECTURAL CONSTRUCTION
– Product structures
Traditional product delivery: building by pieces
This fi rst category refers to building systems relating to traditional crafts and construction processes. Although the strategy is called: Traditional, product examples of this fi rst strategy can actually represent highly industrialised processes during production. Building materials as e.g. gypsum boards, bricks, fl ooring and even different kinds of mortar and fi ller are produced in factories with a high degree of automation, specifi c quality standards and effi cient supply systems (= industrialised). However, in the current context of industrialised building and industrialised architecture, this strategy becomes more problematic: If buildings are to be composed directly by such products (as they are in general today!) it is almost impossible to control all interfaces and thus the fi nal outcome in any industrialised way as defi ned above. The increasing amount of different building materials and the endless possibilities of combinations have eliminated the craftsman’s default solution and blurred the link between craft and modularisation of the building by lack of embedment in an established building tradition. This makes the establishment or agreement of clear interfaces (almost) impossible. Industrially produced building materials can be evident sub-deliveries of large elements or high levels of industrialised building and architecture, however, the industrial focus of building with materials and small components is mainly project oriented. It is primarily restricted to processes and to on-site construction in particular. The product structure therefore remains fragmented and is thus of less interest within the framework of this research. For further elaboration on this strategy, the concept and the theories of Lean Construction ought to be studied. They concentrate on “project based production management in the design, engineering, and construction of capital facilities”.1 The focus on products integrated in highly developed building systems is far more accentuated in the two other strategies described below: The integrated product delivery and the turnkey delivery. Substantiated by cases, this part will elaborate further on these two latter strategies and try to clarify their individual strengths, weaknesses and future prospects.
1 See Lean Construction Institute, http://www.leanconstruction.org/.
Prefabricated staircases, Dalton A/S. Photo: CINARK
Within the strategy of integrated product delivery, the building as a whole is conceived as a total of sub-supplied industrialised building assemblies. Each manufacturer provides a clearly delimited product, which ideally has well-defi ned interfaces with other adjoining assemblies or fi ts into some kind of general standardised frame. The focus of product development within this strategy is the performance of the assembly according to technical demands as well as its capacity to adapt to specifi c conditions set by the context. A determining competitive factor will be the manufacturers’ ability to sustain and maybe enhance these product architectures until they become best practice and eventually industry standards. Today, several examples of building assemblies can be found. Assemblies in our defi nition can have different scale and different degrees of physical/spatial integration with other assemblies or with the building as a whole. However, the idea of putting together a building or dwelling based completely on assemblies is so far not realisable – and perhaps not desirable, at least from an architectural point of view! However, by segregating certain parts of a building into integrated factory produced assemblies, it is possible to make use of both the technical and the economic advantages of a controlled production environment (prefabrication). This again opens new perspectives such as product guarantee, servicing and liability.

Units are transported to the building site on trucks. Photo: Tegnestuen Vandkunsten
Within the strategy of turnkey delivery, it is usually a single company or a consortium that is in charge of a total solution comprising the whole process from sale over production to fi nal delivery. In this sense, it might look like a conventional turnkey contract, but the main focus is a standardised ‘product’ and its entire value chain and not the single project, which is rather seen as a way to learn in order to improve later versions of the product. Furthermore, the turnkey delivery is usually characterised by a high degree of prefabrication. A brand is created with the product, which can have its own name different from the company itself. Questions of interfaces between elements or modules are solved internally within the product solution and the company. Although outsourced integrated product deliveries could be used as part of the solution, this is seldom the case. Due to the complexity of the fi nal delivered solution, a determining competitive factor – despite the product focus – will be the manufacturer’s ability to create and sustain the brand through excellence, highly esteemed references and credibility at project level. Most turnkey deliveries are based on a single base building system. Some concepts are highly standardised consisting of only one or a few types and low adaptation based on a specifi c physical appearance. Other concepts are more neutral and open, based on certain standardised structural principles and details, but are adaptable as regards the layout and appearance. As with the subassemblies, the high degree of control obtained through prefabrication facilitates quality check and product guarantee. Almost all all-encompassing systems are directed towards the single-family house market. However, more large-scale and multi-storey concepts are beginning to appear.
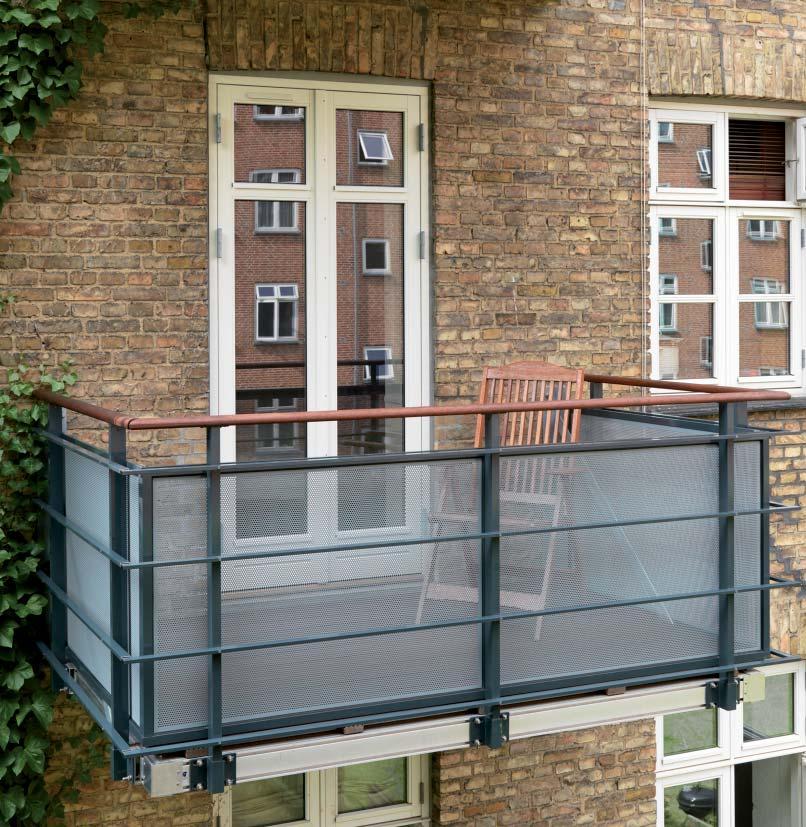
An example of an integrated product delivery from Altan.dk. Photo: Altan.dk